
Монография MMK Metalurji
.pdfпроцессе нагрева вводится известь и плавиковый шпат в соотношении (4…5):1 разовыми порциями.
Для раскисления шлака используется гранулированный алюминий и другие алюминийсодержащие материалы фракцией не более 15 мм, молотый ферросилиций, карбид кремния и другие раскислители (кокс, кальцийсодержащие материалы и др.).
В случае низкой жидкоподвижности шлака проводится электронагрев до или во время раскисления шлака.
После этого производится измерение температуры и отбор пробы металла для лабораторного анализа, а также пробы шлака для визуальной оценки.
При получении результатов анализа пробы металла производится корректировка его химического состава добавлением необходимого количества раскислителей и легирующих материалов. Количество материалов определяется с учетом показаний массы ковша с металлом, установленного на сталевозе.
Для более точной корректировки химического состава или получения узкого предела содержания элементов может использоваться порошковая проволока с различными видами наполнителей. Может использоваться проволока диаметром от 5 до 16 мм. Ввод порошковой проволоки осуществляется трайбаппаратом со скоростью от 5 до 300 м/мин. При вводе проволоки в жидкий металл стараются обеспечить минимальное расстояние между нижней частью направляющей трубы и уровнем металла.
Корректировка содержания углерода в стали может осуществляться углеродсодержащей порошковой проволокой. После введения углеродсодержащей проволоки производится продувка аргоном в течение трех минут. Усвоение углерода из порошковой проволоки в среднем равняется 97 %.
При обработке сталей с содержанием кремния не более 0,04 % для корректировки химического состава используются ферросплавы с содержанием кремния не более 1,0 % и первичный алюминий.
После трех минут усреднительной продувки отбирается проба металла. До получения результатов экспресс-анализа перемешивание металла ведется с расходом, обеспечивающим минимальное оголение металла.
По результатам химического анализа, при необходимости, проводится дополнительная корректировка химического состава.
81
В конце ковшевой обработки плавки на установке «печьковш» продолжительность продувки металла аргоном после присадки последней порции ферросплавов должна быть не менее трех минут. При суммарном расходе ферросплавов в количестве более 1000 кг перед передачей металла на МНЛЗ продолжительность продувки металла аргоном после их присадки должна быть не менее пяти минут.
Температура металла в ковше должна соответствовать заказанной (отклонение – не более ± 3 °С).
С использованием системы «Hydris» измеряется содержание водорода в металле.
Перед передачей на МНЛЗ металл обязательно обрабатывается кальцийсодержащей порошковой проволокой. Во время ввода порошковой проволоки продувка металла аргоном производится с минимальной интенсивностью.
После ввода кальцийсодержащей проволоки металл продувается аргоном с минимальным расходом в течение около двух минут, после чего ковш с металлом сразу передается на МНЛЗ.
Электронагрев и продувка металла аргоном, проводимые после ввода порошковой проволоки, приводят к снижению усвоения кальция в готовом металле.
Одной их главных задач ковшевой обработки стали на установке «печь-ковш» является проведение эффективной десульфурации металла.
Для этого после усреднительной продувки металла аргоном ковшевой шлак раскисляется алюминиевой дробью. В случае отсутствия дроби допускается использование чушкового алюминия, пирамидок алюминия, обрези катанки алюминия, алюминиевой стружки или порошка. В случае недостаточного расхода алюминийсодержащих материалов для раскисления шлака дополнительно используют углеродсодержащие материалы (кокс, электродный бой и др.), кальцийсодержащие материалы, как кусковые, так и в виде порошковойпроволоки.
После окончания раскисления шлака проводится электронагрев с наводкой нового шлака введением твердой шлакообразующей смеси (ТШС), состоящей из извести и плавикового шпата в соотношении (4…5) : 1. Суммарный расход ТШС с учетом смеси, присаживаемой на выпуске из печи, может составлять до 20 кг/т. При введении одной тонны ТШС температура металла снижается примерно на 10…15 °С.
82
После наведения шлака производится его визуальная оценка по цвету и состоянию поверхности. Цвет шлака изменяется от черного к белому, в зависимости от степени его окисленности – содержания в нем оксидов железа и марганца. Белый цвет шлака в ковше характеризуют его высокую степень раскисленности и серопоглотительной способности. При отклонении цвета и поверхности шлака от рекомендуемых необходимо принять меры по исправлению химического состава шлака. Для обеспечения эффективной десульфурации металла в ковше суммарное содержание в шлаке оксидов железа и марганца должно быть не более 1,5 %.
Если шлак имеет темный цвет, то необходимо провести дополнительноераскислениешлака.
После наведения белого шлака устанавливается максимально возможный расход инертного газа на пробки. Расход газа должен обеспечивать интенсивное перемешивание металла и шлака. Так как сера является поверхностно-активным химическим элементом и ее концентрация в приграничных слоях значительно выше, чем в объеме расплава. Интенсивное перемешивание увеличивает площадь контакта между шлаком и металлом и ведет к ускорению процесса десульфурации металла, Продолжительность продувки после наведения шлака должна составлять не менее 10 минут. При содержании серы в металле выше требуемого проводится дополнительная продувка с максимальной интенсивностью. Для успешной десульфурации в течение продувки рекомендуется иметь содержание алюминия вметалле,близкоек верхнемупределудляданноймаркистали.
2.2.2 Технология вакуумирования стали
Производство стали с использованием установки вакуумирования (УВС) может осуществляться по следующим технологическим схемам:
ДСП-250 – УПК – УВС – МНЛЗ (для вакуумной дегазации металла);
ДСП-250 – УВС – УПК – МНЛЗ (для производства стали с низким содержанием углерода).
Перед началом работы на вакуумной установке технологическим персоналом проверяется наличие расходуемых материалов в бункерах и на рабочей площадке, давление аргона и азота в трассах; обеспечение установки энергоресурсами (пар,
83
вода, сжатый воздух, электроэнергия), исправность быстроразъемных соединений и гибких шлангов трубопровода подачи инертных газов.
После простоя установки более восьми часов проверяется:
–передвижение тележки;
–поднятие крышки;
–состояние системы охлаждения;
–видеокамер;
–главные и вторичные блокировки на старт вакууматора;
–запуск цикла вакуумирования без ковша.
Перед постановкой сталеразливочного ковша в вакуумную камеру, при необходимости, производится отлив шлака.
Объем металла и шлака в стальковше должен обеспечивать расстояние от верхнего среза стальковша до поверхности шлака (свободный борт) не менее 900 мм при толщине шлака не более 50 мм. Температура металла перед обработкой должна быть на 60…80 °С выше заказанной на данную марку стали.
На стенде скачивания шлака отлив шлака из ковша производится:
–если толщина слоя шлака превышает 50 мм;
–перед обработкой на вакууматоре с целью глубокой десульфурации (до содержания серы в металле менее 0,003 %);
–перед дегазацией для достижения содержания азота менее 80 ppm и водорода не более 2 ppm.
Шлак сливается в шлаковый короб, при этом не допускается слив металла из ковша.
После скачивания шлака сталеразливочный ковш перевозится к вакуумной камере (рисунок 2.11), где при помощи быстроразъемных соединений подсоединяется к продувочному узлу аргонопровода. Затем ковш устанавливается в вакуумную камеру.
После установки ковша в рабочее положение и подключения трубопровода начинается продувка металла аргоном через донное продувочное устройство с расходом газа 1…2 л/(т·мин) при давлении аргона 1,2…2,5 МПа.
После усреднительной продувки в течение 3…5 мин проводится измерение температуры и отбор пробы металла на химический анализ.
После взятия пробы производится присадка шлакообразующих материалов.
При использовании технологической схемы ДСП-250 –
84

Рисунок 2.11 – Вид одной из двух вакуумных камер, отодвинутой крышки камеры и трайб-аппарата
УПК – УВС – МНЛЗ для раскисления шлака и проведения десульфурации металла в ковш могут дополнительно присаживаться раскислители.
Далее расход продувочного газа снижается до минимума, крышка передвигается и опускается на камеру, включается пароэжекторный насос до получения остаточного давления в камере 0,5 мм рт. ст. В процессе набора вакуума до давления 5 мм рт. ст. возможно вскипание металла. Этот процесс регулируется остановками в наборе вакуума и поддержанием постоянного давления в камере в течение нескольких минут до успокоения ванны.
85
После набора вакуума примерно до 0,3 мм рт. ст. расход аргона для перемешивания увеличивается до 2,5…5,0 л/(т·мин) для лучшего удаления растворенных газов из металла. При остаточном давлении в камере не более 1 мм рт. ст. жидкий металл обрабатывается в течение 8…15 мин.
При необходимости производится ввод в камеру корректирующих добавок ферросплавов и шлакообразующих материалов через шлюзовое устройство. Для этого давление в камере поднимается до значения 200…760 мм рт. ст. Шлюзовое устройство состоит из вакуумного шлюза с загрузочным конусом.
Вдальнейшем восстанавливается и выдерживается в течение 8…15 мин вакуум не более 1 мм рт. ст.
По завершению вакуумной обработки отсечной клапан закрывается и пароэжекторный насос выключается.
После вакуумной десульфурации в камеру закачивается азот для разбавления монооксида углерода, так как при его смешивании с воздухом при достижении концентрации СО 12,5…74,2
%смесь воспламеняется. При достижении содержания монооксида углерода менее 12,5 % открывается подача воздуха до восстановления атмосферного давления и камера открывается.
Расход аргона снижается до значения 1 л/(т·мин) для «мягкого» перемешивания. Измерение температуры металла и отбор проб металла производится после продувки аргоном в течение трех минут от времени последней присадки материалов.
При применении технологической схемы ДСП – УПК – УВС – МНЛЗ для окончательной доводки металла проводится корректировка содержания алюминия при помощи трайбаппарата алюминиевой проволокой и обработка металла кальцием путем ввода порошковой проволоки с силикокальцием или феррокальцием.
После отдачи проволоки осуществляется усреднительная продувка металла аргоном в течение пяти минут, отбираются пробы металла и шлака и измеряется температура металла.
При значительном охлаждении металла в процессе вакуумной обработки и при обработке стали по технологической схеме ДСП – УВС – УПК – МНЛЗ ковш переставляется на установку «печь-ковш».
Вконце обработки отсоединяются аргонопроводы вакуумной камеры от трубной разводки на ковше и ковш транспортируется на УПК или МНЛЗ в зависимости от выбранной схемы.
86
2.3Технология непрерывной разливки стали
2.3.1Подготовка МНЛЗ к разливке
Собранный и просушенный промежуточный ковш со стопорными стержнями, погружными разливочными стаканами и аварийным шибером отсечки устанавливается для разогрева на одну из тележек разливочной площадки. Включаются горелки стенда разогрева промежуточного ковша и начинается разогрев, продолжающийся 90 мин до температуры около 1200 °С. К началу разогрева промежуточного ковша подготавливается следующий ковш.
Подготовка кристаллизатора к разливке состоит в следующем:
–крышка кристаллизатора очищается от скрапа, шлака и
мусора;
–рабочая поверхность медных плит обдувается сжатым воздухом для очистки от твердых частиц;
–оценивается состояние внутренней полости кристаллизатора, при обнаружении дефектов глубиной не более 0,4 мм в виде выбоин, задиров, царапин, производится их зачистка и шлифовка в направлении сверху вниз с повторной обдувкой сжатым воздухом;
–проверяется отсутствие утечек воды;
–при помощи щупа замеряется величина зазора между плитами сборного кристаллизатора, которая не должна превышать 0,3 мм (при превышении этой величины кристаллизатор подлежит замене);
–проверяется состояние роликов на раме под кристаллизатором и форсунок зоны «подбоя» первых трех контуров водяного охлаждения;
–калибруется система измерения уровня металла в кристаллизаторе, состоящая из детектора и источника радиоактивного излучения;
–в течение пяти минут проверяется работа механизма качания кристаллизатора;
–для заданных размеров сечения отливаемого сляба выставляются расстояние между широкими, узкими плитами и конусность стенок кристаллизатора;
–на кристаллизатор устанавливается крышка с уплотнением зазора каолиновой ватой.
87
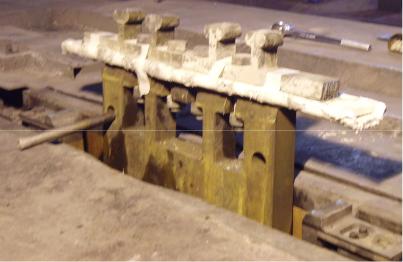
Важным этапом подготовки МНЛЗ к разливке является заведение затравки в кристаллизатор. Перед вводом затравки разводятся плиты широких граней кристаллизатора. Затравка со стенда хранения через роликовую проводку МНЛЗ в автоматическом режиме поднимается до роликов секции «подбоя» и останавливается. Перемещение головки затравки вверх, до выхода из кристаллизатора на высоту 300 мм от верхнего торца плит, производится с помощью дистанционного пульта управления разливщика в ручном режиме. При заведении головки затравки в рабочую полость кристаллизатора для предотвращения повреждения рабочей поверхности медных плит головка удерживается вилкой.
После фиксации головки затравки стопорным штифтом на нее устанавливается набивочный комплект: расходная часть затравки, верхний стальной лист, огнеупорная прокладка, нижний стальной лист, стальные уголки, болты (рисунок 2.12).
Рисунок 2.12 – Головка затравки с набивочным комплектом
После установки набивочного комплекта и удаления стопорного штифта затравка опускается в рабочее положение. При опускании в кристаллизатор головка затравки удерживается
88
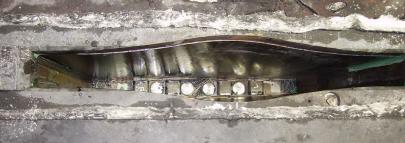
вилкой. При помощи Т-образного шаблона длиной 1000 мм проверяется расстояние от верха кристаллизатора до поверхности основной плиты расходной части затравки.
После установки затравки плиты широких граней кристаллизатора сводятся. В зазор между расходной частью затравки и рабочей поверхностью широких плит кристаллизатора прокладывается и уплотняется трамбовкой каолиновый шнур, засыпается металлическая сечка в качестве холодильников. Вид подготовленного к разливке кристаллизатора приведен на рисунке
2.13.
Рисунок 2.13 – Вид сверху внутренней полости подготовленного к разливке кристаллизатора
Для исключения попадания металла при наполнении кристаллизатора в зазор между рабочими поверхностями плит широких и узких граней стыки плит промазываются силиконовым герметиком. Непосредственно перед поступлением сталеразливочного ковша с металлом на МНЛЗ на рабочие поверхности плит кристаллизатора наносится тонкий ровный слой жидкого графита или смеси масла с графитом.
В период подготовки МНЛЗ проверяется состояние системы вторичного охлаждения: исправность, герметичность и надежность крепления арматуры для подвода воды и воздуха к коллекторам системы вторичного охлаждения, состояние и положение коллекторов относительно роликов и работу форсунок при заданных максимальных расходах охладителя для всего диапазона разливаемых сечений слябов; устраняются утечки воды и воздуха, производится замена засоренных и дефектных форсунок, проверяется правильность их расположения.
89
В поддерживающей системе проверяется:
–состояние роликов, отсутствие скрапин, окалины и других посторонних предметов между роликами;
–исправность, герметичность и надежность крепления арматуры для подвода воды к оборудованию на максимальных расходах;
–система охлаждения оборудования с контролем расходов воды на наличие утечек, при обнаружении утечки устраняются;
–состояние гидроцилиндров;
–герметичность гидравлической системы и системы консистентной смазки;
–вращение приводных роликов с контролем силы тока, а также вращение неприводных роликов в случае использования мерительной головки затравки;
–наличие шумов при холостой прокрутке ручья.
Перед приемкой ковша с жидким металлом проверяется работоспособность и готовность следующих узлов, механизмов
исистем:
–поворотного стенда;
–системы аварийного разворота стенда;
–тележки промежуточного ковша;
–управления стопорами промежуточного ковша;
–механизма качания кристаллизатора;
–поддержания уровня металла в кристаллизаторе;
–системы предупреждения прорывов и подвисаний, отсутствие поврежденных термопар;
–основного гидравлического оборудования;
–первичного контура охлаждения;
–вторичного контура охлаждения;
–третичного контура охлаждения;
–системы обжатия заготовки;
–тянуще-правильной клети;
–маятниковых ножниц;
–устройства парковки затравки;
–промежуточного и транспортного рольгангов;
–основной системы смазки оборудования.
90