
МУ практики итог (Давыдов А.Н
.).pdf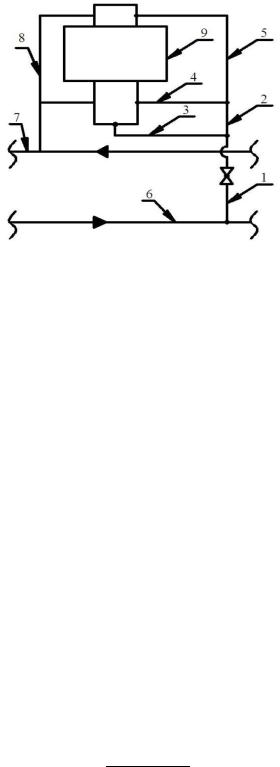
Задача №3. Расчет высоты расположения аккумулирующего бака и объема маслобака
Высота расположения аккумулирующего бака рассчитывается исходя из давления и напора, необходимого для обеспечения работы магистральных насосов во время выбега.
Схема к расчету представлена на рис. 3:
Рис. 3 Схема подводящих трубопроводов, идущих от общего маслопровода к подшипникам магистрального насоса
1 – участок 1 с задвижкой и тройником; 2 – участок 2 с тройником; 3 – участок 3 с поворотом; 4 – участок 4; 5 – участок 5 с поворотом; 6 – общий подводящий трубопровод; 7 – общий отводящий трубопровод; 8 – отводящие трубопроводы, идущие от магистрального насоса к общему отводящему трубопроводу; 9 – насос магистральный
Высота расположения аккумулирующего бака, Нб, м:
(33)
Где Н – потери напора в подводящих трубопроводах, м
(34)
Где – потери напора в подводящих трубопроводах, идущих от общего подводящего трубопровода к магистральному насосу, м
(35)
Определим потери напора для участка 1:
Условие ламинарного течения жидкости определяется условием:
(36)
Где Reнм1 – число Рейнольдса
(37)
11

Где |
– средняя скорость масла на участке 1, м/с; – кинематическая |
|||||
вязкость масла, м2/с; |
– внутренний диаметр трубопровода на участке |
|||||
1, м |
|
|
|
|
|
|
|
|
|
|
|
|
(38) |
|
|
|
|
|
||
Где |
– расход масла на участке 1, м3/ч; |
|||||
|
|
|
|
(39) |
||
|
|
|
Коэффициент гидравлического трения на участке 1, определяется по формуле:
(40)
Потери напора на участке 1 определяются по формуле:
|
|
|
|
|
|
|
|
|
|
|
(41) |
|
Где |
– приведенная длина участка 1, м: |
|
|
|
||||||||
|
|
|
|
|||||||||
|
|
|
|
|
|
∑ |
|
|
(42) |
|
||
|
– длина участка 1,м; ∑ |
|
|
|
|
|||||||
Где |
– суммарный коэффициент местных |
|
||||||||||
потерь на участке 1: |
|
|
|
|
|
|
|
|
||||
|
∑ |
|
|
|
|
|
|
(43) |
|
|||
Где |
– коэффициент, учитывающий потери в задвижке; |
|
|
|||||||||
– коэффициент, учитывающий потери в тройнике |
|
|
|
|
||||||||
|
Потери напора на участках |
2( |
), 3( |
), 4( |
) и |
5( |
) |
|||||
рассчитываются аналогично. |
|
|
|
|
|
|
|
|
||||
|
Условие ламинарного течения жидкости в подводящем |
|||||||||||
трубопроводе, идущим на магистральные насосы: |
|
|
|
|
||||||||
|
|
|
|
|
|
|
|
|
|
|
(44) |
|
Где Reтрнм – число Рейнольдса |
|
|
|
|
|
|
|
|
||||
|
|
|
|
|
|
|
|
|
|
|
(45) |
|
|
|
|
|
|
|
|
|
|
|
|
|
Где – средняя скорость масла в подводящем трубопроводе, идущем на насосы, м/с; – внутренний диаметр подводящего трубопровода, м
12

Коэффициент гидравлического трения в подводящем трубопроводе, идущим на магистральные насосы:
|
|
|
|
|
|
|
|
|
|
(46) |
|
|
|
|
|
|
|
|
|
|
|
||
|
Потери напора в подводящем трубопроводе, идущим на |
||||||||||
магистральные насосы: |
|
||||||||||
|
|
|
|
|
|
|
|
|
|
(47) |
|
Где |
– приведенная длина подводящего трубопровода, м: |
||||||||||
|
|||||||||||
|
|
|
|
|
|
|
|
∑ |
(48) |
||
|
|
|
|
|
|
|
|
||||
Где |
– длина подводящего трубопровода, идущего на магистральные |
||||||||||
насосы, м; ∑ |
– суммарный коэффициент местных потерь в |
||||||||||
подводящем трубопроводе: |
|
||||||||||
|
|
∑ |
(49) |
||||||||
Где |
|
– коэффициент, учитывающий потери на повороте 900. |
|||||||||
|
Высота столба масла, необходимая для поддержания давления масла |
||||||||||
Рм(Н/м2), определяется по формуле м: |
|
||||||||||
|
|
|
|
|
|
|
|
|
|
(50) |
|
|
|
|
|
|
|
|
|
|
|
Где – плотность масла при 200С, кг/м3.
Объём аккумулирующего бака рассчитывается исходя из расхода масла, необходимого для обеспечения нормальной работы магистральных насосов во время выбега:
Объем маслобака определяется по формуле, м3:
(51)
Где – объем масла в трубопроводе, м3:
( |
) |
(52) |
Где – внутренний радиус подводящего трубопровода, м
(53)
– внутренний радиус отводящего трубопровода, м
(54)
– внутренний радиус трубопровода подачи масла на подшипники, м
13
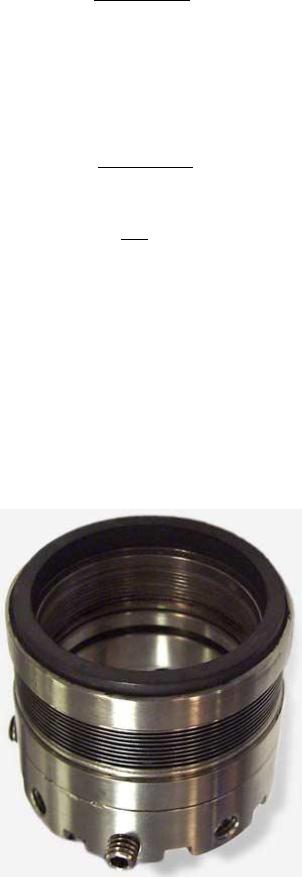
(55)
– суммарная длина трубопровода подачи масла на подшипники и высота аккумулирующего бака, м
(56)
– внутренний радиус трубопровода соединяющего аккумулирующий бак с линией отвода, м
(57)
– объём аккумулирующего бака, м3:
(58)
Где – массовый расход масла в маслосистеме, кг/с;
– время торможения инерционное, с
Задача №4. Расчет торцевого уплотнения
Торцевое уплотнение насоса (рис. 4) – важный узел, обеспечивающий бесперебойную работу насосного оборудования. Торцевые уплотнения обеспечивают надежную герметизацию вращающегося вала насосного агрегата и сводят к минимуму утечку перекачиваемого продукта.
Для обеспечения высокой степени надежности торцевых уплотнений в процессе эксплуатации, необходимо проводить расчет.
Рис. 4 Торцевое уплотнение насосного агрегата
14
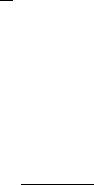
Поверхность трения определяется по |
формуле, см2: |
|||
|
|
( |
) |
(59) |
|
Где и конструктивные размеры рабочих колец уплотнения Неуравновешенная площадь аксиально-подвижного кольца, по
которому осуществляется гидравлический прижим определяется по
формуле, см2: |
|
|
( |
) |
(60) |
Для равномерного распределения давления трущихся поверхностей, рекомендуется устанавливать по периметру не менее шести пружин, равномерно распределенных по окружности.
При максимальном сжатии каждая пружина создает усилие S кгс. Удельное давление от усилий всех пружин при максимальном их сжатии без учета сил трения определяется по формуле, кгс/см2:
(61)
Где m – количество пружин; S – сила сжатия одной пружины, кгс; Т – сила трения, кгс Удельное давления, кгс/см2:
( |
) |
(62) |
Где Р – давление среды в |
камере уплотнения, кгс/см2; |
– |
коэффициент разгрузки.
Результирующее удельное давление в паре трения определяется по формуле, кгс/см2:
(63)
Полученное значение удельного давления должно находиться в пределах рекомендуемого: 3,5 – 7 кгс/см2. Если условие не выполняется, необходимо изменить параметры уплотнения.
Задача №5. Противопомпажная защита центробежных нагнетателей.
Помпаж, или неустойчивый режим работы нагнетателя, является наиболее опасным автоколебательным режимом в системе нагнетатель – газопровод, приводящий к срыву потока в проточной части нагнетателя.
Внешне помпаж проявляется в виде хлопков, сильной вибрации нагнетателя, отдельных периодических толчков, в результате чего возможны разрушение рабочего колеса нагнетателя, повреждение упорного подшипника, разрушение лабиринтных уплотнений и т.д. Возникновение помпажа в нагнетателе вызывает колебания частоты вращения и температуры газа в ГТУ, приводящей во вращение
15

нагнетатель, и, как следствие, к возникновению неустойчивой работы осевого компрессора, что, в свою очередь, приводит к аварийной остановке ГПА.
Причинами возникновения помпажа является изменение характеристики сети (газопровода), вследствие:
колебаний давления газа в газопроводе;
влияния параллельно включенных, но более напорных нагнетателей;
неправильной или несвоевременной перестановкой кранов в трубной
обвязке нагнетателя; Изменение режима работы нагнетателя до значительного
уменьшения расхода газа (приблизительно до 60% расчетного значения) происходит вследствие:
снижения частоты вращения ниже допустимой;
ухудшения технического согстояния газотурбинного привода;
попадания посторонних предметов на защитную решетку нагнетателя, её обледенение и др.
Для устойчивой и надежной работы центробежных нагнетателей производится расчет противопомпажной защиты.
Относительная плотность газа по воздуху определяется по формуле:
|
|
|
|
̅ |
|
|
|
|
|
|
(64) |
|
|
|
|
|
|
|
|
|
|||||
Газовая постоянная вычисляется по формуле 65: |
|
|||||||||||
|
|
|
|
|
|
|
|
|
|
|
|
(65) |
|
|
|
|
|
|
|
̅ |
|||||
|
|
|
|
|
|
|
|
|||||
Коэффициент сжимаемости газа по параметрам входа определяется |
||||||||||||
из соотношения 66: |
|
|
|
|
|
|
|
|
|
|||
|
( |
|
|
|
|
) |
|
|
(66) |
|||
|
|
|
|
|
|
|||||||
Где |
– соотношение температур на входе и критической. |
|||||||||||
Определяется по формуле 67. |
|
|
|
|
|
|
|
|
|
– соотношение давлений на входе и критического. Определяется по формуле 68.
(67)
(68)
Где Ткр – критическая температура, Ркр – критическое давление Определим плотность газа на входе по формуле 69:
(69)
16

Объемная производительность нагнетателя определяется по формуле 70:
(70)
Приведенная объемная производительность находится по формуле
71:
(71)
Режим работы нагнетателя по расходу газа, как правило, ограничивается 10%-м запасом от границы помпажа и определяется по формуле:
( |
) |
(72) |
|
|
|
|
|
Таким образом, рассчитав опасные зоны работы ГТУ, можно предотвратить работу аппарата в режиме помпажа.
Задача №6. Механический расчет пылеуловителей
Толщина стенки корпуса пылеуловителя определяется по формуле:
|
|
|
|
(73) |
[ |
] |
|
||
|
|
|||
Где P – давление, МПа; D – внутренний диаметр пылеуловителя, м; [ ] – |
||||
допускаемое напряжение на |
растяжение, МПа; |
– коэффициент |
прочности сварных швов.
Допускаемое внутреннее избыточное давление в стенке корпуса
рассчитывается по формуле: |
|
|
|
|
|
[ ] |
|
[ ] |
|
(74) |
|
|
|
|
|||
|
|
|
|||
Толщина стенки эллиптических и полусферических днищ |
|||||
рассчитывается по формуле: |
|
|
|
|
|
|
|
|
|
|
(75) |
[ |
] |
|
|
||
|
|
|
Где с=0,002 м – прибавка на коррозию, м; с1=0,002 м – прибавка на вытяжку, м; R – радиус кривизны в вершине днища, м; [ ]
Радиус кривизны в вершине днища определяется по формуле:
(76)
Где Н – высота днища, м Допустимое внутреннее избыточное давление в днище корпуса
рассчитывается по формуле:
17
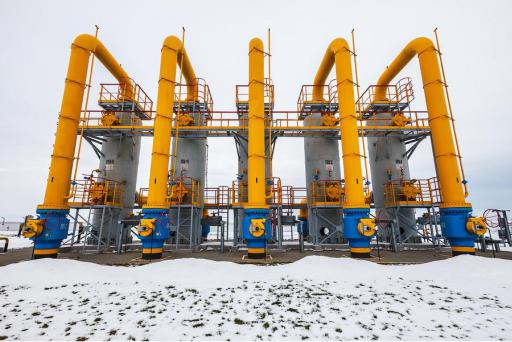
[ ] |
[ |
] |
(77) |
|
|
||
|
|
Расчетные значения, полученные по выше приведенным формулам, являются предельно допустимыми рабочими параметрами для пылеуловителей.
Задача №7. Расчет циклонного пылеуловителя
Для обеспечения безопасной работы оборудования компрессорной станции, необходимо осуществлять очистку газа от механических примесей. Для данных целей в технологической схеме КС после узла подключения предусматривается установка блока пылеуловителей.
Наибольшее распространение получили обеспыливающие устройства, в которых для осаждения частиц используется центробежная сила. В современных усовершенствованных конструкциях циклонных пылеуловителей (рис.5) возможно достаточно эффективно улавливать твердые или капельные частицы размером от 5 мкм и больше. Улавливание пыли в циклонах основано на использовании инерции частиц.
Рис. 5 Блок циклонных пылеуловителей Газовый поток со взвешенными в нем твердыми частицами вводится
с большой скоростью по касательной к стенке цилиндрической части циклона, где делает несколько спиральных витков в сторону пылеотводящего отверстия, а затем по внутренней спирали движется к выхлопной трубе. При входе в циклон взвешенные в потоке частицы по инерции движутся по своим первоначальным траекториям, а затем под воздействием аэродинамических сил их траектории искривляются. Те из
18
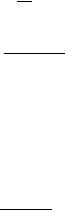
частиц, масса которых достаточно велика, успевают достичь стенок циклона, т.е. отделяются от потока. Под влиянием силы тяжести и увлекающего действия осевого движения отделившиеся частицы опускаются и через пылевыпускное отверстие поступают в бункер, где они оседают.
Циклоны изготовляют правого и левого вращения газового потока. Согласно ГОСТ 9617-67 для циклонов принят следующий ряд
диаметров: 200, 300, 400, 500, 600, 700, 800, 900, 1000, 1200, 1400, 1600,
1800, 2000, 2400 и 3000 мм. |
|
|
|
|
|
|||
|
Расчет параметров циклонного пылеуловителя выполняется в |
|||||||
следующей последовательности: |
|
|
|
|
|
|||
|
Плотность газа при рабочих |
условиях определяется по формуле, |
||||||
(кг/м3): |
|
|
|
|
|
|||
|
|
|
|
( |
) |
(78) |
||
|
|
|
|
|
|
|
|
|
|
( |
|
) |
|
|
|||
|
|
|
|
|
||||
Где |
кг/м3 |
|
|
|
|
|
||
|
Расход газа при рабочих условиях, (м3/с): |
|
||||||
|
|
|
|
|
|
|
|
(79) |
|
|
|
|
|
|
|
|
|
|
Диаметр циклонного пылеуловителя при оптимальной скорости |
|||||||
движения газа определяется по формуле, (м): |
|
|||||||
|
|
√ |
|
|
|
|
(80) |
|
|
|
|
|
|
|
|||
|
|
|
|
|
|
Так как диаметр циклона слишком большой, то необходимо выполнить установку нескольких циклонов (n), что обеспечит лучшее качество очистки. Расход газа на один циклон будет:
(81)
Уточненный диаметр циклонного пылеуловителя
√ |
|
(82) |
|
Принимается ближайший стандартный диаметр циклонного пылеуловителя и находится действительная скорость газа в установке,
(м/с):
(83)
19

Если действительная скорость отличается от оптимальной менее чем на 15%, принимается уточненный диаметр пылеуловителя. В случае, если расхождение составляет более 15%, необходимо изменить диаметр.
Коэффициент сопротивления циклонного пылеуловителя определяется по формуле:
(84)
Коэффициент гидравлического сопротивления группы циклонов определяется по формуле:
(85)
Где К3– коэффициент, учитывающий дополнительные потери давления, связанные с компоновкой циклонов в группу. К3=35 – при двухрядной компановке; К3=60 – при круговой компановке.
Коэффициент сопротивления циклона ζ зависит от ряда факторов: диамет-ра циклона, концентрации пыли, компоновки циклонов в группе, организации выхода газа из выхлопной трубы и некоторых других.
Гидравлическое сопротивление группы циклонов определяется по формуле, (Па):
(86)
20