
книги / Материаловедение. Теория легирования
.pdfВыполнить работу в следующем порядке:
1.Получить у преподавателя методические указания «Определение оптимальной температуры отпуска закаленной стали для получения заданного комплекса свойств» для общего курса «Материаловедение».
2.Выполнить все указанные там индивидуальные задания, вариант выбрать согласно порядковому номеру студента в журнале группы (полный пофамильный список группы).
3.Сделать выводы о проделанной работе.
Практическая работа № 8
ОПРЕДЕЛЕНИЕ ВИДА ОТПУСКНОЙ ХРУПКОСТИ ПО ХАРАКТЕРИСТИКАМ МЕХАНИЧЕСКИХ СВОЙСТВ
ИПОВЕРХНОСТИ РАЗРУШЕНИЯ ОБРАЗЦОВ ПОСЛЕ ИСПЫТАНИЙ НА РАСТЯЖЕНИЕ
Цель работы: ознакомиться с методами оценки отпускной хрупкости, научиться определять наличие отпускной хрупкости по виду излома.
Выполнить работу в следующем порядке:
1.Получить у преподавателя задание, представляющее собой результаты разрывных и ударных испытаний образцов низкоуглеродистых мартенситных сталей (НМС). В качестве материала исследования должны быть выданы образцы предложенных сталей после испытаний на одноосное растяжение или фотографии поверхности разрушения.
2.Выполнить групповые задания, вариант выдает преподаватель на группу из 3–4 человек.
Задание 1
Перенести характеристики механических свойств стали в отчет
опрактической работе. Построить график зависимости характеристик механическихсвойств оттемпературыотпускастали.
Характеристики механических свойств по вариантам приве-
дены ниже, заданы условный предел текучести σ0,2, предел прочности σв, относительное удлинение δ, относительное сужение ψ.
11
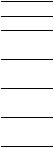
Вариант 1 Сталь 18Х2Г2Н2,5
Термическая обработка |
σ0,2, МПа |
σв, МПа |
δ, % |
ψ, % |
Горячекатаноесостояние |
1144 |
1501 |
15,7 |
59,9 |
Зак. 980 оС(1ч, масло) |
1166 |
1532 |
16 |
55,5 |
Зак. 980 оС(1ч, масло), отп. 200 оС(1ч, воздух) |
1154 |
1442 |
16,2 |
59,9 |
Зак. 980 оС(1ч, масло), отп. 250 оС(1ч, воздух) |
1157 |
1424 |
16,1 |
61,8 |
Зак. 980 оС(1ч, масло), отп. 350 оС(1ч, воздух) |
1163 |
1366 |
15 |
62,3 |
Зак. 980 оС(1ч, масло), отп. 450 оС(1ч, воздух) |
1055 |
1266 |
17,2 |
55,7 |
Зак. 980 оС(1ч, масло), отп. 500 оС(1ч, воздух) |
1024 |
1213 |
16,6 |
55,5 |
Зак. 980 оС(1ч, масло), отп. 550 оС(1ч, воздух) |
965 |
1102 |
15,7 |
47,4 |
Зак. 980 оС(1ч, масло), отп. 650 оС(1ч, воздух) |
637 |
942 |
18,7 |
56,1 |
Вариант 2 Сталь 17Х2Г2Н1,5М0,3
Термическая обработка |
σ0,2, МПа |
σв, МПа |
δ, % |
ψ, % |
Горячекатаное состояние |
1048 |
1353 |
16,5 |
60,782 |
Зак. 980 оС (1ч, масло) |
1061 |
1380 |
13 |
54,74 |
Зак. 980 оС(1ч, масло), отп. 250 оС(1ч, воздух) |
1099 |
1377 |
12,1 |
53,03 |
Зак. 980 оС(1ч, масло), отп. 450 оС(1ч, воздух) |
1038 |
1262 |
15,5 |
48,50 |
Зак. 980 оС(1ч, масло), отп. 550 оС(1ч, воздух) |
994 |
1172 |
15,7 |
58,01 |
Вариант 3 Сталь 22Х2Г2Н1,5М1
Термическая обработка |
σ0,2, МПа |
σв, МПа |
δ, % |
ψ, % |
Зак. 980 оС (1ч, масло) |
1154 |
1528 |
13,9 |
47,9 |
Зак. 980 оС(1ч, масло), отп. 250 оС(1ч, воздух) |
1234 |
1579 |
14,8 |
47,5 |
Зак. 980 оС(1ч, масло), отп. 450 оС(1ч, воздух) |
1117 |
1385 |
17,5 |
52,3 |
Зак. 980 оС(1ч, масло), отп. 550 оС(1ч, воздух) |
1142 |
1358 |
15,2 |
56,5 |
Вариант 4 Сталь 24Х2Г2Н1,5М0,5
Термическая обработка |
σв, МПа |
σ0,2, МПа |
δ, % |
ψ, % |
Зак. 980 С (1ч, на воздухе) |
1593 |
1189 |
15,1 |
43,6 |
Зак. 980 С(1ч, воздух), отп. 250 оС(1ч, воздух) |
1549 |
1224 |
12,1 |
40,3 |
Зак. 980 С(1ч, воздух), отп. 450 оС(1ч, воздух) |
1373 |
1109 |
12,5 |
48 |
Зак. 980 С(1ч, воздух), отп. 550 оС(1ч, воздух) |
1256 |
1069 |
16,2 |
50,4 |
12

Вариант 5 Сталь 17Х2Г2Н1,5М0,3
Термическая обработка |
σв, МПа |
σ0,2, МПа |
δ, % |
ψ, % |
Зак. 980 С на воздухе |
1384 |
1046 |
14 |
54 |
Зак. 980 С(1ч, воздух), отп. 250 оС(1ч, воздух) |
1384 |
1105 |
12,8 |
54 |
Зак. 980 С(1ч, воздух), отп. 450 оС(1ч, воздух) |
1262 |
1038 |
15,5 |
48,3 |
Зак. 980 С(1ч, воздух), отп. 550 оС(1ч, воздух) |
1172 |
994 |
15,7 |
57,9 |
Вариант 6 Сталь 24Х2Г2Н1,5М0,5
Термическая обработка |
σв, МПа |
σ0,2, МПа |
δ, % |
ψ, % |
Зак. 980 С (1ч, на воздухе) |
1620 |
1275 |
15,1 |
48,5 |
Зак. 980 С(1ч, воздух), отп. 250 оС(1ч, воздух) |
1534 |
1252 |
12,3 |
47,7 |
Зак. 980 С(1ч, воздух), отп. 450 оС(1ч, воздух) |
1358 |
1130 |
14,5 |
47,9 |
Зак. 980 С(1ч, воздух), отп. 550 оС(1ч, воздух) |
1179 |
1023 |
15,3 |
51,8 |
Задание 2
Из предложенных фотографий поверхности разрушения образцов (рис. 1–7) или предоставленных преподавателем разрывных образцов, испытанных после закалки и отпуска, выбрать соответствующие своему варианту.
Схематично изобразить поверхности разрушения и провести анализ поверхности разрушения на предмет наличия характерного излома «розетки», свидетельствующего о наличии отпускной хрупкости.
аб
Рис. 1. Изломы образцов из стали 18Х2Г2Н2,5: а – в горячекатаном состоянии; б – после закалки
(зак. 980 С (1ч, масло), отп. 200 С (1ч, воздух)). 28
13

Рис. 2. Излом после испытания |
Рис. 3. Излом после испытания |
на растяжение образца |
на растяжение образца |
из стали 24Х2Г2Н1,5М0,5 |
из стали 24Х2Г2Н1,5М0,5 |
(зак. 980 С (1ч, воздух)). 28 |
(зак. 980 С (1ч, масло)). 28 |
Рис. 4. Излом после испытания |
Рис. 5. Излом после испытания |
|
на растяжение образца из стали |
на растяжение образца из стали |
|
24Х2Г2Н1,5М0,5 (зак. 980 |
С |
24Х2Г2Н1,5М0,5 (зак. 980 С |
(1ч, воздух), отп. 250 С). |
28 |
(1ч, масло), отп. 250 С). 28 |
Рис. 6. Излом после испытания |
Рис. 7. Излом после испытания |
на растяжение образца из стали |
на растяжение образца из стали |
24Х2Г2Н1,5М0,5 (зак. 980 С |
24Х2Г2Н1,5М0,5 (зак. 980 С |
(1ч, масло), отп. 450 С). 28 |
(1ч, воздух), отп. 450 С). 28 |
14 |
|
Оценить температуру начала образования «розетки» при отпуске и температуру, при которой она проявляется наиболее существенно. Сравнить данные, полученные из таблиц и с поверхности разрушения.
3. Сделать выводы о влиянии системы легирования на отпускную хрупкость стали.
Практическая работа № 9
ИЗУЧЕНИЕ СПОСОБОВ ПОВЫШЕНИЯ КОНСТРУКЦИОННОЙ ПРОЧНОСТИ
Цель работы: ознакомиться с методами повышения конструкционной прочности; изучить особенности структурообразования при нагреве, охлаждении, гомогенизации и термоциклировании в наноструктурированных материалах на основе железа, получаемых без использования высокоэнергетических воздействий.
Теоретическая часть
Основные способы получения наноструктурированных низкоуглеродистых мартенситных сталей
Наночастицы находятся на границе квантового и классического микромира. Метастабильное состояние вещества определяет их уникальные свойства. Нижнюю границу определяет потеря индивидуальных свойств наночастиц при формировании из них реального изделия или заготовки. Например, кластер железа почти полностью теряет свои специфические свойства и приближается к классическому металлическому железу при числе атомов n = 15. При n > 15 он остается кластером в масштабном представлении, но теряет качество нанореактора, когдасвойства являютсяфункцией размера.
Нанообъект – объект, линейный размер которого хотя бы в одном направлении составляет порядка 1–100 нм.
Оценки показывают весьма приблизительный выбор 1 и 100 нм в качестве нижней и верхней границы нанообъекта, более важное значение имеет получение новых свойств.
15
Наносистема – система, содержащая структурные элементы размером порядка 1–100 нм, определяющие ее основные свойства
ихарактеристики в целом. К разряду наносистем относятся нано-
устройства и наноматериалы.
Нанотехнологии – технологии, направленные на создание
иэффективное практическое использование нанообъектов и наносистем с заданными свойствами и характеристиками.
Продукция наноиндустрии (нанотехнологическая продук-
ция) – высококонкурентоспособная продукция (товары, работы, услуги), произведенная с использованием нанотехнологий и обладающая вследствие этого ранее недостижимыми техникоэкономическими показателями.
Если ранее основное внимание уделялось получению наноматериалов, то сегодня современное развитие наноиндустрии связано с получением в результате реализации нанотехнологии или создания наноматериала ранее недостижимых техникоэкономических показателей.
По структуре однокомпонентный низкоуглеродистый мартенсит (НМ) состоит из бездефектных областей и аморфных или сильно искаженных кристаллических межфазных (межзеренных) границ, строение которых в настоящее время является предметом исследований. Доля приграничного вещества у НМ может составлять десятки процентов. Это дает основания рассматривать даже однокомпонентный НМ как двухфазный.
Важнейшими, касающимися конструкционных материалов особенностями, неразрывно связанными со структурой НМ, являются немонотонные зависимости модуля Юнга, трещиностой-
кости K1c, прочности и др. от размера зерна. Наиболее высокую прочность обычно имеют металлы с размером характерного элемента структуры в несколько десятков нанометров.
Кнастоящему времени разработано большое количество методов и способов получения наноматериалов. Это обусловлено разнообразием состава и свойств наноматериалов и позволяет расширять ассортимент данного класса веществ, создавая новые, уникальные образцы.
16
Формирование высокодисперсных структур может происходить в ходе таких процессов, как фазовые превращения, химическое взаимодействие, рекристаллизация, аморфизация, биологический синтез, высокие механические нагрузки. Как правило, создание наноматериалов возможно при наличии существенных отклонений от равновесных условий существования вещества, что требует создания специальных условий и часто сложного прецизионного оборудования.
Разработка и совершенствование методов наноструктурирования материалов определили основные требования, которым они должны соответствовать, а именно:
–метод должен обеспечить получение материала контролируемого состава с воспроизводимыми свойствами;
–метод должен иметь высокую производительность и экономичность;
–метод должен обеспечить временную стабильность наноматериалов, т.е. защиту поверхности частицы от самопроизвольного окисления;
–метод должен обеспечить получение наноматериалов с определенным размером частиц или зерен, причем их распределение по размерам должно быть, при необходимости, достаточноузким.
С целью формирования наноструктуры в объемных материалах используют специальные механические системы деформирования, которые позволяют достичь больших искажений структуры образцов при относительно низких температурах.
Основные способы диспергирования структуры до наноуровня основаны на консолидации нанопорошков, кристаллизации аморфных сплавов или применении интенсивной пластической деформации (ИПД).
К методам интенсивной пластической деформации относят следующие:
–кручение под высоким давлением;
–равноканальное угловое прессование;
–метод всесторонней ковки;
17
–равноканальную угловую вытяжку;
–метод «песочных часов»;
–метод интенсивного трения скольжением.
Каждый из указанных выше методов имеет свои недостатки, например: размер образцов-дисков, полученных кручением, слишком мал (диаметр 10–20 мм и толщина 0,2–0,5 мм); существенное измельчение структуры наблюдается уже при деформации в полоборота, тогда как для однородной наноструктуры требуется деформация в несколько оборотов; исходными заготовками в методе прессования служат образцы с круглым или квадратным поперечным сечением, диаметр или диагональ которых, как правило, 20 мм. Это лишь некоторые примеры недостатков методов ИПД, связанные с незначительностью размеров получаемых заготовок. Кроме того, к недостаткам относятся необходимость в специальном оборудовании и невозможность использования данных методов на всем многообразии конструкционных материалов.
Исходя из анализа достоинств и недостатков вышеперечисленных методов наноструктурирования, а также особенностей низкоуглеродистых сталей можно утверждать, что в качестве метода получения наноструктуры целесообразнее применять термоциклическую обработку (ТЦО), которая позволяет получить дисперсную структуру низкоуглеродистого мартенсита в заготовках сечением более 20 мм. Также этот метод позволяет получать свойства во всем объеме детали без применения дорогостоящего оборудования и без применениявысокоэнергетического воздействия.
Особенности сталей со структурой низкоуглеродистого пакетного мартенсита
Наибольшую скорость релаксации в конструкционных сталях обеспечивает однородная структура с максимальной плотностью дислокаций, сохраняющих подвижность. В такой структуре при малом содержании легирующих элементов реализуется преимущественно два механизма упрочнения: дислокационный и зернограничный.
18
Мартенситное превращение является основой современного способа упрочнения конструкционных сталей. Традиционные направления повышения прочности сталей включают закалку на мартенсит и отпуск. Уже в середине прошлого века стало ясно, что дальнейшее совершенствование среднеуглеродистых сталей малоэффективно. В 80-е гг. ХХ в. был создан новый класс конструкционных низкоуглеродистых мартенситных сталей (НМС), содержащих менее 0,2 % С, реечная структура которых обеспечивает высокую подвижность дислокаций при их высокой плотности (1010–1012 см–2). НМС обладают повышенной конструкционной прочностью и технологичностью по сравнению с традиционными конструкционными сталями с прочностью 800–1400 Н/мм2.
Структура низкоуглеродистого мартенсита позволяет осу-
ществлять |
совмещенный |
процесс горячего формообразования |
с закалкой |
на воздухе, |
обеспечивает хорошую свариваемость |
в термоупрочненном и отожженном состояниях всеми способами сварки без предварительного подогрева и ограничений времени между сваркой и отпуском. Стали со структурой НМ не склонны к образованию холодных и горячих трещин, закаливаются охлаждением на спокойном воздухе, не склонны к деформации при закалке и сварке, хорошо деформируются в закаленном состоянии, подвергаются поверхностному упрочнению всеми видами химико-термической обработки и наплавке. Низкоуглеродистые мартенситные стали характеризуются глубокой прокаливаемостью, высокой ударной вязкостью, низкой критической температурой хрупкости Ткр. Продукцию из этих сталей производят в виде листа, ленты, сортового проката, поковок, штамповок и труб. Исключение из процесса термического упрочнения жидких охлаждающих сред и возможность реализации совмещенного процесса формообразования с закалкой обеспечивают экологически безопасную технологию получения продукции.
Единственным морфологическим типом мартенсита, позволяющим фрагментировать характерные элементы структуры при закалке (если в конструкционной стали с относительно низким
19
содержанием углерода существуют несколько видов мартенсита или бейнит), является пакетный мартенсит. Характерным элементом структуры в данном случае следует считать размер рейки, поскольку для низкоуглеродистой стали (0,02 % С и 18 % Ni) экспериментально доказано, что упрочнение от пакетов на 1–2 порядка меньше, чем от реек.
Структура пакетного мартенсита включает в себя слои, пакеты и рейки. Малые углы разориентировки реек (менее 3о) характерны только для реек одного пакета. Поэтому при элек- тронно-микроскопическом исследовании сечений обычно наблюдают геометрические фигуры, по которым сложно судить о тонкой структуре. Однако при прохождении секущей плоскости через пакет или его значительную часть наблюдают параллельные рейки, и их поперечный размер позволяет судить о ширине реек, так как в других плоскостях рейки разориентированы на большие углы. Ширина реек пакетного мартенсита обычно составляет 200–250 нм, а толщина рейки низкоуглеродистого мартенсита всегда меньше ширины в 7 или 9 раз. Меньшие различия толщины и ширины реек (3:1) установлены в работе Ю.Г. Андреева и М.А. Штремеля.
При переходе от пластинчатого к реечному мартенситу резко изменяются свойства стали, кроме того, в самом реечном мартенсите в определенных узких интервалах механические свойства (в первую очередь, характеристики вязкости) сильно зависят от размеров реек. В соответствии с современными представлениями этих факторов достаточно для причисления низкоуглеродистых мартенситных сталей к наноматериалам.
Диспергирование структуры низкоуглеродистого мартенсита
Структура пакетного (реечного) мартенсита представляет собой набор практически параллельных друг другу кристаллов с объемно-центрированной решеткой, имеющих форму трехосного эллипсоида с соотношением полуосей a:b:c = 1:7:30, 1:9:33 и
20