
10783
.pdf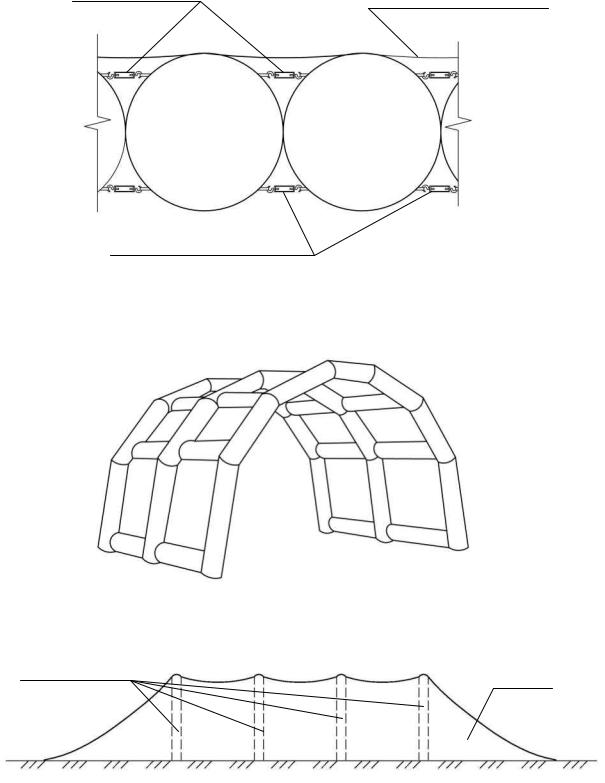
Наружные узлы крепле- |
Наружная оболочка |
|
ния |
||
|
Внутренние узлы крепления
Рис. 25 Схема соединения блоков пневмокаркасных конструкций с помощью винтовых карабинов
Рис. 26 Схема соединения блоков пневмокаркасных конструкций с помощью продольных надувных блоков
Несущие арки |
Тент |
|
Рис. 27 Схема объединения несущих элементов пневмокаркасной конструкции с помощью тента
40
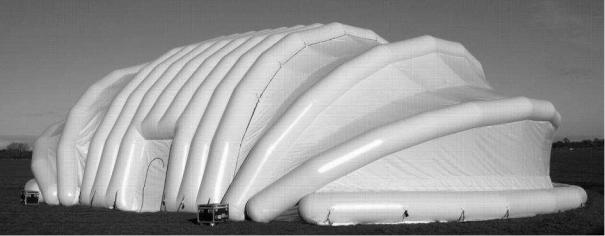
Рис. 28 Пневмокаркасное здание с комбинированной схемой соединения несущих элементов
Время наполнения пневмокаркасной системы воздухом в зависимости от типа нагнетателя и вида модуля составляет 5-15 мин. Полное время монтажа, от выгрузки из машины до готового сооружения занимает от 30 минут до 3 часов, в зависимости от размера конструкции и ее сложности.
Данный тип конструкций не требует постоянного поддува. Достаточно включить компрессор 1-2 раза в 2-3 дня на 10-20 минут. Каждая арка каркаса отделена от магистрального воздуховода обратным клапаном, что делает ее автономной, а все сооружение становится менее чувствительным к повреждениям, т.к. при повреждении одной арки, соседние продолжают работать в штатном режиме [17]. Пневмокаркасное сооружение не требует обязательного наличия шлюза и может комплектоваться самыми различными входными системами: обычные двери, ворота различных типов, докшелтеры, надувные двери с электролебедкой, утепленные шторы, что позволяет варьировать цену изделия, и упростить монтаж и транспортировку изделия.
Для установки пневмокаркасных конструкций не требуется особой специальной подготовки площадки, так как само сооружение практически не дает нагрузки на почву. Подобное здание может быть размещено между другими стационарными зданиями, на площадке неправильной формы,
41
вплотную к существующим инженерным коммуникациям (трубопроводы, ж/д пути и т.д.) или даже объединять объекты, расположенные в разных уровнях. Отсутствие фундамента и глубоких креплений в грунт позволяет избежать опасности повреждения расположенных рядом сооружений или коммуникаций. Для устойчивости конструкции на грунте производители рекомендуют использовать дополнительные балластные «карманы». Это специальные мешки, расположенные по нижнему краю сооружения, прикрепляемые отдельно или нашитые заранее в определенных местах. «Карманы» наполняются грунтом, песком или другими сыпучими материалами и являются дополнительным балластом. Их количество и размер зависит от размеров сооружения. В качестве балласта могут также использоваться водоналивные баллоны. При необходимости может быть произведена дополнительная стабилизация с помощью тросов и канатов. Так же, для фиксации сооружения можно использовать анкерный тип крепления, но в силу специфики применения данных конструкций, он используется намного реже [18].
При установке модулей в неблагоприятных условиях на грунт, снег, грязь должны быть предусмотрены покрытия из водонепроницаемой ткани, или утепленные полы, служащие для теплоизоляции.
Отдельной группой пневматических конструкций принято считать пневмолинзы (рис 29). Они представляют собой две оболочки, соединенные друг с другом по контуру, и по принципу своей статической работы ничем не отличаются от обычных воздухоопорных сооружений. Функциональное отличие лишь в том, что пространство между оболочками с избыточным давлением воздуха не эксплуатируется. Формы линзовых покрытий весьма разнообразны как по профилю, так и по плану, который может быть круглым, эллиптическим, многоугольным и т.п. [9]. Пневмолинзы являются ограждающими элементами сооружения.
42

Рис. 29 Ботанический сад EdenProject, Англия, г. Сент-Остелл, 2001г.
Еще одним вариантом наружных пневматических ограждений являются вакуумные конструкции, представляющие собой две оболочки, закрепленные на каркасе произвольной формы (в том числе, и на пневмокаркасе), из пространства между которыми частично откачан воздух.
2.2.По материалу для изготовления оболочки
∙Пленочные;
∙Тканевые.
Требования, предъявляемые к материалам для изготовления оболо-
чек пневматических конструкций, можно свести к двум: прочность и воздухонепроницаемость. Этим принципиальным требованиям соответствуют современные композиционные материалы, состоящие из прочной негниющей основы (ткани или сетки) и воздухонепроницаемого слоя (полимерного покрытия либо дублирующей пленки). В итоге предлагается два вида
43
материалов – ткани, покрытые или пропитанные полимерами и двойные пленки с расположенным между ними армирующим слоем в виде сетки из синтетического волокна. Не считая первых двух требований, названных принципиальными, так как с ними связана возможность реализации принципа пневматической конструкции вообще, существует ряд дополнительных:
∙пониженная горючесть,
∙светопроницаемость,
∙влагонепроницаемость,
∙эластичность,
∙легкость в сочетании с высокой прочностью на разрыв,
∙долговечность при эксплуатации в различных климатических усло-
виях.
Пленки, как правило, дешевле тканей, но они более деформируемы, менее прочны и недолговечны в эксплуатации. На данный момент использование пленок в качестве оболочки практически прекращено, так как их применение является экономически невыгодным.
Тканевые материалы состоят из основы и пропитки (покрытия). Для современных сооружений основу изготавливают из синтетических (полиамиды, полиэфиры, полиакрилы) волокон. Оболочки первых сооружений изготавливались из натуральных (лен, хлопок) тканей, через некоторое время они были заменены на искусственные (вискоза, стекловолокно, целлюлоза) материалы. Именно благодаря применению синтетических материалов срок эксплуатации пневматических конструкций увеличился с двух лет (как это было у первых сооружений), до 20-30лет. В настоящее время тенденция развития материалов склоняется не столько в сторону прочности, сколько в сторону долговечности [20].
Используются, как правило, полотняное (одна нить) или рогожное (две или три нити) переплетения. Пропитку изготавливают, применяя эла-
44
стичные смеси на основе синтетических и каучуковых смол: из поливинилхлорида, полихлоропрена, хлорсульфополиэтилена, а также этиленпропилена и полиуретана. В зависимости от требований к материалу ее наносят с одной или двух сторон, что придает тканям воздухонепроницаемость, устойчивость к атмосферным явлениям, повышает срок службы. Покрытие наносится в заводских условиях толщиной 0,5÷1 мм. Покрывающие полимеры могут быть светопроницаемы или окрашенные в любой цвет. Пропитки имеют свои недостатки - они подвержены старению, то есть со временем теряют эластичность, появляются трещины, изменяется цвет, а у светопроницаемых элементов снижается прозрачность [10].
Ткани являются анизотропным материалом, поэтому при расчете тканевых оболочек важно учитывать различие в механических характеристиках - по основе (вдоль куска ткани) и по утку (поперек нитям).
Наиболее распространенный на сегодняшний день вариант оболочки - это полиэфирная ткань с ПВХ покрытием. Основа ПВХ ткани состоит из нитей полиэстера и лавсана. Она закладывает такие характеристики как прочность ткани и способность к натяжению. Для полиэфиров характерна меньшая степень вытягивания, чем для нейлоновых оболочек, применявшихся в конце XX века, это позволило сделать конструкцию более прочной и гарантировать большую устойчивость при сильных ветрах. Сверху ткань покрывается поливинилхлоридом, а так же защитными лаками, для придания ей характеристик, необходимых для определенного местоприменения или конкретного вида предприятия – морозостойкость; устойчивость
культрафиолетовому излучению; стойкость к загрязнению; устойчивостью
кгниению. Покрытие бывает как однотак и двухстороннее.
Высокое качество полиэфирных тканей с ПВХ покрытием обеспечивает длительный срок службы изделий (свыше 20 лет).
Основные характеристики материала (полиэфирная ткань с ПВХ покрытием) [21]:
45
∙Вес наружной оболочки: 720 - 1300 г/м2;
∙Вес внутренней оболочки: 520 - 680 г/м2;
∙Растяжение по вертикали и горизонтали: 28 кг;
∙Морозоустойчивость: не теряет свойств при -50 … +70°C;
∙Соответствие требованиям пожарной безопасности:
горючесть: группа Г1,
воспламеняемость: группа В2,
распространение пламени: группа РП2,
что соответствует классу пожарной опасности строительных материалов КМ3 и дает возможность применять в зальных помещениях предприятий общественного питания и спортивных комплексах одновременной вместимостью не более 50 человек.
2.3. По форме оболочки
∙Сферическая;
∙Коническая:
−На круглом плане;
−На квадратном (прямоугольном) плане.
∙Цилиндрическая;
−На квадратном (прямоугольном) плане;
−Со сферическими торцами.
∙Комбинированная.
|
|
Таблица 3 |
Форма оболочек пневматических конструкций (примеры) |
||
|
|
|
Сферическая |
Коническая |
Коническая |
|
46 |
|
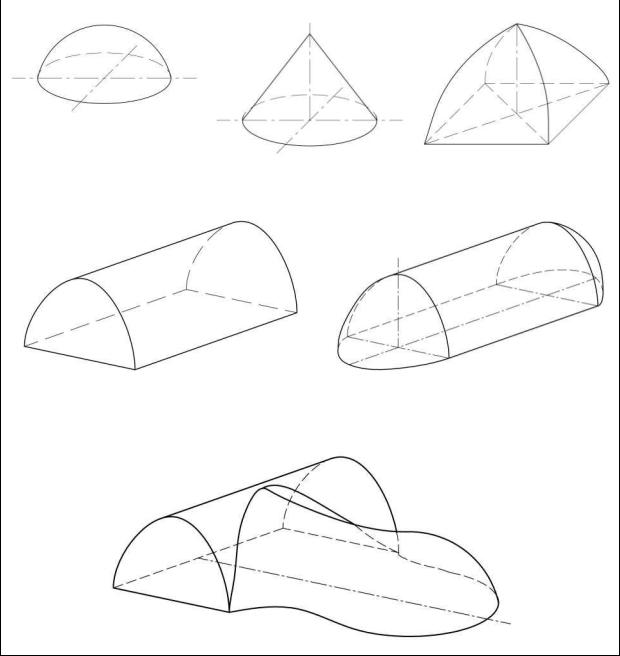
|
на круглом плане |
|
на квадратном плане |
|
|
|
|
|
|
Цилиндрическая |
|
Цилиндрическая |
||
на прямоугольном плане |
со сферическими торцами |
|||
|
|
|
|
|
Комбинированная
Наиболее простыми формами воздухоопорных конструкций являются цилиндрические и сферические поверхности. Но возможны конструкции более сложных гиперболических и параболических форм, либо композиции из нескольких поверхностей (см. табл. 3). Формы воздухоопорных конструкций зависят от размера конструкции и прочности материала [24].
В отношении раскроя и изготовления полуцилиндрические оболочки имеют преимущества, так как склеивают их из прямых полотнищ материа-
47
ла почти без отходов. Наиболее рациональной по раскрою является цилиндрическая на прямоугольном плане. Отходы ткани в этом случае при раскрое составляют всего 5% (на квадратном плане – 7%) [12].
Оболочки в форме полусферы обеспечивают наиболее полное использование перекрываемого пространства, а также данная форма является наиболее оптимальной с точки зрения распределения давления в оболочке. Однако по сравнению с другими оболочками отходы материала составляют до 57%. Следует иметь в виду, что стоимость материала достигает 75% общей стоимости пневматического сооружения [41].
2.4.По количеству слоев материала оболочки
∙Однослойные;
∙Многослойные.
Однослойная оболочка применяется исключительно для воздухо-
опорных конструкций. Такой материал подойдет для небольшого температурного диапазона, т.к. малая толщина материала служит причиной интенсивного охлаждения, образования конденсата и наледи на внутренней поверхности оболочки зимой, а также перегрева воздуха в помещении летом. Поэтому создание и поддержание нужного перепада температур требует больших затрат и применения специальной техники для обогрева и охлаждения воздуха под оболочкой.
Чаще всего однослойные оболочки применяют для неотапливаемых помещений, они служат лишь для защиты от атмосферных воздействий.
Многослойные воздухоопорные конструкции бывают двух или трехслойные. Самый распространенный и востребованный на сегодняшний
48
день вариант – двухслойное покрытие. Благодаря расстоянию в 50-70 сантиметров между слоями, значительно снижаются затраты на отопление конструкции, предотвращается скапливание конденсата на внутреннем своде сооружения, обеспечиваются хорошие теплоизоляционные свойства, улучшается звукоизоляция в здании [21]. Наружный воздух, нагнетаемый в купол, распределяется на два потока. Первый поток поддерживает давление внутри купола, которое незначительно выше атмосферного, второй поток направляется в пространство между слоями. Выполненный из трех слоев купол, позволяет избавиться от так называемых «мостиков холода». Это места соединения первого и второго слоев, где отсутствует воздушная подушка. Будучи закрытыми третьим слоем ткани, они перестают быть проблемным местом конструкции, обеспечивая воздухоопорной конструкции наиболее оптимальную по сравнению с другими аналогами теплоизоляцию. Такие воздухоопорные сооружения требуют наименьших затрат на обогрев.
В качестве дополнительной (внутренней) оболочки применяется техническая ткань, которая обладает характеристиками, во многом схожими с материалами для основной оболочки, но она легче и более устойчивая к возгоранию. Но не стоит забывать о том, что вес и транспортный объем двухслойной оболочки по сравнению с однослойной увеличивается примерно в полтора раза, трехслойной в 2 раза. Стоимость двухслойной возрастает на 25-30%, трехслойной на 50% [12].
Оболочки для пневмокаркасных сооружений всегда многослойны. В зависимости от комбинаций расположения баллонов и защитных слоев используются следующие варианты (рис. 30):
49