
Основы технологии приборостроения (лаб.практ
.).pdfнизма. Коробка подач станка в сочетании с гитарой 4 позволяет устанавливать требуемые передаточные отношения для нарезания резьбы с различным шагом и получения различных продольных и поперечных подач. Гитара соединяет переднюю бабку с коробкой подач. Сменные зубчатые колеса гитары обеспечивают необходимые величины подач.
Фартук 10 передает движение от ходового винта суппорту 8. Встроенная в механизм фартука блокировка исключает возможность одновременного включения продольной и поперечной подач. Ручное перемещение суппорта осуществляется с помощью маховика с контролем величины перемещения по лимбу.
Суппорт крестового типа предназначен для закрепления и подачи режущего инструмента. Нижние салазки суппорта перемещаются в продольном направлении по станине. Сверху, на направляющих нижних салазок установлены поперечные салазки, на которых закреплены поворотные салазки. По направляющим поворотных салазок перемещается (вручную) верхняя каретка, несущая четырехпозиционный резцедержатель, с фиксацией в четырех положениях. Расположение органов управления станка 16Б05А показано на рис. 2.4.
Технические характеристики токарно-винторезного станка особо высокой точности 16Б05А
Класс точности ....................................................................................................... А
Наибольший диаметр обрабатываемой заготовки над станиной …………………………………………………….................250 мм
Наибольший диаметр обрабатываемой заготовки над суппортом ……………………………………………………………..145 мм
Наибольшая длина обрабатываемой заготовки ………………………………500 мм Наибольший диаметр заготовки, проходящего через отверстие шпинделя …26 мм Пределы частот вращения шпинделя ……………………………………….25…2500
Количество продольных подач ……………………………………………………...28 Количество поперечных подач ……………………………………………………...28 Пределы продольных чистовых подач …………………………….0,01…0,14 мм/об Пределы нормальных подач ………………………………………..0,02…0,35 мм/об Пределы поперечных подач …………………………………………………0,5 мм/об Цена одного деления лимба ……………………………………………………..0,02 м
Длина станка …………………………………………………………………...1530 мм Ширина станка ………………………………………………………………….910 мм Высота станка ………………………………………………………………….1389 мм Масса станка ……………………………………………………………………1200 кг
30
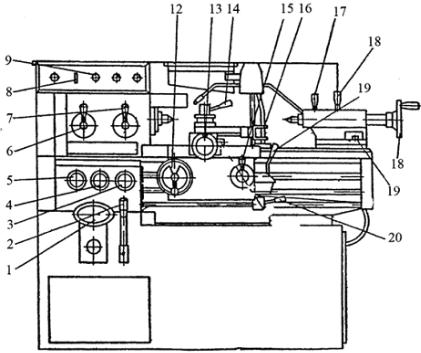
Рис. 2.4. Органы управления станка 15Б05А: 1 – маховик выбора частоты вращения шпинделя, 2 – рукоятка переключения частоты вращения шпинделя, 3,4,5 – рукоятки установки величины подач и шага резьбы, 6 – рукоятка переключения трензеля и звена увеличения шага, 7 – рукоятка переключения перебора, 8 – вводный выключатель, 9 – выключатель электронасоса, 10 – маховик ручной продольной подачи, 11 – маховик ручной поперечной подачи, 12 – рукоятка закрепления резцедержателя, 13 – рукоятка включения и выключения гайки ходового винта, 14 – маховик перемещения верхних салазок, 15 – рукоятка зажима пиноли, 16 – рукоятка закрепления задней бабки на станине, 17 – рукоятка реверсирования подачи, 18 – маховик перемещения пиноли, 19 – гайка для закрепления
задней бабки на станине, 20 – рукоятка пуска и остановки
Порядок выполнения работы
1. Прослушать вводный инструктаж по технике безопасности при работе в механической лаборатории и изучить правила безопасности работы на токарном станке (приложение 2.1).
31
2.Изучить раздел «Необходимые теоретические сведения», методические указания и получить задание у преподавателя, выполнить необходимые расчеты.
3.Изучить устройство станка, используя описание станка и плакаты, обращая внимание на органы управления.
4.После проверки преподавателем результатов расчетов обработать заготовку при принятых режимах резания.
5.Провести замеры диаметра обработанной детали в пяти точках по длине (через 20 мм) и начертить эскиз детали.
6.Определить действительное изменение фактической глубины резания по длине детали и сравнить с расчетным, построив графики t = f(l).
7.По величине погрешности формы Ї = dmax – dmjn определить точность (квалитет точности) обработки.
8.Оформить отчет по лабораторной работе (приложение 2.2).
П Р И Л О Ж Е Н И Е 2.1
Правила безопасной работы на токарно-винторезном станке особо высокой точности 16Б05А
Токарный станок является высокооборотной машиной, и поэтому при работе на нем необходимо строго выполнять следующие указания:
1.Изучить станок прежде, чем начинать работу на нем.
2.Перед началом работы убедиться в прочности закрепления патрона на шпинделе. Патрон крепится на шпинделе разжимным кольцом с помощью винта. Несоблюдение этого правила может привести к свертыванию патрона со шпинделя при реверсе и нанести тяжелую травму.
3.Надежно закрепить деталь.
4.Не касаться вращающихся частей станка до полной его остановки.
5.Не приближаться к зоне резания во избежание травм от отлетающей
стружки.
6.Запрещается пользоваться рукояткой реверса для торможения шпинделя. Это может привести к резким толчкам и ослабить крепление патрона.
7.Запрещается начинать работу с включения высоких чисел оборотов шпинделя (2000, 1340). Предварительно необходимо прогреть подшипники на средних оборотах.
32
П Р И Л О Ж Е Н И Е 2.2
Лаборатория № 2 Отчет по лабораторной работе № 2
«Исследование процесса обработки на токарном станке»
Работа принята________________Студент________________
Руководитель________________Группа________________
«___»_______________ г.
1.Задание
2.Схема обработки
3.Исходные данные
№ п/п |
Наименование |
Размерность |
Числовое значение |
|
|
|
|
|
|
1 |
Наименование и марка материала |
|
Сталь 20 |
|
заготовки |
|
|||
|
|
|
||
|
Прочностные характеристики |
|
2∙104 |
|
|
материала заготовки: |
МПа |
||
2 |
модуль упругости, Е |
МПа |
1630 |
|
|
твердость, НВ |
МПа |
412 |
|
|
предел прочности, & в |
|
|
|
|
|
|
Проходной |
|
3 |
Вид резца |
|
отогнутый правый |
|
|
прямоугольного |
|||
|
|
|
||
|
|
|
сечения державки |
|
4 |
Материал режущей части резца |
|
|
|
|
|
|
|
|
5 |
Величина главного угла |
град |
45 |
|
в плане резца (р) |
||||
|
|
|
||
6 |
Величина угла при вершине резца £ |
град |
90 |
|
|
|
|
|
|
7 |
Диаметр заготовки |
мм |
|
|
|
|
|
|
|
8 |
Диаметр детали |
мм |
|
|
|
|
|
|
|
9 |
Схема закрепления заготовки |
|
Консольное закреп- |
|
|
ление в патроне |
|||
|
|
|
4.Эскиз заготовки, операционный эскиз и эскиз токарного резца
5.Последовательность выполнения расчетов
1.Определение глубины резания.
2.Определение расчетного S0 и паспортного Sп значений подачи.
3.Расчет скорости резания vр и определение числа оборотов шпинделя np.
33
4.Корректировка числа оборотов по паспорту станка nп и соответственно пересчет скорости резания vg .
5.Расчет радиальной составляющей силы резания Pу.
6.Определение величины отжатия детали y1 при различных значениях l.
7.Определение изменения фактической глубины резания по длине заготовки.
6.Эскиз с результатами замеров обработанных деталей, квалитеты точности,
графики
7. Выводы
ЛАБОРАТОРНАЯ РАБОТА № 3
ИССЛЕДОВАНИЕ ПРОЦЕССА ТОРЦЕВОГО ТОЧЕНИЯ
Цель работы – изучить на практике процесс торцевого точения и экспериментально исследовать влияние подачи на степень шероховатости обработанной поверхности.
Необходимые теоретические сведения
Обработка торцевых поверхностей. При обтачивании тор-
цевых поверхностей резец перемещается поперечным суппортом. Для обтачивания применяют подрезные и проходные упорные резцы. Точение торцевых поверхностей производят как от наружной боковой поверхности к центру заготовки, так и наоборот.
Если заготовки имеют на наружной поверхности твердую корку, резец подается от центра заготовки к периферии, предупреждая этим преждевременный износ режущей кромки. Для обработки торцев применяют проходной упорный резец, позволяющий производить как продольное, так и торцевое точение поверхностей (рис. 3.1, а). Особое внимание следует уделять заточке резца по задней поверхности и его точному закреплению, чтобы избежать трения резца о заготовку (рис. 3.1, б).
При точении торцевых поверхностей подрезной резец устанавливают точно по центру, так как в противном случае поверхность торца не будет обработана до конца и останется выступ.
При обработке больших торцевых поверхностей следует применять станок с бесступенчато регулируемой частотой вращения, что позволит сохранять постоянной скорость резания. Установку и
34
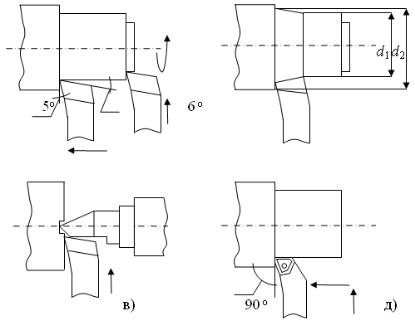
закрепление деталей при подрезании торцов и уступов производят в основном теми же способами, что и при продольном обтачивании. Короткие детали закрепляют в патроне, длинные устанавливают в центрах. Крупные и длинные детали устанавливают и закрепляют одним концом в патроне, а другой конец поддерживают задним центром.
а |
б |
|
в |
|
д |
|
|
|
Рис. 3.1. Продольное и торцевое точение упорным проходным резцом: d1 – фактический диаметр, d2 – заданный диаметр
Прутки и длинные заготовки небольших диаметров (до 50 мм) обычно устанавливают через сквозное отверстие шпинделя, выдвигая заготовку на требуемую длину.
При подрезании торцов деталей, устанавливаемых в центрах, не следует применять обычный центр, так как можно повредить режущую кромку резца. В этих случаях ставят упорный полуцентр
35
(рис. 3.1, в), обеспечивающий свободный подвод резца для подрезания всего торца с подачей от наружной поверхности к центру.
Торцы деталей, закрепляемых в патроне, целесообразно подрезать не подрезным, а проходным упорным отогнутым резцом с подачей резца от периферии к центру и наоборот. Последний имеет более массивную режущую часть и допускает более высокие режимы резания. На рис. 3.1, д показано подрезание уступа высотой до 5 мм за один рабочий ход при продольной ручной подаче. В этом случае используют проходной упорный резец с многогранной неперетачиваемой пластиной из твердого сплава. При подрезании уступа высотой более 5 мм подрезание производят за несколько рабочих ходов.
Уступы большой высоты обрабатывают за несколько рабочих ходов, сочетая продольную подачу с поперечной. При подрезании большого количества одинаковых деталей с уступами применяют упоры, ограничивающие перемещение резца.
При подрезании торцов и уступов припуски в зависимости от длины и диаметра заготовки определяют по табл. 3.1.
|
|
Т а б л и ц а 3.1 |
|
|
|
|
|
Диаметр заготовки, |
Припуск по длине детали, мм |
||
мм |
|
|
|
до 18 |
18–50 |
||
|
|
|
|
До 30 |
0,4 |
0,5 |
|
|
|
|
|
Подачу при черновом и чистовом точении торцов и уступов определяют исходя из глубины резания, шероховатости поверхности и физико-механических свойств заготовки. При этом меньшее значение подачи берется для более прочных материалов. Скорость резания при подрезании торцов непостоянна и уменьшается к центру детали по мере уменьшения диаметра обработки. При подрезании торцов скорость резания определяется в зависимости от наружного диаметра заготовки.
Основные виды брака при обработке торцов и уступов:
1)недостаточное качество обработанной поверхности торцов, получаемое из-за завышенной подачи;
2)непараллельность торцов при обработке их в патроне, получаемая из-за погрешностей при установке и закреплении заготовки
впатроне при обтачивании второго торца.
36
Факторы, влияющие на качество обработанных поверхно-
стей. Параметр шероховатости поверхности зависит от многих факторов: метода обработки, режимов резания, геометрических параметров и качества поверхностей режущей части инструмента, пластической и упругой деформации обрабатываемого материала, жесткости системы «станок–приспособление–инструмент–заготов- ка» и связанных с ней вынужденных колебаний и вибраций при резании, смазочно-охлаждающей жидкости и др.
Для расчета параметра шероховатости используется формула
Rz = Rp + Rпл + Rупр + Rл + Rц + Rж,
где Rp – расчетная высота шероховатости (доля высоты параметра шероховатости, вычисленная по продольной подаче); Rпл – доля высоты шероховатости, получающаяся вследствие пластического деформирования материала перед лезвием инструмента; Rупр – доля высоты шероховатости, получающаяся за счет упругого восстановления материала после прохода режущего инструмента; Rл – доля высоты шероховатости, создаваемая микронеровностью лезвия инструмента; Rц – доля высоты шероховатости, образованная повреждением отходящей стружки, которая не всегда помещается в промежутках между зубьями многолезвийного инструмента; Rж – доля высоты шероховатости, образуемая за счет недостаточной жесткости системы «станок–приспособление–инструмент–заготов- ка». Перечисленные факторы являются основными, поэтому необходимо учитывать лишь их влияние на шероховатость поверхности.
На основании анализа выполненных научно-исследователь- ских работ можно сделать вывод о том, что шероховатость обработанной поверхности представляет, прежде всего, след рабочего движения части режущей кромки инструмента, контактирующей с обрабатываемым материалом. Высоту этой шероховатости определяют расчетным путем в зависимости от геометрических пара-
метров режущей части инструмента: углов в плане − главного φ и вспомогательного φ1, радиуса rв закругления вершины режущего инструмента и подачи.
Например, при точении возможны частные случаи (рис. 3.2): а) расчетная высота неровности поверхности Rp образуется це-
ликом закругленным участком режущей кромки (рис. 3.2, а):
37
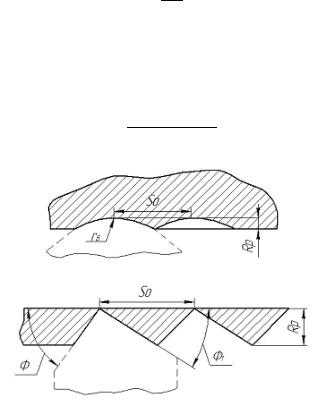
S 2 Rр = 8r0в ,
где S0 — подача, мм/об; rв — радиус закругления резца при вершине, мм;
б) расчетная высота неровности поверхности Rp образуется вершиной резца, у которой отсутствует радиус закругления rв
(рис. 3.2, б):
R= S0 sin φ sin φ1 .
рsin(φ+φ1)
а
б
Рис. 3.2. Схема образования расчетной величины шероховатости
Аналогичные формулы могут быть получены для любых случаев образования расчетной высоты неровности поверхности. При некоторых условиях обработки фактическая шероховатость поверхности определяется ее расчетным значением, а влияние других факторов незначительно.
На искажение расчетной высоты неровности поверхности наиболее сильно влияет пластическая деформация. При обработке материалов, которые не дают нароста, это влияние на высоту шероховатости объясняется главным образом распространением волны деформации в сторону соседнего следа, а при обработке мате-
38
риалов, дающих нарост, кроме того, еще и действием вершины нароста, благодаря чему образуются задиры материала на поверхности среза.
Влияние упругих деформаций на параметр шероховатости поверхности является следствием притупления лезвия любого инструмента. При взаимном перемещении резца и обрабатываемой поверхности наличие скругления на лезвии вызывает упругое деформирование материала около режущей кромки. Минуя ее, материал заготовки приподнимается и занимает прежнее положение. Вследствие того, что конфигурация неровности довольно сложна, упругое восстановление материала может происходить в разной степени на различных участках обработанной поверхности. Вершина может упруго восстанавливаться, больше или меньше, чем впадина, в результате чего происходят искажения высоты неровности.
Обрабатываемая поверхность формируется режущим инструментом, поэтому неровности лезвия копируются на ней. При определенных условиях этот фактор может оказаться определяющим при формировании шероховатости обработанной поверхности.
При выборе или проектировании режущего инструмента, при установлении режимов резания, выборе состава смазочно-охлаж- дающей жидкости и техники ее подвода в рабочую зону необходимо стремиться к рациональному отводу стружки, так как в противном случае нельзя исключить ее отрицательное воздействие на формирование шероховатости обработанной поверхности.
Деформации и колебательные движения в системе «станок– приспособление–инструмент–заготовка» изменяют расчетную высоту неровности, меняя расчетный параметр шероховатости.
Шероховатость поверхности является одной из основных геометрических характеристик качества поверхности деталей и оказывает влияние на эксплуатационные показатели.
Требования к шероховатости поверхности должны устанавливаться с учетом функционального назначения поверхности для обеспечения заданного качества изделий. Требования не включают требований к дефектам поверхности (раковины и пр.), поэтому при контроле шероховатости поверхности влияние дефектов должно быть исключено.
Шероховатость поверхности оценивается по неровностям профиля (чаще всего в нормальном сечении). Для отделения ше-
39