
1481
.pdf2.4. Технологии сварки и пайки в вакууме
Технологии сварки в вакууме предназначены для получения неразъемных соединений элементов приборов, деталей (узлов) конструкций машин, используемых в точном машиностроении, микроэлектронике, при создании атомных реакторов, в аэрокосмической промышленности и других отраслях. Различают два основных вида сварки в вакууме – электронно-лучевая сварка (сварка плавлением) и термодиффузионная сварка(сварка давлением).
Электронно-лучевая сварка (Electron beam welding) осу-
ществляется при остаточном давлении газов 10–1−10–3 Па с помощью установок, включающих в себя вакуумную рабочую камеру, электронно-оптическую систему, формирующую электронный луч, различные приспособления для перемещения свариваемых деталей к электронно-оптической системе и вакуумную откачную систему. Установка включает в себя сварочный пост, энергокомплекс, вакуумную откачную систему, шкафы и пульт управления, комплект соединительных кабелей и трубопроводов. Установка позволяет выполнять линейную и круговую аксиальную сварку в вакууме при рабочем давлении в вакуумной камере 5·10–1−5·10–3Па.
Суть процесса заключается в использовании кинетической энергии потока электронов, движущихся с высокими скоростями в вакууме. Для снижения потерь кинетической энергии электронов при соударении с молекулами воздуха, а также для защиты катода от окисления в электронной пушке поддерживают остаточное давление порядка 10–2–10–4 Па.
При электронно-лучевой сварке проплавление имеет форму конуса (рис. 2.25). Процесс плавления металла происходит на передней стенке кратера, а расплавляемый металл перемещается по боковым стенкам к задней стенке, где происходит его кристаллизация.
Проплавление материала при электронно-лучевой сварке обусловлено, в основном, следующими факторами – давлением потока электронов, характером выделения теплоты в объеме
71

твердого металла, излучением и реактивным давлением вторичных и тепловых электронов и испаряющегося металла. Возможна технология сварки непрерывным электронным лучом, однако
|
|
|
при сварке |
|
легкоиспаряющихся |
|||||
|
|
|
металлов |
(магния, |
алюминия |
|||||
|
|
|
и др.) |
эффективность |
потока |
|||||
|
|
|
электронов и количество выде- |
|||||||
|
|
|
ляющейся |
в |
изделии |
теплоты |
||||
|
|
|
уменьшаются |
вследствие потерь |
||||||
|
|
|
энергии на ионизацию паров ме- |
|||||||
|
|
|
талла. В этом случае целесооб- |
|||||||
|
|
|
разно вести сварку импульсным |
|||||||
Рис. 2.25. |
Схема переноса |
электронным |
лучом |
|
с высокой |
|||||
плотностью |
энергии |
и |
частотой |
|||||||
жидкого |
металла |
при |
||||||||
импульсов 100–500 Гц, в резуль- |
||||||||||
электронно-лучевой сварке: |
||||||||||
1 – электронный луч; 2 – |
тате чего глубина |
проплавления |
||||||||
передняя |
стенка кратера; |
повышается. |
Тем |
не |
менее при |
|||||
3 – зона |
кристаллизации; |
правильной установке соотноше- |
||||||||
4 – путь движения жидкого |
||||||||||
ния времени паузы и импульса |
||||||||||
|
металла |
|
||||||||
|
|
можно |
сваривать |
очень тонкие |
||||||
|
|
|
листы, т.е. при импульсной сварке можно достаточно легко варьировать глубину проплавления. Протяженность зоны термического влияния уменьшается благодаря теплоотводу во время пауз. Однако при этом возможно образование так называемых «подрезов», которые могут быть устранены технологией сварки колеблющимся или расфокусированным лучом.
Основными параметрами режима электронно-лучевой сварки являются: ускоряющее напряжение, сила тока в луче, продолжительность импульсов и пауз, скорость перемещения луча по поверхности изделия, точность фокусировки луча (табл. 2.3) и степень вакууммирования.
Для перемещения луча по поверхности изделия используют либо перемещение изделия, либо самого луча с помощью отклоняющей системы. Отклоняющая система позволяет осущест-
72
влять движение луча вдоль и поперек шва или по заданной программе. Низковольтные установки используют при сварке металла толщиной свыше 0,5 мм для получения швов с отношением глубины к ширине до 8:1. Высоковольтные установки применяют при сварке более толстого металла с отношением глубины к ширине шва до 25:1.
Таблица 2.3
Рекомендуемые режимы вакуумной электронно-лучевой сварки
Металл |
Толщина, |
Режим сварки |
|
Ширина |
|
|
мм |
ускоряющее |
сила тока |
скорость |
шва, мм |
|
|
напряжение, |
луча, мА |
сварки, м/ч |
|
|
|
кВ |
|
|
|
W |
0,5 |
18–20 |
40–50 |
60 |
1,0 |
Ta |
1,0 |
20–22 |
75–80 |
50 |
1,5 |
|
1,0 |
20–22 |
50 |
50 |
1,5 |
Сталь |
1,5 |
18–20 |
50–60 |
60–70 |
2,0 |
типа 18-8 |
20,0 |
20–22 |
270 |
50 |
7,0 |
|
35,0 |
20–22 |
500 |
20 |
– |
Мо + W |
0,5 + 0,5 |
18–20 |
45–50 |
35–50 |
1,0 |
Основные типы сварных соединений, рекомендуемые для электронно-лучевой сварки, приведены на рис. 2.26. Перед сваркой требуется точная предварительная подсборка деталей (при толщине металла до 5 мм зазор не должен превышать 0,07 мм, при толщине до 20 мм – 0,1 мм) и точное позиционирование луча по оси стыка деталей (отклонение не более 0,2–0,3 мм).
При увеличенных зазорах (для предупреждения «подрезов») требуется дополнительный металл для формирования шва в виде технологических буртиков или присадочной проволоки. В случае применения проволоки появляется возможность металлургического воздействия на металл шва. Изменяя величину зазора и количество вводимого металла, можно довести количество присадочного металла в сварном шве до 50 %.
73
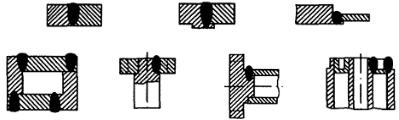
а |
б |
в |
г д е ж
Рис. 2.26. Основные типы соединений при сварке электронным лучом:
а– стыковое (может быть с отбортовкой для получения выпуклого шва);
б– замковое; в – стыковое для деталей разной толщины; г – различные варианты угловых; д, е – стыковые, при сварке шестерен с валами;
ж– стыковые, с отбортовкой кромок
Сварка электронным лучом в вакууме имеет значительные преимущества перед традиционными методами:
1.Высокая концентрация ввода тепловой энергии в изделие, которая выделяется не только на поверхности, но и на некоторой глубине в объеме основного металла изделия. Фокусировкой электронного луча можно получить пятно нагрева диаметром от 0,2 мкм до 5,0 мм, что позволяет за один проход сваривать металлы различной толщины – от десятых долей миллиметра до 200 мм. В результате можно получить швы, в которых соотношение глубины провара к ширине составляет до 20:1 и более. Имеется возможность сварки тугоплавких металлов (вольфрама, молибдена, тантала и др.), керамических материалов и т.д. Снижение протяженности зоны термического влияния понижает вероятность рекристаллизации основного металла в этой зоне.
2.Малое количество подводимой теплоты. Как правило, для получения равной глубины проплавления при электроннолучевой сварке требуется количество теплоты в 4–5 раз меньше, чем при дуговой сварке. В результате резко снижается коробление изделия и термическое воздействие на околошовную зону.
74
3. Отсутствие насыщения нагретого и расплавленного металла газами. Наоборот, в целом ряде случаев наблюдается явление дегазации металла шва и повышение его пластических свойств. В результате достигается высокое качество сварного соединения при сварке химически активных металлов и сплавов, таких как титан, цирконий, ниобий, молибден и др. Хорошее качество электронно-лучевой сварки достигается также на низкоуглеродистых и коррозионно-стойких сталях, а также меди, медных, алюминиевых и никелевых сплавах.
Недостатки электронно-лучевой сварки:
могут образовываться непроплавы и полости в корне шва при сварке металлов с высокой теплопроводностью и швах
сбольшим отношением глубины к ширине;
требуется длительное время для создания необходимого вакуума в рабочей камере после загрузки изделий.
Сначала 60-х гг. прошлого века электронно-лучевую сварку используют в производстве двигательных установок ракетно-космических комплексов (РКК). Применение элек- тронно-лучевой сварки для получения неразъемных соединений в сочетании с новыми высокопрочными материалами позволило создать двигатели нового поколения с высокими эксплуатационными характеристиками. В НПО «Техномаш» освоена локальная электронно-лучевая сварка в вакууме узлов значительных габаритов, таких как кольцевые секции топливных баков ракеты-носителя «Энергия» (рис. 2.27) из термически упрочняемого алюминиевого сплава 1201. Центральный блок ракеты-носителя «Энергия» связывает в единый пакет четыре блока первой ступени (четыре блока А) и орбитальный корабль, состоящий из топливных баков (кислородного и водородного), переходного силового отсека, хвостового отсека, двигательной установки и всех обеспечивающих функционирование ступени систем.
75
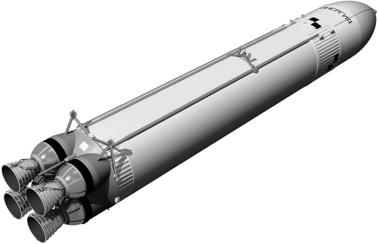
Рис. 2.27. Центральный блок Ц ракеты-носителя «Энергия»
Качество сварки зависит от внешней среды, поэтому технологическим проектом оценивался вариант создания камер общего вакуумирования. Однако он был практически сразу отвергнут из экономических соображений. Было принято направление создания электронно-лучевых сварочных установок с локальным вакуумированием места сварки. Сварочная установка «Луч-4» и дальнейшие ее модификации – «Луч-4М» и «Луч-4М2» с технологией сварки продольных сварных швов с локальным вакуумированием позволили достичь высокого качества сварных швов цилиндрических секций бака горючего блока Ц (рис. 2.28).
Новая перспективная область применения электроннолучевой сварки − проведение работ в условиях космического пространства. Электронно-лучевая сварка широко применяется в технологии микроэлектроники, а также при герметизации металлостеклянных корпусов электронных вакуумных приборов, для сварки разнородных, химически активных и тугоплавких материалов, стальных изделий.
76
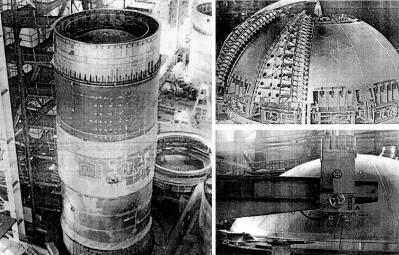
а б
Рис. 2.28. РКК «Энергия»: а – монтаж водородного бака второй ступени ракеты-носителя «Энергия»; б – стапель для сборки меридиональных швов сферических днищ баков со сварочными установками «Луч»
Явление диффузионной сварки было описано известным немецким металловедом Вольфгангом Зайтом еще в 1939 г. В 1953 г. профессором Н.Ф. Казаковым был разработан принципиально новый способ соединения материалов – диффузионная сварка в вакууме (ДСВ). При диффузионной сварке сварное соединение образуется в результате совместного воздействия давления и нагрева. Отличительной особенностью диффузионной сварки является применение относительно высоких температур нагрева и низких удельных давлений, обычно не превышающих предела текучести свариваемых материалов при температуре сварки.
Диффузионная сварка выполняется в вакууме при остаточном давлении 10–3−10–2 Па с нагревом места сварки до температуры до 0,4–0,8 от температуры плавления свариваемых материалов. При сварке разнородных материалов температура нагрева определяется по температуре плавления менее тугоплавкого
77
материала. Таким способом можно сваривать большинство твердых материалов − как однородных, так и разнородных.
При соединении трудносвариваемой пары материалов часто используются промежуточные слои: расплавляемые – припои
иэвтектические сплавы (например, титан – 7 % никеля), нерасплавляемые – порошки формиата никеля, ультрадисперсные порошки и пористые ленты из никеля, фольга никелевая, пермаллоевая и некоторых других пластичных металлов и их смесей, гальванические и вакуумные конденсационные покрытия никеля, молибдена, ниобия и т.п.
Диффузионная сварка обеспечивает вакуумно-плотные, термостойкие и вибропрочные соединения при сохранении высокой точности, геометрических размеров и формы изделия. Этот метод широко применяется в микроэлектронике при сварке термокомпенсаторов кристаллов, катодных ножек, замедляющих систем и других узлов и элементов электронных приборов.
Термодиффузионные сварочные установки обычно состоят из следующих основных узлов: вакуумной системы для получения вакуума в камере, где происходит сварка; системы для создания давления на свариваемые детали; системы для подъема
иопускания камеры; электропривода; автоматики для управления процессом и контроля параметров сварки (рис. 2.29). Одно из основных направлений дальнейшего развития термодиффузи-
онной сварки − использование технологических процессов с применением термокомпрессионных устройств (ТКУ), позволяющих осуществлять диффузионную сварку в вакуумных печах общепромышленного назначения (см. подразд. 2.2). Установка СДВУ-4М предназначена для диффузионной сварки высокочастотным нагревом в вакууме (1·10–1–1·10–3 Па) одновременно до 18 пластин из твердого сплава и быстрорежущей стали с резцедержателем, соединения одновременно до 8 заготовок из магнитной стали с армко-железом, керамических, металлокерамических, жаропрочных и других материалов.
78
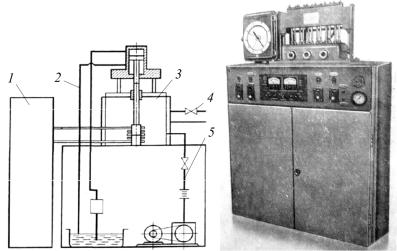
а |
б |
Рис. 2.29. Сварочнаятермодиффузионная установка: а– принципиальная схема: 1 – источник нагрева, 2 – система давления, 3 – рабочая камера, 4 – системаохлаждения, 5 – вакуумная система; б – внешний вид многопозиционной установки СДВУ-4М
Принцип действия ТКУ базируется на использовании разности коэффициентов термического линейного расширения (КТЛР) материалов свариваемых деталей и элементов оснастки для создания и передачи сжимающего усилия на свариваемые детали при их нагреве. В Московском авиационном институте (МАИ) разработано ТКУ, которое помещают в вакуумную камеру печи. Сдавливающее усилие, которое передается на свариваемые детали, возникает при нагревании устройства. По окончании сварки детали совместно с устройством охлаждают, в камеру напускают воздух, извлекают устройство с готовыми изделиями, после чего производят разборку устройства и удаляют сваренные детали. Разработанное ТКУ применяется для диффузионного соединения в вакууме изделий из магнитных и немагнитных сталей, алюминия, меди, нержавеющей стали, бронзы и других материалов.
79
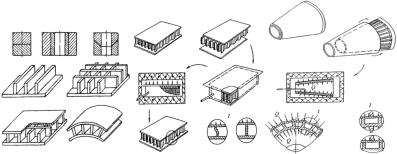
К основным преимуществам диффузионной сварки можно отнести отсутствие необходимости применять электроды, припои, флюсы, защитные газовые среды; в процессе сварки не происходит коробление деталей и изменение свойств металла в зоне соединения. Диффузионную сварку можно применять для получения конструкций самых разнообразных форм. Можно сваривать детали не только по плоскости, но и по сферической (подпятники), конической (корпуса радиоламп), криволинейной (облицовка труб) и сложной рельефной поверхности (слой защитного покрытия мембран) (рис. 2.30).
Рис. 2.30. Некоторые детали и узлы, получаемые диффузионной сваркой в вакууме
Пайка в вакууме − технологический процесс получения неразъемных соединений (из металлов и сплавов, керамики, стекла и других материалов) путем нагрева места пайки и заполнения зазора между соединяемыми деталями расплавленным припоем с его последующим отверждением. Для обеспечения прочного соединения при пайке деталей из разнородных материалов подбирают припои с близкими значениями коэффициента термического расширения или используют высокопластичные материалы. Технологически возможно совмещение вакуумной пайки с дегазационным отжигом. Существует два основных способа пайки в вакууме: пайка с локальным источником нагрева дуговым разрядом и высокотемпературная пайка.
80