
книги / Современные методы и средства балансировки машин и приборов
..pdf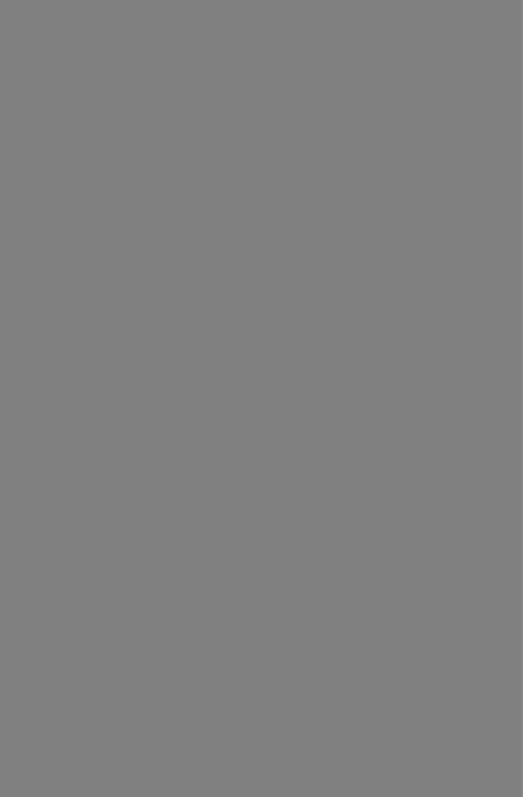
Рис. 7.8. Управляемое балансирующее устройство (США)
размеров. С другой стороны, емкость устройства в процессе работы станка при проведении балансировок снижается, так как постепенно заполняются отсеки резервуара.
К тому же создание устройства данной конструкции большой емкости не имеет смысла в связи с тем, что при останове шлифоваль ного шпинделя через кольцевые щели 6, 7, 13, 15 происходит истече ние жидкости, и последующий пуск шпинделя производится при максимальном значении дисбаланса, которое ограничивают предва рительной балансировкой шлифовального круга вне станка. Несмо тря на указанные недостатки конструкции, данное устройство яв ляется лучшим из действующих устройств по точности, производи тельности, надежности и безопасности.
Вторую схему реализует также устройство [Пат. 3376759 (США)], представленное на рис. 7.8. В данной конструкции четыре коррек тирующие массы 3, 7, 11, 13 кинематически попарно связаны и произ водят балансировку независимо по двум взаимно перпендикулярным направлениям. Их перемещение осуществляется от электродвигате лей 1,9 с помощью червячных передач 2,4 и 10, 8. Симметричность перемещения корректирующих масс обеспечивается зацеплением зубчатых колес 5, 12 и 6, 14. Данное УБУ является характерным представителем целой группы устройств различных конструктивных исполнений, основанных на второй схеме, общим недостатком кото рых является перемещение в процессе балансировки центров масс корректирующих масс вдоль радиуса относительно оси ротора. В результате периодического преодоления центробежных сил в про цессе балансировки снижается надежность устройств и ограничи вается область их применения, т. е. исключается возможность при менения УБУ такого типа для уравновешивания высокоскоростных
шпинделей.
Устройства, работающие по третьей схеме, имеют существ иные преимущества, связанные с тем, что центры масс корректирующих масс перемещаются по дугам окружностей с центром на оси ротора,
T. è. при перемещении корректирующих масс в процессе баланси ровки не производится работа против центробежных сил. Это обстоя тельство является предпосылкой для создания надежных УБУ для скоростных шпинделей. Наиболее удачной реализацией третьей схемы является АБУ мод. ME П123, созданное во ВЗМИ (рис. 7.9). Балансировка шлифовального круга осуществляется последователь ным многократным поворотом корректирующих масс / и 2, выполнен ных в виде колец. Вращение колец осуществляется от привода 3, раз мещенного с противоположной стороны шпинделя 7 Связь между приводом и корректирующими массами осуществляется штоком 3, расположенным внутри шпинделя. Поочередное подключение штока к каждому кольцу производится электромагнитом 4. Вращение колец в виде обгона шпинделя или запаздывания по отношению к нему со скоростью порядка 1 об/мин осуществляется при включении элек тромагнитных муфт 5 и 6 привода. Устройство управляется вручную или автоматически. Балансировка ведется методом случайного поиска. Данное устройство обладает целым рядом положительных свойств, которые обеспечивают его работоспособность. Так, напри мер, кинематика АБУ допускает неограниченное увеличение точно сти балансировки, которая ведется только уменьшением начального значения дисбаланса, при перемещении корректирующих масс не со вершается работа против центробежных сил. Устройство имеет зна чительную емкость, допускает автоматическое управление процессом балансировки и замену шлифовального круга без демонтажа самого устройства.
Не останавливаясь на недостатках данного устройства, перейдем к УБУ (рис. 7.10), также разработанному во ВЗМИ, конструкция которого является развитием устройств, работающих по третьей схеме и лишена ряда недостатков предыдущего АБУ. Устройство (рис. 7.10) снабжено тремя кольцевыми корректирующими массами У, 2, 3, которые при пуске и останове шлифовального шпинделя фиксируются
Рис. 7.9. Автобалаисирующее устройство мод. ME П123 (ВЗМИ):
В — вибро преобразователь
Рис. 7.10. Автобалансирующее устрой ство (ВЗМИ)
подпружиненными штифтами 6. После разгона шпинделя под дей ствием центробежных сил штиф ты 6 расфиксируют кольца и по стоянство их углового положения между отдельными балансиров ками обеспечивается за счет сил трения, создаваемых подпружи ненными штифтами 4.
Перемещены корректирующих масс относительно шпинделя осу ществляется за счет торможения колец фрикционными, гидравли ческими, пневматическими или электромагнитными устройствами 5. Такое УБУ позволяет проводить балансировку только уменьшением начального значения дисбаланса. Для этого начальным положением корректирующих масс должно быть такое положение, при котором дисбалансы отдельных корректирующих масс расположены под уг лом 120° Не останавливаясь на положительных качествах данного устройства общих с предыдущим, рассмотрим его новые положи тельные свойства по сравнению с устройством мод. ME П123. Привод устройства является бесконтактным, отсутствуют переключения ки нематических цепей и детали, находящиеся во взаимном вращении между отдельными балансировками. Конструкция допускает уста новку УБУ на шпиндель станка без его модернизации, состоит из минимального числа деталей, которые являются унифицирован ными.
Существуют однако и недостатки, общие с предыдущим устрой ством. Например, наибольшей производительности устройства можно достичь, осуществляя балансировку одновременно всеми корректи рующими массами, данные устройства этого не допускают. Баланси ровка ведется методом случайного поиска, это уменьшает произво дительность процесса, усложняет систему управления и, следова тельно, снижает ее надежность. Не решен окончательно вопрос фик сации корректирующих масс при пуске и останове шпинделя и обес печения минимального сопротивления их рабочему перемещению при балансировке.
Несмотря на указанные недостатки, данное устройство является простым, надежным, способно работать на быстроходных шпинделях, допускает использование автоматической системы управления и в от личие от устройства [Пат. 1481489 (Великобритания)], обладая боль шой емкостью, допускает замену шлифовального круга без демонтажа устройства.
Конструктивные реализации четвертой схемы идут по двум ос новным направлениям. Первое направление заключается в том, что корректирующие массы совершают движения своими центрами масс не только по дугам окружностей, но и вдоль радиуса. Тем самым при перемещении корректирующих масс совершается работа против
центробежных сил. В данном случае наблюдается явное отступление от прогрессивного начала третьей схемы. Те преимущества, которые дает упрощение системы автоматического управления процессом балансировки (в данном случае можно осуществлять направленную балансировку), компенсируются ограничением области применения этих устройств — такие УБУ не обеспечивают надежности при ис пользовании на быстроходных шпинделях. К устройствам этого типа относится конструкция [Пат. 1203244 (Великобритания)], приве денная на рис. 7.11. Корректирующая масса УБУ 1 установлена на червячном колесе 2 и имеет возможность вращаться вокруг оси этого колеса с помощью электродвигателя 3, изменяя значение дисбаланса. Изменение угла дисбаланса корректирующей массы достигается вращением вокруг оси шпинделя с помощью электродвигателя 5 кор пуса 6, несущего корректирующую массу, оба электродвигателя и соответствующие элементы кинематических цепей. Положение кор ректирующей массы, определяющее значение и угол дисбаланса, отслеживается с помощью датчиков (первый датчик — 4, второй дат чик стоит на оси червячного колеса 2) и регистрируется прибором 8. Электрические сигналы управления и контроля передаются через узел щеток 7
Второе направление конструктивной реализации четвертой схемы заключается в том, что две корректирующие массы 1 и 2 (рис. 7.12) в процессе балансировки имеют возможность перемещений в виде вращения вокруг оси шпинделя. Угол суммарного дисбаланса двух корректирующих масс изменяется одновременным их вращением вместе с обоймой 3 от электродвигателя 4 посредством червячной передачи 5, 6. Значение дисбаланса изменяется при симметричном повороте в противоположных направлениях корректирующих масс 1 и 2, который осуществляется от электродвигателя 7 через червячную передачу 8, 9 и шестерни 10, 11. Реверс одной корректирующей массы
Система
Рис. 7.11. Управляемое балансирующее устройство (Великобритания)
Рис. 7.12. Автобалансирующее устройство (США)
относительно другой осуществляется с помощью паразитного зуб чатого колеса, входящего в зацепление с шестерней 10. Данное устройство [Пат. 3698263 (США)] является более надежным, чем показанное на рис. 7.11. В его конструкции реализованы принципы, позволяющие вести одновременную направленную автоматическую балансировку шлифовального круга по углу и значению дисбаланса и использовать устройство на скоростных шпинделях. Однако сама конструкция является сложной, электродвигатели расположены на значительном расстоянии от оси шпинделя, энергия передается через узел щеток, поэтому по сравнению с устройствами, приведенными на рис. 7.7 и 7.10, данное УБУ является менее перспективным.
В заключение следует отметить, что данный анализ посвящен не столько выбору среди уже известных устройств наиболее перспек тивных конструкций, сколько формированию основных, наиболее существенных критериев их оценок. Такими критериями следует счи тать, по нашему мнению, траектории движения общего центра масс корректирующих масс [10], и предложенные в этом параграфе другие оценки свойств балансирующих устройств.
7.4. ПОГРЕШНОСТИ КОРРЕКТИРОВКИ ДИСБАЛАНСОВ РОТОРОВ СВЕРЛЕНИЕМ
(Б. И. Горбунов)
Среди технологических методов, используемых для корректировки дисбалансов металлических роторов, одно из ведущих мест занимает сверление. Например, оно используется в технологии изготовления шкивов, коленчатых валов, роторов гиромоторов, часовых деталей и т. п.
Оси просверливаемых при балансировке отверстий могут распо лагаться параллельно, перпендикулярно и наклонно к оси ротора,
При сверлении сквозных отверстий не возникает производственный погрешностей, обусловливаемых выбором расчетного положения плоскостей коррекции или упрощением формы отверстия в осевом сечении. Вместе с тем в ряде работ не учитывается наличие кониче ской части в глухом отверстии, что приводит к существенным ошиб кам при определении положения центрамасс высверливаемого объема. Для отверстия диаметром 2 мм и глубиной 2 мм координата центра масс вдоль оси отверстия будет равна 0,81 мм, а при замене реального отверстия отверстием с плоским дном эта координата принимается равной 1 мм, что дает погрешность в 23,5 %. При уменьшении глу бины эта ошибка еще более существенна.
Оценивая высверливаемый объем V суммой объемов цилиндра
Кц и конуса Кк, получим для сверла с углом при вершине 2ср = |
120° |
|
V = Уц + |
= яг2 (Л - 2г/3 /3 ) , |
(7.23) |
где г — радиус отверстия |
(рис. 7.13); h — глубина сверления |
(или |
отверстия). |
|
|
Координату центра масс высверливаемого объема ух при любой глубине сверления х найдем по формуле
6 Уъх- — 8гх + у Ъ 2
(7.24)
12 У Зх — 8г
Эта зависимость отражена на графике (рис. 7.4) для радиусов от верстий 1; 1,5 и 3,0. Здесь наглядно прослеживается методическая ошибка замены реального отверстия отверстием с плоским дном, особенно при глубинах, не превышающих радиуса.
При выборе положения плоскости коррекции вдоль оси ротора рекомендуется пользоваться соотношением ар = Ith, где h — полная расчетная глубина сверления.
В. А. Захаров рекомендует k — 0,414, а К- С. Терехова — k = 0,4 исходя из того, что при этом создаются наиболее благоприят ные условия балансировки, так как при сверлении на неполную глу бину будет иметь место наименьшая моментная погрешность.
Если ротор (см. рис. 7.13) вращается с угловой скоростью ш, то отверстие, просверленное на полную глубину Л, своим центром масс разместится в плоскости коррекции и создаст расчетный момент на плече L. При сверлении более мелких отверстий на глубину х возни
кает погрешность |
в виде |
момента АЛ1 = |
Fl = CiV* (ар — ух), |
где |
|
Cj — постоянная процесса |
корректировки; |
cY= y.M^R/g', R — ра |
|||
диус, на |
котором |
расположены оси отверстий; g — ускорение силы |
|||
тяжести; ум — удельный вес; I — расстояние между расчетным и фак |
|||||
тическим |
центром |
масс; |
— объем материала при сверлении |
на |
|
глубину |
х. |
|
|
|
< |
При сверлении только конической частью сверла, т. е. при х |
|||||
< 0,578г |
|
|
|
|
|
|
|
|
|
(7.25) |
А при отверстии глубиной х ^ 0,578г имеем коническую и цилин дрическую часть и моментную погрешность
2г |
\ и |
6 / з * 2 — 8гх + |
УЪг* ' |
(7.26) |
|
Дм — |
|
_ ' |
12|ЛЗх— 8г |
||
= с ^ 5 ( дг— з 7 з ) ( м |
|
||||
Обе последние формулы выражают зависимость |
|
|
|||
Лм/Ci = |
/ (х, г, h, k) |
|
|
(7.27) |
и были для соответствующих участков просчитаны на ЭВМ. Это позво лило получить графики (рис. 7.15, а—г), вскрывающие влияние раз личных факторов на значение моментной погрешности при разной глубине сверления.
Влияние диаметра сверления (рис. 7.15, а) одинаково как на уст раняемый дисбаланс, так и на возникающую погрешность. Оно опре деляется степенной зависимостью погрешности от этого фактора. При глубине сверления 2 мм погрешность сверления диаметром 2 мм вдвое меньше, чем диаметром 3 мм, и втрое — при диаметре 4 мм. Следует иметь в виду, что данный график построен для полной глу бины в 3 мм.
Полная глубина сверления также влияет на значение погреш ности (рис. 7.15, б). Этот график построен для отмеченной выше вели чины k = 0,4, а на рис. 7.15, в для k = 1 видно влияние полной глу бины сверления на погрешность моментную и подобное же влияние на корректирующий момент.
Влияние значения и знака k на характер изменения моментной погрешности прослеживается на рис. 7.15, а. Отрицательные значе ния этого коэффициента всегда приводят к отрицательным (условно) моментам. Положительные k позволяют получать в зависимости от текущего значения глубины сверления погрешности любого знака и различного значения. Видно, что k — 0,4 не гарантирует получе ния минимальной моментной погрешности. Это следствие того, что в цитированных выше работах принято отверстие с плоским дном,
без конической части. Рассмотрение результатов
расчета позволяет сделать не-
Ух
Г=1
2,0
1,5 1’5//
ЫО
1,0
0,5
2 3 ¥ х,мм
Рис. 7.13. Схема расположения отверстия и плоскости коррекции на роторе Рис. 7.14. Зависимость координаты центра масс отверстия от его глубины I76
которые выводы. Если наблюдение за ходом технологического про цесса показывает, что в значительной по значению выборке глубины сверлений распределяются по какому-то закону, то это и должно служить основой для выбора значения k. На рис. 7.16, а показан случай распределения глубин в выборке по закону равной вероятно сти (прямоугольный). Здесь целесообразно выбрать такое положение плоскости коррекции, при котором наибольшие значения моментных погрешностей с разными знаками равны
I + Дм | — I — Дм I-
Такое требование выполняется при k æ 0,35 (см. рис. 7.15, г). Для распределения глубин по закону Гаусса (рис. 7.16, б) наимень шая погрешность в виде момента будет получаться при k, обеспечи вающих равенство площадей:
«Si = S2 + S3.
S)
Рис. 7.16. Распределение глубин в выборке:
а — по закону равной вероятности; 6 — по закону Гаусса
Здесь наиболее вероятно получение относительно небольших по грешностей, тогда как возникновение относительно больших мо ментов возможно лишь в незначительном числе переходов техноло гических операций. Возможны и иные подходы к оценке выбираемых значений к.
Уменьшение погрешностей возможно и другими приемами: свер лением дополнительного отверстия, сверлением на скорректирован ную глубину и др.
Способ сверления дополнительного отверстия рассмотрен В. А. За харовым и заключается в том, что расчетное положение плоскости коррекции устанавливается по месту центра масс отверстия наиболь шей глубины. Необходимость сверления более мелких отверстий для устранения малых дисбалансов, как отмечено выше, приведет к воз никновению погрешности. Чтобы этого не получалось, образуют необ ходимый небольшой объем с центром масс в плоскости коррекции дисбалансов, дополнительно снятый объем на пути торца ротора до корректирующего объема (массы) уравновешивают подобным же объемом (массой), но просверленным в роторе под углом в 180°, т. е. на том же расстоянии от оси ротора, на том же диаметре, но по дру гую сторону оси ротора. Если h — полная глубина сверления, кг — глубина отверстия с центром масс в плоскости коррекции, устраняю щего имеющийся дисбаланс ротора, a h2— глубина «излишне» про сверленного отверстия и, одновременно, глубина дополнительного отверстия, то можно написать
ар = kh = Л2 + h j 2.
Отметим, что при этих подсчетах наличие конической части при нимается во внимание, а диаметры отверстий считаются равными.
Способ сверления на скорректированную глубину основан на компенсации некоторого увеличения плеча при сверлении отверстия на неполную глубину соответствующим изменением удаляемой массы. Эта компенсация идет за счет уменьшения глубины сверления.