
11012
.pdf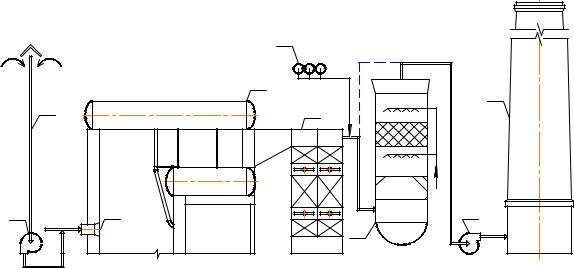
Комплексные схемы (№4, №5) глубокой очистки продуктов сгорания от оксидов азота и серы
Комплексные схемы глубокой очистки продуктов сгорания от оксидов азота и серы можно разделить на окислительно-абсорбционные и хемосорбционные [8,16,19].
Комплексная схема №4 глубокой очистки продуктов сгорания от оксидов азота и серы с использованием озонирования и физической сорбции
Комплексная окислительно-сорбционня схема №4 (рис. 2.4) включает блок окисления (блок 5) и блок физической абсорбции (блок 6).
|
|
9 |
|
|
1 |
|
7 |
2 |
|
|
|
8 |
Подача |
6 |
|
топлива |
3 |
|
|
5
Вода
4
Рис. 2.4. Комплексная схема глубокой очистки продуктов сгорания от оксидов азота и серы:1 – котёл; 2 – экономайзер; 3 – абсорбер; 4 – дымосос; 5 – дымовая труба; 6 – горелка; 7 – воздухозаборная шахта; 8 – вентилятор дутьевой; 9 – озонатор
При физической абсорбции обычно используют в качестве абсорбента воду, а также органические растворители, не реагирующие с извлекаемыми компонентами и их водными растворами. Вода – наиболее дешевый и доступный абсорбент для очистки больших объемом газа.
Однако оксид азота NO и диоксид серы SО3 cлабо растворимы в воде. Следовательно, перед поступлением в адсорбер их необходимо окислить до высших оксидов
(SО3, N2O5), хорошо растворимых в воде.
Вкачестве окислителей можно использовать озон, перекись водорода, СlО2 и др.
Впредлагаемой комплексной схеме использован наиболее эффективный и доступный окислитель – озон. Эффективность озона обуславливается высокой скоростью реакций:
NO + O3 ↔ NO2 + O2 |
(0.1) |
3NO + O3 ↔ 3NO2 |
(0.2) |
Эти реакции осуществляются за доли секунды (0,1-0,9 сек), что позволяет применять этот окислитель в энергетических установках.
Блок окисления (блок 5) состоит из озонаторов, системы транспортировки окис-
11
лителя и устройства для равномерного распределения окислителя в продуктах сгорания. Блок 6 представлен абсорбером, в котором распыливается вода. Высшие оксиды азота и серы (SО3, N2O5), хорошо растворимые в воде, улавливаются орошающей жидко-
стью и превращаются в капли серной и азотной кислот.
По достижении определенных концентраций раствор этих кислот нейтрализуется
аммиаком и в результате получаются сульфат аммония и аммиачная селитра, которые широко используются в качестве удобрения. Достигаемая степень очистки продуктов сгора-
ния от NО - 90%, от SО2 - 80%.
При физической абсорбции обычно используют в качестве абсорбента воду, а также органические растворители, не реагирующие с извлекаемыми компонентами и их водными растворами. Вода – наиболее дешевый и доступный абсорбент для очистки больших объемом газа.
Однако оксид азота NO и диоксид серы SО3 cлабо растворимы в воде. Следовательно, перед поступлением в адсорбер их необходимо окислить до высших оксидов
(SО3, N2O5), хорошо растворимых в воде.
Вкачестве окислителей можно использовать озон, перекись водорода, СlО2 и др.
Впредлагаемой комплексной схеме использован наиболее эффективный и доступный окислитель – озон. Эффективность озона обуславливается высокой скоростью реакций:
NO + O3 ↔ NO2 + O2 |
(0.3) |
3NO + O3 ↔ 3NO2 |
(0.4) |
Эти реакции осуществляются за доли секунды (0,1-0,9 сек), что позволяет применять этот окислитель в энергетических установках.
Блок окисления (блок 5) состоит из озонаторов, системы транспортировки окислителя и устройства для равномерного распределения окислителя в продуктах сгорания.
Блок 6 представлен абсорбером, в котором распыливается вода. Высшие оксиды азота и серы (SО3, N2O5), хорошо растворимые в воде, улавливаются орошающей жидкостью и превращаются в капли серной и азотной кислот.
По достижении определенных концентраций раствор этих кислот нейтрализуется
аммиаком и в результате получаются сульфат аммония и аммиачная селитра, которые широко используются в качестве удобрения. Достигаемая степень очистки продуктов сгора-
ния от NО - 90%, от SО2 - 80%.
Комплексная схема №5 глубокой очистки продуктов сгорания от оксидов азота и серы с использованием озонирования и хемосорбции
Данная комплексная схема (см. рис. 2.5) состоит из блока приготовления абсорбента (блок 7) и скруббера (блок 6). В качестве абсорбента используются как правило растворы щелочей, а также можно применять любые из представленных ранее в методах очистки от серы.
При химической абсорбции молекулы абсорбента вступают в химическую реакцию с молекулами удаляемых веществ, образуя новое химическое соединение. В данной схеме ( см. рис. 2.5) в качестве абсорбента использовано известковое молоко.
12
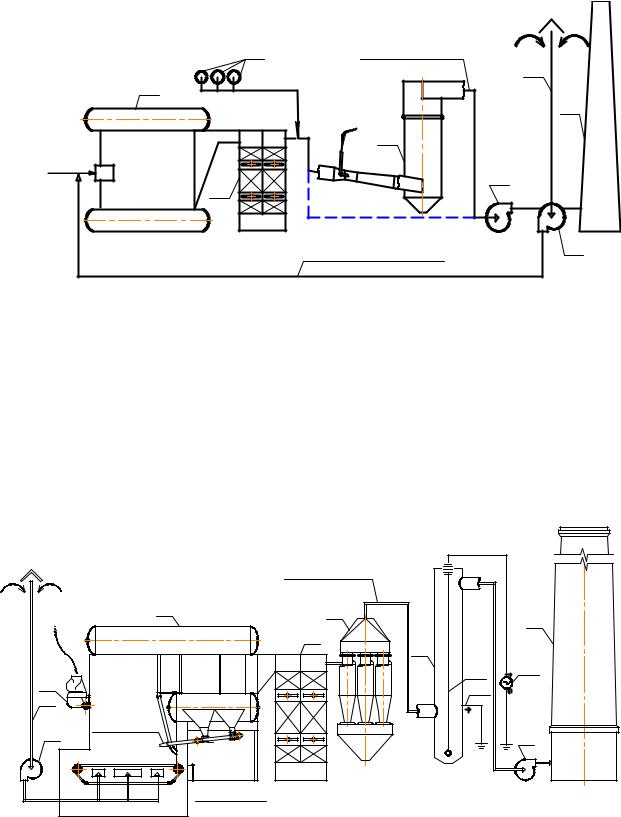
8 |
Ввод |
|
Газоход продуктов |
|
|
|
сгорания |
6 |
|
|
озона |
|||
1 |
|
|
||
|
|
Подача |
|
|
|
|
|
5 |
|
|
|
|
известкового |
|
|
|
|
молока |
|
|
|
|
3 |
|
Подача |
|
|
|
|
топлива |
|
|
|
4 |
2 |
|
|
|
|
|
|
|
|
|
|
|
Подача воздуха на горение |
7 |
|
|
|
|
Рис. 2. 5. Комплексная схема очистки продуктов сгорания от оксидов азота и серы: 1 – котёл; 2 – водяной экономайзер; 3 – скруббер с трубой Вентури; 4 – дымосос; 5 – дымовая труба; 6 – воздухозаборная шахта; 7 – дутьевой вентилятор; 8 – озонаторы
Комплексные схемы очистки выбросов топливосжигающего оборудования от твердых токсичных веществ
В данных схемах возможно сочетание двух аппаратов разной степени сухой очистки (блок циклонов, электрофильтр) или аппарата сухой очистки (блок циклонов) и аппарата мокрой очистки – скруббера.
В качестве примера приведена комплексная схема сухой очистки продуктов сгорания котлоагрегата на основе котла ДКВр.
|
|
Газоход |
|
|
|
продуктов сгорания |
|
|
1 |
4 |
|
Топливо |
|
7 |
|
|
|
||
|
|
3 |
|
|
|
5 |
|
|
|
12 |
10 |
|
|
|
|
2 |
|
11 |
|
|
|
|
|
8 |
|
|
|
9 |
Возврат уноса |
|
|
|
|
6 |
|
|
|
|
Подача воздуха на горение
Рис. 2.6. Комплексная схема сухой очистки продуктов сгорания от твёрдых частиц:1 – котел типа ДКВР; 2 – пневмомеханический забрасыватель твердого топлива; 3 – экономайзер; 4 – блок циклонов; 5 – электрофильтр; 6 – дымосос; 7 – дымовая труба; 8 – воздухозаборная шахта; 9 – вентилятор дутьевой; 10 – источник постоянного тока 11 – осадительный электрод; 12 – коронирующий электрод
13
Тема: Методы очистки сбросов от вредных веществ
Рассматриваются технологические методы очистки сбросов на примере котельной установки. Эти методы включают снижение расхода сточных вод и как следствие, массы выбрасываемых солей в водный бассейн. К технологическим методам относятся: повышение степени возврата конденсата (очистка конденсата), возвращающегося от технологических потребителей, и снижение расхода продувочных вод.
Повышение степени возврата конденсата (очистка конденсата)
Основной составляющей питательной воды паровых котлов является конденсат, возвращаемый потребителями пара.
Потребителями пара отопительно-производственных котельных являются:
–подогреватели: сетевые, горячего водоснабжения, исходной или химически очищенной воды и т. п;
–подогреватели мазута;
–технологические потребители предприятий, для которых сооружается котельная. Загрязнение возвращаемых конденсатов возможно:
–солями кальция, магния и натрия, мазутом за счет неплотностей подогревателей;
–продуктами коррозии паро-конденсатного тракта (особенно из-за углекислоты, об-
разующейся в котле при разложении NаНСОз и Na2CO3);
– в процессе производства примесями, зависящими от характера технологических процессов.
Если конденсат в процессе производства загрязнен примесями в количествах, удаление которых требует больших затрат, чем подготовка соответствующего количества добавочной воды, то использование такого конденсата экономически не целесообразно. В каждом конкретном случае вопрос очистки конденсата должен решаться в соответствии со степенью его загрязнения и требованиями, установленными для данных паровых котлов.
В котельных применяются следующие методы очистки конденсата: обезмасливание, очистка от мазута, обезжелезивание и умягчение [32,33].
Обезмасливание конденсатов
Конденсат, загрязненный смазочными маслами и нефтепродуктами, может содержать этих примесей более 150 мг/л. При содержании масел более 10 мг/л обычно образуется неустойчивая эмульсия, поэтому первоначальная стадия очистки конденсата может осуществляться путем отстоя. Отстой конденсата осуществляется в специальных баках-отстойниках, рассчитанных на 1,5-2 ч пребывания в них конденсата (рис. 2.7).
Принципиальная схема очистки конденсата от масла дана на рис. 2.8. Загрязненный конденсат поступает в бак-отстойник 1. В первом отсеке бака, от-
деленном вертикальной перегородкой, идущей от крышки бака, капли масла укрупняются и всплывают на поверхность; при помощи пробоотборного устройства 10 устанавливают уровень скопившегося в этом отсеке масла и периодически его удаляют.
Из первого отсека бака частично отстоявшийся конденсат поступает во второй отсек, откуда насосом 2 подается на механические фильтры 3.
14
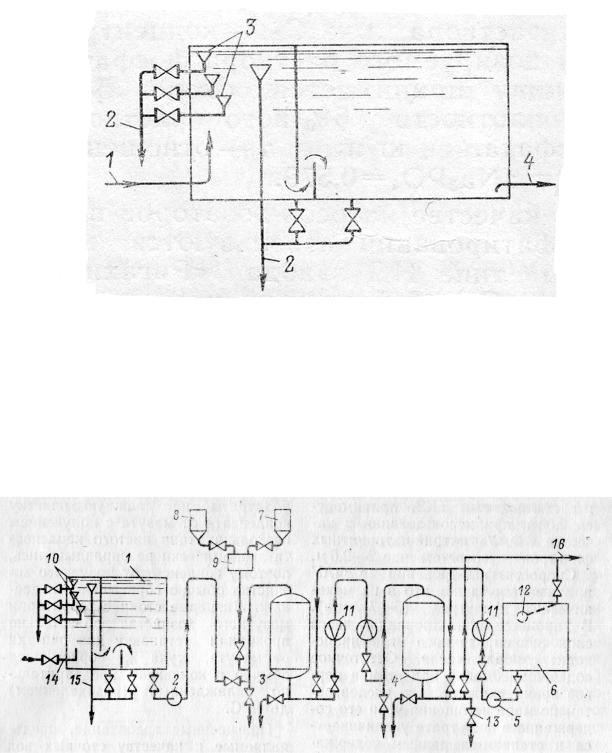
Рис. 2.7 - Бак-отстойник конденсата: 1 - подвод загрязненного конденсата; 2 – сброс в дренаж; 3 - пробоотборное устройство; 4-отвод отстоявшегося конденсата к насосу.
Небольшая вертикальная перегородка, идущая от дна бака, задерживает в первом отсеке бака-отстойника механические примеси, вносимые конденсатом.
Механические фильтры загружаются нефтяным или каменноугольным коксом, дробленым антрацитом, термоантрацитом (возможно отработанным активированным углем); размер зерен фильтрующего материала 1-3 мм.
.
Рис. 2.8. Принципиальная схема очистки конденсата от масла (нефтепродуктов):1- бакотстойник конденсата; 2- насос загрязненного (отстоявшегося) конденсата; 3-механический фильтр; 4-фильтр активированного угля (ФАУ); 5-насос для промывки фильтров; 6-бак для промывки фильтров; 7-мерник раствора коагулянта; 8-мерник раствора щелочи; 9-бак для получения хлопьев гидроокиси алюминия; 10-пробоотборное устройство; 11-расходомер показывающий; 12-автоматический запорный клапан; 13-отбор пробы очищенного конденсата; 14-подвод загрязненного конденсата на очистку; 15сброс в дренаж; 16-очищенный конденсат в деаэратор.
15
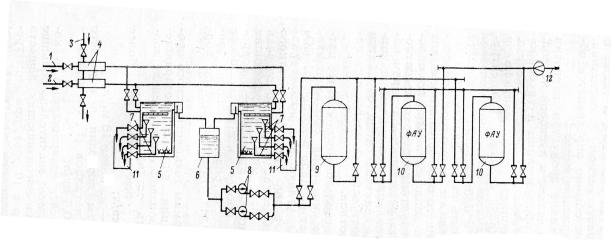
Фильтрование замасленного конденсата через механические фильтры производится со скоростью 5-7 м/ч. Отключение фильтров на промывку производится при достижении сопротивления фильтра примерно до 10 м вод. ст.
Содержание масла после механических фильтров составляет примерно 4-6 мг/л. Для улучшения процесса обезмасливания конденсата применяют периодическую
(примерно 1 раз в сутки) подачу на механические фильтры хлопьев гидроокиси алюминия, которые на поверхности фильтра образуют пленку, хорошо адсорбирующую масло; остаточное содержание масла после механических фильтров составляет примерно 1-2 мг/л.
Очистка конденсата, возвращаемого от мазутного хозяйства
Пар в мазутном хозяйстве котельных используется в подогревателях мазута, резервуарах хранения мазута, лотках и нулевых емкостях. Общий расход пара в мазутном хозяйстве котельных составляет обычно от 1 до 20 т/ч.
Затраты на сложную очистку конденсата от мазута с получением нескольких тонн чистого конденсата экономически не оправдывались, поэтому конденсат от мазутного хозяйства обычно сбрасывался в дренаж. Ливневые стоки с территории мазутного хозяйства обязательно проходили установку для очистки от мазута, туда же сбрасывался обычно и конденсат, предварительно охлажденный (разбавлением) до 40° С.
На Конаковской ТЭЦ впервые была осуществлена установка по очистке конденсата, возвращаемого от мазутного хозяйства без сброса стоков. Схема очистки конденсата, возвращаемого от мазутного хозяйства без сброса стоков, приведена на рис. 2.9.
Рис. 2.9 – Принципиальная схема очистки конденсата, возвращаемого от мазутного хозяйства котельной: 1 – конденсат от подогревателей мазута; 2 – конденсат от лотков, нулевых емкостей и резервуара хранения мазута; 3 – исходная охлаждающая вода; 4 – охладитель конденсата; 5 – приемный бак-отстойник; 6 – расходный бак очищаемого конденсата; 7 – пробоотборное устройство; 8 – насос перекачки конденсата; 9 – механический фильтр; 10 – фильтр активированного угля (ФАУ); 11 – ведро для удаления отстоявшегося мазута; 12 – очищенный конденсат в деаэратор или на умягчение.
Возвращаемый от мазутного хозяйства конденсат 1 и 2 охлаждается в теплообменниках 4 до температуры 95° С и поступает в баки-отстойники 5. Отстоявшийся конденсат с содержанием мазута около 10 мг/л перфорированным коллектором со дна бака 5
16
отводится в расходный бак 6, откуда насосами 8 подается на очистку. Очистка конденсата осуществляется на трех фильтрах (без резервных), работающих последовательно без сброса стоков. Отработанные фильтрующие материалы выгружаются из фильтров вручную и сжигаются.
В качестве первоначальной стадии обработки (после отстоя), задерживающей основную массу проскочившего мазута, устанавливается механический фильтр 9, загруженный коксом или термоантрацитом - более дешевыми, чем активированный уголь. Когда фильтр загрязняется мазутом и сопротивление его возрастает более допустимых пределов (Р > 10 м вод. ст.), верхний слой или весь фильтрующий материал (устанавливается при эксплуатации) выгружается вручную и отправляется на сжигание. Во время перегрузки фильтра 9 установка работает по обводной линии, при этом контроль ведется более тщательно, чтобы мазут не попал на фильтры активированного угля (ФАУ) 10, которые работают по скользящему графику: фильтр, загруженный свежим активированным углем, работает вначале в качестве второй ступени ФАУ. Когда периодический контроль сигнализирует о приближении содержания мазута в фильтре к допускаемой для установленных котлов норме, фильтр переключается на работу в качестве первой ступени ФАУ, а ФАУ, работавший в качестве первой ступени, загружается свежим активированным углем и вновь становится фильтром второй ступени ФАУ.
Описанная схема работы установки обеспечивает защиту ФАУ от проскоков мазута и дает значительную экономию в расходе дефицитного и дорогостоящего активированного угля, обеспечивая надежное удаление мазута из конденсата при отсутствии сбросных вод.
Очистка конденсата от продуктов коррозии и умягчение
Химический состав продуктов коррозии, содержащихся в конденсате, исследован пока еще недостаточно, однако известно, что основными продуктами коррозии являются окислы железа — магнетит Fe3O4 и гематит α Fe2O3 и гидроокиси - Fe(OH)3 и Fe(OH)2.
Продукты коррозии железа могут находиться в конденсате в виде механических примесей (размер частиц более 0,1 мкм) в коллоидно-дисперсном состоянии (размер частиц от 1 до 100 мкм), а также в истинно растворенном состоянии. Анализом обычно определяется общее содержание железа.
Содержание продуктов коррозии особенно велико в пусковой период, когда с оборудования и трубопроводов смываются окислы железа, образовавшиеся при монтаже и предпусковой стоянке. Концентрация продуктов коррозии в возвращаемом с производства конденсате может быть самая различная в зависимости от характера пароиспользующего оборудования и схемы возврата конденсата. При нормальной эксплуатации пароконденсатного тракта решающим фактором образования окислов железа в конденсате является схема обработки воды, поступающей на питание паровых котлов.
При использовании схемы натрий-катионирования образовавшаяся за счет распада в котле NaHCO3 и Ма2СО3 углекислота вызывает затем коррозию пароконденсатного тракта. Следует в первую очередь принять все меры, устраняющие возможность протекания коррозионных процессов, и только после этого рассматривать вопрос очистки конденсата от продуктов коррозии.
17
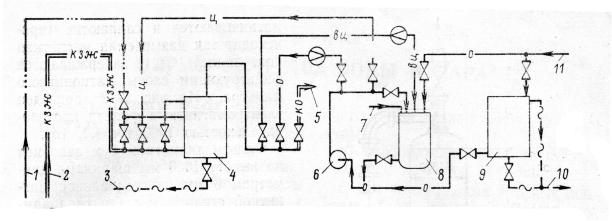
По нормам технологического проектирования возвращаемый с производства конденсат должен иметь состав:
общая жесткость — не более 50 мкг-экв/л; масла — не более 10 мг/л;
продукты коррозии в пересчете на ионы металлов (F, Сu и др.) - не более 0,5 мг/л; Конденсат, возвращаемый в котельные, имеет значительно большие количества загрязняющих веществ (примерно в 10 раз), при этом требуется осуществление таких схем обработки, которые бы обеспечил» требования, предъявляемые установленным
оборудованием.
Для очистки конденсата от оксидов железа используется следующая аппаратура:
1.Целлюлозные фильтры намывного типа (так называемые набивные фильтры требуют значительных затрат труда и времени на перегрузку целлюлозы и поэтому применяются редко).
2.Механические (одно-, двух- и трехкамерные) или водород-катионитные фильтры
сиспользованием в них сульфоугля (при температуре конденсата до 90° С) или катионита КУ-2 (при температуре конденсата до 120° С).
3.Электромагнитные аппараты и намывные ионитные фильтры.
Схема обезжелезивания конденсата на целлюлозных фильтрах намывного типа приведена на рис. 2.10.
Рис. 2.10. Схема обезжелезивания конденсата в целлюлозных фильтрах намывного типа: 1 - сжатый воздух; 2 – конденсат, содержащий железо; 3 -сброс целлюлозы в золоотвал; 4 - целлюлозный намывной фильтр; 5 - обезжелезенный конденсат; 6 - насос для намыва целлюлозы; 7 - загрузка целлюлозы; 8 - гидроразбиватель целлюлозы; 9 - бак осветленной воды; 10 —^ дренаж; 11 - осветленная вода.
При обезжелезивании конденсата сульфоуглем или катионитом КУ-2 высота фильтрующего слоя принимается 0,8 м (при использовании двух - и трехкамерных фильтров - 0,8 м в каждой камере). В фильтрах обезжелезивания предусматривается периодическая промывка фильтрующего слоя раствором кислоты для отмывки от оксидов железа. При установке для обезжелезивания механических фильтров периодическая гидровыгрузка фильтрующего материала производится в специально установленный для этого водород-катионитный фильтр с подводом к нему для регенерации раствора кислоты и сжатого воздуха.
18

Схема обезжелезивания в водород-катионитном фильтре, загруженном катионитом (сульфоуголь или КУ-2), приведена на рис. 2.11.
Рис. 2.11. Схема обезжелезивания конденсата на водород-катионитных фильтрах, загруженных сульфоуглем:1-серная кислота; 2-мерник серной кислоты; 3-насос-дозатор кислоты типа НД; 4 – воздушный колпак; 5-конденсат от насосов; 6 - обезжелезенный конденсат; 7 – дренаж; 8- водород-катионитный фильтр второй ступени; 9-зажелезенный конденсат; 10 - сжатый воздух.
Снижение расхода продувочных сточных вод
Ступенчатое испарение [11,33] позволяет получать пар требуемого качества при сниженном количестве продувочной воды, для чего в верхнем барабане 2 котла устанавливают перегородки 4 с отверстиями, которые разделяют водяной объем барабана на ряд уменьшающихся отсеков — ступеней (рис. 2.12а), а паровое пространство остается общим. Обычно барабан разделяют на три отсека — два торцевых меньших размеров и один средний большего размера. Поверхность нагрева котла, подсоединенная к каждому из отсеков, должна иметь самостоятельный циркуляционный контур.
Вся питательная вода подается в первый - средний отсек, над которым размещен штуцер с вентилем для отвода пара из барабана. Через отверстия в перегородках проходит вся продувочная вода, которая в концевых отсеках (циркуляционных контурах) должна превратиться в пар. При этом по направлению к концевым отсекам концентрация солей в котловой воде увеличивается, а количество получаемого пара уменьшается. Основное количество пара получается в среднем чистом отсеке, в котором за счет большой продувки (равной расходу котловой воды в крайних отсеках) образуется пар с более низким: солесодержанием.
На рис. 2.12б показана схема испарения с выносными циклонами 7, в которые поступает котловая вода с повышенной концентрацией солей, откуда они удаляются продувкой. Сухой остаток котловой воды в чистом отсеке должен быть не выше 1500 мг/л.
19
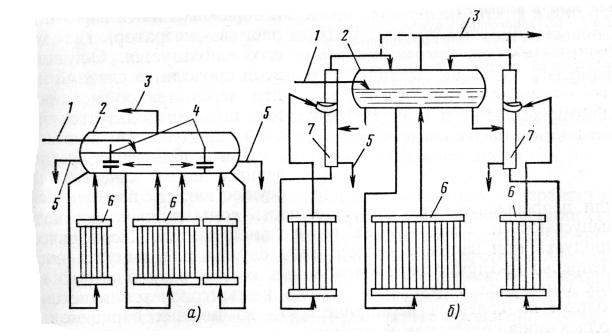
Рис. 2.12. Схемы ступенчатого испарения: а - размещение второй ступени испарения с двух торцов барабана, б - двухступенчатое испарение с выносными циклонами; 1 - питательная магистраль, 2 - барабан котла, 3 - паропровод для отбора пара, 4 - перегородки, 5 - труба для продувки, 6 - экраны, 7 - выносные циклоны
20