
книги / Универсальные методы анализа проблем качества
..pdf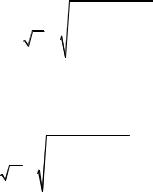
|
|
|
|
|
n |
Xi |
|
|
|
|
|
|
|
|
|
|
|
|
2 n X |
2 |
|
||||||||
|
S |
D |
|
i 1 |
|
|
|
|
|
|
|
, |
||
|
|
|
n 1 |
|||||||||||
|
|
|
|
|
|
|
|
|||||||
где S – выборочное |
стандартное |
отклонение; Х – диаметр; |
||||||||||||
D – дисперсия; n – число измерений. |
|
|
|
|
|
|
|
|||||||
Для расчетов используется пакет Excel: |
|
|||||||||||||
|
|
|
n |
Xi |
2 |
|
|
2 |
|
|
||||
|
|
|
n X |
|
|
|||||||||
S |
D |
i 1 |
|
|
|
|
|
|
|
0,083. |
||||
|
|
n 1 |
|
|
|
|||||||||
|
|
|
|
|
|
|
|
|
|
|
|
Для того чтобы в полной мере оценить процесс, необходимо посчитать процент годных деталей, а также количество дефектных деталей на миллион:
Рг G(U2 ) G(U1 ),
где Рг – процент годных деталей; G(U2) – вероятность появления дефектов выше верхней границы допуска, G(U2) = 0,95; G(U1) – вероятность появления дефектов ниже нижней границы допуска,
G(U1) = 0,39.
Рг G(U2 ) G(U1 ) 0,95 0,39 0,56 100 56 %.
Соответственно, количество негодных деталей
Рн.г 1 Рг 44 %.
Умножение значения Рн.г на миллион даст значение дефектных деталей на миллион (ppm):
ppm = Pн.г 1000 000 440 000 шт/млн.
Итоги. В ходе работы проанализирован процесс изготовления детали типа муфта. Анализ показал, что распределение случайной величины подчиняется нормальному закону распределения, что может являться причиной для утверждения о том, что данный процесс является однородным.
Границы зоны размаха R выходят за рамки поля допуска Td, наблюдается появление дефектных деталей, о чем свидетельству-
101
ет значение ppm = 440 000 шт/млн. Соотношение процента годных деталей к негодным 56/46, что говорит о большой дефектности процесса.
В результате построения гистограмм выявлено, что процесс имеет плохую настройку, так как величина математического ожидания смещена влево от центра. Разность значений центра и математического ожидания Т1 = 0,04 мм. Причиной этому могла послужить халатность рабочего.
Воспроизводимость является недостаточной, так как разброс больше поля допуска, R > Td. Также это подтверждает появление большого количества дефектных деталей – 44 %. Причиной этого могли послужить неполадки в оборудовании или какие-либо изменения в окружающей среде в один из дней работы.
Необходимо акцентировать внимание на совершенствовании процесса, в первую очередь для повышения воспроизводимости.
Точно заявлять на данном этапе о причинах несоответствий нельзя, поэтому рекомендуется провести поиск причины проблем.
Контрольные вопросы
1.Что такое гистограмма?
2.Каковы цели и задачи метода построения гистограммы?
3.Что такое нормальный закон распределения?
4.Назовите виды гистограмм.
5.Как производится анализ гистограмм?
6.Как производится анализ воспроизводимости процесса?
102
12. АНАЛИЗ ХАРАКТЕРА И ПОСЛЕДСТВИЙ ОТКАЗОВ (FMEA)
12.1. Описание FMEA
FMEA – Failure Mode and Effects Analysis – систематический метод профилактики дефектов. Метод FMEA используется на начальных стадиях планирования и создания как продукции, так и производственных процессов. Данный метод является одним из наиболее эффективных методов аналитической оценки результатов конструкторской деятельности, процессов (в том числе и испытаний) на таких важнейших стадиях жизненного цикла продукции, как ее конструирование и подготовка к производству. Анализ и прогнозирование дефектов, а также предупреждение их появления на этапе создания новой техники на основе теории проб и ошибок является важной задачей этого метода.
Анализ характера и последствий отказов выявляет потенциальные ошибки и дает оценку тяжести последствий для заказчика, предлагает пути устранения ошибок или уменьшения степени их влияния на качество. Анализ основан на теоретических знаниях и информации о прошлом опыте.
На этапе создания процессов методом FMEA решаются следующие задачи:
–обнаружение «слабых» мест и принятие мер по их устранению при планировании производства;
–подготовка серийного производства;
–исправление тех процессов серийного производства, которые оказываются нестабильными.
Наиболее часто метод FMEA применяют:
–при разработке новых изделий;
–разработке новых материалов и методов;
–изменении продукции или операции;
–новых условиях применения существующей продукции;
–недостаточных возможностях технологическогопроцесса;
103
–ограниченных возможностях контроля;
–использовании новых установок, машин и инструментов;
–высокой доле брака;
–возникновении риска загрязнения окружающей среды, нарушении норм технической безопасности;
–существенных изменениях организации работы.
Метод FMEA позволяет выявить потенциальные несоответствия, их причины и последствия, оценить риск предприятия
ипринять меры для устранения или снижения опасности. Этот метод позволяет также исключить ошибки на ранней стадии создания продукции и процессов, исходя из детализации процессов
истрогого учета всех исполняемых функций. Он обладает значительной эффективностью при создании конкурентоспособной
продукции в короткие сроки и значительно экономит время и средства.
Введение и проведение метода FMEA возможно лишь при активном участии руководства.
С использованием метода FMEA возможны:
–анализ конструкции,
–анализ процессов.
FMEA комплексной системы (далее – просто системы) учитывает функции взаимодействия между отдельными компонентами, не исследуя при этом сами компоненты. С помощью FMEA системы осуществляют исследование с учетом требований технического задания на раннем этапе.
В классическом методе FMEA конструкции рассматриваются отказы конструкции, касающиеся функций продукции. Искомые причины (первопричины) – это слабые места конструкции. FMEA конструкции анализирует только сами компоненты (узлы или детали). FMEA конструкции часто составляет основу для FMEA процесса, так как при анализе конструкции в качестве причины отказа могут быть обнаружены отклонения в производственном процессе. В рамках классического метода FMEA процесса рассматриваются отказы, касающиеся отдельных этапов
104
процесса, а также зависимые отказы на основании предшествующих этапов процесса и элементов изделия.
Прогнозирование возможных дефектов и анализ их последствий может производиться по требованию заказчика. При конструировании метод FMEA применяют в начале проектирования продукции и перед апробированием конструкции и официальным окончанием разработки. При помощи метода дается оценка состояния производствапри последующем серийномвыпускепродукции.
Оценку риска необходимо производить в отношении слабых мест объекта, которые определяются по совокупности трех показателей: вероятность появления потенциальных отказов, значение потенциальных отказов для заказчика и вероятность необнаружения потенциальных отказов перед поставкой.
12.2. Основные положения FMEA
Анализ характера и последствий отказов производится с использованием коэффициента риска Кр:
Кр Кп Кн Ко ,
который показывает, какие возможные отказы (и их причины) являются наиболее существенными, а следовательно, по каким из них следует принимать предупреждающие меры в первую очередь. Анализ производится с использованием коэффициентов, принимающих во внимание все три указанные важнейшие факторы влияния накачество продукции. Кэтимкоэффициентамотносятся:
–Кп – коэффициент, учитывающий значение последствий отказов (тяжесть последствий проявления причин отказов) для потребителя (табл. 22). Потребителем конструкции выступает конечный потребитель (покупатель).
–Кн – коэффициент, учитывающий вероятность Рн, с которой отказ или его причина не могут быть обнаружены до возникновения последствий непосредственно у потребителя (табл. 23). Нужно отметить, что вероятность необнаружения причины численно равна среднему выходному уровню дефектности.
105
Таблица 2 2 |
||
Значения последствий отказа |
|
|
|
|
|
Значение |
Кп |
|
Вероятность, близкая к нулю, что дефект может иметь ка- |
|
|
кие-либо ощутимые последствия. Видимое воздействие на |
1 |
|
функцию или на дальнейшее выполнение операций процесса |
||
|
||
невозможно |
|
|
Незначительное влияние на функции системы или даль- |
|
|
нейшее выполнение операций процесса (второстепенное не- |
2–3 |
|
соответствие). Потребитель, вероятно, заметит лишь незначи- |
||
|
||
тельную неисправность системы |
|
|
Умеренное влияние. Вызывает недовольство потребителя. |
|
|
Функции системы или дальнейшему выполнению операций |
4–6 |
|
процесса нанесен ущерб (значительное несоответствие) |
|
|
Существенное влияние. Существенные функции системы |
|
|
полностью выпадают или промежуточный продукт не подда- |
|
|
ется дальнейшей обработке (значительное несоответствие). |
7–8 |
|
Несоответствие вызывает досаду потребителя, но безопас- |
|
|
ность или соответствие законам здесь не затрагиваются |
|
|
Очень существенное влияние. Тяжелые последствия, веду- |
9 |
|
щие к остановке производства |
||
|
||
Критическое. Отказ угрожает безопасности (опасность для |
|
|
жизни и здоровья людей) и противоречит законодатель- |
10 |
|
ным предписаниям |
|
Ко – коэффициент, учитывающий вероятность Ро отказа.
Ро 1 Рб ,
где Рб – вероятность отсутствия отказа (табл. 24).
При определении Ро исходят из того, что отказ не обнаружится до тех пор, пока потребитель не начнет пользоваться изделием.
Каждый из этих трех коэффициентов может иметь числовые значения в пределах от 1 до 10, поэтому коэффициент риска Кр колеблется от 1 до 1000. Следует обращать внимание на устранение тех причин, которые характеризуется наибольшими значениями коэффициента риска.
106
Таблица 2 3
Характеристика вероятности пропуска отказа или причины отказа
Характеристика вероятности |
Вероятность |
|
|
невыявления |
Кн |
||
или причины отказа |
|||
Рн, % |
|
||
|
|
||
Близкая к нулю. Возникающие отказы или при- |
|
|
|
чины отказов явно распознаются (например от- |
Не более 0,01 |
1 |
|
сутствие отверстия для сборки) |
|
|
|
Очень маленькая. Выявление возникающих |
|
|
|
отказов или причин отказов очень вероятно, на- |
|
|
|
пример с помощью большого количества незави- |
Не более 0,1 |
2–3 |
|
симых друг от друга испытаний / технологиче- |
|
|
|
ских проверок (автоматический сортировочный |
|
|
|
контроль одного признака) |
|
|
|
Небольшая. Выявление возникающих отказов |
|
|
|
или причин отказов вероятно; проводимые ис- |
Не более 0,3 |
4–5 |
|
пытания / технологические проверки относи- |
|
|
|
тельно достоверны |
|
|
|
Умеренная. Выявление возникающих отказов |
|
|
|
или причин отказов менее вероятно; проводимые |
|
|
|
испытания / технологические проверки недоста- |
Не более 2 |
6–7 |
|
точно достоверны (традиционный контроль – |
|
|
|
выборочный контроль, эксперименты, тесты) |
|
|
|
Высокая. Выявление возникающих отказов или |
|
|
|
причин отказов весьма затруднительно; прово- |
|
|
|
димые испытания / технологические проверки |
|
|
|
неэффективны (например контроль ручным спо- |
Не более 10 |
8–9 |
|
собом, что предполагает сильную зависимость от |
|
|
|
персонала; признак распознается с трудом – не- |
|
|
|
правильно выбран материал) |
|
|
|
Очень высокая. Возникающие отказы или |
|
|
|
причины отказов выявить нельзя: технологиче- |
Более 10 |
10 |
|
ские проверки не проводятся (например: нет |
|||
|
|
||
доступа, нет возможности для контроля) |
|
|
107
108
Таблица 2 4
Характеристика появления отказа
|
|
Доля отказов / |
|
Характеристика появления отказа |
дефектов |
Ко |
|
|
|
Рп, % |
|
Вероятность близка к нулю |
|
Менее 0,00001 |
1 |
Очень незначительная вероятность. Конструкция в общем со- |
|
|
|
ответствует прежним проектам, при применении которых наблю- |
0,00001 < Ро ≤ 0,0005 |
2–3 |
|
далось сравнительно незначительное количество отказов |
|
|
|
Незначительная вероятность. Конструкция в общем соответст- |
|
|
|
вует проектам, применение которых привело к появлению не- |
|
|
|
большого числа отказов. |
|
0,0005 <Ро ≤ 0,5 |
4–6 |
Технология сопоставима с прежней, при которой в незначитель- |
|
|
|
ном объеме появляютсядефекты |
|
|
|
|
|
|
|
Средняя вероятность. Конструкция в общем соответствует про- |
|
|
|
ектам, применение которых в прошлом всегда вызывало трудно- |
0,5 < Ро ≤ 5 |
7–8 |
|
сти. Процесс сопоставим с прежним, |
который часто приводил |
||
к дефектам |
|
|
|
|
|
|
|
Высокая вероятность. Конструкция |
ненадежна. Требования |
|
|
к проекту учтены незначительно (менее 50 %). Процесс нестабилен. |
Ро ≤ 5 |
9–10 |
|
Можно почти с уверенностью сказать, что дефекты появляются в |
|||
значительномколичестве |
|
|
|
|
|
|
|
108
Обычно считают опасными причины при Кр Кр.п 100,
где Кр.п – принятое на предприятии предельное значение Кр.
Для особо ответственных деталей или конструкций считают, что если хотя бы один из коэффициентов Ко, Кн и Кп имеет значение, равное 10, то при любом значении обобщенного коэффициента риска Кр следует проводить FMEA.
Правильным считается подход, при котором все приведенные причины дефектов проверяются на возможность осуществления мероприятий по их устранению. Важнейшим этапом анализа характера и последствий отказа является проведение целенаправленных мероприятий по предупреждению дефектов. В связи с необходимостью ограничения затрат на устранение ошибок и их последствий следует отдавать предпочтение мероприятиям, предупреждающим отказы, а не мероприятиям по их выявлению.
Для анализа объект необходимо разбить по уровням и затем рассматривать его как многоуровневую структуру. Оценивается качество объекта на каждом из уровней, начиная с верхнего и заканчивая нижним.
При анализе процессов нужно также перечислять все возможные ошибки, приводящие к отказу, которые могут появиться при выполнении работ, входящих в рассматриваемый процесс. В практических условиях FMEA производится при групповой работе с участием сотрудников заинтересованных служб и отделов. При анализе действующих производственных процессов бывает также полезно объединение в группу участников, выполняющих отдельные операции. Рабочие группы могут в процессе работы расширяться для выполнения специальных задач.
Один из примеров формы, используемой при проведении FMEA, представлен втабл. 25.
109
110
Таблица 2 5
Пример формы, используемой при проведении FMEA
|
|
|
|
|
|
|
|
|
|
|
Регистрационный |
|||||
Фирма: |
|
|
FMEA конструкции: |
|
|
|
|
|
|
номер |
|
|||||
|
|
|
|
|
|
|
|
|
|
|
|
формуляра: |
|
|||
|
|
|
|
|
|
|
|
|
|
|
|
|
|
|
|
|
Ответственный |
|
|
|
|
|
|
|
|
|
|
|
Страница |
|
|||
|
|
Наименование элемента конструкции: |
|
|
|
документа: |
|
|||||||||
исполнитель: |
|
|
|
|
|
|
||||||||||
|
|
|
|
|
|
|
|
|
Всего страниц: |
|||||||
|
|
|
|
|
|
|
|
|
|
|
||||||
Отдел: |
|
|
Функция: |
|
|
|
|
|
|
Дата: |
|
|||||
Номер |
Вид по- |
Возможное |
|
Возможная |
|
Меры по |
|
|
|
Меры по |
|
|
|
|
|
|
отказа |
тенциаль- |
последст- |
Кп |
причина отказа |
Ко |
обнаруже- |
Кн |
|
Кр |
предупреж- |
1 |
|
1 |
1 |
|
1 |
|
ного |
вие отказа |
|
нию отказа |
|
дению |
Кп |
|
К0 |
Кн |
|
Кр |
||||
|
отказа |
|
|
|
|
|
|
|
|
отказа |
|
|
|
|
|
|
|
|
|
|
|
|
|
|
|
|
|
|
|
|
|
|
|
|
|
|
|
|
|
|
|
|
|
|
|
|
|
|
|
|
110