
Учебный материал / Производственные технологии. А.В.Мовшович.-2006 / Производственные технологии пособие
.pdf
ГЛАВА 17. ОБРАБОТКА МАТЕРИАЛОВ ДАВЛЕНИЕМ
17.1.Сущность и виды обработки материалов давлением
Втехнологии машиностроения под обработкой металлов давлением понимаются различные технологические процессы получения заготовок, полуфабрикатов и готовых изделий пластическим формованием металла в холодном и горячем состоянии. К обработке металлов давлением относятся процессы прокатки, волочения, прессования, свободной ковки, горячей и холодной штамповки.
Большинство процессов обработки металлов давлением отличается высокой производительностью, небольшими отходами, а также возможностью значительного улучшения физико-механических свойств деформируемого металла.
17.2.Производство металлоизделий прокаткой
Металлопрокат преимущественно выпускают металлургические заводы. Однако прокатка металлоизделий в последние годы широко применяется и на машиностроительных и приборостроительных предприятиях, так как является
прогрессивным способом металлообработки. 80 % всех выплавляемых сталей и около 50 % цветных металлов прокатывается.
Сортамент прокатных изделий очень разнообразен: листы, сортовой прокат (профили круглого, квадратного, шестигранного сечений, уголок, швеллер, тавр, двутавр, балки), трубы, специальный прокат. Совокупность профилей и их размеров, а также сплавов, из которых изготавливают прокат, называют сортаментом.
Исходным материалом для проката служат стальные слитки массой до 25 т. На обжимных прокатных станах получают заготовки квадратного профиля. Их называют блюмы и используют для изготовления сортового проката. Слябы – заготовки прямоугольного профиля, из которых получают листы и полосы.
Сущность процесса прокатки заключается в деформации металла между вращающимися валками. Причем, как показано на рис. 17.1, зазор между валками меньше толщины обжимаемой заготовки.
Рис. 17.1. Схема валков различных станов: дуо (блюминг); трио (сортовой стан); кварто (листопрокатный стан)
71
Заготовка толщиной Н захватывается вращающимися валками и за счет сил трения втягивается в зазор между ними. При прокатке подвергается пластической деформации не весь объем материала, а лишь его часть, находящаяся в очаге деформации. Это позволяет обрабатывать большие массы материала при оптимальных энергозатратах и размерах оборудования, производить обработку с огромными скоростями (скорость выхода заготовки из валков может достигать 100 м/с), обеспечивать высокую точность получаемых изделий при минимальном износе инструмента.
Различают три основных способа прокатки: продольная, поперечная и винтовая. Каждый из них можно производить при нагреве обрабатываемых заготовок (горячая) и без нагрева (холодная прокатка).
Продольная прокатка (дуо) наиболее распространена и, как правило, предшествует остальным способам. После прокатывания толщина заготовки уменьшается до величины h. Разность (H–h) между начальным Н и конечным h размерами называется абсолютным обжатием, а отношение – называется степенью обжатия (деформации) или относительным обжатием. Обычно, величина относительного обжатия за один проход не превышает даже для горячего металла 70– 80 %, поэтому получение окончательного профиля достигают многократным прокатыванием заготовки между валками при постепенном уменьшении зазора между ними. При каждом пропуске площадь поперечного сечения постепенно уменьшается, а его форма и размеры приближаются к требуемому профилю.
Различают прокат горячекатаный и холоднокатаный. Если при пластической деформации успевает проходить рекристаллизация (во время нагрева), то такая деформации называется горячей. Обработка металлов давлением в условиях, при которых рекристаллизация не успевает произойти, называется холодной, и металл упрочняется.
Холодной прокаткой получают изделия, у которых площади поперечного сечения относительно небольшие (тонкие листы, тонкостенные трубы и т. д.). Холодная прокатка отличается высокой точностью геометрических размеров металлоизделий и соответствующим качеством поверхностей.
Технологический процесс прокатки
Технологический процесс прокатки включает в себя следующие операции:
•подготовка заготовки к деформации;
•нагрев заготовки (800–1250 оС);
•многократная деформация в прокатных валках;
•резка проката на мерные длины;
•охлаждение и термообработка;
•правка;
•отделка;
•контроль качества;
•упаковка.
Прокатка нагретой заготовки обеспечивает высокое качество проката, минимальный расход энергии, увеличивает обжатие за проход, сокращает аварийные остановки оборудования.
Основным деформирующим инструментом прокатки металлоизделий являются прокатные валки. Они работают в условиях высоких нагрузок, температур и
72
трения скольжения. Валки изготавливают из чугуна, стали и твердых сплавов. Рабочая поверхность валков должна иметь высокую твердость, особенно при холодной прокатке. Диаметр рабочей поверхности валка, в зависимости от назначения прокатного оборудования, может равняться от 1 мм до 1800 мм. Малые диаметры применяют при холодной прокатке изделий из высокопрочных сплавов.
Специальное оборудование для прокатки называют прокатным станом, который включает комплекс технологических машин и устройств. Оборудование прокатного стана подразделяют на основное и вспомогательное. Основное оборудование – главная линия прокатного стана – предназначено для прокатки. На вспомогательном оборудовании прокатного стана выполняют операции, которые делят на четыре основные группы: подготовка металла к прокатке; нагрев металла; транспортировка; отделка и контроль.
Технико-экономические показатели прокатных станов: производительность (часовая, годовая), число часов работы стана в год, расход металла (выход годного %), расходный коэффициент, расход электроэнергии на тонну проката (кВт/т), расход топлива (кДж/т), расход воды (м3/т), расход технологической смазки (кг/т), расход валков (кг/т), количество валков прокатной клети, количество прокатных клетей и их расположение в главной линии, диаметр и длина бочки валков, скорость прокатки (м/с).
17.3. Технология и оборудование процессов волочения и прессования
Волочением называется процесс обжатия металла при протаскивании заготовки через волоку – инструмент с отверстием, сечение которого меньше исходного сечения заготовки. В результате волочения поперечное сечение заготовки уменьшается, а
длина увеличивается. Процесс волочения проводят в холодном состоянии
заготовки и используется для получения тонкой проволоки (от 4 мм до 0,002 мм), калиброванных прутков различного профиля и тонкостенных труб. Изделия имеют точные размеры, заданную геометрическую форму и чистую гладкую поверхность.
Заготовками для волочения служит прокат (катаная проволока, прутки, трубы), а также прессованные профили (прутки, трубы). Для придания изделиям окончательного размера заготовку волочат через несколько последовательно расположенных волок, так как величина обжатия за один проход сравнительно невелика.
Волока (фильер) представляет собой кольцо. Материал волоки выбирается в зависимости от твердости обрабатываемого металла (технический алмаз, металлокерамический сплав или инструментальная сталь).
Технологический процесс волочения состоит из следующих основных стадий:
–подготовки металла (очистка от окалины, нанесение смазки и заделка кон-
цов);
–термообработки материала заготовки – для повышения эластичности;
–волочения по определенному режиму;
–отделки (удаление дефектов, правка, резка на мерные длины, маркировка, консервационная смазка).
Оборудованием для волочения служат волочильные станы двух основных типов: с прямолинейным движением протягиваемых изделий (приводные) и с круговым (барабанные). Различают машины для сухого и мокрого волочения. По
73

количеству одновременно протягиваемых прутков станы бывают однониточные и многониточные.
Прессованием называется процесс выдавливания металла через отверстие матрицы, сечение которого меньше площади сечения исходного металла. Форма отверстия соответствует форме готового изделия. Процесс прессования проводят при температурах горячей обработки давлением в условиях высокой пластичности металла.
Заготовкой для прессования служит либо слиток, либо прокат круглого сечения. Прессованием изготавливают профили сложной формы, которые показаны на рис. 17.2.
Рис. 17.2. Профили прессования
Прессованием получают разнообразные профили из специальных сталей, титановых сплавов и других малопластичных материалов, которые не могут
быть получены другим способом обработки давлением.
Прессование производится на горизонтальных и вертикальных гидравлических прессах. Процесс отличается высокой производительностью, точностью профиля получаемых изделий, простотой замены инструмента (матрицы). К инструменту предъявляются высокие требования, так как он работает в условиях высоких температур и больших нагрузок, его изготавливают из высоколегированных твердых сталей и сплавов.
Метод прессования из-за сложности оборудования и высокой стоимости инструмента применим, в основном, в условиях массового производства сложных профилей.
17.4 Производство металлоизделий ковкой и штамповкой
Свободной ковкой называют способ горячей обработки металлов давлением, при котором нужную форму заготовки получают ударами кувалды, бойка молота или нажатием бойка пресса. Заготовками служат слитки или прокат (круглый, квадратный, прямоугольный). В большинстве случаев поковка служит заготовкой для дальнейшей механической обработки. Различают ручную и машинную свободную ковку.
Ручная ковка для получения мелких штучных поковок производится на наковальне с помощью кувалды и различного вспомогательного инструмента и
74
применяется в основном при ремонтных работах.
Машинная ковка производится на кузнечно-прессовых машинах и позволяет получать поковки массой до 250 т. Мелкие и средние поковки (до 2 т) куют на молотах, а тяжелые на прессах. В чертеже поковки предусматривают по ГОСТу припуски, допуски и напуски, т. е. заведомое увеличение размеров поковки по сравнению с размерами детали. Припуск – превышение размеров поковки над предельными размерами детали, обеспечивающее после обработки резанием необходимые размеры и чистоту поверхности.
Свободной ковкой изготавливают поковки разнообразной формы и размеров. Точность размеров и чистота поверхности поковок невысока, это усложняет и удорожает последующую механическую обработку. Крометого, сампроцесструдоемоки малопроизводителен. Тем не менее, свободная ковка пока является единственным
способом изготовления крупногабаритных поковок для ответственных деталей гидрогенераторов, турбин, прокатного оборудования и т. п.
Листовой штамповкой называют процессы получения изделий или заготовок из листового материала путем деформации его на прессах с помощью штампов.
Холодная листовая штамповка – один из наиболее экономичных и прогрессивных методов изготовления деталей. Детали, полученные листовой штамповкой, отличаются точностью, взаимозаменяемостью и в большинстве случаев не требуют механической обработки. Экономичность процесса обусловлена его высокой производительностью и высоким коэффициентом использования металла (85– 90 %). Холодной листовой штамповкой изготавливают детали для обшивки
вагонов, самолетов, кузова автомобилей и кабины тракторов.
Операции технологического процесса листовой штамповки делятся на два вида: разделительные и формообразующие. К разделительным операциям относятся: отрезка, вырубка, пробивка, надрезка. К формообразующим операциям относятся: вытяжка, формовка, закатка и гибка.
Исходным материалом для листовой штамповки служат листы, полосы и ленты из низкоуглеродистых сталей, цветных металлов и сплавов. Для резки листового металла, поставляемого на предприятия обычно в рулонах или в крупноразмерных листах, применяют ножницы или прессы различных типов. С целью экономии металла, перед вырубкой и закладкой листа в штамп составляется карта раскроя листового металла, на которой указывается наиболее рациональное расположение деталей. При этом все поле листа должно быть использовано.
Штампы (рабочие инструменты) для листовой штамповки бывают простыми для выполнения одной операции и сложными, в которых последовательно или одновременно выполняется несколько операций. Основные рабочие части штампа – пуансон и матрицу (верхняя и нижняя части штампа, соответственно), изготавливают из инструментальных углеродистых или легированных сталей.
Оборудование. Для листовой штамповки применяются гидравлические и механические прессы, листоштамповочные автоматы. Механизация и автоматизация штамповочных работ позволяют повысить производительность труда, избавить рабочих от однообразного труда и полностью его обезопасить.
В связи с внедрением прогрессивных способов формообразования (ОМД) в промышленном производстве непрерывно увеличивается удельный вес кузнечнопрессового оборудования.
75
ГЛАВА 18. ОСНОВЫ ТЕХНОЛОГИИ ЛИТЕЙНОГО ПРОИЗВОДСТВА
18.1. Литейное производство – основная заготовительная база машиностроения
Литейным производством называют процессы получения заготовок деталей машин и разнообразных металлических изделий заливкой жидкого металла в заранее приготовленные формы, где он затвердевает. Полученное изделие называют отливкой. Отливки можно получать массой от нескольких граммов до сотен тонн, простые и сложные по форме. Особенно эффективно применение литья для получения фасонных отливок, отливок из малопластичных, трудно деформируемых металлов и сплавов. Литые детали сложной внешней и внутренней конфигурации стоят намного дешевле, чем такие же детали, изготовленные другими способами. В современных машинах литые детали занимают более 50 % по массе. Основными потребителями отливок являются транспортное, тяжелое и энергетическое машиностроение, станкостроение, производство сельхозмашин. Характерной особен-
ностью способа получения заготовок литьем является техническая и экономическая целесообразность его применения при единичном, серийном и массовом производстве.
Отливки могут быть готовыми деталями или заготовками для последующей обработки резанием. В последнем случае предусматриваются припуски на обработку. Литейные формы могут использоваться один раз или многократно, в связи с этим различают разовые и постоянные литейные формы. Разовые формы разрушаются при извлечении из них отливок. Эти формы могут быть объемными или оболочковыми, их изготавливают из песчано-глинистых или песчано-керамических формовочных смесей. Постоянные формы выдерживают многократную заливку, их делают металлическими (из чугуна, стали или цветных металлов).
18.2. Виды, свойства и получение литейных сплавов
Сплавы, которые используются в литейном производстве, должны обладать высокими литейными свойствами. К литейным свойствам металлов относятся: жидкотекучесть, усадка, ликвация, газопоглощение.
Жидкотекучесть – это способность расплавленного металла заполнять самые тонкие полости формы и образовывать плотные, без внутренних дефектов, отливки.
Усадка – это уменьшение в объеме металла при его затвердевании. Она составляет от 1,5 до 2 % и отрицательно сказывается на свойствах отливок.
Ликвация – это неоднородность химического состава отливки в различных ее зонах. Наибольшая ликвация проявляется у легированных сталей.
Газопоглощение – это способность расплавленного металла вступать в химическую реакцию с кислородом воздуха.
Сплавы, которые используются в литейном производстве, должны обладать высокой жидкотекучестью, минимальной усадкой, наименьшей ликвацией, небольшим газопоглощением и сравнительно невысокой температурой плавления.
Этим требованиям отвечают:
•чугун (серый, высокопрочный, ковкий);
•сталь (углеродистая, легированная);
•медные (бронза, латунь), алюминиевые, цинковые, магниевые сплавы.
76
Наилучшим комплексом литейных свойств обладают серый чугун, бронзы, силумины.
Литейные сплавы получают вторичным переплавом в литейном производстве. Плавка чугуна производится преимущественно в вагранках. Вагранка – это вертикальная шахта-печь непрерывного действия, которая работает на литейном каменноугольном коксе и воздушном дутье.
Выплавка стали производится в плавильных агрегатах литейных цехов, температура плавки достигает 800 оС. В цехах крупного и среднего литья из углеродистой и легированной стали применяются мартеновские печи, электродуговые печи, индукционные высокочастотные печи.
18.3.Способы литья
Взависимости от массовости производства, размеров отливок и требований, предъявляемых к литым деталям, они могут быть изготовлены:
1)литьем в песчано-глинистые формы;
2)литьем по выплавляемым моделям;
3)литьем в постоянные металлические формы;
4)литьем в оболочковые формы;
5)литьем под давлением;
6)центробежным литьем.
Литье в песчано-глинистые формы
Песчано-глинистые формы являются разовыми, объемными. Их получают путем уплотнения специальных материалов, называемых формовочными смесями.
Для приготовления этих смесей используют формовочные кварцевые пески, особые формовочные глины и вспомогательные материалы (древесные опилки, мазут, угольную пыль, тальк). В процессе заливки расплавленного металла органические добавки выгорают и, тем самым, обеспечивают газопроницаемость формовочной смеси. Отверстия и различные полости в отливках получают с помощью специальных фасонных вставок, которые называют стержнями. Их изготавливают из специальных стержневых смесей.
Технологический процесс литья в земляные формы состоит из следующих стадий:
1)приготовление формовочных и стержневых смесей;
2)изготовление модельных комплектов;
3)изготовление форм и стержней;
4)сборка форм;
5)получение литейного сплава;
6)заливка форм;
7)выбивка отливок из форм;
8)обрубка;
9)очистка форм.
Формовочные и стержневые смеси готовят в землеприготовительных отделениях литейного цеха.
Модельным комплектом называют технологическую оснастку, которая включает литейную модель, стержневой ящик, модельные плиты. Модель служит для образования отпечатка, соответствующего наружной конфигурации отливки. В
77
большинстве случаев модели выполняются из двух половинок. В единичном производстве модели выполняются деревянными, а в крупносерийном и массовом – вся модельная оснастка выполняется металлической. Модельная плита предназначена для закрепления на ней одной или нескольких моделей и элементов литниковой системы. Литниковая система – это система каналов, через которые форма заполняется жидким металлом. Для вывода газов из полостей формы и контроля ее заполнения устраиваются вертикальные каналы на самых высоких частях отливки, которые называются выпорами. Для предотвращения образования усадочных раковин в литьевых формах предусматривают специальные полости или прибыли.
Изготовление форм, набивку и уплотнение смеси производят в специальных рамках, называемых опоками. Для заливки металла применяют ручные и механизированные ковши. После затвердевания металла и охлаждения отливок производят их выбивку из форм, очистку и обрубку. Отработанная формовочная смесь транспортируется на переработку в землеприготовительные отделения литейного цеха.
Выбивка отливок из форм – одна из самых тяжелых операций литейного производства. Она сопровождается выделением большого количества тепла и пыли. Сущность процесса выбивки заключается в разрушении формы, освобождении отливок от формовочной земли. Стержни выбиваются пневматическими зубилами на вибрационных машинах. Обрубка литников и выпоров производят с помощью пневматических зубил ленточных и дисковых пил, газовой резки и пр. Очистка отливок от пригоревшей земли и окалины, мелких заусениц производят, чтобы уменьшить трудоемкость последующей механической обработки.
Литье по выплавляемым (вытапливаемым) моделям
Литье по выплавляемым моделям относится к точному литью. Оно состоит в том, что металл заливают в разовую тонкостенную керамическую форму, изготовленную по моделям (тоже разовым) из легкоплавящейся восковой массы, как правило, из смеси парафина со стеарином. Точность размеров и чистота поверхности отливок сокращают объем механической обработки. Технология производства отливок по выплавляемым моделям включает следующие этапы:
•изготовление пресс-форм для моделей;
•получение восковых моделей запрессовкой модельной массы в пресс-формы;
•сборка блока моделей;
•нанесение огнеупорного покрытия на поверхность модели или блока;
•вытапливание моделей из огнеупорных (керамических) оболочек-форм;
•прокаливание форм;
•заливка металла в горячие формы.
Разъемные пресс-формы изготавливают из стали или других сплавов по чертежу детали с учетом усадки модельной массы и металла отливки.
Восковые модели получают запрессовкой модельной массы в пресс-формы с помощью шприца или на запрессовочном станке. Полученные модели извлекают из пресс-форм и облицовывают в несколько слоев огнеупорным покрытием.
Вытапливание восковых моделей из огнеупорных (керамических) оболочек-форм производится горячим воздухом или горячей водой. Прокаливание необходимо для придания форме механической прочности и окончательного удаления восковой массы. Заливка металла производится в горячую форму, что улучшает жидкотекучесть металла и позволяет получать сложные тонкостенные отливки.
78

Внедрения литья по выплавляемым моделям взамен поковок или отливок, полученных другими способами, дает значительный экономический эффект, если в
структуре себестоимости деталей большую долю составляют затраты на металл и фрезерную обработку, особенно при применении трудно обрабатываемых конструкционных материалов.
Литье в кокиль (постоянные металлические формы)
Кокилем называют цельную или разъемную металлическую форму, изготовленную из чугуна, стали, сплавов алюминия или других сплавов. Кокили предназначены для получения большого количества одинаковых отливок из цветных и железоуглеродистых сплавов. Литье в постоянные металлические формы относится к точному литью. Этот метод наиболее прогрессивен. Применяют его в серийном и массовом производстве для изготовления отливок сравнительно несложной формы. Чаще всего его используют для получения цветного литья. Перед заливкой металла кокиль подогревают до температуры 100–300 оС, а рабочие поверхности окрашивают защитными обмазками. Окрашивание удлиняет срок службы кокиля, так как устраняет приваривание металла к стенкам и облегчает извлечение отливок. Подогрев кокиля облегчает заполнение формы металлом. Литье в металлические формы позволяет
снизить расход металла на прибыли и выпоры, получать отливки более высокой точности и чистоты поверхности, улучшить их физико-механические свойства. К недостатком этого способа следует отнести высокую трудоемкость изготовления металлических форм, особенно для производства фасонных отливок. Кроме того, быстрое охлаждение металла затрудняет получение тонкостенных отливок сложной формы.
Схематично процесс литья в кокиль приведен на рис. 18.1.
Рис. 18.1. Литье в кокиль
Литье под давлением
Литье под давлением – способ точного литья, когда жидкий металл заполняет полость металлической формы под давлением. Это один из наиболее производительных методов получения точных фасонных отливок из цветных
79
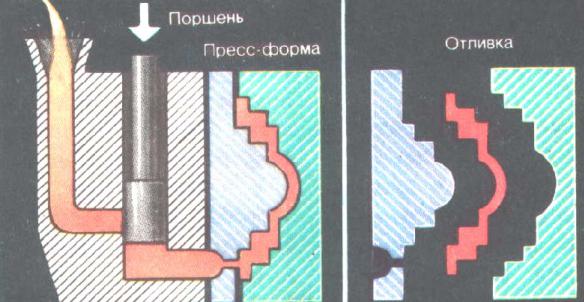
металлов. Для этой цели применяют машины поршневого действия, которые позволяют получать отливки сложных очертаний и толщиной стенок от 1 до 3-х мм. Отливки часто не требуют дальнейшей механической обработки, в них можно получать отверстия, наружную и внутреннюю резьбу, надписи.
Схематично процесс литья под давлением приведен на рис. 18.2.
Рис. 18.2. Литье под давлением
Литьем под давлением можно снизить трудоемкость изготовления отливок в 10–12 раз. Этим способом получают корпусные детали массой до 50 кг, вес которых существенно снижен по сравнению с отливками, полученными литьем в песчаноглинистые формы (в четыре раза) или в кокиль (на 30 %).
Литье в оболочковые формы
Литье в оболочковые формы применяется, главным образом, для получения тонкостенных отливок повышенной точности. Оболочковые формы получают на основе специальных составов, содержащих в качестве отвердителя какой-либо термореактивный полимер, а в качестве наполнителя кварцевый песок. Такая смесь твердеет при 200–250 °С. Поэтому приготовленную смесь наносят на нагретую до этой температуры металлическую модель. Состав отвердевает и получается оболочковая форма. Для повышения механических свойств полученной оболочки ее помещают в печь на 2–3 минуты при температуре 300–350 °С. После извлечения из печи оболочку с модели снимают и направляют на сборку формы. Отливки, полученные в оболочковых формах, отличаются большой точностью и чистотой поверхности. Этим способом получают ответственные детали машин: коленчатые и кулачковые валы, шатуны,
ребристые цилиндры. Высокая точность и чистота поверхности позволяют на 20–
40 % снизить массу отливок, на 40–60 % объем механической обработки.
18.4. Важнейшие проблемы и задачи литейного производства
Проблемы технологии литейного производства:
1. Необходимость плавки или переплавки металлов.
80