
Новиков Суханова Калибры
.pdf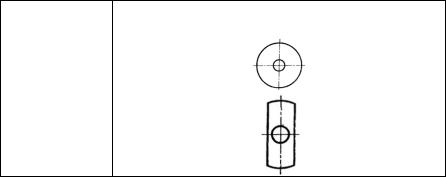
Окончание таблицы 1.2
Обозначение, |
Наименование и схема калибра |
|
номер вида калибра |
||
|
||
|
Калибр гладкий контрольный проходной, непроходной |
К-ПР (8), К-НЕ (9), К-И (10)
Технические требования к нерегулируемым калибрам. Конструктивным отличием непроходных калибров и непроходных сторон калибров является уменьшенная длина рабочей части по сравнению с проходными.
Твердость рабочих поверхностей, поверхностей заходных и выходных фасок (притуплений) должна быть в пределах:
-калибров-пробок диаметром до 1 мм – HRCэ 57…63;
-калибров-пробок с хромовым покрытием – HRCэ 57…63;
-остальных калибров – HRCэ 57…63;
Для калибров с износостойким покрытием эти требования относятся к поверхностям, подготовленным под покрытие.
Числовые значения параметра шероховатости Ra рабочих поверхностей калибров должны соответствовать указанным в таблице 1.3.
Таблица 1.3 – Числовые значения параметра шероховатости RA |
рабочих |
|||||
|
поверхностей калибров |
|
|
|
||
|
|
|
|
|
|
|
|
|
|
|
Параметр шероховатости Ra |
||
|
|
Контролируемое изделие |
по ГОСТ 2789–73, мкм, |
|||
Вид калибра |
|
|
|
для диаметров |
||
|
|
Квалитет |
Класс |
от 0,1 |
|
св. 100 |
|
|
точности |
до 100 мм |
|
до 360 мм |
|
|
|
|
|
|||
|
|
6 |
1 |
0,04 |
|
0,08 |
Калибр–пробка |
|
7–9 |
2–3 |
0,08 |
|
0,16 |
|
10–12 |
3а–5 |
0,16 |
|
||
|
|
|
|
|||
|
|
13 и грубее |
6 и грубее |
0,32 |
|
0,32 |
|
|
6–9 |
2–3 |
0,08 |
|
0,16 |
Калибр–скоба |
|
10–12 |
3а–5 |
0,16 |
|
|
|
|
|
||||
|
|
13 и грубее |
6 и грубее |
0,32 |
|
0,32 |
Контрольный |
|
6–9 |
2–3 |
0,04 |
|
0,08 |
калибр |
|
10 и грубее |
6 и грубее |
0,08 |
|
0,16 |
На каждом калибре должны быть нанесены: - номинальный размер отверстия (вала);
10
-обозначение поля допуска отверстия (вала);
-числовые величины предельных отклонений отверстия (вала);
-обозначение назначения калибра (например ПР, К-И);
-товарный знак предприятия-изготовителя.
1.2Правила применения калибров
Калибры для валов и относящиеся к ним контрольные калибрыпробки. Калибр-кольцо гладкий проходной (1) или калибр-скоба гладкий проходной (2) должен проходить по валу под действием собственного веса или определенной силы.
Калибр-скоба гладкий непроходной (3) или калибр-кольцо гладкий непроходной (4) не должен проходить по валу, в крайнем случае «закусывать».
Калибр-пробка гладкий контрольный проходной (5) или калибр гладкий проходной контрольный (8) для проходного гладкого калибра-скобы (2).
Калибр-скоба гладкий проходной (2) должен скользить по гладкому проходному калибру-пробке (5) или по гладкому контрольному проходному калибру (8) под действием собственного веса или определенной силы.
Калибр-пробка гладкий контрольный, проходной (6) или калибр гладкий проходной контрольный (9) для непроходного гладкого калибра-скобы (3).
Калибр-скоба гладкий непроходной (3) должен скользить по гладкому контрольному проходному калибру-пробке (6) или по гладкому контрольному проходному калибру (9) под действием собственного веса или определенной силы.
Калибр-пробка гладкий контрольный (7) или калибр гладкий контрольный (10) для контроля износа гладкого проходного калибра-скобы (2).
Калибр-скоба гладкий проходной (2) не должен проходить по гладкому контрольному калибру-пробке (7) или гладкому контрольному калибру (10), в крайнем случае, «закусывать».
Взамен контрольных калибров для контроля калибров-скоб размерами до 180 мм допускается применять универсальные измерительные приборы, плоскопараллельные концевые меры и для всех размеров калибров-скоб – аттестованные образцы изделий.
Размер блока плоскопараллельных концевых мер длины и аттестованного образца изделия рекомендуется назначать близким к наименьшему предельному размеру контрольных калибров (5, 8 и 6, 9) и к наибольшему предельному размеру контрольных калибров (7, 10).
Калибры для отверстий. Калибр-пробка гладкий проходной (11) должен свободно проходить через отверстие под действием собственного веса или определенной силы.
11
Калибр-пробка гладкий непроходной (12), как правило, не должен входить в отверстие под действием собственного веса или определенной силы, в крайнем случае, «закусывать».
Правила контроля калибрами. Калибр должен изыматься из употребления, когда его износ дойдет до предела, установленного в ГОСТ 24853–81.
При возникновении разногласий в оценке качества изделия между изготовителем и потребителем рекомендуется:
При контроле отверстия или вала в процессе их изготовления пользоваться новыми или малоизношенными проходными калибрами и непроходными калибрами с размерами, близкими к наименьшему для калибрапробки и наибольшему для калибра-скобы (кольца).
При контроле отверстия или вала контролерами предприятияизготовителя и представителем заказчика пользоваться проходными калибрами с размерами, близкими к пределу допустимого износа, и непроходными калибрами с размерами, близкими к наибольшему для калибра-пробки и наименьшему для калибра-скобы (кольца).
Проверка правильности определения размеров изделий должна осуществляться калибрами с размерами, близкими к границе износа проходного калибра и к границе поля допуска нового непроходного [наименьшего для калибра-скобы (кольца) и наибольшего для калибра-пробки].
1.3 Калибры-скобы регулируемые
Гладкие двухпредельные калибры-скобы с односторонней регулировкой в соответствии с ГОСТ 2216 должны изготавливаться двух исполнений (рисунок 1.1). В связи с наличием подвижных вставок регулируемые калибры позволяют контролировать изделия более грубых квалитетов (начиная с 9-го,10-го квалитетов), в отличие от жестких нерегулируемых калибров (начиная с 6-го квалитета).
Технические требования к калибрам-скобам регулируемым. Конструкция калибра-скобы должна обеспечивать продольное перемещение вставок без их вращения при установке на размер.
Узлы зажима вставок должны надежно закреплять вставки и предохранять их от смещений.
Конструкция калибра-скобы должна обеспечивать возможность опломбирования регулировочного винта. Сопряжение «отверстие корпуса – вставка» должно быть выполнено для калибров-скоб исполнения 1 с посадкой H8/Js6, для калибров-скоб исполнения 2 – с посадкой H7/Js5.
Рабочие поверхности вставок, пяток и губок должны быть изготовлены из твердого сплава марок ВК8, ВК6 или ВК6М, ВК8В по ГОСТ 3882; допускается изготовление из стали марок У8А, У10А или У12А по ГОСТ 1435, с твердостью рабочих поверхностей 59–65 HRCэ.
12

Рисунок 1.1 – Калибры-скобы гладкие регулируемые:
1 – корпус; 2 – подвижная головка;
3 – неподвижная пятка; (для исполнения 2 – губка);
4 – теплоизоляционная накладка;
5 – маркировочная шайба; 6 – регулировочный винт;
7 – узел зажима вставки
Параметр шероховатости Ra по ГОСТ 2789 рабочих поверхностей вставок должен быть не более 0,080 мкм для размеров до 100 мм и не более 0,16 мкм – для размеров более 100 мм.
Плоские рабочие поверхности должны иметь заходные и выходные фаски у проходной и непроходной сторон. Острые кромки должны быть притуплены.
Предельные отклонения рабочих поверхностей калибра-скобы исполнения 2 от параллельности при установке в диапазоне измерений калибраскобы должны быть не более величин, указанных в таблице 1.4.
Таблица 1.4 – Предельные отклонения от параллельности рабочих поверхностей
Диапазоны |
|
|
|
|
|
80– |
120– |
180– |
250– |
|
контролируемых |
0–10 |
10–20 |
20–35 |
35–50 |
50–80 |
|||||
120 |
180 |
250 |
340 |
|||||||
размеров, мм |
|
|
|
|
|
|||||
|
|
|
|
|
|
|
|
|
||
Предельные |
4 |
5 |
6 |
7 |
8 |
9 |
11 |
13 |
15 |
|
отклонения, мкм |
||||||||||
|
|
|
|
|
|
|
|
|
Каждый калибр-скоба должен быть снабжен маркировочной алюминиевой шайбой, предназначенной для маркировки на ней размеров калибра-скобы.
2 Допуски гладких калибров
Для контроля размеров валов применяют предельные калибры-скобы, а размеров отверстий – предельные калибры-пробки (рисунки 1.2, 1.3).
13

Рисунок 1.2 – Схемы расположения полей допусков калибров для номинальных размеров до 180 мм по ГОСТ 24853 для контроля:
а– отверстий квалитетов 6–8; б – отверстий квалитетов 9–17;
в– валов квалитетов 6–8; г – валов квалитетов 9–17
Условные обозначения гладких калибров на схеме: Р-ПР (Р – НЕ) – рабочий проходной (непроходной);
К-ПР (К – НЕ) – контрольный для проверки рабочих новых скоб проходной (непроходной);
К-И – контрольный для проверки износа рабочих проходных скоб.
При контроле ПР калибры должны проходить в изделие под собственным весом, НЕ – не должны проходить в изделие более чем на глубину фасок (иначе неизбежны деформации).
По ГОСТ 24853 приняты следующие обозначения размеров и допусков: D – номинальный размер изделия; Dmin – наименьший предельный размер изделия; Dmax – наибольший предельный размер изделия; T – допуск изделия; H – допуск на изготовление калибров (за исключением калибров со сферическими измерительными поверхностями) для отверстия; Hs – допуск на изготовление калибров со сферическими измерительными поверхностями для отверстия; H1 – допуск на изготовление калибра для вала; Hp – допуск на изготовление кон-
14

трольного калибра для скобы; z – отклонение середины поля допуска на изготовление проходного калибра для отверстия относительно наибольшего предельного размера изделия; z1 – отклонение середины поля допуска на изготовление проходного калибра для вала относительно наибольшего предельного размера изделия; y – допустимый выход размера изношенного проходного калибра для отверстия за границу поля допуска изделия; y1 – допустимый выход размера изношенного проходного калибра для вала за границу допуска изделия; α – величина для компенсации погрешности контроля калибрами отверстий с размерами свыше 180 мм; α1 – величина для компенсации погрешности контроля калибрами валов с размерами свыше 180 мм.
Рисунок 1.3 – Схемы расположения полей допусков калибров для номинальных размеров свыше 180 мм до 500 мм по ГОСТ 24853 для контроля:
а– отверстий квалитетов 6–8; б – отверстий квалитетов 9–17;
в– валов квалитетов 6–8; г – валов квалитетов 9–17
Исполнительные размеры калибров должны определяться по формулам, приведенным в таблице 1.5.
Допуски и отклонения калибров установлены ГОСТ 24853 и приведены в таблице А.4 приложения.
15
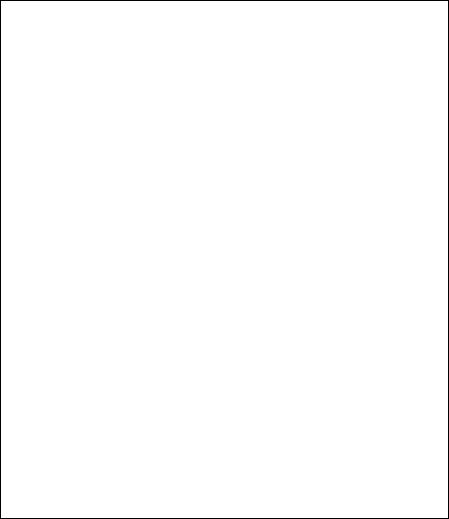
Таблица 1.5 – Формулы для определения исполнительных размеров калибров
по ГОСТ 24853
Номинальный размер изделия до 180 мм
|
|
Калибр |
Рабочий калибр |
|
Контрольный калибр |
||||
|
|
размер |
допуск |
|
размер |
|
допуск |
||
|
|
|
|
|
|||||
- |
|
Проходная сторона |
Dmin + Z |
± H/2 |
|
– |
|
– |
|
|
новая |
|
|
||||||
Дляотвер стия |
|
|
|
|
|
|
|
|
|
|
Проходная сторона |
Dmin –Y |
– |
|
– |
|
– |
||
|
изношенная |
|
|
||||||
|
|
|
|
|
|
|
|
||
|
Непроходная |
Dmax |
± H/2 или ± Hs/2 |
|
– |
|
– |
||
|
|
сторона |
|
|
|||||
|
|
|
|
|
|
|
|
|
|
|
|
Проходная сторона |
Dmax – Z1 |
± H1/2 |
|
Dmax – Z1 |
|
± Hp/2 |
|
вала |
|
новая |
|
|
|||||
|
|
|
|
|
|
|
|
||
|
Проходная сторона |
Dmax + Y1 |
– |
|
Dmax + Y1 |
|
± Hp/2 |
||
Для |
|
изношенная |
|
|
|||||
|
|
|
|
|
|
|
|
||
|
Непроходная |
Dmin |
± H1/2 |
|
Dmin |
|
± Hp/2 |
||
|
|
|
|
||||||
|
|
сторона |
|
|
|||||
|
|
|
|
|
|
|
|
|
|
|
|
Номинальный размер изделия свыше 180 до 500 мм |
|
||||||
|
|
Калибр |
Рабочий калибр |
|
|
Контрольный калибр |
|||
|
|
размер |
допуск |
|
|
размер |
допуск |
||
|
|
|
|
|
|||||
- |
|
Проходная сторона |
Dmin + Z |
± H/2 или ± Hs/2 |
|
|
– |
– |
|
|
новая |
|
|
||||||
Дляотвер стия |
|
|
|
|
|
|
|
|
|
|
Проходная сторона |
Dmin –Y + α |
– |
|
|
– |
– |
||
|
изношенная |
|
|
||||||
|
|
|
|
|
|
|
|
||
|
Непроходная |
Dmax – α |
± H/2 или ± Hs/2 |
|
|
– |
– |
||
|
|
сторона |
|
|
|||||
|
|
|
|
|
|
|
|
|
|
|
|
Проходная сторона |
Dmax – Z1 |
± H1/2 |
|
|
Dmax – Z1 |
± Hp/2 |
|
вала |
|
новая |
|
|
|||||
|
|
|
|
|
|
|
|
||
|
Проходная сторона |
Dmax + Y1 – α1 |
– |
|
Dmax + Y1 – α1 |
± Hp/2 |
|||
Для |
|
изношенная |
|
|
|
|
|
|
|
|
Непроходная |
Dmin + α1 |
± H1/2 |
|
|
Dmin + α1 |
± Hp/2 |
||
|
|
|
|
||||||
|
|
сторона |
|
|
|||||
|
|
|
|
|
|
|
|
|
|
|
П р и м е ч а н и е – При подсчете исполнительных размеров калибров (наибольших для отверстий |
||||||||
и наименьших для валов) необходимо пользоваться следующими правилами округления: |
|
||||||||
|
- округление размеров рабочих калибров (наибольших для отверстий и наименьших для валов) для из- |
||||||||
делий квалитетов 15–17 следует производить до целого микрометра; |
|
|
|
|
|||||
|
- для изделий квалитетов 6–14 и всех контрольных калибров размеры следует округлять до величин, |
кратных 0,5 мкм, при этом допуск на калибры сохраняется; - размеры, оканчивающиеся на 0,25 и 0,75 мкм, следует округлять до величин, кратных 0,5 мкм, в сторону уменьшения производственного допуска изделия.
2.1 Примеры расчета исполнительных размеров калибров
Валы и отверстия с допусками точнее 6-го квалитета не рекомендуется проверять калибрами ввиду большой погрешности измерения. Такие изделия проверяются универсальными средствами. Примеры расчета исполнительных размеров калибров по таблицам ГОСТ 21404–75 приведены ниже.
16
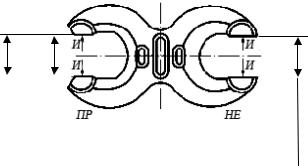
Пример 1.
Определить исполнительные размеры калибров-скоб для вала диаметром D = 120 мм с полем допуска Js6 (рисунок 1.4).
D = 100 мм заключен в интервале св. 80 до 120 мм, и по ГОСТ 21404–75 определяем:
ПРизнош = D + 0,0030 = 120 + 0,0030 = 120,0030 мм. Допуск на изготовление калибра-скобы ПР равен 0,0060 мм.
Следовательно,
ПР = 120,0030+0,0060 мм;
ПРизнош = D + 0,0150 = 120 + 0,0150 = 120,0150 мм;
НЕнаим = (D – 1) + 0,9860 = 120 – 1 + 0,9860 =119,986 мм; Допуск на изготовление калибра-скобы НЕ равен 0,0060 мм. Тогда
НЕ = 119,986+0,0060 мм.
|
|
|
|
|
|
=120,0150 |
+0,0060 |
+0,0060 |
|||
ПР |
120,0030 |
119,986 |
|||
изнош |
|
|
|
|
Рисунок 1.4 – Калибр-скоба для контроля вала 120 Js6:
И – измерительные поверхности
Пример 2.
Определить исполнительные размеры калибров-пробок для отверстия диаметром D = 40 мм с полем допуска Js12 (рисунок 1.5).
По ГОСТ 21401–75 определяем:
ПРнаиб = (D – 1) + 0,9025 = 39,9025 мм.
Допуск на изготовление калибра-пробки ПР составляет 0,0110 мм, т.е. ПР = 39,9025 – 0,0110 мм; ПРизнош = (D – 1) + 0,8750 = 39,875 мм;
НЕнаиб = D + 0,1305 = 40,1305 мм.
Допуск на изготовление калибра-пробки НЕ равен 0,0110 мм, и НЕ = 40,1305–0,0110 мм.
17
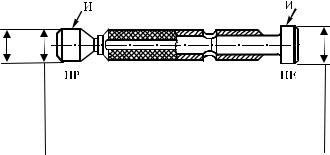
Примеры расчета исполнительных размеров калибров по формулам ГОСТ 24853–81 приведены ниже.
Изделие имеет поле допуска, регламентированное ГОСТ 25346–82.
=39,875 |
–0,0110 |
–0,0110 |
ПР |
39,9025 |
40,1305 |
изнош |
|
|
Рисунок 1.5 – Калибр-пробка для контроля отверстий 40Js12:
И – измерительные поверхности
Пример 3.
Определить исполнительные размеры калибров-скоб для вала диаметром
D = 140 мм с полем допуска h6: 140 0 0 025 (рисунок 1.6).
− ,
Подсчитываем наибольший и наименьший предельные размеры вала: Dнаиб = 140,000 мм; Dнаим = 140 – 0,025 = 139,975 мм.
По таблице 2 раздела 4 ГОСТ 24853–81 (таблица А.4 приложения данного пособия) для квалитета 6 и интервала размеров 120–180 мм находим данные для расчета искомых калибров:
Z1 = 6 мкм; Y1 = 4 мкм; H1 = 8 мкм; Hp = 3,5 мкм.
Расчет размеров калибров производится по формулам, находящимся в таблице 1 раздела 3 ГОСТ 24853–81 (см. таблицу 1.5 данного пособия, рисунок 1.2, в).
Наименьший размер проходного нового калибра-скобы ПР
ПРнаим = Dнаиб – Z1 – H1/2 = 140,000 – 0,006 – 0,008/2 = 139,990 мм. Наибольший размер изношенного калибра-скобы ПР
ПРнаиб = Dнаиб + Y1 = 140,000 + 0,004 = 140,004 мм. Наименьший размер непроходного калибра-скобы НЕ
НЕнаим = Dнаим – H1/2 = 139,975 – 0,008/2 = 139,971 мм.
Схема расположения полей допусков калибров для контроля вала диаметром 140h6 приведена на рисунке 1.6.
Исполнительные размеры калибров-скоб:
ПР = 139,990+0,008 мм; ПРизнош = 140,004 мм; НЕ = 139,971+0,008 мм. Эскиз калибра-скобы для контроля вала 140h6 приведен на рисунке 1.7. Определим размеры контрольных калибров:
18
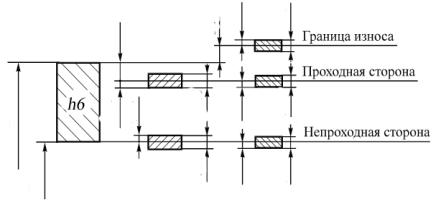
-для контроля проходной стороны новой
К– ПРmax = Dmax – Z1 + Hp/2 = 140,000 – 0,006 + 0,0035/2 = 139,99575 мм;
К– ПРmin = Dmax – Z1 – Hp/2 = 140,000 – 0,006 – 0,0035/2 = 139,99225 мм;
-для контроля проходной стороны изношенной
К– Иmax = Dmax + Y1 + Hp/2 = 140,000 + 0,004 + 0,0035/2 = 140,00575 мм;
К– Иmin = Dmax + Y1 – Hp/2 = 140,000 + 0,004 – 0,0035/2 = 140,00225 мм;
-для контроля непроходной стороны
К– НЕmax = Dmin + Hp/2 = 139,975 + 0,0035/2 = 139,97675 мм;
К– НЕmin = Dmin – Hp/2 = 139,975 – 0,0035/2 = 139,97325 мм. Исполнительные размеры контрольных калибров:
|
К – ПР = 139,9955–0,0035 мм; |
К – И = 140,0055–0,0035 мм; |
|||
|
|
|
К – НЕ = 139,9770–0,0035 мм; |
||
|
0,006 |
|
0,004 |
0,00175 |
0,0035 |
Ø140,000 |
0,004 |
0,004 |
0,008 |
0,00175 |
0,0035 |
|
Ø139,975 |
|
0,008 |
0,00175 |
0,0035 |
Рисунок 1.6 – Схема расположения полей допусков калибров для контроля вала 140h6
Пример 4.
Определить исполнительные размеры калибров-пробок для отверстия диаметром D = 70 мм с полем допуска Js10: 70 +−00,,060060 .
Подсчитываем наибольший и наименьший предельные размеры отверстия Dнаиб = 70 + 0,060 = 70,060 мм; Dнаим = 70 – 0,060 = 69,940 мм.
По таблице 2 раздела 4 ГОСТ 24853–81(таблица А.4 приложения данного пособия) для квалитета 10 и интервала размеров 50–80 мм находим данные для расчета искомых калибров:
Z = 0,013 мм; Y = 0; H = 0,005 мм.
19