
А.А. Клепцов Проектирование станочного приспособления
.pdf
|
20 |
|
|
∆ун = |
0,034 −(−0,043) |
=0,0375 мм; |
|
2 |
|||
|
|
∆н = 0,0432 + 0,03752 = 0,057 мм.
Погрешность вследствие износа режущего инструмента
∆и = 21000Uo l .
Относительный износ сверл по диаметру [6, с. 123]
Uo = 0,005÷0,008 мм/км.
Путь резания при сверлении определяется по формуле [6, с. 124]
l = π D L n , 1000 Sпр
где D – диаметр сверла, мм; L – длина обработки, мм; n – частота вращения шпинделя станка, об/мин; Snp – продольная подача сверла,
мм/об.
Принимая D = 14,75 мм, L = 20 мм, n = 630 об/мин, Snp = 0,25 мм/об, получим
l = |
|
π D L n |
|
= |
3,14 14,75 20 630 |
=2335 мм = 2,335 м. |
|||||
1000 Sпр |
|
|
|||||||||
|
|
|
|
1000 0,25 |
|
|
|
||||
Тогда |
|
|
|
|
|
|
|
|
|
|
|
|
|
∆и = |
|
2Uo l |
= |
2 0,008 2,335 |
= 0,00004 |
мм. |
|||
|
|
1000 |
|
||||||||
|
|
|
|
1000 |
|
|
|
Ввиду малости величиной ∆н можно пренебречь.
Суммарная погрешность формы Σ∆Ф обрабатываемого отверстия не влияет на точность межцентрового расстояния 180±0,15 мм, поэтому принимается Σ∆Ф = 0.
Определяется допустимая погрешность установки
Ey = (δ −Σ∆Ф)2 −∆2y −∆2н −3∆2и −3∆2Т =
= 0,32 −0,132 −0,0572 = 0,264 мм.

21
Определяется погрешность, обусловленная неточностью изготовления приспособления:
Eпр = Еу2 − Ез2 − Еб2 .
Погрешность базирования
Eб = 12 Smax ,
где Smax – наибольший зазор в сопряжении отверстия 32Н9 (+0,062) с установочным пальцем.
Принимая диаметр установочного пальца 32g6 ( −−0,0090,025 ), получим
Smax = +0,062 – (-0,025) = 0,087 мм; Еб = (1/2) 0,087 = 0,044 мм.
Погрешность закрепления принимается по справочнику [6, с. 45,
табл. 3.24].
Ез = 60 мкм = 0,06 мм.
Отсюда
Eпр = 0,2642 −0,0442 −0,062 = 0,251 мм.
Рассчитывается погрешность изготовления приспособления
Eизг = Епр2 − Ес2 − Еи2 .
Принимая погрешность установки приспособления на столе станка Ес = 0,015 мм и допустимую величину износа установочного пальца
по диаметру Ен = 0,01 мм, получим
Eизг = 0,2512 −0,0152 −0,012 = 0,25 мм.
Полученное значение Еизг является допуском замыкающего звена А∆ размерной цепи А (рис. 3).
Вэтой размерной цепи замыкающим звеном А∆ является расстояние от оси V установочного пальца 32g6 до оси I отверстия в кондукторной втулке 14,75F7.
Вцепь входят следующие составляющие звенья:

22
– А1 – несовпадение оси I отверстия в кондукторной втулке с осью II отверстия в промежуточной втулке. Учитывая, что кондуктор-
ная втулка сопрягается с промежуточной по посадке 25 Hh67 , можно
рассчитать величину зазора в сопряжении:
Smax′′ = BOA −HOB ,
где ВОА – верхнее отклонение диаметра отверстия промежуточной втулки, ВОА = +0,021 мм; НОВ – нижнее отклонение диаметра наружной поверхности кондукторной втулки, НОВ = -0,020 мм.
Отсюда
Smax′′ = ±0,021 – (-0,020) = 0,041 мм.
Наибольшее значение A1 равно Smax′′2 , т. е.
ТА1 Smax′′2 = 0,021 мм;
–А2 – расстояние от оси II отверстия в промежуточной втулке до оси III штифта, по которому направляющая колодка IV призмы устанавливается в корпусе приспособления;
–А3 – расстояние от оси III штифта, по которому устанавливается направляющая колодка IV призмы, до оси V установочного пальца
32g6.
Исходными данными при решении размерной цепи являются допуск замыкающего звена ТА∆ = 0,25 мм и допуск на величину составляющего звена А1 ТА1 = 0,021 мм.
Допуски на остальные составляющие звенья назначаются таким образом, чтобы выполнялось условие
4
ТА∆ = ∑TAi.
i=1
Устанавливаются следующие допуски на величины составляющих звеньев:
ТА2 = 0,069 мм; ТА3 = 0,16 мм.

23
Таким образом,
ТА = ТАI + ТА2 + ТА3; 0,25 = 0,021+0,069+0,16.
Очевидно, что условие выполнено. При изготовлении деталей приспособления необходимо выдержать эти допуски на соответствующие размеры.
Силовой расчет приспособления
Составляется расчетная схема действующих на заготовку сил
(рис. 4).
Рис.4. Расчетная схема для определения сил зажима
На заготовку действует сила зажима W , момент крутящий резания Мкр и осевая сила Po .
Сила Po воспринимается основанием приспособления и при расчете силы зажима не учитывается. Сила трения от силы Po увеличивает
коэффициент запаса зажимного устройства.
Крутящий момент Мкр стремится повернуть заготовку вокруг точки O . Ему противодействует момент от силы трения F1, которая создается на пальце силой зажима W , а также моменты от сил трения

24
F2 , которые создаются силой зажима в точках контакта цилиндриче-
ской поверхности заготовки 30 с рабочими поверхностями призмы. N – реакция опор.
Прежде чем составлять уравнения статики, рассчитываются силы резания. Крутящий момент при сверлении рассчитывается по формуле
[7, с. 435]
M кр = СмDqm SУм Км,
где См, qм, Ум, Км – постоянные коэффициенты; D – диаметр свер-
ла, мм; S – продольная подача, мм/об.
В данном примере D = 14,75 мм, S = 0,25 мм/об.
Величины постоянных коэффициентов определены по справочни-
ку [7, с. 436, табл. 31].
См= 0,0345; qм = 2,0; Ум = 0,8; Км = 1.
Крутящий момент
Мкр = 0,0345 14,752 0,250,8 = 2,476 кг м = 2476 кг мм.
Поскольку момент Мкр стремится повернуть заготовку вокруг
точки O , сумма моментов всех сил, действующих на заготовку относительно точки O , должна быть равна нулю.
n
∑Moi = 0.
i=1
Составляется уравнение действующих моментов
Мкр = F1(L −d / 2) +2F2 R .
Вэтом уравнении R = 15 мм; L = 180 мм; d = 32 мм.
F1 =Wf1 ; |
F2 = Nf2 , |
где ƒ1 и ƒ2 – коэффициенты трения.
Коэффициент трения между обработанными поверхностями составляет ƒ1 = 0,15, а между необработанными – ƒ2 = 0,25.
Реакция опор
N = 2sinWα,
где α – угол призмы. Принимается 2α = 120°. Тогда
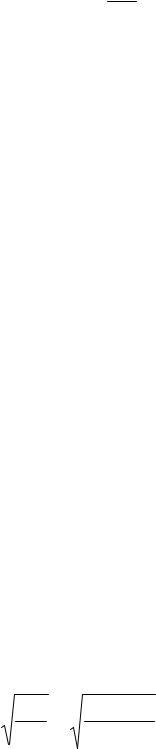
25
2F2 = sinWfα2
Вводится коэффициент запаса К. Окончательно условия равновесия заготовки определяются уравнением
|
|
|
d |
|
Wf R |
|
|||
КМ |
=Wf |
L − |
|
|
+ |
|
2 |
|
. |
|
sinα |
||||||||
кр |
1 |
2 |
|
|
|
Величина коэффициента запаса определяется по справочнику [5,
с. 267, табл. 6.1]. K = 2,6.
Решая уравнение относительно W , получается следующее выражение:
W = |
|
KM кр sinα |
|||
|
|
. |
|||
|
|
||||
|
f1 |
(L − |
d |
) sinα + f2 R |
|
|
|||||
|
|
2 |
|
|
Подставляя в формулу известные значения, получим
W = |
|
2,6 2476 sin 60 |
= 222,5 |
кг |
|||||
|
|
|
32 |
|
|
|
|||
|
|
|
|
|
|
|
|||
0,15 |
180 |
− |
|
|
sin 60 |
+0,2515 |
|
|
|
2 |
|
|
|||||||
|
|
|
|
|
|
|
|
|
При расчете параметров пневмоцилиндра принимаем рабочее давление воздуха в пневмосети Р = 6,3 кгс/см2
Диаметр пневмоцилиндра D , обеспечивающий требуемое усилие W , (для бесштоковой полости пневмоцилиндра двустороннего действия) определяется из формулы
|
W = |
πD2 |
P . |
|
|
|
|
4 |
|
|
|||
Отсюда |
|
|
|
|
|
|
|
|
|
|
|
|
|
D = |
4W |
= |
4 222,5 |
=6,7 |
см. |
|
|
πP |
|
3,14 6,3 |
|
|
Принимается ближайшее стандартное значение диаметра цилиндра
D = 80 мм (ГОСТ 15608-70).
При этом диаметр штока d = 25 мм, действительное толкающее усилие при давлении Р = 6,3 кгс/см2 не менее 278 кг.
26
Составитель Александр Алексеевич Клепцов
ПРОЕКТИРОВАНИЕ СТАНОЧНОГО ПРИСПОСОБЛЕНИЯ
Методические указания к контрольной работе для студентов заочной формы обучения
по специальности 120100 «Технология машиностроения» (сокращенные сроки обучения
на базе среднего профессионального образования)
Редактор З.М. Савина
ИД № 06536 от 16.01.02
Бумага офсетная. Отпечатано на ризографе. Уч.-изд. л. 1.60 Тираж 90 экз. Заказ ГУ Кузбасский государственный технический университет
650026, Кемерово, ул. Весенняя, 28 Типография ГУ Кузбасский государственный технический университет. 650099, Кемерово, ул. Д. Бедного, 4А