
Аэрокосмическая техника высокие технологии и инновации – 2016
..pdfСписок литературы
1.Кацев П.Г. Статистические методы исследования режущего инструмента. – М.: Машиностроение, 1974. – 231 с.
2.Макаров В.Ф. Выбор и назначение оптимальных условий протягивания заготовок из труднообрабатываемых материалов: учеб. пособие. – Пермь: Изд-воПерм. гос. техн. ун-та, 2008. – 396 с.
3.Спиридонов А.А. Планирование эксперимента при исследовании технологических процессов. – М.: Машиностроение, 1981. – 184 с.
4.Макаров В.Ф., Шохрин А.В., Потягайло О.Н. Управление процессом точения деталей ГТД на станках с ЧПУ по физическим параметрам процесса резания [Электронный ресурс]. – URL: http://studydoc.ru/doc/2009815/6-udk-621.9-v.f.-makarov---
a.v.- shohrin---o.n.-potyagajlo (дата обращения: 8.10.2016).
УДК 51-74
ВЛИЯНИЕ КОЭФФИЦИЕНТА ИСПАРЕНИЯ СУБОКСИДА AlO НА ЕГО СОДЕРЖАНИЕ В ПРОДУКТАХ СГОРАНИЯ
АЛЮМИНИЕВО-ВОЗДУШНОЙ СМЕСИ А.Ю. Крюков, В.И. Малинин
Пермский национальный исследовательский политехнический университет, Пермь, Россия
alexkryukov@list.ru, malininvi@mail.ru
Определены зависимости содержания субоксида AlO в продуктах сгорания от коэффициента избытка воздуха алюми- ниево-воздушной смеси и коэффициента его испарения E3 в технологических и энергетических установках. Исследования выполнены для 0,3 1,2 и 0,00025 E3 0,25 с учетом неравновесной термодинамики горения. Установлено, что количество AlO не превышает 0,5 % газовой фазы. Проведены сравнения термодинамических параметров при и предельных значениях E3 для подтверждения адекватности используемой математической модели и соответствующего программного обеспечения.
71
Ключевые слова: математическое моделирование, горение, аэровзвесь, алюминий, субоксид, коэффициент испарения, коэффициент избытка воздуха, неравновесная термодинамика.
Изучение воспламенения и сгорания аэровзвесей металлов методами математического моделирования является актуальным направлением современной теории горения и при наличии специального программного обеспечения позволяет проводить параметрические исследования и устанавливать влияние различных факторов на состав продуктов сгорания и термодинамические параметры реагирующих смесей [1]. В результате появляется возможность проверить некоторые гипотезы, принимаемые на этапе разработки модели, выявить степень влияния учитываемых физических явлений и химических реакций на исследуемые процессы.
Ранее в работе [1] были получены зависимости количества субоксида алюминия AlO от коэффициента избытка воздуха и установлено, что доля AlO достаточно мала при = 0,1–1,2. Следовательно, можно сделать первоначальный вывод о том, что образованием AlO при указанных значениях можно пренебречь. Однако в работе [1] расчеты проводились при одном полученном из анализа конкретных экспериментальных условий значении коэффициента испарения субоксида AlO E3 = 0,0025. Данный параметр [2] характеризует скорость разложения оксида Al2O3 по реакции
0,5Al2O3c AlOg 0,25O2g QE3i .
Для полного обоснования возможности исключения образования AlO из расчетов нужно провести исследования для широкого диапазона изменений E3. Эта задача решается в настоящей работе, целью которой является исследование процесса горения алюминиево-воздушной смеси при 0,3 1,2 и значениях коэффициента испарения 0,00025 E3 0,25 с использованием модели [2], учитывающей неравновесную термодинамику процессов.
В результате моделирования для ряда значений E3 получены зависимости относительного содержания субоксида в газовой фазе от коэффициента избытка воздуха. Результаты расчетов для
72
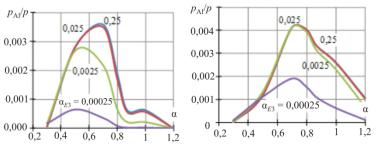
разного времени пребывания реагирующей смеси в камере представлены на рисунке. На их основании можно сделать следующие выводы.
аб
Рис. Зависимости относительного количества субоксида AlO от и E3: p = 0,25 МПа – давление смеси, a – = 5 мс; б – = 10 мс
1.При малых временах пребывания реагирующей смеси в
камере содержание AlO зависит от E3, а с увеличением доля субоксида становится функцией только , причем образование AlO наблюдается только в диапазоне 0,3 1,0 и его количество не превышает 0,5 % от общей доли газовой фазы для всех вариантов расчета (см. рисунок). Отличие температур (на рисунке не показано) также не превышает 0,2 %. Поэтому можно заключить, что образование столь малого количества AlO не влияет на процесс горения.
2.Для > 0,8 при = 5 мс и изменении E3 в 1000 раз содержание AlO меняется более чем в 10 раз. Для = 0,5–0,8 при
= 10 мс и изменении E3 в 100 раз (от 0,0025 до 0,25) содержание AlO меняется не более чем на 20 %.
3. Полученные количественные оценки содержания AlO впродуктах горения совпадают по порядку величины с результатами работы [3], где приведено относительное содержание субоксида ~10–3 пристехиометрическомсоотношенииметаллаивоздуха.
В таблице представлены результаты расчетов термодинамических параметров реагирующей смеси при для предельных значений E3. Как видно из численных данных, при длительных
73

временах расчета термодинамические параметры смеси совпадают для разных E3. Указанные результаты являются тривиальными с точки зрения анализа термодинамики процессов, но позволяют подтвердить адекватность используемой математической модели и оригинального прикладного программного обеспечения, поскольку полученные значения не зависят от коэффициента испарения и практически сравниваются при достаточно больших .
Термодинамические параметры реагирующей смеси при
|
|
E3 = 0,25 |
|
|
E3 = 0,00025 |
||
Tg |
pAL2O/ p |
pAlO/p |
Tg |
|
pAL2O/ p |
pAlO/p |
|
|
|
||||||
0,3 |
2338 |
0,200 |
10–6 |
2338 |
|
0,200 |
10–6 |
0,5 |
3051 |
0,160 |
0,00008 |
3045 |
|
0,160 |
0,00008 |
0,7 |
3776 |
0,064 |
0,00360 |
3771 |
|
0,068 |
0,00360 |
0,8 |
3808 |
0,052 |
0,00400 |
3809 |
|
0,052 |
0,00400 |
1,0 |
3810 |
0,022 |
0,00320 |
3810 |
|
0,022 |
0,00320 |
1,2 |
3773 |
0,001 |
0,00240 |
3774 |
|
0,001 |
0,00200 |
Таким образом, совокупность полученных результатов имеет теоретическое и прикладное значение, демонстрирует реальную возможность использования математического аппарата и соответствующей компьютерной программы для широкого круга параметрических исследований. Появляется основание для технического исключения переменных, описывающих образование AlO, при проведении расчетов с < 1,2 и добавления вместо них новых данных, которые могут описывать, например, образование нитрида AlN при малых .
Однако следует иметь в виду, что для образования AlO характерна большая неравновесность [2], которая выражается, в частности, в сильной зависимости данного процесса от содержания кислорода в смеси. Количество AlO может достигать больших значений, например, при горении Al в воздухе, обогащенном кислородом. Анализ образования субоксидов в таких условиях является отдельной задачей, требующей дополнительных исследований.
74
Список литературы
1.Крюков А.Ю., Малинин В.И. Расчет содержания субоксидов в продуктах сгорания алюминиево-воздушной смеси по модели неравновесной термодинамики // Вестник Пермского национального исследовательского политехнического университета. Аэрокосмическая техника. – 2016. – № 44. – С. 116–131.
2.Малинин В.И., Коломин Е.И., Антипин И.С. Модель горения высокоскоростного потока аэровзвеси частиц алюминия, учитывающая кинетику процессов и особенности накопления окисла // Химическая физика. – 1998. – Т. 17, № 10. – С. 80–92.
3.Бекстед М.В., Лианг У., Паддуппаккам К.В. Математическое моделирование горения одиночной алюминиевой частицы (обзор) // Физикагоренияивзрыва. – 2005. – Т. 41, №6. – С. 15–33.
УДК 621.791.1
ИССЛЕДОВАНИЕ ФОРМИРОВАНИЯ МИКРОСТРУКТУРЫ СПЛАВА АМГ5 ПРИ СВАРКЕ ТРЕНИЕМ С ПЕРЕМЕШИВАНИЕМ МЕТОДАМИ ФИЗИЧЕСКОГО И МАТЕМАТИЧЕСКОГО МОДЕЛИРОВАНИЯ
А.А. Наумов, Ю.А. Голубев, Е.В. Черников
Санкт-Петербургский политехнический университет Петра Великого, Санкт-Петербург, Россия
anton.naumov@spbstu.ru, golubev_yua@spbstu.ru, evgnchernikov@gmail.com
Приведены результаты исследования формирования микроструктуры сплава АМг5 при сварке трением с перемешиванием с помощью методов физического и математического моделирования. В ходе сварки трением с перемешиванием распределение температуры было измерено при помощи термопар с целью калибровки конечно-элементной модели расчета распределения температуры в пакете ANSYSTM. Для детального анализа влияния температуры на формирование микроструктуры были выбраны 14 точек из разных зон сварного шва. Термоциклы в этих точках были рассчитаны с помощью конечно-элемент- ной модели и воспроизведены на комплексе Gleeble-3800. Микроструктура полученных образцов была сравнена с микроструктурой соответствующих точек в сварном шве.
75
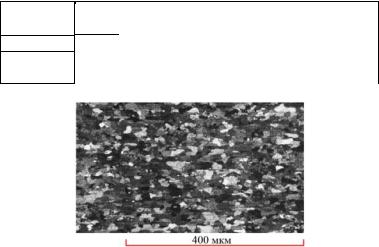
Ключевые слова: сварка трением с перемешиванием, физическое моделирование, математическое моделирование, формирование микроструктуры.
Методом сварки трением с перемешивание (СТП) были получены стыковые соединения из листов сплава АМг5, размеры листов – 400×110×2 мм. Химический состав сплава АМг5 приведен в таблице, исходное состояние листов – М, микроструктура листов в состоянии поставки приведена на рис. 1.
Химический состав сплава АМг5
Стандарт
Фактическая
ГОСТ
4784-97
Концентрация химических элементов, % вес.
Mg |
Si |
Fe |
Cu |
Mn |
Cr |
Zn |
Ti |
4,80 |
0,44 |
0,25 |
0,06 |
0,44 |
0,03 |
0,09 |
0,04 |
4,8–5,8 |
<0,5 |
<0,5 |
<0,1 |
0,3–0,8 |
– |
<0,2 |
0,02–0,1 |
|
|
|
|
|
|
|
|
Рис. 1. Микроструктура листов АМг5 в состоянии поставки
СТП осуществлялась инструментом с диаметром основной части 12 мм, диаметром наконечника 5 мм и длиной 1,8 мм. При СТП постоянными параметрами были осевое усилие – 11 кН, скорость поступательного перемещения инструмента – 250 мм/мин и угол наклона инструмента – 2°; варьировалась скорость вращения инструмента – 700, 850 и 1000 об/мин. В ходе сварки температура на поверхности свариваемых листов измерялась при помощи термопар, схема расположения термопар и результаты измерений представлены на рис. 2 и 3.
76
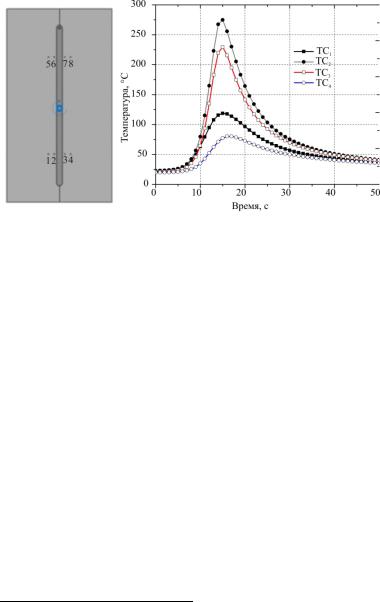
Рис. 2. Схема |
Рис. 3. Результаты измерений термопар |
расположения |
1–4 при СТП, скорости вращения инструмента |
термопар |
700 об/мин |
Данные о температуре с термопар использовались для калибровки конечно-элементной модели расчета распределения температуры в пакете ANSYSTM, разработанной ранее1. По откалиброванной модели были рассчитаны термоциклы в 14 точках сварного шва, схема расположения точек показана на рис. 4. Полученные термоциклы при скорости вращения 700 об/мин для верхних семи точек и нижних семи точек представлены на рис. 5.
Видно, что термоциклы в точках верхнего и нижнего рядов отличаются несущественно, поэтому для дальнейшего физического моделирования с помощью комплекса Gleeble-3800 с целью выявления только температурного влияния на формирование микроструктуры при СТП были выбраны только верхние семь точек. Для этого были изготовлены цилиндрические образцы диаметром 6 мм и длиной 80 мм из листа АМг5, состояние поставки – М, толщина – 8 мм. С использованием данных образцов были реализованы рассчитанные термоциклы (см. рис. 5), после чего был проведен микроструктурный анализ обработанных образцов и сварного шва в выбранных 14 точках.
1 Temperature distribution and welding distortion measurements after FSW of Al 6082-T6 sheets / I.A. Golubev, E.V. Chernikov, A.A. Naumov, V.G. Michailov // TMS Annual Meeting. – 2015. – January. – P. 289–295.
77
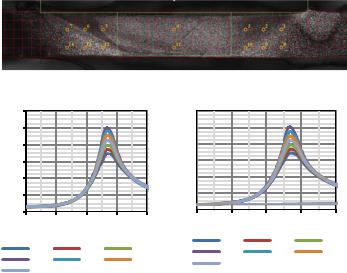
Рис. 4. Схема расположения точек для металлографического анализа
Температура, ºC
600
500
400
300
200
100
0 |
|
|
|
|
|
|
|
|
|
|
|
|
|
|
|
|
|
|
|
20 |
25 |
30 |
35 |
40 |
|||
|
|
|
|
|
|
||||||||
20 |
25 |
30 |
35 |
40 |
|||||||||
|
|
Время, с |
|
|
|
|
|
P8 |
|
P9 |
P10 |
||
|
P1 |
|
P2 |
|
P3 |
|
|
|
|||||
|
|
|
|
|
P11 |
|
P12 |
P13 |
|||||
|
P4 |
|
P5 |
|
P6 |
|
|
P14 |
|
|
|
|
|
|
P7 |
|
|
|
|
|
|
|
|
|
|
|
|
|
|
|
|
|
|
|
|
|
б |
|
|
|
|
|
|
|
а |
|
|
|
|
|
|
|
|
|
Рис. 5. Рассчитанные термоциклы при СТП со скоростью вращения инструмента 700 об/мин: а – для верхнего ряда точек (расстояние от верхней поверхности 0,8 мм); б – для нижнего ряда точек (расстояние от нижней поверхности 0,4 мм)
Как и ожидалось, при анализе микроструктуры в выбранных точках шва было выявлено, что минимальный размер зерна соответствует ядру шва или зоне перемешивания, зоны термомеханического влияния имеют более крупный размер зерна и оно не равноосное, в зоне термического влияния зерно еще более крупное и более равноосное, чем в зоне термомеханического влияния. Анализ микроструктуры образцов после физического моделирования показал, что размер зерна не изменяется после термического воздействия ни в одном из реализованных режимов, соответствующих термоциклам в семи точках верхнего ряда. Это свидетельствует о том, что только температурное воздействие без деформационного не оказывает никакого влияния на размер зерна. Это связано с тем, что период времени, когда материал находится при повышенных температурах, слишком мал для протекания процесса роста зерна. Период времени нахождения материала при температуре выше 200 °С составляет около 10 с (см. рис. 5).
78
Таким образом, основным фактором для формирования микроструктуры шва при СТП является деформация при повышенных температурах.
УДК 621.99
ВЛИЯНИЕ ПЕРЕДНЕГО УГЛА НА УСАДКУ СТРУЖКИ ПРИ ТОЧЕНИИ ВЫСОКОПРОЧНЫХ СТАЛЕЙ
А.С. Ямников1, А.О. Чуприков2, А.И. Харьков1
1 Тульский государственный университет,
2 Тульский оружейный завод, Тула, Россия yamnikovas@mail.ru, artemline@rambler.ru, AlexandrHar@mail.ru
Рассмотрен вопрос определения деформации срезаемого слоя металла при токарной обработке высокопрочных заготовок. Отмечено, что параметры деформации срезаемого слоя металла имеют большое значение для расчета составляющих силы резания. Приведены формулы нескольких авторов для расчета составляющих силы резания и показано, что все они имеют составляющую, характеризующую деформацию срезаемого слоя металла, которую требуется определять экспериментально. Приведены результаты определения утолщения стружки при точении закаленных высокопрочных сталей с положительными, нулевыми и отрицательными передними углами.
Ключевые слова: усадка стружки, высокопрочная сталь, передний угол резца, сила резания.
В настоящее время с развитием технологий обработки металлов резанием и появлением новых режущих инструментов из высокостойких сплавов до сих пор остаются сложности в обработке закаленных заготовках из-за невысокой стойкости резцов. Низкая стойкость обычно ведет к нестабильному получению качества обрабатываемых деталей, в том числе неисправимому браку, что негативно сказывается на экономических показателях предприятия.
Так, при получении упорной резьбы в закаленном корпусе ракеты режущий инструмент, в нашем случае резец, имеет низ-
79
кую стойкость, примерно на 2–3 детали. На стойкость инструмента влияет множество параметров, такие как скорость резания, обрабатываемый материал, материал резца, глубина резания, подача, геометрия резца, охлаждение резца, жесткость станка, приспособления, вспомогательная оснастка, заготовки [1].
Определение силы резания путем расчета явилось одной из первых задач конца XIX и всего XX в., которую пыталась решить наука о резании металлов [2–11]. Обобщенные итоги исследований были подведены в книге [12], посвященной 50-летию советской власти в СССР.
Для установления влияния переднего угла резца на коэффициент усадки стружки необходимо выделить основные параметры режущего инструмента – это геометрия резца и его материал. Остальные параметры, влияющие на процесс резания, можно варьировать во время обработки без подробных исследований [13]. Вопросы определения усадки стружки при точении высокопрочных сталей рассматривались при исследовании результатов обработки закаленной стали. Исходными данными при проведении таких экспериментов послужила сталь с твердостью по Бринеллю HB, равная 217 МПа, предел кратковременной прочности
в = 1080 МПа.
При проведении исследований по влиянию переднего угла γ на усадку стружки были выбраны постоянными следующие исходные данные: скорость резания, подача на оборот, глубина резания. Для экспериментов отобрали три резца с разными передними углами: отрицательный передний угол, равный –5°, нулевой передний угол и положительный передний угол, равный +5°. Параметры режима обработки: скорость резания V = 250 м/мин; подача S = 0,32 мм/об; глубина резания t = 0,5 мм; СОЖ не использовалась.
Как известно, коэффициент усадки стружки – это отношение длин стружки: длины пути, пройденного резцом, к длине срезаемого слоя стружки. Процесс измерения длины стружки трудоемок, так как в некоторых случаях она бывает ломкая, что делает невозможным ее дальнейшее измерение. По итогам эксперимента стружку отсортировали по трем группам для каждого из экспериментов (рисунок). При этом видно, что различие между группами обусловливается целостностью отрезка стружки.
80