
Pekarsh_A_I_Covremennye_tekhnologii_agregatno-s
.pdf
Инструментальный стенд с ЧПУ модели МС-636Ф-2-11 предназначен для монтажа элементов оснастки (вилок, полувилок, ложементов, втулок, реперов ит.п.) накаркасных узлах, носителях БО.
Типовая схема монтажа сборочных приспособлений балочного типа с помощью инструментальных стендов при условии, что рубильники поступают полностью готовыми, состоит из четырех этапов - установка вертикального каркаса, монтаж отдельных балок или рам, монтаж балок на вертикальном каркасе, установка базовых элементов на монтажныеэлементыбалок.
С учетом специфики сборочного производства и сборочной оснастки на предприятиях проводят модернизацию и доработку инструментальных стендов. Примером такой доработки является модель МС-636-2-11, в которой съемные поперечные линейки заменены выдвижными, что позволяет значительно снизить сроки и трудоемкость монтажа приспособленийрамного типа.
Несомненным достоинством монтажа с помощью стационарных координатных стендов является сокращение цикла и стоимости подготовки сборочного производства. Но именно фиксированные габариты координатных систем инструментальных и монтажных стендов ограничивают область их применения. Монтаж сборочных приспособлений в координатно-оптических стендах с использованием специальных оптических и лазерных систем по своей сути является развитием координатногометодамонтажа.
При выполнении операций монтажа и контроля с помощью измерительных систем типа «Axyz» предъявляются следующие требования к помещению, режиму вентиляции, освещенности, времени проведения измерений.
1.Помещениедолжноиметьжесткоеоснованиедляустановкиштат ных штативов с теодолитами (тахеометрами) или лазерного трекера или специально оборудованные места для крепления теодолитов (та хеометров) во избежание изменения ориентации теодолитов (тахео метров), лазерноготрекеравовремяпроведениянаблюдений.
2.Если измерительные приборы располагаются на высоте более 1,8 м, томестастоянокнаблюдателейдолжныбытьоборудованыспе циальнымиподставкамидлястояния.
3.Теодолитынерекомендуетсяставитьвблизинагревательныхпри боров или в местах, связанных с резким колебанием температур во времяпроведениянаблюдений.
4.Вовремяпроведениянаблюденийвпомещениидолженбытьуста новленстабильныйтемпературныйрежимсколебанияминеболее5 °С.

5. Визирные цели должны быть освещены равномерным и достаточной интенсивности освещением. Если освещения, используемого в помещении штатно, недостаточно для четкого наблюдения визирных целей, последние должны быть подсвечены электрической переносной лампочкой.
Монтаж сборочной оснастки с использованием измерительных системтипа«Axyz» осуществляетсявследующейпоследовательности:
1)измерительныеприборырасполагаютсявсборочномцехевместе, удобномдляпроведениянаблюденияэлементасборочнойоснастки;
2)вПОизмерительнойсистемы«Axyz» вводитсяфайлскоордината миреперных точек; вкачестве реперных точек используются центры БО (в БО вставляются штатные цилиндрические целевые знаки с на клееннымисторцакатафотнымиотражающимимарками);
3)производитсязамерреперныхточек;
4)стандартным ПО измерительной системы «Axyz» автоматически определяютсяпараметрыпреобразованиясистемыкоординатприбора всистемукоординатсборочнойоснастки(дальнейшиеизмеренияпро исходятвсистемекоординатсборочнойоснастки);
5)на основанииданных координатной системы БОопределяется те оретическое положение контрольных точек элементов сборочной ос настки;
6)вспециальномрежимеработыизмерительныхсистем(выносточ кивнатуру) приборыспомощьюлазерныхлучейматериализуютэти точкивпространстве;
7)с помощью котировочныхустройствконтрольная точка совмеща ется с еевизуализацией (отметкой лазерного луча);
8)выполняетсяконтрольноеизмерение.
Контроль технологической оснастки
Основным критерием качества технологической оснастки является соответствие действительного обвода собранной СЕ техническим условиям на ее изготовление. Контроль специализированных СП для сборки СЕ классификационных групп II, III осуществляется с помощью ШП (ШМФ).
При изготовлении же технологической оснастки на станках с ЧПУ и использовании при этом для измерения координат точек контуров универсальных измерительных средств возникает резкая диспропор-
ция между временем, затрачиваемым на обработку непосредственно настанке, ивременем, затрачиваемымнаконтроль.
В данном случае методы контроля должны обеспечивать автоматизированный анализ геометрических параметров обработанной оснастки и позволять вносить коррективы в систему автоматизированного расчета и записи управляющей информации для станков с ЧПУ в целях повышения точности изготовления оснастки (рис. 3.53). Точностные требования к методам и средствам контроля оснастки должны соответствовать точности автоматизированного изготовления оснастки наоборудованиисЧПУ. Методыконтролярассмотренывразделе2.4.
В табл. 3.17 приведена классификация методов контроля обводообразующей оснастки, обрабатываемой на оборудовании с ЧПУ. В табл. 3.19 представлены рекомендации по методам и средствам контроля приразличныхспособахизготовления.


Контроль сборочнойоснастки длясборки СЕ классификационных групп I, IV-IX осуществляется с использованием:
1)координатно-измерительныхсистем;
2)теодолитных измерительных систем «Axyz MTM/STM»;
3)интерферометрических измерительныхсистем«Axyz LTD» наба зелазерныхтрекеров.
Контролируютсяследующиегеометрическиепараметрыэлементовсборочной оснастки:

-положение обводообразующих элементов сборочной оснастки по контрольным точкам контуров (процентным рискам, осям стринге ров, обрезамобшивокит.п.);
-взаимноерасположениеэлементовсборочнойоснастки;
-перпендикулярностьипараллельностьэлементовсборочнойоснастки;
-соосностьрасположенияБО в фиксаторах сборочной оснастки.
Список литературы
1.Теоретические основы авиаиракетостроения (в конспектах лек ций): учеб. пособиедлявузов/ А.С. Чумадин, В.И. Ершов, В.А. Барви нок и др. - М.: Дрофа, 2005. - 784 с.
2.Основы технологиипроизводства летательных аппаратов (вкон спектахлекций): Учебноепособие/ А.С. Чумадин, В.И. Ершов, В.А. Бар винок и др. - М: Наука и технологии, 2005. - 912 с.
3.Современныетехнологииавиастроения/ Коллективавторов; Под ред. А.Г. Братухина, ЮЛ. Иванова. - М.: Машиностроение, 1999. - 832 с.
4.Современныетехнологическиепроцессысборкипланерасамоле та / Коллектив авторов; Под ред. Ю.Л. Иванова. - М.: Машинострое ние, 1999. - 304 с.
5.Кривов Г.А. Технология самолетостроительного производства. -
К: КВНЦ, 1997. - 459 с.
6.Сборочные, монтажные ииспытательные процессыв производс тве летательных аппаратов: Учебник для студентоввысших техничес кихучебныхзаведений/ В.А. Барвинок, В.И. Богданович, П.А. Бордаков, Б.П. Пешков, И.Н. Желтов, И.А. Докукина; Под ред. проф. В. А. Барвинка. - М.: Машиностроение, 1996. - 576 с.
7.Технологиясамолетостроения: Учебникдляавиационныхвузов/ А.Л. Абибов, Н.М. Бирюков, В.В. Бойцовидр.; Подред. А.Л. Абибова. 2-еизд., перераб. и доп. - М.: Машиностроение, 1982. - 551 с.
8.Бабушкин А.И. Методы сборки самолетных конструкций. - М.: Машиностроение, 1985. - 248 с.
9.БойцовВ.В. и др. Сборкаагрегатов самолета: Учеб. пособие для студентоввузов, обучающихсяпоспециальности«Самолетостроение»
/В.В. Бойцов, Ш.Ф. Ганиханов, В.Н. Крысин. - М.: Машиностроение, 1988.- 152 с.
10.Волошин И.Н. Обеспечение точности обводовклепаных агрега тов самолетов. - М.: Машиностроение, 1979. - 152 с.

11.Расчетыточностисборкииувязкивсамолетостроении: Учеб. по собие / Федорченко Б.Д. - Харьков: Харьк. авиац. ин-т, 1986 - 68 с.
12.Технология производства самолетов ивертолетов. Раздел: Сбо- рочно-монтажные и испытательные работы в самолето-вертолетост- роении / Ю.М. Букин, Ю.А. Воробьев. - Сборник лекций на английс комирусскомязыках. — Харьков: Нац. аэрокосмическийун-т«Харьк.
авиац. ин-т», 2003.- 331 с.
13.ОСТ 1.42064-80. Сборка самолетов. Термины и определения. Изд. офиц. - Вводится впервые с 01.07.81. - НИАТ, 1981. - 35 с.
14.РТМ-963. Сборка узлов и панелей планера самолета по сбороч ным отверстиям. - НИАТ, 1950.
15.РТМ-1223. Сборкаузловиагрегатовкрупногабаритных самоле тов. - НИАТ, 1970. - 35 с.
16.РТМ-1289. Область применения различных систем сборочных приспособлений. - НИАТ, 1950. - 24 с.
17.РТМ 1.4.1864-88. Сборка агрегатов широкофюзеляжных изде лий. - НИАТ, 1989.
18.ТР-654. Монтаж и увязка сборочной оснастки без применения жестких носителей форм и размеров. - НИАТ, 1974. - 16 с.
19.ПИ-0653. Сборка узлов и агрегатов самолета по координатнофиксирующим исборочным отверстиям. - ХАПО, 1972. - 13 с.
20.СТП07509416.14.016-200. Увязкагеометрическихпараметровуз ловиагрегатовнезависимымметодомсприменениемЭВМ. - КнААПО, 2000. - 37 с.
21.ТИ.07509416.25088.04000. Сборка узлов и агрегатов планера самолетаRRJ сиспользованиемотверстийвкачестве сборочныхбаз/ Г.А. Кривое, В.А. Матвиенко, Ю.А. Воробьев, Б.Н. Марьин, В.Ф. Кузь мин- Комсомольск-на-Амуре, КнААПО, 2006. - 156 с.
Глава 4
МЕХАНИЗИРОВАННАЯ ТЕХНОЛОГИЯ ВЫПОЛНЕНИЯ ВЫСОКОРЕСУРСНЫХ БОЛТОВЫХ СОЕДИНЕНИЙ
Конструктивно-технологические методы обеспечения долговечности болтовых соединений
Одной из основных задач при создании современных пассажирских и транспортных самолетов является обеспечение высоких ресурсных показателей. Отказы вследствие повреждений планера самолета в общей сумме отказов составляют 12-30% [5]. Надежность и долговечность авиационных конструкций в значительной степени определяется усталостнойпрочностьюнаиболее ответственныхдеталейиэлементовконструкции планера. В процессе эксплуатации разрушения возникают, главным образом, вместахвозникновенияочаговконцентрациинапряжений.
Результаты экспериментальных исследований и испытаний на выносливость, а также опыт эксплуатации самолетов показали, что ресурс планера самолета в первую очередь определяется ресурсом болтовых и заклепочных соединений, которые являются концентраторами напряжений и источниками зарождения усталостных трещин. Зарождение усталостных трещин в силовых элементах планера в зоне установки болтов предопределяется концентрацией напряжений в этой зоне и интенсивностью развития фретинг-коррозии при контактном взаимодействии и переменных нагрузках, вызывающих деформации и микросмещениядеталей.

В конструкции современных самолетов количество болтовых соединений (БС) составляет 300-300 000 шт., в зависимости от категории самолета, при этом 50-70% болтов устанавливается в высоконагруженныхзонах.
Ресурс болтовых соединений в значительной степени зависит от конструктивных параметров этих соединений, способов образования отверстий и установки болтов, характера посадки болта в отверстие, параметров свинчивания соединения, характера контакта сопрягаемых поверхностей. Следовательно, задача обеспечения заданной долговеч- ностиболтовыхсоединенийявляетсяконструкторско-технологической.
Основными конструктивно-технологическими параметрами, оказывающимивлияниенаресурсболтовыхсоединений, являются:
-характерпосадкиболтавотверстие;
-упрочняющаяобработкаотверстийподболты;
-осеваястяжкапакетаврезультатесвинчиванияболтовогосоединения;
-точность и стабильность технологических процессов выполнения соединений.
Совокупность конструктивно-технологических параметров болтового соединения должна обеспечивать благоприятное, с точки зрения долговечности конструкции, напряженно-деформированное состояние (НДС) взоне соединения. Характер НДСвэтойзонеопределяется действующими эксплутационными нагрузками и величиной остаточных напряжений, возникших в деталях в процессе обработки отверстийподболты, напряжений, вызванныхустановкойболтоввотверстия с радиальным натягом, и напряжений от силы сжатия пакета деталейврезультатесвинчиванияболтовыхсоединений.
Для болтовых соединений, работающих на срез, предпочтительным следует считатьтакой вариантконструктивно-технологического выполнения этих соединений, при котором абсолютные значения растягивающих напряжений в деталях пакета минимальны, сжимающих - максимальны, амплитудадействующихлокальныхнапряженийминимальна.
Обработка отверстий под болты резанием (сверлением, развертыванием, протягиванием) не создает в поверхностном слое отверстия сколько-нибудь значительных остаточных напряжений. Создание благоприятного НДС достигается применением упрочняющих методов обработки отверстий пластическим деформированием материала деталейвзонеотверстия.
К упрочняющим методам обработки отверстий, нашедшим практическое применение, относятся: раскатка, дорнирование, чеканка переходныхкромокотверстий.
Пластическое деформирование деталей при раскатке и дорнировании осуществляется за счет того, что диаметр инструмента (раскатника, дорна) больше диаметра обрабатываемого отверстия, т.е. инструмент входит в отверстие с натягом. Величина натяга при этом равна разности диаметра инструмента и диаметра отверстия, подготовленногоподобработку.
Упрочнение отверстий раскаткой
Значение оптимального натяга при раскатывании отверстий составляет 0,6-0,8% [4]. После раскатывания с этим натягом отверстий в пластине из алюминиевого сплава Д16Т величина остаточных напряжений на глубине около 0,3 мм достигает 160-200 МПа. Вблизи поверхности отверстия величина этих напряжений уменьшается в 2,5-4 раза. Применение раскатки отверстий под болты позволяет увеличить долговеч- ностьболтовыхсоединенийв2-3 раза.
Достоинствами процесса раскатывания отверстий, кроме указанного обеспечения благоприятного НДС вблизи отверстия, являются:
-снижение шероховатости поверхности отверстия в результате его раскатывания;
-отсутствиенеобходимости в применении специального механизиро ванногоинструмента.
Кнедостаткампроцессараскатывания отверстийследуетотнести:
-отклонения диаметров отверстий после раскатки, превышающие предельныеотклоненияпоН9;
-сложностьконструкции раскатников и, соответственно, их высокая стоимость;
-невозможность создания надежной конструкции раскатников для обработкиотверстийдиаметромменее8 мм;
-необходимость периодической регулировки раскатников для обес печениязаданнойточностиобработкиотверстий;
-необходимостьвыдерживаниявпроцессераскаткиосевойподачивпре делах0,4-0,8 мм/об. Раскатываниесменьшейподачейприводиткмно гократномупрокатываниюроликовпоодномуитомужеместуповерх ностиотверстия, чтовызываетперенаклепишелушениеповерхности.

Упрочнение отверстий методом дорнирования |
Аналогичные результаты получены при испытаниях образцов двух- |
Упрочнениеотверстийметодомдорнированияосуществляетсязасчет |
рядных двухсрезных болтовыхсоединений. Материалобразцовалюми- |
создания остаточных напряжений сжатия вблизи отверстия в резуль- |
ниевый сплав В95Т. Отверстия под болты лорнировались с натягами 1,2, |
татепластическогоиупругогодеформированияматериаладеталипри |
2,4 и 3,6%. Окончательная обработка отверстий осуществлялась развер- |
протягивании дорначерез отверстие. Дорнированиеотверстий позво- |
тыванием. Припуск наразвертывание составлял0,02-0,04 мм насторону. |
ляет создатьостаточные напряжения сжатия величиной150-350 МПа |
Отклонения диаметров отверстий после развертывания не превышали |
взависимостиотвеличинынатягапридорнировании. Максимальные |
предельных отклонений по Н7. Болты диаметром 8 мм устанавливались в |
значенияостаточныхнапряженийсжатиярасположенынарасстоянии |
отверстия с зазором от 0 до 30 мкм. Свинчивание болтовых соединений |
0,2-0,3 мм отстенкиотверстия, аглубина залеганиянапряженийсжа- |
осуществлялось крутящим моментом, равным 16 Нм. Испытания прово- |
тия достигает 1,5-2,5 мм, что позволяет создать более благоприятное |
дились при значениях номинальных растягивающих напряжений 130, |
НДСпосравнениюсупрочнениемметодомраскатки. |
150 и180 МПаикоэффициентомасимметриициклаR = 0,1. |
Результаты испытаний образцов из алюминиевого сплава В95Т со |
Результаты испытаний образцов (рис. 4.2) показали, что при уста- |
свободными дорнированными отверстиями диаметром 8 мм (рис. 4.1) |
новке болтов с зазором дорнирование отверстий повышает долговеч- |
показали, что дорнирование отверстий с натягом 3,0—3,5% повышает |
ность болтовых соединений примерно в 3 раза. Оптимальное (с точки |
долговечностьобразцовпримернов3-5 раз. |
зрения долговечности) значение натяга при дорнировании зависит от |
|
величины действующих напряжений, поэтому величина натяга долж- |
|
на назначаться с учетом величины напряжений, возникающих в конс- |
|
трукцииизделияотдействияэксплуатационныхнагрузок. |
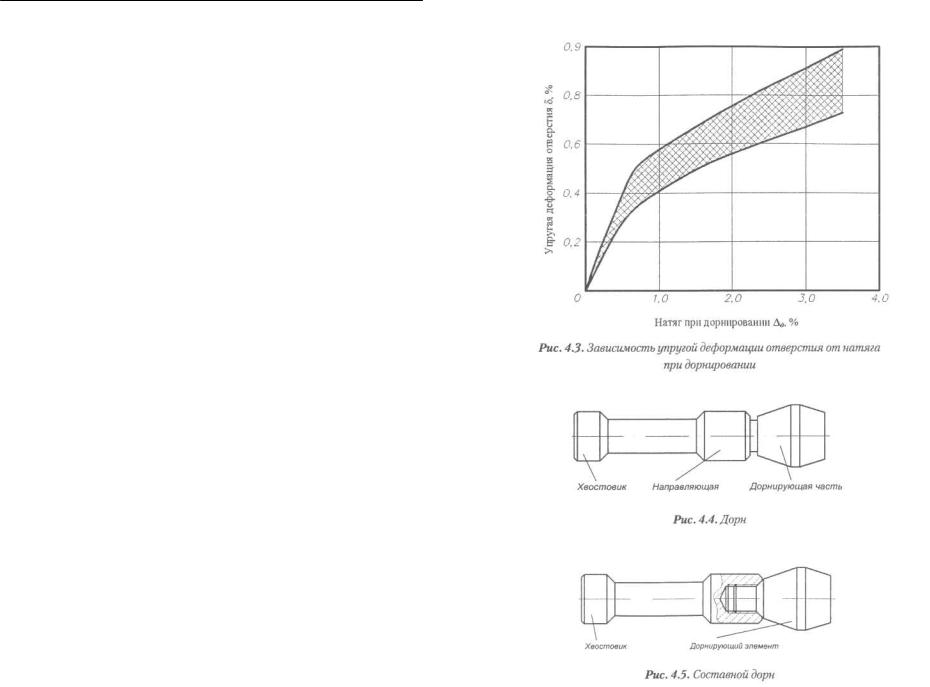
Дорнирование применяется для упрочнения отверстий диаметром 5—16 мм в деталях из алюминиевых сплавов. Величина натяга при дорнировании назначается в пределах 0,5-4 %, исходя из условия достижения заданной долговечности конструкции. К недостаткам дорнирования следует отнести искривление образующей отверстия (так называемая «корсетность») и образование наплывов высотой до 0,1 мм и шириной до 1 мм у кромок отверстий. Эти отклонения оказывают отрицательное влияние на долговечность болтовых соединений из-за уменьшения площади контакта болта и стенки отверстия. Особенно сильно это проявляется при малой толщине деталей, входящих в пакет. Для уменьшения вредного влияния корсетности и наплывов рекомендуется перед выполнением дорнирования по кромкам отверстий снять фаски величиной 0,5x45°.
Точностьотверстий после дорнирования, как правило, не вышеде- вятого-десятого квалитетов. Это обусловлено, во-первых, разбросом величины упругого восстановления диаметра отверстия после дорнирования (рис. 4.3) и, во-вторых, отклонением от цилиндричности отверстия в результате облегченных условий деформирования вблизи кромок отверстия. Поэтому дорнирование в качестве окончательной операции обработки отверстий под болты может применяться для болтов, устанавливаемых спосадкамипоодиннадцатому-двенадцато- му квалитетам. Для болтов, устанавливаемых с посадками по седьмо- му-девятому квалитетам, после дорнирования необходимо выполнить окончательную обработку отверстий развертыванием или режущим протягиванием.
Конструктивно дорн для обработки отверстий состоит из следующихчастей(рис. 4.4):
-хвостовика для установки дорна в захват механизированного инс трумента;
-направляющейдляцентрированиядорнавотверстии;
-дорнирующего элемента сзаборным конусом, цилиндрической лен точкойиобратнымконусом.
Для дорнирования отверстий в местах конструкции изделия с ограниченными подходами в зону обработки могут использоваться составныедорны(рис. 4.5).

Диаметрлорнирующегоэлементарассчитывается сучетомвеличины упругого восстановлениядиаметраотверстияпослепрохождениядорна поформуле:
где Dn - исполнительный диаметр лорнирующего элемента, мм; d - диаметр обработанного отверстия, мм; 5 - величина упругого восстановлениядиаметраотверстия, %.
Дорныизготавливаютсяизинструментальных илибыстрорежущих сталей. ТвердостьдорнирующегоэлементадолжнабытьнеменееHRC 6264. Износдорна впроцессе лорнирования происходит из-заадгезионного схватываниявзонеконтактадорнасобрабатываемымматериалом. При этом наблюдается ухудшение шероховатости поверхности дорна и стенок обрабатываемого отверстия. Для снижения интенсивности адгезионных процессов лорнирование рекомендуется выполнять с применением смазок. Смазка должна обеспечивать режим гидродинамического трения впроцессе лорнирования [17]. К такимсмазкам относятсясмазки, динамическая вязкостькоторыхвыше200 Па-с, в частности, петролатумПП-95/5 ГОСТ4113-80.
Восстановление работоспособности изношенного дорна осуществляетсяполировкойдорнирующегоэлементавпределахдопускаемых
отклоненийнаегоисполнительныйдиаметр.
Упрочнение отверстий под болты методом лорнирования включает всебяследующиеоперации:
- обработку отверстий с припуском под лорнирование развертывани ем в дваилитрипереходаилипротягиванием водин переход(вели чина припуска под лорнирование назначается израсчета получения заданного натяга при лорнировании); - лорнированиеотверстийсприпускомподокончательнуюобработку,
(отклонениедиаметровотверстийпослелорнированиянепревыша етпредельныхотклоненийпоН11; шероховатостьповерхностидорнированныхотверстийнеболее = 0,8 мкм);
окончательнуюобработкуотверстийразвертываниемилипротягиванием в один переход (отклонения диаметров отверстий после обработкине должныпревышатьпредельныхотклоненийпоН9; шероховатость поверхностиотверстийдолжнабытьнеболее = 1,6 мкм).
Совместить указанные операции возможно применением комбинированной протяжки-дорна (рис. 4.6). Трудоемкость обработки отверстий в этом случае снижается в два-три раза, однако затраты на обработку отверстий возрастают из-за существенного увеличения расходов наинструмент.
Для осуществления процесса дорнирования к дорну должно быть приложено осевое усилие, величина которого зависит в основном от диаметралорнирующегоэлемента(см. рис. 4.4).
Дорнированиеотверстийосуществляетсяоднимизспособов:
-протягиваниемдорначерезотверстиеспомощьюпротяжныхмашин илимашиндляустановкиболтовснатягом;
-проталкиванием дорна с помощью прессов или пневматических мо лотков.
Метод протягивания дорна, обеспечивающий более высокую стабильность качественных характеристик лорнированных отверстий, является предпочтительным.
Протягивание дорна через отверстие осуществляется с помощью протяжных машин моделей МП 10-130, МП 12-150 или болтозатягивающих машин моделей МБЗ-1,5, МБЗ-4, оснащенных специальными патронами для закрепления дорнов. При необходимости дорнирования отверстий в местах с ограниченными подходами в зону обработки следует применять указанные болтозатягивающие машины с угловыминасадками.
Модель механизированного инструмента выбирается исходя из условия обеспечения необходимого осевого усилия (рис. 4.7) на штоке машины и величины рабочего хода штока на 5-10 мм больше, чем толщина пакета деталей в месте расположения лорнируемого отверстия.