
СБОРОЧНЫЕ ЧЕРТЕЖИ
.pdf
21
1.Радиусы скруглений острых кромок и углов 2 мм.
2.* Размеры для справок.
Рукоятка
Рис.12

22
Указывают также размеры, определяющие положение арматуры в материале. Размеры самой арматуры не ставят (рис.12). На арматуру выполняют отдельный чертеж. Для прочной фиксации арматуры в материале на арматуре делают рифления, проточки, вырезы и т.п. На рис.13 показаны примеры такой арматуры.
Для материала отдельный чертеж не выполняют, так как материал поступает на сборку в расплавленном виде или в виде массы и приобретает форму при заливке или опрессовке. Его записывают в спецификацию в графу «Материалы».
Порядок выполнения и оформления чертежей армированных сборочных единиц должен соответствовать требованиям ГОСТ 2.109-73.
Рис.13
2.5. Изображения типовых составных частей изделий
На сборочных чертежах таких широко распространенных изделий, как вентили, пробковые краны, задвижки, насосы, встречаются однотипные по своему назначению устройства. К ним относятся уплотнительные (сальниковые) устройства, крепления золотников (клапанов), маховиков и рукояток на штоках (шпинделях). Знание устройства таких составных частей изделий значительно облегчает чтение и выполнение сборочных чертежей.
2.5.1. Уплотнительные устройства
Уплотнительные устройства различных конструкций применяют для того,

23
чтобы предотвратить утечку рабочей среды (жидкости, пара или газа) или смазочных материалов из рабочей полости механизма или устройства. Для этого в неподвижных соединениях применяют различные прокладки, кольца, а в подвижных - кольца, манжеты, воротники и сальниковые устройства. Материалом для изготовления уплотнителей служат техническая резина, пластмассы, технический войлок, паронит, фторопласт и др.
На рис.14а показано уплотнение, выполненное с помощью резиновой прокладки 1. При уплотнении зазоров между цилиндрическими поверхностями с помощью кольца его размеры подбирают таким образом, чтобы кольцо выступало из проточки, в которую оно заложено (рис.14б).
а) |
б) |
Рис.14 Прямоугольные кольца, устанавливаемые в проточки трапецеидального се-
чения, создают уплотнение за счет деформации (рис.15а). На рис.15б показана форма проточки и обозначены размеры для ее изготовления.
Надежное уплотнение создает сальниковое устройство, изображенное на рис.16. По мере ослабления контакта набивки со шпинделем 1 и со стенками отверстия в крышке 2 набивку поджимают (уплотняют) с помощью сальниковой втулки 3 и накидной гайки 4.
На сборочных чертежах сальниковую втулку 3 показывают выдвинутой до соприкосновения с накидной гайкой 4, которую изображают навинченной на 2 - 3 витка на резьбовой цилиндр крышки 2. Это соответствует начальному рабочему положению сальниковой втулки и накидной гайки (до износа набивки).

24
Рис. 15
Широко применяются стандартные типы уплотнений (кольца, манжеты и др.) (ГОСТ 6608-71). В ГОСТ 5152-84 приведены марки сальниковых набивок для той или иной рабочей среды и рекомендации по их применению.
Типовые конструкции сальниковых устройств приведены на рис.17.
Рис.16

25
26
2.5.2. Крепление золотников (клапанов), маховиков и рукояток на штоках (шпинделях)
Крепление клапанов на головке штока или шпинделя должно обеспечивать свободный поворот клапана и прилегание его к гнезду корпуса. В зависимости от формы и назначения клапана применяют крепления различных конструкций, основные из них показаны на рис.18. Для вентилей с малыми условными проходами крепление клапанов чаще всего осуществляется путем обжима втулки клапана (рис.18 а) или при помощи проволочной скобы (рис.18 б). Для вентилей больших размеров крепление клапанов показано на рис.18 в,г. Для предотвращения самоотвинчивания клапанов применяются специальные стопорные шайбы (рис.18 в).
Маховики и рукоятки могут быть съемными и постоянно установленными. Такие соединения выполняют путем сопряжения плоских поверхностей, т.е. путем посадки маховиков и рукояток на лыску или на квадрат штока. Для преду-
преждения осевого смещения деталей используют стандартные гайки (рис. |
19 а), |
|
которые навинчивают на резьбу хвостовика шпинделя (штока). |
17 |
|
Для арматуры трубопроводов с малыми условными проходами, а такжеРис. |
в |
тех случаях, где не требуется больших усилий для поворота рукоятки или маховика, крепление этих деталей может быть выполнено при помощи штифта или стопорного винта (рис.19 б,в), а также путем расклепывания хвостовика штока
(рис. 19 г).
2.6. Выполнение учебного сборочного чертежа
Сборочные чертежи выполняются либо при проектировании нового, еще не существующего изделия, либо путем вычерчивания изделия с натуры. В курсе машиностроительного черчения сборочные чертежи составляются с готового изделия исключительно по эскизам без обращения к натуре.
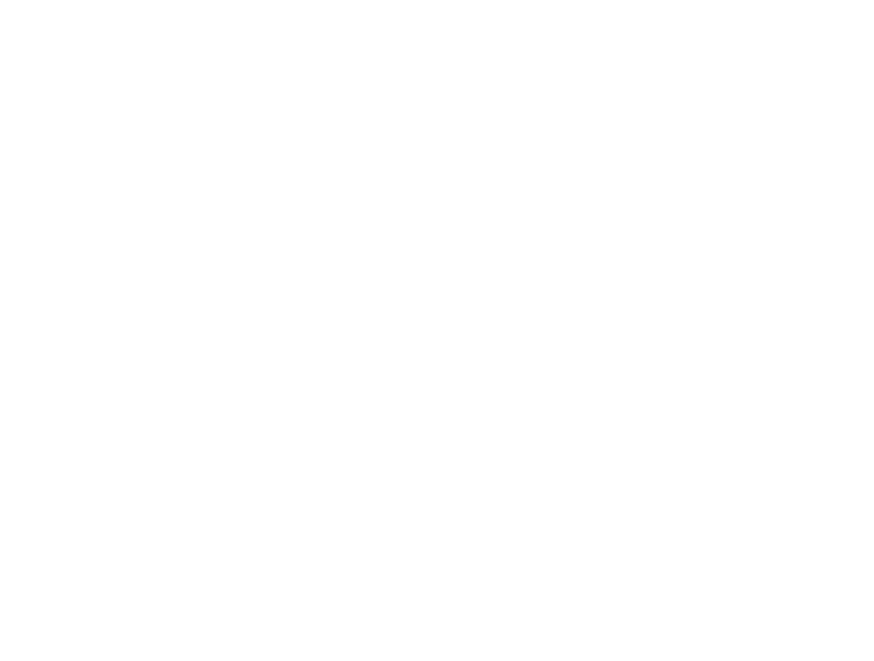
27
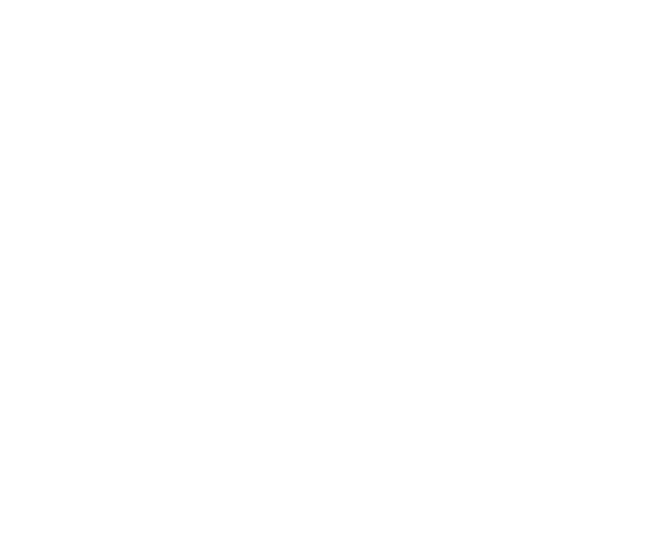
28
Рис.18
Рис.19
Предназначаются эти чертежи для серийного и массового производства. В единичном и мелкосерийном производстве рекомендуется пользоваться чертежами общих видов. По этим чертежам можно представить не только взаимосвязь и способы соединения деталей, но также конструкцию каждой детали в отдельности и принцип работы изделия. В учебной практике разработку сборочных чертежей рекомендуется доводить до требований, предъявляемых к чертежам общего вида.
29
2.6.1. Цель работы
а) Изучение основных положений стандартов ЕСКД: ГОСТ 2.101-68 «Виды изделий»;
ГОСТ 2.102-68 «Виды и комплектность конструкторских документов»; ГОСТ 2.103-68 «Стадии разработки»; ГОСТ 2.104-68 «Основные надписи»; ГОСТ 2.106-96 «Текстовые документы»;
ГОСТ 2.109-73 «Основные требования к чертежам».
б) Приобретение навыков выполнения эскизов деталей с натуры. в) Составление сборочного чертежа по эскизам деталей изделия. г) Приобретение навыков работы со справочной литературой.
2.6.2. Порядок выполнения работы, содержание и оформление
а) Составление структурной схемы.
Ознакомиться с изделием и описанием к нему: выяснить его назначение, рабочее положение, устройство и принцип действия, способы соединения составных частей изделия, последовательность сборки и разборки. Разобрать изделие на составные части, выделив сборочные единицы, отдельные детали, стандартные изделия, материалы, установить их наименования. Составить схему деления изделия на составные части (структурную схему). Схему выполнить на развернутом листе из тетради в клетку (примерно соответствует листу формата А4) с основной надписью по форме 1, ГОСТ 2.104-68 (приложение, стр. 40).
б) Составление спецификации.
Спецификацию составить в соответствии с требованиями ГОСТ 2.106-96. Остальные требования к составлению спецификации подробно рассмотрены выше в пункте 2.2. Пример выполнения приведен в приложении (стр. 41).
в) Выполнение эскизов деталей изделия. Нанесение и увязка размеров. Выполнить эскизы деталей изделия и эскизы сборочных единиц (со специфи-
30
кациями к ним), если таковые входят в состав изделия. При этом учесть рекомендацию ГОСТ2.106-96 (совмещение спецификации со сборочным чертежом). Пример дан на рис.1 приложения. Правила выполнения эскизов, нанесение размеров и основные требования, предъявляемые к эскизам, даны в учебном пособии «Чертежи деталей. Эскизы деталей» [7].
Студентам машиностроительных специальностей следует начать выполнение эскизов с эскиза корпусной детали. Студентам остальных специальностей рекомендуется начать выполнение с эскизов наиболее простых деталей, постепенно переходя к эскизированию более сложных. На эскизе главное изображение детали (вид спереди) следует выбирать независимо от ее рабочего положения в сборке. За главный вид принимают изображение, наиболее полно отражающее форму и размеры детали и отвечающее основной технологической операции ее изготовления. Количество изображений детали должно быть минимальным, но достаточным (оптимальным), чтобы сборочный чертеж можно было выполнить по эскизам, без натуры.
Эскиз каждой детали выполнить от руки на отдельном развернутом листе из тетради в клетку; формат листа А4 или А3 в зависимости от сложности детали (при необходимости допускается применять формат А5), основная надпись по форме 1, ГОСТ 2.104-68 (приложение, рис.1 … 11).
С особым вниманием следует отнестись к нанесению размеров. Детали, из которых собирается сборочная единица, взаимно связаны. Поэтому, проставляя размеры на эскизах таких деталей, необходимо учитывать не только технологию их изготовления, но и конструктивные особенности, а также положение данной детали в изделии (сборочной единице).
Две или несколько деталей, подвижно или неподвижно соединенные друг с другом, называются сопрягаемыми. Поверхности и размеры, по которым происходит сопряжение деталей, также называются сопрягаемыми. Прочие, не связанные между собой поверхности и размеры, называются свободными. Сопрягаемые размеры определяют взаимное положение двух или нескольких деталей в сборочной единице. Они обеспечивают возможность сборки и разборки, а также требуемую взаимозаменяемость.