
2858.Оборудование литейных цехов учебное пособие
..pdfбольшее сопротивление при перемещении ее в опоке. В результате давление воздуха в опоке возрастает, что вызывает резкое изменение перепада давлений и кинетической энергии воздуш- но-песчаной струи и, как следствие, неравномерность уплотнения формы. Поэтому при изготовлении форм пескодувный процесс целесообразно сочетать с интенсивным прессованием. В этом случае смесь можно вдувать в опоку при сравнительно низком давлении воздуха, добиваясь лишь заполнения и незначительного уплотнения формы (δ = 1,5 г/см3), а доуплотнение осуществлять прессованием при повышенном давлении – 1,0– 1,5 МПа (10–15 кгс/см2).
При уплотнении форм на пескодувных машинах живое сечение всех вент должно составлять 0,8–1,0 сечения вдувных отверстий, диаметр вдувных отверстий 20–30 мм.
В последние годы широкое распространение получил безопочный способ изготовления форм на автоматах, в которых уплотнение смеси производится пескодувно-прессовым методом. К машинам этого типа можно отнести формовочные автоматы фирм «Волворк» (Англия) и «Дисаматик» (Дания).
На рис. 9.1, а приведена схема работы пескодувно-прес- сового автомата «Волворк». Безопочные формы, подготавливаемые на этой машине, собираются в виде двух непрерывных горизонтальных стопок 4 и 6. Каждая форма в стопке используется с обеих сторон для отпечатков моделей. На позиции уплотнения 3 имеются пескодувный механизм и два гидроцилиндра 5 для последующего (после надува) прессования форм. Одновременно уплотняются две формы, располагаемые в одной рамке 7, которая при помощи цилиндра 2 совершает челночные движения, останавливаясь то справа, то слева от позиции уплотнения для выталкивания готовых форм. Выталкивание и перемещение форм до встречи со своими стопками, а также дальнейшее продвижение стопок на один шаг (толщину одной формы) осуществляется с помощью цилиндров 7, 8.
181

а
б
Рис. 9.1. Автоматическая линия фирмы «Волворк»
На рис. 9.1, б показан общий вид автоматической линии для безопочного изготовления форм размером 450×350×100 мм, производительностью 750–800 форм/ч. На линии производится заливка форм, охлаждение их и выбивка в барабанах, где осуществляется разделение кома на два потока – отливок и оборотной смеси.
182
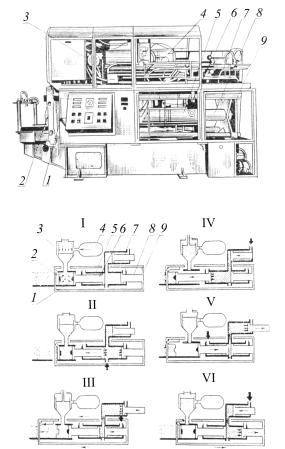
На рис. 9.2, а изображен общий вид автомата «Дисаматик», который состоит из формовочной камеры I (см. также рис. 9.2, б, положение I), поворотной модельной плиты 2, пескодувного резервуара 3, ресивера 4 прессового цилиндра 5 с поршнем 6, аккумулятора 7, заднего плунжера 8 и неподвижной рамы 9.
а
б
Рис. 9.2. Изготовление безопочных форм на автомате «Дисаматик»: а – общий вид машины; б – последовательность операций
183
Весь цикл изготовления форм состоит из шести операций: I – вдув смеси в формовочную камеру;
II– прессование формы. Поворотная модельная плита находится в исходном положении и закрывает формовочную камеру спереди. Затем модельная плита, смонтированная на прессовом поршне, внедряется вобъем камеры, уплотняя внейсмесь;
III– отделение передней (поворотной) модельной плиты. Модельная плита вибрирует и отодвигается от формы, после чего происходит ее поворот в верхнее горизонтальное положение. Формовочная камера спереди открывается для пропуска готовой полуформы. При этом масло подается в правую полость гидроцилиндра, а из центральной части уходит в аккумулятор.
Вэто же время открывается шибер пескодувного резервуара, и происходит наполнение последнего формовочной смесью;
IV – выталкивание изготовленной полуформы из формовочной камеры. Задняя модельная плита при движении вперед (влево) медленно перемещает полуформу до соприкосновения ее с ранее изготовленной, а затем ускоренным движением продвигает весь ряд изготовленных форм на один шаг, равный толщине формы. Такое движение происходит за счет подачи масла в правую полость цилиндра аккумулятора;
V– отделение задней модельной плиты. При подаче масла в левую полость прессующего гидроцилиндра поршень, перемещаясь вправо, направляет масло из центральной части механизма в левую полость цилиндра аккумулятора, отодвигая его поршень назад, в крайнее правое положение;
VI – закрытие формовочной камеры. Обе модельные плиты поочередно устанавливаются в исходное положение. Это достигается при подаче масла вправую полость цилиндрааккумулятора.
Машины этого типа выпускают для безопочных стопочных форм с размерами 500 и 600 мм по ширине и от 400 до 775 мм по высоте при толщине блоков от 125 до 400 мм с металлоемкостью формы до 750 кг, они имеют цикловую часовую производительность от 240 до 300 блоков (форм) в час. Формы могут
184

иметь стержни, которые устанавливаются на вертикальных разъемах блоков с помощью особого стержнеукладчика, принцип работы которого показан на рис. 9.3. На схемах рис. 9.3, а и б представлен вид на машину со стороны стопки блоков. Стержнеукладчик имеет вертикальную плиту, в гнезда которой оператор вставляет стержни, удерживающиеся на ней присосом (вакуумом) в их знаках (рис. 9.3, а). Затем эта плита со стержнями поворачивается и вводится в зону стопки блоков (рис. 9.3, б), передвигается в горизонтальном направлении и вкладывает имеющиеся на ней стержни в очередную (крайнюю) форму, или блок (рис. 9.3, в). В этот момент вакуум, удерживающий стержни в гнездах плиты стержнеукладчика, снимается, и стержни остаются в блоке в своих знаках, в которых они удерживаются за счет соответствующих допусков их размеров (с некоторым натягом). Стержнеукладчик отходит обратно от стопки блоков (рис. 9.3, г), и далее плита его поворачивается в исходное положение (рис. 9.3, д).
а |
б |
в |
г |
д |
Рис. 9.3. Принцип работы стержнеукладчика: 1 – машина; 2 – плита стержнеукладчика; 3 – стопка блоков; 4 – стержни
На рис. 9.4 приведена схема автоматизированной линии безопочной формовки мод. AЛ2002. Линия предназначена для крупносерийного и массового производства стержневых и бесстержневых отливок средней сложности из черных и цветных сплавов.
185
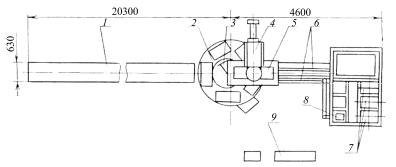
Рис. 9.4. Схема автоматизированной линии безопочной формовки мод. АЛ2002: 1 – шагающий конвейер; 2 – поворотный стол; 3 – механизм выталкивания бракованных форм; 4 – пескодувный узел; 5 – механизм прессования; 6 – разводка трубопроводов; 7 – позиция размещения гидроагрегатов; 8 – гидроагрегат и шкаф
управления; 9 – электрооборудование
Формовочный блок линии включает пескодувный резервуар, механизм двустороннего горизонтального прессования, поворотный шестипозиционный стол с формовочными камерами, механизмы сборки форм в горизонтальную стопку и удаление бракованных форм.
10.ИМПУЛЬСНЫЕ МЕТОДЫ ФОРМОВКИ
Впоследнее десятилетие широкое распространение получили импульсные формовочные машины. По сравнению с широко известным встряхивающе-прессовым методом импульсное уплотнение обеспечивает получение чрезвычайно сложных форм, в том числе с глубокими карманами в оснастке, минимальными расстояниями между моделями, а также между моделями и стенками опоки. Это позволяет не только улучшить геометрическую точность отливок, но и существенно снизить припуски на механическую обработку.
186
Влитейных цехах, использующих импульсную формовку, экономия металла достигает 3–12 %, а трудоемкость очистных
изачистных работ сокращается до 20 % по сравнению с методом уплотнения встряхиванием с допрессовкой. Импульсный метод обеспечивает высокую производительность формовочных машин, экономичен, вызывает меньший износ оснастки; импульсные формовочные машины не требуют массивных фундаментов, просты в эксплуатации вследствие отсутствия подвижных механизмов. Преимущества этого процесса проявляются не только в производстве отливок высокого качества, надежности, универсальности, но также и в вопросах улучшения условий труда формовщика вследствие снижения шума и вибрации.
Кимпульсным способам уплотнения относятся: воздушноимпульсные, газоимпульсные (газовзрывные), электроимпульсные, магнитно-импульсные способы и скоростное (ударное) прессование. В газоимпульсных и воздушно-импульсных установках на формовочную смесь воздействуют сжатый воздух или продукты сгорания горючих газов (метан, пропан и др.) в среде атмосферного воздуха. В электроимпульсных установках (пока промышленного применения не имеют) между двумя электродами, находящимися в рабочей камере, подаются мелкодисперсные частицы воды. В результате взаимодействия электрополя с водой образуется взрыв, и давление газа повышается до 0,8–1,0 МПа, которое и воздействует непосредственно на смесь.
При скоростном прессовании происходит единичный удар прессовой колодки по смеси, находящейся в опоке. В результате удара слои смеси и колодка под действием сил инерции движутся с большой скоростью в направлении модельной плиты, что
иприводит к более равномерному уплотнению, чем при статическом прессовании.
Внастоящее время в промышленности применяются в основном воздушно-импульсные (ВИФ) и реже газоимпульсные формовочные установки (ГИФ). Воздушно-импульсные (ВИФ) подразделяются на два типа: ВИФ высокого давления (5–8 МПа)
иВИФ низкого давления (0,5–0,6 МПа).
187
Воздушно-импульсные формовочные установки высокого давления широкого распространенияне получили по ряду причин:
–эти установки требуют специального компрессора высокого давления;
–уровень шума выше допустимых норм;
–наличие вент в модельной оснастке.
Вданной главе будут рассмотрены в основном импульсные формовочные установки и процессы низкого воздушного давления, которые лишены этих недостатков.
10.1. Принцип импульсного уплотнения и характер распределения плотности по объему формы
Принцип воздушно-импульсного процесса уплотнения литейных форм (рис. 10.1) заключается в том, что при открытии клапана 2 поток сжатого воздуха из ресивера 1 через отверстие 3, подклапанную полость 4 мгновенно воздействует на смесь 5, находящуюся в наполнительной рамке 6 и опоке 7, разгоняет ее по направлению к модели 8 и модельной плите 9, где она резко тормозится и под действием сил инерции уплотняется. Отработанный сжатый воздух через специальный клапан сброса давления или через венты в модельной оснастке, а частично через неплотности соединений оснастки и машины уходит в атмосферу. За время импульса (tи = 0,01…0,02 с) смесь уплотняется до технологически необходимой плотности (δ = 1,45…1,65 г/см3) и твердости (Т = 80…90 ед.).
На рис. 10.1 показана схема воздушно-импульсной установки низкого давления ВИФ/НД. Ресивер 1 имеет значительно больший объем по отношению к объему уплотняемой смеси (в 3–4 раза), а давление воздуха в ресивере составляет 0,5–0,6 МПа. Воздушно-импульсная установка высокого давления ВИФ/ВД по самой сути не отличается от установок низкого давления. Но объем ресивера у последних меньше или равен объему уплотняемой смеси, а давление, как уже отмечалось выше, составляет 5–6 МПа.
188
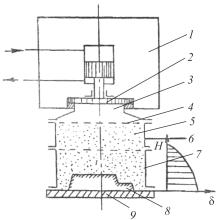
Рис. 10.1. Схема воздушно-импульсного процесса
За счет быстродействия привода клапана длительность импульса в установках ВИФ/НД tи = 0,01…0,02 с, а в установках ВИФ ВД tи = 0,1…0,2 с. Поскольку в установках ВД давление очень высокое, при открытии клапана в смеси от воздействия потока воздуха образуется кратер. С целью избежать этого над смесью устанавливают рассекатель (плита с множеством перфорированных отверстий).
Эпюра распределения плотности по высоте опоки показана на рис. 10.1: внизу по ладу – максимальная плотность, верхний слой – неуплотненный; обычно этот слой ( = 20…50 мм) либо срезают, либо допрессовывают.
Распределение плотности по объему формы также неравномерное: в карманах оснастки плотность ниже, чем в надмодельной области. Однако эта неравномерность существенно ниже при импульсном уплотнении, чем при других способах формовки.
Как средняя плотность, так и неравномерность плотности по объему формы зависит от величины градиента давления dp/dt, воздействующего на смесь.
189
Параметр dp/dt в импульсных машинах является определяющим, так как чем больше dp/dt, тем выше скорость и ускорение движения смеси, тем выше сила инерции и плотность смеси.
Длительность импульса tи в различных импульсных установках сокращают по-разному. Первый путь – повышение быстродействия привода клапана, второй – увеличение суммарной площади выпускных отверстий. Возможно применение этих двух способов вместе. Чем больше площадь сечения выпускных отверстий и меньше время срабатывания привода клапана, тем tи меньше и эффективность процесса уплотнения выше.
Таким образом, параметр dp/dt зависит от конструктивных параметров машины и давления воздуха в ресивере.
Сила инерции смеси – основной фактор уплотняющего воздействия. Она прямо пропорциональна величине градиента давления dp/dt. Градиент давления является суммарным конструк- тивно-технологическим фактором, поскольку на его величину влияют несколько других конструктивно-технологических факторов, а именно: объем ресивера, давление сжатого воздуха в ресивере, объем подклапанной полости (полость, находящаяся между смесью и днищем ресивера), площадь выпускного отверстия клапана и время открытия клапана.
В импульсных установках (особенно в низкоимпульсных) благодаря мощной воздушной волне в начальный момент рабочего процесса происходит разрушение когезионных связей между частицами смеси, образующими объемную вязкость. Смесь на некоторое мгновение переходит в псевдоожиженное состояние. В этот момент в смеси, подобно жидкости, повышается боковое давление (коэффициент бокового давления β = 0,5…0,6), и она хорошо заполняет узкие карманы оснастки.
Сопротивление уплотнению смеси оказывает лишь кулоново трение. По окончании процесса активного трения когезионные связи частиц смеси снова восстанавливаются, причем гораздо интенсивнее, чем до уплотнения, за счет более плотной укладки частиц в объеме. Перемещающиеся частицы смеси ис-
190