
книги / Сопротивление материалов. Ч. 1
.pdf
Например, для стали E = 2 105 МПа, µ = 0,25, откуда следует, что G = 0,8 105 МПа. Зависимость (5.7) подтверждается экспериментально.
Напряжение τт является пределом текучести при сдвиге, т.е. ка-
сательным напряжением, при котором угол сдвига возрастает при постоянном напряжении. Характерно, что для многих материалов предел текучести при сдвиге τт связан с пределом текучести при растяжении σт соотношением
τT ≈ σT3 .
Запишем выражение для абсолютного сдвига ∆, подставив в формулу закона Гука (5.6) полученные ранее соотношения (5.2) и (5.5):
|
τ=Gγ, |
|
|
||||
или |
|
|
|
|
|
|
|
|
Q |
=G |
∆ |
, |
|
||
|
A |
a |
|
||||
|
|
|
|
|
|||
откуда |
|
|
|
|
|
|
|
|
∆= |
Qa |
|
, |
(5.8) |
||
|
GA |
||||||
|
|
|
|
|
где произведение GA называют жесткостью сечения стержня при сдвиге.
Практические расчеты соединений, работающих на сдвиг
Детали, служащие для соединений отдельных элементов машин и строительных конструкций, – заклёпки, штифты, болты и т.п. – во многих случаях воспринимают нагрузки, перпендикулярные к их продольной оси. Поперечная нагрузка в указанных деталях возникает, в частности, при растяжении (сжатии) соединяемых элементов. Соответствующие примеры приведены на рис. 5.7, где изображены: а – штифт; б – заклёпка; в – болт, поставленный без зазора; г –
71

шпонка. Их действительная работа сложна и лишь приближенно может быть охарактеризована как работа на сдвиг (срез). Однако практические расчёты этих соединений очень просты и достаточно надёжны, так как расчётные сопротивления назначаются на основании опытных данных.
а |
б |
в |
г |
Рис. 5.7.
Расчеты деталей на срез базируются на следующих основных допущениях:
1)в поперечном сечении возникает только один внутренний силовой фактор – поперечная сила Q;
2)касательные напряжения распределены равномерно по площади поперечного сечения;
3)в случае, если соединение осуществлено несколькими одинаковыми деталями (заклепками и т.п.), принимается, что все они нагружены одинаково.
Разрушение соединительных элементов (в случае недостаточной прочности) происходит в результате их перерезывания по плоскости, совпадающей с поверхностью соприкосновения соединяемых деталей, как показано на рис. 5.8, поэтому говорят, что эти элементы работают на срез, и возникающие в их поперечном сечении касательные напряжения называют напряжениями среза и обозначают τср.
72
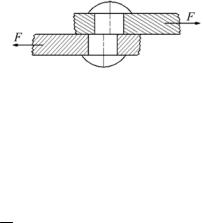
Рис. 5.8.
Условие прочности на срез формулируется как
τ |
ср |
= |
Q |
≤R |
, |
(5.9) |
|
||||||
|
|
|
ср |
|
|
|
|
|
|
Aср |
|
|
где Q – поперечная сила; при нескольких одинаковых соединитель-
ных деталях, Q = Fп ; здесь F – общая нагрузка соединения, п – чис-
ло заклёпок (болтов и т.п.); Rср – расчётное сопротивление на срез материала соединительных элементов.
Формула (5.9) используется для проверочного расчёта соединения. В зависимости от постановки задачи она может быть преобразована для определения допускаемой (расчётной) нагрузки или требуемой площади сечения.
Расчёт на срез обеспечивает прочность соединительных элементов, но не гарантирует надёжность соединения в целом. При недостаточной толщине соединяемых элементов возможно нарушение соединения вследствие их смятия по поверхности контакта с соединительными деталями. Давления, возникающие между поверхностями отверстий и соединительных деталей, принято называть напряжениями смятия и обозначать σсм. Фактическое распределение контактных напряжений весьма сложно. Поэтому расчёт на смятие носит условный характер и ведётся в предположении, что силы взаимодействия между деталями равномерно распределены по поверхности контакта и нормальны к этой поверхности.
Условие прочности на смятие имеет вид
σ |
|
= |
F |
≤R |
, |
(5.10) |
|
пA |
|||||
|
см |
|
см |
|
|
|
|
|
|
см |
|
|
|
|
|
|
|
|
|
73 |
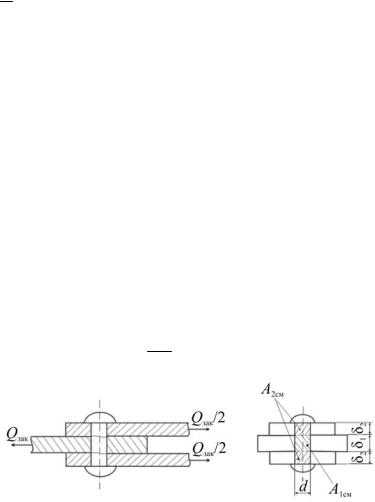
где Fп
площадь смятия; Rсм – расчётное сопротивление на смятие, определяемое экспериментально.
За расчётную площадь смятия при контакте по плоскости (см. рис. 5.7, г) принимают действительную площадь соприкосновения Aсм = tl, где l – размер шпонки в направлении, перпендикулярном плоскости чертежа; при контакте по цилиндрической поверхности (см. рис. 5.7, а, б, в) принимают площадь проекции поверхности контакта на диаметральную плоскость, т.е. Aсм = δd. При различной толщине соединяемых элементов в расчётную формулу следует подставлять δmin .
Для примера рассмотрим некоторые вопросы расчета заклёпочных соединений для случаев, когда соединяемые элементы работают на растяжение и сжатие.
На рис. 5.9, а показана работа одиночной заклёпки, соединяющей три листа и называемой двухсрезной, так как при её разрушении срез происходит по двум сечениям (отмечено волнистой лини-
ей) с площадью среза Aср = πd4 2 .
а |
б |
Рис. 5.9.
Зависимости для проверочных расчётов имеют следующий вид:
а) на срез
74
τ |
ср |
= |
|
|
F |
|
≤R , |
(5.11) |
||
|
|
πd 2 |
||||||||
|
|
|
nk |
|
ср |
|
||||
|
|
|
|
4 |
|
|
|
|
||
|
|
|
|
|
|
|
|
|
|
|
где п – общее число заклёпок, передающих заданную нагрузку F; |
||||||||||
k – число плоскостей среза одной заклёпки; |
|
|||||||||
d – диаметр заклёпки; |
|
|
|
|
|
|
|
|
|
|
б) на смятие |
|
|
|
|
|
|
|
|
|
|
|
σ |
|
= |
|
F |
≤R |
, |
(5.12) |
||
|
|
ndδ |
||||||||
|
|
см |
|
|
|
см |
|
|
где δ – наименьшая суммарная толщина листов, сминаемых в одном направлении. Например, на рис. 5.9, б это будет меньшая из площадей A1см = = δ1 d и A2см = 2 δ2d.
Допускаемую силу на одну заклёпку определяют следующим образом:
а) из условия прочности на срез
Q |
зак |
=R k |
πd |
2 |
; |
(5.13) |
|
|
|
|
|||||
ср |
|
ср |
4 |
|
|
|
|
|
|
|
|
|
|
|
|
б) из условия прочности на смятие |
|
|
|
||||
Qзак =R dδ |
. |
|
(5.14) |
||||
|
см |
см |
|
|
|
|
Из двух сил фактической допускаемой силой для заклёпки Qзак является меньшая из них.
Расчёт заклёпочного соединения обычно состоит в определении необходимого числа заклёпок п при действии на него заданной нагрузки F. Тогда
п= |
F |
. |
(5.15) |
|
|||
|
Q |
|
|
|
зак |
|
75
Лекция 6
КРУЧЕНИЕ
Основные понятия. Крутящие моменты и их эпюры
Кручение – это такой вид нагружения стержня, при котором в его поперечных сечениях возникает единственный внутренний силовой фактор – крутящий момент, обозначаемый Mк (или Мz). Стержень, работающий на кручение, называют валом.
Деформация кручения возникает при нагружении стержня парами сил, плоскости действия которых перпендикулярны к его продольной оси. Моменты этих пар будем называть скручивающими и обозначать буквой М.
На рис. 6.1, а представлен вал, работающий на кручение под действием приложенных к нему скручивающих моментов. При этом на рис. 6.1, б внешний момент условно изображён в виде двух кружков: кружок с точкой обозначает силу, направленную на наблюдателя, а кружок с крестом – силу, направленную от наблюдателя.
Во всех случаях будем считать, что алгебраическая сумма скручивающих моментов равна нулю, т.е. вал находится в равновесии.
Условимся о следующем правиле знаков: крутящий момент считается положительным, если при взгляде на сечение со стороны внешней нормали п он направлен против хода часовой стрелки (рис. 6.2). Соответствующий внешний скручивающий момент направлен по ходу часовой стрелки.
76
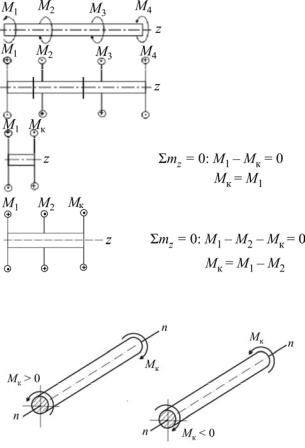
а
б
в
г
Рис. 6.1.
Рис. 6.2.
Применяя метод сечений и рассматривая равновесие отсечённой части (рис. 6.1, в, г), приходим к выводу, что крутящий момент в поперечном сечении вала численно равен алгебраической сумме скручивающих моментов, приложенных к отсечённой части:
Μк = ∑Μiz . |
(6.1) |
отс.ч
77

Помимо сосредоточенных скручивающих моментов на вал может действовать и распределённая по некоторому закону моментная нагрузка интенсивностью m(z).
а
б
Рис. 6.3.
Установим дифференциальную зависимость между интенсивностью m и крутящим моментом Мк. Для этого рассмотрим стержень с моментной нагрузкой m (рис. 6.3, а), из которого вырежем элемент длиной dz (рис. 6.3, б)
На него будут действовать моментная нагрузка m = const, которую можно считать равномерно распределённой ввиду малости dz, и уравновешивающие положительные крутящие моменты (в левом сечении – Мк, в правом – Мк+dМк, где dМк – приращение крутящего момента). Составим уравнение равновесия для элемента:
Σmz =0 ; Μк +mdz−(Mк +dMк )=0,
откуда
dMк |
=m. |
(6.2) |
|
||
dz |
|
График, показывающий закон изменения крутящих моментов по длине вала, называется эпюрой крутящих моментов. Положительные значения на эпюре будем откладывать вверх от горизонтальной базисной линии, а отрицательные значения – вниз. По-
78
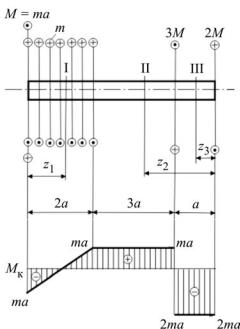
строение эпюры крутящих моментов принципиально ничем не отличается от построения эпюры продольных сил.
Пример. Построить эпюру крутящих моментов для вала, изображённого на рис. 6.4, а.
а
б
Рис. 6.4.
Решение. Разбиваем вал на три участка: I, II, III. Используя метод сечений, на участке I мысленно проводим в произвольном месте сечение, отбрасываем правую часть вала и рассматриваем равновесие отсечённой левой части с приложенным в месте сечения положительным крутящим моментом Мк и внешней нагрузкой. Тогда
всоответствие с принятым правилом знаков для участка I получаем: I. 0≤z1 ≤2a ;
79
Mк =−ma+mz1;
Mк (0)=−ma;
Mк (2а)=ma.
Проведя произвольные сечения на остальных участках вала, получим соответственно:
II. a≤z2 ≤4a (отбрасываем левую часть);
Mк =−2ma+3ma =ma.
III. 0≤z3 ≤a (отбрасываем левую часть);
Mк =−2ma.
По полученным данным строим эпюру Мк (рис. 6.4, б). На участке I величина крутящего момента линейно зависит от координаты сечения, так как действует равномерно распределённая моментная нагрузка интенсивностью m. На участках I и II крутящий момент не зависит от координаты z, поэтому эпюра имеет вид прямоугольников. В тех сечениях, где приложены внешние сосредоточенные моменты, получаются скачки на величину этих моментов.
Напряжения и деформации при кручении вала круглого поперечного сечения
Теория кручения вала круглого сплошного или кольцевого поперечного сечения основана на следующих допущениях, подтверждаемых экспериментально:
1.Сечения, плоские и нормальные к оси вала до деформации, остаются плоскими и нормальными к его оси и после деформации (гипотеза плоских сечений).
2.Радиусы, проведённые в сечении, остаются прямыми и поворачиваются на один и тот же угол.
3.Расстояния между поперечными сечениями не изменяются, т.е. продольные волокна не удлиняются и не укорачиваются.
80