
Конструкция Вагонов
.pdf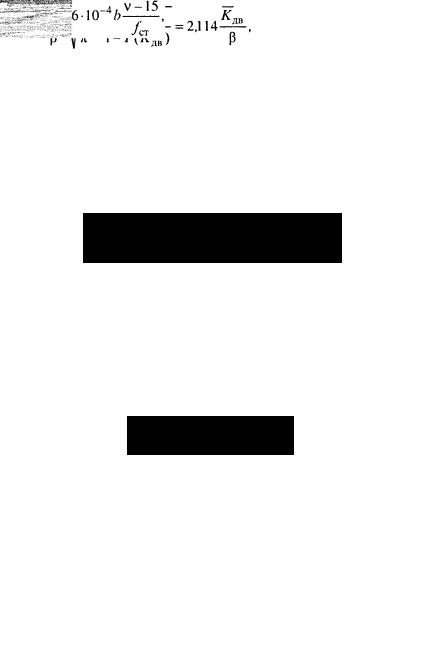
рочиых расчетах элементов вагона, производимых в эксплуатации (при установлении, например, причины транспортных происше- ствий), учитывается фактическая сила тяжести груза и неравномер- ное ее распределение по площади пола.
Сила тяжести груза рассчитывается по формуле:
(1.26)
где >пг — масса груза в вагоне.
Сила тяжести пассажиров с багажом определяется по расчет- ной населенности вагона, т.е.
(1.27)
где— максимальная расчетная населенность вагона;
— средняя масса одного пассажира с багажом: для всех пасса- жирских вагонов принимается
Расчетная населенность пассажирского вагона дальнего следова- ния определяется по наибольшему числу мест, предусмотренных при эксплуатации вагона. Максимальная расчетная населенность ваго- нов межобластного сообщения устанавливается по проектному чис- лу мест для сидения и количеству стоящих пассажиров, из расчет 5 человек на 1 м - свободной площади пола, включая тамбуры и проходы (площадь, занятая ногами сидящих пассажиров шириной 250 мм у края дивана или кресла не учитывается). Максимальная на- селенность второго этажа двухэтажного вагона устанавливается из расчета 4 стоящих пассажира на 1 м2 свободной площади пола.
Сумма собственной силы тяжести вагона и полезной нагрузки составляет силу тяжести (вес) вагона брутто, т.е.
(1.28)
которая приложена в центре масс вагона.
Вертикальная статическая нагрузка от веса вагона брутто, приходящаяся на рассматриваемый элемент,
(1.29)
где — вес частей вагона, через которые передается нагрузка от рас- считываемых элементов на рельсы;
— число параллельно нагруженных рассчитываемых элементов вагона.
42
Для вагона в целом Вертикальная динамическая нагрузка возни-
кает при колебаниях вагона на рессорах и взаимодействии ваго- нов при движении поезда и маневровой работе. Эта нагрузка приложена также в центре масс вагона.
Вертикальная динамическая нагрузка при расчетах на прочность принимается действующей статически и определяется по формуле
(1.30)
где— коэффициент вертикальной динамики.
Коэффициент вертикальной динамики вычисляется по следу- ющей эмпирической формуле
(1.31)
где К s — среднее вероятное значение коэффициента вертикальной динамики;
р— параметр, устанавливаемый по экспериментальным данным: при существующих условиях эксплуатации Р = 1,13 — для
|
|
грузовых вагонов и |
|
— для пассажирских; |
|
|
||||
|
|
— расчетная вероятность |
: при |
расчетах на прочность по допус- |
||||||
|
|
каемым напряжениям принимается |
|
|
|
|
||||
|
Среднее значение коэффициента вертикальной динамики |
|
для |
|||||||
|
|
|||||||||
скорости движения v |
|
15 м/с |
(55 км/ч) определяется по формуле |
|||||||
> |
||||||||||
|
(1.32)
где а — коэффициент, равный для элементов кузова 0.05, для обрессо-
|
|
ренных частей тележки — 0,10, для необрессоренных частей |
||||
|
|
тележки — 0,15; |
||||
b — |
коэффициент, учитывающий влияние числа осей |
|
в тележке |
|||
|
||||||
|
|
или группе тележек под одним концом вагона, |
|
|
||
|
|
|
|
|
||
|
|
|
|
(1.33) |
|
|
|
— |
|
|
|
||
|
расчетная скорость движения вагону, мАв; |
|||||
|
||||||
|
— статический прогиб рессорного подвешивания, м.
43

Вертикальная динамическая нагрузка зависит от скорости движения, а также от конструкции и технического состояния ва- гона и верхнего строения пути.
Характер действия вертикальных статических и динамичес- ких нагрузок в зависимости от времени / показан на рис. 1.15.
Как следует из рис. 1.15, результирующая вертикальная па-
грузка, действующая на вагон, будет равна
(1-34)
Сумма нагрузоквлияет на прочность элементов вагон а разность
характеризует безопасность движения поездо так как при этом происходит обезгруживание колесных пар.
Вертикальная динамическая сила (добавка) на тележку от дей- ствия продольной силы инерции кузова определяется по формуле
(1.35)
где-— продольная сила инерции кузова брутто, определяемая по формулам (1 23) или (1 24);
— расстояние от центра масс кузова до оси автосцепки; _.
— база вагона.
Такая же сила (реакция) действует на опорные элементы кузова.
Рис. 1.15 Характер действия вертикальных статической и динамической нагрузок в зависимости от времени /
44
Боковые нагрузки. К основным расчетным боковым нагруз- кам относятся центробежная сила, сила давления ветра и попе- речная составляющая продольных сил взаимодействия вагонов друг с другом при движении в кривых.
Центробежная сила возникает при движении вагона по кри- вым участкам пути и направлена по горизонтали наружу кривой (рис. 1.16). Она приложена к центру тяжести вагона и стремится опрокинуть вагон.
Центробежная сила определяется по формуле
(1.36)
где v — скорость движения, м/с;
R — радиус кривого участка пути, м.
Для уменьшения действия центробежной силы наружный рельс в кривом участке пути укладывают выше внутреннего. Размер воз-
Рис. 1.16. Схема действия боковых сил, приложенны
прохождении кривого участка пути

вышениязависит от радиуса кривой R, скорости движения v и рассчитывается по формуле
(1.37)
Где 2s — расстояние между кругами катания колес одной колесной пары.
С учетом разгружающего влияния возвышения наружного рельса боковая силасоставит разность центробежной силы и горизонтальной составляющей силы
, т.е.
(1.38)
где— угол, показанный на рис. 1 16.
В практических расчетах центробежная сила, уменьшенная на величину горизонтальной составляющей силы тяжести, определяет- ся в соответствии с рекомендациями Норм приближенно по формуле
|
|
|
|
|
|
|
|
(1.39) |
|
|
|
|
и R: в соответствии с Нормами |
||||
где |
|
— коэффициент, зависящий от |
|
|||||
|
||||||||
|
|
принимают |
|
|
для |
грузовых вагонов и— для |
пассажирских и изотермических вагонов.
О б р а т и т е в н и м а н и е :
•При расчетах рекомендуется учитывать отдельно центробеж- ные силы кузова и тележки. В этом случае в формулу (1.39)
вместо подставляют вес этой части. Равнодействующие указанных сил считаются приложенными в центре соответ- ствующей массы (кузова с грузом и тележек).
Для предварительных расчетов вагонов рекомендуется при- нимать положение центра масс тележки на уровне осей колесных пар, а высоту центра массы груженого кузова над уровнем осей колесных пар, равной 1,7 м для одноэтажных пассажирских ва- гонов, 2,0 м — для грузовых и изотермических и 2,3 м — для двухэтажных пассажирских. Окончательный расчет выполняется по уточненным координатам центров масс.
Сила давления ветра
46
(1.40)
где— удельное давление ветра- согласно Нормам
= 500 Па, F — площадь боковой проекции вагона с учетом груза, м2.
Равнодействующая силы Нв считается приложенной к центру площади F.
Сила давления ветра учитывается только при расчетах па ус- тойчивость вагона от опрокидывания.
Поперечная составляющая продольных сил взаимодействия между вагонами HN возникает в кривых при движении поезда с малой скоростью и маневровой работе и определяется по фор- мулам, которые регламентируются Нормами раздельно для рас- тягивающих (рис. 1.17, а) и сжимающих (1.17, б) продольных сил. Например, при действии растягивающих продольных сил
(1.41)
где . — сила, приложенная вдоль оси корпуса автосцепки, величина которой принимается по табл. 1.2 для I расчетного режима; Н — горизонтальные поперечные силы, действующие на пятники;
— длина вагона по осям сцепления автосцепок;
— радиус кривой: принимается R = 250 м;
— соответственно база вагона и расстояние между упорными плитами автосцепок (рис. 1.17).
Рис. 1.17. Схема дей- ствия поперечной со- ставляющей про- дольных сил взаимо- действиямеждуваго- нами:
а — для случая про- дольных растягиваю- щих сил; б — для случая продольных
сжимающих сил
47

Сила HN прикладывается к раме кузова в плоскости передних упорных угольников автосцепного устройства в случае действия растягивающих сил и в плоскости задних упорных угольников при действии сжимающих сил.
Учет основных нагрузок при расчетах на прочность вагонов.
При оценке прочности вагонов по допускаемым напряжениям основные расчетные нагрузки учитываются в соответствии с рас- четными режимами в сочетаниях, указанных в табл. 1.3.
Таблица 1.3. Сочетания основных сил для расчета на прочность вагонов
Примечание. Нормы 1996 года введены в действие в полной мере только для грузовых вагонов. До их утверждения в части, касающейся пас- сажирских вагонов, разработчикам и изготовителям этих вагонов рекомен- дуется пользоваться Нормами 1983 года.
Сила Рп при суммировании с нагрузками, приведенными в табл. 1.3, учитывается в размере 50%, при суммировании только
с силой тяжести брутто в размере 100%.
Материалы, применяемыев вагоностроении, идопускаемыена-
пряжения. В процессе эксплуатации элементы вагона подверга- ются механическим воздействиям, влиянию коррозии, абразив- ному износу и температурным воздействиям. В связи с этим применяемые в вагоностроении материалы должны быть корро-
зиопно- и износостойкими, технологичными и иметь высокие ме- ханические характеристики.
В вагоностроении применяют стальной прокат и литье, алю- миниевые сплавы и неметаллические материалы.
Стальной прокат является основным строительным материалом для вагонов и идет на изготовление кузовов и час- тично ходовых частей пассажирских вагонов.
Основные несущие элементы кузовов грузовых вагонов выпол- няют из низколегированных сталей 09Г2Д, 10ХНДП и 10Г2БД. Элементы каркаса кузова обычно изготавливают из стали 09Г2Д. Сталь 10ХНДП имеет повышенные механические характеристики и коррозионную стойкость. Поэтому ее рекомендуют применять для обшивки кузова. Перспективной для изготовления несущих сварных и тяжелопагруженных узлов вагона является низколеги- рованная сталь 10Г2БД, имеющая по сравнению со сталью 09Г2Д более высокие прочностные характеристики.
Для изготовления котлов цистерн, предназначенных для пере- возки некоторых кислот, желтого фосфора, расплавленной серы, различных синтетических смол, ядохимикатов, жидких минераль- ных удобрений, молока и особо чистых продуктов используют вы- соколегированные нержавеющие стали. Получили применение двухслойные стали (биметаллы) с плакирующим слоем из высоко- легированных сталей (например, в цистерне для вииоматериалов).
Для кузовов пассажирских вагонов используют как обычные углеродистые стали (15 кп, 15 пс, 20 кп, ВСтЗ), обладающие низ- кой прочностью и коррозионной стойкостью, так и низколегиро- ванные стали 09Г2, 09Г2С и 09Г2Д. Углеродистые стали ограни- чивают возможности снижения массы конструкции и повышения эксплуатационной надежности. Перспективным является приме- нение для обшивки кузова и тонкостенных подкрепляющих эле- ментов каркаса, особенно в его нижнем поясе, нержавеющих ста- лей (например, 12Х18Н10Т). Использование в конструкции ку-
48 |
49 |
зовов пассажирских вагонов нержавеющих сталей, обладающих повышенной коррозионной стойкостью и прочностью, позволяет снизить массу вагона за счет уменьшения сечений.
Стальное литье идет на изготовление деталей тележек грузовых вагонов и автосцепного устройства.
В настоящее время литые детали изготавливают из низколеги- рованной стали повышенной динамической прочности марок 20ГЛ, 20ФЛ, 20ГСЛ, 20ФТЛ и 20Г1ФЛ. Долговечность деталей из сталей этих марок значительно выше, чем углеродистых сталей.
Алюминиевые с п л а в ы применяют в конструкциях грузовых и пассажирских вагонов. Использование алюминиевых сплавов является одним из главных направлений эффективного снижения массы тары вагонов.
Алюминиевые сплавы имеют следующие достоинства: малую объемную массу (в 3 раза больше, чем у стали), высокие механи- ческие характеристики, повышенную коррозионную стойкость, хорошую технологичность и высокую энергоемкость. В то же вре- мя использование алюминиевых сплавов в вагоностроении огра- ничивается вследствие их высокой стоимости и дефицитности.
В России для изготовления кузовов грузовых и пассажирс- ких вагонов применялись технически чистый алюминий и алю- миниевые сплавы марок 1915, АМг5, АМг6, АМг6М и др.
Опыт применения алюминиевых сплавов для изготовления ваго- нов и их частей свидетельствует о перспективности более широкого их использования для создания легких и надежных конструкций.
Неметаллические материалы находят широкое применение в конструкциях грузовых и пассажирских вагонов. К ним относятся полимерные, древесные и резиновые материалы.
Полимерные материалы используют в качестве отделочных (пластик, линолеум), изоляционных (пенополистирол, пенополи- уретан и др.) и конструкционных (стеклопластик).
Древесные материалы применяют для изготовления настилов полов, внутренней обшивки стен и внутреннего оборудования вагонов. В вагоностроении используют древесину хвойных и ли- ственных пород, а также фанеру и плиты (столярные, древесно- стружечные и древесноволокнистые).
Резиновые материалы применяют в качестве амортизирующих устройств в элементах рессорного подвешивания и поглощаю- щих аппаратах автосцепного устройства, а также уплотнителей и звукоизоляции.
Д о п у с к а е м ы е н а п р я ж е н и я [о] в элементах конструкций вагонов устанавливают в зависимости от расчетно- го режима, ответственности и условий работы элемента, свойств используемого материала, опыта эксплуатации и данных экспе- риментальных исследований.
Наибольшие допускаемые напряжения приняты для I расчет- ного режима — режима "большой продольной силы". Допускае- мые напряжения по этому режиму выбираются близкими к преде- лу текучести ат или пределу прочности ав материала с учетом характера действии нагрузки (квазистатическая, ударная и т.п.) и свойств материала. Так для элементов конструкции вагонов, вы- полненных из стали, их принимают [а], = /:,от. При этом коэффи- циент &, обычно устанавливают 0,9-0,95. При расчете по I режиму ударных продольных нагрузок (удара, рывка) [а], = ат. Для котлов цистерн, работающих при высоких температуре (более 100°) и давлении, принимают &, = (0,7-0,95) и k} - 0,8 соответственно.
Допускаемые напряжения по III расчетному режиму устанав- ливаются из пределов выносливости а материала с учетом совме- стного действия квазистатических, вибрационных и ударных на- грузок, влияния коррозии и т.п. В целом они существенно ниже, чем по I режиму. Наиболее низкие значения допускаемых напря- жений принимают для элементов тележек и тормоза, т.е. для эле- ментов, работающих в условиях интенсивного динамического на- гружения и непосредственно связанных с обеспечением безопасности движения.
Оценка устойчивости вагона от опрокидывания. Оценка и про-
изводится при движении вагона по кривым участкам пути для двух случаев опрокидывания: наружу кривой (рис. 1.18, а) и внутрь кривой (рис. 1.18, б).
В первом случае рассматривается его движение с максимальной скоростью в составе поезда. При этом учитываются центробежные силы Н и силы давления ветра И, направленные наружу кривой, а также поперечные составляющие HN продольных квазистатичес- ких сил сжатия N, действующих на вагон через автосцепку.
Во втором случае (случае "стаскивания") рассматривается движение вагона с малой скоростью (когда практически отсут- ствуют центробежные силы) в режиме тяги поезда. При этом учитываются центростремительные силы Н , силы давления вет- ра Н, направленные внутрь кривой, и поперечные составляю- щие Н квазистатических сил тяги N на автосцепках.
N
50 |
51 |
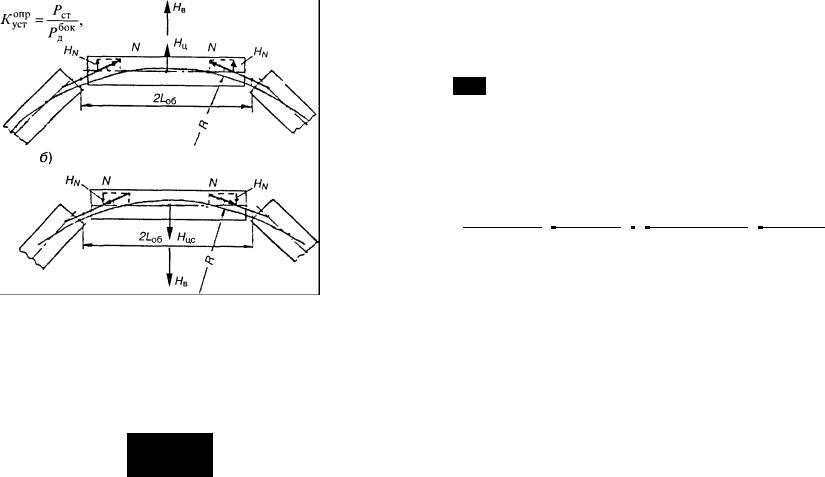
Рис. 1.18. Схема действия сил, учитываемых при оценке прочности вагона от опрокидывания:
а — при опрокидывании наружу кривой; б — при опрокидывании внутрь кривой
Коэффициент запаса устойчивости вагона от опрокидывания §оковыми силами определяется по формуле
(1.42)
где— вертикальная статическая сила давления колеса на рельс (с уче- том обезгрузки при действии вертикальных составляющих про- дольных сил, действующих на вагон через автосцепки);
— динамическая вертикальная сила давления колеса на рельс, вызванная действием боковых сил (с учетом перемещений цен- тров тяжести кузова и тележек).
Силы и
вычисляются по формулам, приведенным в Нормах.
Подсчитанный по формуле (1.42) коэффициент не должен быть меньше допускаемого, т.е. должно сохраняться условие
(1.43)
где — допускаемый коэффициент запаса устойчивости вагона от опрокидывания: принимается равным 1,5 при проверке оп- рокидывания наружу кривой и 1,2 — при проверке опроки- дывания внутрь кривой.
Оценка устойчивости от опрокидывания производится для порожнего и груженого состояний вагона.
1.5. ОСНОВНЫЕ ПОНЯТИЯ О НАДЕЖНОСТИ ВАГОНОВ
Надежность вагонов является одной из основных проблем ва- гоностроения, поскольку безопасность движения поездов во многом зависит от надежности работы узлов и деталей вагонов. Особенность проблемы надежности вагона заключается в ее свя- зи со всеми этапами его жизненного цикла: этапами проектиро- вания, изготовления и эксплуатации. Поэтому для создания ва- гонов требуемой надежности необходимо, чтобы она заклады- валась при его проектировании, обеспечивалась при его изготов- лении и поддерживалась при его эксплуатации.
При проектировании надежность вагона закладывается уров- нем принятых конструктивных решений, применяемыми матери- алами, методами защиты от вредных воздействий, приспособ- ленностью к ремонту и обслуживанию и др.
При изготовлении надежность вагона обеспечивается каче- ством изготовления деталей и сборки узлов, методами контроля, возможностями управления ходом технологического процесса, методами испытаний готовой продукции и др.
При эксплуатации надежность вагона поддерживается приня- той системой его ремонта и технического обслуживания.
Основные понятия и термины. Понятия, термины и определе- ния надежности стандартизированы (ГОСТ 27 002). Рассмотрим основные из них применительно к вагонным конструкциям.
Надежность — свойство объекта сохранять во времени в ус- тановленных пределах значения всех параметров, характеризую-
52 |
53 |
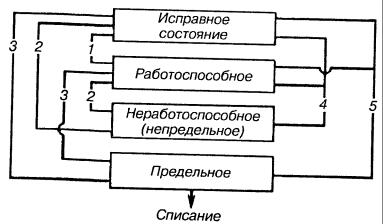
щих способность выполнять требуемые функции в заданных ре- жимах и условиях применения, технического обслуживания, хра- нения и транспортирования.
Применительно к вагоностроению объектом может быть вагон в целом, его узел, сборочная единица, деталь, отдельная система (вен- тиляция, отопление, электрооборудование и др.), элемент системы.
В процессе эксплуатации под воздействием условий работы и других эксплуатационных факторов и происходящих событий вагон может находиться в одном из следующих технических со- стояний: исправном, работоспособном, неработоспособном и предельном (рис. 1.19).
Исправное состояние (исправность) — состояние объекта, при котором он соответствует всем требованиям нормативно-техни- ческой и (или) конструкторской (проектной) документации.
Неисправное состояние (неисправность) — состояние объек-
та, при котором он не соответствует хотя бы одному из требо- ваний нормативно-технической и (или) конструкторской (проек- тной) документации. В зависимости от характера неисправности объект может быть работоспособен или неработоспособен.
Рис. 1.19. Структурная схема технического состояния вагона:
/ — повреждение; 2 — отказ; 3 — переход вагона в предельное со- стояние из-за неустранимого нарушения требований безопасности, сни- жения эффективности эксплуатации, морального старения и других факторов; 4 — восстановление; 5 — ремонт
54
Работоспособное состояние (работоспособность) — состояние объекта, при котором значения всех параметров, характеризующих способность выполнять заданные функции, соответствуют требова- ниям нормативно-технической и (или) конструкторской (проектной) документации. Исправный объект обязательно работоспособный.
Предельное состояние — состояние объекта, при котором его дальнейшая эксплуатация недопустима или нецелесообразна, либо восстановление работоспособного состояния невозможно или нецелесообразно.
Переход объекта из одного состояния в другое обычно про- исходит вследствие повреждения или отказа. Перевод объекта из предельного и неработоспособного состояний в работоспособ- ное осуществляется соответственно при помощи ремонта и вос- становления (рис. 1.19).
Повреждение — событие, заключающееся внарушенииисправно- го состояния объекта при сохранении работоспособного состояния.
Отказ — событие, заключающееся в нарушении работоспо- собного состояния объекта. Это основное понятие, используе- мое в теории надежности.
Различают отказ вагона и отказ элемента вагона. Признаками отказа вагона являются такие неисправности, при которых он не может быть включен в состав поезда или не допускается его следо- вание в составе поезда. Эти неисправности определены действую- щими инструкциями и Правилами технической эксплуатации же- лезных дорог (ПТЭ). Отказом элемента вагона является техни- ческая неисправность элемента вагона, требующая его замены, и устраняемая за время, установленное для технического обслужива- ния в поезде. В противном случае это будет уже отказ вагона.
По причинам возникновения отказы можно разделить на кон-
структивные, производственные и эксплуатационные.
В зависимости от того, может ли быть работоспособность объекта восстановлена в рассматриваемой ситуации после воз- никновения отказа или не может, объект называют восстанавли-
ваемым или невосстаиавливаемъш. Вагон в целом является вос-
станавливаемым объектом, а отдельные его детали могут быть как восстанавливаемыми, так и невосстанавливаемыми.
Наработка — продолжительность или объем работы объекта. Ресурс — суммарная наработка объекта от начала его эксплу- атации или ее возобновления после ремонта до перехода в пре-
дельное состояние.
55
Срок службы — календарная продолжительность эксплуата- ции от начала эксплуатации объекта или ее возобновления после ремонта до перехода в предельное состояние.
Назначенный ресурс иназначенный срок службы — соответствен-
но суммарная наработка и календарная продолжительность экс- плуатации, при достижении которых эксплуатация объекта долж- на быть прекращена независимо от его технического состояния.
Надежность — комплексное свойство, состоящее в общем случае из безотказности, долговечности, ремонтопригодности и сохраняемости.
Безотказность — свойство объекта непрерывно сохранять ра- ботоспособное состояние в течение некоторого времени или на- работки.
Долговечность — свойство объекта сохранять работоспособ- ное состояние до наступления предельного состояния при уста- новленной системе технического обслуживания и ремонта.
Ремонтопригодность — свойство объекта, заключающееся в приспособленности к поддержанию и восстановлению работоспо- собного состояния путем технического обслуживания и ремонта.
Сохраняемость — свойство объекта сохранять в заданных пределах значения параметров, характеризующих способности объекта выполнять требуемые функции, в течение и после хране- ния и (или) транспортирования.
Основные показатели надежности. Для количественной харак-
теристики надежности объекта установлена система показате- лей, которая подразделяется в общем случае на четыре группы (по числу свойств, составляющих надежность объекта): показа- тели безотказности, долговечности, ремонтопригодности и со- храняемости. Для вагонов и их элементов в качестве основных приняты три первые группы.
Безотказность количественно оценивается следующими пока- зателями надежности (показателями безотказности): вероятностью безотказной работы, интенсивностью отказов, па- раметром потока отказов, средней наработкой до отказа и сред- ней наработкой на отказ.
Вероятность безотказной работы — вероятность того, что в пределах заданной наработки отказ объекта не возникнет. Она выражается отношением числа объектов, отказавших в рассмат- риваемом интервале времени, к числу объектов, работоспособ- ных в начальный момент времени.
56
Интенсивность отказов (для невосстанавливаемых объектов) — отношение числа отказов объектов в единицу времени к общему числу объектов, работоспособных в начальный момент времени.
Параметр потока отказов (для восстанавливаемых объектов) — число отказов объектов в единицу времени.
Средняя наработка до отказа — отношение суммарной нара-
ботки эксплуатируемых объектов к числу этих объектов. Средняя наработка на отказ (для восстанавливаемых объек-
тов) — отношение суммарной наработки объекта к числу его отказов в течение этой наработки.
К показателям долговечности относятся гамма- процентный ресурс, средний ресурс, гамма-процентный срок службы и средний срок службы.
Гамма-процентный ресурс и гамма-процентный срок службы —
соответственно суммарная наработка и календарная продолжи- тельность эксплуатации, в течение которых объект не достигнет предельного состояния с вероятностью g, выраженной в процентах.
Средний ресурс и средний срок службы равны средним значе-
ниям соответствующих величин.
Показателями ремонтопригодности являются: вероятность восстановления, среднее время восстановления и средняя трудоемкость восстановления. Для вагонов основным показателем ремонтопригодности является среднее время восста- новления — среднее время восстановления работоспособного состояния объекта после отказа.
Основным п о к а з а т е л е м сохраняемости явля-
ется средний срок сохраняемости.
Основные задачи, решаемые теорией надежности. На этапе проектирования теория надежности занимается определением ве- роятности безотказной работы и сроков службы вагона и его элементов с учетом прогнозирования режима работы его на пер- спективу и поиском оптимального конструктивного решения. С позиции надежности оптимальной будет такая конструкция, при которой с наименьшими затратами средств достигается тре- буемая продолжительность работы отдельных элементов и ваго- на в целом при заданной безотказности и регламентированных затратах на ремонт и техническое обслуживание.
На этапе изготовления вагонов теория надежности решает комплекс вопросов, связанных с обеспечением требуемого каче- ства. Главная задача вагоностроения — повышение качества из-
57
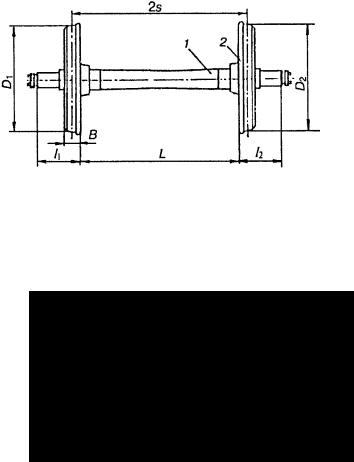
готовления и надежности эксплуатации вагона. Решение этой проблемы основано на системном подходе на всех трех этапах: проектирования, изготовления и эксплуатации. К факторам, оп- ределяющим качество вагона при проектировании и изготовле- нии, относятся: качество нормативно-технической документации, качество оборудования, инструмента и приспособлений, качество сырья, материалов и комплектующих изделий и качество труда исполнителя. Поскольку сами эти факторы являются случайными величинами, задача сводится к выявлению закономерностей рас- пределения параметров, характеризующих их, а затем к разработ- ке методов воздействия на параметры, при которых обеспечива- ется высокое качество.
На этапе эксплуатации вагонов теория надежности решает целый комплекс задач, к которым относятся: оценка потери ва- гоном работоспособности путем сбора соответствующей инфор- мации и использование ее в процессе управления надежностью на стадии проектирования, изготовления и эксплуатации; оцен- ка восстанавливающей способности существующей системы тех- нического обслуживания (СТО) и ремонтной базы; диагностика неисправностей вагона; рациональное использование ремонтоп- ригодности вагонов при техническом обслуживании и ремонте; оптимизация системы технического обслуживания и ремонта. В свою очередь оптимизация СТО и ремонта решает другие важ- нейшие вопросы: размещение по сети дорог вагоноремонтных заводов, вагонных депо, пунктов подготовки вагонов к перевоз- кам, пунктов технического обслуживания; оптимизация пробега вагонов между плановыми видами ремонта; рациональное обес- печение ремонтных объектов материалами и запасными частя- ми; обоснование состава и квалификации работающих в СТО и на ремонтных объектах; обоснование организации восстанови- тельных работ и т.д.
!• КОЛЕСНЫЕ ПИРЫ_________________
2.1.НАЗНАЧЕНИЕ. УСТРОЙСТВО И ОСНОВНЫЕ РАЗМЕРЫ КОЛЕСНЫХ ПАР___________________________
Колесные пары относятся к наиболее ответственным элементам ходовых частей вагона. Они направляют движение вагона по рельсовому пути и воспринимают все нагрузки от вагона на рельсы и обратно.
В связи с этим колесные пары должны:
обладать достаточной прочностью — для обеспечения безо-
пасности движения; иметь небольшую массу — для снижения массы вагона и
уменьшения динамического воздействия на путь; обладать упругостью — для смягчения динамических сил,
возникающих при движении вагона.
Типы, основные размеры и технические условия на изготовление вагонных колесных пар определяются Государственными стандар- тами, а содержание и ремонт — Правилами технической эксплуата- ции железных дорог (ПТЭ) и Инструкцией по осмотру, освидетель- ствованию, ремонту и формированию вагонных колесных пар.
Колесная пара (рис. 2.1) состоит из оси 1 и двух колес 2.
Рис. 2.1. Колесная пара
59

Тип к о л е с н о й п а р ы определяется типом оси и ди; метром колес. Для вагонов магистральных железных дорог ил рокой колеи, кроме моторных вагонов электро- и дизель-пое: дов (ГОСТ 4835), выпускаются два типа колесных пар РУ1-95
иРУ1Ш-950 с диаметром колес 957 мм (табл. 2.1). Кроме тоге
вэксплуатации находятся еще два типа колесных пар РУ1-950 РУ1Ш-950 с диаметром колес 950 мм.
Таблица 2.1. Типы колесных пар вагонов
Тип колесной пары Тип колесной пары Тип оси Диаметр колеса, мм
Диаметр колеса, мм
1>У1 - 950 |
~~~ РУ1 |
957 |
957 |
|
РУ1 |
|
РУ1 |
|
|
РУ1 |
- |
У |
957 |
957 |
"РУ1Ш - 950 |
|
|||
|
|
РУ1Ш |
|
|
П р и м е ч а н и е . В типе колесной пары должен указываться номинальный диаметр колеса. В новом стандарте на вагонные колеса (ГОСТ 9036) он изменен с 950 на 957 мм. Однако, поскольку ГОСТ на колесные пары еще не пересмотрен, то в табл. 2.1 приводятся обо- значения их типов по действующему стандарту.
Все типы колесных пар, приведенные в табл. 2.1, предназна- чены для подшипников качения. Буквы РУ и Ш в обозначении типа оси означают: Р — роликовая, т.е. для подшипников каче- ния; У — унифицированная, т.е. для грузовых и пассажирских вагонов; Ш — крепление подшипников при помощи шайбы.
Колесная пара является тем элементом, который обеспечивает непосредственный контакт вагона и пути. От точности геометри- ческих размеров и других параметров колесной пары в значитель- ной мере зависит безопасность движения и ходовые качества ва- гона. В связи с этим стандартом (ГОСТ 4835) регламентированы основные размеры новой колесной пары (рис. 2.1).
Расстояние L между внутренними боковыми поверхностями обо-
дьев колес составляет: для колесных пар, предназначенных для ско- ростей движения до 120 км/ч, — 1440^; свыше 120. но не более 160 км/ч — 1440^ мм. Таким образом, для вагонов, рассчитанных на большую скорость движения, зазор между1ребнем колеса и рель- сом на 1 мм меньше, а следовательно, меньше и допускаемый разбег колесной пары в колее. В результате уменьшения поперечного сме- щения колесной пары относительно рельсов снижаются боковые
60
силы, передаваемые от колес на рельсы, износ колес и пути, со- противление движению, повышается устойчивость колесной пары от схода с рельсов, улучшается плавность хода вагона.
Уменьшение зазора между колесом и рельсом достигается также увеличением толщины гребня. Поэтому для вагонов, экс- плуатирующихся со скоростями от 120 до 140 км/ч, минималь- ная толщина гребня колеса составляет 28 мм, а при скоростях от 140 до 160 км/ч — 30 мм, против альбомного размера 33 мм.
При напрессовке колес на ось возможна их неточная установ- ка по отношению к торцам оси при строго выдержанном разме- ре между внутренними гранями ободьев. Разность консолей
колесной пары не должна поэтому превышать 3 мм. Консоль — расстояние от торца шейки оси до внутренней боковой поверхности обода колеса. Чем меньше, тем более симметрично установлены колеса на оси.
Колеса, укрепленные на одной оси, должны иметь разность диаметров по кругу катанияне более 1 мм.
Это уменьшает перекос колесной пары и снижает интенсивность проскальзывания колес по рельсам при движении.
При движении с большими скоростями важное значение имеет
уравновешенность колесной пары. Для снижения инерционных сил,
возникающих из-за неуравновешенности (дисбаланса), колесные пары вагонов, эксплуатируемых со скоростью свыше 140 км/ч, под- вергают динамической балансировке на специальном балансиро- вочном оборудовании. Значение допускаемого дисбаланса в плос- кости каждого колеса относительно оси, проходящей через центры кругов катания колес, должно быть не менее 6 Н.м для вагонов, эк- сплуатируемых со скоростями движения от 140 до 160 км/ч.
Колесные пары пассажирских скоростных вагонов и вагонов дизель-поездов оборудованы дисковыми тормозами (рис. 2.2) и поэтому состоят из оси /, двух колес 2 и двух тормозных дисков 3.
Рис. 2.2. Колесная пара с дисковым тормозом
61