
книги / Оптимизация технологических процессов механической обработки
..pdf
Для определения операционных припусков применяют три метода: дифференциально-аналитический, интегрально-анали- тический и табличный [9].
Дифференциально-аналитический метод является наиболее точным и базируется на анализе производственных погрешностей, которые дифференциально учитывают влияние на величину припуска конфигурации и размеров детали, качества заготовки, погрешностей, возникающих при механической и термической обработках [10]. Общий вид формулы для определения минимального припуска на обработку на i-й операции можно представить в виде
Z min i = К(RZ (i−1) +Ti−1 + ρi−1 + εi ),
где RZ (i−1) – высота шероховатости на предшествующей опера-
ции; Тi–1 – глубина дефектного слоя на предшествующей опера-
ции; ρi−1 – векторная сумма пространственных отклонений взаимообязанных поверхностей, получившихся на предшест-
вующей операции; εi – векторная сумма погрешностей базирования и закрепления на выполняемой операции; К – коэффициент, учитывающий характер припуска (для односторонних припусков К = 1, для симметричных К = 2).
Автоматизация расчета припусков по этому методу затруднена из-за необходимости использования большого объема спра- вочно-нормативной информации для определения погрешности базирования, закрепления, пространственных отклонений.
51
Наиболее удобным с точки зрения формализации является интегрально-аналитический метод определения припусков, которые рассчитываются по эмпирическим выражениям следующего вида:
Zmin i = a + bDm + cLn ,
где а – часть припуска, которую необходимо снять, чтобы уда-
лить дефектный слой Ti −1 и микронеровности RZ (i−1) ;
(bD m + cLn ) – часть припуска, которая компенсирует неровно-
сти, обусловленные пространственными отклонениями отдельных участков обрабатываемой поверхности и обусловлена габаритными размерами D и L заготовки.
Коэффициенты a, b, c и показатели степени m и n определяются путем анализа и обработки табличных значений операционных припусков с использованием метода наименьших квадратов. Такой подход позволил установить эмпирические зависимости Zmin = f (D, L) при определении минимальных операционных припусков для различных поверхностей и операций обработки (табл. 2.7–2.9) [8].
Определение операционных размеров выполняется по методике, изложенной в работе [5]. Для наружных поверхностей вращения
Dmin i−1 = Dmin i + Zmin i ;
Dmax i−1 = Dmin i−1 + δi−1 ;
Z max i = Dmax i−1 − Dmax i ,
52
гдеDmin i , Dmax i – соответственно минимальный и максималь-
ный диаметры обрабатываемой поверхности на i-й операции обработки; Dmin i−1 , Dmax i−1 – соответственно минимальный и максимальный диаметры обрабатываемой поверхности на i–1-й операции обработки; Z max i – максимальный припуск на выпол-
нение i-й операции; δ i−1 – допуск на выполнение i–1-й техноло-
гической операции.
Для внутренних поверхностей вращения
Dmin i−1 = Dmax i−1 − δi−1 ; Dmax i−1 = Dmax i − Z min i ;
Z max i = Dmin i − Dmin i−1.
Расчет величин допуска δi для операционных размеров при выполнении различных операций производится по известным зависимостям [7].
Таблица 2.7
Эмпирические формулы для расчета минимальных операционных припусков
при обработке наружных поверхностей вращения
Стадии |
Наименование |
Вид зависимости Zmin = f (D, L), мм |
||||
обработки |
операции |
|
|
|
|
|
1 |
Черновая |
Горячая штамповка |
|
|
||
|
токарная |
Zmin |
= 0,2 + 0,684D |
0,168 |
+ |
0,7 |
|
|
|
0,0235L |
|||
|
|
Прокат обычной точности |
||||
|
|
Zmin |
= 0,155 + 0,527D0,168 + 0,0181L0,7 |
|||
|
|
Прокат повышенной точности |
||||
|
|
Zmin |
= 0,124 + 0,383D0,168 |
+ 0,0132L0,7 |
||
|
|
53 |
|
|
|
|
|
|
Окончание табл. 2.7 |
|
|
|
Стадии |
Наименование |
Вид зависимости Zmin = f (D, L), мм |
обработки |
операции |
|
|
|
Литье в песчаные формы |
|
|
Zmin = 2,03D0,2 – 2,51 |
|
|
Литье в кокиль |
|
|
Zmin = 1,9D0,1 – 1,42 |
|
|
Литье в оболочковые формы |
|
|
Zmin = 1,72D0,1 – 1,28 |
|
|
|
2 |
Получистовая |
Zmin = 1,01D0,1 +0,0007L – 0,821 |
|
токарная |
|
3 |
Чистовая |
Zmin = 0,16 + 0,013D0,5 + 0,00074L |
|
токарная |
Zmin = –0,0127 + 0,0713D0,15 + 0,00021L |
|
Черновая |
|
|
|
|
|
шлифовальная |
|
|
|
|
4 |
Тонкая токарная |
Zmin = 0,133 + 0,00435D0,5 + 0,000248L |
|
Однократное |
Zmin = –0,019 + 0,107D0,15 + 0,00032L |
|
шлифование |
|
|
|
|
|
|
|
5 |
Чистовая шли- |
Zmin = –0,0064 + 0,0356D0,15 + 0,00011L |
|
фовальная |
|
6 |
Тонкая |
Zmin = – 0,0011 + 0,021D0,15 + 0,000043L |
|
шлифовальная |
Zmin = 0 |
|
Полировальная |
|
|
Накатная |
Zmin = 0 |
|
Суперфинишная |
Zmin = 0 |
|
|
|
|
|
54 |
Таблица 2.8
Эмпирические формулы для расчета минимальных операционных припусков
при обработке внутренних поверхностей вращения
Стадии |
Наименование |
|
Вид зависимости |
обра- |
|
||
операции |
|
Z min = f (D, L), мм |
|
ботки |
|
|
|
1 |
Черновое растачивание |
|
Горячая штамповка |
|
|
|
Zmin = 0,2 + 0,5D0,16 + 0,022L0,7 |
|
Рассверливание |
|
Литье в песчаные формы |
|
|
|
Zmin = 2,03L0,2 – 2,51 |
|
Черновое зенкерование |
|
Литье в кокиль |
|
|
|
Zmin = 1,9L0,1 – 1,42 |
|
|
|
Литье в оболочковые формы |
|
|
|
Zmin = 1,72L0,1 – 1,28 |
|
|
|
|
2 |
Получистовое |
|
Zmin = 1,52D0,1 – 1,33 |
|
растачивание |
|
|
|
Чистовое зенкерование |
|
Zmin = 0,191D0,32 |
3 |
Чистовое растачивание |
|
Zmin = 0,22 + 0,052D0,5 |
|
Черновое шлифование |
|
Zmin = 0,044D0,3 |
|
Черновоеразвертывание |
|
Zmin = 0,044D0,3 |
4 |
Тонкое растачивание |
|
Zmin = 0,022D0,3 |
|
Чистое шлифование |
|
Zmin = 0,022D0,3 |
|
Тонкое развертывание |
|
Zmin = 0,022D0,3 |
|
Чистое протягивание |
|
Zmin = 0,001D1,25 + 0,327 |
5 |
Тонкое шлифование |
|
Zmin = 0,01D0,3 |
|
Тонкое развертывание |
|
Zmin = 0,01D0,3 |
|
Хонингование |
|
Zmin = 0 |
|
Притирка |
|
Zmin = 0 |
|
Калибрование шариком |
|
Zmin = 0 |
|
55 |
|
Таблица 2.9
Эмпирические формулы для расчета минимальных операционных припусков при обработке плоских поверхностей
Стадии |
Наименование |
|
Вид зависимости |
|
обра- |
|
|||
операции |
|
Zmin = f (D, L), мм |
||
ботки |
|
|
|
|
1 |
Черновое фрезерование |
Штамповка, литье в песчаные |
||
|
|
формы |
|
|
|
|
Zmin = 0,00164Li + 0,875 |
||
|
Черновое строгание |
Литье в кокиль |
|
|
|
|
Zmin = 0,0011Li |
+0,683 |
|
|
|
Литье в оболочковые формы |
||
|
|
Z min = 0,00082Li + 0,613 |
||
|
|
Литье |
по |
выплавляемым |
|
|
моделям |
|
|
|
|
Zmin = 0,0011Li |
+0,383 |
|
2 |
Чистовое фрезерование |
Zmin = |
0,001L + 0,4 |
|
|
Чистовое строгание |
Zmin = |
0,001L + 0,4 |
|
|
Предварительное |
Zmin = |
0,000548L + 0,0918 |
|
|
шлифование |
|||
|
|
|
|
|
3 |
Тонкое фрезерование |
Zmin = |
0,000548L + 0,0918 |
|
|
Тонкое строгание |
Zmin = |
0,000548L + 0,0918 |
|
|
Предварительное |
Zmin = |
0,000182L + 0,0918 |
|
|
протягивание |
|||
|
|
|
|
|
4 |
Отделочноепротягивание |
Zmin = |
0,00053L + 0,0918 |
|
|
Чистовое шлифование |
Zmin = |
0,00035L + 0,05 |
|
|
Тонкое фрезерование |
Zmin = |
0,0004L + 0,07 |
|
|
Тонкое строгание |
Zmin = |
0,0004L + 0,07 |
|
5 |
Тонкое шлифование |
Zmin = |
0,00023L + 0,0261 |
|
|
Притирка |
Zmin = |
0,00023L + 0,0261 |
|
|
Полирование |
Zmin = |
0,000041L + 0,00917 |
|
|
Вибронакатывание |
Zmin = |
0 |
|
|
Виброполирование |
Zmin = |
0,000041L + 0,00917 |
56
3. ПАРАМЕТРИЧЕСКАЯ ОПТИМИЗАЦИЯ ПРОЦЕССОВ МЕХАНИЧЕСКОЙ ОБРАБОТКИ
3.1. Выбор параметров оптимизируемых процессов обработки
После выбора определенной структуры маршрута обработки, операции, перехода и различных видов технологической оснастки должна ставиться задача их параметрической оптимизации. Параметрическая оптимизация обычно выполняется после выбора структуры перехода и выражается главным образом в определении оптимальных режимов резания (V, S, t) с позиций некоторого критерия. К параметрической оптимизации могут быть также отнесены:
1)расчеты по выбору оптимальной конструкции и геометрии заточки режущего инструмента;
2)расчеты по выбору физико-механических свойств режущих пластин инструментов;
3)расчеты по выбору точностных, силовых и прочностных параметров станочных приспособлений;
4)расчеты по определению оптимальных значений припусков и допусков на выполняемые размеры.
Основная задача, которую решают при параметрической оптимизации ТП, – это определение оптимальных режимов обработки, при которых обеспечивается требуемое качество изделия при минимальных затратах общественного труда. Режимы обработки оказывают основное влияние на стоимость и производительность выполняемой операции, так как от них зависит штучное время, а значит, и доля себестоимости, пропорцио-
57
нальная времени. В значительной степени режимы обработки определяют точность и качество обработанных поверхностей. Режимы обработки – это управляемые переменные, степень влияния которых на основные показатели оптимизируемого процесса различна. Поэтому необходимо при выборе и построении критериев оптимальности учитывать наиболее значимые режимы обработки.
3.2. Постановка задачи расчета оптимальных режимов обработки материалов резанием
Задача определения оптимальных режимов резания – одна из наиболее массовых и встречается при разработке различных ТП мехобработки. При этом исходя из конкретных условий обработки, целей и задач оптимизации процесса резания возникает множество вариантов постановки этой задачи.
При описании процесса обработки выделяют входные и выходные параметры, которые между собой связаны сложными функциональными зависимостями. Совокупность этих зависимостей, дополненная критерием оптимальности, рассматривается как математическая модель процесса обработки.
В задачах расчета режимов резания набор входных параметров разделяют на искомые (управляемые) и заданные (неуправляемые). Задача расчета оптимальных режимов заключается в определении таких значений управляемых параметров из множества их значений, которые являются наилучшими (по некоторым показателям) по совокупности выходных параметров при заданном значении неуправляемых параметров.
58
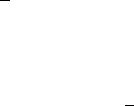
В общем случае постановка задачи оптимизации режимов обработки включает:
1)выбор управляемых параметров;
2)определение множества их возможных значений;
3)выбор анализируемого набора выходных параметров;
4)назначение диапазонов возможных значений выходных параметров;
5)установление функциональных зависимостей между выходными и управляемыми параметрами при фиксированных значениях неуправляемых параметров;
6)формирование целевой функции.
Набор управляемых параметров может быть представлен в виде некоторого множества
Х ={х1 , х2 , ..., хn },
где х1, х2, …, хn – управляемые параметры.
Тогда задача расчета оптимальных режимов резания сводится к следующей задаче математического программирования:
Ri (X ) ≤ Ri , i =1, 2, ..., m,
F(X ) → min (max),
где F(X) – зависимость для принятого критерия оптимальности; Ri(X) – значение i-й характеристики процесса резания в зависи-
мости от значений управляемых параметров (X); Ri – заданное предельное значение i-й характеристики процесса резания; m – число характеристик процесса в математической модели.
59
В зависимости от вида и сложности представления функций
F(X ) и Ri (X ) используются различные математические моде-
ли расчета режимов резания. Эти модели могут быть классифицированы по следующим признакам:
−составу набора Х оптимизируемых переменных;
−составу учитываемых показателей процесса (m);
−принятому критерию оптимальности;
−виду функций F(X ) и Ri (X ) , аппроксимирующих ос-
новные закономерности процесса;
−степени учета индетерминированности процесса резания
инеопределенности исходной информации.
Использование различных матмоделей приводит к необходимости разработки разнообразных методов и алгоритмов решения рассматриваемой задачи.
3.3. Расчет оптимальных режимов резания методом линейного программирования
В основе этого метода лежит построение математической модели, включающей совокупность технических ограничений и упрощенный вид целевой функции, приведенных к линейному виду логарифмированием. Для решения этой задачи на ЭВМ могут быть использованы различные численные методы (Гаусса, перебора, симплексный и др.), а также графический, наглядно представляющий математическую модель процесса.
Качество математической модели процесса резания зависит от выбора количества технических ограничений, которые в наи-
60