
книги / Экспертиза качества и разрушений
..pdf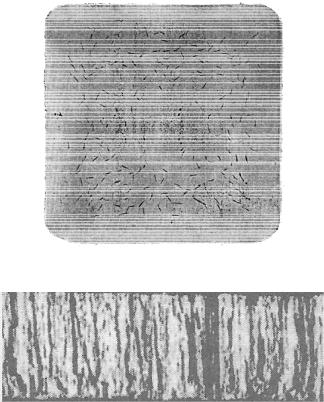
фах при травлении реактивом Обергоффера (100 мл Н2O; 10 мл спирта; 3 мл НCl; 0,2 г CuCl2–2Н2O; 3 г FeCl3; 0,1 г SnCl2) наблюдается полосча-
тость. Наиболее резко шиферность проявляется после закалки и высокого отпуска. Причина образования шиферного излома – загрязненность стали неметаллическими включениями, полосчатость, связанная с дендритной ликвацией. Резко снижается вязкость на поперечных образцах. В большей степени шиферность проявляется в конструкционных, преимущественно легированных сталях, выплавленных в электрических и мартеновских печах. Для предупреждения шиферности следует применять оптимальные условия раскисления и десульфурации в печах.
Рис. 3.29. Флокены на поперечном макрошлифе катанной стали 20Х2Н4А
Рис. 3.30. Шиферный излом
Камневидный излом (рис. 3.31) проходит по границам зерен, наблюдается после высокотемпературного нагрева выше температуры 1250 °С.
Склонность к излому зависит от остаточного содержания раскислителя и присутствия в стали серы, титана и других элементов. Эти элементы при высоких температурах адсорбируются на границах зерен,
91

образуя пленки сульфидов железа и марганца. Это приводит к хрупкости металла при ударном нагружении. Последующая термическая обработка (закалка с отпуском, нормализация) не устраняет камневидный излом. Особенно высокую склонность к камневидному излому имеют стали с высоким содержанием алюминия (38Х2МЮА). Дефект может быть устранен горячей деформацией в условия нормального нагрева. Помогает введение малых добавок титана и редкоземельных металлов.
Рис. 3.31. Камневидный излом
Нафталинистый (нафталиновый) излом (рис. 3.32) представляет собой однородную поверхность разрушения, проходящую по кристаллографическим плоскостям образовавшегося при высоких температурах крупнозернистого аустенита и не имеющую явных признаков макропластической деформации. Вид излома характерен для литых и деформированных сталей.
Рис. 3.32. Нафталинистый излом
92
Крупные плоские участки в изломе имеют характерный оттенок
иселективный блеск, изменяющийся при изменении угла падения света
инапоминающий блеск нафталина. Нафталинистый излом наблюдается
восновном в литых конструкционных сталях. В деформированных сталях встречается реже, причем обнаруживается на промежуточных стадиях передела – после нагрева перед горячей деформацией и быстрого охлаждения.
Рисунок излома в литой стали совпадает с очертаниями зерен при травлении микрошлифа реактивом Кешиена (соляная кислота 500 мл; серная кислота 70 мл; вода 180 мл). В изломе с селективным блеском, как и в микроструктуре, проявляется грануляционная структура литой стали. При больших увеличениях нафталинистый излом имеет структуру скола и реже – квазискола.
Нафталинистый излом обусловлен наследованием текстуры круп-
ных зерен аустенита после γ→α-превращения. Наиболее устойчива текстура крупного зерна аустенита в мартенсите и бейните, менее устойчива – в феррите и еще менее устойчива – в перлите. В нафталинистом изломе разрушение происходит по мелким зернам α-фазы, объединенным в отдельные текстурированные группы в пределах объемов, отвечающих крупному зерну исходной структуры аустенита.
Различают первичный нафталинистый излом, наблюдающийся в литой стали, не прошедшей термической обработки, и вторичный нафталинистый излом, наблюдающийся в литой и деформированной сталях после перегрева.
Вторичный нафталинистый излом отличается от первичного рав-
ноосной формой фасеток, не связанной с характером кристаллизации стали. Нафталинистые изломы обоих видов почти всегда можно получить при испытании стали с камневидным изломом в условиях глубокого переохлаждения. Как правило, они сохраняются после закалки с температуры, незначительно превышающей точку Ас3, однако в этом случае очертания фасеток становятся менее четкими.
Определяющим условием образования вторичного нафталинистого излома является перегрев, температура которого зависит от состава стали и особенностей плавки. При изменении соотношения свойств между границей и телом перегретых зерен аустенита в зависимости от термообработки – длительности пребывания при высоких температурах, скорости охлаждения, режима отпуска – и температуры испытания образуются нафталинистые или камневидные изломы.
93
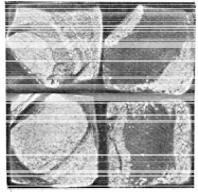
Наиболее часто нафталинистый излом образуется в сталях, содержащих хром, никель, марганец, молибден, ванадий. Кремнистые стали менее склонны к образованию нафталинистого излома даже при очень высоких температурах перегрева.
Наличие в литой термически не обработанной стали первичного нафталинистого излома (как на отдельных участках, так и на всей поверхности) является нормальным явлением. Такой излом встречается в стали любого способа выплавки, и меры к его предупреждению не принимаются. Появление вторичного нафталинистого излома в литой и деформированной сталях связано с перегревом, и его можно предупредить, только исключив перегрев металла.
Для исправления вторичного нафталинистого излома стали подвергают высокотемпературной нормализации или закалке (нагрев на 150– 200 °С выше Ас3) с последующим высоким отпуском. В процессе нагрева происходит рекристаллизация аустенита, обусловленная его внутренним наклепом в связи с объемными изменениями при фазовом превращении. Для устранения нафталинистого излома применяется также промежуточный отжиг.
У сталей, имеющих нафталинистый излом, пластические характеристики и ударная вязкость понижены.
«Черный излом». Некоторые закаленные стали обнаруживают специфическую чешуйчатую поверхность разрушения с частично мраморовидной структурой (рис. 3.33). Вместо обычного светлого кристаллического излома в этом случае наблюдается темный, вплоть до черного. Поверхность разрушения в большинстве случаев совпадает с определенным участком поперечного сечения (где имеются выделения свободного углерода).
Рис. 3.33. «Черный» излом в стали У12
94
При весьма длительном нагреве эвтектоидных и заэвтектоидных сталей несколько ниже А1, а заэвтектоидных сталей также и при нагреве между А1 и Аm и медленном охлаждении происходит растворение карбидов и возможно выделение графита.
3.5.2.Микроструктурный анализ
3.5.2.1.Оптическая микроскопия
Для исследования фаз наиболее актуальным и доступным методом является метод микроструктуры. Основа метода микроструктурного анализа заключается в визуальном наблюдении под микроскопом микроструктуры сплавов, как правило, в отраженном свете.
Микроструктурный анализ проводится с увеличением в 50–2000 раз с помощью металлографических микроскопов. При этом методе можно обнаружить окислы на границах зерен, пережог металла, частицы неметаллических включений, величину зерен металла и другие изменения в его структуре, вызванные термической обработкой.
При микроструктурном анализе обычно решают следующие задачи:
–анализ неметаллических включений;
–изучение распределения фаз и их зеренной структуры.
При решении этих задач начальным этапом является подготовка образцов для исследования.
Отбор образцов. Образцы отбирают из тех участков, которые дают наибольшую информацию о структурной неоднородности металла (в соответствии с нормативными актами). При исследовании деформированных металлов используют продольные шлифы. При анализе разрушения шлиф должен пересекать дефект. Сравнение производят с образцами из бездефектного участка, как правило, с площадью 1–4 см2 и высотой 10–15 мм.
Вырезку образцов желательно проводить тонким абразивным кругом со смазочно-охлаждающей жидкостью.
Монтировка осуществляется заливкой легкоплавкими сплавами или с использованием зажимных приспособлений.
Шлифование проводят на бумажных шлифовальных шкурках. При этом должен быть удален деформированный слой после резки.
Полирование может быть механическим или электролитическим. Механическое полирование производится на круге, покрытом сукном с алмазной пастой или смоченном суспензией окислов алюминия и хрома. Размер абразивных частиц составляет от 50 до 1 мкм. Необходима
95
чистота, помещение должно быть отделено от резки. После окончания полировки не должны быть видны риски. При электролитическом полировании отсутствует деформированный слой, что особенно важно для мягких материалов. Типичные реактивы: хлорная, ортофосфорная, уксусная и другие кислоты, этиловый спирт.
Микроструктура выявляется с помощью химического (пикриновая кислота, слабый раствор азотной кислоты, царская водка) или электролитического травления. Выявляется форма и величина зерен в металле, наличие различных фаз
Микроскопы. Принцип действия микроскопа поясняет рис. 3.34, на котором представлена оптическая схема наиболее типичного микроскопа. Условно микроскоп можно разбить на четыре узла: осветительная система (позиции 1–6 рис. 3.34, препарат 7, с плоскостью препарата сопряжена полевая диафрагма окуляра 10 и полевая осветительная диафрагма 3, апертурная диафрагма 9, с которой сопряжена ирисовая диафрагма 5, окуляр 12. Рассмотрим ход лучей в микроскопе. Объект 7, обозначенный стрелочкой, расположен на предметном столике 7 перед микробъективом 8, на расстоянии несколько большем его фокусного расстояния Fоб. Он строит действительное, увеличенное и перевернутое изображение 7' в плоскости диафрагмы 10. Данное промежуточное изображение расположено за передним фокусом окуляра 12. Поэтому окуляр строит мнимое увеличенное изображение 7'' на расстоянии D = 250 мм от глаза наблюдателя. Такое расстояние считается наилучшим с точки зрения физиологических свойств глаза. Если мы хотим получить действительное изображение объекта на телевизионном приемнике или фотопленке, то достаточно окуляр сдвинуть так, чтобы изображение 7' оказалось перед фокусом окуляра.
Максимальное увеличение достигается применением иммерсии. Для лучшего выявления фаз используют метод фазового контраста, дифференциального интерференционного контраста. Структура обнаруживается без травления.
Автоматический анализ. В отличие от ручного и полуавтоматического анализа, распознавание изображений производится полностью автоматически или при некотором участии оператора. Современные автоматические анализаторы изображений (ААИ) – приборы третьего поколения со сканированием в плоскости изображения, позволяющие как производить анализ изображения непосредственно в процессе его ввода, так и выполнять операции обработки на изображении, хранимом в его памяти (рис. 3.35).
96
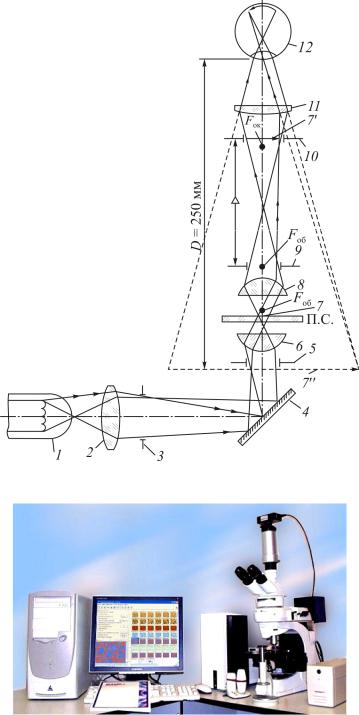
Рис. 3.34. Принципиальная оптическая схема микроскопа
Рис. 3.35. Автоматический анализатор фрагментов микроструктуры твердых тел SIAMS 700
97
К числу серийно выпускаемых ААИ такого типа относятся: Квантиметр (Англия), ИБАС (Германия), Сиамс (Россия). Процессор ААИ производит накопление, классификацию измерений, расчет характеристик, статистическую обработку. Результаты выдаются на дисплее и бумаге в цифровом и графическом виде.
Рассмотрим некоторые моменты анализа контроля качества структуры металла с использованием металлографических микроскопов.
Неметаллические включения в стали являются инородными телами, нарушающими однородность ее структуры, поэтому их влияние на механические и другие свойства может быть значительным. При деформации в процессе прокатки, ковки, штамповки неметаллические включения, особенно неправильной формы с острыми краями и углами, играют роль концентраторов напряжения и могут вызвать образование трещины, являющейся очагом последующего усталостного разрушения стали.
Контроль неметаллических включений производится в соответствии с ГОСТ 1778−70.
Для регламентации неметаллических включений существует стандартная пятибалльная шкала, представляющая собой набор характерных структур, наблюдаемых под микроскопом на нетравленых шлифах при 100-кратном увеличении.
Определение количества неметаллических включений в стали производится на продольных шлифах, изготовляемых на образцах, равных кругу или 1/4 круга для заготовок толщиной более 50 мм и 1/2 круга для заготовок толщиной меньше 50 мм. Длина образца в направлении волокна обычно составляет 10–12 мм.
Оценка производится сравнением наихудшего места на шлифе с эталонной шкалой баллов, которые составлены для различных видов включений: силикатов, оксидов, сульфидов и др. Плавка стали характеризуется либо наибольшим баллом из нескольких образцов, либо среднеарифметическим из нескольких образцов, каждый из которых оценен наибольшим баллом.
Для ряда марок стали, например шарикоподшипниковой, чистота по неметаллическим включениям в сталях является одним из основных факторов, определяющих эксплуатационную стойкость изделий; в этом случае действуют специальные, более жесткие нормы.
Меры борьбы с неметаллическими включениями в стали определяются созданием условий, уменьшающих возможность их попадания в металл. Так, хорошее раскисление, полное расплавление добавок
98
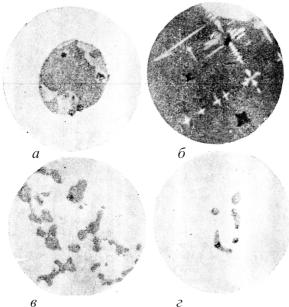
идостаточная выдержка металла в печи уменьшают количество неметаллических включений 1-й группы, тщательная подготовка печи, ковша и изложницы и хорошее качество огнеупоров уменьшают количество включений 2-й группы. Особенно эффективным является вакуумирование жидкого металла перед разливкой.
Некоторые характерные неметаллические включения представлены на рис. 3.36. Неметаллические включения возникают в результате целого ряда физико-химических явлений, протекающих в расплавленном
изатвердевающем металле в процессе его производства.
Рис. 3.36. Характерные неметаллические включения, обнаруженные в 18-тонных слитках малоуглеродистой стали: а – сталь 08кп, оксисульфидное включение с преобладанием оксидной фазы (темная фаза – закись железа, светлая фаза – твердый раствор MnSxFeSxFeO), внутри включения видны зерна железной шпинели; б – сталь 08кп, силикатное включение (темная фаза – железомарганиовистый силикат, светлая – твердый раствор FeOxMnO); в – сталь 08пс, скопление включений железной шпинели FeOxAl2O3; г – сталь 08Ю,
сульфидные включения твердого раствора MnSxFeSxAl2S3
Все неметаллические включения, образующиеся в результате тех или иных реакций, имеющих место в процессе производства металла, обычно называют природными. К ним относятся оксиды, сульфиды, нитриды и фосфиды.
99
Кроме природных включений в металле присутствуют также частицы шлака, огнеупоров, материалов литейной формы, т.е. те вещества, с которыми металл непосредственно соприкасается в ходе производства. Подобного рода неметаллические включения называют посторонними, или случайными.
Основную массу включений в металле восстановительной плавки составляют включения, образующиеся в результате снижения растворимости примесей при охлаждении и затвердении металла. Кроме природных включений, в металле восстановительной плавки присутствуют также посторонние включения.
Современный уровень технологии производства стали позволяет в значительной мере удалить из металла природные и посторонние включения. Однако общее содержание их в различных сталях колеблется в широких пределах и значительно влияет на свойства металла.
Неметаллические включения разделяют по химическому и минералогическому составу, стойкости и происхождению. По своему химическому составу неметаллические включения делятся на следующие группы:
– оксиды (простые – FeO, MnO, Cr2O3, SiO2, Al2O3, TiO2 и др.; сложные – FeO · Fe2O3, FeO · Al2O3, FeO · Cr2O3, MgO · Al2O3, 2FeO · SiO2 и др.);
–сульфиды (простые – FeS, MnS, Al2S3, CaS, MgS, Zr2S3 и др.; сложные – FeS · FeO, MnS · MnO и др.);
–нитриды (простые – ZrN, TiN, AlN, CeN и др.; сложные – Nb(C, N), V(С, N) и др.), встречающиеся в легированных сталях, имеющих
всвоем составе сильные нитридообразующие элементы: титан, алюминий, ванадий, церий и др.;
–фосфиды (Fe3P, Fe2P и др.)
Наибольшее количество включений в металлах составляют оксиды и сульфиды, так как содержание фосфора низкое. Нитриды обычно присутствуют в специальных сталях, имеющих в своем составе элементы с высоким сродством к азоту.
По минералогическому составу кислородные включения делятся на следующие основные группы:
–свободные оксиды – FeO, MnO, Cr2O3, SiO2 (кварц), Al2O3 (ко-
рунд) и др.;
–шпинели – сложные оксиды, образованные двух- и трехвалент-
ными металлами. К этой группе принадлежат ферриты, хромиты и алюминаты;
100