
помощью специальной программы, причём толщина каждого слоя равна разрешающей способности оборудования по координате Z. Затем осуществляется послойный синтез или послойное "выращивание" модели или готового изделия непосредственно по электронным данным без использования технологической оснастки. Преимуществами этой технологии являются скорость, точность и снижение затрат на НИОКР. Быстрое прототипирование особенно привлекательно для изготовления опытных,
единичных, эксклюзивных и уникальных образцов, поскольку не требует изготовления специальной оснастки и минимизирует ручной труд. Оно широко используется в:
машиностроении
электронной и электротехнической промышленностях
полиграфии
медицине
ювелирном деле
архитектурном моделировании и т.д.
Позволяет оценить внешний вид изделия, провести различные испытания и проверить изделие на наличие конструкторских ошибок; кроме того, быстрое прототипирование применяется для изготовления оснастки при необходимости изготовления партии деталей.
Схема всех установок для изготовления прототипов примерно одинакова: специальное математическое обеспечение установки разбивает модель на ряд плоских параллельных сечений, отстоящих друг от друга на малое (0,05 – 0,4 мм) расстояние, определяемое требованиями установки.
При этом каждое сечение исполнено с внешним и внутренним контурами различной сложности. Затем тонкий слой материала (ламинированной бумаги, бумаги, фотополимера, полимерного или металлического порошка,
101
полимерной нити, воска, специального силикатного песка и т. д.) наносят на рабочий стол (элеватор) установки, воспроизводя первое сечение изделия,
после чего элеватор смещается вниз на один шаг и наносится следующий слой, и так далее. Последовательное соединение (наслоение) плоских объектов-сечений приводит к синтезу изделия-прототипа.
Существует множество технологий быстрого прототипирования,
отличающихся друг от друга, главным образом, использующимися для прототипирования материалами и технологией нанесения слоёв:
стереолитография (Stereo Lithography Apparatus (SLA));
послойная заливка экструдируемым расплавом (Fused Deposition Modeling (FDM));
многоструйное моделирование (Multi Jet Modeling (MJM));
отверждение на твёрдом основании (Solid Ground Curing (SGC));
распыление термопластов (Ballistic Particle Manufacturing (BPM));
селективное лазерное спекание (Selective Laser Sintering (SLS));
послойное формирование изделий (Laminated Object Modeling
(LOM))
Ниже представлена краткая информация некоторых из методов. Более подробно можно узнать на этом сайте: https://stanko- arena.ru/article/tekhnologii-bystrogo-prototipirovaniya-.html
Технология стереолитографии StereoLithography (SLA).
В основу процесса положено отвердение жидкого фоточувствительного полимера под действием экспонирования ультрафиолетового излучения
(UV). В основном технология используется для получения прототипов с целью проверки конструкции и собираемости, а также мастер-моделей для последующего тиражирования в силиконовых формах. Используемые расходные материалы позволяют получать функциональные прототипы с
102
различными физико-механическими свойствами, температурной стойкостью,
прозрачностью и т.д.
Прототип создается на платформе, перемещающейся в направлении оси построения моделей (Z) и находящейся внутри ванны с жидким полимером. Ультрафиолетовое излучение вырабатывается гелиево-
кадмиевым либо аргон-ионным неподвижным излучателем (лазерной пушкой) и позиционируется на поверхности полимера при помощи подвижного зеркала. Поглощение и рассеивание светового пучка происходит непосредственно вблизи поверхности, в результате чего образуются трехмерные пиксели (объемные элементы).
Метод послойного синтеза
Является наиболее распространенным. С его помощью могут быть получены модели-прототипы практически неограниченной сложности. При этом математическая модель изделия должна передаваться в установки в виде STL файлов. Специальное математическое обеспечение установок разбивает модель на ряд плоских параллельных сечений, отстоящих друг от друга на малое (0,05-0,4 мм) расстояние, определяемое требованиями установки. При этом каждое сечение исполнено с внешним и внутренним контуром, а контуры могут быть различной сложности. Далее эти сечения последовательно воспроизводятся установками (как плоские объекты) из различных материалов: ламинированной бумаги, бумаги, фотополимера,
полимерного или металлического порошка, полимерной нити, воска,
специального силикатного песка. Последовательное соединение (наслоение)
плоских объектов-сечений приводит к синтезу изделия-прототипа.
Технология отверждения на твердом основании Solid Ground Curing
(SGC)
Cложный, многошаговый процесс (см. рис. 5). Компьютер разделяет модель на сечения (слои, поз. 1, рис. 5). Далее с помощью специального тонера на стеклянной пластине (2) создается изображение заданного слоя,
образующее его «фотомаску» - фотошаблон. Вначале на поверхность стола, а
103
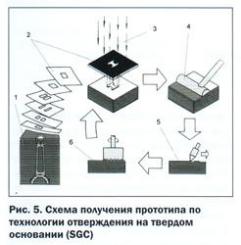
далее (после построения очередного слоя) на образованный слой наносится и выравнивается тонкий слой смолы (фотополимера, поз. 4, рис. 5). Над этим слоем и над находящимся над ним фотошаблоном (2) включают свет ультрафиолетовой лампы (поз. 3, рис. 5). В результате того что лампа включается лишь на несколько секунд, отвердевает только тот слой смолы,
фотомаска которого использовалась в данный момент. Неотвердевшая смола удаляется, полости заполняются расплавленным воском, который быстро затвердевает (поз. 5, рис. 5).
Созданный слой из отвердевшей смолы и воска выравнивают
(фрезеруют) до нужной толщины (поз. 6, рис. 5). Далее деталь вновь подвергается воздействию ультрафиолетового излучения для окончательного формирования слоя. Затем процесс повторяется: создается фотошаблон для следующего слоя (поз. 1, рис. 5), по уже сформированному слою распределяется новый слой жидкой смолы, и т.д.
Технология лазерного спекания - Selective Laser Sintering (SLS).
В основе этой технологии лежит спекание мелкодисперсных частичек расходного материала под воздействием С02 лазера. Расходный материал
(пудра) предварительно разогрет до температуры, близкой к температуре плавления материала (либо связующих элементов). Для данной методики нужны порошки мелкодисперсные, термопластичные, с хорошей вязкостью и быстро затвердевающие - например, полимеры, воск, нейлон, керамика,
104
различные специальные пластики (в том числе стеклонаполненные), песок и металлическая пудра.
В результате применения технологии можно получить функциональные прототипы пластиковых деталей, песчаные формы и стержни для металлургии, модели для литья по выплавляемым моделям, а
также металлические детали или фрагменты формообразующих элементов пресс-форм.
Технология послойной заливки экструдируемым расплавом - Fused
Deposition Modeling (FDM)
Основана на послойной укладке разогретой полимерной нити (рис. 1, а)
в соответствии с геометрией математической модели детали, разработанной в
CAD системе. FDM процесс предусматривает протягивание обжимными роликами через экструдер диаметром менее 0,178 мм нити из стирол-
бутадиен-акрилонитрила (СБА), поликарбоната, воска или эластомера. Нить при этом нагревается, переходит в полужидкое состояние и наносится на матрицу формируемого 3-мерного объекта в ходе построчного сканирования экструдером. Компоновочное вещество, осаждаясь на матрице объекта, при температуре окружающей среды быстро затвердевает.
Широкий набор основных цветов используемого материала (белый,
синий, желтый, черный, красный и зеленый) позволяет моделировать изделие любого цвета.
Процессор FDM системы управляет перемещением головки экструдера по трем осям и регулирует температуру нагрева подаваемого материала.
Особенность FDM системы - прецизионный нагрев материала до температуры, лишь незначительно превышающей температуру его затвердевания. Во многих FDM устройствах используется несколько бобин с различными по цвету или составу нитями, причем сменой бобин также управляет процессор. Время смены не превышает 1 мин.
105
Технология послойного формирования объемных моделей из
листового материала - Laminated Object Manufacturing (LOM).
Эта технология и установки для ее реализации были созданы в 1991 г.
фирмой Helisys, Inc. (США) и получили широкое распространение.
Установка, как и все остальные, использует CAD модель в виде STL файла.
Данные поступают на управляющий компьютер LOM установки, где с помощью специального программного обеспечения из CAD модели создается набор сечений детали. Модель выращивается из рулонной ламинированной бумаги или другого материала. Толщина листов зависит от материала и изменяется от 50 до 500 мкм. В настоящее время показана возможность использования следующих материалов: бумага, пластик,
керамика-композиты
12. Печать методом послойного наплавления.
Печать методом послойного наплавления (Fused deposition modeling –
FDM) .
FDM-принтеры предназначены для печати термопластиками, которые обычно поставляются в виде тонких нитей, намотанных на катушки.
К наиболее популярным материалам относится полилактид, или PLA-
пластик. Из ABS-пластика производятся многие пластиковые предметы,
применяемые повседневно: корпуса бытовых устройств, сантехника,
пластиковые карты, игрушки и т. д.
Кроме PLA и ABS возможна печать нейлоном, поликарбонатом,
полиэтиленом и многими другими термопластиками, широко распространенными в современной промышленности.
Экструдер
Экструдер – печатная головка FDM-принтера.
Экструдер предназначен для плавки и нанесения термопластиковой нити.
Первый компонент – механизм подачи нити, состоящий из валиков и
106
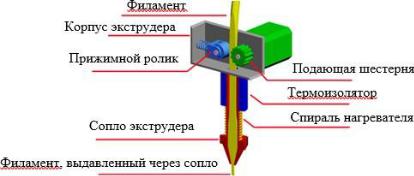
шестерней, приводимых в движение электромотором. Механизм осуществляет подачу нити в специальную нагреваемую металлическую трубку с соплом небольшого диаметра, называемую хот-энд или просто сопло. Тот же механизм используется и для извлечения нити, если необходима смена материала.
Сопло служит для нагревания и плавления нити, подаваемой протягивающим механизмом. Нагревание сопла регулируется термистором.
Регулировка температуры очень важна, так при перегреве материала может произойти пиролиз, т. е. разложение пластика, что способствует как потере свойств самого материала, так и забиванию сопла. Для того чтобы нить не расплавилась слишком рано, верхняя часть сопла охлаждается с помощью радиаторов и вентиляторов.
Рабочая платформа
Построение моделей происходит на специальной платформе, зачастую оснащаемой нагревательными элементами (рис. 6.5). Подогрев требуется для работы с целым рядом пластиков, включая популярный ABS,
подверженных высокой степени усадки при охлаждении.
107
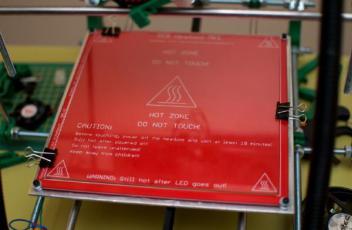
Рис. 6.5. Подогреваемая платформа, накрытая съемным стеклянным рабочим столиком
Платформа требует калибровки перед печатью, чтобы сопло не задевало нанесенные слои и не отходило слишком далеко, вызывая печать «по воздуху», что приводит к образованию «вермишели» из пластика.
Как правило, платформы оснащаются дополнительным элементом – съемным столиком. Такая конструкция упрощает чистку рабочей поверхности и облегчает снятие готовой модели. Столики производятся из различных материалов, включая алюминий, акрил, стекло и пр. Выбор материала для изготовления столика зависит от наличия подогрева и расходных материалов, под которые оптимизирован принтер.
Механизмы позиционирования
Печатающая головка должна перемещаться относительно рабочей платформы, причем в отличие от обычных офисных принтеров позиционирование должно производиться не в двух, а в трех плоскостях,
включая регулировку по высоте.
108

Рисунок 6.6
Схема позиционирования может варьироваться. Самый простой и распространенный вариант подразумевает крепление печатающей головки на перпендикулярных направляющих, приводимых в движение пошаговыми двигателями и обеспечивающих позиционирование по осям X и Y.
Вертикальное же позиционирование осуществляется за счет передвижения рабочей платформы. С другой стороны, возможно передвижение экструдера в одной плоскости, а платформы – в двух (рис. 6.6).
Управление
Управление работой FDM-принтера, включая регулировку температуры сопла и платформы, темпа подачи нити и работы пошаговых моторов,
обеспечивающих позиционирование экструдера, выполняется достаточно простыми электронными контроллерами. Большинство контроллеров основываются на платформе Arduino, имеющей открытую архитектуру.
Программный язык, используемый принтерами, называется G-код (G-Code)
и состоит из перечня команд, поочередно выполняемых системами 3D-
принтера. G-код компилируется программами-«слайсерами» – стандартным
109
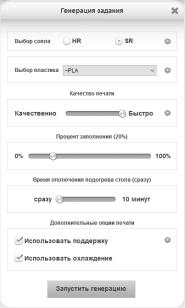
программным обеспечением 3D-принтеров, сочетающим некоторые функции графических редакторов с возможностью установки параметров печати через графический интерфейс.
13. Пакеты программ для проектирования печатных плат
радиоэлектронных средств.
1. «Sprint-Layout» – один из самых простых, но в то же время крайне эффективных программных пакетов для проектирования и разводки печатных плат малой сложности. «Sprint-Layout» не содержит встроенного схемотехнического редактора (не поддерживает Net-листы), поэтому малопригоден для разводки печатных плат с большим количеством электронных компонентов. Основное достоинство программы «Sprint-
Layout» –интуитивно понятный интерфейс, включающий в себя лишь самые необходимые инструменты для подготовки печатных плат с ограничением на размер рабочего поля до 300 мм2.
2. EAGLE (Easily Applicable Graphical Layout Editor) – программный комплекс для разработки электрических схем и трассировки печатных плат электронных приборов. «Schematic Module», предназначенный для
разработки принципиальных электрических схем с помощью стандартных
110