
Lab
.pdfТаблица 12.2 - Физико-механические свойства порошковых конструкционных материалов общего назначения без термической обработки
Марка |
Предел прочно- |
Относительное |
Ударная |
Твёрдость |
материала |
сти при растя- |
удлинение по- |
вязкость, КСV, |
НВ |
|
жении δВ , МПа |
сле разрыва, δ, |
кДж/м2, |
|
|
не менее |
%, не менее |
не менее |
|
СП10-1 |
100 |
6 |
200 |
50-70 |
|
|
|
|
|
СП10-2 |
120 |
8 |
350 |
70-80 |
|
|
|
|
|
СП10-3 |
150 |
12 |
500 |
80-90 |
|
|
|
|
|
СП10-4 |
250 |
18 |
700 |
90-130 |
|
|
|
|
|
СП30-1 |
120 |
6 |
200 |
50-70 |
|
|
|
|
|
СП30-2 |
160 |
8 |
350 |
70-80 |
|
|
|
|
|
СП30-3 |
200 |
12 |
500 |
80-90 |
|
|
|
|
|
СП30-4 |
250 |
18 |
700 |
90-130 |
|
|
|
|
|
СП70-1 |
120 |
5 |
150 |
50-70 |
|
|
|
|
|
СП70-2 |
200 |
8 |
300 |
70-90 |
|
|
|
|
|
СП70-3 |
280 |
10 |
400 |
90-110 |
|
|
|
|
|
СП70-4 |
350 |
15 |
600 |
110-150 |
|
|
|
|
|
СП30Д3-2 |
220 |
4 |
300 |
70-90 |
|
|
|
|
|
СП30Д3-3 |
280 |
6 |
400 |
90-100 |
|
|
|
|
|
СП30Д3-4 |
360 |
10 |
600 |
100-140 |
|
|
|
|
|
СП70Д3-2 |
260 |
3 |
200 |
80-100 |
|
|
|
|
|
СП70Д3-3 |
360 |
5 |
300 |
100-120 |
|
|
|
|
|
СП70Д3-4 |
450 |
8 |
450 |
120-160 |
|
|
|
|
|
СП30Д3П-2 |
300 |
3 |
200 |
90-110 |
|
|
|
|
|
СП30Д3П-3 |
360 |
4 |
300 |
110-130 |
|
|
|
|
|
СП30Д3П-4 |
450 |
6 |
400 |
130-180 |
|
|
|
|
|
12.5 Маркировка порошковых сталей
Марки порошковых сталей обозначают сочетанием букв и цифр. Первые две буквы «СП» указывают, что сталь получена методом порошковой металлургии. Число после букв «СП» показывает среднее содержание общего углерода в сотых долях процента (содержание свободного углерода при этом не превышает 0,2 %). Следующие за этим числом буквы обозначают легирующие элементы. Обозначение как в легированных сталях: Д – медь, Н – никель, С – кремний, Х – хром и т. д.
Цифра после дефиса указывает подгруппу плотности материала: 1 – пористость 26 – 16 %, плотность γ = 6,0 – 6,6 г/см3;
2– пористость 15 - 10 %, плотность γ = 6,7-7,1 г/см3;
3– пористость 9 – 12 %, плотность γ = 7,2-7,7 г/см3;
135
4 – пористость не более 2 %, плотность γ ≥ 7,7 г/см3.
12.5 Микроструктура порошковых сталей
Свойства порошковых сталей зависят от их макро- и микроструктуры. Структурными составляющими порошковых материалов являются металлические фазы, образующие основу материала и неметаллические включения (например, графит, оксиды, карбиды, нитриды и др.). Металлическая основа порошковых сталей, как и литых сталей – ферритная, феррито-перлитная или перлитно-цементитная, согласно диаграмме Fe – Fe3C.
Пористость может рассматриваться как совокупность сообщающихся протяжённых пор – каналов, которые могут быть тупиковыми, изолированными, а также выходить на поверхность и сообщаться между собой. Для определения формы пор и их распределения приготовляют шлифы по различным направлениям по отношению направления прессования и изучают пористость на непротравленных или слегка протравленных шлифах.
При травлении железографитовых сплавов 4 %-ным раствором азотной кислоты в спирте выявляются цементитные и ферритные составляющие. Перлит окрашивается в коричневый цвет, феррит остаётся светлым. Для выявления цементита проводят травление пикратом натрия. При травлении образец часто просто погружают в травитель, однако, если материал пористый, травитель проникает в поры и трудно из них вымывается, что приводит к коррозии шлифа. Для материалов с более 20 % пор целесообразно применять метод втирания. Распределение пористости и включений рекомендуется исследовать при 150–200-кратном увеличении. При исследовании пористых материалов на микрошлифах трудно отличить поры от включений графита. В этом случае следует обращать внимание на разность очертания границ. Границы пор очерчены более чётко, в то время как включения графита не имеют резких очертаний. Поры легко отличить от включений графита при изменении фокусировки микроскопа, так как при приближении к окуляру выявляется дно поры.
Из анализа микроструктур (рисунки 12.1, 12.2) следует, что если до спекания образец представляет собой конгломерат поверхностнодеформированных частиц, разделённых между собой межчастичными границами и порами различной формы (рисунок 12.1), то после спекания частицы приобретают более равновесную форму, межчастичные границы утончаются, а их сплошность нарушается, что приводит к возникновению качественно новых контактных участков с характерными металлическими свойствами
(рисунок 12.2).
Порошковые стали характеризуются значительной химической и структурной неоднородностью. Это определяется тем, что спекание выполняется при температурах ниже температуры плавления; скорости диффузии элементов, входящих в состав сплава, не обеспечивают полного растворения
(рисунок 12.3).
136
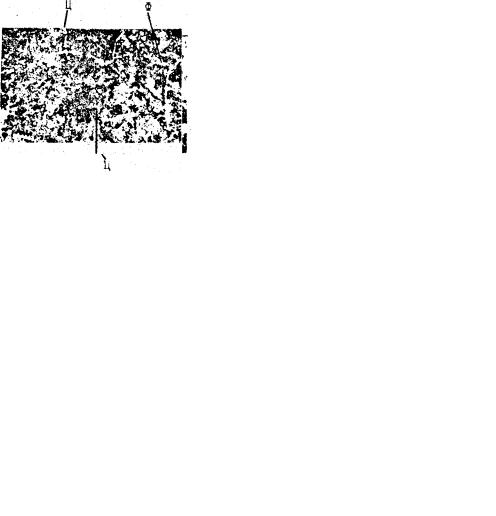
На нетравленых шлифах хорошо различимы некоторые металлические включения, например, меди (рисунок 12.4). Залегания видны в виде розовожёлтых включений, расположенных на стыках частиц, прилегающих к порам. После травления крупные включения графита хорошо заметны.
|
|
|
|
|
|
|
х340 |
Феррит, перлит, свободный |
|||
|
|
|
графит, поры х340 |
||
Рисунок 12.1- Микроструктура |
Рисунок 12.2 - Микроструктура |
||||
спрессованного образца из |
спеченной стали СП50-1 |
||||
шихты СП50 |
|
|
|
|
|
|
|
|
|
|
|
|
|
|
|
|
|
|
медь |
||
Феррит, перлит, цементит, |
Феррит, перлит, цементит, |
||||
графит, поры х340 |
выделения меди, поры х450 |
||||
Рисунок 12.3 – Микроструктура |
Рисунок 12.4 - Микроструктура |
||||
спеченной стали СП100-2 |
спечённой стали СП150Д2-1 |
12.6 Термическая обработка порошковых сталей
Для порошковых сталей возможно применение различных видов термической обработки. Наличие пористости в изделиях вызывает необходимость ряда условий: нагрев под закалку необходимо вести в защитных средах или вакууме время нагрева и время выдержки должно быть на 20-30 % больше, чем для литых сталей аналогичного состава, вследствие пониженной теплопроводности необходимы повышенные скорости охлаждения.
137
Принципиальное отличие закалённых порошковых сталей от беспористых состоит в том, что если твёрдость у порошковых сталей после закалки повышается (как в беспоритых сталях соответствующего химического состава), то прочность либо повышается несущественно по отношению к спечённому состоянию, либо даже несколько понижается. В порошковых сталях при закалке на величину и распределение закалочных напряжений будут оказывать влияние поры, межчастичные границы, химическая неоднородность. Это влияние проявляется в крайне неравномерном распределении в изделиях внутренних напряжений, появлении их пиков в устьях пор и других дефектах структуры, что снижает вязкость и способствует хрупкому разрушению.
Повышение прочности в закалённых сталях происходит только после отпуска с температур, обеспечивающих снятие закалочных напряжений. Установлено, что максимальная прочность закаленных порошковых сталей достигается после проведения отпуска в интервале температур 200-450 ºС.
Скорость охлаждения при термической обработке оказывает решающее влияние на структуру и свойства изделий, поэтому она строго устанавливается в зависимости от назначения обработки и требований, предъявляемых к термически обрабатываемым изделиям. При закалке в масле твёрдость ниже, чем при закалке в воде, но наблюдается повышение прочности. Объясняется это тем, что более «мягкая» закалка в масле снижает величину и неоднородность внутренних напряжений и обеспечивает более устойчивое состояние структуры по сравнению с закалкой в воде. Охлаждение в масле при закалке
вбольшинстве случаев не обеспечивает получение мартенситной структуры,
асоответственно высокой прочности и твёрдости.
Преимущество воды в качестве закалочной жидкости заключается в том, что она, обладая высокой охлаждающей способностью в интервале температур 650-550 ºС, подавляет диффузионное превращение аустенита в области его минимальной устойчивости.
Это свойство воды является особенно ценным для порошковых сталей в связи с пониженной устойчивостью аустенита. Одновременно повышенная охлаждающая способность воды в области температур 300-100 ºС не обеспечивает равномерного охлаждения, способствует появлению в закалённых изделиях внутренних трещин, а также трещин и «мягких» пятен на поверхности.
Температура нагрева при термической обработке оказывает большое влияние на структуру и свойства обрабатываемых порошковых сталей, поэтому она устанавливается в зависимости от состава стали, её пористости и назначения обработки. Температура нагрева под закалку для углеродистых и низколегированных сталей выше точки Ас3 на 60-80 ºС. Оптимальная температура отпуска связана также с пористостью, с увеличением пористости сталей температура отпуска повышается.
На кафедре МТМ ОГУ проведён большой объём работ по термической и химико-термической обработке порошковых сталей с нагревом в соляных ваннах.
138
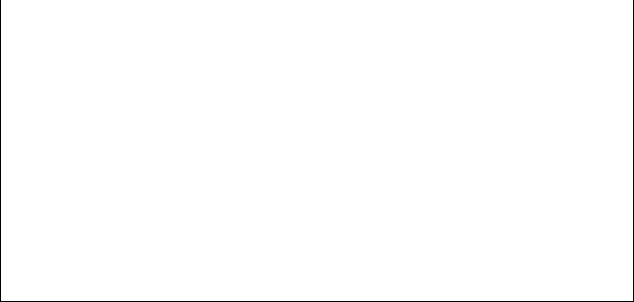
Порошковые стали из-за наличия пор имеют повышенную склонность к коррозии по сравнению с литыми сталями. Снижение коррозии порошковых сталей достигается проведением термической обработки по предложенной нами технологии, а также за счёт введения операций пассивации и маслопропитки после термической обработки (таблица 12.3).
Таблица 12.3 - Технология термической обработки спечённых сталей
№ |
Наименование |
Среда |
Темпе- |
Время, |
|
операций |
|
ратура, |
мин. |
|
|
|
ºС |
|
1 |
Ванна нагрева |
Соляная ванна состава |
760-950 |
В зависимо- |
|
деталей |
75-80 % BaCl2 + 25-20 % NaCl |
|
сти от разме- |
|
|
|
|
ров и массы |
2 |
Ванна закалки |
Вода + 0,5 % NaCl или масло |
|
1-2 |
3 |
Участок сушки |
Сжатый подогретый воздух |
70-100 |
3-6 |
|
после закалки |
|
|
|
4 |
Ванна отпуска |
50 % KNO3 + 50 % NaNO2 |
160-500 |
9-18 |
5 |
Первая отмывка |
Вода + 1 % Na2CO3 |
90-100 |
3-6 |
6 |
Вторая отмывка |
Вода |
90-100 |
3-6 |
7 |
Пассивация |
Вода + 4-5 % NaNO2 + 1-1,5 % Na2CO3 |
90-100 |
3-6 |
8 |
Сушка |
|
100-120 |
3-6 |
9 |
Ванна пропитки |
Масло И-20 |
80-90 |
3-6 |
Примечание - Время 3-6 минут в зависимости от размеров деталей
Проведённые коррозионные испытания показали, что скорость коррозии порошковых изделий различной пористости при относительной влажности воздуха 90 % практически равна скорости коррозии аналогичных порошковых материалов после спекания. Установлено, что и после длительного хранения коррозионная стойкость термообработанных в соляных расплавах порошковых материалов сравнима с коррозией аналогичных материалов после спекания.
Сравнительные исследования различных защитных сред при термической обработке порошковых сталей позволяют сделать заключение, что при нагреве порошковых сталей в соляных ваннах свойства их выше и стабильнее, чем при применении газовых защитных атмосфер (рисунок 12.5).
Кроме того, время термической обработки с использованием соляных ванн в 4-6 раз меньше и операция выполнения термической обработки легко поддаётся автоматизации.
12.7 Порядок выполнения работы
12.7.1Ознакомиться с образцами деталей, изготовленных методом порошковой металлургии.
12.7.2По излому сделать выводы о равномерности спекания образца,
139

140
Сплошные линии - термообработка в соляных ваннах, штриховые линии – термообработка в среде водорода
Рисунок 12.5 – Влияние среды нагрева и температуры отпуска на механические свойства порошковой стали СП150Д2,5

наличии оплавления, окисления.
12.7.3Просмотреть под микроскопом микрошлифы порошковых сталей в нетравленом виде и травленные.
12.7.4Описать наличие пор, их форму, размеры, распределение по объёму изделия.
12.7.5Определить и записать микроструктуру стали, металлические фазы, наличие неметаллических включений.
12.7.6По маркировке определить химический состав порошковых
сталей.
12.7.7Определить массу и объём порошковой детали. Вычислить относительную плотность θ, % и пористость П, %.
Относительная плотность определяется отношением плотности спечённого изделия к плотности компактного сплава
θ= γ 100 ,
γк
где γ – плотность спрессованного или спечённого изделия, г/см3; γ к - плотность того же изделия в беспористом состоянии (компактного
сплава), г/см3.
П= 100 - θ
12.7.8Измерить твёрдость HB спечённых образцов порошковой
стали.
12.8 Содержание отчета
12.8.1Цель работы.
12.8.2Характеристика основных процессов порошковой металлургии.
12.8.3Описание микроструктуры образцов порошковой стали.
12.8.4Расчёт плотности и пористости спечённого образца.
12.8.5Результаты измерения твёрдости.
12.8.6Выводы.
12.9 Контрольные вопросы
12.9.1Что такое порошковая металлургия?
12.9.2Преимущества и недостатки метода порошковой металлургии.
12.9.3Технологическая схема получения изделий методом порошковой металлургии.
12.9.4Сущность процесса формообразования.
12.9.5Методы формования заготовок.
141
12.9.6Назначение процесса спекания. При каких температурах и в каких защитных средах ведётся спекание? Внешние признаки спекания.
12.9.7Какова структура порошковых сталей?
12.9.8Маркировка порошковых сталей.
12.9.9Классификация и области применения порошковых материалов.
142
13 Лабораторная работа № 13
Твёрдые сплавы
13.1 Цель работы
Ознакомиться с технологией изготовления твердых сплавов, их свойствами, микроструктурой и применением.
13.2 Основные сведения
Порошковые твердые сплавы впервые появились в 1923-1925 годах (изготовитель - германская фирма "Осрам"), что позволило увеличить скорости резания в 5-10 раз. При эксплуатации инструмента выяснилось, что дорогостоящий вольфрам, используемый при изготовлении твердых сплавов, даёт гораздо больший эффект, чем, например, в составе быстрорежущей стали. Так, инструментом с одной и той же массой вольфрама, в случае применения твердосплавного инструмента можно обработать в 6 раз больше металла, чем инструментом из быстрорежущей стали.
В нашей стране промышленное производство твердых сплавов было начато на Московском электрозаводе в 1929 году выпуском вольфрамокобальтового твердого сплава марки ВК10 ("Победит").
Большая часть имеющихся твердых сплавов предназначена для обработки резанием различных материалов, в том числе чугунов, нержавеющих, жаропрочных и специальных сталей и сплавов. Важной областью применения твердых сплавов является их использование для волочения и калибрования проволоки, прутков, труб и т.д. Штамповый твердосплавный инструмент высокой прочности и износостойкости применяют для работы в условиях ударных нагрузок и для высокопроизводительного горного инструмента.
13.3 Классификация и маркировка твердых сплавов
Твердые сплавы представляют собой сплавы на основе карбидов тугоплавких металлов (WC, TiC, TaC) и металлической связки (кобальт или никель). Твердые сплавы обычно содержат 70-97 % тугоплавких карбидов. Они обладают высокой твердостью (86-92 HRA), красностойкостью (800-1000 °С) и износостойкостью при меньшей прочности по сравнению с быстрорежущей сталью (σ < 2500 МПа).
Твердые сплавы условно делят на 4 группы:
1) однокарбидные вольфрамовые, состоящие из карбида вольфрама
икобальта (WC – Co);
2)двухкарбидные титановольфрамовые, состоящие из карбида вольфрама (основа), карбида титана и кобальта (WC - TiC - Co);
143
3)титанотанталовольфрамовые сплавы, в состав входят карбиды вольфрама (основа), титана, тантала и кобальт (WC – TiC – TaC – Co);
4)безвольфрамовые твёрдые сплавы, состоящие из карбида или карбонитрида титана, связки Ni или сплава Ni - Mo: TiC - Ni - Mo (сплавы ТН); TiC – TiN - Ni - Mo (сплавы КНТ).
Вольфрамовые сплавы обозначаются буквами ВК и цифрой, указывающей процентное содержание кобальта, например, сплав ВК6 содержит 6 % кобальта, остальное (94 %) - карбид вольфрама. К этой группе относятся сплавы ВК3, ВК4, ВК6, ВК8, BKIO, BKI5, ВК20, ВК25. Чем больше кобальта
втвердом сплаве, тем выше прочность, но ниже твердость и износостойкость. Теплостойкость их - до 800 °С. Для сплава ВК8, например, предел
прочности при изгибе σu = 1717 МПа, твёрдость 87,5 НRА, а для сплава ВК25: σu = 2452 МПа, 83 HRA.
Буква М в марке сплава обозначает, что сплав мелкозернистый (ВК6 М), буква К – крупнозернистый (ВК20 – К), буква В указывает, что изделия спекались в атмосфере водорода (ВК6-В). Сплавы с крупным зерном отличаются повышенной ударной вязкостью. Чем меньше зерно карбидной фазы, тем выше износостойкость твёрдого сплава.
Титановольфрамовые твердые сплавы обозначаются буквами ТК и цифрами, стоящими после каждой цифры, которые указывают конкретное содержание карбида титана и кобальта. Так, Т15К6 содержит 15 % карбида титана, 6 % кобальта, остальное - карбид вольфрама. Теплостойкость сплавов группы ТК – до 900-1000 °С.
Титанотанталовольфрамовые сплавы обозначаются буквами ТТК и цифрами: ТТ7К12 - карбидов титана и тантала - 7 %, кобальта 12 %, остальное - карбид вольфрама. Теплостойкость сплавов группы ТТКдо 1000 °С.
Безвольфрамовые твердые сплавы отличаются высокой окалиностойкостью, отсутствием дефицитного вольфрама, вдвое меньшей плотностью по сравнению со сплавами группы ВК, однако уступают им по прочности, ударной вязкости и теплопроводности.
Химический состав безвольфрамовых твёрдых сплавов:
карбидотитановые – 70-80 % TiC, 20-40 % Ni-Mo (сплавы TH-20, TH30, TH-40);
карбидонитридотитановые – 25-45 % TiC, 25-45 % TiN, 30-35 % Ni-Mo (KHT16 и др.)
При обработке сталей используются сплавы группы ТК, а чугунов - группы ВК. Сплавы группы ТТК более универсальные, применяются как при обработке сталей, так и чугунов. Безвольфрамовые твердые сплавы рационально использовать при получистовой и чистовой обработке углеродистых сталей и цветных металлов.
144