
fel14M190
.pdf20
Настройка станка. Настройка станка заключается в установлении частоты вращения шпинделя, определении величины хода хонинговальной головки и числа двойных ходов хона.
Необходимую частоту вращения шпинделя устанавливают с помощью коробки передач станка, а число двойных ходов хонинговальной головки сменными шестернями, расположенными с левой стороны станка под крышкой.
Обработка отверстий хонингованием алмазными брусками проводится на следующих режимах, приведенных в табл. 7.
|
|
|
Таблица 7 |
|
Режимы резания при хонинговальной обработке |
|
|||
|
|
|
|
|
Параметры |
Операция хонингования |
|||
|
|
|
||
Первая |
Вторая |
Третья |
||
|
||||
|
|
|
|
|
Частота вращения хонинговальной |
120 |
160 |
240 |
|
головки, мин-1 |
||||
Число двойных ходов головки, ход/мин |
60 |
60 |
60 |
|
|
|
|
|
|
Длина хода, мм |
165 |
165 |
165 |
|
Давление на разжим брусков, МПа |
1,5 |
1,2 |
1,0 |
|
Количество брусков в комплекте, шт. |
6 |
6 |
6 |
|
Время хонингования, с |
40...45 |
20...25 |
15 |
|
|
|
|
|
|
Цилиндричность отверстия, мм |
0,02 |
0,1...0,02 |
0,01...0,02 |
|
Шероховатость поверхности, Ra |
0,8 |
0,63 |
0,25 |
Хонингование гильз производят на тех же одношпиндельных вертикально-хонинговальных станках, используя специальное приспособление.
Для хонингования гильз используют хоны с брусками из синтетических алмазов АСР 50/40 (предварительное) и АСР 20/14 (окончательное). В качестве смазочно-охлаждающей жидкости используют смесь керосина и индустриального масла.
Режим предварительного хонингования: окружная скорость хона– 60...80 м/мин.; скорость возвратно-поступательного движения – 15...
25 м/мин; давление брусков – 0,5...1,0 МПа. Режим чистового (окончательного) хонингования такой же, как и предварительного, но давление брусков снижают до 0,3...0,5 МПа.
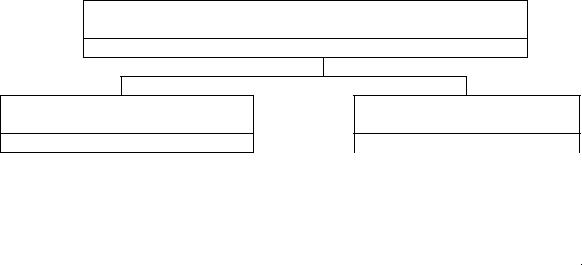
21
После хонингования отклонение геометрической формы рабочей поверхности гильзы должно быть не более 0,01...0,02 мм, а шероховатость Ra = 0,08 мкм.
Методика определения нормативов времени операций растачивания и хонингования
Техническая норма времени (норма штучно-калькуляционного времени tШК) – это регламентированное время выполнения технологической операции в определѐнных организационно-технических условиях одним или несколькими исполнителями соответствующей квалификации.
Техническая норма времени на операцию (норма штучно-калькуляционного времени ТШК)
tШК = tП-З + tШТ
Подготовительнозаключительное время
tП-З = ТП-З / Z
Штучное время
tШТ = tОП + tОРМ+ tЛП
|
|
|
|
|
|
|
|
|
|
|
|
|
|
|
|
|
|
|
|
|
|
|
|
|
|
|
|
|
|
|
|
|
|
|
|
|
|
|
|
|
|
|
|
|
|
|
|
|
|
|
Время |
|
|
|
Время на личные |
|
||||||
Оперативное время |
|
|
обслуживания |
|
|
|
|
|||||||||||||
|
|
|
|
|
надобности |
|
||||||||||||||
|
|
|
|
|
|
|
рабочего места |
|
|
|
|
|||||||||
|
|
|
|
|
|
|
|
|
|
|
|
|
|
|
|
|||||
|
tОП = tО+ tВ |
|
|
|
tОРМ |
|
|
|
|
tЛП |
|
|||||||||
|
|
|
|
|
|
|
|
|
|
|
|
|
|
|
|
|
|
|||
|
|
|
|
|
|
|
|
|
|
|
|
|
|
|
|
|
|
|||
|
|
|
Основное время |
|
|
|
|
|
|
Вспомогательное время |
|
|||||||||
|
|
|
|
tО |
|
|
|
|
|
|
|
|
tВ |
|
|
|
|
|
||
|
|
|
|
|
|
|
|
|
|
|
|
|
|
|
|
|
||||
|
|
|
|
|
|
|
|
|
|
|
|
|
|
|
|
|
||||
Машинное |
|
Машинно- |
|
Ручное |
|
|
Время на ус- |
|
Время, |
|||||||||||
|
ручное |
|
|
тановку и сня- |
|
связанное с |
||||||||||||||
время |
|
|
время |
|
|
|
||||||||||||||
|
время |
|
|
|
тие детали |
|
переходом |
|||||||||||||
|
|
|
|
|
|
|
|
|
|
|
||||||||||
tМ |
|
|
tМР |
|
|
tР |
|
|
|
|
tВ У/С |
|
|
tВ П |
Рис. 8. Структура технической нормы времени операций механической обработки
Для работ механической обработки блоков и гильз цилиндров техническая норма времени tШК определяется по формуле, представленной на рис. 8. Главным движением при расточке и хонинговании ци-

22
линдров и гильз двигателей является вращение инструмента обработки, а вспомогательным – его возвратно-поступательное перемещение.
При нормировании работ механической обработки блоков и гильз цилиндров придерживаются следующей последовательности:
определяют диаметр d обрабатываемой поверхности и припуск Z. Значение диаметров для отверстий принимается после обработки. Припуск – величина, которую снимают в процессе обработки;
определяют глубину резания t, которую принимают, как правило, равной припуску на сторону;
рассчитывают число рабочих ходов по формуле
(14)
выбирают по нормативам величину подачи s в зависимости от вида обработки и сопоставляют еѐ с имеющимися подачами оборудования (по паспорту станка) и принимают для последующих расчѐтов ближайшее значение sф;
рассчитывают или определяют по нормативам скорость резания (м/мин), значение которой зависит от механических свойств обрабатываемого материала, материала инструмента, глубины ре-
зания t, подачи sф, геометрии режущего инструмента; рассчитывают частоту вращения детали n по формуле:
(15)
где – скорость резания, м/мин; d – наибольший диаметр обрабатываемой поверхности, мм.
Частота двойных ходов при совершении инструментом или изделием возвратно-поступательного движения определяется по формуле:
(16)
где в-п – скорость возвратно-поступательного движения, м/мин; Lр – длина рабочего хода, мм.
Рассчитанную величину частоты вращения или частоты двойных ходов сопоставляют с значениями этих параметров оборудования и принимают ближайшее большее значение nф или nд-х ф;

23
рассчитывают фактическую скорость резания (возвратнопоступательного движения) по формуле:
(17)
рассчитывают, для определения правильности выбранного оборудования и его оптимальной загрузки, по наиболее загруженному переходу для каждой операции коэффициент использования оборудования по мощности ηN, используя зависимость:
(18)
где Nнэ – необходимая мощность главного электродвигателя станка, кВт; Nдэ – действительная мощность главного электродвигателя выбранного станка, кВт.
Необходимую мощность станка Nнэ определяют по следующей зависимости:
(19)
где Рz – сила резания, Н; ф – фактическая скорость резания, м/мин; ηм – механический коэффициент полезного действия, равный – 0,97.
Силу резания Рz определяют расчѐтом или по нормативным данным.
При значении коэффициента использования оборудования по мощности ηN близком к единице станок выбран правильно, а при меньших значениях этого коэффициента необходимо выбирать станок
сменьшей мощностью главного двигателя;
определяют для каждого перехода основное tо время по формуле:
(20)
где Lр – расчѐтная длина обработки, мм; sф – фактическая, принятая по паспорту станка, величина подачи изделия или инструмента, мм/об; nф – фактическая, принятая по паспорту станка, частота вращения детали или инструмента, мин–1; i – число ходов инструмента.
Расчѐтную длину обработки Lр определяют по формуле

24 (21)
где l – действительная длина обработки, определяемая по чертежу, мм; lх – величина, связанная с врезанием и перебегом инструмента и для каждого способа обработки имеет свои особенности в определении, мм;
выбирают по нормативам вспомогательное время на все переходы операции и определяют их сумму. При назначении вспомогательных времен следует учитывать следующее: на вспомогательные переходы назначают время, связанное с установкой детали; на технологические переходы – вспомогательное время, связанное с переходом; на переходы, после которых необходимо производить замеры обрабатываемой поверхности – время, связанное с замерами;
определяют оперативное время;
определяют время на обслуживание рабочего места tОРМ и личные надобности tЛП, которое составляет (6–7)% к оперативному времени tОП;
определяют штучное время;
принимают по нормативам подготовительно-заключительное время ТП-З;
определяют штучно-калькуляционное время tШК. Последовательность определения штучно-калькуляционного
времени tШК для всех видов станочных работ одинакова. Особенностью для каждого вида обработки является определение основного (машинного) времени.
Определение элементов технической нормы времени для расточных работ
В основе расчѐта основного времени tо лежит обработка внутренней цилиндрической поверхности, необходимые технологические параметры которой определяются с учѐтом следующих положений:
глубина резания t выбирается в зависимости от общего припуска на обработку, шероховатости и точности обрабатываемой поверхности;

25
рассчитывают число рабочих ходов i с учѐтом общего припуска на обработку и глубины резания каждого рабочего хода по формуле 15;
выбирают подачу s по нормативам в зависимости от обрабатываемого материала, вида обработки, глубины резания, диаметра и шероховатости обрабатываемой поверхности по табл. 8.
Таблица 8 Подачи sпри получистовом растачивании отверстий при глубине
резания t до 2 мм для достижения шероховатости 40–20 мкм, мм/об
Диаметр растачиваемого отверстия, мм
До 30 |
31 – 50 |
51 |
– 80 |
81 – 120 |
121 |
– 180 |
|
|
|
|
|
|
|
0,04 – 0,08 |
0,06 – 0,1 |
0,08 |
– 0,13 |
0,10 –0,15 |
0,12 |
– 0,18 |
|
|
|
|
|
|
|
определяют по нормативам или рассчитывают скорость резания по формуле
(22)
где С , х и у – коэффициент и показатели степени, зависящие от механических свойств обрабатываемого материала, металла инструмента и условий работы, определяемые по табл. 9; t – глубина резания, мм; s – подача, мм/об; КТ – коэффициент, зависящий от стойкости резца; КМ – коэффициент, зависящий от механических свойств обрабатываемого материала; КИ – коэффициент, зависящий от материала режущей части инструмента; Кφ – коэффициент, зависящий от главного угла в плане резца.
|
|
|
|
|
Таблица 9 |
||
Значения коэффициента Сv и показателей степени х |
и у |
|
|||||
|
|
|
|
|
|
|
|
Материал |
Обрабатываемый |
|
|
|
|
|
|
материал и его |
Характеристика |
|
|
|
|||
резца |
С |
х |
у |
||||
механические |
обработки |
||||||
и его марка |
|
|
|
||||
свойства |
|
|
|
|
|
||
|
|
|
|
|
|
||
|
|
Получистовая |
77 |
0,13 |
0,20 |
||
Твердый |
|
s |
0,4 мм |
||||
Серый чугун НВ 190 |
|
|
|
||||
сплав ВК8 |
|
Грубая |
68 |
0,20 |
0,40 |
||
|
|
||||||
|
|
s |
0,4 мм |
||||
|
|
|
|
|
|||
|
|
|
|
|
|
|

26
Значения коэффициентов КТ, КМ, КИ и Кφ принимаются по табл. 10. Скорость резания при растачивании отверстий расточными резцами определяют по формуле 22 с учѐтом поправочного коэффициента КР, зависящего от диаметра растачиваемого отверстия: при диаметре отверстия менее 75 мм – КР = 0,80; при диаметре 76–150 мм – КР = 0,90; при диаметре 151–250 мм – КР = 0,95; а при диаметре от-
верстия более 250 мм – КР = 1,0.
рассчитывают частоту вращения детали n по формуле 16; Таблица 10
Поправочные коэффициенты на скорость резания
В зависимости от стойкости резца
Обрабаты- |
|
|
|
|
|
Стойкость резца Т, мин |
|
|
|
|
|
|
||||||||||||||
20 |
30 |
45 |
|
60 |
|
75 |
|
90 |
|
120 |
|
150 |
180 |
|
240 |
360 |
||||||||||
ваемый |
|
|
|
|
|
|
||||||||||||||||||||
|
|
Поправочные коэффициенты КТ |
|
|
|
|
||||||||||||||||||||
материал |
|
|
|
|
|
|
||||||||||||||||||||
|
|
|
|
|
на скорость резания |
|
|
|
|
|
|
|||||||||||||||
|
|
|
|
|
|
|
|
|
|
|
|
|||||||||||||||
Незакалѐнная |
1,33 |
1,24 |
1,15 |
|
1,08 |
|
1,04 |
|
1,00 |
|
0,94 |
|
0,91 |
0,87 |
|
0,82 |
0,76 |
|||||||||
сталь |
|
|
|
|
|
|
||||||||||||||||||||
|
|
|
|
|
|
|
|
|
|
|
|
|
|
|
|
|
|
|
|
|
|
|
|
|
|
|
В зависимости от обрабатываемого материала |
|
|
|
|
||||||||||||||||||||||
Обрабатывае- |
|
Механические свойства |
|
|
|
|
Поправочный |
|||||||||||||||||||
Твердость |
|
|
|
|
|
Прочность |
|
|
|
|
коэффициент |
|||||||||||||||
мый материал |
|
|
|
|
|
|
|
|
|
|||||||||||||||||
|
НВ |
|
|
|
материала |
В, МПа |
|
|
|
|
КМ |
|
||||||||||||||
|
|
|
|
|
|
|
|
|
|
|||||||||||||||||
|
140 – 160 |
|
|
|
|
|
|
|
– |
|
|
|
|
|
|
|
|
|
1,50 |
|
||||||
|
160 – 180 |
|
|
|
|
|
|
|
– |
|
|
|
|
|
|
|
|
|
1,20 |
|
||||||
Серый чугун |
180 – 200 |
|
|
|
|
|
|
|
– |
|
|
|
|
|
|
|
|
|
1,00 |
|
||||||
200 – 220 |
|
|
|
|
|
|
|
– |
|
|
|
|
|
|
|
|
|
0,85 |
|
|||||||
|
|
|
|
|
|
|
|
|
|
|
|
|
|
|
|
|
|
|||||||||
|
220 – 240 |
|
|
|
|
|
|
|
– |
|
|
|
|
|
|
|
|
|
0,72 |
|
||||||
|
240 – 260 |
|
|
|
|
|
|
|
– |
|
|
|
|
|
|
|
|
|
0,63 |
|
||||||
Алюминий |
|
– |
|
|
|
|
|
|
|
7 – 16 |
|
|
|
|
|
|
|
|
|
6,00 |
|
|||||
и силумин |
|
– |
|
|
|
|
|
|
|
17 – 28 |
|
|
|
|
|
|
5,00 |
|
||||||||
Дюралюминий |
|
– |
|
|
|
|
|
|
|
|
|
35 |
|
|
|
|
|
|
|
|
|
|
5,00 |
|
||
|
– |
|
|
|
|
|
|
|
|
|
35 |
|
|
|
|
|
|
|
|
|
|
4,00 |
|
|||
|
|
|
|
|
|
|
|
|
|
|
|
|
|
|
|
|
|
|
|
|
|
|||||
В зависимости от марки твердого сплава инструмента |
|
|||||||||||||||||||||||||
Марка твѐрдого сплава |
|
|
|
Т5К |
|
Т15 |
|
Т30 |
|
|
|
ВК8 |
|
ВК6 |
ВК |
|||||||||||
|
|
|
10 |
|
К6 |
|
К4 |
|
|
|
|
3 |
||||||||||||||
|
|
|
|
|
|
|
|
|
|
|
|
|
|
|
|
|
|
|
||||||||
Поправочный коэффициент КИ |
|
0,65 |
|
1,0 |
|
|
1,5 |
|
1,0 |
|
1,2 |
1,5 |
||||||||||||||
В зависимости от главного угла в плане резца φО |
|
|
|
|
||||||||||||||||||||||
Обрабатываемый |
|
|
|
|
|
Главный угол резца в плане |
|
|||||||||||||||||||
|
|
30 |
|
|
|
45 |
|
60 |
|
|
|
|
|
70 |
|
|
|
80 |
||||||||
материал |
|
|
|
|
|
|
|
|
|
|
|
|
|
|
||||||||||||
|
|
|
|
Поправочный коэффициент Кφ |
|
|||||||||||||||||||||
|
|
|
|
|
|
|
||||||||||||||||||||
Серый чугун |
|
|
1,20 |
|
|
1,00 |
|
0,88 |
|
|
|
|
0,83 |
|
0,73 |

27
рассчитывают основное (машинное) время по формуле 20. Величина врезания и выхода резца lх в формуле 21 равна
(23)
где l1 – величина врезания резца, равная
(24)
t – глубина резания, мм; φ – главный угол резца в плане, градус; l2 – перебег резца при расточке на проход (l2 = 2 – 3 мм); l3 – взятие пробной стружки (l3 = 1...2 мм).
определяют по нормативам табл. 11 вспомогательное время tВ У/С на установку и снятие детали на станок;
Таблица 11 Вспомогательное время tВ У/С на установку и снятие детали электроталью при работе на расточных и хонинговальных
станках, мин
Способ установки детали |
|
Масса детали, кг (до) |
|
||||
на столе станка |
30 |
50 |
80 |
120 |
200 |
300 |
500 |
На столе с креплением |
|
|
|
|
|
|
|
болтами с планками |
2,8 |
3,0 |
3,3 |
3,6 |
4,0 |
4,4 |
5,3 |
по обработанной поверхности |
|
|
|
|
|
|
|
На угольнике с креплением |
|
|
|
|
|
|
|
болтами с планками |
5,5 |
6,0 |
7,0 |
– |
– |
– |
– |
с простой выверкой |
|
|
|
|
|
|
|
На столе в тисках |
|
|
|
|
|
|
|
с эксцентриковым зажимом |
2,3 |
2,5 |
2,8 |
3,1 |
3,5 |
3,9 |
4,8 |
без выверки |
|
|
|
|
|
|
|
То же, с выверкой |
2,8 |
3,0 |
3,3 |
3,6 |
4,0 |
4,4 |
5,3 |
определяют вспомогательное время tВП, связанное с переходом по табл. 12, на дополнительные приѐмы работ – по табл. 13, на очистку приспособления от стружки – по табл. 14;
определяют оперативное время tОП;
определяют время на обслуживание рабочего места tОРМ и личные надобности tЛП, которое составляет (6–7)% к оперативному времени tОП;
рассчитывают штучное время tШТ;
28
определяют по табл. 15 подготовительно-заключительное время ТП-З при обработке партии деталей Z;
определяют штучно-калькуляционное время tШК.
Таблица 12 Вспомогательное время, связанное с переходом tВП1
при расточке цилиндров (на один ход), мин
|
|
|
Длина стола станка, мм |
|
|
|
||||||||||
|
Характеристика |
750 |
|
1250 |
|
|
|
1800 |
|
|
||||||
|
|
|
|
|
|
|
|
|
|
|
|
|
|
|
|
|
|
|
Длина обрабатываемой |
|
|
|
|||||||||||
|
выполняемой работы |
|
|
|
|
|||||||||||
|
|
|
поверхности, мм (до) |
|
|
|
|
|
||||||||
|
|
|
|
|
|
|
|
|
||||||||
|
|
100 |
200 |
100 |
200 |
|
300 |
|
100 |
|
200 |
|
300 |
|
||
|
Резец, установленный |
0,12 |
0,17 |
0,15 |
0,21 |
|
0,26 |
|
0,18 |
|
0,26 |
|
0,34 |
|
||
|
на размер |
|
|
|
|
|
||||||||||
|
|
|
|
|
|
|
|
|
|
|
|
|
|
|
|
|
|
С взятием одной пробной стружки |
|
|
|
|
|
|
|
||||||||
|
с измерением линейкой или шаблоном: |
|
|
|
|
|
||||||||||
|
при размере 100 мм |
0,53 |
0,58 |
0,64 |
0,70 |
|
0,75 |
|
0,76 |
|
0,84 |
|
0,92 |
|
||
|
при размере 300 мм |
0,55 |
0,60 |
0,66 |
0,72 |
|
0,77 |
|
0,78 |
|
0,86 |
|
0,94 |
|
||
|
С взятием одной пробной стружки с измерением штангенциркулем: |
|
||||||||||||||
|
при размере 100 мм |
0,58 |
0,63 |
0,69 |
0,75 |
|
0,80 |
|
0,81 |
|
0,89 |
|
0,97 |
|
||
|
при размере 300 мм |
0,67 |
0,72 |
0,78 |
0,84 |
|
0,89 |
|
0,90 |
|
0,98 |
|
1,06 |
|
||
|
С взятием двух пробных стружек |
|
|
|
|
|
|
|
||||||||
|
с измерением линейкой или шаблоном: |
|
|
|
|
|
||||||||||
|
при размере 100 мм |
0,85 |
0,90 |
1,00 |
1,06 |
|
1,11 |
|
1,17 |
|
1,25 |
|
1,33 |
|
||
|
при размере 300 мм |
0,91 |
0,96 |
1,06 |
1,12 |
|
1,17 |
|
1,23 |
|
1,31 |
|
1,39 |
|
||
|
С взятием двух пробных стружекс измерением штангенциркулем: |
|
||||||||||||||
|
при размере 100 мм |
1,07 |
1,12 |
1,22 |
1,28 |
|
1,33 |
|
1,39 |
|
1,47 |
|
1,55 |
|
||
|
при размере 300 мм |
1,37 |
1,42 |
1,52 |
1,58 |
|
1,63 |
|
1,69 |
|
1,77 |
|
1,85 |
|
||
|
Примечание. При перемещении стола вручную к времени, |
|
|
|
||||||||||||
|
указанному в таблице добавляется время, равное 0,05 мин |
|
|
|
||||||||||||
|
на каждые 100 мм хода стола |
|
|
|
|
|
|
|
|
|
|
|
|
|
|
|
|
|
|
|
|
|
|
|
|
|
Таблица 13 |
||||||
|
Вспомогательное время, связанное с переходом tВП2 |
|
|
|
||||||||||||
|
на дополнительные приѐмы работы, мин |
|
|
|
|
|
||||||||||
|
|
|
|
|
|
|
|
|
|
|||||||
|
Характеристика приѐмов работ |
|
|
Длина стола станка, мм |
|
|||||||||||
|
|
|
750 |
|
1250 |
|
1800 |
|
||||||||
|
|
|
|
|
|
|
|
|
||||||||
|
1 |
|
|
|
|
|
2 |
|
3 |
|
|
|
4 |
|
||
|
Изменить частоту вращения шпинделя: |
|
|
|
|
|
|
|
|
|
|
|
|
|||
|
одним рычагом |
|
|
|
|
0,04 |
|
0,04 |
|
|
0,05 |
|
||||
|
двумя рычагами |
|
|
|
|
0,06 |
|
0,06 |
|
|
0,08 |
|

29
Продолжение табл. 13
1 |
2 |
3 |
4 |
|
Изменить величину подачи: |
|
|
|
|
одним рычагом |
0,03 |
0,03 |
0,04 |
|
двумя рычагами |
0,05 |
0,05 |
0,06 |
|
Повернуть приспособление |
– |
0,09 |
0,09 |
|
с рабочей позиции на загрузочную |
|
|||
|
|
|
|
|
Поставить щиток ограждения |
0,16 |
0,18 |
0,20 |
|
от стружки и снять |
|
|||
|
|
|
|
|
|
|
Таблица 14 |
Вспомогательное время tВП3на очистку приспособления
от стружки при работе на расточных и хонинговальных станках, мин
Характери- |
Характеристика применяемого приспособления |
|||||||||
Без выступов |
С выступами |
Коробчатое |
||||||||
стика |
||||||||||
и впадин |
и впадинами |
|||||||||
способа |
|
|
|
|||||||
|
|
|
|
|
|
|
|
|
||
|
Размеры очищаемой поверхности, см |
|
||||||||
очистки |
|
|
||||||||
10х10 |
20х30 |
30х50 |
10х10 |
20х30 |
30х50 |
10х10 |
20х30 |
30х50 |
||
|
||||||||||
|
|
|
|
|
|
|
|
|
|
|
Сжатым |
0,06 |
0,07 |
0,08 |
0,08 |
0,09 |
0,11 |
0,10 |
0,12 |
0,14 |
|
воздухом |
||||||||||
|
|
|
|
|
|
|
|
|
||
|
|
|
|
|
|
|
|
|
|
|
Щѐткой |
0,06 |
0,08 |
0,10 |
0,08 |
0,11 |
0,13 |
0,10 |
0,15 |
0,17 |
Определение элементов технической нормы времени для хонинговальных работ
В основе расчѐта основного времени tо лежит обработка внутренней цилиндрической поверхности, необходимые технологические параметры которой определяются в следующей последовательности:
определяют припуски 2Z на обработку на диаметр, которые для предварительного хонингования составляют 0,02...0,08 мм и для окончательного – 0,01...0,02 мм;
определяют длину хонингования lХ (рис. 6б), которая равна длине зеркала блока или гильзы цилиндров, мм;
определяют длину брусков хонинговальной головки по формуле
(25)
определяют выход U брусков за торцы обрабатываемой поверхности по формуле U = (0,2...0,4) lИ;