
Модуль 4
.pdf
На рис. 14.6, а показана фотография пламенной трубы снаружи (горелочное устройство устанавливается сверху). Внизу пламенной трубы видны упомянутые выше прямоугольные окна для прохода вторичного воздуха. Фотография, представленная на рис. 14.6, б, дает вид на крышку пламенной трубы изнутри (со стороны выхода газов). Хорошо видно расположение всех восьми горелочных модулей, облицовочные керамические плитки и окна для прохода вторичного воздуха.

На рис. 14.7 приведена схема горелочного модуля, представляющий собой комбинацию трех горелок, т.е. устройств, предназначенных для сжигания газа, и одной форсунки, служащей для сжигания жидкого топлива. Такой горелочный модуль называется комбинированным. При мощности ГТУ более 50 %, т.е. при нормальной ее работе используется так называемая горелка с предварительным смешением. Топливный газ подается в коллектор 1, а из него
— к многочисленным перфорированным трубкам 6. В кольцевое пространство между трубками подается воздух. Решетка 10 турбулизирует поток и в результате на выходе из горелки создается однородная смесь топлива и воздуха. Эта смесь поджигается постоянно горящей пилотной («дежурной») горелкой (о ней рассказано ниже). Горение такой смеси происходит по законам кинетики химических реакций. Поэтому его называют кинетическим. Оно происходит сразу во всем объеме и на коротком участке пламенной трубы. Главная особенность горения топлива с предварительным смешением — образование малого количества оксидов азота и оксида углерода.
Однако горелки с предварительным смешением имеют и недостаток: при малых нагрузках, т.е. при малых расходах топливного газа по отношению к поступающему воздуху (напомним, что, так как компрессор имеет постоянную частоту вращения, то расход воздуха можно уменьшить сравнительно мало только с помощью входного направляющего аппарата компрессора), горение становится неустойчивым. Поэтому горелочный модуль снабжают диффузионной горелкой (без предварительного смешения), работающей при малых нагрузках, в частности при пуске и наборе начальной нагрузки. Через кольцевые полости 3 подается горючий газ, который не успевает смешаться с воздухом VI, а само горение происходит на выходе из горелки в факеле по мере перемешивания топлива и воздуха. Такое горение определяется скоростью диффузии, т.е. механического проникновения топлива в воздух. Поэтому его называют диффузионным, а саму горелку — диффузионной. Горелку, сочетающую в себе горелку с предварительным смешением и диффузионную, часто называют гибридной. Диффузионное горение более устойчиво, чем кинетическое, но характеризуется высоким уровнем вредных выбросов.
Наконец, третья горелка — это пилотная диффузионная горелка, к которой газ подается по нескольким трубкам 2. Она горит постоянно при работе и горелок с предварительным смешением, и диффузионных.
При работе на жидком топливе используется центробежная форсунка 9. С ее помощью на выходе создается коническая закрученная струя топлива, которая распадается на мелкие капли, смешивается с воздухом и обеспечивает диффузионное горение. К форсунке жидкое топливо подается в постоянном количестве (поток IX), а отводится в разном (поток X). Увеличивая обратный поток, изменяют расход топлива в зону горения.

На рис. 14.8 показана конструкция горелочного модуля. Его закрепляют фланцем 3 на корпусе камеры сгорания. Нижней конической поверхностью модуль свободно входит в отверстия верхней части камеры сгорания. Пользуясь рис. 14.7, легко уяснить назначение отдельных элементов горелочного модуля, показанного на рис. 14.8. Дополнительно на нем показан коллектор 4 подачи пара или воды для так называемого «экологического впрыска», предназначенного для подавления оксидов азота при работе на специфических видах топлива. При этом вместе с подавлением оксидов азота происходит и снижение экономичности. Заметим, однако, что горелки, установленные на ГТУ V94.2 Северо-Западной ТЭЦ экологического впрыска не имеют.
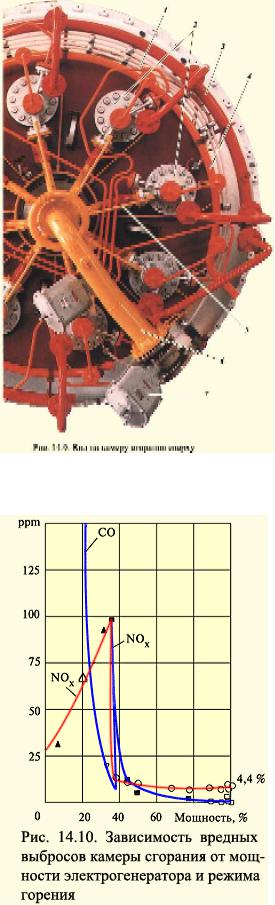
На рис. 14.9 показан вид на камеру сгорания, дающий представление о подаче топлива. Видны фланцы горелочных модулей 2. Топливо к ним подводится с помощью топливных клапанов 7 и коллекторов. Топливные клапаны управляются системами управления и регулирования.
На рис. 14.10 показано, как изменяется количество оксидов азота и оксида углерода в процессе нагружения ГТУ. Пуск и начальное нагружение ведут с использованием диффузионной горелки при прикрытом ВНА, вплоть до нагрузки примерно 40 %. Далее переходят на горелки с предварительным смешением и вредные выбросы резко уменьшаются, обеспечивая хорошие экологические показатели.
14.3. Устройство газовой турбины и система ее охлаждения
Достаточно подробно конструкция газовой турбины представлена на рис. 14.11. Она состоит из четырех ступеней.

Сопловые лопатки турбины 4, 6, 8 и 11 выполнены заодно с бандажными полками, с помощью которых они закрепляются в обойме 10, которая, в свою очередь, устанавливается в средней части 2 корпуса ГТУ (см. поз. 9 на рис.
14.1).
Рабочие лопатки 5, 7, 9 и 11 с помощью хвостовиков крепятся на дисках 17, 16, 14 и 13 соответственно. Мощность с диска на диск передается посредством хиртовых соединений и стяжного болта 15. Мощность с ротора газовой турбины на ротор компрессора и далее на ротор электрогенератора передается посредством цилиндрического соединительного элемента 19.
Газы из пламенных труб двух камер сгорания поступают в газосборник 3 и из него — в газовую турбину. Перед газовой турбиной, как указывалось выше, температура газов составляет 1100 ° С. После расширения газов в турбине их температура в диапазоне нагрузок 50—100 % должна поддерживаться постоянной и составлять 535 ° С. Это очень важная температура, так как она обеспечивает надежную и экономичную работу паросиловой установки ПТУ.
В газовой турбине охлаждаются первые пять из восьми венцов газовой турбины. Охлаждение всех сопловых аппаратов осуществляется из кольцевых полостей б, воздух в которые поступает из выходного диффузора компрессора 1 через отверстия а в обойме. Охлаждающий воздух из полостей б поступает внутрь сопловых лопаток и охлаждает их конвекцией. Нагретый воздух сбрасывается в проточную часть турбины.
Поступление воздуха в полости б одновременно обеспечивает низкую и равномерную температуру обоймы. Для охлаждения рабочих лопаток 1-й ступени используется воздух, отбираемый после рабочих лопаток
последней ступени компрессора. Воздух поступает в кольцевую полость между цилиндрическими перегородками 18 и 19, из нее — в отверстия а в диске, снабжающие воздухом каждую из рабочих лопаток. Воздух входит в лопатки через отверстия в хвостовиках, охлаждает лопатку и выходит в проточную часть газовой турбины.
Для охлаждения рабочих лопаток 2-й ступени турбины используется воздух от 12-й ступени компрессора, который поступает в кольцевую полость между цилиндрической перегородкой 18 и стяжным центральным болтом 15.
Профильные части рабочих лопаток 3-й и 4-й ступеней не охлаждаются, однако охлаждающий воздух из 12-й ступени направляется также в пространство между диском 16 и 14, а также 14 и 13, откуда по отверстиям а подается к монтажным зазорам в хвостовиках. Проходя через них, воздух отбирает теплоту, идущую из профильной части лопатки, и тем самым охлаждает их.
14.4. Сборка ГТУ, транспортировка на ТЭЦ и установка в машинном зале
Сборка ГТУ производится на турбинном заводе после изготовления в его цехах отдельных деталей и узлов. На рис. 14.12 показан сборочный стенд предприятия Интертурбо, на котором осуществляется сборка одновременно трех ГТУ.
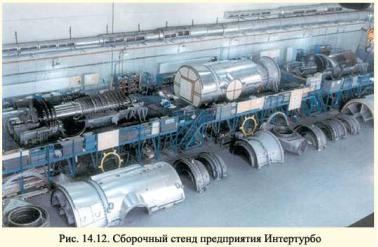
На левом стенде показана нижняя часть корпуса ГТУ с уложенным ротором. На правом стенде виден ротор, установленный в подшипниках, и внутренняя средняя часть, формирующая подвод воздуха в камере сгорания и выход газов из них к 1-й ступени. На среднем стенде показана собранная ГТУ с установленными заглушками, готовая к отправке на место монтажа.
В отличие от паровой турбины, после сборки на заводе ГТУ испытаний не проходит. В результате с турбинного завода на монтажную площадку ТЭС уходит несколько отдельно транспортируемых сборочных единиц:
турбогруппа (компрессор и турбина); две камеры сгорания;
маслобак с установленным на нем оборудованием; входной патрубок компрессора; выходной диффузор.
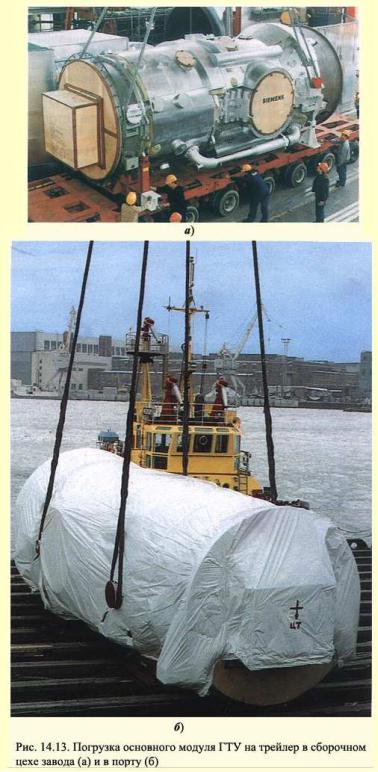
На рис. 14.13 показана установка самой габаритной и тяжелой сборочной единицы (турбогруппы) на трейлер в сборочном цехе, а затем при погрузке в порту.
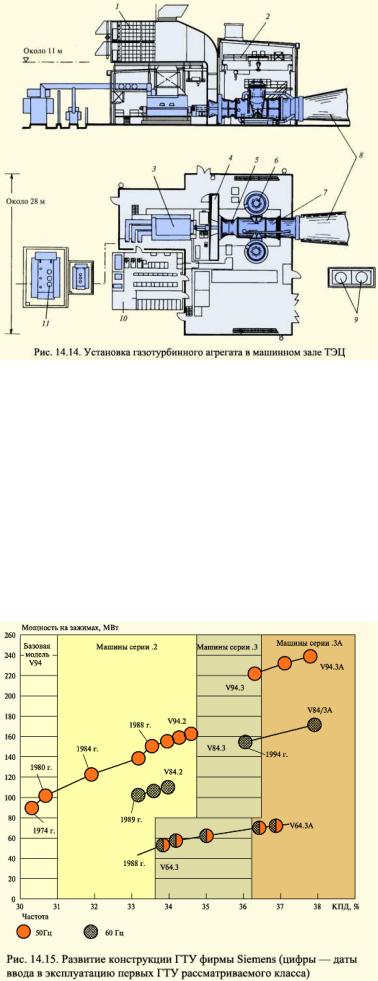
В отличие от паровой турбины, ГТУ размещают на ТЭС не на рамном фундаменте, а непосредственно на бетонном основании, установленном на нулевой отметке машзала (рис. 14.14). Входную шахту 4 компрессора посредством воздушного короба соединяют с КВОУ 1, где происходит тщательная фильтрация воздуха, исключающая износ проточной части компрессора, забивание охлаждающих каналов в рабочих лопатках и другие неприятности. КВОУ размещают на крыше здания, экономя площадь здания. К выходному концу вала компрессора присоединяется ротор электрогенератора 3, а к выходному диффузору ГТУ — переходный диффузор, направляющий газы в котелутилизатор.
14.5. Развитие конструкций ГТУ фирмы Siemens и место ГТУ V94.2 в этом развитии
Главной особенностью ГТУ V.94.2 является использование непосредственного привода электрического генератора (без редуктора), вырабатывающего электрический ток с частотой 50 Гц. Наряду с этим рядом, фирма Siemens выпускает ГТУ ряда V84 (рис. 14.15), предназначенных для частоты сети 60 Гц. ГТУ ряда V64 являются универсальными: выбором передаточного числа редуктора их можно использовать для выработки электроэнергии частоты 50 и 60 Гц. Рассмотрим кратко эволюцию ГТУ фирмы Siemens ряда V94. Это позволит, во-первых, понять уровень V94.2 ЛМЗ-Siemens, а, во-вторых, проследить тенденции развития и будущее ГТУ.
Эволюция ГТУ вообще и ГТУ фирмы Siemens, в частности, протекала под действием двух тенденций. Первая тенденция — стремление повысить начальную температуру перед турбиной и улучшить жаропрочные свойства
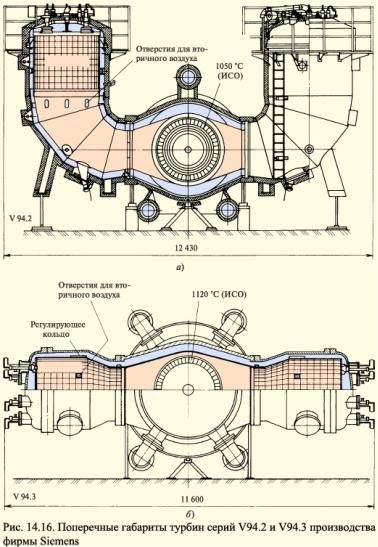
материалов, а также усовершенствовать систему охлаждения деталей газовой турбины. Вторая тенденция — все ужесточающиеся экологические требования к уменьшению выбросов окислов азота и оксида углерода.
Базовая модель ГТУ ряда V94, внешне весьма похожая на только что рассмотренную ГТУ V94.2, оформилась в начале 70-х годов (см. рис. 14.15) имела мощность 90 МВт при КПД 30,3 %. Господствующим способом сжигания в те годы было диффузионное сжигание, характеризуемое высокой температурой горения и длинным факелом. Эти два обстоятельства способствуют превращению атмосферного азота в его оксиды. Принятая силосная конструкция камер сгорания с длинными переходными патрубками вполне отвечала отмеченным выше особенностям: для полного сгорания топлива и понижения температуры газов до приемлемого уровня требовались большие габариты и необходимость в подаче вторичного воздуха.
Мощность ГТУ ряда V94 постепенно росла, наряду с диффузионными горелками начали использовать горелки с предварительным смешением. К настоящему времени ГТУ V94.2 — достаточно совершенная машина мощностью
160 МВт с КПД 34,2 %.
Появление горелок с предварительным смешением воздуха и газа позволило резко сократить продольные габариты камеры, и, несмотря на то, что новая ГТУ серии V94.3 имела большую мощность (220 МВт) и почти на 20 % больший расход воздуха через компрессор, габариты ее оказались меньше (рис. 14.16). Конструкция этой турбины рассмотрена в лекции 7.
Естественным развитием ГТУ V94.3 явился переход к встроенной кольцевой камере сгорания. Продольный разрез этой ГТУ, относящейся к серии 94.3А показан на рис. 14.17, а фрагмент самой кольцевой камеры — на рис. 14.18. Камера облицована специальными термощитами из металла и оксидной керамики. Слева на рисунке видны гибридные горелки (всего 24), а справа — сопловые лопатки первой ступени.
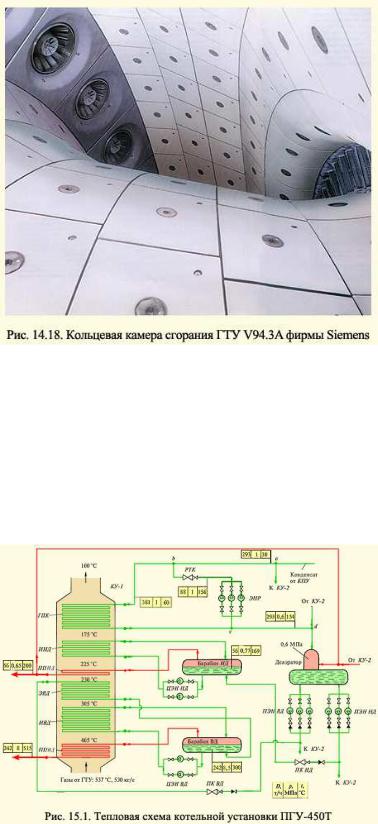
КОТЕЛЬНАЯ УСТАНОВКА ПАРОГАЗОВОЙ УСТАНОВКИ ПГУ-450Т 15.1. Тепловая схема котельной установки
Котельная установка ПГУ служит для максимальной утилизации тепла уходящих газов ГТУ путем его передачи воде и водяному пару, причем его расход и параметры должны быть такими, чтобы из тепловой энергии этого пара можно было бы получить максимум электроэнергии в паровой турбине.
Котельная установка ПГУ-450Т состоит из двух одинаковых котлов, каждый из которых включает: двухконтурный барабанный котел-утилизатор вертикального (башенного) типа; систему рециркуляции конденсата, обеспечивающую постоянную температуру конденсата на входе в котел; систему многократной принудительной циркуляции воды в испарителях котла; систему деаэрации конденсата в деаэрационной установке.
На рис. 15.1 показана тепловая схема половины котельной установки (или, как говорят, — одного корпуса), в которую поступают уходящие газы из одной ГТУ [ГТУ-1 (см. рис. 13.2)]. Второй корпус выполнен точно также с той лишь разницей, что деаэратор для этих половин является общим. На рис. 15.1 в прямоугольных рамках нанесены значения параметров (расходов пара или воды, давления и температуры), полученные при расчете тепловой схемы котла.
Котел-утилизатор КУ-1 ПГУ-450Т представляет собой вертикальный противоточный теплообменный аппарат. Горячий теплоноситель (газы ГТУ) поступает снизу и движется вверх к дымовой трубе. Холодный теплоноситель (вода) и движется сверху вниз по трубам. Газы передают свое тепло воде (пару), остывают и при температуре примерно 100 ° С выбрасываются через дымовую трубу в атмосферу. (Заметим, что все приведенные на схеме значения параметров относятся к номинальному режиму, но являются приблизительными, так как они зависят от температуры наружного воздуха.) В нижней части КУ, куда поступают горячие газы, размещены теплообменные поверхности контура ВД, а в верхней — контура НД.