
книги / Несущая способность сварных соединений
..pdfШ0Х11М2Т (сварной шов выполняли сварочной проволокой того же класса) и сплав АМгб. В результате сварки в сжатом состо янии брусьев получали образцы с радиусом непровара в корке шва р=0,018 ... 0,022 мм (для АМгб) и р=0,02 ... 0,025 мм (для •стали HI0X11M2T). Достоверные значения характеристики мате риалов бс получают экспериментально при р^рэ. Если непровар составляет р > р э, то образцы нельзя использовать для определе
ния бс.
Образцы испытывали на внецентренное растяжение с записью диаграмм нагрузка—смещение Р— V в условиях нормальных и криогенных температур. Величину бс определяли по методикам [52, 116, 152]. Для исследуемой стали при 293 К бс составляет 0,19... 0,21 мм, при 77 К — 0,0125 мм; для (сплава АМгб — соответственно 0,022 и 0,0074 мм.
Определить величину рэ можно на основе данных о ресурсе •пластичности Ар материала в зоне предразрушения. Последний
находят из диаграмм пластичности материалов |
АР(Я) [86\ |
по |
|||||
известному показателю жесткости |
напряженного |
состояния |
Я— |
||||
= ~ |
(<То — |
гидростатическое давление (шаровая часть тензора |
|||||
*i |
|
Tt — интенсивность |
касательных |
напряжений). |
|||
напряжений), |
|||||||
Для определения показателя жесткости напряженного |
состояния |
||||||
в окрестности |
вершины концентратора в образцах типа ЦКТИ |
||||||
использовали |
метод |
линий скольжения. Аналогично |
[98], поле |
||||
линий |
скольжения |
в образце состоит из двух дуг окружности |
'(см. рис. 4.15). Угол, образованный дугами в точке пересечения у вершины концентратора, равен 72°. Показатель жесткости напря женного состояния в окрестности вершины (в точке 0) П = 3,08 |98]. При таком показателе П ресурс пластичности материалов Лр— 0,47 (сталь Н10Х11М2Т) и Лр=0,12 (сплав АМгб). Полагая, что в вершине рассматриваемого концентратора реализуются условия плоской деформации (vo= 0 ), с учетом (4.28) получены приблизительно одинаковые значения эффективной остроты кон центратора рэ= р 0= 0,023 мм для обоих исследуемых материалов. Аналогичные результаты расчетов р9 получены в [117, 140] для низкоуглеродистой стали (р9=ро=0,023 мм) и закаленных ста лей 40Х и 45ХН2МФА (ро=0,025 мм). Полученные значения ро>Ро в вершине непровара для образцов [26] характеризуют критическое раскрытие трещины бс-
Для хрупких или квазихрупких разрушений (см. п. 2.2.2) при определении б0(р) необходимо знать величину бс, получаемую при испытании в условиях заданной температуры. При этом зна чение рэ, определенное экспериментально при нормальной темпе ратуре, используют для поправки на величину радиуса в верши не дефекта.
Сравним полученные данные для определения критического раскрытия трещиноподобного концентратора конечного радиуса (4.29) с известными подходами других авторов. В [75] предло-
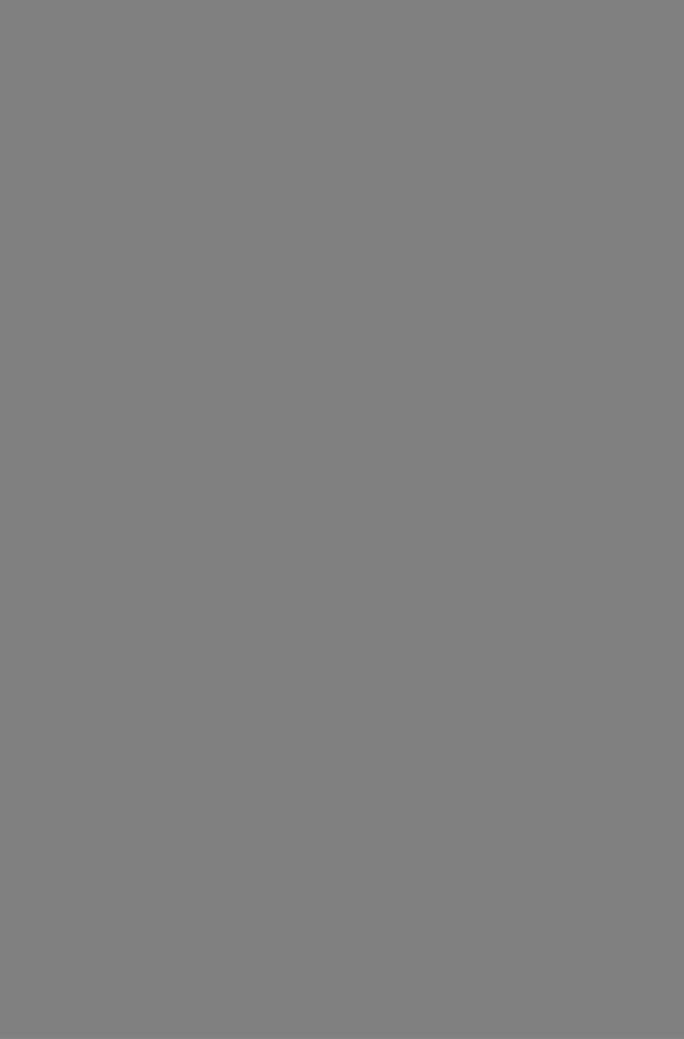
Rue = °т ,+,"[1 +h(=Jfe)’]l- |
,4>2> |
Однако точные данные о величине р0 в литературе отсутству ют. В связи с этим нами [180] на основе данного выражения установлена связь между величиной RMC и зависимостью ресурса пластичности материала от жесткости' напряженного состояния (диаграммой пластичности), отражающей связь предельной сте-
Т а б л и ц а 4.13
Сопротивление микроскопу R HC сталей некоторых марок
|
М атериал |
О’р , |
п ЭКСП |
о |
Р“ ч |
Относит. |
И сточник |
|
|
М П а |
* НС, |
н |
м с, |
погреш |
|||
|
|
|
М Па |
М Па |
ность, % |
|
||
В Ст. |
3 |
кп (состояние |
290 |
1020...1080 |
1140 |
9,6 |
Данные |
|
поставки |
|
авторов. |
||||||
17ГС |
(состояние постав |
360' |
1390 |
1440 |
3,0 |
|
||
ки) |
|
|
|
|||||
17Г1С-У (состояние по |
|
|
|
|
|
|
||
ставки) |
(состояние по |
380 |
1390...1520 |
1440 |
2,9 |
|
||
14Г2АФУ |
405 |
1550 |
1515 |
1,6 |
|
|||
ставки) |
(состояние по |
|
||||||
14Г2САФ |
|
|
|
|
|
|
||
ставки) |
|
370 |
1300... 1350 |
1445 |
7,0 |
|
||
09Г2С |
(состояние постав |
|
|
|
|
|
|
|
ки) |
(термообработка) |
394 |
1500 |
1560 |
4,0 |
|
||
17Г1С |
360 |
1140...1180 |
1346 |
14,0 |
|
|||
17Г1С |
(отжиг,, охлажде |
360 |
1350...1400 |
1415 |
1,0 |
|
||
17Г1С |
270 |
940...980 |
1080 |
10,2 |
|
|||
ние с печью |
»> |
|||||||
ЗОХГСА |
|
680 |
1050 |
1100 |
4,25 |
[87] |
||
М16С |
|
|
200 |
870 |
|
920 |
5,7 |
[87] |
пени интенсивности деформаций сдвига ЛР/ накопленной к момен ту разрушения, с жесткостью напряженного состояния в зоне предразрушения.
Предположим, что в момент разрушения металла пластическая деформация ei=emax сосредоточена в устье концентратора ра диусом ро. Тогда его критическое раскрытие находим из выраже ния [107]
|
|
6c= 2poEmai |
(4.33) |
С учетом |
(4.23) |
|
|
|
|
Клс=Ует ахросгт£. |
(4.34) |
Используя |
(4.25), |
(4.26) и (4.34), выражение для |
определе |
ния сопротивления микросколу преобразуем к виду |
|
||
|
У?«=»т{ |
1 + l n f l + 0 . 1 3 8 ( 5 ^ ) 1 } . |
(4.35) |
MS
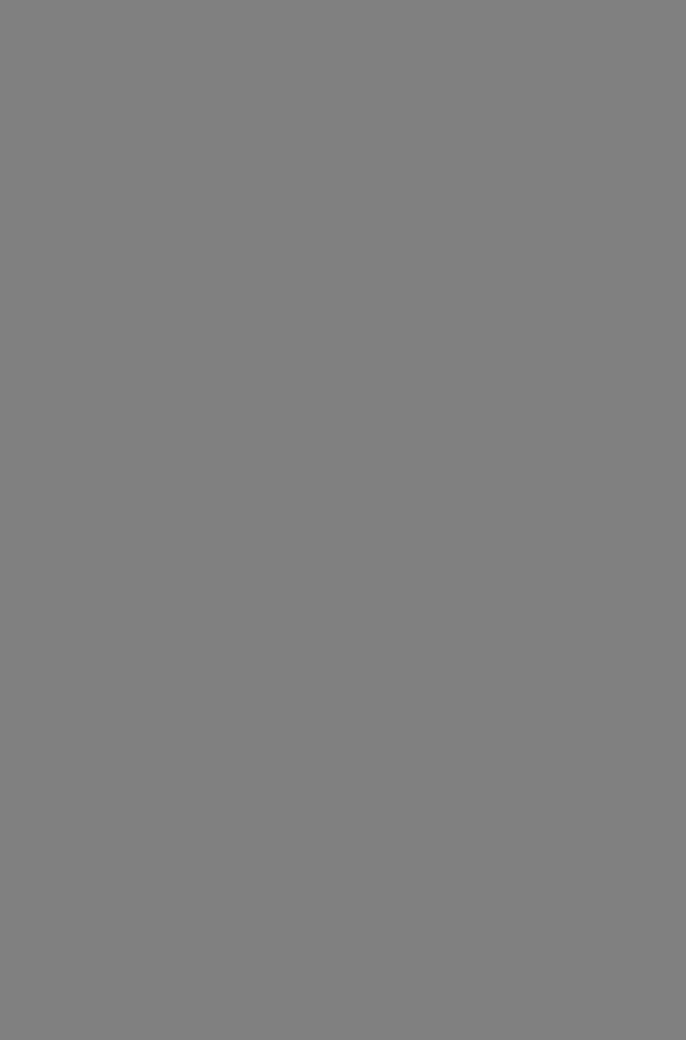
нем усталостной трещины, устанавливали периоды зарождения и распространения трещины (ti и тг). Полученные данные при за данном постоянном нагружении для образцов каждой партии и соответствующей термообработки показали, что режим термооб работки существенно влияет на кинетику роста усталостной трещины.
Так, для образцов после низкого отпуска характерен больший период зарождения трещины (ti=44 мин) и меьший период ее
распространения (тг=12 мин). Для образцов |
после среднего |
от |
||||
пуска наблюдается общее |
повышение периодов |
зарождения |
и |
|||
распространения |
трещины |
соответственно |
(ti= 46 |
мин., тг=; |
||
= 52 мин). И, наконец, для |
образцов после высокого отпуска ус |
|||||
тановлено уменьшение ti и тг, т. е. Т|=32 мин, |
Тг=47 мин. |
|
||||
Учитывая тот факт, что при среднем отпуске 723 К определе |
||||||
на максимальная |
усталостная прочность стали |
(тСуи=98 мин), |
||||
то этот режим был использован при термообработке |
натурных |
|||||
цилиндрических пружин. |
|
|
|
|
|
Несмотря на значительные материальные затраты при созда нии мощной испытательной техники, стендов, устройств, проведе нию усталостных испытаний на натурных деталях уделяется боль шое внимание, поскольку последние более достоверно отражают поведение материала с учетом реальных условийэксплуатации. В нашем случае объектом натурных испытаний были цилиндриче ские пружины, навитые в горячем состоянии механическим путем
из стали 60С2А |
круг 12—4 ГОСТ 14959—79 (0 80 |
мм, L = |
= 377 мм) и круг |
16—4 ГОСТ 7417—75 (0 120 мм, L = |
372 мм). |
Испытаниям подвергали гладкие и надрезанные двух типоразме ров цилиндрические пружины после закалки и отпуска соответ ственно 473 и 723 К. В надрезанных пружинах форма надре за ^/-образная. Его наносили отрезным кругом на третьем витке
снизу под углом а=45° к оси витка шириной |
4 мм и глубиной |
3 мм с радиусом закругления дна р ^ 2 мм. |
*\ |
Опыты на усталостную прочность пружин проводили на много местной установке, разработанной на базе двигателя внутреннего сгорания грузового автомобиля ЗИЛ-131 с У-образным расцололожением восьми цилиндров с поршнями в блоке, закрепленном на резиновых подушках к раме сварной конструкции *.
Вращение коленчатого вала двигателя осуществляется от электромотора через муфту сцепления. Рабочие стаканы для помещения в них испытываемых пружин крепятся механически сверху блока в местах отверстий, где перемещаются в возвратно поступательном направлении рабочие поршни. Внутри стаканов находятся нижние направляющие вставки, которые по скользя щей посадке входят в отверстия блока до соприкосновения с тор цевыми поверхностями поршней. Сверху стаканов прикреплены
* Предложенная конструкция установки работает во Львовском политех ническом институте (кафедра технологии машиностроения).
крышки с |
верхними |
направляющими вставками, перемещение |
||||||
которых осуществляется от прижимных винтов. |
|
|
|
|||||
Испытание пружин осуществляли таким образом. Установлен |
||||||||
ные в цилиндрические стаканы две |
гладкие |
и |
две надрезанные |
|||||
пружины после двух |
режимов |
термообработки |
(отпуска 473 и |
|||||
723 К) перед циклическим деформированием |
подвергали |
предва |
||||||
рительному |
сжатию |
(QCjK=5203 |
Н, |
виток 0 |
16 |
мм) |
и |
(Q « K= |
= 4403 Н, |
виток 0 12 мм) верхними |
вставками |
от |
прижимных |
винтов, рассчитанному согласно тарировочных диаграмм сжатия для хода поршня (/= 100 мм) от верхней до нижней точки цик ла. Пуском электромотора в процессе эксперимента фиксировали количество циклов сжатия или время циклического деформиро вания до полной поломки каждой пружины с соответствующей термообработкой.
Результаты испытаний, полученные при частоте деформиро вания w — 5С_| на упомянутой установке, показали различную долговечность до поломки как гладких, так и надрезанных пру жин для двух режимов термообработки. Она минимальна (тсУм =
= |
154 и 125 мин) для надрезанных витков 0 16 мм после отпус |
|||
ка |
473 К и максимальна (тСУм=225 |
и |
198 мин) |
для надрезан |
ных витков 0 12 мм после отпуска |
723 К. Для |
гладких витков |
||
соответственно тсум= 273 и 205 мин и тсУм=286 и 248 мин. |
||||
|
Подтверждением сказанному служит |
также |
визуальный ос |
мотр изломов витка пружины. Для отпуска 473 К он светло-се рого цвета, характерного для хрупкого разрушения, а для отпус ка 723 К излом темно-серого цвета, присущий для квазихрупкого разрушения.
Таким образом, различная сопротивляемость разрушению пружинной стали 60С2А наблюдается особенно в присутствии острых концентраторов^ трещин, что связано с формированием мелкозернистой игольчатой мартенситной структуры (закалка и отпуск 473 К ),
Закалка и отпуск 723 К формирует стохастическую структуру, способную до 5 0 . . . 60% повысить сопротивляемость разрушению и при этом практически не снизить упругих свойств данной ста ли.
Усталостные испытания натурных цилиндрических пружин на ©тнулевое циклическое сжатие подтвердили результаты испыта ний лабораторных образцов. Следовательно, эту теромообработку можно рекомендовать при производстве пружин для работы в более тяжелых условиях их эксплуатации.
На основе проведенных исследований и обнаруженных закономер
ностей установлено, что влияние |
механической неоднородности |
на напряженно-деформированное |
состояние и несущую способ |
ность сварных соединений весьма существенно. Без учета указан ного фактора невозможно правильно оценить работоспособность сварных соединений и конструкций, выбрать их оптимальные гео метрические параметры, разработать технологию получения со единений, определить допустимый уровень дефектности сварных швов.
Метод оценки вязкой прочности механически неоднородных сварных соединений открывает широкие возможности для их ра ционального конструктивно-технологического проектирования. Он позволяет наряду с технологическими и экономическими сооб ражениями по назначению тех или иных типов разделки кромок, геометрических параметров стыков, величин зазоров под сварку, а также режимов сварки и термообработки учитывать уровень предельной несущей1способности сварных соединений. Последнее делает подход к назначению основных конструктивно-технологи ческих параметров научно обоснованным. На его основе выбор различных технологических вариантов, например назначение раз делки кромок под сварку или пайку, необходимо производить с учетом того, что более высокие прочностные свойства при одина ковой степени механической неоднородности соединений и равных относительных зазорах между стыкуемыми кромками и углах их скоса имеют соединения из пластин с шевронной мягкой про слойкой и далее в порядке снижения прочности с прямоугольной, косой, X- и V- образными мягкими прослойками. Для соединений с большой поперечной жесткостью, например для толстостенных труб с кольцевым стыком, предпочтительны шевронная и наклон ная (косая) мягкие прослойки.
Важными для практики будут также приведенные оптималь ные геометрические размеры зазоров под сварку или пайку, ве личины скоса свариваемых кромок, при которых в случае меха нической неоднородности соединений можно достичь их равнопрочности с основным, более прочным металлом, рекомендации по выбору присадочного для сварки (или пайки) металла и др.
На основе установления влияния компактности поперечного сечения на несущую способность сварных соединений предложена методика определения механических свойств крупногабаритных сварных элементов конструкций по результатам испытаний выре заемых из них лабораторных образцов. Данная методика может служить основой для создания нормативов по проведению стати-
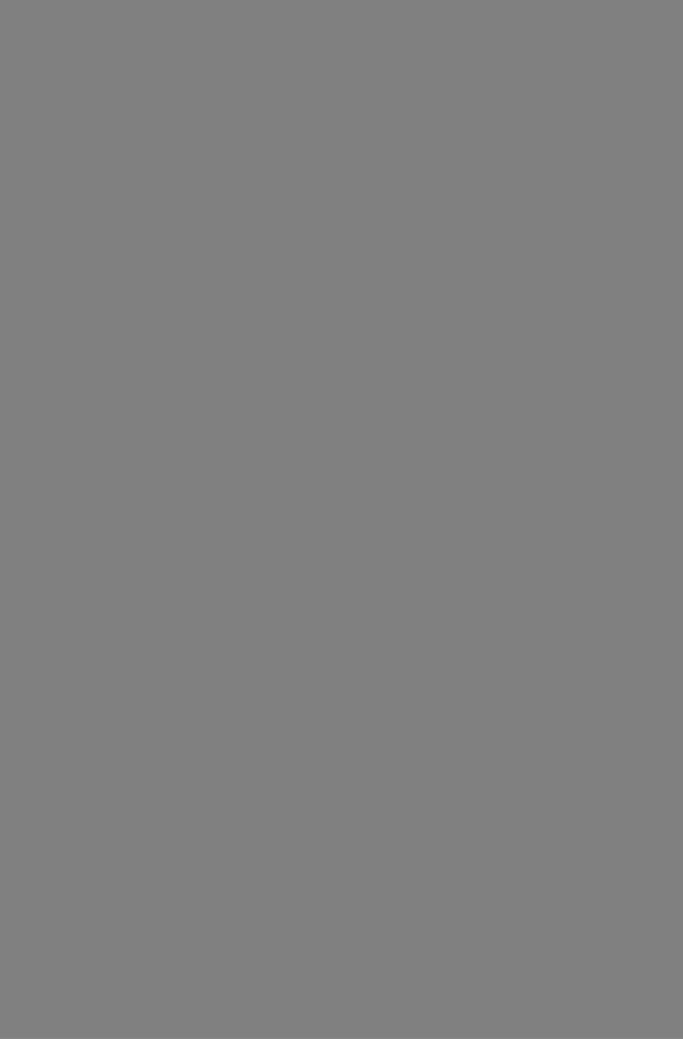
На стадии контроля качества:
— получать научно обоснованные данные для принятия реше ния о вырезке или исправлении обнаруженных дефектов сварки в статически нагруженных конструкциях либо о возможности оста вить дефект определенных (допустимых) размеров без исправ ления;
—оценивать степень опасности дефектов при диагностике сварных конструкций по характеру возможного разрушения и уровню средних предельных напряжений;
—разрабатывать дифференцированные требования к уровню
истабильности механических характеристик основного металла и металла различных локальных зон неоднородных соединений для
получения интегральных свойств последних;
— для сварных стыковых, тавровых и нахлесточных соедине ний, выполненных с неполным проплавлением присоединяемых пластин, разрабатывать ряд мероприятий по снижению опасности непровара путем увеличения (до необходимых расчетных разме ров) радиуса в его вершине.
Отдельные разработки, предложенные авторами в настоящей монографии, внедрены на ряде предприятий транспортного ма шиностроения, судостроения, черной металлургии и в строитель стве и дают значительный экономический эффект.
Заказчики могут обращаться за консультациями или полу чением необходимой документации на разработки авторов по та ким адресам:
290046 Львов-13, ул. Мира, 12. Политехнический институт, ка федра технологии машиностроения.
454080 Челябинск, просп. Ленина, 76.
Технический университет, кафедра сварки и сварочного произ водства.
СПИСОК ЛИТЕРАТУРЫ
1.Акулов Г. П., Пашкевич М. Ф. К исследованию зарождения и развития зон деформаций у вершины надреза методом голографической интерфероме трии//Пробл. прочности. 1978. № 5. С. 74—77.
2.Аммосов А. П., Попов В. В., Ларионов В. П. О разрушении сварного
соединения/ / Физ.-хим. механика материалов. |
1982. № 4. С. 116—118. |
|
3. |
Андрейкив А. Е. Разрушение квазихрупких тел с трещинами при слож |
|
ном напряженном состоянии. К-» 1979. |
|
|
4. |
Андрейкив А. Е. Пространственные задачи теории трещин. K.i 1982. |
|
5. |
Антонов А. А. Разработка методики и оборудования голографического |
|
контроля остаточных напряжений в сварных |
соединениях/ / Сварочное пр-во. |
|
1983. № 12. С. 26—28. |
|
6.Астафьев А. С. Навьев В. С. Сварка термически упрочненной стали // Сварочное пр-во. 1965. № 3. С. 1—4.
7.Бакши О. А. О напряженном состоянии мягких прослоек в сварных со
единениях при растяжении (сжатии) //Тр. Челябинск, политезн. ии-та, 1965, Вып. 33. Вопр. сварочн. пр-ва. С. 5—26.
8.Бакши О. А. Деформационная способность (пластичность) сварных со единений и пути ее регулирования//Тр. Челябинск. политехи, ин-та. 1968. Вып. 63. Вопр. сварочн. пр-ва. С. 3—19.
9.Бакши О. А., Зайцев Я. Л., Гооге С. Ю. Сопротивляемость хрупким раз
рушениям сварных нахлесточных соединений с лобовыми швами/ / Автомат, сварка. 1984. № 8. С. 19—23.
10. Бакши О. А., Зайцев Н. Л ., Гооге С, Ю. Оценка прочности тавровых соединений с угловыми швами, находящимися к хрупком состоянии, по крите
риям механики |
разрушения//Сварочн. пр-во. 1981. № |
7. С. 13— 16. |
И. Бакши О. А ., Зайцев Н. Л., Маковецкий В. А. Несущая способность |
||
лобовых швов |
нахлесточных • соединений // Автомат, |
сварка. 1972. № 6. |
С.34—37.
12.Бакши О. А., Зайцев Н. Л., Матвеев М. И. Исследование напряжен но-деформированного состояния и прочности тавровых соединений с лобовыми швами // Тр. Челябинск, политехи, ин-та. 1978. Вып. 203. Вопр. сварочн. пр-ва.
С.63—70.
13.Бакши О. А., Зайцев Н. Л., Шрон Л. Б. Влияние геометрии угловых швов на коэффициенты концентрации и градиенты напряжений в тавровых со единениях/ / Сварочн. пр-во. 1982. № 8. С. 3—5
14. Бакши О. А., Зайцев Я. Л., Шрон Р. 3. Повышение несущей способ
ности |
нахлесточных и тавровых соединений с лобовыми |
швами // Сварочн. |
пр-во. |
1977. № 9- С. 3—5. |
|
15. Бакши О. A.j Зайцев Я. Л., Шрон Р. 3. Прочность нахлесточных со единений с лобовыми швами//Тр. Челябинск, политехи, ин-та. 1975. Вып. 168. Вопр сварочн. пр-ва. С. 62—69.
16. Бакши О. А., Купершляк-Юзефович Г. М. О работе сварных стыковых соединений при импульсном нагружении/ / Сварочн. пр-во. 1965. № 1. С. 2—4.
17. Бакши О. А., Моношков А. Я. Анисимов Ю. И. К вопросу о работо способности сварных соединений при низкой температуре и ударном нагруже нии//Тр. Челябинск, политехи, ин-та. 1968. Вып. 63. Вопр. сварочн. пр-ва.
С.57—62.
18.Бакши О. А., Шахматов М. В., Ерофеев В. В. Напряженно-деформи
рованное состояние сварных соединений с дефектом в центре мягкого ш ва// Автомат, сварка. 1982. № 3. С. 9—11.
19. Бакши О. А., Шрон Р. 3. О расчетной оценке прочности сварных со единений с мягкой прослойкой/ / Сварочн. пр-во. 1971. № 3. С. 3—5.