
книги / Технология конструкционных материалов. Способы получения деталей (заготовок) и конструкций
.pdf
или кистью. После нанесения огнеупорного покрытия кокиль нагревают до рабочей температуры 150…350 С.
При сборке кокилей (рис. 19, б) устанавливают, если необходимо, песчаный или металлический стержень 6, полуформы соединяют и скрепляют специальными зажимами. Затем производят заливку кокиля расплавом 7 (рис. 19, в). После затвердевания отливки металлический стержень частично извлекают, раскрывают кокиль, удаляют металлический стержень, извлекают затвердевшую и охлажденную отливку. Из отливки выбивают песчаный стержень, обрезают литники, прибыли и выпоры.
4.6. Изготовление отливок электрошлаковым литьем
В охлаждаемый водой медный кристаллизатор 6 (рис. 20) заливается расплавленный шлак. Электрический ток подводится к расходуемым электродам 7 и затравке 1.
Из-за малой электропроводно- |
|
|
|
||
сти шлаковая ванна нагревает- |
|
|
|
||
ся |
до высокой |
температуры |
|
|
|
и оплавляет погруженные в нее |
|
|
|||
7 |
|
||||
электроды. Капли металла, |
6 |
|
|||
проходя через шлаковую ванну |
|
||||
5 |
|
||||
4, |
собираются |
в металличес- |
4 |
|
|
кую ванну 3. Электроды под- |
3 |
|
|||
2 |
|
||||
нимаются вверх. Для оформле- |
|
||||
ния полости в отливке 2 пере- |
|
|
|
||
мещается металлический водо- |
|
|
|
||
охлаждаемый стержень 5. |
|
|
|
||
|
Получаемые отливки име- |
|
|||
|
|
1 |
|||
ют более высокие механические |
|
|
|
свойства, чемпоковки. |
Рис. 20. Схема электро- |
|
шлакового литья |
||
|
||
|
51 |
Расплавленный шлак очищает металл от серы и фосфора, защищает его от кислорода и азота воздуха, является тепловой надставкой, что устраняет усадочные раковины и необходимость в прибылях и, образуя на поверхности отливки пленку, обеспечивает чистую поверхность. Кристаллизация отливки происходит снизу вверх с участием малых объемов жидкого металла, что исключает ликвацию и осевую рыхлоту в отливке.
ЭШЛ применяют в энергетическом машиностроении (задвижки паропроводов сверхвысоких давлений, парогенераторы, корпусы атомных реакторов); литье труб из труднообрабатываемой аустенитной стали в атомной энергетике; судостроении (коленчатые валы мощных дизелей); металлургии (прокатные валки, калибры трубопрокатных станов, кузнечные штампы, кокили для литья и др.).
5. Технологические требования к конструкции отливки
При конструировании отливки должны быть соблюдены основные требования: равностенность отливки; отсутствие поднутрений и большого скопления металла в отдельных ее частях; наличие формовочных уклонов на вертикальных стенках (перпендикулярных к плоскости разъема формы), плавные переходы при сопряжении стенок; наличие галтелей и др.
Форма отливки должна быть простой для облегчения изготовления модельного комплекта и литейной формы.
Формовочные уклоны облегчают удаление модели из готовой формы без ее разрушения. На рис. 21, а, б показаны формовочные уклоны (закрашены) при горизонтальном и вертикальном положениях отливки в форме.
52

Рис. 21. Формовочные уклоны и сопряжения стенок отливки
Охлаждение отливки в форме сопровождается возникновением внутренних напряжений. Напряжения, образование раковин и пористости зависят от правильного сопряжения стенок и оформления углов отливки. Недопустимое сопряжение двух стенок различной толщины показано на рис. 21, в. При сопряжении стенок выполняют закругления определенного радиуса (рис. 21, г) в отливках для деталей, подвергающихся ударным нагрузкам, или сопрягают стенки плавным клиновым переходом (рис. 21, д). Неудачным сопряжением ребер жесткости (рис. 21, е) считают крестоподобное (образующее местное скопление металла), которое заменяют Т-образным вразбежку (рис. 21, ж). Сопряжение стенок под острым углом (рис. 21, з), ослабляющее отливку в этом месте, заменяют углом с закруглением (рис. 21, и).
6. Изготовление отливок из различных сплавов
6.1. Изготовление отливок из чугунов
Серый чугун имеет высокую жидкотекучесть и малую усадку (до 1,3 %). Отливки из него получаются качественными, без усадочных раковин, пористости и трещин; толщина стенок у крупных фасонных отливок можетбыть доведенадо 3…4 мм.
53
Обычный серый чугун выплавляют в вагранках, высококачественный в дуговых или индукционных печах. Вагранка плавильный агрегат в виде шахты доменного типа с водоохлаждаемым кожухом. Процесс плавки в вагранках автоматизирован.
Отливки серого чугуна получают в песчаных формах, литьем в оболочковые формы, в кокили, литьем по выплавляемым моделям, центробежным литьем. Отливку, полученную вкокиле, дляустранениявозможногоотбелаподвергаютотжигу.
Высокопрочный чугун обладает жидкотекучестью серого чугуна, что позволяет получать отливки с толщиной стенки 3…5 мм. Усадка высокопрочного чугуна значительна (до 1,7 %), поэтому отливки имеют усадочные дефекты. В связи с этим осуществляют направленную кристаллизацию металла отливок путем создания прибылей и холодильников.
Высокопрочный чугун выплавляют в вагранках, дуговых печах, а также в индукционных печах.
Отливки из высокопрочного чугуна получают различными способами.
Ковкий чугун получают отжигом белого чугуна. Белый чугун обладает худшими литейными свойствами, чем серый чугун. Это приводит к повышенным температурам заливки, особенно при получении тонкостенных отливок, и возникновению усадочных раковин, пористости и трещин.
Белый чугун получают дуплекс-процессом: сначала плавят в вагранке, а затем переливают в дуговую или индукционную печь, где осуществляются нагрев до нужной температуры и доводка расплава до заданного химического состава.
Отливки получают в песчаных формах, а также в оболочковых формах и кокилях; толщина стенок этих отливок 5…50 мм. Отливки подвергают длительному отжигу на ковкий чугун.
54
6.2. Особенности изготовления стальных отливок
Углеродистые литейные стали содержат 0,12…0,6 % углерода.
Литейные свойства стали хуже, чем чугуна и других литейных сплавов (усадка доходит до 2,5 %). При этом низкоуглеродистые стали имеют склонность к образованию горячих трещин при повышенных температурах разливки. В высокоуглеродистых сталях возникают внутренние напряжения из-за меньшей пластичности и теплопроводности.
Стали плавятся в дуговых и индукционных печах. Часто применяется плавка стали в плазменных печах, что приводит к лучшему растворению легирующих добавок из отходов легированных сталей, уменьшению загрязнения окружающей среды и лучшим условиям труда.
Стальные отливки массой в несколько граммов и десятков тонн с толщиной стенки 1…300 мм получают в песчаных формах и другими способами. Они подвергаются последующей термической обработке (отжигу или нормализации) для снятия литейных напряжений и улучшения структуры.
Из углеродистых сталей получают отливки для корпусов и станин, зубчатых колес, прокатных валков.
Применяют и легированные литейные стали: 15Х25ТЛ, 09Х16Н4БЛ, 08Х17634В5Т3Ю2Л, 12Х18Н9ТЛ и другие, ко-
торые используют для литья турбинных лопаток, клапанов арматуры и других ответственных деталей.
6.3. Особенности изготовления отливок из цветных металлов
В производстве применяется пять групп литейных алю-
миниевых сплавов. Это Al Si, Al Cu Si, Al Cu, Al Mg
и сложнолегированные сплавы. Сплавы системы Al Si (силумины марок АЛ2, АЛ4, АЛ9) обладают наилучшими литейными свойствами, усадка составляет 0,8…1,1 %.
55
Выбор метода плавки цветных металлов определяется их свойствами. Алюминиевые и магниевые сплавы имеют низкие температурные интервалы плавления и обладают повышенным сродством к кислороду. Плавку алюминиевых сплавов ведут в пламенных печах, в электрических печах сопротивления, в индукционных печах.
Большуючастьотливокизалюминиевыхсплавов(70…80 %) получают литьем в постоянные формы (в кокиль, под давлением, под низким давлением), остальные в разовые формы (песчаные, оболочковые, по выплавляемым моделям).
Лучшими литейными магниевыми сплавами являются сплавы системы Mg Al Zr марок МЛ5 и МЛ6.
Магниевые литейные сплавы имеют недостаточные литейные свойства, хорошую растворимость водорода в расплаве (что приводит к охрупчиванию металла) и самовозгораются при плавке и заливке форм. Поэтому плавку магниевых сплавов ведут в тигельных электрических и индукционных печах под слоем специальных флюсов или в среде защитных газов, чтобы предотвратить возгорание сплава.
Около 40 % отливок из магниевых сплавов получают литьем в постоянные формы (в кокиль и под давлением). Отливки также изготовляют в разовых формах (песчаных и оболочковых). Чтобы избежать возгорания при разливке, струю металла припыливают порошком серы.
Лучшими литейными свойствами среди отливок из медных сплавов обладают оловянные бронзы (усадка 1,4…1,6 %) БрОЦ4-3, Бр05Ц5С5, Бр06Ц6С2, Бр01ОФ1. Безоловянные бронзы БрАЖ9-4; БрАЖН10-4,4; БрКМц3-1, БрС30, БрБ2 имеют бóльшую усадку (1,6…2,4 %). Латуни ЛА60-1-1, ЛЦ16К4, ЛЦ40Мц3Ж, ЛЦ23А6Ж3МЦ2 имеют удовлетворительную жидкотекучесть и сравнительно высокую усадку (1,6…2,2 %). Медные сплавы склонны к образованию усадочных раковин и пористости, а также трещин.
56
Плавку медных сплавов ведут в отражательных, электродуговых и индукционных печах; на воздухе, в среде защитных газов и в вакууме.
Около 80 % отливок получают литьем в разовые формы (песчаные, оболочковые, по выплавляемым моделям), остальные в постоянные (в кокиль, под давлением, центробежное литье).
Титановые сплавы имеют литейную усадку 1,5 % при литье в керамические и 2…2,3 % в металлические формы.
Основной литейный сплав ВТ5Л обладает хорошими механическими и литейными свойствами. Кроме того, применяются сплавы ВТ1Л, ВТ6Л, ВТ14Л и др.
Плавят титановые сплавы вследствие их высокой химической активности в вакууме, а также в атмосфере аргона или гелия. Используются вакуумно-дуговые, электронно-лучевые и плазменные печи с графитовыми тиглями или медными водоохлаждаемыми кристаллизаторами.
Из-за высокой химической активности заливка титановых сплавов в формы осуществляется в вакууме.
Около 80 % отливок из титановых сплавов производят литьем в разовые высокоогнеупорные формы. Используют формовочные смеси на основе плавленого оксида алюминия (электрокорунда), магнезита, диоксидов циркония и графита. Отливки получают также в графитовых керамических формах по выплавляемым моделям и в оболочковых формах. Простые отливки изготавливают литьем в металлические или графитовые кокили.
57
IV. ОБРАБОТКА МЕТАЛЛОВ ДАВЛЕНИЕМ
1. Сущность обработки металлов давлением
Обработка металлов давлением основана на их способности в определенных условиях пластически деформироваться (изменять свою форму и размеры без разрушения) под действием внешних сил.
Взависимости от величины напряжений, возникающих
вметалле при нагрузке, различают упругую и пластическую деформации. При упругих деформациях деформируемая заготовка восстанавливает форму и размеры после снятия внешних сил. При пластических деформациях изменение формы и размеров сохраняется и после прекращения действия этих сил. Упругая деформация приводит к смещению
атомов на величину, меньшую межатомных расстояний, и после снятия внешних сил атомы возвращаются в исходное положение. При пластических деформациях атомы смещаются на величины, бóльшие межатомных расстояний, и после снятия внешних сил занимают новые положения равновесия. В новые положения равновесия атомы могут переходить в результате смещения в определенных параллельных плоскостях, без существенного изменения расстояний между этими плоскостями. Деформация происходит без нарушения сплошности металла, плотность которого практически не изменяется (рис. 22, б, в, г). Скольжение одной части кристаллической решетки относительно другой происходит по плоскостям наиболее плотного размещения атомов (плоскостям скольжения) (рис. 22, а). В реальных металлах кристаллическая решетка имеет линейные дефекты (дислокации), перемещение которых облегчает скольжение.
58
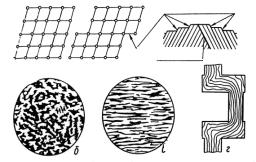
Плоскостискольжения
Границазерен
а
|
|
|
|
г |
|
б |
|||||
|
в |
Рис. 22. Схема скольжения (а) и изменения микроструктуры металла при его деформировании (б, в, г)
Величина пластической деформации не безгранична, при определенныхеезначенияхможетначатьсяразрушениеметалла.
2. Факторы, влияющие на пластичность металла
Пластичность металла зависит от его химического состава. Наибольшей пластичностью обладают чистые металлы. Сплавы твердые растворы обычно более пластичны, чем сплавы, образующие химические соединения. С повышением содержания углерода в стали пластичность уменьшается. Кремний понижает пластичность стали.
Влегированных сталях хром и вольфрам уменьшают,
аникель и ванадий повышают пластичность стали. Сера, фосфор охрупчивают сталь.
Марганец, образуя тугоплавкое соединение MnS, нейтрализует вредное действие серы. При отсутствии марганца
сера может образовать легкоплавкую эвтектику Fe FeS, способствующую образованию горячих трещин при обработке давлением. Фосфор увеличивает пределы прочности и текучести, но уменьшает, особенно при низких температурах, пластичность и вязкость стали, вызывая ее хладноломкость.
59
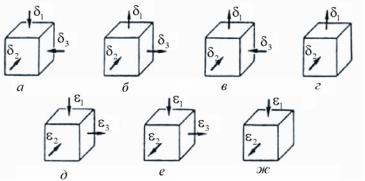
Пластичность литого металла ниже, чем того же, но деформированного.
Металл, имеющий мелкозернистую структуру, пластичнее крупнозернистого.
Стали, подвергнутые отжигу, пластичнее закаленных, а цветные металлы имеют пластичность выше после закалки.
Равномерное расположение неметаллической фазы и приближение ееформыкформе шараувеличивает пластичность.
Пластичность зависит также от скорости деформации изменения степени деформации в единицу времени d dt.
В общем случае с увеличением скорости деформации предел текучести возрастает, а пластичность падает.
Напряженное состояние металла. Деформированное состояние характеризуется схемой главных деформаций, т.е. деформаций в направлении трех осей, перпендикулярных к площадкам, в которых касательные напряжения отсутствуют (рис. 23, д, е, ж). Совокупность схем главных напряжений
Рис. 23. Схема главных напряжений и деформаций
и главных деформаций позволяет судить о характере главных напряжений и деформаций при различных видах обработки давлением и пластичности металла: чем больше сжимающие напряжения и меньше напряжения и деформации растяжения, тем выше пластичность обрабатываемого металла. По-
60