
Медноникелевые сплавы применяются в химической технике в качестве конструкционных материалов, работающих в агрессивных средах. Основными медноникелевыми сплавами этой группы являются:
монель-металл (НМЖМц28-2,5-1,5) и хастеллой (Н70МФВ-ВИ, ХН58В, ХН65МВУ), использующиеся для изготовления элементов химической аппаратуры, работающей в средах – сильных восстановителях;
мельхиор (МНЖМц30-1), нейзильбер (МНЦ15-20), применяющиеся для изготовления химической аппаратуры, работающей с сильными минеральными кислотами, щелочами, растворами, содержащими ионы хлора.
2.5. Титан и сплавы на его основе
Чистый титан марок ВТ1-00 и ВТ и титановые сплавы, обрабатываемые давлением, марок ОТ4-0, ОТ4-1, ОТ4 (легированы Мn и Al), ВТ5, ВТ14, ВТ20 (легированы Al, V, Сr, Mo, Zr, Fe), ПТ-7М, ПТ-ЗВ (легированы Al, V, Zr) соответствуют по химическому составу ГОСТ 19807 и используются для изготовления ответственных элементов оборудования, работающих в окислительных средах.
Титан и его сплавы при умеренных температурах превосходят по коррозионной стойкости большинство легированных сталей. Коррозионная стойкость этих конструкционных материалов обусловлена образованием весьма прочной и плотной оксидной пленки TiO2, надежно защищающей эти материалы от взаимодействия с окружающей коррозионной средой.
Технический титан и его сплавы обладают и другими ценными технологическими и физико-механическими свойствами: сохраняют работоспособность при нагреве до температур 550...600 °С. Механическая прочность титана и его сплавов соизмерима с прочностью конструкционных сталей при существенно меньшей плотности. Для этих материалов характерна хорошая или удовлетворительная свариваемость, подверженность большинству известных видов обработки давлением, особенно в горячем состоянии. Недостатками титана и его сплавов следует считать низкую теплопроводность, малый модуль упругости, трудность обработки резанием и получения фасонных отливок. Из титана и его сплавов изготавливают фильтры, автоклавы, емкостные аппараты, детали насосов, компрессоров и центрифуг, теплообменники, трубопроводы и арматуру для агрессивных сред и т. п.
В химическом машиностроении наибольшее распространение получили следующие марки титана и его сплавов, чистый титан марок ВТ1-00 и ВТ и титановые сплавы марок ОТ4-0, ОТ4-1, ОТ4 (легированы Мn и Al),
ВТ5, ВТ14, ВТ20 (легированы Al, V, Сr, Mo, Zr, Fe), ПТ-7М, ПТ-ЗВ (легированы Al, V, Zr).
21
3. КОЛОННЫЕАППАРАТЫМАССООБМЕННЫХПРОЦЕССОВ
В условиях многообразия продукции химической, нефтехимической, нефтеперерабатывающей и других смежных отраслей промышленности ее часто получают в виде смесей жидких компонентов, из которых необходимо выделить затем тот или иной компонент в чистом виде.
Для грубого разделения двух взаимно растворимых жидкостей применяют простую перегонку, основанную на различной температуре кипения компонентов данной смеси.
Для качественного разделения взаимно растворимых смесей применяют ректификацию.
Ректификация – процесс разделения жидких однородных смесей на составляющие вещества или группы составляющих веществ в результате противоточного взаимодействия паровой и жидкой смесей.
Около 60 % изготовляемых аппаратов в стране для абсорбции и ректификации представляют собой тарельчатые колонны, остальные – насадочные колонны. При правильной организации гидродинамики процесса насадочные колонны более экономичны, чем тарельчатые. Колонные аппараты конструктивно состоят из унифицированных и стандартных элементов: крышек, обечаек, днищ, штуцеров, фланцев, люков, опор, внутренних устройств.
Корпуса колонных аппаратов изготовляют трех типов:
1)из отдельных царг, соединяемых между собой фланцами на про-
кладках;
2)цельносварные с крышкой на фланцах (для осмотра в корпусе предусматриваются смотровые люки);
3)цельносварные с приваренными верхним и нижним днищами (для монтажа и демонтажа тарелок предусмотрены люки-лазы).
3.1. Тарельчатые аппараты
Тарельчатые колонные аппараты, применяемые в нефтеперерабатывающей и нефтехимической промышленности, – один из важнейших видов технологического оборудования, от работы которого в значительной степени зависит качество получаемых продуктов. Удельный объем тарельчатых колонных аппаратов составляет по весу не менее 25 % от общего объема нефтеперерабатывающего и нефтехимического оборудования. В тарельчатых колоннах взаимодействие пара и жидкости осуществляется на специальных барботажных устройствах – тарелках.
Тарельчатые колонные аппараты состоят из вертикального корпуса, сферической или эллиптической крышки, днища и жестко скрепленной с корпусом опорной обечайки цилиндрической или конической формы.
22
Использование конических опор для высоких колонн небольшого диаметра способствует повышению их устойчивости и уменьшению нагрузки на опорную поверхность фундаментального кольца. Внутри корпуса колонны смонтированы тарелки, устройство для ввода сырья, отбойное устройство и штуцера для жидкости и пара.
Для удобства монтажа и ремонта тарелок расстояние между ними желательно принимать не менее 450 мм. Монтаж и обслуживание тарелок
ваппаратах с цельносварным корпусом выполняют через люки. Люки на корпусе рекомендуется располагать через каждые пять-десять тарелок в зависимости от диаметра аппарата и типа контактных устройств. Диаметр люков может колебаться от 450 мм до 600 мм, а расстояние между тарелками в месте установки люка – от 800 мм до 1000 мм.
Корпуса тарельчатых колонных аппаратов изготавливаются большей частью с постоянным по высоте диаметром, хотя для колонн больших размеров, в случае, если нагрузка по жидкости и пару значительно меняется по высоте, корпус изготавливают из частей разного диаметра, соединенных конусными переходами.
На корпусе колонны предусматриваются штуцера для ввода продукта и вывода пара, ввода флегмы и пара из кипятильника, вывода кубового остатка и циркулирующей кубовой жидкости в кипятильник. Кроме того, аппарат снабжают штуцерами для измерения давления и температуры по высоте аппарата, уровня жидкости, отбора проб и др.
Корпуса аппаратов, работающих при больших рабочих давлениях, а также аппаратов диаметром более 1200 мм выполняют цельносварными.
Втарельчатых аппаратах поверхность контакта фаз развивается потоками газа, распределяющегося в слое жидкости, находящейся на тарелке,
ввиде пузырьков и струй. Такое явление носит название барботаж.
Внасадочных колоннах контакт газа (пара) и жидкости осуществляется по схеме противотока. Интенсивность контакта зависит от гидродинамического режима. При малых нагрузках по газу жидкость стекает по насадке в виде тонких ламинарных пленок, поверхность межфазного контакта при этом не развита. Такой режим называется пленочным. Повышение скорости газа приводит к увеличению сил трения и турбулизации потоков стекающей жидкости и поднимающегося газа. В результате этого жидкость подвисает в насадке и более равномерно распределяется по сечению колонны, наступает режим барботажа, что приводит к увеличению поверхности межфазного контакта. Переход от пленочного режима к режиму подвисания принимается за нижний предел устойчивой работы насадочной колонны.
При дальнейшем увеличении скорости движения газа по сечению колонны движение жидкости становится турбулентным, она дробится на тонкие пленки, пронизываемые газом, поверхность межфазного контакта
23
вновь дополнительно увеличивается. Начиная с некоторой скорости газа, заметно возрастает количество жидкости, удерживаемой в насадке, а в верхней части слоя насадки появляется барботирующий слой жидкости. Общее гидравлическое сопротивление слоя резко возрастает. Это явление называют режимом захлебывания.
Оптимальной скоростью движения газа по сечению колонны принято считать скорость на 15 - 20 % ниже скорости захлебывания, так как при данной скорости развивается высокая поверхность контакта фаз, а пульсаций в колонне не наблюдается.
Колонны с тарелками, или тарельчатые колонны, являются эффективными и наиболее распространенными аппаратами. Они выполняются в виде вертикальных цилиндров, внутри которых одна под другой размещено определенное количество горизонтальных тарелок различных конструкций, обеспечивающих контакт газа (пара) и жидкости.
Различают тарельчатые колонны с переливными устройствами и колонны с неорганизованным переливом жидкости, или с провальными тарелками.
По конструкции корпусов различают в основном три типа колонн:
1)корпус собран из отдельных царг, соединяемых между собой фланцами на прокладке; крышку и днище крепят таким же способом; в таком корпусе не устраивают люков-лазов;
2)корпус цельносварной: крышку крепят с помощью фланцевого соединения; для осмотра в корпусе предусматривают смотровые люки;
3)корпус цельносварной; крышка и днище приварные; обязательно имеются люки-лазы.
На рис. 3.1 представлена конструкция колпачковой царговой колонны. В отдельной царге помещают обычно 4 - 6 тарелок. Царговая конструкция позволяет свободно монтировать и разбирать внутренние устройства колонн (переливы, приемные карманы, контактные устройства, уплотнения тарелок).
Колонный аппарат состоит, как правило, из вертикального корпуса 3, сферической или эллиптической крышки 4, днища 2 и жестко скрепленной
скорпусом опорной обечайки 1 цилиндрической или конической формы. Использование конических опор способствует повышению устойчивости. Внутри корпуса колонны смонтированы тарелки 9, устройство для ввода сырья и штуцеры для вывода жидкости и пара.
Упорные кольца 8 предназначены для герметизации тарелок. В зазоре между тарелкой и корпусом колонны установлены прокладки 7 из асбестового шнура, закрепленные нажимным кольцом 6, скобами 10 и шпильками 11. Царги соединяются между собой с помощью фланцев 13.
24
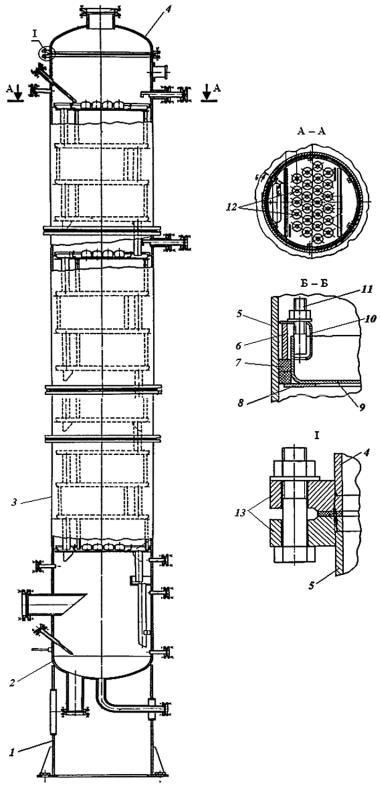
Рис. 3.1. Колонна тарельчатая царговая: 1 – опора; 2 – днище; 3 – царга; 4 – крышка;
5 – корпус царги; 6 – кольцо нажимное; 7 – уплотнение; 8 – упорное кольцо; 9 – тарелка; 10 – скоба; 11 – шпилька; 12 – колпачки, 13 – фланец
25

3.2. Насадочные аппараты
Насадочные аппараты – колонные аппараты, предназначенные для интенсификации тепло- и массообмена и обеспечения однородных гидродинамических условий проведения химико-технологических процессов. С этой целью часть объема насадочных аппаратов заполнена слоями твердых тел различных размеров и формы – неподвижными и подвижными насадками, которые служат для создания развитой поверхности контакта между взаимодействующими потоками в гетерогенных системах, главным образом газ (пар) - жидкость. В насадочных аппаратах неподвижная насадка засыпается на опорные решетки, имеющие отверстия для стока жидкости и прохождения газа (рис. 3.2).
Рис. 3.2. Насадочный аппарат: 1 – насадка;
2 – опорная решетка;
3 – разбрызгиватель;
4 – перераспределительная жидкость
Жидкость подается на насадку сверху при помощи специальных распределительных устройств. По всей высоте насадки равномерное распределение жидкости невозможно, что объясняется так называемым пристеночным эффектом – большей плотностью загрузки насадки в центральной части аппарата, чем около его стенок, вследствие чего жидкость стремится растекаться в направлении от центра к периферии. Для предотвращения этого и улучшения смачивания насадки ее зачастую укладывают не сплошь на всю высоту, а отдельными слоями (секциями) высотой 1,5 - 3,0 м, и под каждым из них, кроме нижнего, размещают направляющие устройства. Газ и жидкость движутся, как правило, противотоком; используют также насадочные аппараты с прямоточным (нисходящим) движением фаз при высо-
26
кой скорости газа (до 10 м/с). В слое насадки жидкость стекает по ее элементам главным образом в виде тонкой пленки, и поверхностью контакта фаз является в основном смоченная поверхность насадки, поэтому насадочные аппараты можно рассматривать как разновидность пленочных аппаратов. При перетекании жидкости с одного элемента насадки на другой жидкая пленка разрушается, и на нижележащем элементе образуется новая пленка. При этом часть жидкости проходит в виде струй и капель через расположенные ниже элементы насадки, а некоторое количество задерживается в ней вследствие смачивания поверхности и скопления в узких каналах, образуемых соприкасающимися насадочными телами, что приводит к увеличению гидравлического сопротивления и снижению эффективности массообмена.
В зависимости от скорости газа насадочные аппараты могут функционировать в следующих гидродинамических режимах: пленочном, подвисания, эмульгирования и брызгоуноса. Пленочный режим наблюдается при малой скорости газа, а также небольшой плотности орошения насадки (объем жидкости, проходящей через единицу площади поперечного сечения аппарата в единицу времени). В таком режиме скорость газа практически не влияет на количество задерживаемой в насадке жидкости.
С возрастанием скорости газа при противотоке фаз сила трения между ними увеличивается, жидкость движется медленнее и быстро накапливается (подвисает) в насадке. В режиме подвисания спокойное течение жидкой пленки нарушается (возникают завихрения, брызги) и газ начинает проходить через слой жидкости в виде пузырьков (барботировать). В результате межфазная поверхность контакта и соответственно интенсивность массообмена значительно возрастают при одновременном резком увеличении гидравлического сопротивления.
Накопление жидкости в насадке происходит до тех пор, пока сила трения между поднимающимся по колонне газом и стекающей жидкостью не уравновесит силу тяжести жидкости, находящейся в насадке. При этом наступает режим эмульгирования, характеризующийся инверсией фаз (газ становится дисперсной фазой, а жидкость – сплошной) и образованием га- зо-жидкостной эмульсии. Для обеспечения нормального проведения хими- ко-технологических процессов в этом режиме, который отвечает максимум эффективности тепло- и массообмена и одновременно относительно большому гидравлическому сопротивлению, разработаны специальные аппараты с искусственно затопленной насадкой. В режимах подвисания и эмульгирования целесообразно работать, если повышение гидравлического сопротивления не играет существенной роли, например в абсорбционных процессах, осуществляемых при высоких давлениях. В насадочных аппаратах, действующих при атмосферном давлении, гидравлическое сопротивление может оказаться недопустимо большим, что приведет к необхо-
27
димости проводить процесс в пленочном режиме. Поэтому в каждом конкретном случае оптимальный гидродинамический режим можно установить только технико-экономическим расчетом. При дальнейшем увеличении скорости газа сила трения между фазами становится больше силы тяжести, жидкость перестает стекать, выбрасывается из насадки (наступает так называемое захлебывание) и выносится из верхней части аппарата в виде брызг газовым потоком (режим брызгоуноса). На практике этот режим не используется. Для работы с загрязненными газами и жидкостями применяют аппараты с подвижной насадкой, сравнительно легкие элементы которой поддерживаются потоком газа во взвешенном (псевдоожиженном) состоянии. Положение слоя взвешенных элементов фиксируется нижней (опорной) и верхней (ограничительной) решетками. В аппаратах с несколькими слоями насадки верхняя решетка нижерасположенного слоя служит опорой для вышерасположенного. Высота слоя насадки в неподвижном состоянии (без газового потока) 0,2 - 0,3 м, расстояние между решетками 1 - 1,5 м. Для улучшения контакта между газом и жидкостью в аппаратах большого диаметра пространство между решетками разделяют вертикальными перегородками на прямоугольные отсеки. С целью улучшения распределения жидкости и уменьшения брызгоуноса предложены конические аппараты, в которых сечение возрастает по ходу газа.
Аппараты с подвижной насадкой могут функционировать при больших скоростях газа без захлебывания и обеспечивают более высокий коэффициент массопередачи, однако характеризуются большим гидравлическим сопротивлением, значительным брызгоуносом и износом насадочных тел. Для эффективной работы насадочных аппаратов насадки должны удовлетворять следующим основным требованиям: иметь большую поверхность, хорошо смачиваться орошающей жидкостью, оказывать малое гидравлическое сопротивление газовому потоку, равномерно распределять орошение, быть стойкими к химическому воздействию газа и жидкости, обладать малой материалоемкостью и высокой механической прочностью, иметь невысокую стоимость. Насадочные тела изготовляют обычно из металлов, стекла, керамики, пластмасс, дерева и загружают в аппараты навалом (нерегулярные насадки) либо укладывают или монтируют в определенном порядке, в частности в жесткую структуру (регулярные насадки).
Основные характеристики насадок – удельная поверхность и свободный объем. Под удельной поверхностью f понимают суммарную поверхность всех насадочных тел в единице объема аппарата (м2/м3). Чем больше f, тем выше эффективность работы насадки, но больше гидравлическое сопротивление и меньше производительность. Свободный объем e – суммарный объем пустот между насадочными телами в единице объема аппарата (м3/м3). Для непористой насадки е определяют, как правило, заполнением ее объема водой. Отношение объема воды к объему, занимаемому насад-
28
кой, дает величину e. Чем она больше, тем выше производительность, меньше гидравлическое сопротивление и эффективность насадки. Поскольку при тепло- и массообмене количество переносимых компонентов газа и жидкости или теплоты пропорционально поверхности контакта фаз, целесообразнее пользоваться мелкими насадками (размеры 20 - 30 мм), имеющими большую удельную поверхность. Коэффициент массопередачи, как правило, больше при наличии мелкой насадки. Однако с уменьшением размеров насадочных тел ухудшается их смачивание и уменьшается доля активной поверхности насадки, участвующая в массообмене. В мелких насадках эффективно смоченной бывает менее 50 %, а иногда даже менее 10 % всей поверхности. В крупных, особенно регулярных, насадках степень смоченности может достигать почти 100 %.
Элементы нерегулярных насадок выполняют в виде колец, спиралей, роликов, шаров, полусфер, седел и др. (рис. 3.3). Наиболее распространены кольца Рашига с высотой, равной диаметру. Известны модификации этой насадки с лучшими характеристиками, например кольца Палля и Лессинга. Среди седловидных насадок особенно широко применяют седла Берля, а также насадки Инталлокс. В лабораторных условиях используют насыпные сетчатые насадки типа колец Барада, пластмассовые розетки Теллера, насадки из проволочных геликоидов. В ряде случаев применяют кусковые насадки из кокса, кварца и т. д. Для аппаратов с подвижной насадкой, как правило, используют полые или сплошные шары из полиэтилена и других пластмасс, а также из пористой резины. Регулярные насадки в отличие от нерегулярных характеризуются низким гидравлическим сопротивлением и более высокой пропускной способностью. Простейшая регулярная насадка
– хордовая, представляющая собой ряд деревянных брусьев, закрепленных на некотором расстоянии друг от друга. Плоскопараллельная насадка изготовляется в виде набираемых из металлических листов пакетов, обычно устанавливаемых один на другой "крест-накрест". Сетчатые насадки могут быть пакетными (типа Зульцера и др.) и складчатыми, например в виде кубиков. Значительно проще в изготовлении, монтаже и эксплуатации, рулонные сетчатые насадки типа Гудлоу, Стедмена и т. п., выполненные из сетчатых лент специального плетения либо из гофрированной сетки, которая скатана в рулон диаметром, равным диаметру аппарата. Использование таких насадок позволяет существенно снизить влияние пристеночного эффекта и упростить сборку насадочных аппаратов. Трубчатые регулярные насадки – пучки вертикальных труб, которые касаются друг друга стенками или закрепляются в трубных досках с определенным шагом. Применяют также насадки, собираемые из гофрированных лент с противоположным наклоном гофр на смежных лентах. Эти типы насадок обладают сравнительно большой материалоемкостью, поэтому их иногда заменяют керамическими сотовыми блоками.
29
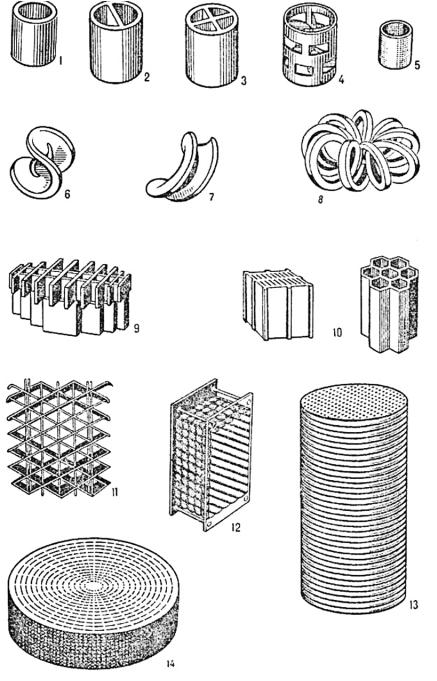
Рис. 3.3. Некоторые типы насадок: 1 - 5 – кольца соответственно Рашига, Лессинга, с крестообразной перегородкой, Палля, Барада; 6, 7 – седла соответственно Берля и Инталлокс; 8 – розетка Теллера; 9 – хордовая; 10 – керамические блочные; 11 – из перфорированных металлических листов (Спрейпак); 12 – Зульцера; 13 – Стедмена; 14 – Гудлоу
30