
А.А. Кречетов Проектирование технологического процесса горячей обработки давлением
.pdf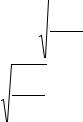
10
выгодно применять квадратный профиль. Круглую по сечению заготовку используют: при гибке с резкими изгибами, приводящей при штамповке из квадратного профиля к образованию зажимов; если на поковке круглый по сечению участок, не подвергающийся штамповке; в случае применения высадочного ручья.
Длину заготовки определяют как
V / |
|
||
lзг = |
зг |
. |
(11) |
|
|||
|
Sзг/ |
|
7.2 Поковки, штампуемые осадкой в торец
Геометрические параметры исходной заготовки для изготовления поковки, штампуемой осадкой в торец, во избежание ее искривления при обработке должны удовлетворять условию [2, гл. 3-4]:
m = |
|
lзг |
= |
lзг |
≤2,8, |
(12) |
|||
|
Dзг |
|
|||||||
|
|
|
Азг |
|
|||||
где m – коэффициент, имеющий значение от 1,5 до 2,8. |
|
||||||||
|
|
Чтобы облегчить обрезку заготовки (обеспечить минимальную |
|||||||
толщину заготовки), принимают m ≈ 2,8 . |
|
||||||||
|
|
Задавшись значением m, можно найти диаметр круглой или сто- |
|||||||
рону квадратной заготовки по формулам |
|
||||||||
Dзг/ |
=1,083 |
V / |
|
(13) |
|||||
зг , |
|||||||||
|
|
|
V / |
m |
|
||||
Aзг/ |
= 3 |
|
|
|
(14) |
||||
|
зг . |
||||||||
|
|
|
|
m |
|
|
|
|
Длину заготовки определяют по формуле (11).
8. Выбор оборудования
8.1 Выбор штамповочного молота
Для выбора штамповочного молота рассчитывают массу падающих частей, необходимую для штамповки данной поковки [2, гл. 3].
Для круглых в плане поковок, штампуемых в открытых штампах, массу падающих частей (кг) паровоздушного молота рассчитывают по формуле
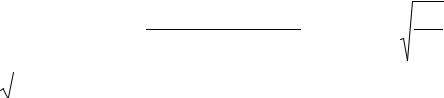
11
|
|
|
|
|
|
|
|
|
|
|
|
|
D |
|
|
|
G0 = 5,6 |
10−4σ( 1 −0,0005Dп ){ 3,75 b + |
п |
(75 +0,001Dп2 )+ |
|||||||||||||
|
||||||||||||||||
|
|
|
|
|
|
|
|
|
|
|
|
|
4 |
|
|
(15) |
|
|
2 |
|
|
|
|
2 |
|
|
|
|
|
2 |
|
||
|
|
|
bDп |
|
|
|
|
}, |
||||||||
b |
|
|
|
|
Dп |
|
|
|
|
2,5(75 +0,001Dп ) |
||||||
+ Dп |
|
|
+ |
|
+ |
|
ln |
1 |
+ |
|
|
|
||||
2 |
|
4 |
50 |
D h |
|
|||||||||||
|
|
|
|
|
|
|
|
|
|
|
|
п 0 |
|
|
|
где Dп – диаметр поковки, мм; σ – предел текучести материала поков-
ки при данной температуре, МПа; b – ширина мостика облойной канавки, мм; h0 – толщина мостика облойной канавки, мм.
При штамповке некруглых в плане поковок в открытых штампах необходимую массу (кг) падающих частей паровоздушного молота находят из выражения
|
|
|
|
−4 |
|
|
|
|
|
|
|
|
|
|
Dпр |
|
2 |
|
|
|
|||
Gm =5,6 10 |
|
|
|
|
|
|
|
|
|
|
+ |
|
|
|
|
|
|
|
|
||||
|
|
|
|
|
|
|
|
|
|
|
|
|
|
|
|
||||||||
|
σ(1 −0,0005Dпр ){3,75 b |
4 |
|
(75 +0,001Dпр)+ |
|
||||||||||||||||||
|
|
|
|
|
|
|
|
|
|
|
|
|
|
|
|
|
|
|
|
|
(16) |
||
b2 |
bDпр |
|
|
Dпр2 |
|
|
|
2,5(75 +0,001Dпр2 |
) |
|
lп |
|
|||||||||||
|
|
|
|
|
|
|
|
|
|
|
|
|
|
|
|
|
|
|
|
|
|
|
|
+ Dпр |
2 |
+ |
|
4 |
|
|
+ |
50 |
ln |
1 + |
D |
h |
|
|
|
|
}1 +0,1 |
b |
, |
|
|||
|
|
|
|
|
|
|
|
|
|
|
пр |
0 |
|
|
|
|
|
ср |
|
||||
где Dпр =1,13 |
|
|
|
– приведенный диаметр поковки, мм; |
Fп – площадь |
||||||||||||||||||
|
Fп |
||||||||||||||||||||||
проекции в плане, мм2; l |
п |
– длина поковки в плане; b = F / l |
п |
– сред- |
|||||||||||||||||||
|
|
|
|
|
|
|
|
|
|
|
|
|
|
|
|
|
|
ср |
п |
|
|
няя ширина поковки в плане, мм.
Массу падающих частей молота простого действия определяют по выражениям (15) или (16) и умножают на переводной коэффициент:
Gп.м = (1,5÷1,8)G0 ( Gm ).
При штамповке в закрытых штампах массу падающих частей находят по формулам (15) или (16), назначая параметры условной облойной канавки для данной поковки, которая имелась бы при штамповке в открытых штампах. Затем получившийся результат уменьшают на
20-25 %.
8.2 Выбор пресса
Для выбора пресса рассчитывают усилие, необходимое для штамповки данной поковки [2, гл. 4].
Усилие при штамповке осаживанием в открытых штампах определяют по формулам:
для круглых и квадратных в плане поковок, а также поковок, приближающимся к ним по форме,

12
|
|
|
|
|
|
|
|
|
|
|
|
|
|
|
|
|
|
|
P =σ |
|
|
|
|
|
b |
|
|
2µ0b |
|
|
d |
|
|
|
|||
|
|
1,5 |
+ µ |
|
|
F |
+ |
|
−0,375 |
+1,25ln |
|
F |
; |
(17) |
||||
|
|
|
|
|
||||||||||||||
т |
|
0 h |
|
|
h |
h |
|
|||||||||||
|
|
|
|
0 |
|
|
|
п |
|
|
||||||||
|
|
|
|
|
0 |
|
|
|
|
0 |
|
|
0 |
|
|
|
для удлиненных в плане поковок, а также поковок, имеющих в плане форму прямоугольника или близкую к прямоугольнику форму.
|
|
|
|
|
|
|
|
|
|
|
|
|
|
|
|
|
|
|
|
|
|
|
|
|
b |
|
|
2µ0b |
|
|
a |
|
|
|
|||
P =1,155σ |
|
|
1 |
+ µ |
|
|
F |
+ |
|
−0,25 |
+1,25ln |
|
F |
. |
(18) |
|||
|
|
|
|
|||||||||||||||
т |
|
0 h |
|
|
h |
h |
|
|||||||||||
|
|
|
|
0 |
|
|
|
п |
|
|
||||||||
|
|
|
|
|
0 |
|
|
|
|
0 |
|
|
0 |
|
|
|
В формулах (17)-(18) σт – предел текучести металла при температуре штамповки, Па; µ0 – коэффициент внешнего трения (на мостике облоя), в расчетах принимают равным 0,5; b, h0 – ширина и толщина мостика облоя, мм; F0 – площадь проекции мостика облоя, мм2; d ,
a – соответственно диаметр поковки и размер поковки по ширине, мм; Fп – площадь проекции поковки на плоскость разъема, мм2.
Для поковок, близких по форме к круглым или квадратным в плане, принимают
d =1,13 Fп |
(19) |
среднюю ширину удлиненных поковок |
|
a = Fп , |
(20) |
Lп |
|
где Lп – максимальный габаритный размер поковки в плане (в направ-
лении длины), мм.
При штамповке в закрытых штампах необходимое усилие определяется как:
P =σ |
|
|
− |
2r |
2 |
|
|
|
1,5H |
r |
|
2r |
|
− |
|
|||
{2,07 1 |
|
2 |
+1,5ln |
п +12 2 |
1− |
2 |
|
|
||||||||||
|
|
т |
|
|
d |
|
|
|
2r2 |
d |
d |
|
|
|||||
|
|
|
|
|
|
|
, |
(21) |
||||||||||
|
H |
|
H2 |
|
|
d |
|
2 |
|
|
|
|
|
|
||||
|
|
|
|
|
(H −r −r )−1,5}F |
|
|
|||||||||||
−4,5 |
|
п |
+1,92 |
|
п |
+ |
|
|
+ |
|
|
|
|
|||||
|
d |
|
6Hп |
d |
|
|
|
|||||||||||
|
|
|
d2 |
|
|
|
п |
1 2 |
|
п |
|
|
|
|||||
где r1 |
– радиус закругления поковки около пуансона, мм; r2 – естест- |
венный радиус закругления угла дна матрицы, мм; Hп – высота поковки, мм; d – диаметр поковки, мм.

13
9. Разработка технологической оснастки
9.1 Разработка молотового штампа
Вначале проектируют ручьи штампа, необходимые для получения данной поковки в соответствии с принятой последовательностью переходов штамповки [2, гл. 3].
Ручьи на поверхности разъема штампов координируют относительно центра штампа. Штамповочные ручьи размещают вблизи центра штампа, а заготовительные – по его бокам.
Если в штампе один штамповочный ручей (окончательный), то центр ручья совмещают с центром штампа. Если кроме окончательного ручья используют предварительный, то эти ручьи располагают по обе стороны от центра штампа: центр окончательного ручья – на расстоянии в 2 раза меньшем, чем центр предварительного ручья.
Стенки между полостями ручьев и боковыми гранями штампа, а также между ручьями должны обладать достаточной прочностью. Толщина стенок зависит от глубины полости ручьев, уклона прилегающих стенок ручьев и радиуса перехода от стенки к дну полости. Чем глубже полости и меньше уклон и радиус, тем толще должна быть стенка.
Толщины стенок определяют с помощью вспомогательной величины T , значения которой получены эмпирическим путем и приведены в виде номограмм в справочной литературе.
На основе размеров ручьев, толщин стенок между ручьями и гранями штампа определяют размеры штампового кубика (длину и ширину). Минимальную высоту штампового кубика можно определить в зависимости от размеров наиболее глубокой полости штампа.
Размеры штампа должны обеспечивать необходимую площадь соударения. В табл. 3 приведена минимальная допустимая площадь соударения на 1 т массы падающих частей в зависимости от размеров штампа.
Таблица 3
Минимальная допустимая площадь соударения
Размеры штампа |
Минимальная допустимая площадь соударения, см2 |
Мелкие |
150 |
Средние |
300 |
Крупные |
450 |
14
9.2 Разработка штампа для пресса
Штампы КГШП имеют сборную конструкцию, благодаря чему упрощается изготовление сменного инструмента и создаются условия для экономии дорогих инструментальных сталей. Штампы состоят из штамповых вставок, в которых выполнены ручьи, и блоков (пакетов) или державок, в которых закрепляют вставки [2, гл. 4].
Блок состоит из верхней и нижней монтажных плит (оснований, башмаков), связанных между собой направляющими колонками, деталей крепления штамповых вставок и выталкивающего механизма.
Размеры универсальных блоков для прессов, толщина основной и подкладной плит зависят от усилия пресса. Блоки в основном проектируют двухили трехручьевыми, вставку с окончательным ручьем располагают в центре блока. Если для штамповки достаточны один или два ручья, то в блок добавляют до комплекта гладкие вставки из простых конструкционных сталей.
Из выталкивающих механизмов универсальных блоков наибольшее распространение получил рычажно-кулачковый выталкивающий механизм. Размеры рычагов выталкивателей и длина хода толкателей выталкивающих механизмов блоков прессов зависят от номинального усилия пресса.
На штамповой вставке, как правило, располагается только один ручей. Поверхности разъема вставок при штамповке не должны соприкасаться, чтобы исключить работу пресса в распор. Между верхней и нижней вставками необходим зазор, величину которого принимают не менее толщины заусенца.
10.Проектирование вспомогательных операций
Квспомогательным операциям относят обрезку облоя и пробивку перемычек, правку, калибровку и очистку поковок [2, гл. 10].
Обрезку облоя и пробивку перемычек производят в горячем и холодном состоянии поковок. В холодном состоянии обрезку облоя производят у мелких и средних поковок из углеродистой стали с содержанием углерода до 0,4 % и поковок из низколегированной стали, штампуемых на молотах с массой падающих частей до 1-2 т и на КГШП с усилием до 10-20 МН, причем только в тех случаях, когда после обрезки поковки не требуют дальнейших операций в горячем состоянии.
15
Необходимое усилие (МН) обрезки облоя или пробивки перемычки определяют по формуле
P = (1,5 ÷1,8)106 Stσв, |
(22) |
где S – периметр среза, мм; t |
– действительная толщина среза пере- |
мычки или облоя, мм; σв – предел прочности при температуре обрезки,
МПа.
Зазор между пуансоном и матрицей оказывает большое влияние на качество и точность поверхности среза, изнашивание и стойкость штампа, величину потребного усилия и работы обрезки. Размер зазора зависит от формы и размеров сечений поковки в плоскости, перпендикулярной к разъему.
Правку проводят с целью устранения искривления поковок. Искривление происходит главным образом при обрезке облоя и пробивке перемычек в результате неплотного прилегания опорной поверхности пуансона к поверхности поковки. Большое влияние на величину искривления оказывает состояние режущих кромок обрезных матриц и пунсонов, а также зазор между матрицей и пуансоном. Коробление поковок возникает также при неправильном режиме охлаждения поковок после штамповки и термической обработки. Правку необходимо назначать в тех случаях, когда величина искривления превышает допуск на размеры поковок.
В целях упрощения правочного ручья и облегчения правки рекомендуется:
•упрощать контур ручья при сложных в плоскости разъема контурах поковки;
•небольшие выступы на поковке не обжимать, предусмотрев вокруг них зазор 0,3-0,5 мм;
•правочный ручей для удобства укладки и удаления поковок делать открытым с торцов поковки.
Калибровку применяют для повышения точности формы и размеров поковки, снижения шероховатости поверхности, исключения обработки поковок резанием. Различают калибровку плоскостную и объемную, по температурным условиям – холодную и горячую.
Плоскостную калибровку применяют для получения точных вертикальных размеров поковки на одном или нескольких ее участках, лежащих в различных по высоте параллельных плоскостях. При плоскостной калибровке деформируют металл только отдельных частей поковки.
16
При объемной калибровке деформации подвергается весь металл поковки. Свободное течение металла в горизонтальном направлении ограничено боковыми стенками ручья штампа.
Для получения поковок с высоким качеством поверхности, требующих минимальной обработки резанием, необходимо очищать заготовки перед нагревом и после ковки и штамповки от поверхностных дефектов, окалины, ржавчины и других загрязнений (мазута, масла, песка). В зависимости от размеров поковок, а также от технических условий на изготовление применяют механическую очистку поковок, гидравлическую, пневматическую струйноабразивную, гидроабразивную, виброабразивную, очистку в галтовочных барабанах, очистку дробью, травлением и огневую очистку.
11. Определение вида и режима термообработки поковок
Термическая обработка поковок имеет ряд особенностей [1, гл. 11]. Одна из них – возникновение значительного перепада температур по сечению поковки (особенно у крупных), что приводит к неодновременности протекания фазовых превращений, а следовательно, к получению различных структур (от мартенситной на поверхности до перлитной в центре заготовки). Кроме того, перепад температур по сечению поковки и, как следствие, неодновременность структурных превращений приводят к возникновению внутренних напряжений, отрицательно сказывающихся на свойствах поковки.
В связи с этим при термической обработке необходимо добиваться минимальных остаточных напряжений, применяя для этого отпуск при высоких температурах и минимальную скорость охлаждения, особенно в области температур упругопластического состояния металла
(700-450 °С).
Еще одной особенностью термообработки поковок является обработка на перераспределение водорода, присутствующего в стали, в объеме заготовки для уменьшения опасности образования флокенов. Поковки из углеродистых и низколегированных сталей переохлаждаются до температур 450-650 °С, из высоколегированных сталей – до 200-350 °С. Длительность изотермической выдержки определяется составом стали и размерами поковок.
17
Рекомендуемая литература
1.Ковка и штамповка: Справочник. В 4-х т. / Ред. совет: Е.И. Семенов (пред.) и др. – М.: Машиностроение, 1985. – Т. 1. Материалы и нагрев. Оборудование. Ковка / Под ред. Е. И. Семенова. 1985. – 568 с.
2.Ковка и штамповка: Справочник. В 4-х т. / Ред. совет: Е. И. Семенов (пред.) и др. – М.: Машиностроение, 1986. – Т. 2. Горячая штамповка / Под ред. Е. И. Семенова. 1986. – 592 с.
3.ГОСТ 7505
4.ГОСТ 7831
18
Составитель
Андрей Александрович Кречетов
ПРОЕКТИРОВАНИЕ ТЕХНОЛОГИЧЕСКОГО ПРОЦЕССА ГОРЯЧЕЙ ОБРАБОТКИ ДАВЛЕНИЕМ
Методические указания к лабораторной работе по курсу «Проектирование заготовок» для студентов специальностей 120100 «Технология машиностроения»,
120200 «Металлорежущие станки и инструменты»
Редактор З.М. Савина
ИД № 06536 от 16.01.02
Подписано в печать 21.03.02. Формат 60х84/16. Бумага офсетная. Отпечатано на ризографе. Уч.-изд. л. 1,00 Тираж 100 экз. Заказ. ГУ Кузбасский государственный технический университет.
650026, Кемерово, ул. Весенняя, 28.
Типография ГУ Кузбасский государственный технический университет. 650099, Кемерово, ул. Д. Бедного, 4А.