
Учебное пособие 800427
.pdf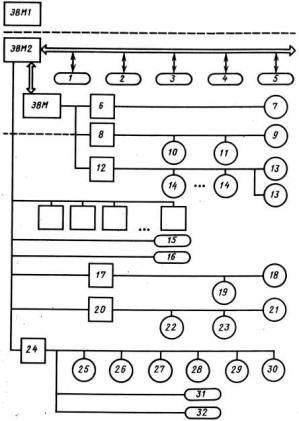
Система управления ГПС трехуровневая, с отдельной ЭВМ для управления складом деталей, транспортом и конвейерной системой (рис.1.23.). ЭВМ верхнего уровня выполняет долгосрочное планирование, автоматическое проектирование и подготовку УП. ЭВМ цеха промежуточного уровня служит для управления производ-
ством и контролем. Эта ЭВМ связана каналом с ЭВМ управления транспортом, скла-
дом и фактически обеспечивает выполнение функции концентратора сети микропро-
цессорных устройств нижнего уровня.
Рис. 1.23. Функциональная схема системы управления ГПС, приведенной на рис. 1.22:
ЭВМ1 и ЭВМ2 – вычислительные машины верхнего и среднего уровня; 1 – центральный монитор; 2 – монитор системы подготовки УП и обработки данных; 3 – монитор функционирования ГПС; 4, 5 – мониторы прямого управления технологическими процессами; 6 – контроллер автоматизированного склада; 7 – автоматизированный склад; 8 – контроллер конвейерной линии; 9 – конвейерная линия; загрузочно-разгрузочная станция; 10 – устройства ЧПУ ГПМ; 11 – наладочная станция; 12 – контроллер двух транспортных тележек для инструмента и трех для заготовок; 13 – транспортные тележки для инструмента; 14 – транспортные тележки для заготовок; 15 – терминал данных о загрузке-разгрузке заготовок; 16 – графический дисплей для установки заготовок; 17 – контроллер станции очистки и станции за- грузки-разгрузки паллет; 18 – станция очистки; 19 – станция загрузки-разгрузки паллет; 20 – контроллер конвейера для отвода стружки (21), бункера для сбора стружки (22) и пылеотсасывающей установки (23); 24 – контроллер инструментальной мастерской; 25 – склад инструментов; 26 – устройство смены инструмента; 27 – накопитель инструментальных кассет; 28 – накопитель инструмента; 29 – устройство считывания штрихового кода; 30 – устройство
настройки инструмента; 31 и 32 – графические дисплеи для оснастки и настройки инструмента.
На нижнем уровне, кроме УЧПУ для управления ГПМ, не используются кон-
троллеры (ПК) для управления вспомогательным оборудованием. Графические дис-
плеи на нижнем уровне и мониторное оборудование на уровне ЭВМ цеха обеспечи-
вают получение информации для работы оператора по контролю, подготовке инстру-
мента и установке заготовок. В каждой подсистеме предусмотрен активный контроль,
информация которого обрабатывается в ЭВМ и может быть получена оператором на любом уровне.
В ГПС имеется развитое автоматизированное инструментальное хозяйство.
Причем оперативное планирование учитывает вопрос обеспечения инструментом с введением системы переменных приоритетов. Сущность его сводится к следующему:
первоначально высший приоритет назначается инструментом, необходимым для вы-
полнения самого срочного задания. Однако по мере выполнения этого задания его приоритет снижается и одновременно повышается приоритет задания, обработка де-
талей которого еще не начата. В определенный момент приоритеты этих заданий уравниваются, а затем меняются местами. Переменный приоритет позволяет сокра-
тить число смен комплектов инструмента и разгрузить транспортную систему.
Система автоматизированного проектирования верхнего уровня обеспечивает операторов рабочими чертежами универсальных сборочных приспособлений для ус-
тановки заготовок и чертежами инструмента для настройки. Эти чертежи выводятся на графические дисплей, установленные на нижнем уровне в цехе. Мощная ЭВМ верхнего уровня обеспечивает также решение задач моделирования, которые вначале использовались при создании системы ГПС, а затем при планировании производства.
Система автоматического программирования в диалоговом режиме наряду с под-
готовкой УП для ГПМ осуществляет выбор оптимального числа инструментов в группе и магазине с учетом номенклатуры деталей.
ГПС второго поколения выполняются также менее мощными, нежели рассмот-
ренная. Однако характерным является совершенствование конструкции ГПМ с введе-
нием активного контроля и расширением диагностики, а также повышение гибкости транспортно-складской системы. При этом ГПС имеют самые различные конфигура-
ции. Пример такой малой ГПС приведен на рис.1.24. Тележка с роботом обеспечивает
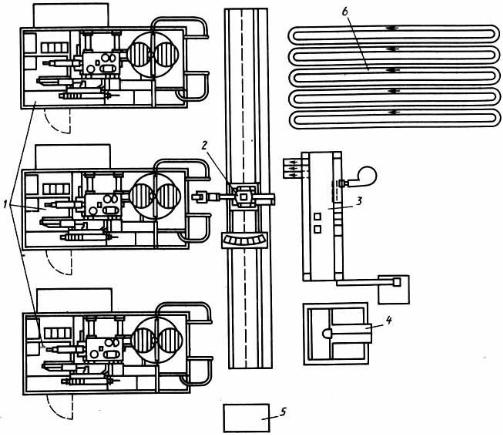
перемещение заготовок от накопителя по всем установкам ГПС и возврат готовых де-
талей. Система управления трехуровневая: ЭВМ-УЧПУ с промежуточным концен-
тратором. Компоновка системы рассчитана на безлюдную технологию.
Рис. 1.24. Компоновка малой ГПС для обработка корпусных деталей:
1 – горизонтальные фрезерно-сверлильно-расточные ГПМ; 2 – автоматизированная тележка с роботом; 3 – роботизированная многокоординатная измерительная машина; 4 – прецезионная измерительная машина; 5 – моечная машина; 6 – пятиконвейерный накопитель.
Дальнейшее развитие гибкости производственного процесса идет в направле-
нии включения в ГПС кроме металлообработки других технологических операций. В
частности, концепция гибкости может быть расширена для большой группы изделий,
заготавливаемых в виде полуфабриката с помощью одного из многочисленных мето-
дов пластической деформации, а затем окончательно обрабатываемых резанием.
Применение смешанной ГПС для изготовления штампов и обработка деталей после штамповки является очень важным и прогрессивным направлением. Данные на про-
ектирование штампов могут вводиться в общую базу данных и использоваться при разработке УП для механической обработки с учетом получаемых размеров заготов-
ки. Эти данные могут быть также использованы для проектирования приспособлений
и зажимных устройств, используемых при механической обработке. Отдельные пози-
ции ГПС связаны автоматизированными тележками, которые могут транспортировать штампы для ковочных прессов с ЧПУ, инструменты и заготовки для ГПМ.
Заготовки получают из предварительно проверенных стандартных прутков на отрезном станке с ЧПУ. В состав подготовительного участка входит система автома-
тизированной сортировки, производящая эту операцию по массе заготовки. После контроля заготовки загружаются на палету и доставляются автоматизированной те-
лежкой к автоматической индуктивной нагревательной печи. При холодной штампов-
ке этап нагрева исключается.
Работа толкателя печи, перемещающего заготовки, синхронизирована с работой пресса с помощью контроллера, установленного в модуле. Заготовки подаются из пе-
чи к позиции, расположенной в непосредственной близости от штампа, конвейером небольшой длины. Температура на этом этапе контролируется для того, чтобы была полная уверенность в ее соответствии с требуемой для проведения операции штам-
повки. Система контроля удаляет бракованные заготовки на отводящий конвейер, ко-
торый расположен рядом с подающей системой. Загрузка в штамповочный пресс вы-
полняется роботом, который рассчитан на заготовки всех типоразмеров, входящих в состав партии. Далее робот загружает обработанные заготовки на палету, подготов-
ленную для транспортирования с помощью автоматической тележки на позицию очи-
стки.
Заготовки, поступающие на позиции механической обработки, устанавдиваются на стандартных палетах, подготовленных для транспортирования на тележках к тре-
буемому участку механической обработки. Формующие и обрезные штампы склади-
руются в виде пуансонов, матриц и закодированы. Они установлены на соответст-
вующие транспортные палеты.
В составе ГПС предусмотрены накопители и промежуточные склады, так как время производственного цикла и производительность различных функциональных модулей системы не одинаковы. Не менее перспективно сочетание в ГПС механиче-
ской обработки и лазерной технологии (рис.1.26).
Структура потока движения деталей в ГПС (рис.1.27) является одним из показа-
телей, определяющих ее гибкость. Петлевая структура является наиболее распростра-
ненной. В этом классе транспортных средств наименьшее применение находит коль-
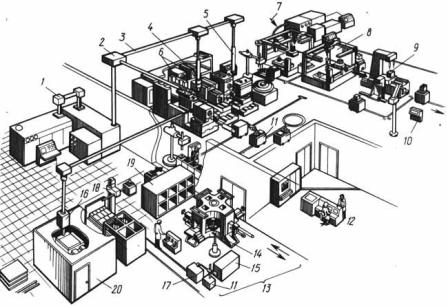
цевая структура (типы C, D) используют в системах с автоматизированными транс-
портными тележками. Поэтому применение этих структур имеет доминирующую тенденцию развития.
Рис. 1.26. ГПС с механической и лазерной обработкой для изготовления деталей типа тел вращения:
1 – лазер-генератор; 2 – распределитель потока лазера; 3 – световод для луча лазера; 4 – головка для сверления лучом лазера; 5 – головка для поверхностной обработки лучом лазера; 6
–участок обработки резанием; 7 – комплектующие детали; 8 – сборочные приспособления; 9
–измерительная машина с ЧПУ; 10 – накопитель готовых деталей; 11 – манипулятор; 12 – участок управления производством; 13 – участок термообработки; 14 – заготовительный участок; 15 – индукционная печь; 16 – головка для резки лучом лазера; 17 – склад заготовок; 18
–устройство для измерения направления луча лазера; 19 – промежуточный склад; 20 – уста-
новка для переработки отходов.
В транспортно-складских и инструментальных системах ГПС применяют раз-
личные методы кодирования, в том числе, как было указано выше, высокоинформа-
тивные штриховые коды с лазерными считывающими устройствами. Промышленный код 2 из 5 состоит из пяти штрихов в каждом разряде числа (табл.1.3), причем два из них могут быть широкими (рис.1.28). Широкий штрих соответствует логической еди-
нице, а узкий – нулю.
Таблица 1.3. Кодирование разрядов
Разряд |
|
Последовательное расположение штрихов |
|
||||
0 |
0 |
|
0 |
1 |
1 |
|
0 |
1 |
1 |
|
0 |
0 |
0 |
|
1 |
2 |
0 |
|
1 |
0 |
0 |
|
1 |
3 |
1 |
|
1 |
0 |
0 |
|
0 |
4 |
0 |
|
0 |
1 |
0 |
|
1 |
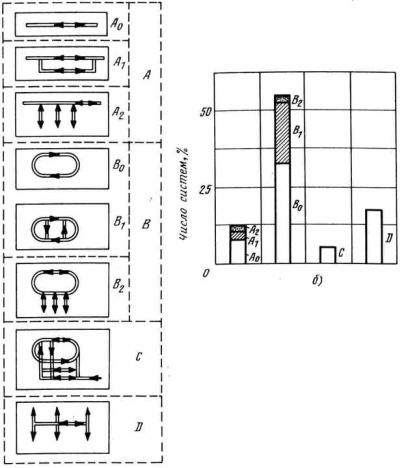
5 |
1 |
0 |
1 |
0 |
0 |
6 |
0 |
1 |
1 |
0 |
0 |
7 |
0 |
0 |
0 |
1 |
1 |
8 |
1 |
0 |
0 |
1 |
0 |
9 |
0 |
1 |
0 |
1 |
0 |
а)
Рис. 1.27. Структуры транспортных трасс ГПС (а) и соотношение типов структур в ГПС для обработки корпусных деталей (б):
А – линейная (А0 – одинарная; А1 – параллельная; А2 – с ответвлениями); В - петлевая (В0 – круговая; В1 – круговая с перемычками; В2 – с ответвлениями); С – сетевая; D - разветвленная
Закодированные числа отделяются друг от друга интервалами, а начало и конец
числа указываются тремя кодовыми штрихами. Штриховой код считается сканирую-
щим лазерным лучом (рис.1.29.). Вращающееся зеркало отклоняет луч, который про-
ходит интервал считывания кода с частотой 400-500 Гц. При этом различная степень
яркости штрихов и интервалов между ними фиксируется оптическим устройством и
передается в электронный блок. Последний генерирует серию импульсов различной
длительности в соответствии со штриховым кодом.

Наряду с рассмотренным кодом применяют различные модификации его, в том
числе с кодовым значением как штрихов, так и пробелов.
Рис. 1.28. Промышленный штриховой код |
Рис. 1.29. Оптическое устройство для |
2 из 5 (интервалы между числами равны |
считывания штриховых кодов |
10 интервалам между штрихами) |
А-В – интервал записи кода; 1 – световой |
|
луч; 2 – круглое зеркало; 3 – отражающее |
|
зеркало; 4 – вогнутое зеркало; 5 – плос- |
|
кость считывания |
2. Структурно-алгоритмическая организация систем управления
Структурно-алгоритмическое построение систем управления ПР и технологи-
ческим оборудованием определяется прежде всего задачами автоматизации конкрет-
ных видов производств, которые описываются технологической программой управ-
ления робототехническим комплексом оборудования с различными иерархическими уровнями. При этом организация технологической «среды» в отношении ее опреде-
ленности и (детерминированности) и сложности обусловливает использование на низшем уровне управления специализированных, так называемых жестких средств управления с аппаратной реализацией алгоритма, а на высшем – универсальных, в
том числе адаптивных средств со свободно программируемым алгоритмом управле-
ния.
Развитие микропроцессорной техники, унификация объектов управления, рас-
ширяющаяся сфера применении ПР и т.д. создали благоприятные предпосылки для реализации принципов блочно-модульного построении систем управления ПР, позво-
ляющих без особых затрат создавать разнообразные модификации систем для реше-
ния конкретных задач автоматизации.
Повышение информационно-вычислительных возможностей систем управле-
ния, особенно универсального типа и группового управления, приводит к использо-
ванию мультипроцессорных многоуровневых структур управления. Однако по-
прежнему актуально coздание простых автономных специализированных систем управления циклового и позиционного типов.
Ниже с учетом развития принципов структурно-алгоритмического построения систем управлении ПР будут рассмотрены некоторые обобщенные структуры систем управ-
ления и примеры реализации таких структур для основных классификационных групп в подклассах локального и группового управления, отражающих качественное разли-
чие иерархических уровней управления робототехническими комплексами.
2.1. Цикловые системы
Характерной особенностью цикловых систем управления является программи-
рование |
исключительно |
логической и технологической информации дискретно- |
го вида, |
определяющей |
последовательность движения звеньев манипулятора, дли- |
тельность позиционирования и т.д. Информация о величинах перемещений, как пра-
вило, задается при помощи регулируемых упоров или датчиков положения, подаю-
щих сигнал в систему управления о достижении исполнительным органом заданного перемещения. В настоящее время большинство цикловых систем управления ПР строится с использованием электронной элементной базы. Однако для ряда конкрет-
ных специальных применений ПР в условиях пожаро- и взрывоопасности, при высо-
ких или низких температурах, значительных уровнях электромагнитных полей или радиации, а также при воздействии достаточно сильных вибрационных и ударных на-
грузок предпочтительнее использование для построения систем управления, напри-
мер, элементов струйной техники.
Принцип действия струйных элементов основан на использовании различных аэродинамических эффектов, возникающих при взаимодействии струй друг с другом или со стенками элементов Проектирование дискретных пневматических систем про-
граммного управления не отличается существенно от построения аналогичных сис-
тем, выполненных на других логических элементах.
В качестве примера рассмотрим функциональную схему цикловой системы управления, построенную на элементах струйной техники и имеющую следующие основные устройства: задания и ввода программы, переработки информации с про-
граммоносителя, контроля отработки программы (входные устройства), а также вы-
ходные и исполнительные устройства.
В устройстве задания программы содержится информация о цикле, нанесенная на программоноситель. Программоноситель может быть выполнен в виде перфокарт,
перфолент, штекерной панели или наборного поля. Устройство поэтапного ввода про-
граммы, в котором осуществляется сдвиг тактовых импульсов, поступающих с блока формирования тактовых импульсов, может иметь различное конструктивное испол-
нение, вызванное применением:
-исключительно струйных логических элементов;
-струйно-механического или пневмомеханического обегающего устройства
(шаговый искатель);
-струйно-мембранного командозадающего устройства.
В зависимости от способа управления (по положению или по времени) такто-
вые импульсы могут формироваться с помощью путевых выключателей и других дат-
чиков, контролирующих выполнение предыдущей операции с помощью реле времени через определенные программируемые временные интервалы.
Из устройства поэтапного ввода программы тактовые импульсы поступают в блок задания программы и далее в соответствии с алгоритмом управления – в блок логики или непосредственно на исполнительные элементы. В устройстве переработки информации вырабатываются команды в соответствии с сигналами, поступающими
из блока задания программа и входных устройств.
Отечественный и зарубежный опыт разработки и эксплуатации систем на эле-
ментах струйной техники подтверждает эффективность их использования в различ-
ных производствах.
Рассмотренное выше устройство является одной из разновидностей специали-
зированных систем циклового управлении с ограниченными функциональным соста-
вом и возможностями управления.
Не останавливаясь более на других специализированных устройствах, постро-
енных, например, с использованием релейно-контакторной аппаратуры, много-
функциональных элементов памяти и т. д., рассмотрим обобщенный функциональный состав оборудования электронного устройства циклового программного управления с
«жестким» аппаратно-реализуемым алгоритмом. В состав такого устройства могут входить блок управления, программоноситель, блоки сопряжения с манипулято-
ром и технологическим оборудованием, панель управления, пульт ручного управле-
ния (обучения) манипулятором.
Блок управления строят обычно на основе микропрограммного управляющего автомата, работающего по жесткому циклу; он содержит дополнительно ряд операци-
онных узлов, обеспечивающих адресацию программоносителя, текущее фиксирова-
ние и дешифрацию управляющей информации, опрос состояния органов управления устройства и т.д.
В качение программоносителя могут быть использованы электромеханические информационные носители – штекерные и коммутационные поля, диодные перепро-
граммируемые матрицы, перфокарты и т. п.
В современных устройствах программоноситель выполняют на основе БИС по-
лупостоянных запоминающих устройств с электрической перезаписью информации,
что позволяет существенно увеличить объем памяти, надежность программоносителя и уменьшить его габаритные размеры.