
книги / Влияние степени наполнения арматурой, предварительного циклического нагружения и температуры на механические характеристики волокнистых полимерных композиционных материалов
..pdf
|
|
|
|
|
Таблица 1 |
|
Характеристики стекловолокон [11] |
|
|||
|
|
|
|
|
|
|
|
Плотность, |
Прочность, |
Модуль |
Предельная |
Марка волокон |
|
упругости, |
деформация, |
||
|
|
кг/м3 |
ГПа |
ГПа |
% |
|
|
|
|
||
|
|
|
|
|
|
Алюмоборосиликатное |
2540 |
3,5 |
73,5 |
4,8 |
|
(Россия) |
|
||||
|
|
|
|
|
|
|
|
|
|
|
|
Высокомодульное |
|
2580 |
4,2 |
95,0 |
4,8 |
ВМ-1 (Россия) |
|
||||
|
|
|
|
|
|
|
|
|
|
|
|
Высокопрочное |
|
2580 |
— |
93,0 |
— |
ВМП (Россия) |
|
||||
|
|
|
|
|
|
|
|
|
|
|
|
Кислотостойкое |
|
2560 |
2,0 |
74,0 |
3,6 |
№7-А (Россия) |
|
||||
|
|
|
|
|
|
|
|
|
|
|
|
М-стекло (США) |
|
2890 |
3,5 |
110,0 |
3,2 |
|
|
|
|
|
|
Армирующими элементами в конструкционных стеклопластиках являются непрерывные волокна, организованные в виде нитей и жгутов различной степени крутки, либо ткани различного плетения. Слоистые стеклопластики на основе тканей называются стеклотекстолитами.
Выбор связующего для стеклопластиков определяется условиями их изготовления и эксплуатации. В производстве стеклопластиков широко используются как термореактивные смолы (полиэфирные, эпоксидные, фенолформальдегидные), так и различные термопластические полимеры.
Органопластики [11, 13, 14]
Органопластики на основе высокопрочных арамидных волокон обладают высокими удельными прочностными и упругими характеристиками, ударной вязкостью, электрическим сопротивлением, химической стойкостью, высокими теплоизоляционными свойствами. Армирующими элементами конструкционных органопластиков являются непрерывные волокна, представленные в виде нитей и жгутов различной линейной плотности и степени крутки, а также в виде тканей. Арамидные волокна при текстильной и других видах переработок незначительно снижают свои механические свойства, что послужило причиной широкого применения метода намотки при изготовлении изделий из органопластика. Характеристики органических волокон представлены в табл. 2.
11

Характеристики органических волокон [11] |
Таблица 2 |
||||
|
|||||
|
|
|
|
|
|
|
Плотность, |
Прочность, |
Модуль |
Предельная |
|
Марка волокон |
упругости, |
деформация, |
|||
кг/м3 |
ГПа |
||||
|
|
|
ГПа |
% |
|
Кевлар-129 |
1440 |
3,3 |
75 |
4,5 |
|
(высокопрочный) (США) |
|||||
|
|
|
|
||
Кевлар-49 (США) |
1450 |
2,9 |
120 |
2,7–3,5 |
|
|
|
|
|
|
|
Кевлар-149 (США) |
1470 |
2,4 |
160 |
— |
|
|
|
|
|
|
|
Тварон (высокомодульный) |
1450 |
2,8 |
125 |
— |
|
(Нидерланды) |
|||||
|
|
|
|
||
Токмилон (Япония) |
960 |
3,5 |
100 |
4 |
|
|
|
|
|
|
|
СВМ (Россия) |
1420–1450 |
3,8–4,2* |
125–140 |
3–4 |
|
|
|
|
|
|
|
Терлон (Россия) |
1450 |
3,2* |
100–150 |
2,7–3,5 |
|
|
|
|
|
|
|
Армос (Россия) |
1420–1450 |
4,5–5,2 |
145–160 |
— |
|
|
|
|
|
|
Примечание. * Прочность в микропластике.
1.1.2. Методы статических испытаний колец*
Развитие и промышленное применение процесса намотки потребовало разработки специальных материалов (их иногда называют намоточными)
иновых технологических приемов. В их числе программированная намотка, намотка с дополнительным давлением, с послойным отверждением, комбинированная намотка. Появились новые намоточные высокомодульные материалы – боро-, угле- и органопластики. Применение плоских прессованных образцов для сравнения способов намотки, оценки свойств этих материалов
ивлияния параметров намотки оказалось безуспешным. Особенности намотки заставляют учесть такие факторы, как влияние натяжения искривления армирующих волокон, переменное натяжение по толщине материала, наличие дополнительного уплотняющего межслойного давления, опасность размотки, слабое сопротивление межслойному сдвигу ипоперечному отрыву. Перечисленные явления нельзя исследовать на плоских образцах. Это потребовало разработки таких методов испытания намоточных изделий из композитов, при которыхучитывалисьбыуказанныеособенностиэтогоклассаматериалов.
Вначале была сделана попытка использования образцов, вырезанных по образующей (полосок) и в тангенциальном направлении (сегментов), для исследования свойств в направлениях армирования (рис. 1, а, б). Была соз-
* Раздел написан по материалам книг [17, 18].
12
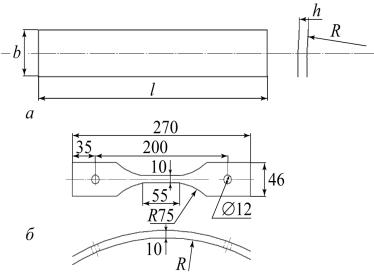
дана и серия специальных приспособлений для нагружения в направлении волокон образцов с криволинейной осью. Трудности получения надежных численных результатов на криволинейных образцах, особенно с большой кривизной, очевидны. Высокая стоимость образцов исключала возможность их использования при отработке оптимальной технологии и геометрии намотки.
Принципиальный шаг в изучении свойств намоточных композитов связан с созданием кольцевых образцов. Кольцевые образцы предложены в 1955 г. Военно-морской лабораторией вооружения (США) – Naval Ordnance Laboratory (NOL) – отсюда и их название NOL-Ring. Образцы пред-
назначались для исследования влияния технологии создания материала и параметров намотки. Однако избранный способ нагружения при помощи
полудисков позволял измерять только прочность и модуль упругости Е в направлении волокон, причем с известными ограничениями. Дело в том, что именно и Е гораздо менее чувствительны к технологии на-
мотки, чем характеристики, определяемые полимерной матрицей. Это было причиной ряда ошибочных рекомендаций, особенно для материалов, работающих на сжатие. Найденная форма образца оказалась, несомненно, удачной; размеры и способ нагружения нуждались в уточнении.
Наиболее приемлемыми для исследования упругих и прочностных свойств намоточных композитов являются образцы, имеющие форму кольца или его части – сегмента. При изготовлении кольцевых образцов сравнительно легко воспроизводятся разные варианты технологии намотки и параметры процесса. Техника испытания указанных образцов достаточно проста; трудности возникают при выборе аппарата для обработки результатов эксперимента. Далее, используя разные схемы нагружения, легко добиться получения всего комплекса упругих и прочностных характеристик, необходимых для полной оценки материала и технологии.
Исследования последних лет были направлены на поиски новых способов нагружения целых и разрезных кольцевых образцов и разработки
13
аппарата для оценки и анализа полученных результатов. Кольцевые образцы испытываются наружным и внутренним давлением, что позволяет оценить их свойства при растяжении-сжатии в направлении армирования, на изгиб сосредоточенными силами – для оценки сдвиговых свойств намоточных материалов. Кольца с прорезями используются для изучения прочности при межслойном сдвиге. Для получения полного комплекса механических характеристик намоточных материалов освоены новые схемы нагружения разрезных колец. Учет особенностей механических свойств современных армированных пластиков привел к пересмотру методов испытаний сегментов кольца.
Размеры колец для испытания намоточных армированных пластиков
ипрежде всего относительная толщина h/R зависят от схемы нагружения
ицелей исследования. Наибольшее распространение получили NOL-кольца. Это тонкостенные кольца (h/R ≈ 1/25…1/50), пригодные лишь для изучения характеристик в направлении армирования. Область их применения была неоправданно расширена, что привело к появлению большого числа ошибочных результатов. Для изучения сдвиговых и трансверсальных характеристик потребовалось применение более толстостенных колец. В настоящее время доказана необходимость выбора размеров колец в соответствии с целью испытаний.
Намотанные кольца из материалов со слоистой или волокнистой структурой обладают отчетливо выраженной анизотропией: модуль Юнга в окружном направлении E (определяется жесткой арматурой) значительно выше, чем
врадиальном Er , и выше модуля межслойного сдвига G r . Причем степень анизотропии растет для материалов, армированных высокомодульными волокнами. Прочностьприрастяжениивнаправленииарматуры значительно превышает сопротивление поперечному отрыву r и сжатию перпендикулярно волокнам, а также прочность при сдвиге r . Такая существенная
анизотропия механических свойств ограничивает область применения широко известных зависимостей сопротивления материалов для обработки результатов испытаний, полученных в предположении бесконечной трансверсальной исдвиговой жесткости материала, т.е. при G r и Er . Именно поэтому
вдальнейшем везде указаны геометрические границы, начиная с которых для разных классов материала необходим учет толстостенности. Для высокомодульных материалов особое значение приобретает знак радиальных напряжений r ; необходимо устранять опасность возникновения даже сравнительно
малыхрастягивающихрадиальныхнапряжений.
При несомненных достоинствах кольцевые образцы обладают и недостатками. Главный из них – трудность изучения на кольцах влияния
14
геометрии намотки, особенно для случаев спиральной намотки нитью при углах, заметно отличающихся от прямого. Для этого требуется значительное увеличение ширины образца. Необходимость устранения эффекта «перерезанных нитей» заставляет использовать для изучения геометрической оптимизации процесса более дорогие трубчатые образцы. Использование трубок позволяет изучить не только свойства в главных направлениях; они применяются и для изучения сдвиговых характеристик намоточных материалов в плоскости путем кручения тонкостенных цилиндров разной структуры, изготовленных намоткой.
Кроме испытания колец, сегментов и трубчатых образцов для изучения свойствнамоточныхматериалов, механикинамоткииоптимизациитехнологии, широкораспространеныиспытаниянатурныхизделий– труб, сосудоввысокого давления – и вырезаемых из их технологического припуска образцов-свидете- лей. Приэтомнамоточныеизделия, работающиепринаружномиливнутреннем давлении, испытываются главным образом для оценки несущей способности; проверяется работоспособность оболочки при заданной нагрузке. Если конструкция доводится до разрушения, то замеряется только разрушающее усилие иоцениваетсястойилиинойточностьюпрочностьматериала.
Рассмотрим NOL-метод, который использовался при испытании кольцевых образцов из стекло- и органопластика.
NOL-метод
NOL-метод стандартизован в США (АSТМ D 2291–03 [19]) и широко используется в Европе. Первоначально он был разработан для оценки влияния способов химической обработки стеклянной ровницы на прочность стеклопластиков. Стандартом установлены следующие размеры колец (в мм) после механической обработки:
Внутренний диаметр |
Ширина |
Толщина |
146,05 ± 0,5 |
6,35 ± 0,3 |
1,5 ± 0,05 |
146,05 ± 0,5 |
6,3 ± 0,13 |
1,5 ± 0,25 |
146,05 ± 0,5 |
6,3 ± 0,13 |
3,1 ± 0,05 |
К приведенным размерам поперечного сечения следует отнестись критически.
Исследования однонаправленных эпоксидных стеклопластиков показывают, например, что при определении прочности ширина колец играет большую роль, чем при испытаниях плоских образцов. Так, при угле намотки 86° (т.е. почти в плоскости кольца) ширина образца должна быть не меньше 15–20 мм, при 55° – не меньше 80–120 мм. При меньшей ширине
15
образца прочность получается заниженной. На замеренную прочность колец влияют не только размеры поперечного сечения кольца, т.е. масштабный и краевой эффекты, но и отношение h/R.
В настоящее время NOL-метод используется для определения модуля упругости, прочности при растяжении в тангенциальном направлении и сопротивления сдвигу, а модифицированный NOL-метод – для оценки прочности при сжатии. Кольца, изготовленные намоткой на многосекционную оправку или вырезанные из цилиндров, при испытаниях надеваются на полудиски, которые с помощью приспособления устанавливаются в испытательной машине. Это же приспособление используется и при испытании колец, изготовленных намоткой на разрезную оправку (полудиски). Перед надеванием колец смазываются их контактные поверхности и приспособление или применяются прокладки, уменьшающие трение (например, ленты из фторопласта). Как показывает опыт, влияние трения при применении специальных мер, например графитовых смазок, при определении прочности кольца может быть пренебрежимо малым.
Скорость перемещения захватов испытательной машины по ASMT D 2291–03 равна 2,5 мм/мин.
Для определения модуля упругости E производится измерение де-
формаций с помощью тензодатчиков сопротивления, наклеенных на наружную поверхность кольца, или измеряется перемещение захватов испытательной машины, т.е. увеличение зазора между полудисками. При измерении зазора модуль упругости определяется по формуле
E |
P |
|
|
D |
, |
(1) |
||
|
|
|
||||||
|
2bh 2 U |
|
||||||
|
|
|||||||
где b – ширина кольца; h – толщина; D – средний диаметр; |
U – изменение |
|||||||
расстояния между полудисками при увеличении нагрузки на |
P. |
|||||||
Модуль упругости в этом случае определяется формулой |
||||||||
E |
|
|
|
P |
, |
|
(2) |
|
|
|
|
|
|
||||
|
|
2bh |
|
|
|
|||
|
|
|
|
|
||||
где Р – нагрузка по шкале машины; |
– относительная деформация, изме- |
ряемая тензодатчиком.
Использование метода полудисков для определения модуля упругости при измерении относительных деформаций в одной или двух точках по окружности возможно лишь при относительно малых нагрузках. Увеличение нагрузки приводит к неравномерности распределения деформаций по окружности кольца, о чем свидетельствуют данные, приведенные на рис. 2; угол отсчитывается от направления действия нагрузки.
16
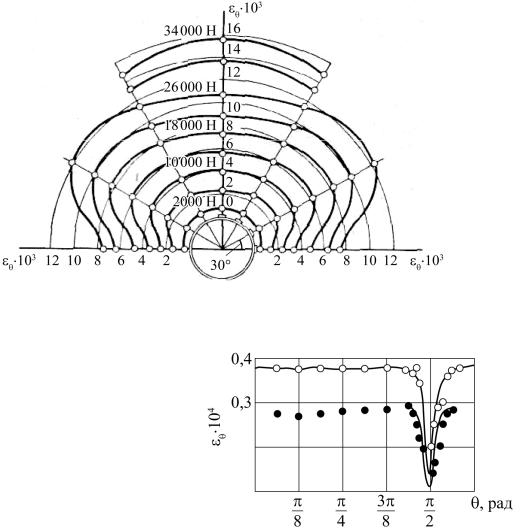
Рис. 2. Распределение деформации εθ по окружности колец при испытаниях жесткими полудисками
На рис. 2 показаны экспериментально измеренные окружные деформации при разных уровнях нагружения (P = 2000… …34000 H). Нелинейность резко увеличивается с ростом нагрузки. Это требует осреднения относительных деформаций, измеряемых в нескольких точках, или измерения деформации в точках, удаленных от места разреза. При этом удается избежать участков с резко повышенной деформацией (рис. 3).
Прочность материала кольца определяется зависимостью
Рис. 3. Распределение деформации εθ по окружности кольца при растяжении его жесткими полудисками. Материал – однонаправленный стеклопластик на связующем ЭДТ-10. Размеры кольца:
Dвн = 150 мм; Dн = 157,4 мм;
b = 18 мм. Нагрузка: ● – 22000 Н; ○ – 28000 Н
|
|
Pразр |
|
|
|
|
|
|
. |
(3) |
|
2bh |
|||||
|
|
|
|
Однако характеристики, определяемые по формулам (1)–(3), не являются истинными характеристиками материала, так как при нагружении по этой схеме деформация кольца на участках около разъема полудисков состоит из деформаций растяжения и изгиба (вследствие изменения радиуса кривизны кольца). Соотношение этих деформаций зависит от относительной толщины кольца h/R.
С увеличением этого соотношения, а также степени анизотропии и величины предельной деформации материала влияние указанных факто-
17

ров усиливается. Для очень тонких колец (h < 3 мм) возникает опасность расслоения и размотки.
При исследовании напряженного состояния кольца установлено, что напряжения σθ и τθr практически не зависят от угла θ, кроме области вблизи разъема полудисков, т.е. при углах, близких к θ = π/2. Ширина этой области зависит от относительной толщины кольца, характеризуемой величиной r1 Rвн /Rн упругих характеристик материала. Вне этой области касатель-
ные напряжения равны нулю. Вблизи же сечения θ = π/2 касательные напряжения меняются весьма резко как по координате θ (рис. 4), так и по радиусу R. С увеличением относительной толщины кольца и степени анизо-
тропии E /G r прирост напряжений в этой области уменьшается. Измене-
ние степени анизотропии E / Er меньше влияет на максимальные значения
нормальных и касательных напряжений. Появление зазора между кольцом и полудисками (взаимный отход контактных поверхностей) несколько снижает концентрацию напряжений.
Распределение окружных напряжений σθ в сечении θ = π/2 существенно отлично от постоянного, характерного для сечений, далеких от θ = π/2. Концентрация окружных напряжений может быть оценена при помощи коэффициента концентрации
k = σθmax/σo, |
(4) |
где o 1 1r 1 dr.
1 r1
Рис. 4. Зависимость нормальных напряжений Rн на внутренней границе кольца
E
и касательных напряжений |
|
r Rн |
на среднем радиусе кольца для двух значении |
|
|
||||
r |
|
E |
||
|
|
|||
относительной толщины кольца: r1 |
= 0,85 (1) и r1 = 0,95 (2). Характеристики стекло- |
|||
пластика: Er / E |
= 0,25; G r / E = 0,1; r = 0,3 |
Численные значения коэффициента k в зависимости от отношения Е"/Е' и r1 даны на рис. 5.
18

Рис. 5. Зависимость коэффициента концентрации окружающих напряжений k
от отношения модулей упругости компонентов материала Е"/Е' при различных значениях относительной толщины кольца r1 : 1 – 0,80; 2 – 0,85; 3 – 0,90; 4 – 0,90; 5 – 0,98
Учет зазора между полудисками, образовавшегося во время нагружения, мало сказывается на напряженном состоянии кольца.
1.2. Описание технологии изготовления образцов для испытания
1.2.1. Процесс изготовления изделий намоткой из полимерных волокнистых композитов*
Одним из самых распространенных и совершенных процессов изготовления высокопрочных армированных колец и оболочек является процесс непрерывной намотки. При этом методе лента, образованная системой нитей или сформированная из ткани, пропитывается полимерным связующим, подается на вращающуюся оправку, имеющую конфигурацию внутренней поверхности изделия, и укладывается в ней в различных направлениях. После получения необходимой толщины и структуры материала проводится отверждение и удаление оправки. Метод непрерывной намотки позволяет получать оболочки вращения сложной формы и реализовывать с высокой точностью большое количество схем армирования изделий из композитов.
Существует несколько технологических методов формования изделий намоткой в зависимости от способа нанесения связующего на волокнистый армирующий материал.
Способ «сухой» намотки заключается в том, что волокнистый армирующий материал перед формованием предварительно пропитывают связующим на пропиточных машинах, которые обеспечивают не только качественную пропитку, но и требуемое равномерное содержание связующего
впрепреге на основе стекло-, органо- и углеволокон за счет применения
*Раздел написан по материалам книг [14, 15, 20, 21].
19
различных растворителей для регулирования вязкости связующего в процессе пропитки. Особенно эффективно применение предварительно пропитанных ровингов, полотен стеклоуглетканей.
Способ «мокрой» намотки отличается тем, что пропитка армирующего волокнистого материала связующим и намотка на оправку совмещены. Необходимая вязкость связующего в данном случае обеспечивается выбором соответствующей смолы и применением подогрева связующего в пропитывающей ванне. Преимущество такого способа заключается в более низком контактном давлении формования, что требует оборудования с меньшей мощностью привода и лучшей формуемостью поверхностей изделия.
По типу укладки армирующего волокнистого материала в намотанном изделии различают несколько видов намотки, например прямую (окружную) намотку, спиральную, спирально-перекрестную, продольно-попе- речную намотку. Независимо от способа намотки технологические стадии и физико-технические процессы образования структуры армированных волокнами композитов мало отличаются. Поэтому технологический цикл формования в зависимости от происходящих процессов разделен на следующие стадии: намотка и получение заготовки изделия, нагрев заготовки на оправке до температуры стеклования связующего, выдержка – отверждение связующего при постоянной температуре, охлаждение до температуры стеклования и далее до конечной температуры, съем изделия с оправки.
1.2.2. Параметры процессов намотки
Одним из наиболее значимых технологических факторов процесса «мокрой» намотки, позволяющих существенным образом влиять на формирование структурных и прочностных показателей, является натяжение волокнистого армирующего материала. В зависимости от типа армирующего материала, применяемого связующего, а также габаритов изделия характер влияния натяжения на структуру композитов может изменяться.
Эффективный способ уменьшения фильтрации связующего из внутренних слоев на поверхность наматываемой оболочки, а следовательно, и степени неоднородности структуры – управление процессом миграции связующего путем изменения технологического натяжения по специально отработанной программе. Натяжение при намотке – это фактор, регулирующий начальное напряженное состояние двухкомпонентной системы волокнистого композита. Изменяя усилие натяжения волокон при намотке по заданному закону, можно существенно влиять на начальные напряжения в готовом изделии.
20