
Аэрокосмическая техника высокие технологии и инновации – 2016
..pdf
погрешности исполнительного привода. Пакет Simulink позволяет синтезировать оптимальное и адаптивное управление, реализовывать системы стабилизации частоты вращения, производить настройку регуляторов и т.д.
Рис. Визуализация поворотного стола в Simulink с помощью stl-файлов
Регулирование частоты вращения двигателя осуществляется с помощью PID-регулятора [2], настройка которого происходит в автоматическом режиме в Matlab (Simulink) в соответствии с требованиями технологического процесса и параметрами качества регулирования. При этом блок регулятора устанавливается в полученную динамическую модель.
Для рассматриваемого стола получены следующие настраи-
вающие коэффициенты: P |
– пропорциональный, P = 0,014; |
||||
D – дифференциальный, D = 0,165; I – интегрирующий, I = 0,0001. |
|||||
Р I |
1 |
D |
|
N |
. |
s |
|
1 |
|||
|
|
|
|
||
|
|
1 |
N s |
|
Схема предполагает настройку регуляторов в зависимости от текущей частоты вращающегося стола.
Показатели качества переходного процесса: время регулирования – 0,01 с, перерегулирование – 10 %.
Погрешности позиционирования составляют:
–0,0015 радиан на регуляторе;
–0,00157 радиан на роторе;
171
– 0,00180 радиан на планшайбе.
Все вышесказанное позволяет заключить, что пакет Matlab расширяет возможности САПР SolidWorks в части динамического моделирования 3D-моделей механизмов, что позволяет моделировать механизмы, состоящие из множества твердых тел и их компонентов – соединений, ограничителей движения, управляющих элементов и датчиков движения. Такой комплексный подход к исследованию динамических и статических характеристик упрощает анализ сложных конструкций, сокращает процесс проектирования и затраты на проектирование.
Список литературы
1.Гультяев А. Визуальное моделирование в среде Matlab: учеб. курс. – СПб.: Питер, 2000. – 432 с.
2.Лазарев Ю. Моделирование процессов и систем в
Matlab. – СПб.: Питер, 2005. – 512 с.
УДК 621.9:658 (0,7)
ДИАГНОСТИКА ТЕХНИЧЕСКОГО СОСТОЯНИЯ ШПИНДЕЛЬНОГО УЗЛА МЕХАТРОННЫХ СТАНКОВ С ИСПОЛЬЗОВАНИЕМ ИСКУССТВЕННЫХ НЕЙРОННЫХ СЕТЕЙ
Н.С. Устинов, Ю.В. Идрисова, С.И. Фецак
Уфимский государственный авиационный технический университет, Уфа, Россия
ustinov2113@rambler.ru
Диагностика оборудования в автоматическом режиме, без простоев и в режиме реального времени является актуальной производственной задачей. Выявление диагностических признаков оборудования и сопоставление их параметров с возможным техническим состоянием оборудования можно отнести к задачам распознавания образов. Алгоритм диагностирования, созданный на базе искусственных нейронных сетей, является эффективным решением поставленных задач.
Ключевые слова: амплитудно-частотный спектр, диагностические признаки, нейронная сеть.
172
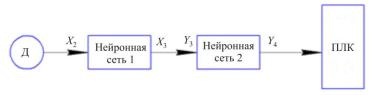
Технической диагностикой оборудования называется обследование технического устройства, эксплуатируемого на опасном производственном объекте или являющегося им, с целью определения его состояния, а именно: наличия дефектов и повреждений; степени износа; правильности функционирования и др. [1].
Целью данной работы является создание математической модели источника колебания, а именно погрешности изготовления и сборки подшипников качения шпиндельного узла.
Математическую модель указанного источника колебания представляют в виде амплитудно-частотных спектров разложения в ряд Фурье выражений возмущающих сил [2].
По расчетным спектрам вибровозмущений были получены эталонные значения частоты, Гц, и амплитуды, Н, возможных неисправностей модуля главного движения, а также случайным образом были выбраны значения частот и амплитуды для нештатной ситуации (резкое возрастание оборотов – плавление сепаратора, повреждение колец подшипника, повреждение шариков, увеличение температуры масла, повреждение шейки валов, приложение силы резания).
Структурная схема системы диагностики мехатронных станков с применением искусственных нейронных сетей показана на рисунке.
Рис. Структурная схема диагностируемой системы
На вход первой нейронной сети приходит спектр частот (X2), получаемый с датчика, расположенного на валу шпиндельмотора. Данная сеть обучается по принципу многослойного персептрона (MLP), т.е. сети прямого распространения, в которой каждый нейрон текущего слоя связан со всеми нейронами предыдущего. На выходе сети получаем спектр частот X3, который сравнивается с целевым спектром, заданным уже в самой сети,
173
затем параметры сети корректируются таким образом, чтобы сократить различие между фактическим и желаемым выходом сети.
Каждому спектру частот соответствует свой спектр амплитуд, и тем самым на вход второй нейронной сети приходит спектр амплитуд Y3. Вторая нейронная сеть обучается по амплитуде и работает аналогично первой сети. На выходе этой сети получаем амплитуды Y4, которые являются входным сигналом для логического контроллера.
ПЛК – программируемый логический контроллер, представляет собой микропроцессорное устройство, предназначенное для сбора, преобразования, обработки, хранения информации и выработки команд управления, имеющий конечное количество входов и выходов.
Вданном случае контроллер необходим для принятия решения о том, что оборудование:
– работоспособное;
– неработоспособное;
– работоспособное, но неисправное;
– работоспособное и исправное.
Моделирование нейронных сетей было выполнено в про-
граммном пакете Statistica 8.0 [3, 4].
Врезультате моделирования искусственных нейронных сетей были получены диаграммы рассеивания, которые показывают, насколько наши наблюдения примыкают к линии точности сети, а также была получена средняя относительная ошибка обучения сети, которая составляет 1 %.
Данная система на основе математических моделей источника колебания позволяет производить оперативную диагностику
врежиме реального времени, что дает возможность контролировать работу модулей станка.
Список литературы
1.Вибродиагностика приводов металлообрабатывающих станков с применением искусственных нейронных сетей / М.С. Басманов, А.С. Басманов, Ю.В. Идрисова, С.И. Фецак // Молодежный вестник УГАТУ. – 2012. – 198.
2.Идрисова Ю.В., Кудояров Р.Г., Фецак С.И. Диагностика
приводов металлообрабатывающих станков с автоматическим управлением: учеб. пособие / УГАТУ – Уфа, 2013. – 153 с.
174
3.Боровиков В.П. Нейронные сети. Statistica Neural Networks / Горячая Линия – Телеком, 2008. – 392.
4.Боровиков В.П. Statistica. Искусство анализа данных на компьютере: для профессионалов. – 2-е изд. – СПб.: Питер, 2003. – 688 с.
УДК 621.78.011
РАСЧЕТ ДЕФОРМАЦИЙ ЗУБЧАТОГО КОЛЕСА ПРИ ТЕРМООБРАБОТКЕ
Н.С. Подкина1, Е.В. Кузнецова1, Д.Н. Токаев2, А.С. Горбунов2
1 Пермский национальный исследовательский политехнический университет, 2 Редуктор-ПМ, Пермь, Россия
mellen75@mail.ru
Проведен анализ расчета деформаций заготовки спиральноконического зубчатого колеса промежуточного редуктора вертолета МИ-28Н в процессе термообработки. Предложена геометрия заготовки перед операцией термообработки с целью получения максимально приближенной геометрии к конструкторской документации после термообработки с целью улучшения показателей ремонтопригодности, надежности деталей, также снизить потерю металла, а значит повысить экономичность изготовления деталей, что является актуальными задачами машиностроения. Построены кривые распределения отклонений размеров, предложен метод компенсации деформации после термообработки.
Ключевые слова: деформация, зубчатое колесо, термообработка, ремонтопригодность, надежность, отклонения от геометрических размеров, коробление, компенсация деформаций.
Термообработка спирально-конического колеса. Спирально-
коническое зубчатое колесо выполнено из конструкционной легированной стали марки 12Х2Н4А-Ш. Такую сталь используют в промышленности для изготовления зубчатых колес, валов, роликов, поршневых пальцев и других крупных особо ответственных
175
цементуемых деталей, к которым предъявляются требования высокой прочности, пластичности и вязкости сердцевины и поверхностной твердости, работающие под действием ударных нагрузок или при отрицательных температурах до –120 °С [1].
Термообработку спирально-конического колеса условно можно разделить на три этапа. На первом этапе проводится предварительная закалка при температуре 870 °С с отпуском при температуре 500 °С. Затем заготовка отправляется на меднение, целью которого является защита нецементируемых поверхностей детали. После деталь отправляется на цементацию при температуре 870 °С с отпуском при 650 °С. Перед третьим этапом деталь размедняют и отправляют на закалку при температуре 830 °С с последующей обработкой холодом и отпуском [2].
При термообработке происходит деформация деталей, которая заключается в изменении их геометрической формы и размеров. Такая деформация может возникать как при нагреве, так и при охлаждении в процессе [3]. Деформация при охлаждении вызывается двумя причинами: во-первых, термическими напряжениями и, во-вторых, структурными превращениями (рисунок) [4].
В отделе технического контроля на предприятии АО «Ре- дуктор-ПМ» после термообработки (цементации и закалки) были произведены замеры интересующих нас размеров на контрольноизмерительной машине и вручную. По результатам замеров было выявлено отклонение длин от заданных технологической документацией.
Проведен анализ отклонений измеренных величин от требований технологической документации. На рисунке показаны эмпирические кривые распределения результатов измерений в зависимости от частоты появления количественного результата в ходе измерений.
Как видно из рис., а отклонения монтажного размера от расчетного распределены по нормальному закону, где средним отклонением с самой высокой частотой является отклонение ≈1,57 мм. На рис., б видно, что отклонения внутренней длины составляют ≈1,68 мм.
Исходя из полученных данных, становится очевидным, что при термообработке спирально-конического колеса уменьшается внутренний размер а совместно с монтажным размером б. То есть
176
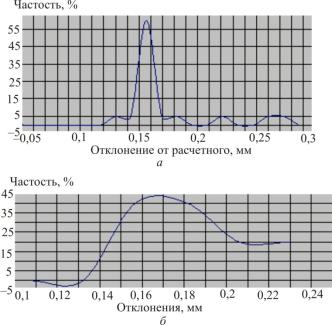
происходит «раскрытие» зубчатого венца, уменьшается угол конуса конического зубчатого колеса.
Рис. Эмпирические кривые распределения результатов: а – монтажная длина; б – внутренняя длина
Для компенсации коробления зубчатых колес при закалке применяются следующие меры:
–специальные способы закалки (прерывистая, ступенчатая, изотермическая и др.);
–специальные закалочные прессы.
Наиболее экономически целесообразным является направленное изменение геометрических размеров заготовки зубчатого колеса перед термообработкой с учетом последующих деформаций детали при термообработке. Таким образом, деформацию детали или отклонения размеров, получаемых при термообработке, учитывают в геометрии заготовки до этапа термообработки для «упреждения» при последующей деформации во время термической обработки [5].
177
Список литературы
1.Александров В.Г., Справочник по авиационным материалам. – Транспорт, 1972. –328 с.
2.Производство зубчатых колес / А.С. Калашников, С.Н. Калашников, Г.И. Коган [и др.]; под общ. ред. Б.А. Тайца. – 3-е изд., перераб. и доп. – М.: Машиностроение, 1990. – 464 с.
3.Першин В.П. Методические указания к лабораторной работе цементация / ФАО ТГАСУ ЛИ. – Томск, 2008. – 14 с.
4.Решетилов Д.Н. Детали машин. – М.: Машиностроение, 1974. – 656 с.
5.Томсен Э., Янг Ч., Кобаяши Ш. Механика пластических деформаций при обработке металлов. – М.: Машиностроение, 1968. –504 с.
УДК 629.7.036.22.001(075.8)
ОПРЕДЕЛЕНИЕ ОБЛАСТИ РАБОЧИХ ПАРАМЕТРОВ КОМБИНИРОВАННОГО ПРЯМОТОЧНОГО ВОЗДУШНОРЕАКТИВНОГО ДВИГАТЕЛЯ НА ПОРОШКООБРАЗНОМ АЛЮМИНИЕВОМ ГОРЮЧЕМ
В.И. Малинин, Я.Э. Богомолов
Пермский национальный исследовательский политехнический университет, Пермь, Россия
bogomolov200@yandex.ru
Рассматривается комбинированный прямоточный воздушнореактивный двигатель (ПВРД) на порошкообразном алюминиевом горючем (ПАГ). Прототипом послужил комбинированный ракетно-прямоточный двигатель на твердом топливе. Определены области рабочих значений параметров ПВРД на ПАГ, тяговооруженность и проведено сравнение ее с прототипом для базовой траектории полета, равной 0,5 км.
Ключевые слова: комбинированный ракетно-прямоточный двигатель на твердом топливе, прямоточный воздушнореактивный двигатель на порошкообразном алюминиевом горючем, летательныйаппарат, областьзначенийрабочихпараметров.
178
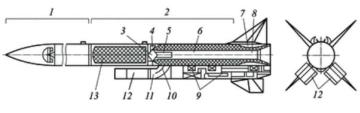
Впоследнее время уделяется особое внимание двигательным установкам, энергетические возможности которых могут быть улучшены за счет использования воздуха в качестве окислителя. Также большое значение имеет изменение тяги двигательной установки в широком диапазоне значений, отвечающее современным требованиям, предъявляемым к управляемым летательным аппаратам.
Вданной работе рассматривается комбинированный прямоточный воздушно-реактивный двигатель (КПВРД) на порошкообразном алюминиевом горючем (ПАГ). Прототипом комбинированной двигательной установки послужил комбинированный ракетно-прямоточный двигатель на твердом топливе (КРПДТ) летательного аппарата «Метеор» класса «воздух-воздух» [1]. Комбинированный РПДТ включает в себя следующие элементы конструкции (рис. 1): модуль носовой части 1, двигательный отсек 2, узел регулирования расхода продуктов сгорания газогенератора (ГГ) 3, воспламенитель 4, бессопловой стартоворазгонный двигатель 6, маршевое сопло 7, стартовое сопло 8, агрегаты управления в гаргротах за воздухозаборным устройством (ВЗУ) 9, заглушки ВЗУ на стартовом режиме 10, переходный канал 11, ВЗУ 12, твердотопливный ГГ 13.
Рис. 1. Схема летательного аппарата с КРПДТ
За основу КПВРД на ПАГ (рис. 2) принимается конструкция КРПДТ, однако вместо ГГ устанавливается система подачи горючего 13 и в камере дожигания выделяется форкамера для воспламене- нияипервичногогоренияалюминиево-воздушнойсмеси[2].
Задачами работы является определение термодинамических параметров и области работы ПВРД на ПАГ. Расчеты проведены в программе Astra 4 [3]. Исходные данные для расчета: коэффициент избытка окислителя α = 1–7; базовые траектории полета
179

летательного аппарата – 0,5; 10; 18 км, атмосфера стандартная; число Маха – 2; 2,5; 3; 4. Проходные значения сечений потока: площади захвата ВЗУ, критического сечения и среза сопла приняты такими же, как и для летательного аппарата «Метеор». ВЗУ является нерегулируемым [1].
Рис. 2. Схема летательного аппарата с КПВРД на ПАГ
Рис. 3. Область рабочих параметров ПВРД на ПАГ: 1 – ограничения по предельно допустимым давлениям
в камере сгорания; 2 – ограничения по максимальному расходу ПАГ; 3 – ограничение по минимальному значению тяги двигателя
На первом этапе определялись термодинамические параметры и область работы на высоте 0,5 км. Находили энтальпию, температуру и давление торможения, значения коэффициентов расхода и восстановления полного давления в ВЗУ [1] и соот-
180