
книги / Прогнозирование несущей способности композитных фланцев корпусных деталей авиадвигателей
..pdfК подготовительной группе операций относится сухая примерка панелей. Примерка панелей производится прикладыванием их на оправку с целью замера возникающего зазора или нахлеста между ними. Если величина последних не превышает заданного норматива, начинается процесс формования корпусной де тали. Схема примерки панелей для кожуха обшивки показана на рис. 1.5.
1
Рис. 1.5. Примерка панелей кожуха обшивки авиадвигателя: 1 — жгут. 2 — поджимное кольцо. 3 — оправка
Формовочные операции начинаются с выкладки внутренней оболочки корпусной детали на предварительно обезжиренную оправку. В качестве приме ра рассмотрим формовочные операции для изготовления кожуха обшивки авиа двигателя. В конусной части кожуха кольцевые слои наматываются лентой препрега шириной 50 мм с шагом на ширину ленты, в цилиндрической - лентой ши риной, равной длине самой цилиндрической части. Процесс выкладки внутрен ней оболочки кожуха показан на рис. 1.6. Продольные слои выкладываются из ранее нарезанных кусков ткани. После набора необходимой толщины внутрен ней оболочки укладываются готовые конструктивные элементы — панели и на кладки (рис. 1.7). Сверху аналогично внутренней формируется наружная оболоч ка.
Следующий этап — формование стыковочных фланцев. Формование фланца конусной части кожуха показано на рис. 1.8. На рис. 1.8,а изображена
первая стадия этой операции, заключающаяся в укладке секторов между пакета ми слоев внутренней и наружной оболочек. Во время второй стадии подрезают, а затем подгибают слои наружной оболочки (рис. 1.8,6). Следующая стадия —
подрезка и подгиб слоев внутренней оболочки. После чего к торцу кожуха приформовывают пакет из десяти слоев препрёга (рис. 1.8,в). На заключительной стадии (рис. 1.8,г) производится поджим торца кожуха специальным кольцом.
f
Рис. 1.6. Выкладка внутренней оболочки кожуха обшивки авиадвигателя: 1 — продольный слой, 2 — кольцевой слой, 3 — оправка
Рис. 1.7. Установка панелей и накладок при изготовлении кожуха авиадвигателя: I— панель. 2— накладка
Процесс формования стыковочного фланца цилиндрической части кожуха показан на рис. 1.9. Сначала укладывают шесть слоев из ранее выкроенных заго товок, затем еще пять слоев и далее один слой согласно рис. 1.9,а. Затем, после укладки пакета из четырнадцати слоев, закрепляют весь пакет формующим ре зиновым жгутом с хомутом (рис. 1.9,6). После этой операции все предваритель но выложенные слои загибают на торец жгута, доформовывают еще девять слоев и устанавливают поджимное кольцо (рис. 1.9,в).
Завершает группу формовочных операций процесс отверждения скомпо нованного кожуха. Перед началом полимеризации кожух упаковывают в ваку умный мешок, проверяют герметичность и помещают в автоклав.
Режим полимеризации включает следующие операции: 1) поднятие давления в автоклаве до 5±0,5 кг/схМ2; 2) включение системы нагрева автоклава;
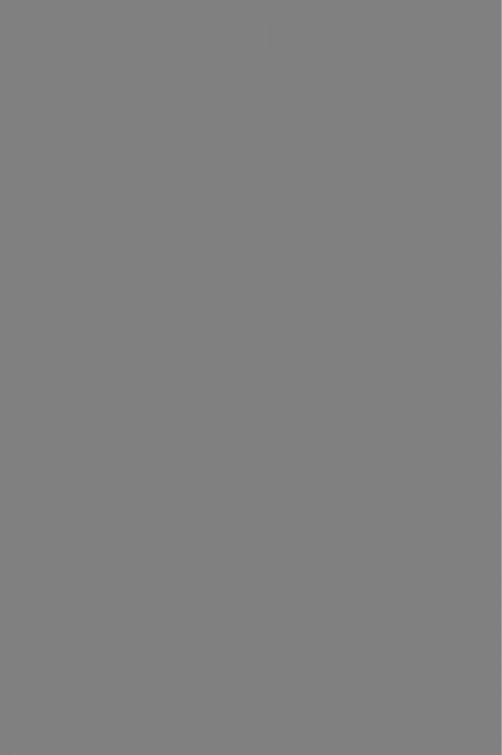
3) поднятие температуры в узле до 140±5СС (температура контролируется по ранее установленным термопарам), время подъема не должно превышать 6
часов;
4) выдержка при температуре в узле 140±5°С в течение 2±0,25ч;
5) поднятие температуры в узле до 160±5°С. температура воздуха в авто
клаве не должна превышать 180СС;
6) выдержка при температуре в узле 160±5°С в течение 4±0,25ч; 7) охлаждение до 100°С, скорость охлаждения не более 10 град/ч, одно
временно снижение давления в автоклаве до 3±0,5 кг/см2, скорость сброса дав ления не более 0,5кг/см2 в час, при этом давление в автоклаве 3±0,5 кг/см2 долж
но быть достигнуто при температуре 100-110°С; 8) отключение вакуумной системы;
9) охлаждение до 40еС, скорость охлаждения не более 10 град/ч; 10) сброс давления до 0 кг/см2;
После окончания полимеризации кожух извлекают из автоклава, демонти руют дренажно-вентиляционный пакет, демонтируют оправку, снимают отвер жденную конструкцию и проводят перфорацию. Затем производят доводочные операции.
Доводочные операции изготовления композитных корпусных деталей предусматривают ремонт дефектов. После внешнего осмотра изделия и нахож дения дефектных мест их зачищают, обезжиривают и покрывают специальным клеем. Клей отверждают при температуре 15-35°С в течение 24 часов. Отремон тированное место снова зачищают и контролируют.
Заключительная, стадия технологического процесса изготовления компо зитных корпусных деталей содержит следующие стандартные операции:
1) дефектоскопия,
2) нанесение лакокрасочного покрытия,
3)окончательный контроль,
4)укупорка;
после чего изделие готово к транспортировке.
Опыт отработки технологии изготовления композитных корпусных дета лей свидетельствует, что уровень остаточных напряжений в них невелик. В ча стности, при хранении готовых корпусных деталей и комплектующих элементов в течение года не выявлено ни одного случая заметного нарушения формы или коробления детали, а также случаев смещения осей смежных отверстий.
2. МАТЕМАТИЧЕСКАЯ ПОСТАНОВКА ЗАДАЧИ РАСЧЕТА НАПРЯЖЕННО-ДЕФОРМИРОВАННОГО СОСТОЯНИЯ КОМПОЗИТНЫХ ФЛАНЦЕВ КОРПУСНЫХ ДЕТАЛЕЙ
2.1. Постановка осесимметричной задачи теории упругости для неоднородного тела
Объектом исследования являются композитные многослойные фланцы корпусных деталей авиадвигателя, полученные последовательной выкладкой слоев эпоксидных стеклопрепрегов ЭДТ-69Н-С на основе ткани Т-10-80 и одно направленных карбопрепрегов 11Э. В некоторых конструктивных вариантах применяется также кольцевая подмотка однонаправленным стеклоровингом РВМН-10, пропитанным связующим ЭДТ-694. Схемы армирования рассматри ваемых фланцев показаны на рис.2.1-2.3. В расчетную схему каждого фланца включался также небольшой участок соответствующей корпусной детали, со стоящий из наружной и внутренней оболочки, сформированной слоями стеклопрепрега ЭДТ-69Н-С, и серединного элемента жесткости коробчатого сечения, состоящий из двух слоев стеклопрепрега ЭДТ-69Н-С.
На рассматриваемые корпусные детали действуют инерционные попереч ные силы, обусловленные весом деталей с присоединенными устройствами с учетом заданной перегрузки 5,33g ; отрывающая продольная сила сопла и внут реннее давление. В соответствии с принятой схемой расчета прочности фланце вых соединений [8, 9, 11, 25] внешние силы приводились к эквивалентным на
грузкам, равномерно распределенным по поверхностям сопряжения фланцев с деталями (St). На участках Su, соответствующих зонам болтового соединения,
принимались условия свободного опирания. Схемы граничных условий для че тырёх исследуемых фланцев показаны на рис.2.4,а-г. Далее для расчета напря женно-деформированного состояния и оценки прочности фланцев сформулиру ем осесимметричную задачу теории упругости для неоднородного тела, глобаль ная система координат OrzO приведена на рис.2.4,д.
Математическая постановка осесимметричной задачи теории упругости в вариационной формулировке заключается в отыскании минимума функционала Лагранжа [1], вариация которого при отсутствии массовых сил имеет вид
|
(2. 1) |
где ztj и 5б/у - тензор и вариация тензора деформаций, |
тензор упругих мо |
дулей, Siij - вариация вектора перемещений, F, - вектор внешних сил.
Многосвязная область V имеет внешнюю границу S=Su-St и состоит из
подобластей соответствующих слоям стекло- и карбопрепрегов различной ориентации, с межслойной границей Sd (см. рис.2.4).
Рис. 2.1. Схема армирования фланца силового корпуса реверсивного устройства 1— ------ * — слой тканого стеклопластика с основой вдоль образующей,
Д - Д - Ч — слой тканого стеклопластика с основой вдоль кольцевого направления,
□r i u j — слой однонаправленного углепластика с волокнами в кольцевом направлении,
—слой однонаправленного углепластика с волокнами вдоль образующей
PNRPU
Рис. 2.2. Схема армирования фланца корпуса наружной задней подвески со звукопоглощающим контуром: 1__ LZT.1 — слой тканого стеклопластика с основой вдоль образующей;
[М- U — слой тканого стеклопластика с основой вдоль кольцевого направления;
— слой однонаправленного стеклопластика с основой вдоль кольцевого направления

Рис.2.4. Схема граничных условий в задаче расчета напряженно-деформированного состояния
композитных фланцев
Дополнительными условиями для функционала (2.1) являются геометри ческие уравнения
|
|
£' j = \ ( ll'j |
+ ии)> |
|
|
(2.2) |
||
кинематические граничные условия на части поверхности Su |
|
|||||||
|
|
|
и2 = 0 |
I |
|
|
|
(2.3) |
|
|
|
z |
I О |
|
|
|
|
и условия на межслойной границе 5^(см. рис.2.4,а) |
|
|
|
|||||
U {1) |
= U |
i2) I |
£ j..(1) • Yl |
= (Т- (2) |
• Y\ |
J |
(2.4) |
|
ui |
ui |
I |
о ,u /y |
п] |
uij |
rt |
|
|
|
|
|
bd |
|
|
|
|
|
Для каждого ортотропного слоя подобласти V*p) компоненты тензора мо
дулей упругости Су*} зависят не только от вида препрега, но и от его ориента
ции относительно глобальной системы координат.
Введем локальную систему координат слоя~препрега ОХ[Х2Хз. В ней ось OXj совпадает с направлением основы, ОХ2- утка, ОХз - перпендикулярна плос
кости слоя. В установленной локальной системе координат компоненты тензора
С будем определять через технические упругие постоянные слоев по формулам
[36]:
|
1 n |
|
SJ |
V |
|
|
|
< |
|
||
Q 111= |
|
bJt o |
|||
E22A 4 Eyi |
Ец> |
||||
C 2222 = |
1 |
f — - |
V3l)I |
||
|
ЕъгА ^ 1 1 |
£3 3 )I' |
|||
|
1 |
|
|
|
(2.5) |
Q 3 3 3 = EnA <E22 |
|
||||
|
|
||||
|
1 |
|
|
|
N |
Q 1 2 2 = |
|
V3lV23 ^ |
v 12 |
||
E^A < |
^22 |
|
£\\) |
||
|
1 |
|
v 12v 23 ^ |
V3]_ |
|
Ci 133“ |
ЕЪЪА |
|
|
—,---- |
|
^ |
^11 |
|
E |
||
|
|
|
ЗЗУ |
||
|
1 |
|
V12V31 ^ |
V32_ |
|
C2233 = |
EUA l |
|
1 |
E21J |
|
£33 |
^ |
||||
C2323 = |
Gn,< |
|
3 , C, |
||
|
(•1313 = |
|
|||
|
|
|
Е,-
Л = - * a ~ 7 v v v - E i i . v 2 - Е Ж у,1 ^33 ч
U v23V31— р: v31— — vi2 — — v23 j
^ 11^22-^33 |
33 |
£11 |
'22 |