
книги / Процессы обработки заготовок В. А. Бахвалов. Слесарная обработка
.pdf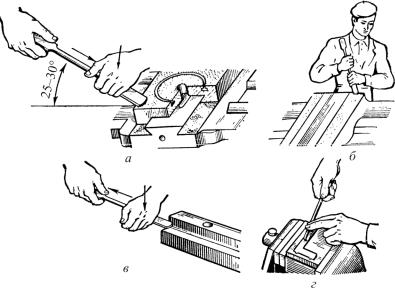
Рис. 134. Приемы шабрения плоских поверхностей деталей машин: а – от себя; б – на себя; в – расположенных под углом;
г– при отделочных операциях
11.5.Шабрение плоских поверхностей
Для получения поверхности высокого качества последовательно выполняют черновое, получистовое и чистовое шабрение.
Черновое шабрение (предварительное) заключается в грубой обработке поверхности, а именно удаляют следы и риски предшествующей шабрению лезвийной обработки. Работу выполняют шабером шириной 20–30 мм при длине рабочего хода 10–15 мм. Направление шабрения непрерывно меняют так, чтобы последующий штрих наносился под углом 90о к предыдущему штриху.
За один ход шабера снимают слой 0,02–0,05 мм. Шабрят до тех пор, пока неисчезнутвидимыериски от предыдущей обработки.
Качество шабрения проверяют на краску, которую наносят на поверочную плиту (линейку). После наложения и движения (плиты илидетали) обнаруженныевыступающиеместашабрятвторично.
151
Получистовое шабрение (точечное) заключается в удалении материала наиболее выступающих мест (серых пятен), выявляемых проверкой на краску. Работу выполняют плоским узким шабером (12–15 мм) при длине рабочего хода 5–10 мм. Направление движения шабера непрерывно меняют так, чтобы последующий штрих шел под углом 90о к предыдущему штриху. За один ход снимают слой материала 0,01–0,02 мм.
Чистовое шабрение (отделочное) применяют для получения поверхности высокой точности. При легком нажиме на шабер снимают за один рабочий ход 0,005–0,01 мм материала. Применяют шаберышириной8–10 мм при длинерабочего хода 3–5 мм.
Какправило, применяютприемшабрения«отсебя» (рис. 134, а), так как прием шабрения «на себя» (рис. 134, б, в, г) имеет следующие недостатки:
–при рабочем ходе шабер недостаточно устойчив, вследствие чего стружка неодинакова по сечению и поверхность получается неровной, рваной;
–в конце каждого рабочего хода шабер оставляет заусенцы, которые приходится снимать дополнительно.
Шабер, разработанный новатором А.А. Барышниковым, отличаетсяотшаберовобщеизвестных конструкцийбольшейдлиной(500 мм
иболее), что позволяет качественно шабрить приемом «на себя». При работе этим приемом шабер берут за среднюю часть обеими
руками в обхват и устанавливают к обрабатываемой поверхности не под углом 30о, как это делают при шабрении приемом «от себя», а под углом 75–80о (см. рис. 134, б, в, г). Верхний конец шабера, на которомимеется деревяннаяручка, рабочийупирает вплечо.
Преимущество такого приема шабрения заключается в том, что, кроме рук, рабочий использует при шабрении плечо, а это повышает устойчивость шабера и качество шабрения. Кроме того, длинный шабер пружинит, поэтому режущая часть шабера врезается в поверхность детали и выходит из нее плавно: шабреная поверхность получается более ровная, без рванин, а в конце штриха не остается заусенцев.
152
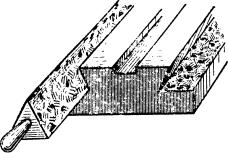
Прием шабрения «на себя» в 1,5–2 раза производительнее приема шабрения «от себя», однако, как показала практика производства и личный опыт автора пособия, большинство слесарейшабровщиков предпочитают применять при шабрении прием «от себя», так как при этом лучше обзор обрабатываемой поверхности, чем при шабрении «на себя».
Шабрение плоскостей, расположенных под острыми углами, –
суппортов, кареток, консолей, станин и некоторых других частей металлорежущих станков, представляющих собой сопряжения типа «ласточкинхвост», выполняюттрехграннымишаберами.
Перед шабрением направляющих типа «ласточкин хвост» (рис. 135) трехгранной линейкой, покрытой краской, выявляют выступающие места.
Рис. 135. Нанесение краски перед шабрением направляющих типа «ласточкин хвост»
Шабрят плоскости, расположенные под острыми углами, так же, как и открытые, параллельные плоскости (приемы шабрения описаны выше).
Метод трех плит является весьма точным, дающим возможность получить правильные плоскости независимо от точности имеющегося поверочного инструмента.
Этот метод заключается в следующем: каждой из трех одинаковых по размерам и весу плит, предварительно опиленных, фрезерованных или строганных, прошедших искусственное или
153
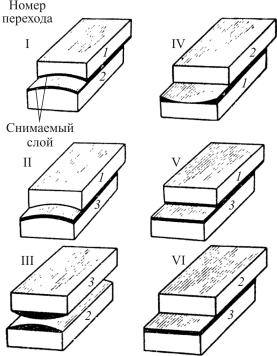
естественное старение (для снятия внутренних остаточных напряжений), присваивается порядковый номер, и на них наносят клейма: на первую плиту – № 1, на вторую плиту – № 2, на третью плиту – № 3 (рис. 136).
Рис. 136. Шабрение по методу трех плит
После указанной подготовки плиты шабрят в следующей последовательности:
–I переход – плиту № 1 пришабривают по плите № 2;
–II переход – плиту № 1 пришабривают по плите № 3;
–III переход – плиту № 2 пришабривают по плите № 3;
–IV переход – плиту № 2 пришабривают по плите № 1;
–V переход – плиту № 3 пришабривают по плите № 1;
–VI переход – плиту № 3 пришабривают по плите № 2.
154
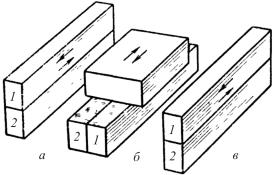
Такое чередование плит дает возможность после каждого перехода шабрения плиты получать более точную поверхность.
В конце работы все три плиты будут весьма точными (отклонение от прямолинейности и от плоскостности составляет порядка 0,001–0,003 мм).
Шабрение по методу совмещения граней обеспечивает точ-
ные плоскости и гарантирует их перпендикулярность боковым сторонам детали. Этот метод шабрения применяют при шабрении рабочих граней деталей прямоугольно-призматической формы. Шабрение начинают со взаимной пригонки двух рабочих граней (рис. 137, а). После этого обработанные грани совмещают друг с другом (рис. 137, б). Это совмещение дает возможность одновременно проверить обе шаброванные поверхности одной и той же поверочной плитой. После окончания этого цикла переходов процесс повторяют (рис. 137, в). По этому методу шабрят грани детали параллельно одной из ее сторон, но при совмещении пользуются не боковыми, а параллельными плоскостями, установив деталь на второй контрольной (поверочной) плите, и процесс шабрения, таким образом, ведутмеждудвумяконтрольными(поверочными) плитами.
Рис. 137. Шабрение по методу совмещения граней: а – пригонка двух граней; б – совмещенная пригонка; в – повторение перехода «а»
Отклонение от плоскостности и прямолинейности составляет
0,003–0,01 мм.
155

Контроль качества шабрения производят по числу пятен (точек), приходящихся на единицу площади шаброванной поверхности. Чем больше это число, тем выше качество шаброванной поверхности.
Для определения степени точности используется квадратная рамка размером 25,4 25,4 мм (рис. 138), которую накладывают на пришабренную поверхность.
Рис. 138. Контроль качества шабрения рамкой
Шабрение завершают при следующем числе пятен на поверхности, ограниченной рамкой 25,4 25,4 мм: черновое – 4–6 пятен; получистовое – 8–16 пятен; чистовое – 20–25 пятен.
При обработке шабрением направляющих станин особо точных (прецизионных) станков шабрение завершают при достижении 35–37 пятенна одинквадратныйдюйм пришабреннойповерхности.
11.6. Шабрение криволинейных поверхностей
Шабрение криволинейных поверхностей, например вкладышей подшипников скольжения, выполняют следующим образом.
На вал или шейку вала (рис. 139, а), с которой будет сопрягаться подшипник, равномерно наносят тонкий слой краски.
Вал накладывают на вкладыш подшипника или вкладыш подшипника накладывают на шейку вала и легким усилием поворачивают его, после чего снимают вал (рис. 139, б) и шабрят трехгранным шабером выступающие места (рис. 139, в).
Шабер устанавливают так, чтобы металл (сплав) снимала средняя часть режущей кромки.
156
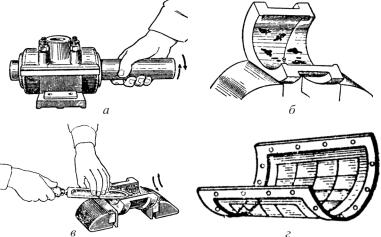
Рис. 139. Шабрение криволинейных поверхностей: а – нанесение краски на вал; б – вкладыш со следами краски; в – процесс шабрения;
г– шаблон-сетка для проверки количества пятен после шабрения
Шабер удерживают за ручку правой рукой, слегка вращая,
алевой рукой прижимают шабер к обрабатываемой поверхности. Шабрение продолжают до тех пор, пока не получат необхо-
димое количество пятен, которое определяют шаблоном-сеткой.
11.7. Заточка и доводка (заправка) трехгранных шаберов
При заточке шабер держат правой рукой за рукоятку, а пальцами левой руки – за его канавки (желобки), расположенные на боковых гранях, и плавно, с легким нажимом подводят нижнюю плоскость шабера к шлифовальному кругу (рис. 140, а).
При движении шабера вперед правая рука должна плавно опускаться вниз, а острый конец шабера должен подниматься вверх. При движении назад правая рука плавно поднимается вверх, а острый конец шабера опускается вниз до соприкосновения с поверхностью шлифовального круга. Такие плавные движения шабером производят несколько раз, создавая закругленную поверхность
157
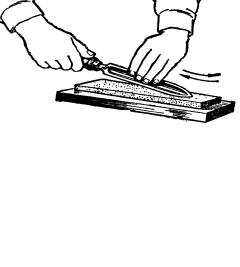
с острыми гранями. Поворачивая шабер второй, а затем третьей гранью, их затачивают аналогично первой грани шабера. Во избежание перегрева и получения прижогов и трещин заточку ведут с охлаждением водой. Шаберы доводят (заправляют) на корундовых шлифовальных брусках, устойчиво закрепленных неподвижно на плите. Поверхность шлифовального бруска смазывают тонким слоем машинного масла. Доводку осуществляют легким нажимом левой руки и подворачиванием правой рукой при одновременном движении боковой грани шабера вдоль шлифовального бруска (рис. 140, б). Остальные грани шабера доводят таким же образом.
а
б
Рис. 140. Заточка на шлифовальном круге (а) и правка на шлифовальном бруске (б) трехгранного шабера
Для шабрения высокой точности шабер дополнительно заправляют на чугунной плите с применением наждачного порошка, разведенного в машинном масле или с нанесенной на плиту пастой ГОИ.
Показателями правильной доводки шабера являются гладкая поверхность режущих кромок шабера и их острота.
158

11.8. Механизация процесса шабрения
Процесс ручного шабрения требует высокой квалификации работников, больших физических усилий, он весьма трудоемок и удлиняет цикл обработки. Одним из путей повышения производительности и снижения затрат живого труда является механизация процесса шабрения. В связи с этим начиная с 50-х годов ХХ века по сегодняшний день делаются попытки механизировать процесс шабрения с целью замены ручного труда машинным. Ниже приведены некоторые из подобных разработок.
Пневматический шабер применяют для мелких работ, связанных с опиловкой и шабрением (рис. 141).
Рис. 141. Пневматический шабер: 1 – шабер-напильник; 2 – цанговый патрон; 3 – поршень; 4 – втулка; 5 – поршневая коробка; 6 – шланг; 7 – турбинка; 8 – пусковой крючок
Перед включением шабера в работу заготовку закрепляют в тисках, затем, наложив напильник на обрабатываемую поверхность, нажимают пусковой крючок 8 и производят обработку. Длина шабера-напильника составляет 200 мм. Шабер делает от 500 до 5000 двойных ходов в минуту.
Шабер с электроприводом, показанный на рис. 142, приво-
дится в действие от электродвигателя 1, подвешенного на тележ-
159
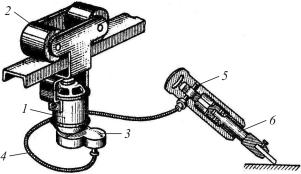
ке 2 к монорельсу. Электродвигатель 1 через редуктор 3, с которым соединен гибкий вал 4, приводит в движение кривошип 5, который сообщает движение шаберу 6.
В шабере с электроприводом вращательное движение гибкого вала, получаемого от электродвигателя, преобразуется в воз- вратно-поступательное движение шабера. Рабочий левой рукой давит на шабер, прижимая его к обрабатываемой поверхности, а правой рукой поддерживает шабер за рукоятку.
Рис. 142. Шабер с электроприводом: 1 – электродвигатель; 2 – тележка; 3 – редуктор; 4 – гибкий вал; 5 – кривошип; 6 – инструмент
На рис. 143 показана стационарная установка для шабрения. Она имеет электродвигатель 1, установленный в кронштейне 2 станины 3. Клиноременная передача 6 передает вращательное движение от электродвигателя 1 с помощью гибкого вала 5 головке 4 с закрепленным в ней шабером.
Практически все механизированные шаберы имеют существенный недостаток, а именно: трудность регулирования режимов обработки; сравнительно сильные толчки; невозможность регулирования усилия, передаваемого шаберу.
В связи с этим механизированные шаберы нашли применение только при черновом (предварительном) шабрении.
160