
7904
.pdf31
объема цементного теста, прочность (марка) цемента. Студенты изучают эти свойства на 2 курсе в рамках дисциплины «Строительные материалы» и некоторых других специальных дисциплин.
В данном курсе отметим только марки портландцемента.
Марка цемента определяется пределом прочности при сжатии и изгибе образцов размером 40x40x160 мм, изготовленных и выдержанных в стандартных условиях. По прочности различают следующие марки портландцемента: 300, 400, 500, 550, 600. Цифра обозначает предел прочности при сжатии, кгс/см2 (или, соответственно, 30; 40; 50; 55; 60 МПа).
После затворения происходит схватывание цементного теста, затем его твердение. При этом прочность образующегося цементного камня нарастает довольно быстро в течение первых 7 суток, затем от 7 до 28 суток рост прочности замедляется, а далее при положительной температуре и во влажной среде, рост прочности продолжается в течение нескольких лет.
На основе портландцементного клинкера промышленностью освоено производство более 30 видов цементов.
Портландцемент применяют при изготовлении кладочных и штукатурных растворов, а также в производстве бетонов.
Пример обозначения портландцемента ПЦ400Д20 – портландцемент арки 400, количество минеральных добавок 20%.
3.4. Строительные растворы
Строительный раствор – это рационально подобранная смесь вяжущего вещества, воды, мелкого заполнителя и добавок, которая после затвердевания становится камнем.
Строительные растворы предназначаются для скрепления камней и кирпичей в процессе кладки, для заполнения швов при монтаже зданий из крупноразмерных бетонных и железобетонных элементов, для оштукатуривания поверхностей и для придания им специальных свойств (водонепроницаемости, кислотостойкости и др.).
По плотности строительные растворы подразделяются на тяжелые с массой в сухом состоянии свыше 1500 кг/м3 и легкие - менее 1500 кг/м3. По виду вяжущего: на простые - с одним вяжущим, и смешанные (сложные), состоящие из нескольких вяжущих (цементно-известковые, цементноглиняные, известково-гипсовые). Кроме того, растворы подразделяются на воздушные (изготовленные на основе воздушных вяжущих), предназначенные для работы в сухих условиях, и гидравлические (на основе гидравлических вяжущих) - для работы во влажных условиях.
По прочности на сжатие кгс/см2 растворы подразделяются на марки: 4, 10, 25, 50, 75, 100, 150, 200, 300. Марка раствора определяется испытанием на сжатие образцов-кубов со стороной 7,07x7,07x7,07 см или половинок балочек

32
(после испытания балочек на изгиб) размером 4x4x16 см в возрасте 28 суток после твердения при температуре 20±5° С.
Вкачестве вяжущих для приготовления растворов используют все виды цементов, известь, гипсовые вяжущие и др.
Вкачестве мелкого заполнителя при приготовлении растворов применяют природные и искусственные пески, так называемые высевки. Растворы на искусственных песках (продукт дробления пород – гранитов, мраморов, известняков, шлаков и т. п.) чаще всего используются при штукатурных работах
Для выполнения тех или иных строительных работ необходимы растворные смеси разной густоты (подвижности). Подвижность смеси характеризуется глубиной погружения в растворную смесь эталонного конуса (рис. 1). Например, при кирпичной кладке применяются растворы с глубиной погружения конуса 9-13 см; для растворов, используемых при монтаже панельных и крупноблочных зданий, глубина погружения 5-7 см.
Расчет состава раствора производится по таблицам и аналитическим путем. Более подробно этот вопрос изучается в курсе «Строительные материалы».
Рис. 1. Прибор для определения подвижности растворной смеси:
1 – прибор для определения глубины погружения; 2 – фиксатор; 3 – конус; 4 – сосуд с раствором;
3.5. Бетоны и железобетон
Бетоном называют искусственный камень, полученный в результате затвердевания рационально подобранной смеси вяжущего, воды, мелкого и крупного заполнителя, а также различных химических добавок.
Бетон – прочный и огнестойкий материал – известен очень давно. В Древнем Риме, например, из бетона на извести был построен ряд сложных инженерных сооружений. Но широкое применение бетона началось после
33
появления портландцемента. Современное строительство немыслимо без бетона: бетон стал основным строительным материалом.
3.5.1. Классификация бетонов
Бетоны классифицируются по следующим признакам: основному назначению, виду вяжущего, виду заполнителей, структуре.
По назначению различают бетоны конструкционные и специальные. Конструкционные - используются для изготовления несущих и огра-
ждающих конструкций зданий и сооружений. К ним предъявляются требования главным образом по механическим свойствам, а также, при необходимости, по морозостойкости, водонепроницаемости, истираемости и др.
Специальные - жаростойкие, химически стойкие, декоративные, ра- диационно-защитные, теплоизоляционные и др. - применяются при возведении специальных конструкций или их элементов.
Главным критерием качества бетона является его прочность при сжатии, которая определяется прочностью контрольных образцов размером
15x15x15 см.
В качестве показателей прочности используют марку и класс бетона. Марка бетона - это нормируемое значение его качества, принимаемое
как среднее значение результатов испытания образцов.
Строительными нормами и правилами для тяжелых бетонов установлены следующие марки: М50; М75; М100; М150; М200; М250; М300; М350; М400; М450; М500; М600 и выше (через М100), единица измерения - кгс/см2.
Класс бетона - это нормируемое значение показателя прочности, принимаемое с гарантированной обеспеченностью (0,95), Это значит, что установленное классом свойство обеспечивается не менее чем в 95 случаях из
100.
Бетоны подразделяются на классы: В1; В1,5; В2; В2,5; В3,5; В5; В7,5;
В10; В12,5; В20; В25; В30; В40; В45; В50; В55; В60, единица измерения -
МПа.
В зависимости от средней плотности бетоны подразделяются на:
-особо тяжелые (ρ ³ 2500 кг/м3), в качестве заполнителей в них используют железные руды, чугунную дробь, обрезки стали;
-тяжелые (обыкновенные) (ρ = 2200-2500 кг/м3), заполнителями в них служат плотные горные породы (гранит, известняк);
-облегченные (ρ = 1800-2200 кг/м3);
-легкие (ρ = 500-1800 кг/м3);
-особо легкие (ρ £ 500 кг/м3).
3.5.2.Тяжелые бетоны на плотных заполнителях
Виды бетонов подробно рассматриваются в дисциплине «Строительные материалы» и некоторых специальных дисциплинах, изучаемых на старших курсах. В данной работе дается только общее представление о бето-
34
не, в частности, о тяжелом бетоне на плотных заполнителях, в котором в качестве вяжущего используется портландцемент.
Исходные материалы. Как указано выше, в качестве вяжущего в таких бетонах чаще всего применяется цемент.
К воде, используемой для затворения бетонной смеси, предъявляются определенные требования. Она не должна содержать вредных примесей, препятствующих его твердению. Нельзя применять болотную воду и воду, загрязненную различными примесями (кислотами, солями, маслами и т. д.), а также любую «неизвестную» воду, то есть такую, которая имеет непривычный цвет и запах. Пригодность воды устанавливается химическим анализом, а также сравнительным испытанием бетонных образцов на прочность. Без предварительной проверки можно применять питьевую воду.
Вкачестве мелкого заполнителя, состоящего из зерен размером от 0,16 до 5 мм, чаще всего в тяжелых бетонах используют кварцевый песок. Зерновой состав песка, то есть соотношение зерен различной крупности, имеет очень большое значение, от него зависит плотность бетона и расход вяжущего.
Примеси пыли, глины, ила, обволакивая зерна песка, ухудшают их сцепление с цементом. Кроме того, эти примеси увеличивают суммарную поверхность заполнителя, повышают водопотребность, что приводит к увеличению расхода цемента, уменьшению прочности и долговечности бетона, понижают его морозостойкость.
Согласно нормативным документам, содержание этих примесей не должно превышать 3 %. В песке ограничивается также содержание органических примесей.
Вкачестве крупного заполнителя в тяжелых бетонах используют щебень и гравий.
Щебень - это продукт дробления горных пород. Крупность зерен щебня от 5 до 70 мм. Зерна щебня имеют рваную, развитую поверхность, что улучшает прочность сцепления растворной части бетона (цемент + вода + мелкий заполнитель) с ними.
Гравий - это природные зерна таких же размеров, что и у щебня. Гравий имеет окатанную, гладкую поверхность и сцепление его с растворной частью бетона меньше.
Крупный заполнитель должен соответствовать определенным стандартным требованиям.
Прочность крупного заполнителя определяется испытанием на сжатие образцов правильной формы в виде цилиндра или куба, выпиленных из исходной горной породы. При невозможности испытать таким образом (например, для определения прочности гравия), пригодность заполнителя определяют по показателю дробимости.
Для получения наиболее экономичного плотного бетона необходимо иметь зерна крупного заполнителя разных размеров и в определенном соотношении. Зерновой состав заполнителей определяют по результатам просеивания пробы через стандартный набор сит с отверстиями, мм: 70; 40; 20; 10;

35
5. Содержание илистых, глинистых, пылевидных и органических примесей в крупном заполнителе, как и в песке, не должно превышать 3%.
Как указывалось выше, при приготовлении бетонной смеси, для придания ей или затвердевшему бетону специфических качеств, вводятся различные химические добавки. Например, применение пластифицирующих добавок позволяет уменьшить количество воды затворения и тем самым получить экономию цемента. В настоящее время нашли применение различные химические вещества для пластификации бетонных смесей: гидрофилизирующие, гидрофобизирующие, микропенообразующие, комплексные добавки, а также суперпластификаторы, весьма значительно повышающие подвижность бетонных смесей.
Свойства бетонной смеси. Бетонная смесь должна обладать такими свойствами, которые обеспечивали бы хорошую укладку в опалубку или форму и уплотнение без расслоения и излишнего водоотделения.
Оценка удобоукладываемости бетонной смеси производится с помощью стандартного конуса (рис. 2) и прибора для определения ее жесткости (рис. 3). Для уплотнения бетонной смеси с целью придания ей максимальной плотности (а, следовательно, и прочности) применяют различные виброустройства (поверхностные и глубинные вибраторы, виброплощадки и т. п.). Следует помнить, что недоуплотнение приводит к резкому снижению качества бетона и в первую очередь прочности.
Рис. 2. Определение подвижности бетонной смеси:
П1 - мало-подвижная; П2 - подвижная; ПЗ – сильно подвижная; П4 - литая
Нарастание прочности бетона возможно лишь при определенных теп- ло-влажностных условиях. Наиболее простым методом при положительной температуре является создание влажной среды регулярной поливкой бетона водой, укрытием влажным песком, опилками, эмульсиями, и т.д. Чем выше температура при обеспечении влажности, тем быстрее твердеет бетон.

36
Рис. 3. Определение жесткости бетонной смеси
В заводских условиях широко используют различные приемы ускорения твердения - тепловлажностную обработку при температуре 80-95° С, в результате которой через 10-16 часов бетон имеет прочность 70 % марочной и более.
3.5.3. Железобетон
Прочность бетона при растяжении примерно в 10-20 раз ниже, чем при сжатии, большинство же несущих конструкций в процессе работы испытывают напряжение сжатия и растяжения. Это наглядно можно представить при рассмотрении схемы работы изгибающего элемента (рис. 4). Для восприятия растягивающих усилий в бетон вводят стальную арматуру. Сочетание бетона и арматуры и представляет собой новый строительный материал - железобетон.
Создание железобетона стало возможным благодаря следующим факторам:
1)коэффициенты линейного расширения стали и бетона примерно одинаковы;
2)бетон (цементный камень) надежно защищает арматуру от кор-
розии;
3)бетон прочно сцепляется со стальной арматурой, составляя, таким образом, единый монолит.
Создание железобетона стало революционным переворотом в строительстве.
Железобетон применяется в строительстве в виде сборных и монолитных конструкций. Сборные конструкции изготавливаются на заводах железобетонных конструкций в многократно используемых металлических формах, затем доставляются на строительную площадку, где из них возводят здания и сооружения.
Конструкции из монолитного бетона изготовляются непосредственно на месте, где в качестве форм используются различного вида опалубки. Начиная с 50-х годов, в нашей стране высокими темпами развивалась промышленность сборного железобетона, объем же применения монолитного желе-
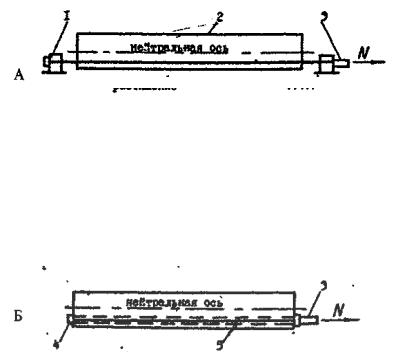
37
зобетона неуклонно снижался (за исключением гидротехнического строительства).
В настоящее время производство монолитного железобетона обретает как бы «второе дыхание», и объем его применения расширяется.
Со временем было замечено, что в растянутой зоне железобетонных конструкций с обычным армированием появляются трещины из-за прогибов изгибаемых элементов, что приводит к коррозии стальной арматуры, уменьшению ее живого сечения, увеличению прогиба и раскрытию трещин (рис. 4). В конечном итоге это снижало долговечность железобетонных конструкций. В результате возникла идея предварительного натяжения арматуры, которое состоит в том, что путем искусственного обжатия бетона за счет предварительного натяжения арматуры появление нежелательных растягивающих напряжений в бетоне исключается. Таким образом, в этих конструкциях свойства бетона и арматуры используются наиболее полно. Смысл предварительного натяжения арматуры и работы предварительно напряженной железобетонной конструкции можно представить из рис. 5
Рис. 4. Схема работы железобетонного элемента на изгиб
Рис. 5. Схема предварительного напряжения железобетонных конструкций:
а– предварительное напряжение в твердеющем бетоне; б – последующее напряжение в затвердевших готовых изделиях; 1 - упор; 2 - форма; 3 - натяжное устройство; 4 -анкерное устройство; 5 - стенка канала
3.6.Основные стеновые материалы
Наиболее распространенными стеновыми материалами в настоящее время являются силикатный и керамический (глиняный) кирпич и камни.
Вообще, кирпич как строительный материал изготавливается с древних времен, но если история применения силикатного кирпича насчитывает не-
38
многим более 100 лет, то керамический кирпич насчитывает уже несколько тысячелетий.
3.6.1.Производство силикатного кирпича
Внашей стране силикатный кирпич выпускается двух размеров, мм: 250x120x65 - одинарный или условный кирпич;
250x120x88 - утолщенный или модульный кирпич.
Всоответствии с ГОСТ 379-95 масса кирпича в высушенном состоянии не должна превышать 4,3 кг. По этой причине утолщенный кирпич должен изготовляться с несквозными пустотами.
По прочности при сжатии, с учетом прочности при изгибе, силикатный кирпич подразделяется на марки: 300, 250, 200, 150, 125, 100, 75. Цифра обозначает предел прочности при сжатии, кгс/см2 (или 30; 25; 20; 15; 12,5; 10; 7,5 МПа).
Поскольку силикатный кирпич применяется для кладки ограждающих конструкций, он должен сохранять свою прочность при воздействии знакопеременных температур (замораживание и оттаивание), что характерно для большинства районов России.
По морозостойкости (см. раздел 3.2) силикатный кирпич подразделяется на марки: 50, 35, 25, 15. Сырьем для получения силикатного кирпича и камней служат воздушная известь, обыкновенный кварцевый песок и вода; вместо кварцевого песка или для частичной его замены могут быть использованы отходы и попутные продукты промышленности (золы, шлаки и т. п.), в составе которых имеется SiO2..
Состав сырьевой смеси по массе примерно следующий:
-известь - 5 ÷ 9 %;
-мол. песок - 5 ÷ 9%
-песок - 90 ÷ 81 %;
-вода - 13 %.
Часть песка, равная массе извести, размалывается до тонкодисперсного состояния; чаще всего он размалывается совместно с известью.
Процесс изготовления силикатного кирпича состоит из следующих основных технологических операций:
дробление извести, совместный помол извести с частью песка (приготовление известково-кремнеземистого вяжущего), тщательное перемешивание молотых извести и песка с немолотым песком и водой, гашение полученной сырьевой смеси в силосах в течение 1-4 часов, повторное перемешивание и последующее прессование под давлением 20-30 МПа.
Полученный сырец с помощью автоматов-укладчиков размещается на запарочных вагонетках и направляется в специальные аппараты, называемые автоклавами, на автоклавную обработку.
39
Автоклавы представляют собой металлические сосуды диаметром 2 м
идлиной 17, 19, 21, и 40 м. В них подается водяной пар под давлением 0,8- 1,6 МПа, который при этих параметрах имеет температуру 174,5 – 197,0° С.
Процесс автоклавной обработки при указанном давлении пара продолжается 6-8 часов (общий цикл автоклавирования составляет 10-14 часов).
Цементирующим веществом в силикатном кирпиче являются гидросиликаты кальция (CSН), которые связывают в единый монолит все компоненты формовочной смеси.
Это явление образования прочных и долговечных гидросиликатов кальция впервые открыл в конце XIX века австрийский профессор Михаэлис,
ис тех пор силикатная промышленность во всех странах бурно развивалась. В России в настоящее время более 15 % зданий строятся из силикатного кирпича.
Силикатный кирпич - несгораемый материал, но его нельзя применять при сооружении печей, дымоходов, дымовых труб, для кладки цокольных зданий ниже гидроизоляционного слоя, для кладки водопроводных и канализационных колодцев, для кладки стен зданий с мокрым режимом работы (бани, прачечные, душевые и т. д.).
Кроме одинарного кирпича промышленностью строительных материалов освоено производство пустотелого силикатного камня с размерами
250x120x138 мм.
Газобетонные изделия.
В качестве стеновых материалов используются газобетонные мелкоразмерные блоки размерами 390x190x190 мм, которые изготавливают из газобетонной смеси, процесс получения которой заключается в следующем.
При совместном помоле извести, кварцевого песка и воды образуется сметанообразная масса - шлам, в который добавляется небольшое количество газообразователя; чаще всего для этих целей используется алюминиевая пудра. В процессе реакции между алюминием и гидроксидом кальция выделяется водород, который вспучивает шлам, образуя газобетонную массу. Формы с газобетонной смесью направляются на автоклавную обработку с теми же параметрами, что и при производстве силикатного кирпича. В результате образуется пористый камень, средняя плотность которого может колебаться в широких пределах от 300 до 1200 кг/м3.
Применяя смешанные вяжущие (что в настоящее время чаще всего и делается), состоящие из извести и цемента, можно получить так называемую распалубочную прочность (как правило, значение ее невысокое), и в этом состоянии массив разрезается на блоки нужных размеров, а затем уже направляется в автоклав для окончательного твердения.
Пенобетонные изделия.
Если жидкий шлам перемешать с заранее приготовленной устойчивой пеной и далее обработать паром высокого давления в автоклаве или пропарить при атмосферном давлении, то получится пенобетон – материал, аналогичный по свойствам газобетону.
40
Ячеистые стеновые материалы являются исключительно эффективными, и в настоящее время в России они находят все более широкое применение.
3.6.2. Производство керамического (глиняного) кирпича
Основным компонентом для производства керамического кирпича и камней являются легкоплавкие глины; как уже. указывалось выше, к ним относятся глины со степенью огнеупорности ниже 1350° С.
В соответствии с ГОСТ 530-95 керамический кирпич и камни изготовляются следующих размеров, мм:
250x120x65 - одинарный или условный кирпич; 250x120x88 - утолщенный или модульный кирпич; 250x120x138 - керамический камень.
Модульный кирпич и керамические камни выпускаются пустотными. К этим материалам предъявляются требования по прочности, средней плотности, теплопроводности, морозостойкости и некоторым другим показателям.
По пределу прочности при сжатии с учетом прочности при изгибе (кгс/см2) кирпич подразделяется на следующие марки: 300, 250, 200, 175, 150,
125, 100, 75.
По морозостойкости кирпич имеет 4 марки: 50, 35, 25, 15. Керамические стеновые материалы подразделяются на рядовые и лице-
вые, последние используют для кирпичной кладки наружных, фасадных поверхностей без последующей их декоративной отделки.
Кроме глины при производстве кирпича применяют отощающие, выгорающие, пластифицирующие и некоторые другие добавки.
Формование кирпича осуществляют способом пластического формования и способом полусухого прессования.
При пластическом способе формования глина вначале дробится, затем подается в глиносмеситель, в котором перемешивается с добавками и водой. Влажность формовочной массы при этом способе формования находится в пределах 20-25 %. Формование осуществляется на ленточных прессах с последующей разрезкой бруса не отдельные кирпичи. Полученный сырец подвергается сушке до влажности около 5 %, после чего высушенный сырец укладывается на вагонетки и обжигается в специальных печах при температуре 950 ÷ 1050° С. Обжиг – завершающий и самый ответственный этап в производстве керамических изделий. Процесс охлаждения также весьма ответственен, так как в случае резкой смены температуры могут образоваться трещины.
При полусухом способе формования глина вначале дробится в вальцах и подсушивается в сушильных барабанах до влажности 5 ÷ 8 %. Высушенная глина измельчается в дезинтеграторах и подается в смеситель, где увлажняется до 10 ÷ 12 %. Формование сырца производится на специальных прессах с усилием прессования 30 ÷ 50 МПа. Обжиг сырца при этом способе формования производится при более высокой температуре 1000-1100° С.