
Учебники 80351
.pdfОкончание таблицы 3.2
Показатели |
ДРС 12×12 |
ДРС 16×16 |
ДРС 20×20 |
|
|
|
|
Индекс изделия |
СМД-94 |
– |
– |
Производительность, |
200 |
310 |
500 |
Размеры ротора, : |
|
|
|
диаметр |
1250 |
1600 |
2000 |
длина |
1250 |
1600 |
2000 |
Размер максимального куска за- |
375 |
480 |
600 |
гружаемого материала, |
|
|
|
Установочная мощность, кВт |
200 |
320 |
400 |
Масса дробилки, т |
18 |
30 |
50 |
|
|
|
|
П р и м е ч а н и е. Окружная скорость бил ротора 20; 24; 28,8 34,3; 41,5 и 50 с.
4. ВЫБОР КОНСТРУКТИВНЫХ ПАРАМЕТРОВ
На выбор оптимальных конструктивных параметров дробилки влияют многие факторы, которые еще не изучены настолько обстоятельно, чтобы можно было принимать достоверные решения поставленных задач. Однако, взаимосвязанность этих факторов при различных сочетаниях элементов конструкций позволяет получить ряд оптимальных решений конструкции дробилки в целом.
Ротор. Главными параметрами дробилки являются диаметр и длина ротора. У однороторных дробилок крупного дробления диаметр ротора определяется главным образом размером наибольших кусков загружаемого материала:
Dp = (1,5 ÷ 3) Dmax .
У двухроторных дробилок одноступенчатого дробления Dp =1, 2Dmax .
Дробилки среднего дробления имеютDp = (3 ÷10) Dmax ; мелкого дробления
-Dp ³10Dmax . Однако решающим фактором для выбора Dp y дробилок послед-
них двух типов является производительность.
31

Длина ротора Lp = (0,5 ÷1,5) Dp . Соотношение |
Lp |
в указанных пределах |
|
||
|
Dp |
не оказывает влияния на эффект дробления. При выборе оптимального соотношения руководствуются следующим:
- чтобы получить больший момент инерции ротора при меньшей его мас-
се, выгоднее у дробилок крупного дробления иметь Lp <1, y дробилок средне-
Dp
го и мелкого дробления Lp ³1; габаритные размеры дробилки по длине и вы-
Dp
соте могут быть уменьшены при заданной производительности, когда Lp >1;
Dp
- при создании ряда дробилок различной производительности. с целью унификации рекомендуется с одним диаметром делать несколько размеров Lp .
При этом в одном ряду дробилок получаются, например, такие соотношения
Lp : 0,5; 0,8; 1,00; 1,25;
Dp
- в любом случае Lp не должно быть Меньше 1,5Dmax
Условное число бил ротора z зависит от диаметра ротора и назначения дробилки по крупности дробления. При выборе условного числа бил удобно
пользоваться отношением mz = Dzp , которое по аналогии с зубчатыми колесами
можно назвать модулем ротора. Эта величина умноженная на π и равная дуге окружности ротора между рабочими поверхностями соседних бил, характеризует вероятность и глубину проникновения кусков в рабочую зону ротора, что, в свою очередь, влияет на эффект удара и степень дробления. По выбранному модулю определяют условное число бил:
D
Z = p .
m
z
Обычно у дробилок крупного дробления mz = 300 ÷ 500 мм; y дробилок среднего и мелкого дробления mz = 170 ÷ 300 мм. При выборе модуля ротора следует учитывать, что более крупные размеры загружаемых кусков требуют и больших значений mz , большие степени дробления - меньших значений mz .
При определении числа z необходимо помнить, что для упрощения операции балансировки роторов выгоднее иметь четное число бил, так как в этом случае достаточно попарно подобрать била равной массы. При z = 3 это выполнить труднее. Еще более осложняется балансировка ротора при z = 5 . Поэтому нечетное число бил более трех делается редко.
32

Далее приводятся методики, которые используются при выборе конструктивных параметров дробилок.
Число бил по длине ротора определяется технологическими соображениями, удобством крепления и обслуживания. Била длиннее 600 мм труднее отлить с точностью, обеспечивающей плотное прилегание к опорным поверхностям корпуса ротора. Они тяжелы и требуют специальных подъемных средств для замены. Поэтому при Lp > 600 мм устанавливают по два била. При этом
общее число бил становится равным 2z . Два била по длине ротора позволяют по мере износа менять их местами, обеспечивая более равномерный износ по длине ротора. Установка более двух бил по длине ротора осложняет их крепление, при этом средние била становятся менее доступными. Поэтому часто для крупных дробилок изготовляют более длинные била, чтобы не усложнять их крепление.
Высота била может сказываться на производительности при hб < 0,1Dp .
Так как по мере износа высота hб не уменьшается, то при hб < 0,1Dp произво-
дительность дробилки заметно падала бы с износом бил. Чтобы снизить влияние износа на производительность, делают 0,18Dp > hб > 0,1Dp . Увеличение
hб > 0,18Dp нежелательно по следующим причинам. Скорости удара по кускам,
|
|
|
2h |
|
, т. е. ниже 0,64ϑ |
|
|
|
проникающим на глубину |
. могут снижаться до 1 |
− |
б |
ϑ |
p |
|
, |
|
|
|
|||||||
б |
|
|
|
|
|
p |
|
|
|
|
|
Dp |
|
|
|
|
при этом увеличивается вероятность пропуска сверхмерных кусков. Однако имеются дробилки; у которых hб
Уменьшенная высота била может быть оправдана для дробилок мелкого дробления материалов невысокой абразивности, когда стремятся получить продукт дробления более равномерной крупности. Поэтому могут быть дробилки с
отношением hб Dp
Толщина била b0 (рис. 4.1) определяется из соображений минимального удельного износа и условиями прочности. Увеличение толщины била не повышает его срок службы, так как его внешняя поверхность истирается в раз быстрее рабочей независимо от ширины внешней поверхности. Вследствие этого било быстрее укорачивается по высоте до предельного размера, чем изнашивается по толщине. Если било опирается по всей длине опорной поверхности и изготовлено из вязкой стали аустенитного класса, например из стали марки 110Г13Л (ГОСТ 2176—67), его толщина может составлять(0, 4 − 0,6)hб .Била,
изготовленные из более хрупких сталей повышенной твердости, могут иметь большую толщину. Встречаются била, у которых b0 ³ hб .
Плоскость рабочей поверхности била чаще всего проходит через ось вращения ротора, что обеспечивает прямой удар. Более эффективный удар создает
33
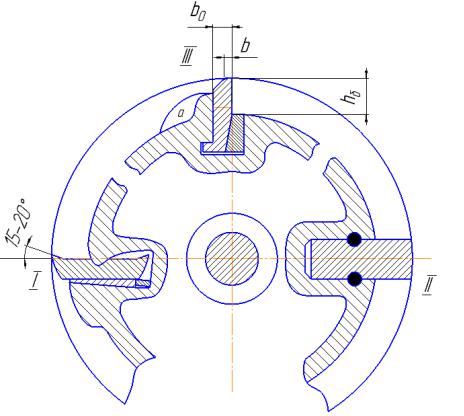
передняя кромка била, однако в результате интенсивного изнашивания она постепенно закругляется и эффект удара снижается. Чтобы компенсировать эту потерю эффективности, часть рабочей поверхности наклоняют по ходу вращения на 15 ÷ 20o (рис. 4.1, вариант I), что увеличивает концентрацию напряжений. возникающих в куске дробимого материала при ударе, при некотором закруглении кромки.
Форма внешней поверхности ротора влияет на вероятность проникновения куска в рабочую зону ротора‚ поэтому наиболее рациональной формой поперечного профиля ротора для глубины проникновения является круглый цилиндр с выступающими билами (рис. 4.1, вариант II).Такая форма применяется при слабых ударных нагрузках на било, т. е. при мелком дроблении. При дроблении крупных кусков, создающих сильные ударные нагрузки, последние требуют более надежного крепления со стороны опорной поверхности, поэтому у дробилок крупного и среднего дробления корпус ротора выполняют с подпорной стенкой. При этом внешняя поверхность описывается по спирали либо по окружности с выступами (рис. 4.1, вариант I). Чтобы выступ меньше снижал глубину проникновения, целесообразно делать его в виде отдельных ребер (рис. 4.1, вариант III)‚ тогда часть кусков сможет проникать в промежутки между рёбрами, что повысит среднюю глубину проникновения. На дробилках крупного дробления рёбра следует делать достаточно прочными, чтобы не ослабить опорные части корпуса ротора.
Рис. 4.1. Элементы бил и варианты их исполнения
34
Камера дробления. Закономерности движения частиц материала в камере дробления дают основания разработать основные положения проектирования камеры дробления.
Первая камера дробления образуется рабочими поверхностями приемного лотка первой отражательной плиты и окружностью вращения ротора. Положение приемного лотка принято характеризовать двумя параметрами: угловом ϕ л наклона и углом ϕ установки. Оба параметра влияют на показатели движения материала к ротору, условия его соударения и разлета частиц после удара.
Угол наклона лотка влияет на скорость скольжения материала по лотку. При угле наклона, меньшем угла трения, движение материала по лотку под действием сил тяжести невозможно. Поэтому обычно угол наклона лотка берут равным 45 ÷ 60o .
Угол установки приемного лотка принимают из условий максимального использования верхней полуокружности ротора для дробления материала и минимального выброса частиц обратно в приемное отверстие. Уменьшение угла установки позволяет увеличить рабочую часть окружности ротора. Однако при малых углах установки наблюдается выброс дробленого продукта навстречу исходному материалу. Графоаналитические исследования показывают, что при углах ϕ = 25 ÷ 35o выброс частиц в зону приемного отверстия навстречу исходному материалу практически близок к нулю. Угол ϕ установки в этом диапазоне является наименьшим, при котором обеспечивается движение потоков дробимого материала без взаимного пересечения. Встречаются углы ϕ = 0o . Но в этих конструкциях приходится применять специальные приемные коробки, зигзагообразные приемного отверстия B0 , что возможно лишь при загрузки мелкокускового материала.
Следующим элементом, управляющим потоком материала в камере дробления, является отражательная плита.
При выборе профиля отражательной поверхности первой отражательной плиты или решетки руководствуются следующим. Первая отражательная плита выполняет две основные функции: рабочего органа, при ударе о который разрушаются куски дробимого материала, отбрасываемые билами, вследствие чего используется часть кинетической энергии, приобретенной кусками, а также функцию направляющего устройства. Роль плиты как рабочего органа (если сравнить с работой бил) невелика, однако ею не следует пренебрегать. так как всякая возможность использования затраченной кинетической энергии кусков на их разрушение повышает эффективность дробилки.
Более важна вторая функция отражательного органа. Если большая доля потока направляется к приемному лотку или к ротору, то каждый кусок подвергается многократным ударам, при этом снижается вероятность малоэффективных ударов и повышается средняя степень дробления. Если же плита значительную часть потока отраженных кусков направляет на ротор ближе к выход-
35
ной щели, то повышается вероятность удаления нераздробленных кусков из рабочей камеры и снижается средняя степень дробления.
Размер выходной щели. Расчетным путем установлено, что за один удар кусок материала не дробится на частицы менее критического размера. Необходимо не менее трех центральных ударов, чтобы все частицы продукта дробления были бы не больше критического размера. С этой целью в роторной дробилке предусмотрены несколько камер, в которых продукт последовательно измельчается до заданных размеров. Крупность продукта дробления контролируется выходной щелью. Поэтому размер выходной щели устанавливается для дробилок мелкого и среднего дробления близким к заданному максимальному размеру dmax зерна.
Для дробилок типа СМД-75, СМД-94 рекомендуется определять размер выходной щели:
s = 2dmax − dкр ,
где dкр − критический размер дробления, м.
Размеры зазоров между колосниками колосниковых решеток. В дробил-
ках с колосниковыми решетками часть продукта удаляется из камеры дробления через зазоры между колосниками. Крупность этого продукта должна соответствовать крупности продукта дробления, разгружающегося через выходную щель, т. е. быть равной 0 − dmax .
Опыты показывают, что размеры кусков, прошедших через колосниковые решетки, достигают 1,5 ÷1,7 величины зазоров между колосниками. Очевидно, при настройки дробилки на режим работы обеспечивающий выход продукта крупностью до dmax , зазор должен быть
|
SK = |
dmax |
. |
|
|
1,5 ÷1,7 |
|
||
|
|
|
|
|
Поперечный размер приемного отверстия. Определяется |
B0 величиной |
|||
наибольших |
кусков загружаемого |
материала и назначается равным |
||
(1, 2 ÷1,7) Dmax |
для дробилок крупного дробления и (1,5 ÷ 3) Dmax |
для дробилок |
среднего и мелкого дробления. При загрузки кусков больших размеров, когда появляется опасность перегрузки, следует выбирать B0 возможно меньше, чтобы приемное отверстие ограничивало размеры принимаемых кусков. В ГОСТе 12375-70 принято B0 = 0,7Dp , что соответствует B0 = (1,4 ÷1,5) Dm ; у
дробилок среднего и мелкого дробления типа ДРС принято B0 = 0,5Dp или
B0 = 1, 7 Dmax
Число отражательных плит в дробилке повышает вероятность ударов бил по материалу и его степень дробления.
36
Параметры отражательной плиты определяются углом β установки и профилем отражательной поверхности. Далее будет отмечено, что угол β существенно влияет на показатели дробилки. С его увеличением повышается производительность, но снижается степень дробления, и наоборот. Кроме того, с увеличением угла установки увеличивается расстояние между приёмным лотком и отражательной плитой, что имеет существенное значение при дроблении крупнокускового материала. Поэтому угол установки отражательной плиты является важным параметром роторной дробилки. Обычно для дробилок среднего
имелкого дробления принимают β = 0 ÷15o , для дробилок крупного дробления
β= 15 ÷ 90o .При этом обращают внимание на то, что многокамерные дробилки
лучше контролируют сверхмерные куски дробимого материала и обеспечивают более равномерный продукт по зерновому составу. Поэтому угол установки первой отражательной плиты выбирают минимальным, чтобы обеспечить установку второй, третьей и других плит.
Профиль первой отражательной плиты строят так, чтобы она удовлетворяла ряду условий: наибольшей степени дробления и равномерности зернового состава; обеспечению наибольшей производительности камеры дробления.
Наибольшая степень дробления достигается при соударении частиц с отражательной плитой δи = 0 , так как при этом наиболее полно используется запас кинетической энергии частиц. При этом среднее значение угла отражения также равно нулю и, следовательно, направлено навстречу движению основного потока материала. Это приводит к соударению частиц и снижению эффективности их дробления. Поэтому в практике конструирования отражательных
плит угол соударения принимают δи = (10 ÷15)o . Для этих условий обеспечива-
ется наибольшее использование кинетической энергии на дробление и устанавливается направленное движение отраженных частиц. Для первой отражательной плиты угол δи принимают положительным, т. е., таким, при котором отражение частиц было, в сторону приемного лотка. Это позволяет направить большинство частиц на приемный лоток, а оттуда на повторное дробление ротором и обеспечивает более равномерный зерновой состав, Для второй, третьей и .т. д. плит угол δи принимают отрицательным с целью получения направленного движения частиц к разгрузке.
Соответствующий этим условиям профиль отражательной плиты определяется уравнением логарифмической спирали
ρ = ρ0e ± ϕ ptgδu ,
где , ϕ p − текущие координаты;
начальное значение, соответствующее нижней точки отражательной поверхности плиты;основание натурального логарифма.
37

Исходя из условий наилучшего использования дробящего пространства и упрощения конструкции для роторных дробилок с отдельными отражательными плитами, рекомендован шаг их установки .
5. РАСЧЁТ УДАРНЫХ НАГРУЗОК
Механическое разрушение каменных материалов представляет собой сложный процесс различных явлений, протекающих практически одновременно. Образованию и развитию трещин в телах при механическом воздействии сопутствуют тепловые, химические, электрические явления и структурные преобразования материала. При этом общая энергия, расходуемая на дробление, превышает примерно в 1000 раз поверхностную энергию вновь образованных поверхностей материала.
Современные гипотезы не в состоянии оценить многообразие явлений, происходящих при дроблении, хотя и дают удовлетворительные результаты для некоторых условий разрушения. Необходимо знать физическую сущность процессов, протекающих при разрушении, чтобы обоснованно применять известные закономерности и уметь оценить точность используемых уравнений. При любом виде деформации процесс разрушения можно представить в следующем виде. Внешние силы вызывают накопление внутренней энергии упругих деформаций. Внешние силы вызывают накопление внутренней энергии упругих деформаций. Напряжения в куске возрастают, пока в каком-то месте вследствие концентрации напряжений, вызванных местными дефектами, они не превысят предела прочности. Начинается развитие трещины, сопровождающееся перераспределением энергии упругих деформация, часть которой превращается в энергию вновь образованных поверхностей. Эта часть энергии и является полезной энергией дробления. Остальная энергия уходит главным образом на упругие деформации сжатия и рассеивается в виде тепла и других видов энергии.
Дробилки как статического действия (щековые, конусные, валковые), так и ударного действия (роторные, молотковые, центробежно-ударные) вызывают в дробимом материале все виды деформаций, среди которых преобладает сжатие. Дробилки первой группы отличаются от дробилок второй группы меньшими скоростями нарастания напряжений, обусловленными соответствующими скоростями приложения нагрузок. Однако строгой границы между дробилками по этому признаку установить нельзя. Сами же процессы разрушения в дробилках той и другой группы, как утверждает H. Mö lling, принципиально не отличаются. Различие следует искать в способе передачи энергии или в механизме воздействия рабочего органа на дробимый материал. Таких механизмов можно назвать три:
1) кусок подвергается нагружению между двумя твердыми сближающимися поверхностями рабочих органов. Усилие, создаваемое одной из поверхностей, уравновешивается реакцией, возникающей на другой поверхности;
38
2)кусок подвергается воздействию со стороны только одной поверхности рабочего органа. Возникающее при этом усилие уравновешивается силами инерции массы самого куска. Инерционная сила, равная произведению массы куска на его ускорение, должна быть достаточной для создания разрушающих напряжений;
3)кусок разрушается без соприкосновения с рабочими поверхностями под действием напряжений растяжения, возникающих от центробежных сил при вращении куска вокруг своего центра тяжести.
Дробилкам первой группы присущ первый механизм воздействия, дробилкам второй группы – все механизмы воздействия, но преобладает второй и в меньшей степени третий механизм воздействия. В роторных дробилках второй механизм воздействия в дальнейшем будем называть односторонним ударом, а первый – двусторонним. Оба механизма воздействия могут возникать одновременно.
В настоящее время процесс дробления в роторных дробилках ударного действия рассматривают как с позиций классической механики, так и волновой. Классическая механика предполагает положение сил удара к центру инерции тел, а сами тела при упругом ударе – абсолютно твердыми.
На основе закона количества движения и импульсов сил выведены формулы, описывающие удар двух абсолютно упругих или неупругих тел с масса-
ми m1 и m2 и скоростями до удараυ0 |
и υ0' соответственно. |
||||||||||||||||||||
При абсолютно упругих телах скорость движения тела 1 после удара |
|||||||||||||||||||||
|
υ1 = υ2 |
− 2 |
m2 (υ0 − υ0' ) |
. |
|
|
|||||||||||||||
|
|
m1 |
+ m2 |
|
|
||||||||||||||||
|
|
|
|
|
|
|
|
|
|
|
|
|
|
|
|
||||||
При υ' = 0 |
|
|
|
|
|
|
|
|
|
|
|
|
|
|
|
|
|
|
|
|
|
0 |
|
|
|
|
|
|
(m1 − m2 )υ0 |
|
|
|
|
|
|
||||||||
|
|
|
|
υ = |
. |
|
|
|
|
|
|||||||||||
|
|
|
|
|
|
|
|
|
|
|
|
|
|
|
|||||||
|
|
|
|
1 |
|
|
|
m1 + m2 |
|
|
|
|
|
||||||||
|
|
|
|
|
|
|
|
|
|
|
|
|
|||||||||
Скорость движения тела 2 после удара |
|
|
|
|
|
||||||||||||||||
|
υ |
|
|
= υ' |
+ |
2 |
m1 (υ0 −υ0' ) |
|
. |
|
|
||||||||||
|
2 |
m1 + m2 |
|
|
|
||||||||||||||||
|
|
0 |
|
|
|
|
|
|
|
|
|
||||||||||
|
|
|
|
|
|
|
|
|
|
|
|
|
|
|
|
||||||
При υ0' = 0 |
|
|
|
|
|
|
|
|
|
2m1υ0 |
|
|
|
|
|
|
|
|
|||
|
|
|
|
υ |
2 |
= |
|
|
. |
|
|
|
|
|
|||||||
|
|
|
|
|
|
|
|
|
|
|
|
|
|||||||||
|
|
|
|
|
|
|
m1 + m2 |
|
|
|
|
|
|||||||||
|
|
|
|
|
|
|
|
|
|
|
|
|
|
||||||||
Кинетическая энергия до удара и после удара остается постоянной: |
|||||||||||||||||||||
Э + Э' = |
m1υ02 |
|
+ |
m2υ0'2 |
= |
m1υ12 |
+ |
m2υ22 |
. |
||||||||||||
|
|
|
|
||||||||||||||||||
0 |
0 |
|
|
2 |
|
|
|
2 |
|
2 |
2 |
|
|||||||||
|
|
|
|
|
|
|
|
|
|||||||||||||
|
|
|
|
|
|
|
|
39 |
|
|
|
|
|
|
|
|
|
|
Энергия, отдаваемая телом с массой m1 телу с массой m2 приυ0' = 0
|
m2υ 2 |
||
1 |
0 |
|
|
Э1 = 2m2 |
|
. |
|
(m + m )2 |
|||
1 |
2 |
|
При неупругих телах скорости движения тела 1 и тела 2 после удара одинаковы и равны:
υ = υ |
|
= |
m υ |
+ m υ' |
||
|
1 0 |
2 |
0 |
. |
||
2 |
|
+ m2 |
|
|||
1 |
|
m1 |
|
|
||
|
|
|
|
|
При υ ' |
= 0 |
|
|
|
|
|
|
|
|
|
|
|
0 |
|
|
|
|
|
m1υ0 |
|
|
|
|
||
|
υ1 |
= υ2 = |
|
. |
|
|
||||||
|
m1 |
|
|
|
|
|
||||||
|
|
|
|
|
|
+ m2 |
|
|||||
Кинетическая энергия тел 1 и 2 до удара |
|
|
|
|
||||||||
|
Э + Э' |
= |
m1υ02 |
+ |
m2υ0'2 |
. |
|
|||||
|
|
|
|
|||||||||
|
0 |
0 |
|
2 |
|
|
2 |
|
|
|||
|
|
|
|
|
|
|
|
|||||
Кинетическая энергия тел 1 и 2 после удара |
|
|||||||||||
|
Э + Э = |
(m1υ0 |
+ m2υ0' )2 |
. |
||||||||
|
2 |
(m1 + m2 ) |
||||||||||
|
1 |
2 |
|
|
||||||||
|
|
|
|
|
|
|
|
|
|
|
Разность этих кинетических энергий представляет собой потерю энергии, расходуемую на деформацию тел:
|
Эр = (Э0 + Э0' ) − Э1 |
+ Э2 |
= |
|
m1m2 (υ0 −υ0' |
)2 |
. |
||||||
|
|
|
2 |
(m1 |
+ m2 ) |
|
|||||||
|
|
|
|
|
|
|
|
|
|
||||
При υ ' |
= 0 |
|
|
|
|
|
|
|
|
|
|
|
|
0 |
|
|
|
m m υ 2 |
|
|
|
|
|
|
|||
|
Э = |
|
|
. |
|
|
|
|
|||||
|
|
1 |
2 |
0 |
|
|
|
|
|
||||
|
|
р |
2 |
(m1 + m2 ) |
|
|
|
|
|
||||
|
|
|
|
|
|
|
|
|
|
|
|
|
Рассмотренные положения теории удара на основе волновой механики действительны для случаев, когда длина соударяющихся тел намного больше поперечных размеров, соприкасающиеся торцы абсолютно плоски, а касание при ударе происходит одновременно по всей плоскости.
Ни одна из приведенных теорий не рассматривает разрушение тел и не дает методов расчета объемов разрушений. Использование теорий удара в прикладных расчетах становится возможным при пополнении общих аналитических закономерностей экспериментальными.
При υ0' = 0
40