
3302 ЭИ
.pdf• определяя соотношение фаз для доэвтектического белого чугуна с содержанием 2,5 % углерода при температуре 900 °С, в котором имеются структурные составляющие – аустенит, цементит вторичный и ледебурит, следует сначала выявить фазы, из которых состоит сплав при данных условиях (аустенит и цементит), и далее определить их количество в процентах. При этом важно учесть, что перлит и ледебурит являются механическими смесями фаз (перлит = феррит + цементит; ледебурит = аустенит + цементит; при температурах ниже 727 °С ледебурит состоит из перлита и цементита или, в конечном итоге, из ферритаицементита). ПризаданнойтемпературефазовыйсоставсплаваА+ Ц=100 %.
Вопросы 91–120 требуют знания маркировки и свойств легированных сталей, твердых сплавов, цветных сплавов, а также процессов термической и химико-термической обработки. Отвечая на них, необходимо привести полный химический состав и свойства рассматриваемого материала, указать влияние легирующих элементов, привести примеры применения этих материалов на железнодорожном транспорте.
Следует указать, какие именно легирующие элементы или их сочетания придают сталям требуемые свойства, например, повышение прочности и вязкости, жаропрочности и жаростойкости и т. д., и как эти элементы влияют на поведение легированных сталей в процессе их термической обработки. Так, температура отпуска легированных сталей выбирается несколько выше, чем для обычных углеродистых сталей, так как легированный аустенит более устойчив, учитывается возможная отпускная хрупкость и т. д.
Вопросы 121–150 относятся к термической и химико-термической обработке конструкционных и инструментальных сталей. Для ответа на них необходимо знать превращения в сталях по диаграмме состояний «железо–цементит», принципы классификации сталей и процессы, происходящие при нагреве и охлаждении аустенита, а также классификацию видов термической обработки и их назначение. Отвечая на эти вопросы, нужно начертить необходимый участок диаграммы состояний (стальной уголок) «железо– цементит» и нанести на него ординату сплава, соответствующего марки сплава по заданию. На ординате указать температуры нагрева для соответствующих видов термической обработки (закалка полная, неполная, отпуск низкий, средний или высокий, ХТО), выбрать охлаждающую закалочную среду.
Послеэтоговкоординатах «температура–время» следуетпостроитьграфиктермической обработки. Приэтомвремянагрева, выдержкииохлаждения можноназначатьусловно.
Необходимо указать цель того или иного вида термической или химикотермической обработки, обосновать выбранные температуры нагрева, описать превращения. Нужно указать структуру в исходном, промежуточном (в нагретом до оптимальной температуры) и конечном состояниях.
При необходимости применения поверхностной закалки или химико-термической обработки следует изложить их сущность.
Следует обращать внимание на технико-экономическую эффективность внедрения полимерных материалов как заменителей дорогостоящих и дефицитных материалов из металлических сплавов, например, цветных металлов, ценных пород древесины. Необходимо вначале ознакомиться с классификацией синтетических смол по ГОСТ, составом и свойствами пластических масс.
Рекомендуется приводить конкретные примеры использования того или иного полимерного материала. Важно оценить состав и свойства синтетического клея (адгезию и когезию – прочность клеевого слоя) в связи с технологией склеивания и влиянием влаги, масла, бензина, а также температуры.
При описании технологических методов переработки пластмасс в изделия нужно приводить схемы процессов с необходимыми пояснениями.
21
Диаграмма состояния двойного сплава Fe–C (Fe–Fe 3 C)
Диаграмма определяет в условиях равновесия фазовый состав сплава в зависимости от температуры и концентрации компонентов, позволяет качественно характеризовать многие физико-химические, механические и технологические свойства сплавов. На основе анализа диаграммы состояния решаются инженерные задачи, а именно можно определить, какие сплавы и в каком направлении изменяют свою структуру (нагрев и охлаждение), изменение структуры и свойств при переходе к неравновесному состоянию, зависящему от реальных условий производства изделий и заготовок.
Превращения в зависимости от состава сплава могут протекать различно, а следовательно, сплавыимеютразныепохарактерутемпературныекривыеохлаждения(нагревания).
В системе «железо – углерод» выделяются сплавы с превращениями:
•перитектическими и доэвтектоидными (0,16 < C < 0,8 %)
•эвтектоидным (С = 0,8 %)
•заэвтектоидными (0,8 < C < 2,0 %)
•доэвтектическими (2,0 < C < 4,3 %)
•эвтектическим (С = 4,3 %)
•заэвтектическими (4,3 < C < 6,67 %)
Первичная кристаллизация, т. е. кристаллизация из жидкого состояния, протекает для чистого железа при температуре t = 1539 °C, для эвтектического сплава белого чугуна t =1147 °C, для химического соединения Fe3C t = 1260 °C с выделением тепла, вследствие чего на кривых охлаждения при температуре затвердевания обнаруживаются остановки (обозначаются горизонтальными участками кривой охлаждения).
Первичная кристаллизация остальных сплавов происходит в интервале температур: 1539 до 1390 °C – доэвтектоидные стали;
1499 до 1147 °C – заэвтектоидные сталеи;
1480 до 1147 °C – доэвтектические белые чугуны;
1260 до 1147 °C – заэвтектические белые чугуны.
Начало процесса кристаллизации этих сплавов отмечается перегибом на кривой охлаждения. Окончание процесса кристаллизации может в зависимости от числа фаз характеризоваться на кривой охлаждения перегибом (стали) или горизонтальным участком (белые чугуны). Перегиб характеризует быстрое превращение во времени, горизонтальный участок характеризует замедленное превращение во времени, связанное с выделением тепла (охлаждение) или с поглощением тепла (нагрев).
В сплавах в виде механических смесей (гетерогенные системы), образующих эвтектику, в момент окончания затвердевания на линии солидус находятся в равновесии три фазы: кристаллы аустенита Feγ(С ≈ 2 %), цементита первичного Fe3C (C = 6,67 %) и жидкая фа-
за. В соответствии с правилом фаз это равновесие нонвариантное, число степеней свободы С = 2 + 1 – 3 = 0, и отмечается горизонтальный участок при температуре (t = 1147 °C).
Правило фаз показывает, происходит ли процесс кристаллизации при постоянной температуре или в интервале температур, и указывает, какое число фаз может одновременно существовать в системе. Число степеней свободы – это число независимых переменных внутренних (состав фаз) и внешних (температура, давление) факторов, которые можно изменять без изменения числа фаз, находящихся в равновесии. Правило фаз и определение числа степеней свободы выражается формулой:
С = К + 1 – Ф,
где К – число компонентов в системе; Ф – число фаз; С – число степеней свободы.
22
Положение основных точек метастабильной диаграммы Fe–Fe3C
Точка |
t, °C |
Концентрация углерода |
|
|
(по массе), % |
A |
1539 |
0,00 |
B |
1499 |
0,51 |
C |
1147 |
4,30 |
N |
1392 |
0,00 |
H |
1499 |
0,10 |
J |
1499 |
0,16 |
E |
1147 |
2,14 |
G |
911 |
0,00 |
S |
727 |
0,80 |
P |
727 |
0,02 |
Q |
20 |
0,006 |
Чтобы указать протяженность горизонтального участка на кривой охлаждения, следует выбрать масштаб, соответствующий содержанию 100 % эвтектики. Удобно принять горизонтальный участок на кривой эвтектического сплава длиной 10 мм, по правилу отрезков определить относительное количество эвтектики, образующейся при кристаллизации сплава (доэвтектический и заэвтектический чугуны) и показать кристаллизацию эвтектики в виде горизонтального участка, соответствующего по длине ее относительному количеству (< 10 мм). При наличии в сплаве 50 % эвтектики на кривой охлаждения сплава будет горизонтальная линия длиной 5 мм.
Сплавы с перитектическим превращением содержат углерода 0,1…0,5 %. На кривой охлаждения фиксируется:
-перегиб, указывающий начало кристаллизации с выделением из жидкого сплава кристаллов, богатых тугоплавким компонентом (высокотемпературный феррит – область АНJВ);
-горизонтальный участок, отвечающий перитектической реакции (НJВ), на котором
вусловиях равновесия находятся три фазы: кристаллы феррита высокотемпературного, богатые тугоплавким компонентом, жидкость и кристаллическая фаза с легкоплавким компонентом – аустенитом (НJN);
-перитектическое превращение (t = 1499 °C) сплавов с содержанием углерода 0,16 % заканчивается затвердеванием с образованием структуры феррит и аустенит; для
сплавов с содержанием углерода 0,16…0,5 % имеет место превращение феррита высокотемпературного (ФВ) в аустенит:
Ж + ФВ → Ж + А.
Вторичная кристаллизация – превращение в затвердевшем сплаве (Ж = 0 %) обуславливается полиморфными превращениями, полным (или частичным) распадом твердого раствора. В чистом железе превращения в твердом состоянии (полиморфное) протекает при постоянной температуре, поэтому на кривых охлаждения (нагревания) при температуре превращений наблюдается горизонтальный участок:
А→ Ф.
Вдоэвтектоидных сталях без перитектических превращений (С = 0,5…0,8 %) первичная кристаллизация начинается при t =1499 °C с выделения из аустенита жидкой фазы, сплав Ж +А состоит из двух фаз, и процесс кристаллизации заканчивается на линии
23
солидус. Сплав имеет однофазную структуру аустенита, содержание углерода в котором соответствует содержанию углерода жидкого сплава.
В доэвтектоидных сплавах (С < 0,8 %) вторичная кристаллизация протекает в следующей последовательности: полиморфное превращение железа Feγ → Feα в интервале
температур 910…727 °C и насыщение аустенита углеродом. Полиморфизм приводит не только к образованию феррита (твердый раствор Feα с содержанием углерода до 0,02 %),
но и к повышению в аустените содержания углерода до 0,8 %.
В заэвтектоидных сплавах (0,8 < C < 2,0 %) в интервале температур (линии SE–SK) из аустенита выделяется цементит вторичный. Содержание углерода в аустените при температуре 727 °С составляет 0,8 %, на линии перлитных превращений А0,8 → П0,8, то есть имеет место полиморфное превращение А0,02 → Ф0,02 с выделением кристаллов цементита вторичного. Процесс заканчивается образованием структуры П + ЦII. Содержание углерода в перлите составляет 0,8 %, в цементите – 6,67 %.
Всплаве с содержанием углерода 0,4 % в соответствии с диаграммой имеются 5 точек, характеризующих фазовые превращения при понижении температуры (рис. 1).
Вточке 1 t =1500 °С начинается кристаллизация Ж0 ,4 с выделением из нее ферри-
та. В интервале температур 1500…1499 °C, С = 2 + 1 – 2 = 1. Охлаждение до t = 1499 °C (точка 2) приводит к изменению химического состава жидкой фазы и феррита. В точке 2 сплав испытывает перитектическое превращение, С = 2 + 1 – 3 = 0.
Ф0 ,1 + Ж0 ,51 → А0 ,16 + Ж0 ,51(ост) или
ФН + ЖВ → АJ + ЖВ(ост) .
Ниже линии JB (точка 2) сплав двухфазный: А + Ж, С = 2 + 1 – 2 = 1. Кристаллизация закончится по достижении температур, соответствующих линии солидус JЕ. После затвердевания сплав приобретает однофазную структуру А0 ,4 (0,4 % – содержание углерода в ау-
стените). Точка 3 диаграммы показывает температуру конца кристаллизации 1450 °C. Охлаждение сплава до точки 4 t4 = 820 °C приводит к измельчению зерен аустенита
без изменения химического состава. С дальнейшим понижением температуры по границам зерен аустенита образуются зародыши феррита, которые растут, превращаясь в зерна. Количество А (аустенита) уменьшается, а содержание в нем углерода увеличивается, так как Ф (феррит) почти не содержит углерода, С = 2 + 1 – 2 = 1.
На линии перлитных превращений (точка 5) содержание углерода в аустените достигает 0,8 %. Аустенит, имеющий эвтектоидную концентрацию, распадается с одновременным выделением из него феррита и цементита вторичного, образующих механическую смесь под названием перлит.
A = Ф + Fe C .
1S442Р 443
перлит
Эвтектоидное превращение AS протекает при постоянной температуре (площадка
на кривой охлаждения) 727 °C. При наличии 3 фаз (Ф0 ,02 ,Ц6 ,67 ,А0 ,8 ) – система нонвариантная (С = 2 + 1 – 3 = 0). Ниже точки 5 сплав имеет структуру: феррит + перлит, и эта структура сохраняется и до температуры окружающей среды (комнатной температуры), С = 2 + 1 – 2 = 1. Сплав такого фазового состава называется доэвтектоидной сталью, содержит углерода 0,4 %.
24
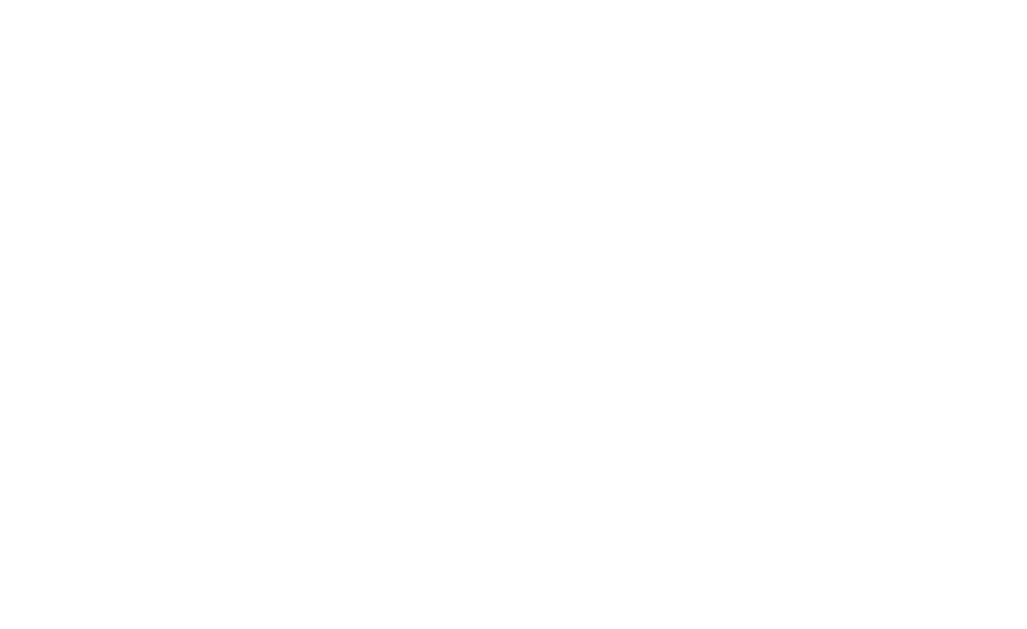
25
Рис. 1. Диаграмма состояния «железо–углерод»
Пример решения задачи по термической обработке детали из углеродистой стали
Термическая обработка представляет собой комплекс операций, выполняемых последовательно: нагрев, выдержка и охлаждение.
Параметрами процесса ТО детали и инструмента являются:
•скорость нагрева до температуры tmax ( VH );
•максимальная температура нагрева сплава определяется по диаграмме Fe–Fe3C для углеродистых сталей и по справочникам для легированных сталей;
•продолжительность выдержки сплава при температуре нагрева (tнагр ) определя-
ется экспериментально;
• скорость охлаждения нагретой детали (Vохл ) выбирается в зависимости от того,
какую структуру (равновесную, неравновесную) требуется получить.
Технически допустимая (технологическая) скорость нагрева (VH ) устанавливается в
зависимости от химического состава стали, структуры, конфигурации изделий, интервала температур нагрева. Скорость нагрева определяется теплопроводностью металла. Изделия из углеродистой стали толщиной до 100–120 мм нагревают с любой скоростью, скорость нагрева изделий из легированных сталей в 2–3 раза меньше.
Время выдержки при температуре нагрева (tmax ) необходимо для завершения про-
цессов фазовых (получение аустенита однородного) и структурных превращений по всему объему изделий.
Охлаждение деталей сопровождается отводом теплоты, динамика процесса определяется теплопроводностью сплава и конвекцией. В процессе охлаждения формируется структура равновесная (отжиг, нормализация) или неравновесная (закалка полная или неполная). Для получения структуры равновесной скорость охлаждения должна быть минимальной, а для неравновесной – максимальной. Критической скоростью закалки называется наименьшая скорость охлаждения, при которой аустенит превращается в мартенсит (процесс бездиффузионный). Критическая скорость закалки является функцией химического состава стали. Низкоуглеродистые стали (С < 0,3 %) в практических условиях охлаждения образуют мартенсит реечный (пакетный) с минимальной твердостью. Двойниковый (пластинчатый) мартенсит образуется в сталях с содержанием С > 0,3 %, между пластинами мартенсита при комнатной температуре сохраняется остаточный аустенит. Пластинчатый мартенсит имеет максимальную твердость.
Закалка на мартенсит является промежуточной операцией ТО. Закаленные детали подвергают повторному нагреву ниже t = 727 °C, выдержке при нагреве и охлаждению. Производят отпуск обычно на воздухе. Отпуск обеспечивает уменьшение внутренних напряжений после закаливания с образованием мартенсита (низкий отпуск) и получения структур, приближающихся к промежуточным структурам типа троостита (средний отпуск) и сорбита (высокий отпуск). Твердость сплава снижается, максимальную твердость имеет сплав со структурой мартенсит.
Многолетней эксплуатационо-производственной практикой установлены три основные группы изделий, требующие «своих» специфических вязкостно-прочностных комплексов и других технических характеристик:
•режущие и измерительные инструменты;
•штампы для холодной штамповки (HRC > 58 – структура мартенсит или мартенсит с карбидами);
•рессоры, пружины (40 < HRC < 58 – структура троостит);
26
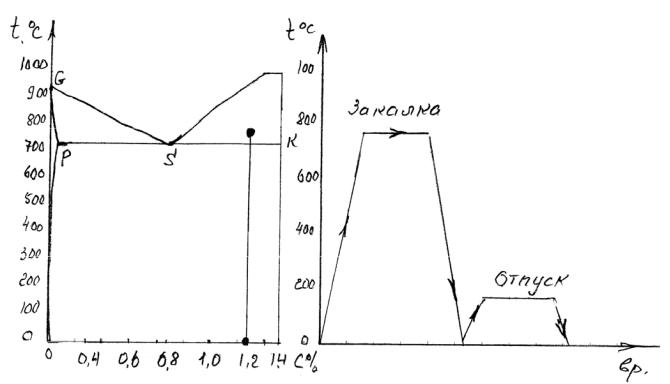
• детали и изделия, сочетающие удовлетворительные прочностные свойства с максимальной вязкостью (HRC < 40 – структура сорбит).
Инструмент из стали У12 (заэвтектоидная сталь) содержит углерода 1,2 %, в равновесном состоянии имеет структуру П + Ц11. При промышленных скоростях нагрева под
закалку перлит вплоть до температуры нагрева АС1, сохраняет пластинчатое строение. При температуре АС1 в стали начинается превращение феррита, входящего в состав пер-
лита, в аустенит. Кристаллы аустенита зарождаются преимущественно на межфазных поверхностях феррита и цементита. Нагрев вызывает два параллельно возникающих процесса: полиморфного Feα → Feγ перехода и растворения в Feγ кристаллов цементи-
та. Скорость полиморфного превращения выше скорости растворения цементита, поэтому аустенит первичный неоднороден по распределению углероду во вновь образовавшихся фазах. Устраняют химическую ликвацию выдержкой в нагретом состоянии. Превращение при температуре А1 сопровождается измельчением зерна.
Нагрев от АС1 до АСТ вызывает растворение избыточного цементита в аустените.
Процесс сопровождается диффузией углерода, приводящей к выравниванию концентраций и небольшим укрупнением кристаллов аустенита. Дальнейший нагрев стали в однофазной аустенитной области приводит к росту зерна аустенита, так как возникает собирательная рекристаллизация. Чем выше температура нагрева и чем длительнее выдержка в нагретом состоянии, тем крупнее будут кристаллы аустенита.
Сталь У12 подвергают неполной закалке для сохранения цементита вторичного в
структуре. Нагрев производят до температуры А + (30…50 °C) = 727 + 40 = 767 °C,
С1
температура отмечена на стальном уголке диаграммы как tЗАК (1 этап), рис. 2.
Термическая обработка включает операции (рис. 2): неполная закалка (1 – нагрев, 2 – выдержка при tЗАК , 3 – быстрое охлаждение) и низкий отпуск (4 – нагрев, 5 – вы-
держка при t ≈ 200 °C , 6 – охлаждение).
Рис. 2. График термической обработки (закалка, отпуск) детали из заэвтектоидной стали
27
1 – нагрев приводит к изменению фазового состава сплава П + ЦΙΙ → А+ ЦΙΙ ;
2 – выдержка при tЗАК необходима для получения однородного аустенита с равно-
мерным распределением углерода;
3 – быстрое охлаждение со скоростью большей Vкр в специальной среде обеспечива-
ет формирование структуры МЗАК + ЦΙΙ + АОСТ . Сохранение кристаллов ЦΙΙ в структуре
при неполной закалке заэвтектоидной стали способствует повышению твердости и износостойкости.
Для полного (или частичного) устранения внутренних напряжений, возникающих при закалке, и превращения АОСТ в мартенсит производят нагрев закаленной стали до
температуры ниже АС1 , выдерживают при заданной температуре нагрева и охлаждают с
определенной скоростью. Такая ТО называется отпуском. Температура нагрева для углеродистых сталей составляет порядка 150…200 °C, такой отпуск называют низким (низкотемпературным). Низкотемпературному отпуску подвергают режущий и измерительный инструмент. В результате этой операции сталь заэвтектоидная изменяет структуру и приобретает требуемые эксплуатационные и механические свойства.
МЗАК + ЦΙΙ + АОСТ → МОТП + ЦΙΙ .
БИБЛИОГРАФИЧЕСКИЙ СПИСОК
1.Берлин В.И. Транспортное материаловедение : учебник для вузов ж.-д. тр-та / В.И. Берлин, Б.В. Захаров, П.А. Мельниченко. – М.: Транспорт, 1982. – 287 с.
2.Материаловедение : учебник для высших техн. учеб. завед. / Б.Н. Арзамасов, И.И. Сидорин, Г.Ф. Косолапов [и др.]. – 2-е изд., испр. и доп. – М.: Машиностроение, 1986. – 384 с.
3.Материаловедение и технология металлов : учебник для студентов машиностр. спец. вузов / Г.П. Фетисов, М.Г. Карпман, В.М. Матюнин [и др.]. – М.: Высшая школа, 2000. – 638 с.
4.Марочник сталей и сплавов / В.Г. Сорокин, А.В. Волосникова, С.А. Вяткин [и др.]. – М.: Машиностроение, 1989. – 640 с.
5.Воронин Н.Н. Материаловедение и технология конструкционных материалов для железнодорожной техники / Н.Н. Воронин [и др.]. – М.: Маршрут, 2004. – 456 с.
28

ПРИЛОЖЕНИЕ
|
Стали, применяемые на железнодорожном транспорте |
||||
|
|
|
|
Свойства в |
|
Класс |
Марка |
Содержание |
Обозначение |
Область |
|
|
|
углерода |
|
состоянии |
применения |
|
|
|
|
поставки |
|
|
|
|
|
σв, МПа |
|
|
Ст3сп |
0,14...0,22 |
Группа А, |
380...490 |
Малонагруженные |
|
|
|
3 – порядковыйномер, |
|
детали (рамы тележек) |
|
|
|
сп – спокойная |
|
с невысокими требова- |
|
|
|
|
|
ниями к прочности |
Углеродистые |
Ст5сп |
0,28...0,37 |
Группа А |
500...640 |
Детали, восприни- |
обыкновенного |
|
|
5 – порядковыйномер, |
|
мающие небольшие |
качества |
|
|
сп – спокойная |
|
нагрузки (подвеска, |
|
|
|
|
|
тяга и т.д.) |
|
45 |
0,42...0,5 |
Спокойная, |
598 |
Втулка шпинтона |
|
|
|
углерода 0,45 % |
|
тележки |
|
45Л |
0,42...0,5 |
Изделия получают Л |
550 |
Шатун дизеля |
|
|
|
– литьем, |
|
4ДВ-224 |
|
|
|
углерода 0,45 % |
580...660 |
|
|
ОС |
0,42...0,5 |
Заготовки осей |
Заготовки осей |
|
|
|
|
|
|
для колесных пар |
Углеродистые |
Марка 1 |
0,44...0,52 |
Колеса |
880...1078 |
Цельнокатанные |
качественные |
|
|
|
|
колеса пассажирских |
|
|
|
|
|
вагонов |
|
Марка 2 |
0,55...0,65 |
|
911...1107 |
Цельнокатанные |
|
Марка 3 |
0,58...0,67 |
|
|
колесагрузовыхвагонов |
|
|
|
|
||
|
|
|
|
категории |
|
|
К78ХСФ |
0,74...0,89 |
К – конверторная, |
Рельсы Р65 |
|
|
|
|
углерода0,78 %, |
качества В, |
|
|
|
|
спокойная, легирована |
Т1, Т2, |
|
|
|
|
Х– хромом, С– крем- |
1290 (ТО) |
|
|
|
|
нием, Ф– ванадием |
|
|
|
М76Ф |
0,71...0,82 |
М – мартеновская, |
|
Рельсы Р65 |
|
|
|
углерода0,76 %, |
|
|
|
|
|
легирована |
|
|
Легированные |
|
|
Ф – ванадием, |
|
|
|
|
спокойная |
|
|
|
|
09Г2Д |
0,09 |
Низкоуглеродистая, |
440 |
Кузов вагона |
|
|
|
Г2 % марганца, |
|
|
|
|
|
Д1% меди |
|
|
|
60С2А |
0,60 |
С2 % кремния, |
1570…1770 |
Тяжелонагруженные |
|
|
|
А – пониженное |
(ТО) |
пружины |
|
|
|
содержание S и Р |
|
|
|
|
|
|
|
|
29

Класс |
Марка |
Содержание |
Обозначение |
|
|
углерода |
|
|
|
|
|
|
5ХГМ |
0,50...0,60 |
Х0,6…0,9 % хрома, |
|
|
|
Г1,2…1,6 % марганца, |
|
|
|
М0,15…0,3 % мо- |
|
|
|
либдена |
|
9ХС |
0,90 |
Х1 % хрома, |
|
|
|
С1,2…1,6 % кремния |
|
ШХ15 |
1,00 |
Х1,5 % хрома |
Легированные |
|
|
|
|
110Г13Л |
0,90...1,40 |
Г 13 % марганца, |
|
|
|
изделия получают |
|
|
|
литьем |
|
Х12ВМ |
2,00...2,20 |
Х12 % хрома, |
|
|
|
В0,7 % вольфрама, |
|
|
|
М 0,8 % молибдена |
|
Р18 |
0,73...0,83 |
Высоколегированная |
|
|
|
18 % вольфрама |
|
|
|
|
Свойства в |
Область |
состоянии |
применения |
поставки |
|
σв, МПа |
|
1420 |
Молотовые штампы |
(ТО) |
для горячей штамповки |
590...690 |
Режущие инструменты |
590…730, |
Подшипниковая |
2160 |
|
(ТО) |
|
640...710 |
Крестовины |
(ТО) |
стрелочных переводов |
HRCэ61-63 |
Холодные штампы вы- |
(ТО) |
сокой устойчивости |
840, 2150 |
Режущий инструмент, |
(ТО) |
сохраняющий режущие |
|
свойства при нагрева- |
|
нии до 600 °С |
30