
Технология конструкционных материалов
.pdf
|
|
|
|
|
|
|
|
Таблица2.3 |
|
|
|
|
|
|
|
|
|
|
|
|
|
|
Механические свойства |
|
|
|
|||
Структура (фаза) |
Твердость НВ, |
|
Предел |
|
Поперечное |
|
|||
МПа |
|
прочности при |
|
сужение, % |
|
||||
|
|
|
|
растяжении, |
|
|
|
|
|
|
|
|
|
МПа |
|
|
|
|
|
Феррит |
700 |
900 |
|
190 |
250 |
|
40 |
50 |
|
Цемент |
7500 |
8000 |
|
|
30 |
|
< 1 |
|
|
Перлит |
1900 |
2400 |
|
880 |
900 |
|
9 |
12 |
|
пластинчатый |
|
|
|
|
|
|
|
|
|
Перлит |
1600 |
1900 |
|
650 |
700 |
|
18 |
25 |
|
зернистый |
|
|
|
|
|
|
|
|
|
(0,8 % С) |
|
|
|
|
|
|
|
|
|
Рис. 2.2. Схематическое изображение микроструктурызаэвтектоиднойстали:
феррит и цементит зернистый
Стали, содержащие углерода более 0,7 %, используются, в основном, как инструментальные: высокоуглеродистые (С 1,0 %) стали характеризуются повышенной твердостью, износостойкостью, применяютсядляизготовлениярежущегоинструмента. Сталис меньшимсодержанием углерода обладают наряду с высокой твердостью и прочностью достаточной вязкостью, используются для инструмента, подвергающегося ударам.
Для проведения микроанализа используются специальные образцы, называемые микрошлифами. Приготовление микрошлифа состоит в вырезании образца, шлифовке и полировке до зеркального блеска его поверхности, выбраннойдляисследования. Шлифовкупроводятнашлифовальной бумаге с зернами различной крупности при постепенном переходе от шлифовальной бумаги с крупнымзерном к шлифовальнойбумаге с более мелким зерном до полного удаления рисок.
н
кгс, кг/см2
н
Рис. 2.3. Механические свойства углеродистой стали в зависимости от содержания углерода
Механическаяпредварительнаяполировкаведетсянавращающихся кругах, обтянутых грубым сукном, на которые периодически наносятся воднаявзвесь окисихрома, алюминияили другихокисловввидемелкодисперсныхпорошков. Окончательнаяполировкаведетсянатонкоммягком сукне (фетре), смачиваемом тонкой взвесью тех же окислов.
Широко применяют электролитическое полирование, при котором образец в качестве анода помещается в электролитическую ванну.
Для выявления микроструктуры образец после полировки подвергают травлению, которое позволяет определить число, размеры, форму, взаимное расположение и количественное соотношение фаз и структурных составляющих. Травление заключается во взаимодействии металла поверхности микрошлифа с химически активными растворами кислот, щелочей, солейвспиртеиливводев зависимостиотсвойствистроения исследуемого металла.
Впроцессе травления образуются микрогальванические пары,
иструктурысболееотрицательнымэлектроднымпотенциаломбудутигратьвнихрольанодаирастворяться. Болееинтенсивно, чемсамозерно, протравляются границы зерен металла, которые обогащены различны-
20 |
21 |
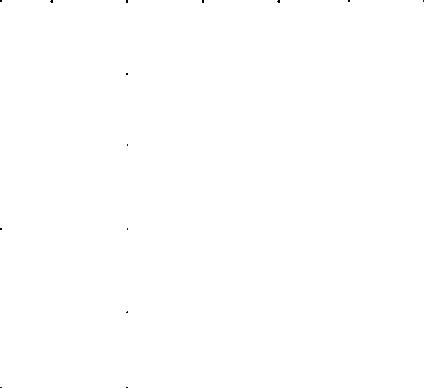
мипримесями, чтоспособствуетобразованиюмикрогальваническихэлементов. В результате на границах зерен после травления образуются углубления, которые под микроскопом дают больше рассеянных лучей
ивыглядят более темными, поэтому структура перлита под микроскопом имеет вид темных и светлых полос, так как феррит растворяется быстрее, чем цементит.
Практическая часть работы состоит в изучении микроструктуры типичных железоуглеродистых сплавов: технического железа, доэвтектоидной, эвтектоидной и заэвтектоидной сталей. Студенты выполняют эту работу под руководством преподавателя и учебного мастера
иобязаны сделать следующее:
1.Зарисовать (схематично) микроструктуру образцов коллекции, указав увеличение микроскопа, структурные составляющие, фазовые составляющие. Результаты представить в виде табл. 2.4.
|
|
|
|
|
Таблица2.4 |
|
|
|
|
|
|
|
|
|
Техниче- |
Содержа- |
Структур- |
Фазовые |
Зарисовка |
|
№ об- |
ское назва- |
ние угле- |
ные со- |
состав- |
микро- |
|
разца |
ние сплава |
рода |
ставляю- |
ляющие |
структур |
|
|
|
в сплаве |
щие |
|
|
|
1 |
|
|
|
|
|
|
|
|
|
|
|
|
|
2 |
|
|
|
|
|
|
|
|
|
|
|
|
|
3 |
|
|
|
|
|
|
|
|
|
|
|
|
|
4 |
|
|
|
|
|
|
|
|
|
|
|
|
|
2.Определить содержание углерода в образцах (по указанию преподавателя) наоснованииколичественнойоценкиотносительногообъема структурных составляющих. Результаты занести в табл. 2.4.
3.По указанию преподавателя расшифровать марку строительной стали, указав при этом ее качество, способ раскисления, примерное содержание химических элементов и область рационального применения.
Содержание отчета
1.Цель и задачи работы.
2.Результаты исследования микроструктуры заданных образцов.
3.Расшифровка указанной марки строительной стали с указанием области ее практического применения.
4.Выводы по работе (зависимость микроструктуры и фазового состояния от состава углеродистой стали: какие фазы образуют сетку по границамзерен; что сильнее влияет на свойства стали – фазовое состояние или ее микроструктура).
22 |
23 |
Лабораторная работа № 3
МИКРОСТРУКТУРНЫЙ АНАЛИЗ СТРОЕНИЯ ЧУГУНОВ
Цель лабораторной работы – ознакомиться с микроструктурой и свойствами чугунов.
При выполнении лабораторной работы необходимо:
1)изучить теоретические вопросы получения белых, серых, ковких и высокопрочных чугунов;
2)по диаграмме железо–цементит изучить строение белых чугунов, а по диаграмме железо–графит – строение серых чугунов, обратив особое внимание на структуру металлической основы;
3)с помощью металлографического микроскопа изучить структуру различных чугунов, используя коллекцию микрошлифов.
Оснащение участка лабораторной работы:
оборудование– металлографическиемикроскопыМИМ-6, МИМ-7, ММУ-3, МЕТАМ РВ-22;
материалы – коллекция микрошлифов белых, серых, ковких
ивысокопрочных чугунов;
плакаты– диаграммасостоянияжелезо–цементитижелезо–гра-
фит;
фотоальбом – микроструктура белых, серых, ковких и высокопрочных чугунов.
Микроструктурный анализ строения чугунов
Чугунами называютсяжелезоуглеродистыесплавы с содержанием углерода более 2,14 %. Структура чугуна и его основные свойства зависяткакотхимическогосостава, такиоттехнологическогопроцессапроизводства и режима термической обработки. Углерод в чугуне может находиться в виде карбида железа Fe3С или графита, или одновременно в виде Fe3С (цементита) и графита. Графит в чугуне может образоваться врезультатераспадацементита. Этотпроцессназываетсяграфитизацией.
В зависимости от состояния углерода различают следующие чугуны:
1.Белые чугуны, в которых углерод находитсяв связанном состоя-
нииввидекарбида железаFe3С(цементита). Своеназвание ониполучили по виду чугуна, который имеет светлый (белый) цвет. Структура бе-
лых чугунов точно соответствует метастабильной диаграмме Fe–Fe3C. По структуре белые чугуны делятся на три типа:
а) доэвтектические – состоят из перлита, вторичного цементита и ледебурита;
б) эвтектические – состоят из ледебурита; в) заэвтектические – состоят из первичного цементита и ледебу-
рита.
Белый чугун из-за присутствия в нем большого количества цементитаобладаетвысокойтвердостью, хрупкостьюипрактическинеподдается обработке резанием. Высокая твердость обусловливает хорошую сопротивляемость износу, особенно абразивному, и поэтому белый чугун применяется для звёздочек при очистке литья, шаров для мельниц и т. д. Белый чугун используется при переделе в сталь ипри отливке деталей с последующим отжигом на ковкий чугун.
2.Серые чугуны, в которых углерод в значительной степени или полностьюнаходитсявсвободномсостояниивформепластинчатогографита и поэтому в изломе имеет тёмно-серый цвет.
Образование стабильной фазы графита в чугуне может происходить в результате непосредственного выделения его из жидкого раствора или вследствие распада предварительнообразовавшегося цементита. Процесс образования в чугуне графита называется графитизацией.
В стабильной системе Fe–С (штриховые линии на рис. 1.2 в лабо-
раторной работе № 1) при температурах, соответствующих линии D
, кристаллизуетсяпервичныйграфит. ПолинииE
C
F
образуетсяграфитнаяэвтектика(аустенит+ графит). ПолинииЕ
S
выделяетсявторичный графит, а по линии P
K
образуется эвтектоид, состоящий из феррита
играфита. Основная масса графита в серых чугунах формируется в период кристаллизации из жидкой фазы. В отличие от белых чугунов, которые получают при ускоренном охлаждении сплава, серые чугуны получают при медленном охлаждении.
Кремний способствует процессу графитизации. Марганец, напротив, замедляетпроцессграфитизации, способствуяотбелучугуна. Изменяя, с одной стороны, содержание в чугуне углерода и кремния, а с другой – скорость охлаждения, можно получить различную структуру металлической основы чугуна.
24 |
25 |
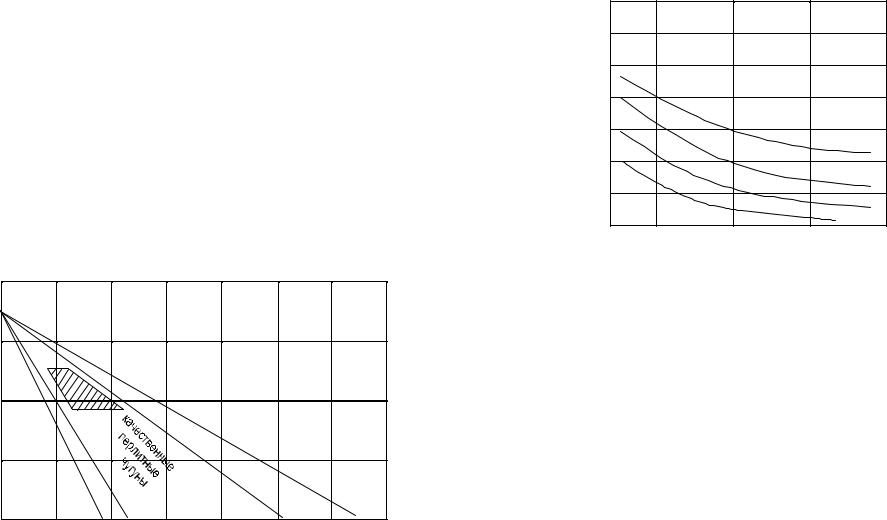
Структурная диаграмма для чугунов, показывающая, какой должна быть структурав отливкес толщинойстенки 50 мм, взависимости от содержаниявчугунекремнияиуглеродаприведенанарис. 3.1. Чембольше в чугуне углерода, темменьше требуется кремния для получения заданной структуры. При данном содержании углерода и кремния графитизацияпротекаеттемполнее, чеммедленнееохлаждение(рис. 3.2). Скорость охлаждения удобно характеризовать толщиной стенки отливки. Чемтоньшеотливка, тембыстрееохлаждениеивменьшейстепенипротекаетграфитизация.
Построениюметаллическойосновывзависимостиотполнотыраспада цементита различают ферритный, ферритно-перлитный и перлитный серые чугуны.
Серый ферритный чугунполучаетсяпри полном распаде всегоцементита. Структура чугуна состоит из феррита и графита. Этот чугун применяется для деталей, испытывающих небольшие нагрузки при работе: строительныхколонн, фундаментных плит, литых деталеймашин.
|
5 |
|
|
|
|
|
|
|
% |
|
|
|
|
|
|
|
|
углерода, |
4 |
|
|
|
|
|
|
|
Содержание |
3 |
|
|
|
|
|
|
|
|
2 |
|
II |
|
|
|
|
|
|
|
|
|
|
|
|
|
|
|
|
|
I |
|
III |
IV |
|
V |
|
1 |
|
|
|
|
|
|
|
|
0 |
1 |
2 |
3 |
4 |
5 |
6 |
7 |
|
|
|
|
Содержаниекремния, % |
|
|
|
Рис. 3.1. Влияние углерода и кремния на структуру чугуна:
I – белые чугуны; II – половинчатые чугуны; III – перлитные серые чугуны; IV – ферритно-перлитные серые чугуны; V – ферритные серые чугуны
26
(C + Si), %
8,5 |
|
|
|
|
|
7,5 |
|
|
|
|
|
6,5 |
|
|
|
|
|
5,5 |
|
|
|
|
|
4,5 |
|
|
V |
|
|
|
|
|
|
|
|
3,5 |
|
|
IV |
|
|
|
|
III |
|
|
|
2,5 |
|
II |
|
|
|
|
|
|
|
||
|
I |
|
|
|
|
|
|
|
|
|
|
0 |
20 |
|
50 |
80 |
110 |
|
|
Толщинаотливки, мм |
|
|
Рис. 3.2. Влияние скорости охлаждения (толщины отливки) и суммы (C + Si) на структуру чугуна:
I – белые чугуны; II – половинчатые чугуны; III – перлитные серые чугуны; IV – ферритно-перлитные серые чугуны; V – ферритные серые чугуны
Серый ферритно-перлитный чугун характеризуется меньшей сте-
пенью графитизации, поскольку ей подвергается цементит, входящий в состав ледебурита, вторичный цементит и частично цементит, входящийвсоставперлита. Приэтомраспавшийсяцементитобразуетферрит
играфит, а нераспавшийся цементит сохраняется в перлите. Структура ферритно-перлитная, с графитом. Ферритно-перлитный серый чугун применяетсядлялитыхдеталеймашин, станков, автомобилей, арматуры
идругих деталей, не несущих ударных нагрузок.
Серый перлитный чугунобразуется, когда графитизации подвергается полностью цементит, входящий в состав ледебурита, и вторичный цементит. Структура перлитного чугуна состоит из перлита и графита. Перлитныйсерыйчугунприменяетсядляотливкистанинымощныхстанкови механизмов, поршней, цилиндров, деталей, работающихна износ, и т. д. Свойства серого чугуна зависят от структуры металлической основы и от формы, размеров и количества графитных включений.
27
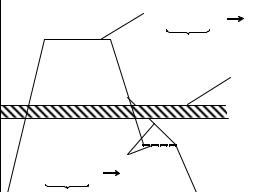
Чем мельче графитные пластинки и чем больше они изолированы друг от друга, тем выше прочностные свойства чугуна при одной и той же металлическойоснове. Такаяболееблагоприятнаяструктураможетбыть получена модифицированием, т. е. введением в жидкий чугун небольших количеств модификаторов (ферросилиция, силикокальция). Чемменьшевметаллическойосновеферрита, темвышепрочностьчугуна.
Серый чугун обладает высокими литейными свойствами, хорошо обрабатывается, менее хрупок, чем белый; ему присущи хорошие антифрикционные свойства.
3. Ковкиечугуныполучаютпутёмотжигаотливокизбелогочугуна (рис. 3.3). В ковком чугуне углерод находится в свободном состоянии в форме хлопьевидного графита (углерод отжига). Такая форма графита обусловливает высокие прочностные и пластические характеристики ковкого чугуна.
|
|
1-ястадияграфитизации |
|
θС |
950–970θC |
(А+ Fe3C) |
А+Г |
, |
|
|
|
Температура |
|
Л |
Эвтектоидныйинтервал |
|
|
||
|
760 θC |
температур |
|
|
|
||
|
|
|
|
|
2-ястадия |
720 θC |
|
|
графитизации |
|
|
|
Ф+ Гр |
|
|
|
(Ф+ Fe3 |
|
|
|
П |
|
Время, ч |
|
Рис. 3.3. Режим отжига белого чугуна на ковкий |
C Отжигпроводитсявдвестадии. Первоначальноотливки(чащеупакованные в ящикис песком) выдерживаютпри температуре 950–970 °С. В этот период протекаетпервая стадия графитизации – распад цементита, входящего в состав ледебурита (А + Ц). В результате распада цементита образуется хлопьевидный графит (углерод отжига). Затем отливки охлаждаются до температур, соответствующих эвтектоидному превращению(РSК). Приохлаждениипроисходитвыделениеиз аустенита вторичного цементита, его распад и в итоге – рост графитных включений. При достижении эвтектоидного интервала температур охлаждение рез-
28
козамедляютилидаютдлительнуювыдержкупритемпературенесколько ниже. В этот период протекает вторая стадия графитизации – распад аустенитасобразованиемферритно-графитнойсмесиилираспадцемен- тита, входящегов перлит, с образованием феррита играфита в процессе выдержки ниже эвтектоидной температуры. После окончания второй стадии графитизации структура чугуна состоит из феррита и хлопьевидногографита. Есливрайонеперлитногопревращенияотливкиохлаждать несколько быстрее, то наряду с ферритом в его структуре будут присутствоватьзернаперлитавбольшемилименьшемколичестве. Регулируя скорость охлаждения, можно получить ковкий чугун, структура которого будетсостоять только из перлита и хлопьевидного графита. Термин «ковкий чугун» является условным, поскольку изделия из него, так же как и излюбого другогочугуна, изготавливают нековкой, апутем литья.
Составковкого чугунавыдерживаетсяв довольно узких пределах: 2,2...3,0 % С; 0,7...1,5 % Si; 0,2...0,6 % Mn; 0,2 % P и 0,1 % S. Невысокое содержание углерода в ковком чугуне необходимо для получения высоких прочностных характеристик и пластичности, а также чтобы избежать выделения пластинчатого графита при охлаждении отливок в металлической форме. Толщина сечения отливки не должна превышать 40...50 мм впроцессе охлажденияих в форме. При большем размере отливок в сердцевине образуется пластинчатый графит, и чугун становится непригодным для отжига.
Отливки из ковкого чугуна применяют для деталей, работающих при ударных и вибрационных нагрузках. Например, из ферритного ковкого чугуна изготавливают картеры редукторов, задний мост, ступицы и т. д. Перлитный ковкий чугун обладает высокой прочностью, умереннойпластичностьюихорошимиантифрикционнымисвойствами. Изнего изготавливают вилки карданных валов, звенья и ролики цепей конвейера, муфты, тормозные колодки и т. д.
4.Высокопрочные чугуны имеют шаровидную форму графита.
Вэтихчугунахуглеродвзначительнойстепениилиполностьюнаходится в свободном состоянии в вида графита шаровидной формы. Возможность получения отливок из чугуна с графитом шаровидной формы в литой структуре была установлена сравнительно недавно. Исследованиями выявлена возможность получения чугуна с шаровидным графитом путём присадок не только магния и церия, но и таких элементов, каклитий, кальций, барий, теллуридр. Установленатакжевозможность получениячугуназасчетдобавкиазотапутёмдлительнойвыдержкижид-
29
)

кого металла при высоких температурах, а также путём повышенного перегрева и выплавки в вакууме.
Однако перечисленные добавки и различные способы получения чугуна с шаровидным графитом без обработки магнием не нашли промышленного применения. Магний вводится либо в чистом виде в автоклавных установках и герметизированных ковшах, либо в виде магниевыхсплавов. Магнийявляетсяхорошимграфитизаторомиспособствует удалению серы.
Микроструктура высокопрочного чугуна с шаровидным графитом и, следовательно, его механические свойства могут быть различными в зависимости от химического состава, скорости охлаждения отливок и режима термической обработки. Изменяя скорость охлаждения, можно получить ферритную, ферритно-перлитную и перлитную структуру металлическойосновычугунасшаровидным графитом. Следовательно, структурасерого, ковкогоивысокопрочногочугунаотличаетсяотструктуры стали только наличием свободного графита.
Сочетание высоких физико-механических и технологических свойств позволяет эффективно использовать магниевый чугун взамен обычного серого, ковкогочугуна, литойикованой стали, а такжевзамен некоторых цветных сплавов на основе меди во многих отраслях машиностроенияистроительства(например, прокатныевалки, кузнечно-прес- совое и прокатноеоборудование, изложницы для разливки стали, штампы различного назначения, коленчатые валы, поршневые кольца, картеры заднего моста, кронштейны, подшипники качения, детали тепловозов, подъемно-транспортных сооружений и т. д.).
Содержание отчета
1.Цель и задачи работы.
2.Изображениедиаграммыжелезо–графит, определениеосновных линийдлядиаграммы, атакжефаз(аустенит, феррит, цементит) иструктурных составляющих.
3.Краткиесведенияизтеории, касающиесяусловийполученияразличных чугунов.
4.Структурныедиаграммыдлячугунов, схемаотжигабелогочугуна на ковкий, схематические зарисовки микроструктур рассмотренных чугуноввнетравленномсостоянииипослетравлениясуказаниемструктурных составляющих.
5.Выводы по работе.
Лабораторная работа № 4
СТРУКТУРА И СВОЙСТВА МЕТАЛЛА СВАРНОГО ШВА И ОКОЛОШОВНОЙ ЗОНЫ
Цель лабораторной работы – изучение структуры и механических свойств сварных соединений, выполненных сваркой плавлением и давлением.
При выполнении лабораторной работы необходимо:
1)изучить особенностиобразованияструктурыметаллашваиоколошовной зоны в условиях сварки плавлением и давлением;
2)произвестисравнительныйанализизмененийструктурыисвойств сварныхсоединений, полученныхсваркойплавлениемидавлением, дать оценку их качества.
Оборудование участка лабораторной работы:
оборудование– металлографическиемикроскопыМИМ-6, МИМ-7, приборы для измерения твердости и микротвердости металла Роквелла
иПМТ-3;
материалы – коллекция шлифов, приготовленных из образцов, сваренных различными способами, реактивы;
плакаты – термокинетическая диаграмма распада аустенита малоуглеродистойстали, микрофотографииструктурстроительныхсталей
справочная литература – справочники, ГОСТы.
Всварномсоединении, выполненномсваркойплавлением, обычно выделяют четыре характерные зоны (рис. 4.1): металл шва, участок неполного расплавления, зону термического влияния и основной металл, не подвергшийся термическому воздействию.
Разделениесварногосоединения наотдельныезонывызванотем, что структура, а иногда и свойства металла шва и околошовной зоны после сварки отличаются от свариваемого металла в исходном состоянии.
30 |
31 |

4 |
3 |
2 |
1 |
2 |
3 |
4 |
|
Рис. 4.1. Строение стыкового сварного соединения:
1 – металл шва; 2 – зона сплавления; 3 – зона термического влияния; 4 – основной металл
1. Особенности структурообразования металла шва при сварке плавлением
При сварке плавлением под воздействием источника теплоты расплавляются кромки основного (свариваемого) металла и электродный металл, подаваемый в сварочную ванну, а также покрытие или флюс. Плавление происходит в зоне сварки – плавильном пространстве, которое перемещается вместе с источником теплоты. Плавильное пространство, или сварочная ванна, условно может быть разделено на две части: головнуюихвостовую. Вголовнойчастипроисходитплавление, авхвостовой – кристаллизация металла и формирование шва.
В отличие от кристаллизации слитка для кристаллизации металла сварочной ванны характерны следующие условия:
незначительный объем расплавленного металла;
быстрыйлокальный нагревметалла источникомтеплоты и быстрое его охлаждение;
наличие подвижного температурного поля, создаваемого источникомтеплоты, вследствиечегосредняяскоростькристаллизациивпервом приближении равна скорости сварки.
Посравнениюс основнымметалломсварнойшовимееттипичную структуру литого металла, быстро затвердевшего в условиях интенсивного отвода теплоты. Литой металл, как правило, уступает прокатному иликованомупосвоимпластическимивязкимсвойствам, таккак имеет болеекрупнозернистуюструктуру. Однаковотличиеотслитковсварной шов обычно содержит меньше N2, S, Р и С, имеет меньшие зональную и внутрикристаллическуюликвации. Крометого, из-заособенностей первичнойкристаллизацииметаллшва имеетболеемелкозернистуюструк-
туру. Вбольшинствеслучаевсварныешвыизмалоуглеродистойинизколегированной сталей обладают высокими механическими свойствами даже без дополнительной термической обработки. Микроструктура металла шва зависит, главным образом, от условий первичной кристаллизации, которая во многом определяет его свойства.
Переходметалла сварочной ванны из жидкого состоянияв твердое называетсяпервичнойкристаллизацией. Процессзатвердеванияпредставляетсобойросткристалловврезультатеприсоединениякихповерхности атомов из окружающего расплава.
Для большинства сварных швов характерна столбчатая структура. Рост столбчатых кристаллов в сварочной ванне начинается от частично оплавленныхзереносновногометалла. Наних, какнасвоеобразнойподкладке, начинают свой рост первичные кристаллы, количество которых ограничено. Кристаллы развиваются нормально к поверхности охлаждения, внаправлении, обратномотводутепла, – вглубьжидкогометалла ванны. В результате они приобретают столбчатую форму (рис. 4.2).
Металл шва
Основной металл
Рис. 4.2. Схема роста кристаллов от границы сплавления в сварочной ванне
Размеры столбчатых кристаллов зависят также от способа и режимов сварки. Снижение температуры ванны и длительности пребывания металла в жидком состоянии способствует образованию крупных кристаллов.
Ростстолбчатыхкристалловспособствуетудалениюизрасплавленногометаллагазовишлаковыхвключений. Посколькутемпературакри-
32 |
33 |
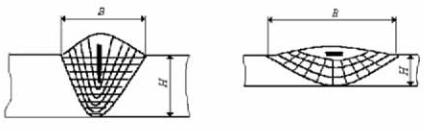
сталлизации зависит от чистоты металла, то в первую очередь затвердевает менее загрязненный примесями металл. В процессе затвердевания сварных швов перед фронтом растущих кристаллов маточный раствор непрерывнообогащаетсяпримесями. Впоследнюю очередьзатвердевает средняя часть шва, в которой сосредоточивается максимальное количество примесей. Химическая неоднородность, называемая ликвацией, снижает механические свойства металла шва, так как ослабляет связь междукристаллами и является одной изпричин возникновения горячих (межкристаллизационных) трещин. Ликвация зависит от формы шва. Вузкомшвемаксимальноеколичествопримесейконцентрируетсявсреднейчасти(рис. 4.3, а), авшироком– вверхнейчасти(рис. 4.3, б). Вследствие этого влияние примесей в широком шве менее опасно.
а |
б |
Рис. 4.3. Влияние формы шва на химическую неоднородность (ликвацию) металла:
а – узкий шов; б – широкий шов
Присваркесплавовнаосновежелезакристаллыимеютаустенитную структуру при первичной кристаллизации. В процессе дальнейшего ох- лажденияуэтихсплавовпроисходяталлотропическиепревращения-же- леза в
-железо с появлением новых образований в пределах первичного зерна аустенита. Этот процесс называется вторичной кристаллизацией, а возникающая в результате структура – вторичнойструктурой.
Похимическомусоставуметаллшвапредставляетсобойнечтосреднее между основным и электродным металлом (с учетом возможного выгорания легирующих элементов, окисления и азотирования за счет окружающей среды).
Участок неполного расплавления представляет собой узкую полоску металла, в которой он в процессе сварки находится в твердожидкомсостоянии. Завремяконтактажидкойитвердойфазвнемпротекают
диффузионные процессы и развивается химическая неоднородность, а структура металла представляет собой иглообразное расположение структурных составляющих. На этом участке, представляющем собой тонкуюпереходнуюполоскуотметаллашвакосновномуметаллу, ипроисходит собственно сварка, т. е. формирование кристаллов шва на частично оплавленных зернах основного металла.
Свойства этого участка и металла шва во многих случаях оказывают решающее влияние на работоспособность сварного соединения, так как здесь часто образуются трещины, ножевая коррозия, хрупкие разрушения и т. п. Ширина участка неполного расплавления невелика и для дуговой сварки составляет примерно 0,1…0,5 мм.
Далее следует околошовная зона, называемая зоной термического влияния.
2. Формирование структуры металла в зоне термического влияния сварных соединений
Зона термического влияния (ЗТВ) является обязательным спутником сварного шва при всех способах сварки плавлением и давлением, кроме холодной сварки. Эта зона охватывает основной металл, не расплавляющийсявпроцессе сваркиисохраняющий неизменным свой химический состав, но изменивший свою структуру и механические свойства вследствиенагреваиохлаждения(термообработки) впроцессесварки.
Прочность сварного соединения и его эксплуатационные свойства вомногомзависятотструктурныхизменений, которыепроисходятвЗТВ. Строение и размеры ЗТВ зависят от химического состава и теплофизических свойств свариваемого металла, мощности источника теплоты, степени его концентрированности, скорости движения и других факторов. Ширина ЗТВ меняется от 1…3 мм при ручной дуговой сварке до 20 мм и более – при электрошлаковой сварке.
Термический цикл любой точки металла сварного соединения характеризуется максимальной температурой нагрева, длительностью нагрева до определенной температуры и скоростью охлаждения. Для ЗТВ характерно неравномерное распределение максимальных температур нагрева (рис. 4.4).
Результат теплового воздействия на металл в ЗТВ зависит от его отношенияктермообработке. Взависимостиотспособаипогоннойэнергии сварки возможны два предельных случая:
34 |
35 |
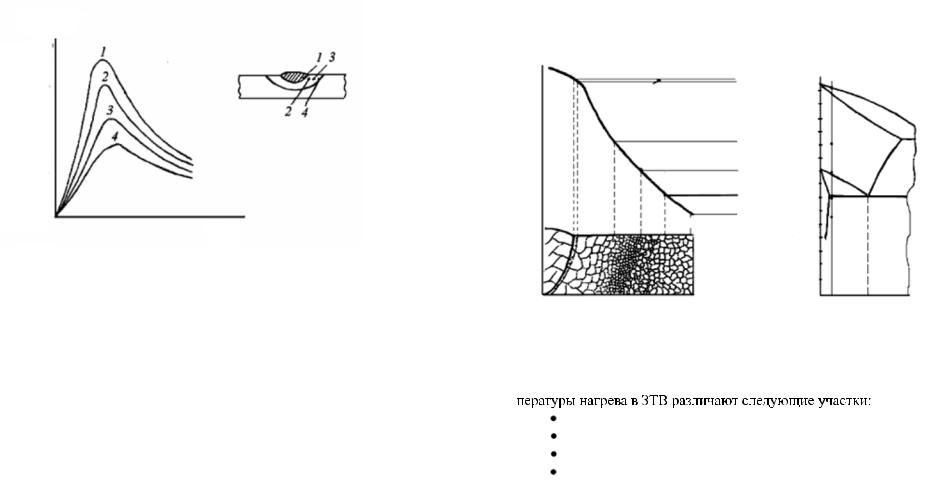
1)закалка – при быстром охлаждении – с образованием твердых и хрупких структур и возникающих при этом значительных по величине напряжений;
2)перегрев – при медленном охлаждении – характеризующийся чрезмерным ростом зерна и снижением пластических и вязких свойств металла.
t, оС
1600
1400
1200
1000
800
600
400
200
τ, с
Рис. 4.4. Термический цикл при сварке плавлением: 1, 2, 3, 4 – точки, в которыхизмерялась температура
Оценить общий характер возможных превращений, протекающих вЗТВприсваркенизкоуглеродистыхсталей, можноподиаграмме желе- зо–цементит, априразличныхскоростяхохлаждения– пользуясьтермокинетическимидиаграммамираспадааустенита, которыепостроеныдля большинства марок углеродистых и легированных сталей. Скорость охлаждения обычно оценивается в интервале температур наименьшей устойчивости аустенита (500…550 °С). Прималых скоростяхохлаждения, соответствующих электрошлаковой и ванной сварке, превращение аустенита приводит к формированию структуры, состоящей из феррита и перлита. При средних скоростях охлаждения (автоматическая сварка подфлюсом) в зависимости от марки сталиобразуютсяперлитибейнит илибейнитимартенситснебольшимколичествомферрита. Прискоростиохлаждениявышекритическойобразуетсятолькомартенсит. Мартенситное превращение сопровождается увеличением объема стали и воз-
никновением больших напряжений, которые могут вызвать разрушение металла. Вподобныхслучаях приходитсяприниматьспециальныемеры к улучшению структуры металла ЗТВ и предотвращению образования мартенсита. Эти меры сводятся к изменению теплового режима в процессе сварки, выбору рациональной формы разделки кромок под сварку и последующей термообработке.
На рис. 4.5 показана схема структур, образующихся в зоне термического влияния при сварке стыкового соединенияиз малоуглеродистой стали за один проход.
Металл шва |
t, оС |
|
|
Участок неполного |
1500 |
расплавления |
1400 |
|
1300 |
Участок перегрева |
1200 |
|
1100 |
Участок нормализации |
1000 |
Участок неполной |
900 |
перекристаллизации |
800 |
Участок |
700 |
600 |
рекристаллизации 500
400
300
200
100
Рис. 4.5. Строение ЗТВ при сварке низкоуглеродистой стали
Над сечением шва показана кривая температур, а рядом – часть диаграммыжелезо–цементит втом же масштабе. В зависимости от тем-
перегрева; нормализации;
неполной перекристаллизации; рекристаллизации.
Участок перегрева. Он включает металл, нагретый до температуры выше 1100 °С, т. е. несколько ниже температуры плавления. Металл на этом участке в процессе нагрева претерпевает аллотропические превращения (-железа в
-железо), сопровождающиеся ростом аустенит-
36 |
37 |
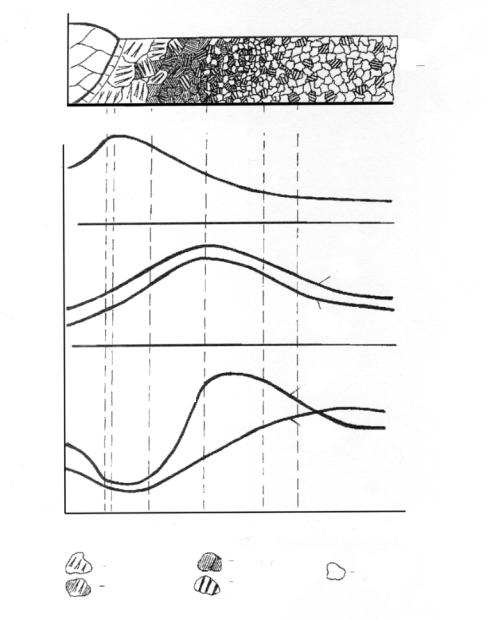
ного зерна. В тех случаях, когда перегрев сочетается с последующим быстрым охлаждением (закалка), металл на этом участке после сварки обладаетпониженной пластичностью и прочностью по сравнению с основным металлом. Участок особенно опасен для закаливающихся сталей, поэтомувыборрациональнойтехнологиисваркисводитсявпервую очередь к обеспечению наименьшего ухудшения свойств на этом участке ЗТВ.
Участок нормализации (перекристаллизации). Этот участок ох-
ватываетметалл, нагретыйдотемпературы, немногопревышающейтемпературуаллотропическихпревращений(900…1050 °С). Происходящий здесь процесс перекристаллизации при нагреве и охлаждении приводит к значительному измельчениюзерен металла. Структура металла становится более мелкозернистой по сравнению с исходной. Механические свойства металла этого участка обычно лучше, чем основного металла.
Участок неполной перекристаллизации. Он включает металл,
нагретый до температур 700…850 °С. При этих температурах происходитчастичнаяперекристаллизация, т. е. частьферритаостаетсявисходномсостоянии, другая– образуетаустенит. Припоследующем охлаждении и распаде аустенита образуется мелкозернистая структура, поэтому здесь, нарядусзернамиосновногометалла, неизменившимисявпроцессе сварки, присутствуютзерна, образовавшиеся при перекристаллизации.
Участокрекристаллизации(старения). Оннаблюдаетсяприсвар-
кесталей, предварительноподвергшихсяпластическойдеформации(ковке, прокатке). Температурный интервал участка 450…650 °С. На этом участке ЗТВ происходят сращивание (укрупнение) раздробленных при нагартовке зереносновного металла и некоторое его разупрочнение посравнениюсисходнымсостоянием. Присваркеизделийизлитьярекристаллизацииненаблюдается. Дляметалловисплавов, склонныхкстарению, необходимоучитыватьнекотороеснижениепластичностинаэтом участке.
Об изменении прочностных и в определенной степени пластических свойств в различных участках металла шва и ЗТВ можно судить по изменению твердости (рис. 4.6).
Повышение твердости обычно связано с повышением прочности
иснижением пластичности. Характер распределения твердости в ЗТВ может быть различным. Он определяется химическим составом стали
ирежимомсварки. Обычновсварныхизделияхнедопускаетсятвердость в зоне сварки более НВ = 300 МПа.
38
HV,
кгс/мм2
ςв; ς0,2
кгс/мм2
Γ
а
ςв
б
ς0,2
в
Γ
Расстояние от оси шва, мм |
|
|
||
|
|
|
|
|
– мартенсит |
|
– троостит |
|
– феррит |
– бейнит |
|
– сорбит |
|
|
|
|
|
||
|
|
перлит |
|
|
|
|
|
|
|
Рис. 4.6. Изменение механических свойств в металле шва и околошовной зоне: а – твердость; б – прочность; в – пластичность
39