
Производственная и пожарная автоматика / Shishov - Tekhnologii promishlennoy avtomatizatsii 2007
.pdf•возможность подключения матричной (4 x 4, 5 x 4) и AT совместимой клавиатуры;
•до 48 линий запроса прерываний через универсальный порт ввода/вывода;
• напряжение питания +5 В ±5%; максимальный потребляемый ток:
750мА;
•один оптоизолированный вход удаленного сброса;
•диапазон рабочих температур от -40 до +85°С;
•относительная влажность воздуха от 5 до 95% при 25°С без конденсации влаги;
•габаритные размер 124,5 х 114,3 мм.
11.1.2 Релейные универсальные контроллеры
Понятие «автоматизация производства» часто, и причём небезосновательно, ассоциируется с масштабными компьютеризированными системами. Разработка и внедрение таких систем требует огромных материальных, финансовых и интеллектуальных затрат. Вместе с тем существует большое число задач автоматизации гораздо меньшего масштаба, которые, тем не менее, от этого не теряют своей актуальности.
Как уже отмечалось выше, существует класс универсальных контроллеров, который по вычислительной мощности и набору встроенных функциональных возможностей оптимально соответствует таким несложным задачам. При решении большинства простейших задач автоматизации необходимы устройства управления с дискретными управляющими сигналами, которые формировались бы также по дискретным входным воздействиям. До недавнего времени такие устройства управления реализовывались на основе релейных логических схем. Контроллеры, предназначенные для замены таких схем, исходя из всего этого часто называют релейными.
Рассмотрим конкретный пример – сравнительно простую и вместе с тем достаточно типичную схему смесительной установки (рис. 1.30). Алгоритм работы установки очень прост. После её запуска в работу открывается клапан Y1, и ёмкость начинает заполняться компонентом № 1. При достижении уровня 2 срабатывает датчик SL2, закрывается клапан Y1 и открывается клапан Y2. В ёмкость начинает поступать компонент № 2. После заполнения ёмкости до уровня 1 по сигналу от датчика SL1 закрывается клапан Y2 и включается привод мешалки М. Через 15 минут он выключается, смесь готова. Для её выгрузки открывается клапан Y3. Окончание процесса фиксируется датчиком SL3 (уровень 3). После закрытия клапана Y3 установка готова к новому циклу приготовления смеси.
59
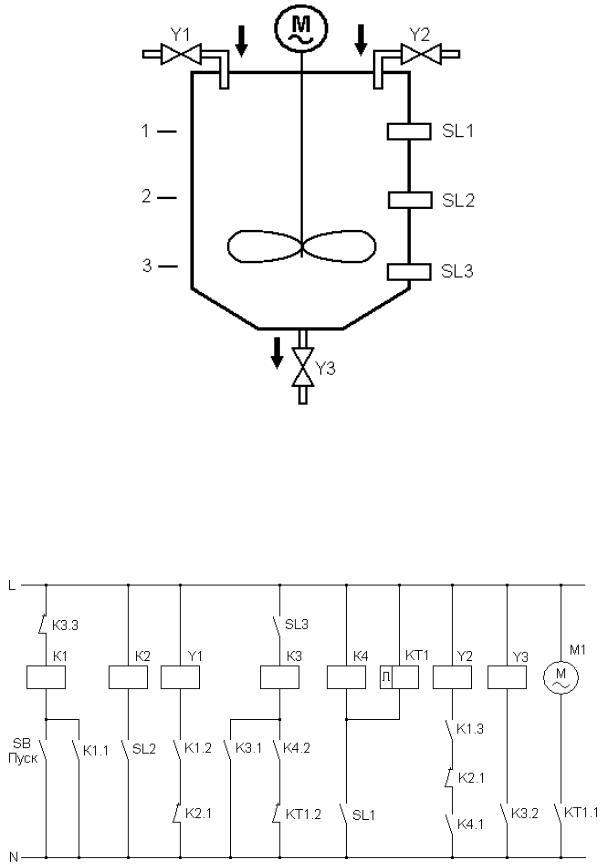
Р и с. 1.30. Схема смесительной установки
Как поступил бы разработчик системы управления, скажем, лет 10-15 назад? Он использовал бы схему, подобную той, что приведена на рис. 1.31. Вся система реализуется с помощью четырёх промежуточных реле и одного реле времени.
Р и с. 1.31. Электрическая схема системы управления на реле.
Все просто, но усложним немного задачу и добавим условие возможности приготовления на этой же установке смеси по другой рецептуре. Это озна-
60
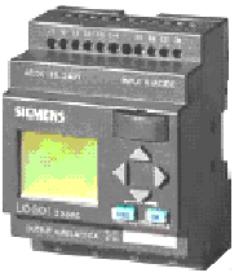
чает, что в ёмкость должно загружаться иное число компонентов с индивидуальными для каждого из них дозой и порядком загрузки, а также изменено время работы мешалки. Нет необходимости говорить о том, что такое условие уже не может быть реализовано с помощью релейной схемы. Но такая задача по плечу контроллеру, в котором алгоритм управления реализуется программно, а аппаратных средств имеется ровно столько, сколько необходимо для решения подобных по сложности задач.
К классу контроллеров, предназначенных для решения таких задач, относится логический модуль LOGO! фирмы Siemens. Рассмотрим решение поставленной задачи на его примере.
Р и с. 1.32. Внешний вид LOGO!
Логический модуль LOGO! (рис. 1.32) изначально задумывался как промежуточное звено между традиционными релейными элементами автоматики (контакторы, реле времени и т.п.) и программируемыми контроллерами. В нём вместо соединения проводов должно используется логическое соединение функций, обычно реализуемых аппаратно с помощью отдельных устройств. Сложность устройств позволяет работать с ними персоналу без специальных знаний в области программирования.
Для подключения к источникам сигналов и исполнительным устройствам модули LOGO! первых поколений имели 6 или 12 дискретных входов и 4 или 8 дискретных выходов (варианты Basic и Long соответственно). Затем к дискретным входам добавилось два аналоговых. В 2001 году фирма Siemens выпустила модульный LOGO!, в котором увеличение числа обслуживаемых входов и выходов обеспечивается с помощью дополнительных модулей расширения.
В модульном варианте контроллер LOGO! можно реализовать с 24 дискретными и 8 аналоговыми входами, а также 16 дискретными выходами. Напряжение питания входных цепей в LOGO! соответствует напряжению питания модуля, которое может быть 12/24 В постоянного тока, 24 и 230 В пере-
61
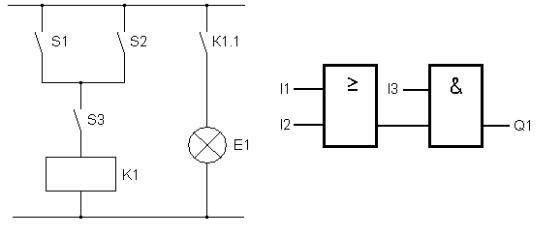
менного тока. Выходы могут быть транзисторными или релейными. Нагрузочная способность последних (до 10 А) обеспечивает непосредственное подключение достаточно мощных исполнительных устройств. Кроме того, к такому микроконтроллеру можно подключить коммуникационные модули для работы в сетях. Существуют логические модули с дисплеем и клавиатурой и без них.
Главной особенностью микроконтроллеров LOGO! является то, что схема релейной автоматики собирается из программно реализованных функциональных блоков. В распоряжении пользователя имеется восемь логических функций типа И, ИЛИ и т.п., большое число типов реле, в том числе реле с задержкой включения и выключения, импульсное реле, реле с самоблокировкой, а также такие функции, как выключатель с часовым механизмом, тактовый генератор, календарь, часы реального времени и др.
Рассмотрим на примере, как в LOGO! представляется обычная коммутационная схема, приведенная на рис. 1.33. На ней потребитель Е1 включается и выключается с помощью выключателей S1, S2 и S3. Реле К1 срабатывает, когда замкнут хотя бы один из выключателей S1 или S2 и обязательно S3. В LOGO! указанная схема реализуется двумя последовательно соединёнными логическими блоками OR (ИЛИ) и AND (И). Выключатель S1 подключается ко входу I1 модуля, выключатель S2 – ко входу I2, S3 – к I3, а потребитель Е1 подключается к релейному выходу Q1.
Р и с. 1.33. Типовая коммутационная схема и ее реализация с помощью LOGO!
Программирование модулей LOGO!, а точнее – ввод схемы, может выполняться с помощью встроенных клавиатуры и дисплея. Оно сводится к выбору необходимых функциональных блоков, соединению их между собой и заданию параметров настройки блоков (задержек включения/выключения, значений счётчиков и т.д.). Для хранения управляющей программы в модуле имеется встроенное энергонезависимое запоминающее устройство. Создание резервной копии программы, а также перенос ее в другие LOGO! может быть осуществлён с помощью специальных модулей памяти, устанавливаемых в интерфейсное гнездо.
62
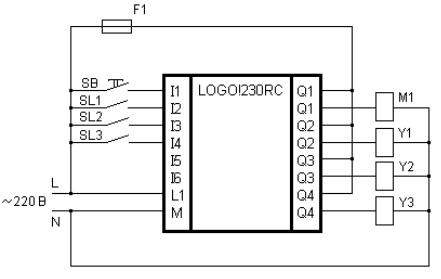
Однако ввод программы с панели управления является делом неблагодарным и может быть оправдан только для небольших по объёму программ или
вслучае острой необходимости внесения корректив в уже работающую программу непосредственно на объекте. А учитывая то, что программу всё равно предварительно приходится прорисовывать на бумаге, становится очевидным необходимость использования специализированного программного продукта –
вданном случае пакета LOGO!Soft Comfort. Этот пакет позволяет разрабатывать в графической форме и документировать программы для LOGO! на компьютере и, кроме того, отлаживать их в режиме эмуляции логического модуля. Выбранные функциональные блоки мышью перетаскиваются на рабочее поле, затем соединяются и параметрируются. Для каждого функционального блока может быть написан комментарий, который существенно облегчит понимание принципа работы программы другому пользователю или поможет самому разработчику через некоторое время вспомнить собственные замыслы. При вводе программы будут автоматически контролироваться все имеющиеся ограничения по объёму памяти и возможности использования тех или иных функций. Имеет смысл разработанную программу протестировать с помощью встроенного эмулятора контроллера. Если по результатам эмулирования корректировка программы не требуется, то её можно загрузить в память LOGO! с помощью специального кабеля, подключаемого к тому же интерфейсному гнезду, что и модули памяти.
Вернемся вновь к рассматриваемому ранее примеру. Посмотрим, как контроллер может облегчить жизнь разработчику системы управления смесительной установки.
Висходном варианте система управления смесительной установкой с использованием контроллера LOGO! реализуется очень просто. На рис. 1.34 приведена схема подключения контроллера, а на рис. 1.35 блок-схема программы.
Р и с. 1.34 Схема подключения
63
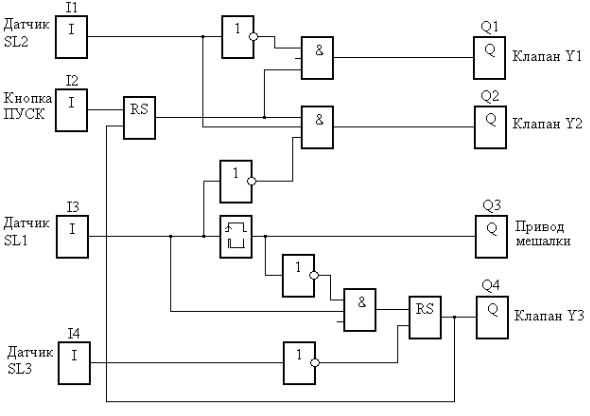
Р и с. 1.35. Блок-схема программы
Теперь посмотрим, как с помощью модуля LOGO! могут быть реализованы новые функции системы управления. Для дозирования компонентов в зависимости от их физико-химических свойств могут быть использованы различные методы, такие как, например, измерение расхода или уровня. Обработка импульсного сигнала с выхода счетчика (расходомера) в LOGO! легко реализуется с помощью функционального блока «Реверсивный счетчик», изображение которого приведено на рис. 1.36. Значение параметра блока определяет число импульсов, соответствующее необходимому количеству компонента в смеси. Это значение может быть фиксированным или задаваемым с панели управления. Выход счетчика может быть подключен к любому дискретному входу
LOGO!
64

Р и с. 1.36. Функциональный блок «Реверсивный счетчик»
Аналоговый сигнал от уровнемера может быть подан на один из входов I7 или I8 базового модуля LOGO! (сигнал 0 - 10 В) или аналогового модуля расширения АМ2 (сигнал 4 - 20 мА) и обработан функциональным блоком «Аналоговый компаратор» (рис. 1.37). При этом значение сигнала может быть выведено на дисплей модуля. Как и в предыдущем случае, значение параметра блока определяет количество того или иного компонента смеси. Это значение также может быть фиксированным или оперативно изменяемым с помощью панели управления LOGO!.
Р и с. 1.37. Функциональный блок «Аналоговый компаратор»
Время работы мешалки, как и в исходной программе, определяется функциональным блоком «Таймер», параметр которого также может быть оперативно изменён обслуживающим персоналом установки.
И, наконец, если переход от одной рецептуры смеси и технологии её приготовления к другой не может быть выполнен простым изменением параметров, то достаточно будет оформить рецепты в виде отдельных программ,
65
записать их в модули памяти и активизировать путём замены одного модуля памяти на другой.
Siemens начала массовое производство LOGO! в 1996 году. Что же предлагается потребителю сегодня? В первую очередь, это мощный 32-разрядный процессор и усовершенствованная архитектура программы, что обеспечило высокое быстродействие и соответственно более короткий цикл работы программы контроллера. Значительный объем памяти дает возможность использовать в программе до 130 функциональных блоков, а также снимает ограничения на максимальное количество в одной программе таймеров, счётчиков, часов, аналоговых триггеров и некоторых других блоков.
В LOGO! применён дисплей в котором имеются 4 строки по 12 знакомест в каждой. Для удобства использования в тёмное время суток или в условиях с недостаточным освещением дисплей снабжён системой задней подсветки. В одной строке дисплея могут быть одновременно отображены и текстовое сообщение, и текущее значение величины, и значение параметра настройки, которое может быть еще и оперативно изменено. Общее количество текстовых сообщений, используемых в одной программе, до 10. Появилось несколько новых функций, в частности, 8-разрядный регистр сдвига, аналоговый усилитель, аналоговый дифференциальный триггер и др. Не осталось без изменений и программное обеспечение. В новой версии пакета LOGO!Soft Comfort учтены все изменения аппаратного обеспечения модулей LOGO! и, кроме того, в нее добавлены новые возможности. При создании программы пользователь теперь может, кроме языка FBD, использовать и язык – LAD. Клавиши управления курсором могут быть задействованы в программе в качестве входов, что в некоторых случаях позволяет отказаться от подключения дополнительных внешних кнопок. Функциональные блоки могут иметь редактируемые 8-символьные имена вместо имевших место буквенно-цифровых номеров. Новое программное обеспечение позволяет осуществлять отладку программы в реальном времени на работающем устройстве.
Рассмотрим более конкретно основные характеристики, параметры LOGO! и их исполнение.
Маркировка модулей несет информацию об их конструктивных особен-
ностях:
•12: модуль с напряжением питания 12 В пост. тока;
•24: модуль с напряжением питания 24 В пост,;
•230: модуль с напряжением питания 115/230 В переменного тока;
•R: модуль с релейными выходами;
•С: модуль со встроенными часами;
•о: без дисплея и клавиатуры (LOGO!Pure);
•L: 12 входов и 8 выходов (LOGO!Long);
•AS: модуль с интерфейсом AS-i (LOGO!Long Bus).
Базовые варианты модулей (LOGO!Basic) имеют 6 входов и 4 выхода. В версиях с напряжением питания 12 и 24 В имеется два дополнительных аналоговых входа (0 - 10 В), которые могут использоваться и как цифровые. Логиче-
66
ские модули LOGO!Pure являются функциональными аналогами LOGO!Basic, но в отличие от них не имеют встроенного дисплея и клавиатуры. Варианты LOGO!Long и LOGO!Long Bus имеют 12 входов и 8 выходов. Все варианты имеют:
•релейные выходы с нагрузочной способностью до 10 А для активной нагрузки (до 3 А для индуктивной), кроме LOGOI24/24L, имеющих транзисторные выходы (24 В/0,3 А);
•разъем для подключения внешнего модуля памяти или компьютера;
•встроенные часы реального времени (кроме LOGOI24/24L);
•8 основных и 21 специальную функции;
•максимальный объём программы до 56 функциональных блоков;
•крепежный узел для монтажа на 35 мм профильную DIN-шину;
•диапазон рабочих температур от 0 до 55°С;
•степень защиты корпуса IP20.
Зачастую при решении задачи автоматизации возникает потребность в контроле температуры. Специализированный аналоговый модуль АМ2 PtlOO предназначен для непосредственного подключения двух термометров сопротивления PtlOO для контроля температуры в диапазоне от -50 до +200°С. С помощью LOGO! можно обеспечить и регулирование температуры. Такая задача решается с помощью обычного двухпозиционного регулятора, реализуемого с помощью платинового термометра сопротивления, аналогового модуля АМ2 PtlOO и функционального блока «Аналоговый триггер». Сигнал с выхода этого блока будет являться управляющим для электрического нагревателя. Конечно, качество регулирования будет далеко не идеальным, но для многих применений оно может оказаться вполне приемлемым.
Подобные контроллеры выпускают многие фирмы. Следующим примером таких контроллеров может служить программируемое реле ZEN фирмы
OMRON
Программируемые реле ZEN это компактный контроллер для локальной автоматизации. Процессорный блок имеет 6 универсальных входов и 4 релейных выхода. Имеется возможность добавить до трех блоков расширения, тем самым можно автоматизировать объекты, имеющие до 34 точек ввода/вывода. Выходы на блоках расширения изолированы и обладают высокой коммутационной способностью 8 А при 250 В переменного тока 5 А при 24 В постоянного тока. Встроенные блоки питания у ZEN работают при напряжениях 100 - 240 В переменного тока и 24 В постоянного тока. Модели с блоком питания на 24 В имеют 2 аналоговых входа 0–10 В постоянного тока. Контроллер имеет встроенный календарь и часы, многорежимные таймеры, инкрементальные и декрементальные счетчики. Существует два типа процессорных блоков: с жидкокристалическим дисплеем (LCD-тип) и кнопками программирования и более простая модель без дисплея (LED-тип). Есть возможность установки пароля
Для удобства отладки и написания программ разработчики предусмотрели пакет программирования, который не требует существенных ресурсов
67
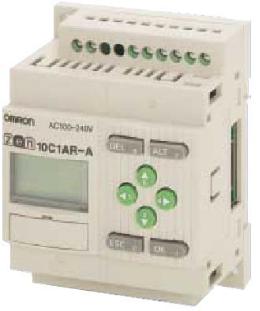
компьютера и является простым инструментом для всех категорий специалистов.
Рабочая температура от –25 до +55оС. Монтаж осуществляют на DIN рейку. Размер – 70 х 90 х 56 мм. Внешний вид ZEN (рис. 1.38) схож с внешним видом контроллера LOGO!
Р и с. 1.38. Внешний вид программируемого реле ZEN фирмы OMRON
11.1.3 Контроллеры фирмы Siemens серии SIMATIC S7-200
Типизация и стандартизация постепенно охватывает все стороны организации универсальных контроллеров. Выше уже было показано, что программирование универсальных контроллеров осуществляется с помощью типовых языков. Это во многом предполагает использование в них и одинаковых типов переменных и способов адресации к ним и многого другого. Ниже на примере контроллеров фирмы Siemens будет осуществлено знакомство с подобными типовыми решениями.
Семейство контроллеров SIMATIC S7 фирмы Siemens состоит из нескольких подклассов, отличающихся друг от друга вычислительной мощностью и широтой функциональных возможностей.
Общая характеристика контроллеров семейства SIMATIC S7-200.
Контроллеры SIMATIC S7-200 предназначены для решения задач управления и регулирования в небольших системах автоматизации. При этом SIMATIC S7200 позволяют создавать как автономные системы управления, так и системы управления, работающие в общей информационной сети. Обладает модульной
68