
Конструкции из дерева и пластмасс. Волик А.Р. 2005
.pdf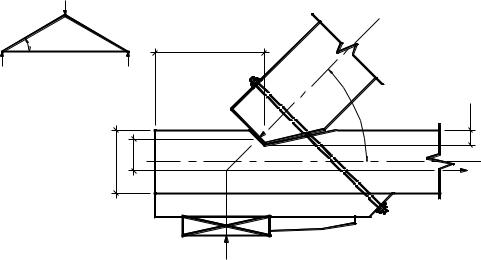
Лабораторная работа 1 ИСПЫТАНИЕ ЛОБОВОЙ ВРУБКИ
Цель работы:
•определить расчетную несущую способность соединения и сравнить ее с разрушающей нагрузкой;
•определить деформации смятия врубки и построить график зависимости деформаций от нагрузки.
1.1.Общие сведения
Врубкой называют соединение (рис. 1.1), в котором усилие элемента, работающего на сжатие, передается другому элементу непосредственно без вкладышей или других рабочих связей. За этим видом соединения сохранилось старое название «врубка», хотя в настоящее время врезка и гнезда выполняются не топором, а электро-, мотопилой и т.д.
Лобовая врубка может утратить несущую способность при достижении одного из трех предельных состояний:
•смятие площадки упора;
•скалывание площадки;
•разрыв ослабленного врубкой нижнего пояса.
Qi,d |
|
|
α = 30° |
lV |
|
V |
V |
|
|
α |
h1 |
|
R |
|
|
e |
|
|
h |
|
|
|
N |
|
V |
|
|
Рис. 1.1. Конструкция лобовой врубки |
|
Расчетная несущая способность соединения на смятие определя-
ется по формуле
Rсm.d = f cm.α.d Acm , |
(1.1) |
91

где A – рабочая площадь cмятия, определяемая по формуле |
A |
= |
b h1 |
, |
|||
|
|||||||
cm |
|
|
|
cm |
|
cos α |
|
где b – ширина сминаемого участка; h1 – глубина врубки; |
|
|
|||||
|
|
|
|
||||
f cm.α.d – расчетное сопротивление смятию древесины под углом к |
|||||||
волокнам, определяемое по формуле |
|
|
|
|
|
|
|
f cm.α.d = |
f |
cm.0.d |
; |
|
(1.2) |
f cm.0.d sin2 α + cos2 α
f cm.90.d
f cm.0.d , f cm.90.d – расчетные сопротивления смятию вдоль волокон и поперек, определенные в соответствии с [6, п. 2.1.2];
Расчетная несущая способность соединения на скалывание опре-
деляется по формуле
Rv.d = f v.mod.d Av , |
(1.3) |
где f v.mod d – расчетное среднее по площадке скалывания сопротивление древесины скалыванию вдоль волокон, определяемое по формуле
f v.mod.d = |
f v.0.d |
, |
(1.4) |
||
|
|||||
1+β |
lv |
|
|
|
|
e |
|
||||
|
|
|
где f v.0.d – расчетное сопротивление древесины скалыванию вдоль воло-
кон, определяемое по приложению 2; β– коэффициент, равный 0,25 (при обеспечении обжатия площадки скалывания β = 0,125 ); e – плечо сил скалывания, принимаемое 0,5h; h – полная высота поперечного сечения скалываемого элемента; lv – расчетная длина плоскости скалывания, принимаемая не более 10 глубин врезки в элемент;
Aν – расчетная площадь скалывания, определяемая по формуле Aν = b lν , где b – ширина скалываемого участка.
Расчетная несущая способность соединения на растяжение в ос-
лабленном сечении определяется по формуле
Rt.0.d = f t.0.d k0 Ainf , |
(1.5) |
92
где f t.0.d – расчетное сопротивление древесины растяжению вдоль воло-
кон, определяемое по приложению 2; kо= 0,8 – коэффициент, учитывающий концентрацию напряжений в деревянных элементах при наличии ослаблений в соответствии с [6, п. 2.1.2.9]; Ainf – площадь поперечного сечения элемента нетто, т.е. с учетом ослаблений.
1.2. Методика проведения испытаний Приборы и оборудование: машина испытательная МС-100, приспо-
собления для испытаний, штангенциркуль, индикаторы часового типа, электровлагомер.
Геометрическая схема образца, его размеры показаны на рис. 1.1. Подготовленную к испытаниям конструкцию устанавливают в прес-
совую установку. Путем обмера определяют необходимые для расчета фактические геометрические размеры элементов лобовой врубки (табл. 1.1) перед ее испытанием.
Таблица 1.1
Результаты испытаний и расчетов
Показатели |
|
|
|
|
|
Величины |
|
|
|
|
|
|
|
1 |
|
|
|
|
|
2 |
1. Порода |
|
|
|
|
|
|
2. Геометрические размеры |
|
|
|
|
|
|
• ширина сечения, мм |
b = |
|
|
|
|
|
• полная высота поперечного сечения скалы- |
h = |
|
|
|
|
|
ваемого элемента, мм |
|
|
|
|
|
|
• глубина врубки, мм |
h1= |
|
|
|
||
• расчетная длина плоскости скалывания, мм |
lv= |
|
|
|
|
|
• плечо сил скалывания, мм |
e = |
|
|
|
|
|
• угол наклона, град. |
α = |
|
|
|
|
|
• рабочая площадь cмятия, мм2 |
A |
= b h1 |
= |
|||
|
c |
|
cos |
α |
|
|
|
|
|
|
|||
• расчетная площадь скалывания, мм2 |
Aν = b lν = |
|
||||
• площадь поперечного сечения элемента нет- |
Ainf = (h − h1 ) b = |
|||||
то, т.е. с учетом ослаблений, мм2 |
|
|
|
|
|
|
3. Расчетныесопротивлениядревесины, МПа: |
|
|
|
|
|
|
• смятию вдоль волокон (с учетом kmod , kx в |
f cm.0.d = |
|
|
|
||
соответствии с [6, п. 2.1.2]) |
|
|
|
|
|
|
• смятию поперек волокон (с учетом kmod , kx |
f cm.90.d = |
|
|
|
||
в соответствии с [6, п. 2.1.2]) |
|
|
|
|
|
|
93
Окончание табл. 1.1
1 |
|
|
|
|
|
2 |
|
|
||
• расчетное сопротивление смятию древесины |
f cm.α.d = |
|
|
|
|
|
|
f cm.0.d |
= |
|
под углом к волокнам |
|
|
|
|
|
|
||||
|
f cm.0.d |
sin2 α+cos2 α |
|
|||||||
|
|
|
|
|
|
|
|
|
||
|
|
|
|
f cm.90.d |
|
|||||
• расчетное сопротивление древесины скалы- |
f v.0.d = |
|
|
|
|
|
|
|
|
|
ванию вдоль волокон (с учетом kmod , kx в со- |
|
|
|
|
|
|
|
|
|
|
ответствии с [6, п. 2.1.2]) |
|
|
|
|
|
|
|
|
|
|
• расчетное среднее по площадке скалывания |
f v.mod.d = |
|
f v.0.d |
|
= |
|
||||
сопротивление древесины скалыванию вдоль |
1+β |
lv |
|
|
|
|
||||
волокон |
|
|
|
|
|
|||||
|
|
|
|
|||||||
|
|
|
|
|
e |
|
|
|
|
|
• расчетное сопротивление древесины растя- |
f t.0.d = |
|
|
|
|
|
|
|
|
|
жению вдоль волокон (с учетом kmod , kx в со- |
|
|
|
|
|
|
|
|
|
|
ответствии с [6, п. 2.1.2]) |
|
|
|
|
|
|
|
|
|
|
4. Расчетная несущая способность соедине- |
|
|
|
|
|
|
|
|
|
|
ния, кН: |
|
|
|
|
|
|
|
|
|
|
• на смятие |
Rсm.d = |
f cm.α.d Ac = |
|
|||||||
• на скалывание |
Rv.d = |
f v.mod.d Av = |
|
|||||||
• на растяжение в ослабленном сечении |
Rt.0.d = |
f t.0.d k0 Ainf = |
|
|||||||
5. Расчетная нагрузка, кН: |
|
|
|
|
|
|
|
|
|
|
• на смятие |
Qсm.d = 2 Rcm.d / cos α= |
|
||||||||
• на скалывание |
Qv.d = 2 Rv.d tgα= |
|
|
|
|
|
||||
• на растяжение в ослабленном сечении |
Qt.0.d = 2 Rt.0.d tgα= |
|
||||||||
6. Минимальная расчетная нагрузка, кН |
Qi.d.min = |
|
|
|
|
|
|
|
|
Испытания производятся при кратковременном машинном нагружении ступенями по 1 кН. На каждой ступени нагрузки снимают отсчеты по двум индикаторам для определения деформаций смятия врубки и записывают в журнал испытания, форма которого приведена в табл. 1.2. После
приложения нагрузки 0,8Qi.d.min индикаторы снимают, и производится
дальнейшее нагружение образца до разрушения.
Определение полных деформаций смятия врубки производится по данным отсчетов индикаторов с учетом их масштаба. Для этого из отсчета при нагрузке, соответствующей ступени нагружения, нужно вычесть отсчет при нулевой нагрузке. А затем определить среднее значение полной деформации по двум индикаторам.
94

|
|
Испытание соединения |
Таблица 1.2 |
||
|
|
|
|||
|
|
|
|
||
Нагрузка, |
Индикатор № 1 |
Индикатор № 2 |
Средняя полная |
||
|
|
|
|
||
Отсчет по |
Полная |
Отсчет по |
Полная |
||
кН |
деформация, |
деформация, |
деформация, мм |
||
|
прибору |
мм |
прибору |
мм |
|
|
|
|
|
||
0 |
|
|
|
|
|
1
……
Q max, exp
По вычисленным средним значениям деформаций смятия строится график зависимости этих деформаций от нагрузки (рис. 1.2). По графику определяют полную деформацию смятия врубки при расчетной нагрузке Qсm.d , величины рыхлой и упругой деформаций.
Q i.d, кН |
|
|
Qcm,d |
|
|
εpl |
εel |
ε, мм |
|
εсm,exp |
|
Рис. 1.2. График зависимости деформаций смятия от нагрузки |
В завершение работы следует произвести сопоставление экспериментальных данных с теоретическими по выражениям:
95
• опытное значение разрушающей нагрузки Qmax .exp составляет от теоретического значения разрушающей нагрузки Q i .d . min
|
|
Qmax.exp −Qi.d.min |
100% ; |
|
|
|
|
||
|
|
Qi.d.min |
||
• |
опытное значение деформаций смятия врубки εcm.exp при расчет- |
|||
ной нагрузке Qcm.d составляет |
от величины деформации соединения |
|||
εcm.max , |
определенного с учетом СНБ 5.05.01-2000 εcm.max = 1,5 мм [1, |
|||
табл. 8.1], |
|
|
||
|
|
εсm.exp |
−εсm.max |
|
|
|
|
100%. |
|
|
|
εcm.max |
Отчет должен содержать рисунки образца с указанием действительных размеров, таблиц расчетов и испытаний соединения со всеми вычислениями, график зависимости деформаций смятия от нагрузки и анализ результатов испытания.
Лабораторная работа 2 ИСПЫТАНИЕ СОЕДИНЕНИЯ НА НАГЕЛЯХ
Цель работы:
•определить разрушающую нагрузку и сравнить ее с расчетной несущей способностью соединения;
•определить нагрузку, при которой резко возрастают остаточные деформации;
•определить деформацию соединения при расчетной несущей способности соединения.
2.1. Общие указания
Расчетную несущую способность соединения на цилиндрических нагелях из одного материала (сосны или ели) и одинакового диаметра следует определять по формуле
Rd = Rld.minnnns , |
(2.1) |
где Rld.min – минимальное значение несущей способности одного среза на-
геля в соединении; nn – количество нагелей в соединении; nS – количество швов в соединении для одного нагеля.
96

Расчетную несущую способность одного среза в односрезных и симметричных двухсрезных соединениях (рис. 2.1.) следует принимать как наименьшее значение из найденных по приведенным ниже формулам:
|
|
fh.1.d t1dkα |
|
|
||
Rld |
|
fh.2.d t2dkα |
; |
(2.2) |
||
= min |
||||||
|
|
|
2 |
(1 + βn ) kα |
|
|
|
fn.d d |
|
|
|
fh.1.d , fh.2.d следует принимать по [6, табл. 4.1, 4.2], где расчетное со-
противление древесины смятию приведено для сосны и ели при нормальных условиях эксплуатации. Для соединения элементов из древесины других пород или для других условий эксплуатации следует учитывать коэффициенты kmod , kx , kt в соответствии с [6, п. 2.1.2];
– расчетное сопротивление изгибу нагеля [6, табл. 4.3]. При соединении элементов из древесины других пород, отличающихся от сосны и ели, или для условий эксплуатации, отличающихся от нормальных, расчетное значение сопротивления изгибу нагеля следует умножать на квадратный корень соответствующих коэффициентов ( kmod , kx , kt );
t1 – толщина крайних элементов в симметричных соединениях или более тонких элементов в односрезных соединениях;
t2 – толщина средних элементов в симметричных соединениях или более толстых, или равных по толщине элементов в односрезных соединениях;
d – диаметр нагеля;
βn – коэффициент, зависящий от отношения толщины более тонкого
элемента к диаметру нагеля, определяется по формуле |
|
|||
βn = kn |
t1 |
, |
(2.3) |
|
d |
||||
|
|
|
где kn – коэффициент, зависящий от типа нагеля [6, табл. 4.3]. Значение коэффициента βn , определенного по формуле (2.3), не должно превышать значение βn.max , приведенного в [6, табл. 4.3];
kα – коэффициент, учитывающий угол α между силой и направлением волокон, принимается по [6, табл. 4.4].
Промежутки и расстояния между осями нагелей не должны быть меньше приведенных в [6, табл. 4.5, 4.6].
97
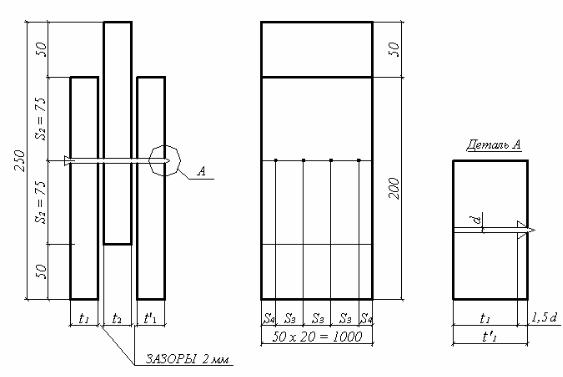
2.2. Методика проведения испытаний Приборы и оборудование: индикатор часового типа, машина испы-
тательная МС-100 (ГОСТ 8902-82), штангенциркуль, линейка измерительная металлическая, электровлагомер.
Для испытания применяют образцы на нагелях в виде стальных стержней или проволочных гвоздей (рис. 2.1.), изготовленных из сосновых или еловых досок W = 10 ÷ 15 % (по возможности без пороков).
Рис. 2.1. Конструкция образца нагельного соединения
Предварительно производят геометрические измерения и необходимые расчеты, результаты которых сводят в табл. 2.1.
При испытании образца определяют деформации сдвига соединения и разрушающую нагрузку.
Для измерения деформаций сдвига в швах на образцах устанавливают два индикатора, которые закрепляют на крайних досках так, чтобы их штрихи упирались в уголки, привинченные к средней доске (рис. 2.2.).
Ниже индикаторов на швы накладывают полоски миллиметровой бумаги, которые после отвердения клея осторожно разрезают по шву лезвием безопасной бритвы. Перед разрушением образца (после того, как индикаторы будут сняты) по этим разрезанным полоскам измеряют деформации сдвига ε .
98

Таблица 2.1
Результаты измерений и расчетов
|
Показатели |
|
|
|
|
|
Обозначение |
|
||||
1. Порода древесины |
|
|
|
|
|
|
|
|
|
|
|
|
|
|
|
|
|
|
|
|
|
|
|
|
|
2. Толщина элементов, мм: |
|
|
|
|
|
|
|
|
|
|
|
|
• |
крайних |
|
|
|
|
|
|
|
|
|
|
|
– |
со стороны забивки гвоздя |
t1= |
|
|
|
|
|
|
|
|
|
|
– |
со стороны острия гвоздя |
t1' = |
|
|
|
|
|
|
|
|
||
• |
среднего |
t2= |
|
|
|
|
|
|
|
|
|
|
• |
расчетная толщина крайнего элемента со стороны |
t |
= t' |
−1,5d |
|
|||||||
острия |
1 |
|
|
|
1 |
|
|
|
|
|
|
|
|
|
|
|
|
|
|
|
|
|
|
||
3. Диаметр нагеля |
d= |
|
|
|
|
|
|
|
|
|
||
4. Количество нагелей |
nn= |
|
|
|
|
|
|
|
|
|||
5. Количество швов для одного соединения |
ns= |
|
|
|
|
|
|
|
|
|
||
6. Расстояния, мм |
|
|
|
|
|
|
|
|
|
|
|
|
• |
между осями вдоль волокон |
S1 = |
|
|
|
|
|
|
|
|
||
• |
до торца элемента вдоль волокон |
S2 = |
|
|
|
|
|
|
||||
• |
между осями поперек волокон |
S3 = |
|
|
|
|
|
|
|
|||
• |
до кромки элемента поперек волокон |
S4 = |
|
|
|
|
|
|
|
|||
7. Минимальныерасстоянияпонормам[6, табл. 4.5, 4.6], мм: |
|
|
|
|
|
|
|
|
|
|
|
|
• |
между осями вдоль волокон |
S1.min = |
|
|||||||||
• |
до торца элемента вдоль волокон |
S2.min |
= |
|
|
|
||||||
• |
между осями поперек волокон |
S3.min |
= |
|
|
|
||||||
• |
до кромки элемента поперек волокон |
S4.min = |
|
|||||||||
8. Расчетная несущая способность одного среза, кН: |
|
|
|
|
|
|
|
|
|
|
|
|
из условия смятия крайнего элемента |
|
|
|
|
|
|
|
|
|
|
|
|
– |
со стороны забивки гвоздя |
Rld |
1 = fh.1.d t1dkα = |
|||||||||
– |
со стороны острия гвоздя |
Rld |
2 = fh.1.d t1dkα = |
|||||||||
• |
из условия смятия среднего элемента |
|
|
3 |
= fh.2.d t2dkα |
= |
||||||
|
|
Rld |
|
|||||||||
|
из условия изгиба нагеля |
|
|
|
|
|
|
|
|
|
|
|
– |
со стороны забивки гвоздя |
Rld |
4 |
|
= fn.d (1+βn ) |
kα d 2 |
||||||
|
|
βn |
= kn |
t1 |
≤ βn.max |
|
||||||
|
|
|
|
|
||||||||
|
|
|
|
|
|
|
|
|
d |
|
||
– |
со стороны острия гвоздя |
Rld |
5 |
= fn.d (1+βn ) |
kα d 2 = |
|||||||
|
|
βn |
= kn |
t1 |
≤ βn.max |
|
||||||
|
|
|
|
|||||||||
|
|
|
|
|
|
|
|
|
d |
|
||
9. Минимальнаянесущаяспособностьодногосоединения, кН |
|
|
|
|
|
|
|
Rld.min = |
|
|||
10. Расчетная несущая способность соединения, кН |
|
|
|
Rd = Rld.minnnns |
||||||||
11. Разрушающая нагрузка, кН |
|
|
|
|
|
|
|
Qmax.exp = |
|
|||
12. Полная величина деформации сдвига, мм |
|
|
|
|
|
|
|
|
|
εv.exp = |
|
99
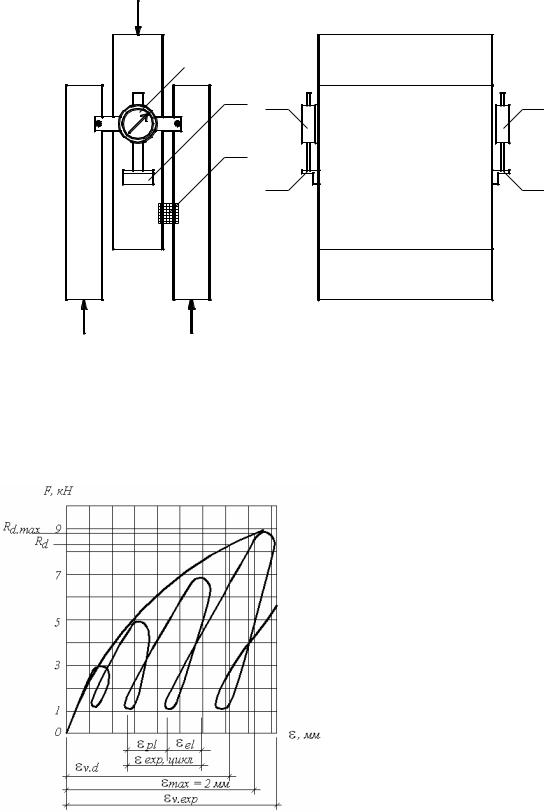
|
Q |
|
1 |
|
2 |
|
3 |
Q/2 |
Q/2 |
1 |
1 |
2 |
2 |
Рис. 2.2. Схема расстановки индикаторов:
1 – индикаторы; 2 – уголки для упора штифтов; 3 – миллиметровая бумага
Для ликвидации рыхлых деформаций образец предварительно загружают нагрузкой 1 кН, которая принимается в дальнейшем за условный нуль. Нагружение производится ступенями с равномерной скоростью 0,3 кН/с. При последующих нагружениях на каждой ступени нагрузки, равной 1 ÷ 2 кН, с разгрузкой после каждого цикла до условного нуля (рис. 2.3.) снимают отсчеты и записывают
в табл. 2.2.
Величину разрушающей нагрузки определяют по силоизмерителю машины, когда при непрерывном росте деформаций нагрузка не увеличивается.
Рис. 2.3. График зависимости деформации сдвига нагельного соединения от нагрузки: εv.exp – полная деформация от начала испытаний; εpl – остаточная деформация за цикл; εel – упругая деформация; εexp, цикл – полная деформация за цикл
100