
Ашихмин Размерный анализ технологических процессов 2010
.pdf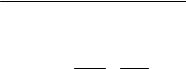
Группы стали определяются по процентному содержанию угле-
рода: М1 – до 0,35 %; М2 – (0,35–0,65) %; М3 – 0,65 % и более. В
нашем случае для стали 30 группа стали будет М1.
Степень сложности определяют либо отношением Vп/Vф, где Vп – объем поковки, Vф – объем элементарной геометрической фигуры, в которую вписывается поковка, либо отношением Мп.р/Мф, где Мп.р – расчетная масса поковки, Мф – масса элементарной геометрической фигуры.
Степеням сложности поковок соответствуют следующие численные значения отношения: С1 – св. 0,63; С2 – св. 0,32 до 0,63; С3 – св. 0,16 до 0,32; С4 – до 0,16. Определяем степень сложности по отношениям масс. Ориентировочно размеры элементарной фигуры находим увеличением в 1,05 раза габаритных размеров детали
(Dmax и H).
Находим массу элементарной фигуры:
Мф Vф Rф2 Hф (1,05 Rmax)2 1,05 H
3,14 (1,05 60)2 (1,05 75) 7,8 8,2 кг. 106
Определяем степень сложности:
СМп.р. 4,23 0,51.
Мф 8,2
Это соответствует С2 (диапазон 0,32...0,63).
По диаграмме (табл. 1.1) определяем исходный индекс поковки. В первой колонке таблицы находим интервал, в который попадает расчетная масса поковки Мп.р = 4,23 кг (3,2–5,6). По горизонтали перемещаемся в следующую колонку до линии М1. Поскольку материал поковки соответствует группе М1, продолжаем движение по горизонтали в следующую колонку до линии С1. Затем по наклонной линии спускаемся до вертикали С2 и снова по горизонтали перемещаемся в колонку «Класс точности» до линии Т4. Далее спуск по наклонной линии до вертикали Т5 и по горизонтали выходим на индекс 14.
11

Таблица 1.1
Исходный индекс поковки
Примечание. Исходный индекс поковки должен быть указан на чертеже поковки.
12
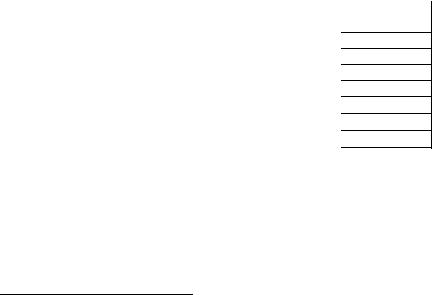
Определение припусков на механическую обработку и допусков на размеры исходной заготовки [1, 3]. Припуски и допуски стальных штампованных поковок приняты по ГОСТ 7505-89. В табл. 1.2 припуск задан на сторону. Величина его определяется:
1)исходным индексом − 14;
2)размером, связывающим поверхности – из чертежа детали;
3)шероховатостью поверхности готовой детали по чертежу;
4)способом формирования поверхностей, связанных линейным размером. Если поверхности, связанные размером, формируются в разных половинах штампа, то размер выбирается в строке «Толщина детали». Если эти поверхности формируются в одной половине штампа, то размер выбирается в строке «ДЛИНА, ШИ-
РИНА, ДИАМЕТР, ГЛУБИНА и ВЫСОТА детали» таблицы П6 приложения [1]1.
Эти же факторы, кроме третьего, будут определять и величину допуска на размеры поковки.
|
|
|
|
Таблица 1.2 |
|
|
Основные припуски |
|
|
|
|
|
|
Основной |
Поверхность |
Толщина, |
Высота, |
Шероховатость, |
|
|
мм |
диаметр, мм |
Ra, мкм |
припуск, мм |
1 |
75 |
— |
3,2 |
2,5 |
7 |
3,2 |
2,5 |
||
5 |
— |
43 |
12,5 |
1,7 |
7 |
3,2 |
2,5 |
||
2–2 |
— |
120 |
12,5 |
1,9 |
6–6 |
— |
100 |
1,6 |
|
4–4 |
— |
80 |
1,6 |
|
Общий припуск (табл. 1.3) на механическую обработку включает в себя основной и дополнительный припуски. Определение основных припусков отражено в табл. 1.2.
Дополнительные припуски учитывают смещение поковок, изо-
гнутость, отклонение от плоскостности и прямолинейности. Оп-
ределение расчетных размеров исходной заготовки с учетом общих припусков приведено в табл. 1.3.
1 Вработе [1] содержатся данные, необходимые для формирования таблиц 1.2; 1.3; 1.4.
13
Таблица 1.3
Общие припуски и расчетные размеры исходной заготовки
По- |
|
Припуски Z, мм |
Общие припуски, |
|
||
верх- |
Размер, |
|
|
мм |
Расчетный |
|
ность |
мм |
основ- |
дополни- |
на сто- |
на диа- |
размер, мм |
|
|
ной |
тельный |
рону Z0 |
метр 2Z0 |
|
2-2 |
120 |
1,9 |
0,3 |
2,2 |
4,4 |
120+4,4=124,4 |
6-6 |
100 |
2,0 |
0,3 |
2,3 |
4,6 |
100+4,6=104,6 |
4-4 |
80 |
2,0 |
0,3 |
2,3 |
4,6 |
80–4,6=75,4 |
1 |
75 |
2,5 |
0,5 |
3,0 |
— |
75+6=81,0* |
7 |
2,5 |
0,5 |
3,0 |
— |
||
5 |
43 |
1,7 |
0,5 |
2,2 |
— |
43–2,2+3=43,8* |
7 |
2,5 |
0,5 |
3,0 |
— |
*Уточняются по результатам размерного анализа.
Усреднено примем дополнительный припуск для цилиндрических поверхностей 0,3 мм, для торцовых – 0,5 мм. Таблицы для определения дополнительных припусков приведены в ГОСТ 7505 – 89. Размеры исходной заготовки сведены в табл. 1.4.
Таблица 1.4
Допуски, предельные отклонения и размеры исходной заготовки
Расчетный |
Допуск |
ВО, мм |
НО, мм |
Принятый |
размер, мм |
Т, мм |
|
|
размер, мм |
124,4 |
3,2 |
+2,1 |
-1,1 |
124,4−+1,12,1 |
104,6 |
3,2 |
+2,1 |
-1,1 |
104,6−+1,12,1 |
75,4 |
2,8 |
+1,0 |
-1,8 |
75,4−+1,81,0 |
81,0 |
3,2 |
+2,1 |
-1,1 |
81,0−+12,,11 * |
|
|
|
|
|
|
|
|
|
|
43,8 |
2,8 |
+1,8 |
-1,1 |
43,8−+1,11,8 * |
*Уточняются по результатам размерного анализа.
4. Разработка стартового варианта технологического процес-
са. Проектирование единичного технологического процесса (ТП)
14
может быть реализовано либо на основе использования прототипов (аналогов), либо как индивидуальное проектирование.
Рассмотрим случай, когда прототипов нет и необходимо применить индивидуальное проектирование (метод синтеза) [4]. Каждый технологический переход связан со снятием промежуточного припуска, который будет замыкающим звеном соответствующей технологической размерной цепи.
В дальнейшем будем использовать стратегию проектирования «синтез снизу вверх». В этом случае проектирование начинается с формирования плана обработки каждой поверхности.
Этапы обработки, правила их выбора. План обработки по-
верхности. За один технологический переход, как правило, невозможно при обработке исходной заготовки обеспечить параметры поверхности готовой детали. Поэтому необходимо выполнять несколько переходов, формируя промежуточные поверхности обрабатываемой заготовки. Сложились определенные закономерности назначения того или иного количества промежуточных поверхностей и, соответственно, этапов обработки.
Этап обработки – это часть технологического процесса, включающая однородную по характеру и точности обработку различных поверхностей и детали в целом.
Если уточнить эту формулировку, то этап обработки определяется состоянием поверхности после обработки, т.е. сочетанием точности и шероховатости обработанной поверхности. В качестве примера приведем назначение этапов обработки отверстия 20Н7 в сплошном материале. Установление необходимого количества этапов обработки является первым шагом к формированию плана обработки каждой поверхности.
План обработки поверхности – это последовательность методов обработки (или технологических переходов), необходимых для достижения заданного чертежом состояния поверхности.
План обработки отверстия в рассматриваемом примере будет следующий: сверлить, зенкеровать, развернуть предварительно, развернуть окончательно.
С учетом обобщения литературных данных и накопленного опыта можно рекомендовать для назначения пять этапов чисто механической обработки, которые приведены в правой части рис. 1.5.
15
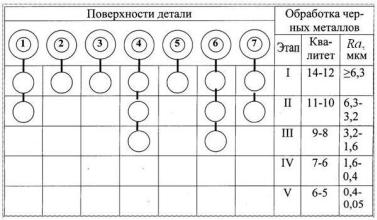
Рис. 1.5. Определение необходимых этапов обработки
Сразу оговоримся, что данные эти усредненные, применительно к среднему (по размерам изделий) машиностроению. В каких-то других конкретных условиях могут быть другие рекомендации по разграничению этапов обработки с точки зрения обеспечиваемого состояния обработанной поверхности. Состояние поверхности будет характеризоваться точностью и шероховатостью обработанной поверхности.
На рис. 1.5 показано назначение необходимых этапов обработки для каждой поверхности заданной детали. Цифрами в двойных кружках в верхней строке обозначены номера поверхностей готовой детали (см. рис. 1.1). Ниже каждого номера поверхности вертикально располагается линейный граф, отражающий план обработки этой поверхности. Самая нижняя вершина каждого линейного графа должна соответствовать состоянию поверхности, которое задано на чертеже детали. Например, для поверхности 6 это будет состояние, соответствующее третьему этапу обработки (8-й квалитет,
Ra = 1,6 мкм).
Таким образом, мы получаем план обработки каждой поверхности с точки зрения количества необходимых этапов, т.е. технологических переходов. Но содержание технологических переходов, т.е. какие методы обработки будут применены на каждом переходе, неизвестно. Поэтому следующим шагом при разработке стартовой
16
структуры технологического процесса будет выбор методов обработки поверхностей.
Выбор методов обработки поверхностей. На каждом этапе выбор методов обработки обусловлен видом поверхности (цилиндр, плоскость и др.), ее положением (наружная или внутренняя) и состоянием поверхности (квалитет, Ra, мкм), достигаемом на этом этапе. Назначение того или иного метода обработки на конкретном этапе обработки зависит от экономической точности, которую обеспечивает метод обработки. Например, при обработке наружных цилиндрических и торцовых поверхностей точение предварительное (черновое) обеспечивает 14–12 квалитеты, а шлифование предварительное – 9–8 квалитеты. В табл. 1.5 для каждого метода обработки приведены лучшие точностные показатели в пределах конкретного этапа.
Таблица 1.5
Назначение плана обработки наружных цилиндрических поверхностей
Методы |
|
|
|
|
|
Этапы обработки |
|
|
|
|
|
||||
обработки |
|
V |
|
IV |
|
III |
|
II |
|
I |
|||||
|
IT |
|
Ra, |
IT |
|
Ra, |
IT |
|
Ra, |
IT |
|
Ra, |
IT |
Ra, |
|
|
|
|
мкм |
|
|
мкм |
|
|
мкм |
|
|
мкм |
|
|
мкм |
Точение одно- |
– |
|
– |
– |
|
– |
– |
|
– |
– |
|
– |
12 |
|
6,3 |
кратное |
|
|
|
|
|
||||||||||
|
|
|
|
|
|
|
|
|
|
|
|
|
|
|
|
Точение предва- |
12 |
|
6,3 |
12 |
|
16,3 |
12 |
|
6,3 |
12 |
|
6,3 |
12 |
|
6,3 |
рительное |
|
|
|
|
|
||||||||||
|
|
|
|
|
|
|
|
|
|
|
|
|
|
|
|
Точение чистовое |
10 |
|
3,2 |
10 |
|
3,2 |
10 |
|
3,2 |
10 |
|
3,2 |
|
|
|
Точение оконча- |
|
|
|
|
|
|
|
|
|
|
|
|
|
|
|
тельное или шли- |
8 |
|
1,6 |
8 |
|
1,6 |
8 |
|
1,6 |
|
|
|
|
|
|
фование предва- |
|
|
|
|
|
|
|
|
|
||||||
|
|
|
|
|
|
|
|
|
|
|
|
|
|
|
|
рительное |
|
|
|
|
|
|
|
|
|
|
|
|
|
|
|
Точение тонкое |
|
|
|
|
|
|
|
|
|
|
|
|
|
|
|
или шлифование |
6 |
|
0,4 |
6 |
|
0,4 |
|
|
|
|
|
|
|
|
|
окончательное |
|
|
|
|
|
|
|
|
|
|
|
|
|
|
|
Шлифование тон- |
5 |
|
0,05 |
|
|
|
|
|
|
|
|
|
|
|
|
кое или притирка |
|
|
|
|
|
|
|
|
|
|
|
|
|
17
При выборе методов обработки необходимо учитывать производственную среду, т.е. возможности имеющегося оборудования. Приведенные данные являются некоторым усреднением таблиц экономической точности обработки.
По табл. 1.5 в соответствии с назначенным этапом окончательной обработки, выбирается метод окончательной обработки поверхности, и сразу же в план обработки поверхности должны быть включены все предшествующие методы обработки. В качестве примера рассмотрим выбор методов обработки наружной цилиндрической поверхности 6 на рис. 1.1. Состояние поверхности в готовой детали характеризуется требованием к точности – 8-й квалитет
итребованием к шероховатости – Ra = 1,6 мкм.
Всоответствии с таблицей этапов обработки (см. рис. 1.5) необходимо предусмотреть три этапа обработки этой поверхности. По табл. 1.5 для окончательного третьего этапа обработки определяем, что завершающим методом обработки может быть точение окончательное второе или шлифование предварительное. Выберем шлифование предварительное (однократное). Далее автоматически мы должны включить в план обработки поверхности 6 два предшествующих метода: точение предварительное (этап I) и точение чистовое (этап II).
Табл. 1.5 можно использовать для назначения методов обработки торцовых поверхностей осесимметричных деталей. Методы обработки внутренних цилиндрических поверхностей, полученных в исходной заготовке, можно назначать в соответствии с рис. 1.6.
При использовании токарно-револьверного станка (например, типа 1Е340П), когда отверстие в детали окончательно формируется на этапе III, возможны следующие наборы методов обработки:
1) ПРС – ЧЗ – Р;
2) ПРС – ЧРС – Р ;
3) ПЗ – ЧЗ – Р;
4) ПЗ – ЧРС – Р.
При обработке отверстий по 7-му квалитету точности дополнительно необходим IV этап обработки, который может быть реализован методом окончательного развертывания после предварительного развертывания на этапе III.
18
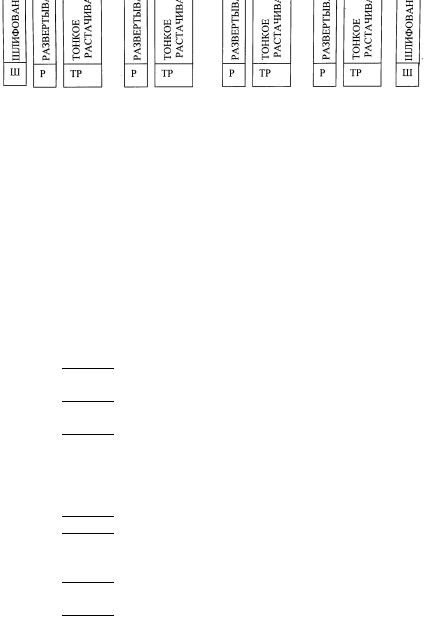
|
Рис. 1.6. Обработка отверстий по 8–9-му квалитету |
|||
|
|
|
|
Таблица 1.6 |
|
Выбор методов обработки и назначение |
|||
|
|
технологических переходов |
||
|
Ква- |
|
|
|
Поверх- |
Ra, |
Этап |
Технологический переход |
|
ность |
литет |
мкм |
|
|
1 |
14 |
3,2 |
I |
Подрезать торец предварительно |
|
14 |
|
II |
Подрезать торец окончательно |
2 |
12,5 |
I |
Точить поверхность |
|
3 |
14 |
― |
I |
Сверлить отверстие |
4 |
8 |
1,6 |
I |
Расточить отверстие предварительно |
|
|
|
II |
Расточить отверстие окончательно |
|
14 |
|
III |
Развернуть отверстие |
5 |
12,5 |
I |
Подрезать торец |
|
6 |
8 |
1,6 |
I |
Точить поверхность предварительно |
|
|
|
II |
Точить поверхность окончательно |
|
14 |
|
III |
Шлифовать поверхность |
7 |
3,2 |
I |
Подрезать торец предварительно |
|
|
|
|
II |
Подрезать торец окончательно |
|
|
|
|
19 |
Наличие планов обработки всех поверхностей позволяет, вопервых, получить представление об общем объеме механической обработки детали и, во-вторых, приступить к формированию технологических операций стартового варианта.
При назначении конкретных методов обработки необходимо учитывать наличие того или иного оборудования в конкретной производственной обстановке.
Для рассматриваемого примера используются токарноревольверный, вертикально-сверлильный и круглошлифовальный станки. Технологические переходы, соответствующие выбранным методам обработки, заносим в табл. 1.6, которая содержит планы обработки всех поверхностей.
Формирование технологических операций. В пределах одной группы станков выбор вида станка (например, токарновинторезного или токарно-револьверного) определяется типом производства или конкретными производственными условиями. Модель станка будет определяться габаритами детали.
При формировании технологических операций стартового варианта технологического процесса необходимо стремиться к максимальной концентрации обработки. При этом обычно решаются и вопросы выбора как установочных, так и настроечных технологических баз.
Под установочными базами будем подразумевать поверхности детали, которые контактируют с установочными элементами приспособления. Работа ведется на настроенном станке, и от установочных баз производится настройка режущего инструмента на выдерживаемый размер. Например, в табл. 1.7 для позиции ПР-I установочной базой является поверхность 7.
Настроечной базой является обработанная ранее поверхность (при этом же установе), от которой настраиваются на размер инструменты для обработки других поверхностей. В табл. 1.7 на позиции ЗР-I установочной базой для обработки поверхности 5 будет поверхность 1. Затем поверхность 5 будет использоваться в качестве настроечной базы для обработки поверхности 7.
В рассматриваемом сквозном примере стартовый вариант технологического процесса будет состоять из трех операций.
20