
учебник по ОПОВ
.pdf2.8 Химические реакторы
Технологические схемы химических процессов включают большое количество аппаратов и устройств, предназначенных для подготовки исходного сырья, транспортировки различных жидких, газообразных и твердых продуктов от одного аппарата к другому, очистки продуктов реакции от побочных примесей, упаковки готовой продукции предприятия. Во всех перечисленных устройствах проводятся процессы подготовки, нагрева или охлаждения, смешения или разделения начальных, промежуточных или конечных продуктов, без чего не может быть осуществлена химическая переработка. Однако основным элементом установки для проведения химико-технологического процесса является аппарат, в котором происходит химическая реакция. Такой аппарат называется химическим реактором. К химическим реакторам относятся только такие аппараты, в которых происходит химическое превращение исходных продуктов в вещества, получение которых является целью технологического процесса.
Во всех реакторах, как правило, помимо химического превращения протекают физические процессы тепло- и массообмена. Для осуществления этих процессов реакторы снабжаются специальными приспособлениями - мешалками и теплообменниками различных конструкций. Таким образом, химические реакторы представляют собой комплексные аппараты, состоящие из реакционного объема, в котором происходит химическое взаимодействие, и специальных приспособлений и устройств для осуществления процессов тепло- и массообмена.
Конструкции реакционных объемов различных реакторов зависят от типа химической реакции, теплового и гидродинамического режимов работы реактора, способа и отвода реагентов. Количество типов перемешивающих устройств и теплообменников также велико. В связи с этим существует большое количество типов реакторов, в которых сочетаются различные конструкции реакционных объемов и вспомогательных устройств. Кроме того, один и тот же химико-технологический процесс, требующий определенных условий, может быть реализован в реакторах различной конструкции. Этим объясняется тот факт, что принятая классификация химических реакторов основана не только на конструктивных особенностях аппаратов для проведения химической реакции, но и на способах ведения технологического процесса.
200

2.8.1 Классификация химических реакторов
Химические реакторы классифицируются по ряду признаков:
По агрегатному состоянию реагирующих веществ различают:
реакторы гомогенные и гетерогенные. В гомогенных реакторах в процессе участвует только одна фаза: газовая или паровая, жидкая или твердая. В гетерогенных реакторах в процессе участвует несколько фаз. Эти реакторы бывают газо-фазными, жидкофазными и газожидкостными.
По способу организации процесса реакторы бывают:
непрерывного, полунепрерывного, периодического действия.
Вреакторах полунепрерывного или полупериодического действия один из реагентов поступает непрерывно, а второй периодически, или же реагенты подаются периодически, а продукты реакции удаляют непрерывно. Выравнивание концентраций компонентов достигают непрерывным перемешиванием.
Вреакторе непрерывного действия подвод исходных веществ и удаление продуктов реакции из аппарата осуществляются непрерывно. Реактор работает в стационарном режиме, при котором значения всех технологических параметров, в том числе концентраций компонентов, температуры и давления, в отдельных точках аппарата не изменяются во времени.
По режиму движения реакционной среды реакторы делятся на:
реакторы смешения и реакторы вытеснения.
Вреакторах смешения происходит непрерывное перемешивание реакционной смеси, при котором элемент объема потока исходных веществ, поступающего в реактор, мгновенно перемешивается с содержимым реактора, концентрация веществ в этом объеме резко меняется от состава питания до состава смеси в реакторе. Аппараты, в которых осуществляется такие условия, называются реакторами идеального смешения.
Вреакторах вытеснения любой элемент объема потока движется через аппарат с постоянной скоростью, не смешиваясь с соседними, а вытесняя их. Состав элемента объема изменяется последовательно по длине реактора вследствие химическоой реакции. Такие аппараты называются реакторами идеального вытеснения.
По тепловому режиму реакторы делятся на: изотермические,
адиабатические и политропные.
Изотерические реакторы работают при постоянной температуре, которая сохраняется во всех точках реакционного объема. Для осуществления условий изотермичности подводят или отводят определенное количество тепла через поверхность теплообмена в форме змеевика, рубашки.
201
Адиабатические реакторы работают практически без теплообмена с внешней средой. Это достигается путем теплоизоляции наружной поверхности реактора.
Политропные реакторы характеризуются тем, что их тепловой режим определяется не только собственным тепловым эффектом процесса, но и теплотехническими и конструктивными факторами аппарата.
По величине давления в реакционном объеме различают: реакторы, работающие под вакуумом, при атмосферном (или близком к нему) давлении и под высоким давлением (выше 10 МПа).
По конструктивным особенностям - классификация реакторов объединяет всю реакционную аппаратуру в следующие группы:
емкостные реакторы;
трубчатые реакторы
колонные реакторы;
реакторы теплообменного типа (печи)
По способу размещения катализатора в рабочем объеме реактора:
с неподвижным слоем катализатора;
с движущимся слоем катализатора;
с псевдоожиженным слоем катализатора.
2.8.2 Реакторы вытеснения
В реакторах вытеснения химическое взаимодействие осуществляется при движении реагентов в трубах.
Реактор вытеснения характеризуется большим отношением длины к диаметру и не имеет никаких механических приспособлений для перемешивания потока в реакционном объеме. В реакторе вытеснения любой элемент объема потока, непрерывно протекающего через аппарат, движется с постоянной скоростью, не смешиваясь с соседними элементами потока. По мере движения элемента потока вдоль реактора в нем происходит изменение концентраций взаимодействующих веществ.
На входе в реактор (рис.2.8.1.) состав элемента потока 1 соответствует составу исходных продуктов, элемент 2 на выходе из реактора содержит только продукты химического превращения. При движении по реактору элемент объема подобно поршню вытесняет все, что находится перед ним, поэтому такой аппарат называется часто реактором с полным
вытеснением или реактором идеального вытеснения.
202

Рис.2.8.1 Реактор вытеснения: 1, 2 – элементы объема потока
В реакторе с полным вытеснением скорость химической реакции изменяется по длине реактора, т. е. меняются концентрации взаимодействующих веществ. Если расход исходных компонентов на входе не меняется, то в каждой точке реактора скорость реакции строго постоянна, так как состав реакционной смеси в данной точке реактора не изменяется во времени. Поэтому при неизменном входном потоке реактор вытеснения непрерывного действия работает в стационарном режиме.
Степень превращения исходных веществ в продукты реакции зависит от времени пребывания компонентов в реакторе. Время Ʈ(с) пребывания реакционной смеси в реакторе вытеснения находят делением длины реактора L (м) на линейную скорость потока W (м/с):
|
´L |
(2.8.1) |
|
W |
|||
|
|
Величина Ʈ тем больше, чем больше длина реактора L и чем меньше скорость потока W. При проектировании и расчете реакторов скорость потока выбирают из соображений минимальных денежных затрат на сооружение реактора.
На практике приблизиться к режиму идеального вытеснения позволяет применение труб малого диаметра и большой длины. Снаружи эти реакторы могут быть снабжены теплообменными устройствами в виде рубашки.
Достоинствами таких реакторов является высокая интенсивность смешения и возможность эффективного теплообмена. К недостаткам можно отнести трудности, возникающие при необходимости дополнительного ввода компонентов в процессе реакции.
Указанные реакторы применяют для проведения гомогенных и гетерогенных реакций, например синтеза аммиака и метилового спирта, хлорирования этилена и др.
2.8.3 Реакторы смешения
Реактор смешения представляет собой некоторый объем, в котором происходит непрерывное перемешивание реакционной смеси одним из известных способов: механическим, пульсационным, пневматическим перемешиванием газов или циркуляционным перемешиванием жидкости.
203
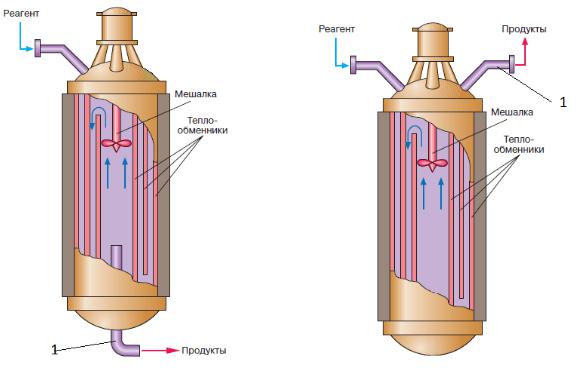
Элемент объема потока исходных веществ, поступающий в реактор через питающий трубопровод, мгновенно перемешивается с содержимым реактора. Состав элемента, т. е. концентрация веществ в этом элементе, резко изменяется от состава питания до состава смеси в реакторе. Чем выше интенсивность перемешивания, тем ближе такой реакционный аппарат к
реактору с полным перемешиванием или реактору идеального смешения.
Реактор смешения может быть аппаратом периодического действия (рис.2.8.2.), в котором перерабатываются определенные порции продуктов, либо аппаратом непрерывного проточного действия (рис.2.8.3.). Последний отличается от реактора периодического действия расположением выходного патрубка 1, который позволяет непрерывно отводить продукты реакции из реактора.
Рис.2.8.2. Реактор смешения периодического действия: 1 – выходной
Рис.2.8.3. Реактор непрерывного действия: 1
патрубок.
– выходной патрубок.
Важной характеристикой аппарата смешения непрерывного действия является время пребывания взаимодействующих компонентов в реакционном объеме.
Этот показатель характеризует продолжительность контакта взаимодействующих веществ и, следовательно, определяет степень превращения исходных веществ в продукты реакции. Время пребывания Ʈ(с) компонентов в аппаратах смешения рассчитывается как отношение объема
204
реакционной смеси в реакторе V (м3) к объемному расходу реагентов Q (м3/с) через аппарат:
|
V |
(2.8.2) |
|
Q |
|||
|
|
Из формулы (2.2) следует, что время пребывания Ʈ компонентов в реакторе тем больше, чем больше объем аппарата. При постоянном объеме V значение Ʈ уменьшается с увеличением расхода компонентов Q.
Реактором, близким по своим характеристикам к реактору идеального смешения, является кубовый аппарат с мешалкой. Чем интенсивнее осуществляется перемешивание в кубовом реакторе, тем быстрее выравниваются концентрации компонентов и температура реакционной смеси по объему реактора, и тем ближе этот аппарат к идеальному реактору смешения.
В реальных реакторах смешения вследствие несовершенства конструкции смесителя и самого реактора возможно образование застойных зон (например, в придонной области или у стенок реактора). Для предотвращения этого явления реактор снабжают вертикальными перегородками, а днищу придают сферическую или эллиптическую форму. В реакторах такого типа проводят смешение, полимеризацию и другие процессы.
2.8.4 Конструктивные особенности реакторов
Конструкция реакционного аппарата зависит от следующих основных факторов:
агрегатного состояния исходных веществ и продуктов реакции;
температуры и давления в реакционной зоне;
теплового эффекта и интенсивности теплообмена;
химических свойств перерабатываемых веществ;
интенсивности перемешивания реагирующих веществ;
непрерывности или периодичности ведения процесса;
наличия катализатора и его фазового состояния.
Многообразие химических процессов потребовало разработки значительного количества конструкций реакторов с учетом перечисленных выше факторов. Все реакционные аппараты подразделяют на типовые и нестандартные (не типовые). К типовым аппаратам, широко используемым для химических процессов, относятся: реакционные камеры (емкостные реакторы) и аппараты с мешалками, трубчатые аппараты, колонные аппараты и др. К
205
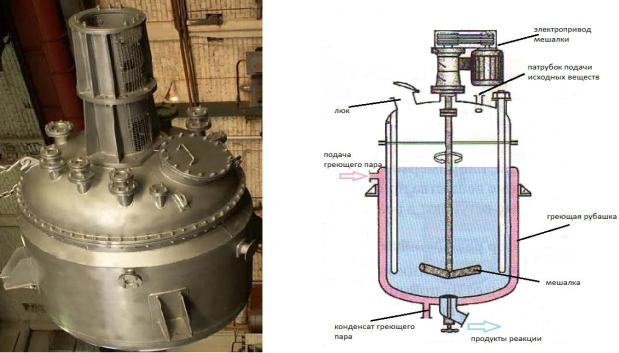
нестандартным относятся большинство химических реакторов: коксовые кубы, реакторы и регенераторы каталитического крекинга, реформига и др.
2.8.5 Емкостные реакторы с мешалкой
В емкостных реакторах химическая реакция проводится в рабочем объеме – емкости, куда через специальный штуцер загружают сырье, а через сливной штуцер осуществляют выгрузку продукта. В емкостных реакторах проводят гомогенные реакции в жидкой фазе. Емкостные аппараты – периодические и проточные. Конструкции реакторов в жидкой фазе зависят в основном от вязкости среды и определяются различным исполнением мешалок.
Рис.2.8.4. Емкостной реактор с приварной рубашкой
В зависимости от условий проведения того или иного процесса объем аппарата с мешалкой может составлять от нескольких долей до нескольких тысяч кубических метров.
По скорости вращения мешалки условно подразделяют на две группы: тихоходные (якорные, рамные и другие, у которых окружная скорость концов лопастей примерно 1 м/с) и быстроходные (пропеллерные, турбинные и другие, у которых окружная скорость порядка 10 м/с).
Например, для перемешивания высоковязких сред при ламинарном режиме используют ленточные, скребковые и шнековые мешалки. Для перемешивания жидкостей сравнительно невысокой вязкости применяют тихоходные мешалки якорные и рамные.
206
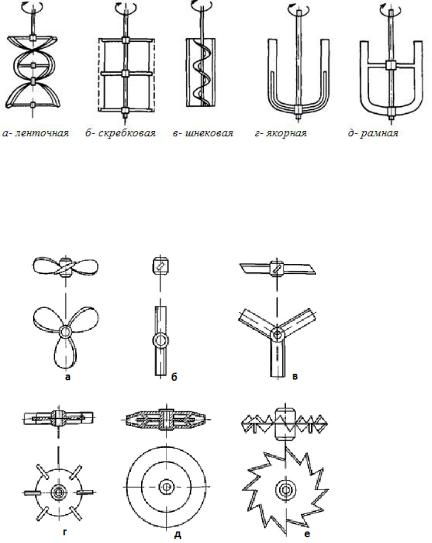
Рис.2.8.5. Конструкции тихоходных мешалок
Быстроходные лопастные, турбинные, пропеллерные мешалки (рис. 2.8.6.) различаются способностью создавать осевое циркуляционное течение.
Рис. 2.8.6. Быстроходные мешалки а – пропеллерная, б – двухлопостная, в – трехлопастная, г – турбинная открытая, д – турбинная закрытая, е – фрезерная.
В котле с мешалкой могут протекать реакции периодического действия - обычно в условиях окружающей среды либо при умеренно высоком давлении и температуре до 250°С. В зависимости от производственных требований, подобные емкости изготовляются из нелегированной или легированной стали, иногда плакируются, снабжаются эмалевым или резиновым покрытием.
На производстве емкостные реакторы работают в непрерывном режиме и часто устанавливают последовательно. Такое размещение называют каскадом реакторов смешения. В каскаде значительно активизируется перемешивание за счет уменьшения реакционного объема, снижения отрицательного влияния застойных зон и зон циркуляции. В конечном счете, это приводит к достижению более высоких значений степени превращения исходных веществ и выхода продуктов реакции.
При ступенчатой компоновке несколько непрерывно действующих реакторов располагаются последовательно друг за другом (рис. 2.8.7.). При этом конечный продукт 1-го реактора становится исходной смесью для 2-го
207

реактора, а конечный продукт 2-го реактора — исходной смесью для 3-го бака и т. д.
Рис. 2.8.7. Ступенчатая (последовательная) схема соединения реакторов
Таким образом, химическая реакция здесь распределяется по нескольким реакционным сосудам. Концентрация реакционной массы в отдельных баках изменяется ступенями до достижения концентрации продукта реакции. Такая ступенчатая схема используется:
когда имеют дело с сильно экзотермической реакцией и требуется установить в отдельных баках (за счет разной степени отвода тепла) разные температуры и, следовательно, разные скорости реакции;
когда по ходу реакции приходится прибегать к промежуточной выгрузке нежелательных побочных продуктов.
При батарейной компоновке несколько смесителей параллельно включаются в производственный процесс (рис.2.8.8.).
Эта параллельная схема используется, в частности, при опасности регулярных сбоев в работе — например, из-за частых засорений отдельных реакторов. Тогда соответствующий бак можно исключить из процесса (остановить и привести в порядок), продолжив работу в двух други х реакторах. То же относится и к случаям проведения плановопрофилактических ремонтов.
Рис.2.8.8.. Батарейная (параллельная) схема соединения реакторов.
208
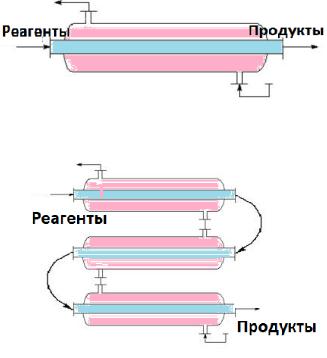
2.8.6 Трубчатый реактор
Трубчатые реакторы широко распространены в химической промышленности для проведения непрерывных процессов с большим тепловыделением. Реакторы этого типа довольно сложны по конструкции и имеют значительную стоимость.
Типичным примером трубчатого реактора является реактор типа "труба в трубе" (рис. 2.8.9.).В таком реакторе теплоноситель циркулирует через рубашку реактора. Выбор пространства для теплоносителя и реакционной массы определяется тем, какой из этих потоков быстрее загрязняет пространство. Для того, который загрязняет быстрее, выбирается внутренняя труба, т.к. ее проще
прочищать.
Рис.2.8.9. Трубчатый реактор типа «труба в трубе»
Если требуется достаточно большое время пребывания реакционного потока в зоне реакции, то выбирается многосекционный аппарат "труба в трубе" (рис.2.8.10.).
Рис.2.8.10. Многосекционный аппарат типа «труба в трубе»
Аппараты этого типа непрерывные, змеевиковые с поверхностным теплообменом. Используются для процессов при сравнительно небольшом времени пребывания исходных веществ в зоне реакции. Недостатки аппаратов: большой расход металла, значительная длина, большое количество соединений, большие гидравлические сопротивления, сложность осмотра, чистки, ремонта. Достоинства: отсутствие утечек через уплотнительные устройства, возможность применения высоких давлений, реализация режима идеального вытеснения при турбулентном характере движения смеси в трубах.
В высокотемпературных процессах (например, в термическом крекинге углеводородов) проще помещать секцию трубок в камеру сгорания, в которой аккумулируется тепло, необходимое для обеспечения необходимой температуры (рис.2.8.11). Такие реакторы называются трубчатыми печами.
Трубка обычно заполнена насадочными телами либо зернистым катализатором, что позволяет значительно увеличить реакционную поверхность. Чаще всего в таком реакторе вступают в реакцию друг с другом газообразные вещества. При
209