
книги / Получение наночастиц и наноматериалов
..pdfнопорошка и газообразных веществ или вступают в химические реакции также с образованием порошка и газообразных веществ.
Недавно разработанным методом, который тоже можно отнести к технологиям химического осаждения из паровой фазы,
является метод высокотемпературного гидролиза. Он основан на взаимодействии соединений, преимущественно хлоридов и карбонилов металлов, в водородно-кислородном пламени. За счет высокотемпературного гидролиза образуются мельчайшие капли расплавленного оксида. Например, при синтезе TiO2 в пламени протекает реакция
ТiCl4 + 2H2O = TiO2 + 4HCl.
Затем проводят резкое охлаждение, в результате чего формируются твердые наночастицы. Высокотемпературным гидролизом получены оксиды кремния, алюминия, титана, хрома, железа, церия, никеля, олова, ванадия, циркония и др. Этим способом можно получать многокомпонентные соединения.
Технологии высокоэнергетического синтеза
Данная группа технологий основана на использовании реакций, протекающих с высокой скоростью в условиях, далеких от равновесия, при высокоэнергетическом воздействии. Для получения нанопорошков нашли применение два метода – детонационный и плазмохимический.
Детонационный синтез. Основан на воздействии ударной волны с давлением до нескольких десятков ГПа на смесь исходных реагентов. По этому методу с помощью ударно-волновой обработки смесей графита с металлами получают нанокристаллические алмазные порошки со средним размером частиц 4 нм.
Детонация взрывчатых веществ, т.е. энергия взрыва, достаточно широко используется для осуществления фазовых переходов в веществах и детонационного синтеза. Детонационный синтез как быстро протекающий процесс позволяет получать тонкодисперсные порошки в динамических условиях, когда важную роль играют кинетические процессы.
31
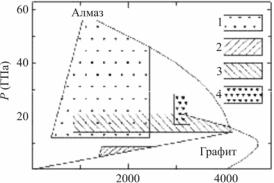
Впервые детонационный синтез алмаза осуществлен путем ударно-волнового нагружения ромбоэдрического графита до 30 ГПа. Впоследствии алмазные порошки были получены удар- но-волновой обработкой смесей графита с металлами; длительность ударной волны была 10–20 мкс, а создаваемое ею давление 20–40 ГПа. Позднее было показано, что полученный в этих условиях алмазный порошок содержит одиночные кристаллы размером не более 50 нм, а также скопления и плотно спаянные агломераты размером до 5 мкм и более, состоящие из отдельных кристаллов с размерами 1–4 и 10–160 нм.
В настоящее время используют метод образования наноалмазов при детонации взрывчатых веществ с отрицательным кислородным балансом, т.е. разлагающихся с выделением свободного углерода, из которого образуется алмазная фаза (обычно берется смесь тротила и гексогена, взятых в оптимальном соотношении). Синтез осуществляется при давлении от 165 до 23 ГПа и температуре свыше 3000 К в условиях термической стабильности алмаза (рис. 1.14).
Рис. 1.14. Фазовая р-Т-диаграмма состояния углерода с указанием областей синтеза алмаза различными методами: 1 – ударно-волновой синтез с использованием графита; 2 – статическое превращение с использованием катализатора; 3 – статическое превращение без катализатора; 4 – детонационный синтез смеси тринитротолуола и гексогена
32
Вдетонационном синтезе при малом времени существования высоких давлений и температур, необходимых для образования алмаза, важная роль принадлежит кинетике образования
ироста зародышей алмазной фазы. Однако если не происходит быстрого охлаждения продуктов синтеза, то возможна графитизация образовавшихся алмазных частиц. Поэтому при взрывном синтезе наноалмаза продукты детонации интенсивно охлажда-
ются газообразными (СО2, азотом, аргоном) (сухой синтез), жидкими (вода) (мокрый синтез) или твердыми (лед) хладоагентами. При этом в наиболее удачных синтезах лишь от 6 до 8 % углерода переходит в конденсированные продукты детонации (так называемую алмазную шихту), которые могут содержать 60–70 % алмазной фазы наряду с неалмазным углеродом и примесями металлов. Поэтому важной является стадия выделения или очистки наноалмаза.
Вроссийской промышленности освоен конверсионный метод получения алмазного нанопорошка путем взрыва боеприпасов в специальных камерах; в результате развивающихся при взрыве высоких давлении и температуре происходит синтез алмаза из углеродсодержащих взрывчатых веществ, катализируемый частицами и парами металла из оболочек боеприпасов.
Характерной особенностью алмазных нанопорошков, получаемых детонационным синтезом, является чрезвычайно малая дисперсия размеров наночастиц, основная доля частиц имеет размер 4–5 нм. Наблюдаемый в разных исследованиях узкий диапазон размеров нанокристаллов алмаза есть следствие того, что при малых размерах наночастиц именно алмаз, а не графит является стабильной формой углерода.
Образцы детонационного наноалмаза представляют собой серый порошок с разной интенсивностью окраски и обязательно содержат кроме алмаза неалмазный углерод, кислород, азот, водород
идругие элементы. Форма частиц алмаза определяется условиями синтеза. В случае мокрого синтеза форма приближается к сферической, тогда как при сухом синтезе получаются близкие к идеальным по структуреограненные нанокристаллы алмаза.
33
Другой детонационный способ реализован для синтеза различных морфологических форм углерода и нанопорошков оксидов Al, Mg, Zr, Zn. Слой исходного вещества (высокопористая металлическая среда, химическое соединение, соль или гель гидроксида металла) подвергается ударно-волновому воздействию от контактного заряда взрывчатого вещества. В ударной волне происходит сжатие и прогрев высокопористого металла или же протекают реакции разложения исходного соединения до оксида с последующей стабилизацией оксидных фаз. После выхода ударной волны на свободную поверхность исходного вещества материал разлетается в газовую атмосферу взрывнойкамеры.
Если в качестве исходного вещества используются металлы, то применяется активная кислородсодержащая среда. В этом случае на стадии разлета происходит горение металла с образование наночастиц оксида. При использовании углеродсодержащей атмосферы СО2 удается синтезировать нанотрубки и сферические частицы углерода, атакже нитевидные кристаллы MgO.
Плазмохимический синтез. Одним из самых распространенных химических методов получения высокодисперсных порошков нитридов, карбидов, боридов и оксидов является плазмохимический синтез (рис. 1.15).
Основными условиями получения высокодисперсных порошков этим методом являются протекание реакции вдали от равновесия и высокая скорость образования зародышей новой фазы при малой скорости их роста. В реальных условиях плазмохимического синтеза получение наночастиц целесообразно осуществлять за счет увеличения скорости охлаждения потока плазмы, в котором происходит конденсация из газовой фазы; благодаря этому уменьшается размер образующихся частиц, а также подавляется рост частиц путем их слияния при столкновении.
При плазмохимическом синтезе используется низкотемпературная (4000–8000 К) азотная, аммиачная, углеводородная, аргоновая плазма дугового, тлеющего высокоили сверхвысокочастотного разрядов; в качестве исходного сырья применяют элементы, их галогениды и другие соединения. Характеристики
34
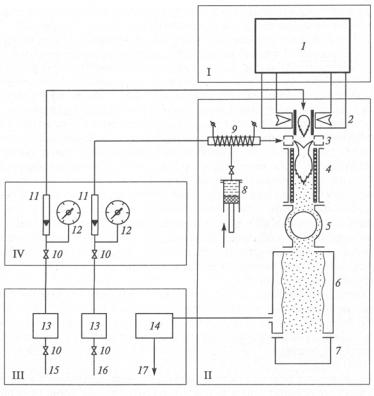
получаемых порошков зависят от используемого сырья, технологии синтеза и типа плазмотрона. Частицы плазмохимических порошков являются монокристаллами и имеют размеры от 10 до
100–200 нм и более.
Рис. 1.15. Схема СВЧ-установки плазмохимического синтеза: I – силовое оборудование (1 – микроволновой генератор); II – основное технологическое оборудование (2 – плазматрон, 3 – устройство ввода реагентов, 4 – реактор,
5– теплообменник, 6 – фильтр, 7 – сборник порошка, 8 – дозатор реагентов, 9 – испаритель); III, IV – соответственно вспомогательное оборудование
Все известные плазмохимические способы получения нанопорошков могут быть объединены в три метода исходя из агрегатного состояния исходного сырья, вводимого в плазму:
35
1)переработка газообразных соединений;
2)переработка капельно-жидкого сырья;
3)переработка твердых частиц, взвешенных в потоке плазмы. Плазмохимический синтез включает несколько этапов. На
первом этапе происходит образование активных частиц в дуговых, высокочастотных и сверхвысокочастотных плазменных реакторах. Наиболее высокой мощностью и коэффициентом полезного действия обладают дуговые плазменные реакторы, однако получаемые в них материалы загрязнены продуктами эрозии электродов; безэлектродные высокочастотные и СВЧ-плазменные реакторы не имеют этого недостатка. На следующем этапе в результате закалки происходит выделение продуктов взаимодействия. Выбор места и скорости закалки позволяет получить порошки с заданными составом, формой иразмером частиц.
В качестве исходных продуктов для плазмохимического синтеза используются хлориды металлов, металлические порошки, кремний- и металлоорганические соединения.
Плазмохимические порошки карбидов металлов, бора и кремния обычно получают взаимодействием хлоридов соответствующих элементов с водородом и метаном или другими углеводородами в аргоновой высокочастотной или дуговой плазме; нитриды получают взаимодействием хлоридов с аммиаком или смесью азота и водорода в низкотемпературной СВЧплазме. С помощью плазмохимического синтеза можно получать также многокомпонентные субмикрокристаллические порошки, представляющие собой смеси карбида и нитрида, нитрида и борида, нитридов разных элементов и т. д.
Синтез оксидов в плазме электродугового разряда проводится путем испарения металла с последующим окислением паров или окислением частиц металла в кислородсодержащей плазме. Плазмохимическим синтезом были получены наночастицы оксида алюминия со средним размером 10–30 нм. Образование нанопорошков оксида алюминия с минимальным размером частиц достигается при взаимодействии паров металла с кислородом воздуха в условиях интенсивного вдувания возду-
36
ха, за счет чего происходит быстрое уменьшение температуры. Интенсивное охлаждение не только тормозит рост частиц, но и увеличивает скорость образования зародышей конденсированной фазы. Плазмохимический синтез с окислением частиц алюминия в потоке кислородсодержащей плазмы приводит к образованию более крупных частиц оксида по сравнению с окислением предварительно полученного пара металла.
Плазмохимический метод используется и для получения порошков металлов. Например, субмикрокристаллические порошки меди с размером частиц менее 100 нм и сравнительно узким распределением частиц по размеру получают восстановлением хлорида меди водородом в аргоновой электродуговой плазме с температурой до 1800 К.
Плазмохимический синтез обеспечивает высокие скорости образования и конденсации соединения и отличается достаточно высокой производительностью. Главные недостатки плазмохимического синтеза – широкое распределение частиц по размерам и, вследствие этого, наличие довольно крупных (до1–5 мкм) частиц, а также высокое содержание примесей в порошке.
К настоящему времени плазмохимическим методом получены высокодисперсные порошки нитридов титана, циркония, гафния, ванадия, ниобия, тантала, бора, алюминия и кремния, карбидов титана, ниобия, тантала, вольфрама, бора и кремния, оксидов магния, иттрия и алюминия. Наиболее широко плазмохимический метод применяется для синтеза нитридов переходных металлов IV и V групп.
Газофазный синтез с использованием лазерного излучения для создания и поддержания плазмы, в которой происходит химическая реакция, оказался эффективным методом получения молекулярных кластеров. Наиболее известны среди них фуллерены.
Растворные методы
Основными условиями получения коллоидных наносистем, независимо от применяемых методов синтеза, являются малая растворимость дисперсной фазы в дисперсионной среде и нали-
37
чие в системе, в которой образуются частицы, веществ, способных стабилизировать эти частицы, а в случае конденсационных методов замедлять или приостанавливать их рост.
Методы химического осаждения (соосаждения). Методы химического осаждения заключаются в совместном осаждении (соосаждении) компонентов продукта из раствора в виде нерастворимых солей или гидроксидов. При синтезе оксидных порошков осаждением готовят растворы (преимущественно водные), содержащие требуемые катионы, и смешивают эти растворы с растворами осадителя. Осадок отделяют фильтрованием и сушат, получая вещество-предшественник, которое после термообработки (термолиза) в соответствующей газовой среде образует порошок требуемого соединения.
На процесс осаждения оказывают влияние концентрации исходных веществ, температура, давление, наличие добавок по- верхностно-активных веществ. В качестве осаждаемых веществ предпочтительно использовать хорошо растворимые соли азотной, соляной, уксусной и других кислот.
Наиболее распространены три типа химического осаждения –
гидроксидный, оксалатный икарбонатный методы.
Для осаждения гидроксидов в качестве осадителя используются растворы аммиака или щелочи.
Меx(A)y + (K)OH → Меx(OH)y + KA.
Для осаждения оксалатов в качестве осадителей используются смеси щавелевая кислота–аммиак, щавелевая кислота– триэтиламин либо избыток насыщенного раствора оксалата аммония при фиксированной кислотности раствора, либо водный раствор диметилоксалата.
Осаждение карбонатов аналогично осаждению оксалатов. В качестве осадителя при осаждении карбонатных солей используются избыток гидрокарбоната аммония, избыток карбоната натрия либо карбонат тетраметиламмония. Осаждение проводят при pH > 8, создаваемом добавлением раствора аммиака
38
или гидроксида натрия. Однако приходится уделять особое внимание стадии промывки осадка, поскольку примеси щелочных металлов могут изменять свойства получаемых материалов.
Контакт осадка с жидкой фазой приводит к его старению. Это влияет на характеристики частиц и агрегатов, которые могут упрочняться, уплотняться и вырастать в крупные кристаллы. Особенно интенсивно процессы старения идут в водных растворах. Для предотвращения образования крупных и прочных агрегатов удаляют не прореагировавшие исходные вещества и продукты реакции, используют ПАВ, регулируют рН среды, замещают маточный раствор другой жидкостью, в которой старение происходит медленнее. Водные маточные растворы замещают водорастворимыми органическими жидкостями, например этанолом, ацетоном.
Осаждение в неводных органических средах значительно замедляет процесс старения осадков, исключает необходимость замещения воды органической жидкостью, облегчает сушку, что позволяет получать непрочно агрегированные высокодисперсные порошки. Однако выбрать хорошо растворимые в органических жидкостях дешевые исходные вещества и осадитель весьма сложно. К тому же большинство органических жидкостей токсично и огнеопасно, что требует специальных мер по технике безопасности.
В расплавах солей, металлов и других веществ после образования осадка смесь охлаждают, а растворитель, побочные продукты и непрореагировавшие вещества удаляют растворением их в воде, кислоте или другой подходящей среде. Основной проблемой является исключение захвата синтезируемым порошком компонентов растворителя и побочных соединений.
На рис. 1.16 представлены изображения частиц порошка диоксида циркония, стабилизированного РЗЭ, полученного методом осаждения с применением золь-гель-технологии.
Для отделения осадка от жидкой фазы используют фильтрование, центрифугирование, распылительную сушку. Наиболее экономичным является фильтрование, наиболее производительный процесс – распылительная сушка, которую можно совме-
39
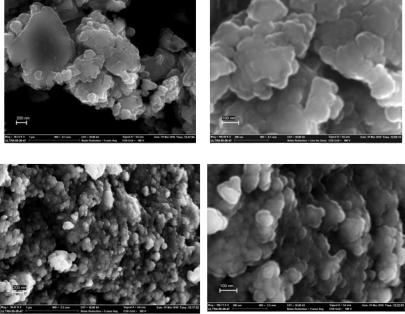
щать с процессом термолиза. На рис. 1.17 представлены полученные на сканирующем электронном микроскопе изображения первичных частиц нанопорошка и гранул после распылительной сушки.
а
б
Рис. 1.16. Морфология частиц диоксида циркония, стабилизированного РЗЭ, после сушки (а) и отжига при температуре 600 °С (б)
Пример синтеза сложного оксида этим методом – получение Mg4Nb2O9. В качестве исходных веществ использовали гексагидрат нитрата магния Mg(NO3)2·6H2O, оксид ниобия Nb2O5 и гидроксид натрия. Nb2O5 растворяли в минимальном количестве плавиковой кислоты (HF) при нагревании, после чего раствор охлаждали до комнатной температуры. Mg(NO3)2·6H2O растворяли в дистиллированной воде. Затем растворы смешивали в необходимых соотношениях и добавляли водный раствор щелочи до pH = 12, при котором обеспечивалось полное осаж-
40