
Н.Г. Розенко Взаимозаменяемость, стандартизация и технические изменения
.pdf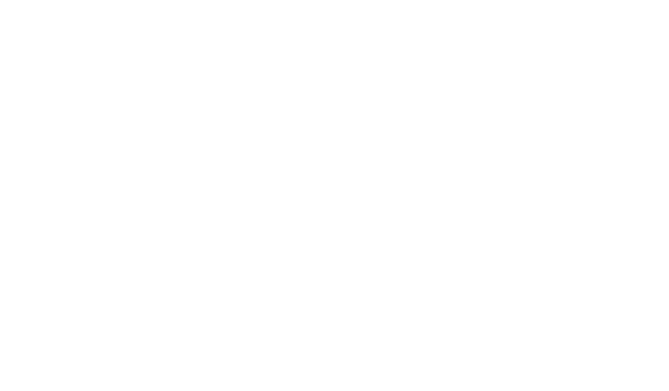
10 |
|
смазки. Это достигается при толщине масляного слоя |
|
h min ≥ hЖ.Т. ≥ kЖ.Т. (RZ1 + RZ 2 +∆д), |
(14) |
где hЖ.Т. - толщина масляного слоя, при котором обеспечивается жидкостное трение;
kЖ.Т. - коэффициент запаса надежности по толщине масляного слоя; RZ1 , RZ 2 - высота микронеровностей вкладыша подшипника и цап-
фы вала; ∆д - добавка, учитывающая отклонение нагрузки, скорости, темпе-
ратуры от расчетных значений, а также механические включения в масле и другие неучтенные факторы ( ∆д =1 ÷2 мкм).
Рис. 8. Схема расположения цапфы вала в неподвижном состоянии (пунктирная линия) при установившемся режиме работы подшипника
Одновременно с обеспечением жидкостного трения необходимо, чтобы подшипник обладал требуемой несущей способностью, характеризуемой радиальной силой R:
R = |
1,07 |
10−9 µnldCR |
, |
(15) |
|
ψ2 |
|||
|
|
|
где R - радиальная сила, кгс;
µ - динамическая вязкость масла, сП;

11
n - частота вращения, об/мин; l - длина подшипника, см;
d - диаметр подшипника, см;
CR - безразмерный коэффициент нагруженноcти подшипника, зависящий от χ и l/d;
ψ - относительный зазор, равный S/d.
Порядок расчета гидродинамического подшипника скольжения рассмотрим на примере.
Пример.
Выбрать посадку для подшипника скольжения, имеющего следующие конструктивные параметры и условия работы:
диаметр цапфы d=90 мм ; длина подшипника l =110 мм ; частота вращения n=750 об/мин;
удельное давление на поверхности контакта p=10 кгс см2 ;
вязкость масла µ =20 сП .
Проектный расчет 1. Окружная скорость цапфы
V = |
πdn |
= |
3,14 90 750 |
= 3,53 м/с. |
|
1000 60 |
1000 60 |
||||
|
|
|
|||
2. Относительный диаметр зазора |
|||||
ψ = 0,8 10−3 4 V = 0,8 10−3 4 |
3,53 = 0,0011 . |
3.Абсолютный диаметральный зазор
S =ψ d = 0,0011 90 = 0,0099 .
4.Выбор посадки
Рассчитанный в п.3 диаметральный зазор принимается за оптимальный. По ГОСТ 25347-82 (СТ СЭВ 144-75) выбирается посадка, средний зазор которой наиболее близок к оптимальному. Такой посадкой в
данном случае является 90 He77 . Схема расположения полей допусков этой посадки приведена на рис. 9.
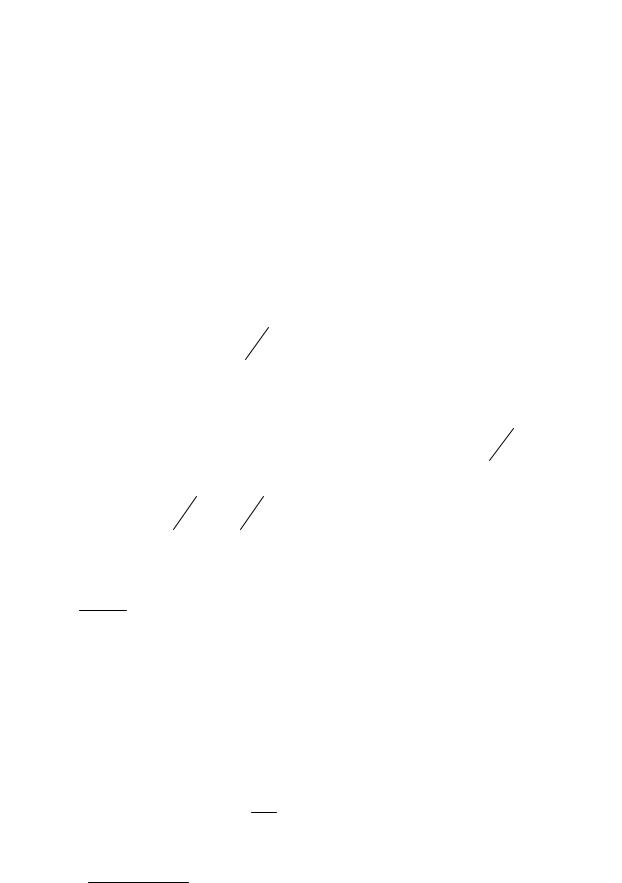
12
Для данной посадки S max = 0 ,142 мм; S min = 0 ,072 мм;
S m = 0 ,107 мм.
Проверочный расчет 1. Коэффициент нагруженности подшипника определяем по форму-
ле (15), в которой принято |
R |
dl |
= p : |
|
|
||||||||||||
|
|
|
|
|
|
|
|
|
|
|
|
|
|
|
|
||
CR = |
|
p ψ2 |
|
= |
|
|
10 |
0,00112 |
= 0,75 . |
||||||||
1,07 |
10 |
−9 |
µn |
1,07 10 |
−9 |
20 750 |
|||||||||||
|
|
|
|
|
|
|
|||||||||||
2. В зависимости от величины CR |
и отношения l d определяется |
||||||||||||||||
относительный эксцентриситет χ [4, с 284]. |
|||||||||||||||||
|
|
R = |
0,75 и |
l |
d |
=110 |
90 |
=1,22 |
χ = |
0,40 . |
|||||||
Для C |
|
|
|
|
|
3. Наименьшая толщина масляного слоя определяется по формуле
(13):
h min = 0,1072 (1 −0,40)= 0,0321 мм.
4. Коэффициент запаса надежности по толщине слоя смазки определяется на основании формулы (14):
kЖ.Т. = |
h min |
|
|
. |
|
RZ1 + RZ 2 + ∆д |
Высота микронеровностей RZ выбирается в зависимости от квалитетов сопрягаемых размеров деталей по таблице 1 приложения.
Для деталей посадки 90 He77 ; RZ1 = 6,3 мкм; RZ 2 = 3,2 мкм. Тогда
kЖ.Т. = |
32,1 |
= 2,79 > 2. |
6,3 +3,2 + 2 |
Так как kЖ.Т. >2, то выбранная посадка соответствует условиям на-
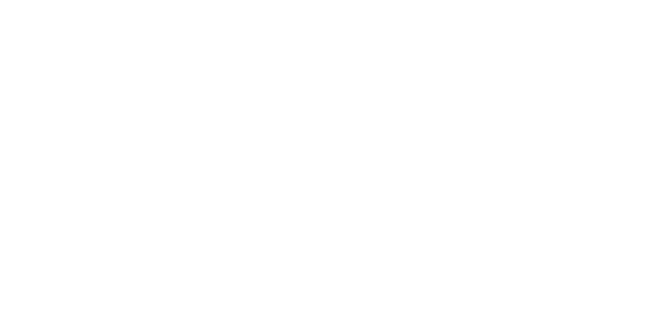
13
дежной работы подшипника в режиме жидкостного трения.
В случае, если kЖ.Т. <2, необходимо назначать ближайшее меньшее стандартное значение высоты микронеровностей RZ и вновь произвести проверку на обеспечение жидкостного трения в сопряжении.
б) Выбор посадки для прессового соединения Посадки с натягом предназначены для получения неподвижных не-
разъемных соединений без дополнительного крепления деталей. Относительная неподвижность деталей обеспечивается за счет сил сцепления (трения), возникающих на контактирующих поверхностях вследствие их деформации, создаваемой натягом при сборке соединения.
Величина натяга N определяется разностью диаметров вала и внутренним диаметром втулки до сборки. При запрессовке соединения происходит деформация растяжения втулки на величину N и одновременно деформация сжатия вала на величинуNd , причем N = ND + Nd
Рис. 10. К расчету посадок с натягом
Предельные значения натягов выбранной посадки должны удовлетворять следующим условиям:
1) при наименьшем натяге должна обеспечиваться прочность соединений, т.е. не должно быть относительного поворота деталей от действия внешнего крутящегося момента или осевого усилия, или их совместного действия.
Например, при нагружении крутящим моментом это условие будет

|
14 |
выполнено, если |
|
Мкр < Мтр, |
(16) |
где Мкр - наибольший крутящий момент, прикладываемый к одной детали;
Мтр - момент трения, зависящий от натяга, размеров соединяемых деталей, шероховатости поверхности и других факторов;
2) при наибольшем натяге должна обеспечиваться прочность соединяемых деталей, т.е. наибольшее напряжение, возникающее в материалах деталей, не должно превышать допустимого значения.
Величина наименьшего расчетного натяга при осевом нагружении
N min расч = |
|
p |
|
|
C1 |
|
C2 |
|
|
||
|
|
|
|
|
|
+ |
|
, |
(17) |
||
πlf |
|
E1 |
|
||||||||
|
1 |
|
|
|
E2 |
|
|
||||
при нагружении крутящим моментом |
|
||||||||||
N min расч = |
|
2Mкр |
|
C1 |
|
C2 |
|
|
|||
|
|
|
|
|
|
+ |
|
, |
(18) |
||
πdlf 2 |
|
E2 |
|||||||||
|
|
E1 |
|
|
|
||||||
где p - осевая сила; |
|
|
|
|
|||||||
l - длина соединения; |
|
|
|
||||||||
f 1 и f 2 - |
коэффициенты трения сцепления, |
соответственно при |
продольном смещении и при относительном вращении деталей; при сборке с помощью пресса f = 0,08 ; при сборке с нагревом ох-
ватывающей детали или с охлаждением охватываемой детали f |
= 0,14 ; |
|||||||||||||||
d - номинальный диаметр сопрягаемых поверхностей; |
|
|||||||||||||||
E1 |
и E2 - модуль упругости материала соединяемых втулки и вала |
|||||||||||||||
(для стали E =2,1 104 кгс |
|
); |
|
|
|
|
|
|
||||||||
C1 |
|
|
|
|
|
|
|
мм2 |
|
|
|
|
|
|
|
|
и C2 - коэффициенты, определяемые по следующим зависимо- |
||||||||||||||||
стям: |
|
|
|
|
|
|
|
|
|
|
|
|
|
|
|
|
|
|
|
d |
2 |
|
|
d1 |
2 |
|
|
||||||
|
|
1 + |
|
|
|
|
1 + |
|
|
|
|
|
||||
|
|
|
|
|
|
|
|
|
||||||||
C1 |
= |
|
d 2 |
|
+ µ1; C2 = |
|
d |
|
− µ2; |
(19) |
||||||
|
d |
2 |
|
d1 |
2 |
|||||||||||
|
|
|
|
|
|
|||||||||||
|
|
1 − |
|
|
|
|
1 − |
|
|
|
|
|
||||
|
|
|
|
|
|
|
|
|
||||||||
|
|
|
d 2 |
|
|
|
d |
|
|
|
d1 - диаметр отверстия вала;
d 2 - наружный диаметр втулки (см. рис. 10);
µ1 и µ2 - коэффициенты Пуассона для втулки и вала (для стали
15
µ = 0 ,3 , для чугуна µ = 0 ,25 ).
Для учета уменьшения посадочного натяга за счет смятия микронеровностей вводится поправка U , которая для материалов с одинаковыми свойствами определяется по следующей зависимости:
U = 2k (Rz1 + Rz2), |
(20) |
где k - коэффициент, учитывающий величину смятия неровностей отверстия втулки и вала (при механической запрессовке при нормальной температуре без смазки k = 0,25 ÷ 0,5 ); микронеровностей сопрягаемых поверхностей втулки и вала.
Значения Rz1 и Rz2 выбираются в зависимости от принятых полей допусков деталей сопряжения по табл.1 и 2 приложения.
Наименьший функциональный натяг, при котором обеспечивается прочность соединения, будет равен
N min F = N min расч +U. |
(21) |
По этому натягу подбирается ближайшая посадка по ГОСТ 2534782 (СТ СЭВ 144-75). Величина наименьшего функционального натяга должна быть не больше наименьшего натяга выбранной посадки.
Условие прочности соединяемых деталей заключается в отсутствии пластической деформации на контактных поверхностях вала и втулки
при наибольшем табличном натяге: |
|
||||||||||
P ≤ Pдоп. |
|
|
|
|
|
|
|
|
(22) |
||
Давление при наибольшем табличном натяге |
|
||||||||||
P = |
N max T |
|
|
. |
|
|
|
(23) |
|||
|
C1 |
|
C2 |
|
|
|
|||||
|
d |
|
+ |
|
|
|
|
|
|
||
|
|
E2 |
|
|
|
||||||
|
E1 |
|
|
|
|
|
|||||
Допустимое давление на контактирующей поверхности втулки |
|
||||||||||
Pдоп = 0,58σТ |
|
|
d |
2 |
|
|
|||||
1 |
− |
|
|
, |
(24) |
||||||
|
|||||||||||
|
|
|
|
|
|
|
d 2 |
|
|
|
|
|
|
|
|
|
|
|
|
|
|
|
|
на поверхности вала |
|
|
|
||||||||
Pдоп = 0,58σТ |
|
|
d1 |
2 |
|
(25) |
|||||
1 |
+ |
|
, |
||||||||
|
|
|
|
|
|
|
d |
|
|
|
|
|
|
|
|
|
|
|
|
|
|
|
|
где σТ - предел текучести материала деталей при растяжении.
Пример Рассчитать и выбрать посадку с натягом для соединения, имеющего
следующие конструктивные данные и условия работы:
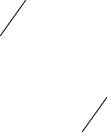
16
Mкр = 4,2 105 кгс мм; d =140мм;
материал деталей - сталь 40; d 2 = 230мм;
σТ = 34 кгс мм2 ; l = 0,8d .
Наименьший расчетный натяг определяем по формуле (18). Принимаем: для сборки под прессом f 2 = 0 ,08 ; для стали:
E1 = E2 = 2,1 104 кгс |
|
2 ; |
µ = 0,3 |
|
|
|
|
|
|||||||||||||
|
|
|
|
|
|
|
|
2 |
|
мм |
|
|
|
|
|
|
|
|
|
||
|
|
|
|
140 |
|
|
|
|
|
|
|
|
|
|
|
|
|||||
1 |
+ |
|
|
|
|
|
|
|
|
|
|
|
|
|
|
|
|
||||
230 |
|
|
|
|
|
|
|
|
|
|
|
|
|||||||||
C1 = |
|
|
|
|
+0,3 |
= 2,48, |
|
|
|
|
|
|
|
||||||||
|
|
|
140 |
2 |
|
|
|
|
|
|
|||||||||||
|
|
|
|
|
|
|
|
|
|
|
|
|
|
|
|
||||||
1− |
|
|
|
|
|
|
|
|
|
|
|
|
|
|
|
|
|
||||
|
230 |
|
|
|
|
|
|
|
|
|
|
|
|
||||||||
|
|
|
|
|
|
|
|
|
|
|
|
|
|
|
|
|
|||||
|
|
|
|
|
|
0 |
2 |
|
|
|
|
|
|
|
|
|
|
|
|
||
|
1+ |
|
|
|
|
|
|
|
|
|
|
|
|
|
|
|
|
||||
|
140 |
|
|
|
|
|
|
|
|
|
|
|
|
||||||||
C2 = |
|
|
|
|
−0,3 |
= 0,7, |
|
|
|
|
|
|
|
|
|||||||
|
|
|
|
0 |
2 |
|
|
|
|
|
|
|
|
|
|||||||
|
|
|
|
|
|
|
|
|
|
|
|
|
|
|
|
|
|||||
|
1− |
|
|
|
|
|
|
|
|
|
|
|
|
|
|
|
|
||||
|
140 |
|
|
|
|
|
|
|
|
|
|
|
|
||||||||
|
|
|
|
|
|
|
|
|
|
|
|
|
|
|
|
|
|||||
N min расч = |
|
|
2,42 |
105 |
|
|
|
2,48 |
|
0,7 |
|
=0,032мм. |
|||||||||
|
|
|
|
|
|
|
|
|
|
+ |
|
|
|||||||||
3,14 140 0,8 140 0,08 |
2,1 105 |
2,1 104 |
|||||||||||||||||||
|
|
|
|
|
|
|
|
|
|
|
Так как величина наименьшего расчетного натяга имеет небольшую величину, то предварительно принимаем, что отверстие будет изготавливаться по 7 квалитету, а вал - по 6 квалитету. В этом случае Rz1 = 12,5 мкм; Rz 2 = 6,3 мкм (табл. 2 приложения). Принимаем величину коэффициента k=0,4.
U = 2 0,4 (12,5 +6,3)=15 мкм.
Наименьший функциональный натяг определяем по формуле (21)
N min F = 0,032 +0,015 = 0,047мм.
По этому натягу подбираем по ГОСТ 25347-82 (СТ СЭВ 144-75)
ближайшую посадку. Такой посадкой будет 140 |
H 7 |
, для |
которой |
s6 |
|||
N min F = 52мкм,N max F = 117 мкм.Схема расположения полей |
допусков |
||
этой посадки приведена на рис. 11. |
|
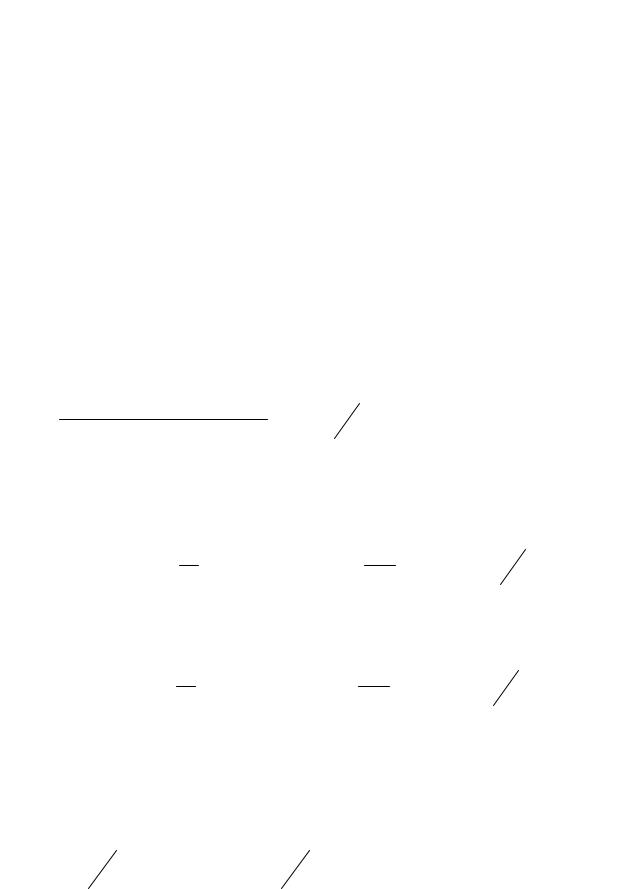
17
Проверяем прочность соединяемых деталей при наибольшем табличном натяге N max T . Для этого по формуле (23) находим давление при указанном натяге:
P = |
|
0,117 |
|
|
= 5,52кг |
мм2 |
. |
|
|
2,48 |
|
0,7 |
|
||||
|
140 |
|
+ |
|
|
|
|
|
|
2,1 104 |
2,1 104 |
|
|
|
|||
|
|
|
|
|
|
|
По уравнению (24) находим допустимое давление на контактирующей поверхности втулки
Pдоп = 0,58σT |
|
− |
d1 |
2 |
|
− |
|
140 |
|
2 |
=12,41 |
кг |
|
|
||
1 |
|
|
|
|
= 0,58 34 1 |
|
|
|
|
|
2 |
|||||
|
|
|
d |
|
|
130 |
|
|
мм |
|||||||
|
|
|
|
|
|
|
|
|
|
|
|
|
|
|||
|
|
|
|
|
|
|
|
|
|
|
|
|
|
|
|
|
По уравнению (25) находим допустимое давление на поверхности вала
Pдоп = 0,58σT |
|
− |
d1 |
2 |
|
− |
|
0 |
|
2 |
=19,72 |
кг |
|
|
||
1 |
|
|
|
|
= 0,58 34 1 |
|
|
|
|
|
2 |
|||||
|
|
|
d |
|
|
140 |
|
|
мм |
|||||||
|
|
|
|
|
|
|
|
|
|
|
|
|
|
|||
|
|
|
|
|
|
|
|
|
|
|
|
|
|
|
|
|
Условие прочности деталей, которое заключается в отсутствии пластической деформации, выполняется, так какP < Pдоп.
Сравнивая допустимое давление с давлением, возникающим при наибольшем табличном натяге, определяем запас прочности втулки и вала:
k1 =12,41 |
5,52 |
= 2,25; |
k2 =19,72 |
5,52 |
= 3,57 |
|
|
|
|
18
Контрольная работа №2 Задача № 4
1.Изобразить графически сопряжение радиального подшипника качения с валом и корпусом. Построить поля допусков этих сопряжений. На полях допусков указать обозначения и отклонения.
2.Для нормальных диаметров и посадок, принятых в сопряжениях подшипника качения, графически изобразить поля допусков для сопряжения вала и отверстия, выполненных с допусками для обычных гладких цилиндрических сопряжений.
3.На всех графических изображениях сопряжений указать наибольшие и наименьшие натяги (зазоры) и дать объяснение: чем отличаются сопряжения подшипника качения с валом и корпусом от обычных гладких цилиндрических сопряжений, как это влияет на характер сопряжения.
Методические указания к задаче № 4
Для сокращения номенклатуры подшипников посадки наружного кольца с корпусом осуществляются по системе вала, а посадки внутреннего кольца с валом - по системе отверстия. Однако поле допуска на диаметр отверстия внутреннего кольца подшипника расположено в “минус” от нормального размера, а не в “плюс”, как у обычного основного отверстия. Для соединения колец подшипников с валами и корпусами применяются подшипниковые посадки. Отличие этих посадок от посадок по ГОСТ 25347-82 (СТ СЭВ 144-75) состоит в том, что зазоры и натяги в них имеют другие величины. Это вызвано тем, что предельные отклонения размеров колец по ГОСТ 520-89 (СТ СЭВ 774-85) отличны от отклонений, установленных ГОСТ 25347-82 (СТ СЭВ 144-75). Соединение колец подшипников с валами и отверстиями в корпусах, по сравнению с обычными гладкими цилиндрическими соединениями, может давать другой характер посадок.
Номер квалитета сопрягаемых с подшипником качения деталей определяется в зависимости от класса точности подшипника по табл. 3 приложения. Подшипниковые посадки обозначаются одним полем допуска - полем допуска сопрягаемой с подшипниковым кольцом детали.
Пример Выполнить действия, предусмотренные в задаче № 4, для следую-
щих исходных данных:
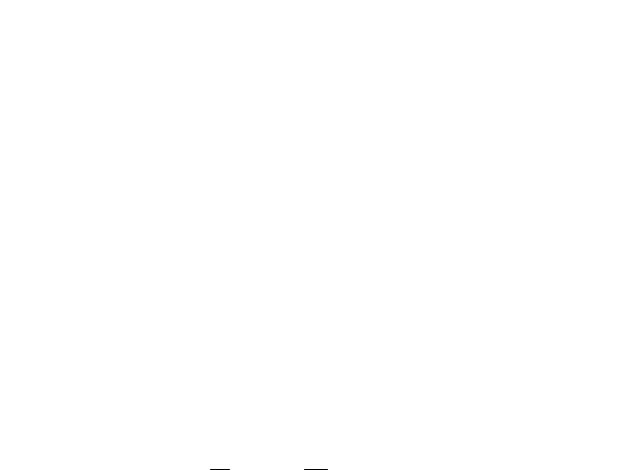
19
наружный диаметр подшипника - 110 мм; внутренний диаметр подшипника - 50 мм; основное отклонение отверстия корпуса - по G; основное отклонение вала - по k;
класс точности подшипника - 5.
1. Для подшипника 5-го класса точности согласно табл.1 и 3 приложения присоединительный размер вала выполняется по 5 квалитету, а отверстия - по 6 квалитету. Графическое изображение сопряжения подшипника качения с валом и корпусом приведено на рис. 12. Схемы расположения полей допусков подшипниковых соединений приведены на рис. 13а и 14а. Предельные отклонения колец подшипников взяты по ГОСТ 520-89 (СТ СЭВ 774-85); обычных гладких цилиндрических деталей - по ГОСТ 25347-82 (СТ СЭВ 144-75). Заданные подшипниковые соединения имеют следующие обозначения:
50k 5 - сопряжение внутреннего кольца с валом;110G6 - сопряжение корпуса с наружным кольцом.
2. Посадки для обычных гладких цилиндрических деталей образуются следующим образом:
внутреннее кольцо подшипника (основное отверстие) заменяется основным отверстием по ГОСТ 25347-82 (СТ СЭВ 144-75);
наружное кольцо подшипника (основной вал) заменяется основным валом по ГОСТ 25347-82 (СТ СЭВ 144-75).
Тогда соответствующие посадки для обычных гладких соединений
будут следующие: 50 Hk 55
и 110 Gh66 .