
Модуль 1 ответы
.pdf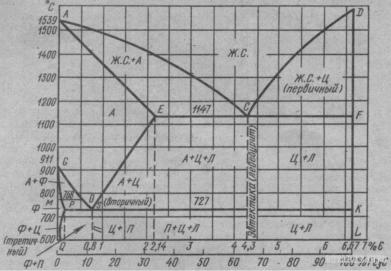
Диаграмма состояния железо углерода
А – Аустенит Ф – Феррит Ц – Цементит П – Перлит
Л – Ледебурит
Жаростойкие стали
Жаростойкие (окалиностойкие) стали и сплавы, стойкие против химического разрушения поверхности в газовых средах при температуре более 500 ° С, работающих в ненагруженном и слабо нагруженном
состоянии.
Жаростойкие (окалиностойкие) стали и сплавы марок 15Х5, 08Х18Т1, 15Х18СЮ, 08Х20Н14С2, 09Х14Н16Б, 12Х18Н12Т, ХН78Т и др. применяют для изготовления труб с температурой нагрева 600 ° С и более; марок 40Х9С2, 40Х10С2М, 30Х13Н7С2, 55Х20Г9Н4, 45Х22Н4МЗ - для изготовления клапанов двигателей; марок. 12X13, ХН28ВМАБ, ХН70Ю и др. для изготовления деталей турбин и котлов.
Зависимость твёрдости от прочности
σв = k * HB
kстали = 0,33 – 0,35
kмеди = 0,4 – 0,5
kалюминия = 0,33 – 0,36
НВ – число твердости по Бринеллю.
Закалка и ее виды
Закалка – процесс термической обработки, при которой деталь нагревают до определенной температуры, выдерживают при этой температуре и быстро охлаждают, предназначена для предания сплавам большей твердости и прочности. На качество закалки большое влияние оказывает скорость охлаждения деталей.
Виды:
Поверхностная (увеличивает твердость только поверхностных слоев деталей, а структура сердцевины остаётся без изменений)
По способы нагрева делиться на:
a)Пламенную (нагревают кислородно-ацетиленовым пламенем, а потом под воду – охладить)
b)Электроконтактную (ею повергают цилиндрические детали)
c)Высокочастотную (нагрев токами высокой частоты, от 100 кГц и более, в специальных электрических индукторах, потом охлаждение водой)
d)Электролитную (нагрев до закалочных температур и их охлаждение в электролитических ваннах)
Износостойкие, коррозионностойкие и жаростойкие чугуны
К износостойким чугунам относятся антифрикционные и фрикционные
чугуна.
Антифрикционными называются износостойкие чугуны, имеющие низкий коэффициент трения. Из них изготавливают детали, которые работают в условиях трения скольжения: подшипники скольжения, их вкладыши, грундбуксы, сальники и другие подобные детали. Маркируются: АЧС-1, АЧС-2, АЧС-3, АЧС-4, АЧС-5, АЧС-6, АЧК-1, АЧК-2, АЧВ-1, АЧВ-2. Буквы АЧ означают антифрикционный чугун, а буквы С, К, В - базовый чугун (серый, ковкий, высокопрочный), на основе которого он получен, цифра - условный номер марки.
Фрикционные чугуны имеют высокий коеф. трения. Маркируются аналогично, вместо А пишется Ф.
Коррозионностойкие чугуны, так как даже обычные чугуны имеют более высокую коррозионную стойкость в атмосфере и морской воде, чем углеродистые стали, то вводя в чугун более 12% хрома и снижая содержание углерода, получают нержавеющий чугун. ЧНХТ, ЧН1ХМД, ЧНИ5Д7Х2 и др.
Жаростойкое чугуны - устойчивые против окисления и сохраняющие механические свойства при высоких температурах нагрева (=600 градусов) ЧХ16, ЧС5, ЧЮ30 и др.
Многие детали из высокопрочных чугунов выгодно изготовлять из жаростойких чугунов, чем из жаропрочной стали, так как они дешевле. Пример: двигатели внутреннего возгорания, поршневые кольца, коленчатые валы и др.
Изоляционные материалы
Изоляционные материалы применяют для покрытия поверхностей, чтобы уменьшить теплообмен между средами с различной температурой, а также снизить уровень шума в судовых помещениях. В связи с этим изоляционные материалы делят на теплоизоляционные и звукоизоляционные.
Теплоизоляционные материалы должны удовлетворять следующим требованиям: иметь низкий коеф. теплопроводности (<0,1 Вт/м*градус), низкую гигроскопичность и водопоглощение, быть тепло- и огнестойкими, стойкими против гниения, порчи насекомыми и грызунами, нетоксичными. Их плотность составляет 30 – 400 кг/м3.
По назначению материалы делятся на: для изоляции корпусных конструкций, машин, механизмов и судовых трубопроводов. К примеру: пробка, минеральная вата, стекловолокнистые материалы, пеностекло, алюминиевая фольга, капроновые волокна, пенопласт и поропласт, албест (шнуры, ткань, картон и бумагу), напыляемую изоляцию и др.
Инструментальные углеродистые и легированные стали. Маркировка. Область применения.
Инструментальная углеродистая сталь делится на качественную и высококачественную. Качественную сталь выплавляют в мартеновских печах, а высококачественную - в электрических.
У7, У8, У8Г, У9, У10, У11, У12, У13. Буква У означает инструментальная углеродистая сталь, а цифры - содержание углерода в десятых долях процента. Например, У11 - качественная инструментальная углеродистая сталь с содержанием углерода 1,1%, остальное - железо, другие элементы и примеси. А - показатель высококачественной стали. Например, У7А - высококачественная инструментальная углеродистая сталь, содержащая 0,7% углерода.
У7, У7А, У8, У8А, У8Гта У8ГА – зубила, молотки, отвертки, пробойники, ножници по металлу, пуансоны, матрици и т.п.
У9, У9А, У10 и У10А - строгальные резци, калибры, фасонные штампы, развертки, столярные инструменты и т.
У11, У11А, У12, У12А, У13 и У13А – напильники, шаберы, метчики, фрезы, волочильный инструмент и тому подобное.
Высоколегированные быстрорежущие стали Р18, Р12, Р9, Р6М3, Р6М5, РИ8Ф2, Р14Ф4, Р9Ф5, Р18К5Ф2, Р10К5Ф5, Р9К5,
Р6М5К5, Р9К10, Р9М4К8. В обозначении марки стали начальная буква Р означает быстрорежущей стали (Р - начальная буква слова рапид, что означает быстрый). Цифры, стоящие за ней, показывают среднее содержание вольфрама в процентах, другие буквы и цифры, если они есть, - содержание обозначенных легирующих элементов в процентах. В обозначении марок стали не указывается содержание хрома (от 3 до 4,6%), углерода (от 0,7 до 1,1%) и молибдена (до 1% включительно). Например, Р9Ф5 - быстрорежущая сталь, содержащая 9%. вольфрама и 5% ванадия, остальное - железо, хром, углерод и другие примеси.
Р18 и Р12 служит для изготовления всех видов режущего инструмента, применяемого при обработке конструкционных материалов.
Р12 с режущими свойствами почти не уступает стали марки Р18, а по износостойкости превосходит ее.
Р9 используют для изготовления инструмента простой формы Р6М3 - для изготовления инструмента небольших сечений, который
работает под ударными нагрузками Р6М5 применяют для изготовления всех видов инструмента и в
частности резьбонарезного, который работает под ударными нагрузками Р18Ф2 изготавливают инструмент, который применяется при обработке
материалов повышенной твердости и вязкости Р14Ф4 и Р9Ф5 - инструмент, который работает со снятием небольшой
стружки Р18К5Ф2, Р9М4К8, Р10К5Ф5, Р6М5К5 применяют для изготовления
инструмента, предназначенного для обработки высокопрочных нержавеющих и жаропрочных сталей и сплавов
Р9К5 и Р9К10 используют для изготовления инструмента, предназначенного для обработки нержавеющих и жаропрочных сталей и сплавов, а также сталей повышенной твердости и вязкости.
Испытание металлов на твердость, методы, приборы, принцип испытания, единицы измерения.
Твердостью называется способность металла сопротивляться проникновению в него другого более твердо материала. Самые распространенные методы, при которых в металл под действием статической нагрузки вдавливают специальный
наконечник-индентор (шарик-конус или пирамида). Эти методы называют по фамилиям их авторов Бринелю, Роквелла и Виккерса. Твердость определяют также ударным вдавив шарики (метод Польди) и методом упругой отдачи бойка (метод Шора). Примерно твердость можно оценить и по углублением, которые оставляют чертилка, кернер, зубило и другие режущие инструменты. О твердости судят по глубине отпечатка, оставленного на металле наконечником или режущим инструментом. Чем больше глубина отпечатка при одинаковой нагрузке на внедряемый материал одинакового размера, тем меньше твердость и наоборот. Испытывая металл на твердость, можно просто и быстро определить его механические свойства, причем не только в лабораториях, но и на производстве. По величине твердости можно примерно судить и о других механические свойства металлов: прочность, износостойкость и др., А также обрабатываемость. Чем металл тверже, тем труднее его обрабатывать.
Метод Бринелю заключается в вдавливании под действием статической нагрузки в поверхность испытуемого образца стального шарика диаметром 2,5; 5 или 10 мм. Твердость по методу Бринелю выражается в числах твердости НВ (Н
-твердость, В - Бринелю). Испытания на твердость по методу Бринелю проводятся на приборах твердомер Бринелю с применением плоских или круглых образцов и деталей. Для получения точных результатов на поверхности образца не должно быть ржавчины, окалины, вмятин и тому подобное. Метод Роквелла заключается в вдавливании под действием статической нагрузки в поверхность испытуемого металла алмазного конуса или стальной закаленной шарики диаметром 1,59 мм. В приборах (твердомеры) Роквелла в отличие от приборов Бринелю число твердости определяют непосредственно по шкале индикатора. При испытании сначала прикладывают предварительную нагрузку 0,1 кН, а затем дополнительное с таким расчетом, чтобы полное нагрузка составляла 0,6; 1,0 и 1,5 кН Стрелка индикатора при полной нагрузке образца показывает разницу глубин проникновения наконечника в испытуемый металл под действием полного и предварительной нагрузки. Индикатор имеет всего 100 делений и две шкалы: черную и красную. Чера шкала применяется для измерения твердости при испытании левою шариком под нагрузкой 1 кН, черная
-при испытании алмазным конусом под нагрузкой 1,5 или 0,6 кН. Красная шкала обозначается буквой В, а черная - буквой С, если испытания ппроводиться под нагрузкой 1,5 кН, или буквой А, если испытание проводится под нагрузкой 0,6 кН. Числа твердости по Роквепом не имеют размерности и обозначаются символом НР (Н - твердость, Р - Роквелл). К символу добавляется обозначение шкалы индикатора (А, В или С), при которой измерялась твердость, и
соответствующее числовое значение твердости. Методом Роквелла можно испытать мягкие и твердые металлы, а также готовые изделия, так как отпечатки от наконечника незначительны. Испытания занимает мало времени (не более 50 с), не требует никаких измерений, показания читаются непосредственно на шкале индикатора. Метод Виккерса заключается в вдавливании под действием статической нагрузки на поверхность испытуемого металла четырехгранной алмазной пирамиды. Вдавливания выполняют одним из следующих нагрузок: 50, 100, 200, 300, 500, 1000 или 1200 Н. Величину нагрузки выбирают в зависимости от толщины испытуемого металла. Чем тоньше металл, тем меньше нагрузка. Метод Виккерса проводят на приборах Виккерса, измеряют полученный отпечаток с помощью микроскопа и находят значения твердости Н \ / (Н - твердость, V - Виккерс) по специальной формуле.
Практически число твердости по Виккерсу находят из разработанных для этого метода таблиц (по среднеарифметической длине диагоналей отпечатка). Метод Виккерса дает результаты повышенной точности. Метод Польди заключается в вдавливании стального шарика под действием динамического (ударного) нагрузки на поверхность испытуемого металла и эталонного образца. По соотношению площадей или диаметров отпечатков расчетным путем по таблицам определяют твердость металла. Она будет тем меньше, чем больше отпечаток на испытуемому металле по сравнению с отражением на эталонном образце, и наоборот. При испытании методом Польди твердость выражается в числах твердости по Бринелю (НВ). Метод Польди прост. Его применяют для измерения твердости массивных изделий с приближенной точностью.
Испытание металлов на ударную вязкость. Принципиальная схема маятникового копра, работа, затраченная на разрушение образца.
Ударной вязкостью (динамической прочностью) называется способность металлов сопротивляться воздействию ударных (динамических) нагрузок. Многие детали машин, конструкции и инструменты испытывают в эксплуатации ударные нагрузки.
Металлы, которые легко разрушаются под действием ударной нагрузки, называются хрупкими. Они не пригодны для изготовления деталей, работающих в условиях ударных нагрузок. Вязкими называются металлы, которые разрушаются при значительных ударных нагрузках и больших пластических деформациях. Испытания металлов на ударную вязкость проводят на механизмах, которые называются маятниковыми копрами . Оно заключается в
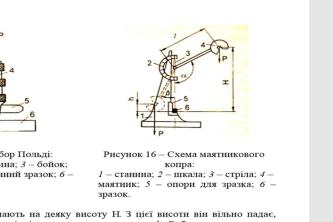
ударном взломе (изгибе) маятником копра образца и в подсчете потраченной работы на разрушение образца.
Маятник поднимают на некоторую высоту Н. С этой высоты он свободно падает, разрушает образец и снова поднимается на некоторую высоту b. Работа, затраченная на разрушение образца, A = P (H - h)
или A = Pl (cosβ - cosα)
где P - сила тяжести (вес) маятника, Н; Н - высота подъема маятника до
удара, м; h - высота подъема маятника после удара, м; l - длина маятника., г. Ударную вязкость металла определяют по величине удельного ударной вязкости αН, равной отношению работы, затраченная на разрушение образца, к площади его поперечного сечения в месте разрушения, αн = А / Р
где А - работа, затраченная на разрушение образца, Дж; Г - площадь поперечного сечения образца в месте разрушения, м2.
Современный маятниковый копер имеет шкалу, градуированную непосредственно в единицах работы. Если поднять маятник на некоторую высоту Н, то стрелка покажет запас энергии маятника к удару РН в джоулях. После разрушения образца маятник поднимается на некоторую высоту h, в это время стрелка покажет запас энергии маятника Рh после удара. Таким образом, ударная вязкость
αН = (PH - Ph) / F
Ударная вязкость зависит не только от рода металла, но и от его температуры, химического состава, структуры и тому подобное. Например, две марки стали с различной структурой могут иметь совершенно разные значения ударной вязкости, но почти одинаковые другие механические свойства. Образцы для испытания металла на маятниковом копре изготавливают квадратного сечения 10x10 мм в. Чтобы облегчить злом, в средней части образца на одной из граней делают надрез глубиной 2 мм и радиусом закругления 1 мм. Такой образец устанавливают на две опоры надрезом в сторону, противоположную удара маятника. По виду разрушения образца можно определить хрупкость или пластичность металла.
Испытание металлов на усталостную прочность. Оборудования и образцы.
Способность металлов сопротивляться разрушению от усталости называется уставшей прочностью (выносливостью). Показателем ее является граница усталости (выносливости), которую определяют в ходе испытаний на специальных машинах. Испытания проводят в переменный изгиб, растяжениесжатие и кручение. Чаще применяют способ испытания изгибом при вращении . В этом случае один конец образца закрепляют в патроне, а ко второму через шарикоподшипник подвешивают груз При вращении внешние волокна образца будут попеременно испытывать растягивая и сжимая усилия. При достижении некоторого числа изменений (циклов) образец разрушается. Число циклов определяют по установленному на станке счетчику. Границей усталости металлов называется максимальное напряжение, при котором образец еще выдерживает неограниченное число циклов, не разрушаясь. Предел усталости обозначают: при изгибе - σ-1; при растяжении-сжатии - σ-1Р; при кручении - τ-1. Между границей усталости и пределом прочности существует такая приблизительная зависимость: σ-1 = 0,47σв; σ-1Р = 0,32 σв; τ-1 = 0,22 σв Прочность от усталости зависит от значения переменных напряжений, поверхности деталей и других факторов. ее следует учитывать при созидания, например, быстроходных судов, сверхзвуковых самолетов, космических кораблей из мощных турбин, которые испытывают при эксплуатации переменных нагрузок. Металлы, которые работают в сложных условиях, испытывают при повышенных и пониженных температурах, в условиях коррозии, при стирании и тому подобное.
Испытание на растяжение-сжатие, прочность, упругость, пластичность, относительное сужение. Пределы прочности и текучести.
Испытания металлов на растяжение. Испытания металлов растяжения позволяет определить наиболее важные механические свойства металлов: прочность, упругость и пластичность. Прочность - способность металлов сопротивляться разрушению под действием внешних нагрузок. Упругость способность - металлов восстанавливать первоначальную форму и размеры после прекращения действия нагрузок, которые вызвали их изменения. Пластичность - способность металлов необратимо изменять свою форму и размеры, не разрушаясь под действием нагрузки. Противоположным пластичности свойством является хрупкость. Предел прочности, называемый также временным сопротивлением, - важнейшая характеристика. Если
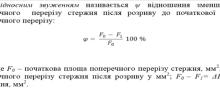
напряжение в изделии, конструкции или инструменте превысят предел прочности, то они разрушаются. Относительным сужением называется ψ отношение уменьшения площади поперечного сечения стержня после разрыва к начальной площади его поперечного сечения:
где F0 - начальная площадь поперечного сечения
стержня, мм2; F1 - площадь поперечного сечения стержня после разрыва в мм2; F0 - F1 = ΔF
абсолютное сужение, мм2. Чем больше значение относительного удлинения и сужения, тем пластичнее металл. Испытания металлов на растяжение проводят на разрывных машинах, которые обеспечивают приложения к образцам статических, то есть постоянных или плавно растущих нагрузок, для испытания применяют образцы определенных размеров и форм.
При больших нагрузках удлинение образца не будет подлежать закона пропорциональности, что вызовет остаточные деформации. Увеличим нагрузку к так называемому нагрузки предела текучести. При этом длина образца будет увеличиваться без увеличения нагрузки. Отношение нагрузки РТ, к площади поперечного сечения образца F называется пределом текучести: σТ = РТ / F металлов, которые не имеют при испытаниях участка текучести определяют условную предел текучести при остаточном удлинении, равное 0,2% расчетной длины образца. Условным пределом текучести называется напряжение, при котором образец получает остаточное удлинение, равное 0,2% своей расчетной длины σ0,2 = Р0,2 / F где P0,2 - условное нагрузки предела текучести, Н.
Качественная сталь. Маркировка. Область применения.
Качественную сталь выплавляют в мартеновских печах.. Высококачественная сталь отличается от качественной меньшим содержанием серы и фосфора и, значит, имеет большую прочность и сопротивляемость ударным нагрузкам. Качественная сталь содержит не более 0,030% серы и 0,035% фосфора, а высококачественная - не более 0,020% серы и 0,030% фосфора. Качественная инструментальная углеродистая сталь имеет следующие марки: У7, У8, У8Г, У9, У10, У11, У12, У13. Буква В означает инструментальная углеродистая сталь, а цифры - содержание углерода в десятых долях процента. Например, У11 - качественная инструментальная углеродистая сталь с содержанием углерода 1,1%, остальное - железо, другие элементы и примеси. Сталь марок У7, У7А, У8, У8А, У8Гта У8ГА применяют для изготовления инструментов, испытывающих ударных нагрузок: зубил, крейцмейселей, Кернер, молотков, отверток, пробойников, ножниц по металлу, пуансонов, матриц и т.п. (буква Г означает
повышенное содержание марганца в стали марок У8Г и У8ГА по сравнению со сталью марок У8 и У8А). Сталь марок У9, У9А, У10 и У10А предназначена для изготовления инструментов, которые не поддаются сильным толчкам и ударам, но требуют высокой твердости: строгальных резцов, калибров, фасонных штампов, разверток, столярного инструмента и т. Из стали марок У11, У11А, У12, У12А, У13 и У13А изготовляют особенно твердые инструменты, которые работают под определенной нагрузкой или без него: напильники, шаберы, метчики, фрезы, волочильный инструмент и тому подобное.
Керамические материалы, виды и область применения.
Керамические материалы (керамику) получают спеканием порошков минеральных веществ (глина, полевой шпат, кварц, тальк и т.п.). Керамика обладает высокой теплостойкостью, химической стойкостью и водостойкостью. Она имеет хорошие диэлектрические свойства и твердость, не поддается старению и не дает остаточных деформаций под действием механических нагрузок. Основной ее недостаток - хрупкость и высокая усадка изделий при обжига. Керамику используют в электрической и радиотехнической промышленности как диэлектрики - установочные (изоляторные), конденсаторные и пьезоэлектрические. Установочную керамику (электрофарфор, радио фарфор и др.) Применяют для изготовления изоляторов, колодок, плат, катушек, каркасов и тому подобное. Конденсаторная керамика (сегнетокерамики, тиконды, термокоды и др.) Служит для изготовления конденсаторов различной емкости. Пьезоэлектрическую керамику на основе титаната бария (ТБС и ТБКС), ниобата бария (НБС), ниобата и титаната свинца (НТС) используют в устройствах генерации и приема ультразвука. Огнеупорные материалы (огнеупоры) применяют для облицовки (футеровки) внутреннего пространства нагревательных устройств. По составу их делят на кремнеземистые, алюмосиликатные, магнезиальные, магнезиальновапняни. магнезиальносиликатные, углеродные и др. В машиностроении и других отраслях керамику как долговечный материал, устойчивый против сноса, нагрева и агрессивных сред, используют для изготовления огнеупоров, санитарно-технических изделий, посуды, плиток для облицовки труб, строительного кирпича, черепицы и тому подобное. В судостроении керамику применяют в судовых паровых котлах, камерах сгорания газотурбинных установок, газовых турбинах, различных нагревательных устройствах, в электро- и радиоустановках в виде плиток для покрытия палуб, во влажных помещениях и для облицовки помещений общего пользования (ванн, умывальников, гальюнивта др. ), для изготовления умывальников, унитазов и других санитарно-технических изделий.