
книги / Эксплуатация, техническое обслуживание и ремонт горных машин калийных рудников
..pdf
корпуса электрооборудования оказываются под напряжением. На эти случаи для защиты людей от поражения электрическим током предусматривается преднамеренное соединение с землей металлических корпусов электрооборудования, а также других металлических частей, которые могут оказаться под напряжением при нарушении изоляции токоведущих частей. Такое соединение выполняется с помощью заземляющих проводников и заземлителей. Так как электрическое сопротивление заземлителя намного меньше сопротивления человека, ток, в соответствии с большим потенциалом, обходя человека, уходит в землю.
В электроустановках напряжением выше 1000 В в сети с заземленной нейтралью допустимое сопротивление заземляющего устройства в соответствии с правилами эксплуатации электроустановок [5] должно быть не более 4 Ом в любое время года, то есть Rдоп ≤ 4 Ом. Тип и параметры заземлителя выбираются заранее, исходя из общей схемы обвязки защиты от растекания электрического тока.
Расчетное сопротивление заземлителей определяется в соответствие с формой и расположением стержня:
– вертикальный протяженный заземлитель трубчатого или уголкового сечения:
R0 = |
|
ρ |
э |
|
|
|
|
2L |
|
+ 0,5 |
7T + 4L |
|
|
или |
|||||||||
|
|
|
|
ln |
|
з |
|
|
з |
|
|
||||||||||||
|
|
|
|
|
|
|
|
|
|
|
|
||||||||||||
|
|
|
|
|
|
|
|
|
|
||||||||||||||
|
2πLз |
|
|
d |
|
|
|
7T + Lз |
|
|
|
|
|
||||||||||
|
|
|
|
|
|
|
|
|
|
|
|
||||||||||||
R0 = |
ρ |
э |
|
|
|
|
2L |
|
|
+ 0,5 |
|
7T + |
4L |
|
; |
||||||||
|
|
|
ln |
|
|
|
з |
|
|
|
|
|
|
з |
|||||||||
2πL |
|
|
0,95b |
7T + |
L |
||||||||||||||||||
|
|
|
|
|
|
|
|
|
|
|
|||||||||||||
|
|
|
|
з |
|
|
|
|
|
|
|
|
|
|
з |
|
|
– горизонтальный протяженный заземлитель трубчатого или уголкового сечения:
R0 = |
ρэ |
ln |
Lз |
|
или R0 = |
ρэ |
ln |
1,5Lз |
; |
πLз |
|
πLз |
|||||||
|
|
dT |
|
|
bT |
|
– пластинчатыйзаземлитель(расположенныйгоризонтально):
51
R0 = |
ρэ |
|
− |
2 |
|
D |
|
|
|
1 |
|
arcsin |
|
|
, |
||
|
π |
|
||||||
|
4πD |
|
|
3T |
|
где ρэ – эквивалентное удельное сопротивление почвы, в которую установлен заземлитель,
ρэ = ρψ,
где ρ – удельное сопротивление грунта, Ом·м. Принимается в соответствии с параметрами грунта, приведенными в табл. 1.4; ψ – коэффициент климатических условий, выбираемых по табл. 1.4; Lз – длина заземляющего стержня, м; d – диаметр стержня, м; D – ширина пластины, м; b – ширина полки уголка, м; T – расстояние от поверхности почвы до заземлителя, м. Принимается с учетом особенности грунта. Распространено углубление заземляющих стержней на глубину 0,6…1,0 м.
|
|
|
|
Таблица 1.4 |
|||
|
Параметры грунта |
|
|
|
|||
|
|
|
|
|
|
|
|
|
Удельное сопротивление грунта, ρ, Ом·м |
Климатический |
|||||
|
|
|
|
коэффициент* |
|||
Грунт |
при |
возможные |
|
|
|
|
|
влажности |
границы |
рекомендовано |
ψ1 |
ψ2 |
ψ3 |
||
|
|||||||
|
грунта |
колебания |
для расчетов |
||||
|
10…12 % |
значений |
|
|
|
|
|
Торф |
20 |
– |
20 |
1,4 |
1,1 |
1,0 |
|
Чернозем |
200 |
9…53 |
30 |
– |
1,32 |
1,2 |
|
Садовая земля |
40 |
30…60 |
50 |
– |
1,3 |
1,2 |
|
Глина |
40 |
8…70 |
60 |
1,6 |
1,3 |
1,2 |
|
Суглинок |
100 |
40…150 |
100 |
2,0 |
1,5 |
1,4 |
|
Мергель |
250 |
200…300 |
250 |
– |
– |
– |
|
Известняк |
300 |
150…400 |
300 |
2,0 |
1,5 |
1,4 |
|
Песчаник |
700 |
400…2500 |
500 |
2,4 |
1,56 |
1,2 |
Примечание: * ψ1 – очень влажный грунт; ψ2 – грунт средней влажности; ψ3 – сухойгрунт.
Для обеспечения требуемого сопротивления заземляющей линии может быть установлено несколько заземлителей, которых должно быть не менее двух:
52
n = |
R0 |
|
, |
R K |
|
||
|
доп |
исп |
где Kисп – коэффициент использования набора заземлителей. Выбирается ориентировочно исходя из предварительного числа электродов соотношения R0/Rдоп, по табл. 1.5.
|
|
Таблица 1.5 |
|
Коэффициент использования набора заземлителей |
|||
|
|
|
|
Отношение расстояния |
Числоэлектродов |
Kисп |
|
между вертикальными |
|||
в ряду |
|||
электродами к их длине a / l |
|
||
|
|
||
|
4 |
0,66…0,72 |
|
|
6 |
0,58…0,65 |
|
|
10 |
0,52…0,58 |
|
1 |
20 |
0,44…0,50 |
|
|
40 |
0,38…0,44 |
|
|
60 |
0,36…0,42 |
|
|
100 |
0,33…0,39 |
|
|
4 |
0,76…0,80 |
|
|
6 |
071…0,75 |
|
|
10 |
0,66…0,71 |
|
2 |
20 |
0,61…0,66 |
|
|
40 |
0,55…0,61 |
|
|
60 |
0,52…0,58 |
|
|
100 |
0,49…0,55 |
Длина опоясывающей заземлители полосы:
L = a (n – 1),
где a – расстояние между вертикальными заземлителями, м. Вторым эффективным способом обеспечения безопасности
работы с оборудованием, является его зануление. Зануление – это преднамеренное электрическое соединение с нулевым защитным проводником металлических нетоковедущих частей, которые могут оказаться под напряжением.
53
Принцип работы зануления: если напряжение (фазовый провод) попадает на соединенный с нулем металлический корпус прибора, происходит короткое замыкание. Сила тока в цепи при этом увеличивается до очень больших величин, что вызывает быстрое срабатывание аппаратов защиты (автоматические выключатели, плавкие предохранители), которые отключают линию, питающую неисправный прибор.
Зануление осуществляется специально предназначенными для этого проводниками. При однофазной проводке – это, например, третья жила провода или кабеля.
Помимо быстрого отключения неисправной линии от электроснабжения, благодаря тому, что нейтраль заземлена, зануление обеспечивает низкое напряжение прикосновения на корпусе электроприбора. Это исключает вероятность поражения током человека. Поскольку нейтраль заземлена, зануление можно рассматривать как специфическую разновидность заземления.
54
2. СИСТЕМЫ ТЕХНИЧЕСКОГО ОБСЛУЖИВАНИЯ И РЕМОНТА ГОРНЫХ МАШИН КАЛИЙНЫХ РУДНИКОВ
2.1. Определение ремонта. Этапы ремонта
Проблемы ремонта оборудования решает теротехнология – это наука об обслуживании техники. Она обобщает и систематизирует принципы и элементы технического обслуживания и ремонта с учетом морального износа. Теротехнология – технология обеспечения эффективного функционирования оборудования в течение всего срока службы. Она увязывает это обеспечение с качеством проектирования, монтажа и эксплуатации оборудования.
В процессе эксплуатации оборудования детали постоянно изнашиваются и изменяются под влиянием внешних нагрузок, внутренних технологических напряжений и коррозионного воздействия. Этот износ характеризуется отклонениями размеров и формы деталей, изменением механических и химических свойств поверхностных и внутренних слоев деталей. Совокупность таких изменений при достижении определенных границ называется эксплуатационным повреждением детали. Оно устраняется ремонтом или заменой данного узла. Для удлинения срока работы деталей необходимы:
а) переход при проектировании от приближенных расчетов на статическую прочность к расчетам, учитывающим усталость при повторно переменных нагрузках;
б) учет явлений концентрации напряжений; в) применение износоустойчивых материалов; г) поверхностное упрочнение деталей и т.п.
Ремонт оборудования включает в себя комплекс мероприятий, осуществляемых с целью восстановления нормальной работоспособности деталей, узлов, агрегатов. Ремонты состоят из следующих этапов:
–разборка машины и ее дефектация;
–ремонтная обработка детали;
55
–сборка узлов и машин с проверочными операциями;
–испытание машин и аппаратов.
Технологическое обслуживание – операция или комплекс операций по подготовке изделия к использованию по назначению, хранению и транспортированию и приведению его в исходное состояние после этих процессов. Типовые операции технологического обслуживания:
–настройка машины на правильное функционирование (наладка);
–заправка технологическими материалами;
–установка вспомогательных приспособлений;
–очистка машины после завершения работы и др. Техническое обслуживание может осуществляться при ис-
пользовании по назначению, ожидании, хранении и транспортировании.
Ожидание – нахождение изделия в состоянии готовности для использования по назначению.
Система технического обслуживания и ремонта (СТОиР) –
комплекс взаимосвязанных положений и норм, определяющих организацию и порядок проведения работ по техническому обслуживанию (ТО) и ремонту для заданных условий эксплуатации и показателейкачества. СтруктураСТОиРпредставленанарис. 2.1.
Различают три основные системы организации технического обслуживания и ремонта горных машин и оборудования.
1. Обслуживание по фактическому техническому состоянию (послеосмотровая) – обязательные периодические осмотры машины в строго постоянные сроки. Данная система организации технического обслуживания и ремонта характеризуется широким применением средств технического диагностирования и приборного контроля. По результатам проведенных осмотров определяют техническое состояние машин и назначают сроки и виды ремонта. В рабочем состоянии машины поддерживают проведением текущих ремонтов, различных по объему.
56
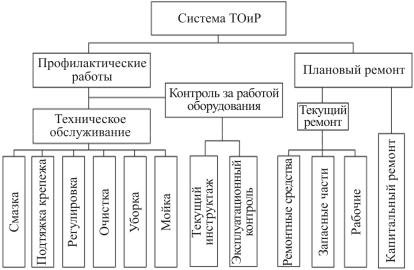
Рис. 2.1. Структура системы технического обслуживания и ремонта
2.Система планово-предупредительного ремонта (ППР) – проведение периодических осмотров и ремонтов через определенные промежутки времени с учетом условий работы машины и
еесостояния. Такая СТОиР применяется для машин, работающих
впеременном режиме. Ремонтные мероприятия разделяют на три группы: межремонтное техническое обслуживание, текущие и капитальные ремонты.
3.Реактивная система – ремонт осуществляется по факту возникновения отказа.
Наибольшее распространение на калийных рудниках получила планово-предупредительная СТОиР. Обслуживание и ремонт производятся силами ремонтной службы и рабочими, эксплуатирующими обслуживаемую технику по графику, являются обязательными, независимо от состояния оборудования. В этом случае ТО нумеруют в порядке возрастания их периодичности
(ТО1, ТО2).
57
2.2. Система планово-предупредительного ремонта
Безотказность машин ухудшается по мере эксплуатации. При определенной отработке ресурса и техническом состоянии эксплуатация машин без капитального ремонта нецелесообразна из-за высоких затрат на текущие ремонты. При сохраняющейся общей тенденции увеличения разноресурсности составных частей машин в машиностроении применяют такой принцип их создания, который предусматриваетзамену иливосстановлениесоставныхчастей.
Для поддержания в рабочем состоянии технологического оборудования необходим комплекс организационных и технических мероприятий по обслуживанию и ремонту машин и оборудования. Таким наиболее распространенным комплексом является система планово-предупредительного ремонта. При этом мероприятия по обслуживанию и ремонту оборудования регламентированы и проводятся по заранее составленному плану для обеспечения безотказной работы оборудования. Цели, которые достигаются при реализации системы планово-предупредительных ремонтов (ППР) следующие:
–предупреждение аварий оборудования;
–возможность выполнения ремонтных работ по плану, согласованному с планом производства;
–своевременная подготовка запчастей материалов и минимальный простой оборудования в ремонте.
Для каждого конкретного производства система ППР реализуется в виде графика, составляемого на один год службой главного механика. В графике на каждую единицу основного оборудования указываются виды ремонта (Т – текущий, К – капитальный) и сроки проведения их по месяцам. Также предусматриваются нормативы времени на производство ремонтных работ по каждому виду ремонта (T1 – первый текущий ремонт; T2 – второй текущий ремонт) и указываетсяисполнитель(ремонтнаябригада).
Текущий ремонт – ремонт, необходимый для обеспечения или восстановления работоспособности изделия, состоящий в
58
замене или восстановлении основных частей. В него входит повторение всех операций ТО: частичный разбор машин и узлов с наибольшим износом; очистка и промывка всех разобранных деталей; проверка зазоров в сопрягаемых деталях, замена изношенных шестерен, крепежа, сальников; ремонт предохранительных устройств, сборка разборных узлов, опробование на холостом ходу и т.д.; выявление деталей, которые должны заменяться при очередном ремонте. Текущий ремонт осуществляется силами ремонтной службы и эксплуатационного персонала в сроки, предусмотренные графиком.
Капитальный ремонт необходим для восстановления исправности и полного или близкого к полному восстановлению ресурса оборудования с заменой или восстановлением любых его частей, включая базовые.
Перед капитальным ремонтом должны быть проведены подготовительные работы: сооружения лесов, изготовление фланцев, получение сложных узлов с машиностроительных заводов. Для капитального ремонта разрабатывается проект проведения ремонта, который включает следующие этапы:
–подготовку техдокументации (чертежи оборудования, ремонтные чертежи);
–описание технологии ремонта;
–описание и подготовку ремонтной оснастки;
–составление дефектной ведомости.
Капитальный ремонт финансируется из амортизационных отчислений. После капитального ремонта оборудование сдается по акту комиссии в составе главного механика, инженераэнергетика, специалиста по охране труда и промышленной безопасности и начальника производства. Следует отметить, что при планировании ремонтов с длительной остановкой оборудования, особенно капитального ремонта, предусматривают проводить эти мероприятия в теплое время года, так как часть оборудования находится на открытых площадках.
59
2.3. Структура и расчет графика планово-предупредительных ремонтов
Месячный график плановых ремонтов составляется на основании годового графика, в обязательном порядке указывается трудоемкость по каждому виду ремонта и исполнители.
При составлении плана учитывается межремонтный цикл – это время работы оборудования между двумя капитальными ремонтами. В ремонтный цикл входят, кроме T1, T2 и K, также и техническое обслуживание (ТО).
Приспособленность различных типов машин к ТО определяется коэффициентом технического обслуживания Kт.о. и рассчитывается по формуле
Kт.о. = Tт.о. ,
Tм
где Тт.о. – время, потраченное на ТО; Тм – время наработки за период эксплуатации. Обычно этот коэффициент находится в пре-
делах Kт.о. = 0,14…0,2.
Нормативами на ремонт оборудования вводится еще два коэффициента: Кп. – коэффициент использования парка по рабочему времени; Ки.м. – коэффициент использования оборудования по машинному времени
Kи.м = Tм ; Kп = Tэ ,
Tp Tк
где Тэ – время эксплуатации оборудования в течение смены; Тк – календарное время нахождения оборудования на предприятии.
Обычно значение коэффициента Ки.м. находится в пределах от 0,6 до 1. Например, если Ки.м. = 0,8, а количество однотипных машин на предприятии Nм = 20, то количество одновременно работающих машин Np.м.
Nр.м = Kи.м Nм = 0,8 20 =16.
60