
книги / Технология машиностроения.-1
.pdf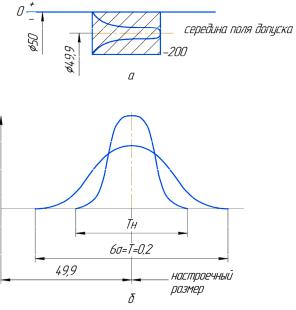
3.4. Методы настройки станков
Статическая настройка заключается в установке режущих инструментов по различным калибрам и эталонам на неподвижном станке (либо деталь-эталон, либо специальный калибр, либо набор мерных плиток).
Инструмент доводится до соприкосновения с поверхностью калибра и закрепляется. Одновременно устанавливаются соответствующие упоры. Могут применяться специальные установочные приспособления с индикаторными устройствами.
Настройка по пробным заготовкам с помощью специального мерительного инструмента. Сущность этого метода (рис. 3.3) настройки станков заключается в том, что установка режущих инструментов и упоров и других устройств производится на определенный
Рис. 3.3. Настройка станка по пробным заготовкам: а – поле допуска размера; б – закон нормального распределения
31
рабочий настроечный размер, а правильность настройки устанавливается обработкой некоторого количества пробных заготовок. Настройка признается правильной, если среднее арифметическое размеров пробных заготовок находится в пределах некоторого допуска на настройку. Задачей расчета настройки в этом случае является определение поля допуска настройки.
Контрольные вопросы по главе
1.Понятие точности механической обработки.
2.Сущность метода пробных ходов и промеров.
3.Достоинства метода пробных ходов и промеров.
4.Недостатки метода пробных ходов и промеров.
5.Сущность метода автоматического получения размеров на настроенных станках.
6.Достоинства метода автоматического получения размеров на настроенных станках.
7.Недостатки метода автоматического получения размеров на настроенных станках.
8.Наладка станка.
9.Поднастройка станка
10.Статическая настройка станка.
32
4. ПРОЕКТИРОВАНИЕ ТЕХНОЛОГИЧЕСКИХ ПРОЦЕССОВ
Проектирование технологических процессов обработки деталей машин имеет целью установить наиболее рациональный и экономичный способ обработки; при этом обработка деталей на металлорежущих станках должна обеспечить выполнение требований, предъявляемых к точности и шероховатости обработанных поверхностей, правильности контуров и форм и т.п.
Проектирование технологических процессов изготовления деталей машин включает решение ряда основных вопросов.
1.Установление вида (типа) производства и организационных форм выполнения технологического процесса.
2.Определение величины партии деталей, запускаемых в производство единовременно (цикл производства) для серийного производства.
3.Выбор вида заготовок и определение их размеров.
4.Установление плана и методов механической обработки поверхностей деталей с указанием шероховатости технологических операций (маршрут обработки).
5.Выбор типов и определение технических характеристик станочного оборудования, приспособлений, режущего и мерительного инструмента, а также определение их количества, потребного для выполнения намеченной обработки.
6.Определение размеров обрабатываемых поверхностей деталей (длины ходов).
7.Определение режимов работы на выбранных станках на каждой операции.
8.Определение норм времени на обработку на каждой операции. Разработка технологического процесса изготовления конкрет-
ной детали производится в соответствии с технологической инструкцией, имеющейся на каждом машиностроительном предприятии. Приведем некоторые ее положения.
33
1.Разработать маршрут и стратегию обработки, включающие
всебя
1.1.Перечень технологических операций и технологических методов получения обработанных поверхностей с заданной точностью, шероховатостью и другими требованиями; в том числе такие операции, как:
•термообработка (закалка);
•покрытия;
•слесарные, моечные, контрольные и т.п.
1.2.Последовательность обработки детали (стратегия) с учетом основного требования: любая технология обработки любой детали начинается с подготовки баз:
•предварительные (черновые) операции для создания технологических баз;
•окончательные (чистовые) операции – условие: сохранение конструкторских баз (по возможности).
2.Разработать операционный технологический процесс изготовления детали; в этот раздел входят:
2.1.Разработка технологических операций, выполняемых на определенном технологическом оборудовании, включающем в себя:
•технологические операционные эскизы обработки детали для каждой технологической операции с указанием установочных, измерительных и зажимных баз; с указанием (по номерам) всех обрабатываемых поверхностей, выполняемых на заданной технологической операции; с простановкой всех размеров (с допусками) всех поверхностей (от измерительных баз), выполняемой на заданной технологической операции;
•оформление технологических карт технологического процесса, где должны быть прописаны технологические переходы, оформляющие порядок и последовательность действий при обработке конкретной детали (конкретных поверхностей).
34
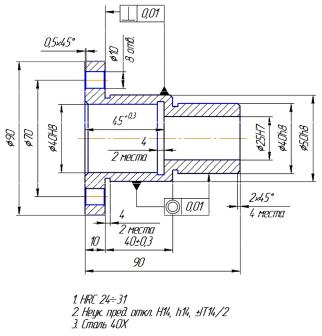
Разработка типового технологического процесса обработки детали «Втулка»
Составление маршрута обработки детали «Втулка» (рис. 4.1). Любая технология обработки любой детали начинается с подготовки баз.
Маршрут:
1)получение заготовки: отрезка;
2)токарная обработка (может быть несколько операций). Предварительная обработка с созданием чистовых баз под термообработку (лезвийная обработка);
3)термообработка (закалка);
4)токарная обработка (может быть несколько). Окончательная обработка – обеспечение размеров по чертежу (лезвийная обработка).
Рис. 4.1. Чертеж детали «Втулка»
35
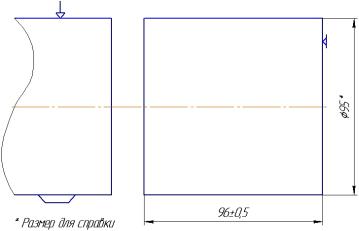
Выбор стратегии обработки:
•сначала с левой стороны по чертежу (предварительно и окончательно);
•затем с правой стороны по чертежу (так заданы размеры) с сохранением конструкторских баз (предварительно и окончательно).
Технологические операции обработки детали «Втулка»
Операция 010: Заготовительная – отрезка (операционный эскиз на рис. 4.2). Для мелкосерийного производства используют прокат:
•калиброванный или некалиброванный;
•холоднотянутый или горячекатаный;
•в состоянии поставки (твердость по Бринеллю НВ180) или термообработанный.
Рис. 4.2. Операция 010: Заготовительная
Все поверхности заготовки являются черновыми (после отрезки и прокатки).
Операция 020: Токарная (предварительная обработка). Операционный эскиз на рис. 4.3. Деталь установлена и зажата в трехку-
36
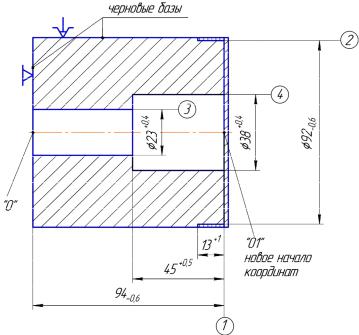
лачковый самоцентрирующийся патрон токарного станка с ЧПУ. Базирование заготовки производится по черновым базам.
Рис. 4.3. Операция 020: Токарная
Технологические переходы:
1.Установить деталь, закрепить, снять.
2.Подрезать (точить) торец (поверхность 1, рис. 4.3) в размер
94–0,6; таким образом создана новая вспомогательная измерительная база для данной операции; создана чистовая база для последующей
операции. При обработке размера 94–0,6 технологическая база совмещена с измерительной.
3.Точить поверхность 2, выдерживая размеры 92–0,6 и 13+1; таким образом, создана чистовая база для последующей обработки.
37
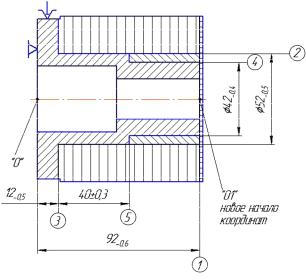
4.Центровать торец (на поверхности 1); создано направление для сверления.
5.Сверлить отверстие 23+0,4 (поверхность 3) на проход; это почти глубокое сверление: соотношение глубины отверстия к диаметру 94/23 > 4, следовательно, сверло необходимо выводить из отверстия как минимум три раза.
6.Расточить отверстие 38+0,4 (поверхность 4), выдерживая размер 48+0,5.
7.Притупить острые кромки – кругом.
Операция 030: Токарная (предварительная обработка). Опера-
ционный эскиз представлен на рис. 4.4.
Рис. 4.4. Операция 030: Токарная
Деталь установлена и зажата в трехкулачковый самоцентрирующийся патрон токарного станка с ЧПУ. Базирование заготовки производится по чистовым базам, обработанным на предыдущей операции.
38

Технологические переходы:
1.Установить деталь, закрепить, снять.
2.Подрезать (точить) торец (поверхность 1) в размер 92–0,6; создана вспомогательная измерительная база для последующей обработки; создана чистовая база (технологическая) для последующей
обработки. При обработке размера 92–0,6 технологическая база совмещена с измерительной.
3.Точить поверхность 2 в размер 52–0,5 с одновременной подрезкой торца (поверхность 3) в размер 12–0,5; обработкой поверхности 3 создана новая вспомогательная измерительная база для после-
дующего перехода. При обработке размера 12–0,5 технологическая база совмещена с измерительной.
4.Точить поверхность 4 в размер 42-0,4 с одновременной подрезкой торца (поверхность 5) в размер 40±0,3. Технологическая база
сизмерительной не совпадают.
5.Притупить острые кромки – кругом.
Операция 040: Термообработка (закалка) – закалить и отпустить до твердости HRC 24-31 (твердость по Роквеллу).
Операция 050: Токарная (окончательная обработка слева по чертежу (см. рис. 4.1)). Операционный эскиз – на рис. 4.5.
Рис. 4.5. Операция 050: Токарная
39
Базы аналогичны базам на операции 020. Установочная база совмещена с измерительной для размера 91–0,5. Новая измерительная база (поверхность 1) создана подрезкой торца и используется для выполнения размера 45+0,3.
Технологические переходы:
1.Установить деталь, закрепить, снять.
2.Подрезать (точить) торец (поверхность 1) в размер 91–0,5; создана измерительная база для последующих переходов и установочная (чистовая база) для последующих операций.
3.Точить поверхность 2 на проход, выдерживая размер 90–0,6.
4.Расточить отверстие (поверхность 3) (черновые, получистовые, чистовые проходы) в размер 40Н8(+0,039), выдерживая размер
45+0,3.
5.Выточить канавку (по чертежу).
6.Точить фаску 2 45°.
7.Расточить отверстие (поверхность 4) (черновые, получистовые, чистовые переходы) в размер 25Н7(+0,021) на проход. Вместо
чистового растачивания можно применить развёртывание (предварительное и окончательное).
8. Притупить острые кромки.
Операция 060: Токарная (окончательная обработка справа по чертежу). Операционный эскиз – на рис. 4.6. Базы – аналогичны базам в операции 030. Возможен альтернативный вариант баз: в оправке на разжим.
Технологические переходы:
1.Установить деталь, закрепить, снять.
2.Подрезать (точить) торец (поверхность 1) в размер 90–0,6; создана измерительная база – в дальнейшем не используется.
3.Точить поверхность 2 в размер 50–0,039 с одновременной подрезкой торца (поверхность 3) в размер 10–0,36; обработкой поверхно-
сти 3 создана измерительная база для последующего перехода.
4. Точить поверхность 4 в размер 40–0,039 с одновременной подрезкой торца (поверхность 5) в размер 40±0,3.
40