
учебник по ОПОВ
.pdf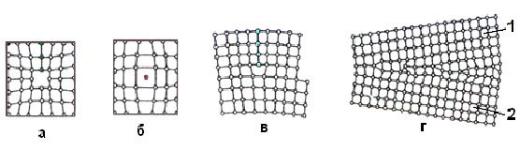
имеет решетку ОЦК, в интервале 911°С…1392°С железо имеет решетку ГЦК. Способность менять тип решетки в зависимости от температуры называется
аллотропией или полиморфизмом.
В кристаллах всегда имеются дефекты (несовершенства) строения, обусловленные нарушением правильного расположения атомов кристаллической решетки. Дефекты кристаллического строения подразделяют по геометрическим признакам на точечные, линейные и поверхностные.
Атомы совершают колебательные движения возле узлов решетки, а с повышением температуры амплитуда этих колебаний увеличивается.
Наиболее легко перемещаются атомы поверхностного слоя, выходя на поверхность. Место, где находится такой атом, называется вакансией.
Кточечным дефектам относят также
атом, внедренный в междоузлие кристаллической решетки (рис. 1.1.3., а),
замещенный атом, когда место атома одного металла замещается в кристаллической решетке другим, чужеродным атомом (рис. 1.1.3, б).
Линейные дефекты - несовершенства кристаллической решетки, при которой сдвиг на одно межатомное расстояние одной части решетки относительно другой приводит к тому, что число рядов атомов в верхней части решетки на один больше, чем в нижней. Этот дефект называют линейной дислокацией (рис. 1.1.3,
в).
Из-за дислокаций реальная прочность железа примерно в 70 раз ниже теоретической.
Поверхностные дефекты представляют собой границы раздела между отдельными кристаллами (рис. 1.1.3, г). На границе раздела атомы расположены менее правильно, чем в его объеме.
Рис.1.1.3. Дефекты в кристаллах: а – вакнсия; б – внедренный атом; в – линейная дислокация; г – поверхностный дефект на границе 1 и 2 кристаллов
Кристаллизация – переход из жидкого состояния в твердое. Каждый чистый металл кристаллизуется при строго индивидуальной температуре.
Процесс кристаллизации состоит из двух стадий:
10
зарождение кристаллов;
рост кристаллов из этих центров.
Сначала образовавшиеся кристаллы растут свободно и имеют правильную форму. Затем при соприкосновении растущих кристаллов их правильная форма нарушается. Рост кристалла продолжается только в тех направлениях, где есть свободный доступ жидкого металла. В результате после затвердевания кристаллы получают неправильную форму и их называют кристаллитами или зернами.
Величина зерен зависит от
числа центров кристаллизации (чем их больше, тем мельче зерно);
скорости роста кристаллов (чем выше скорость охлаждения, тем мельче зерно).
Чтобы получить мелкое зерно, в расплавленный металл вводят специальные вещества: модификаторы (для стали это алюминий, титан, ванадий).
1.1.3 Основные сведения о сплавах
Чистые металлы характеризуются низким пределом прочности, поэтому в машиностроении применяют главным образом их сплавы. Например, мягкая медь с добавлением олова превращается в более твердую бронзу.
Металлическим сплавом называют сложное вещество, полученное сплавлением (или спеканием) нескольких металлов или металлов с неметаллами.
Компонентами называют вещества, образующие сплав. Чистый металл представляет собой однокомпонентную систему, сплав двух металлов – двухкомпонентную систему. Получение сплава не всегда возможно. Например, железо со свинцом не образуют сплава, так как в жидком виде они не дают раствора. Обязательное условие для образования сплава – получение однородного жидкого раствора соединившихся компонентов.
При затвердевании жидкого раствора в сплавах получаются три типа соединений:
жидкое состояние;
твердый раствор;
химическое соединение;
механическая смесь.
Однородные жидкие растворы характерны почти для всех металлов, растворяющихся друг в друге в жидком состоянии в любых соотношениях (Рис.
1.1.4, а).
11

Рис.1.1.4. Компоненты в сплавах: а – жидкое состояние; б – твердый раствор; в – химическое соединение; г – механическая смесь
Твердые растворы образуются в результате перехода в твердое состояние однородных жидких растворов (Рис. 1.1.4, б). В твердом растворе одно из веществ, входящих в состав сплава, сохраняет кристаллическую решетку, а другое в виде отдельных атомов распределяется в кристаллической решетке первого вещества. Твердые растворы бывают двух типов: твердые растворы замещения и твердые растворы внедрения.
Втвердых растворах замещения часть атомов в кристаллической решетке одного из компонентов замещены атомами другого.
Втвердых растворах внедрения атомы растворенного компонента внедряются в межатомное пространство кристаллической решетки другого компонента.
Химические соединения образуются при сплавлении различных металлов или металла с неметаллом (Рис. 1.1.4, в).
Химическое соединение – однородное кристаллическое тело, имеет кристаллическую решетку, которая отлична от решеток элементов, образующих это соединение.
Механическая смесь двух компонентов образуется тогда, когда при кристаллизации компоненты сплава не способны к взаимному растворению в твердом состоянии (Рис. 1.1.4, г).
1.1.4 Свойства металлов и сплавов
Чтобы судить о том, насколько различные металлы и сплавы пригодны для изготовления деталей оборудования, необходимо знать, какими свойствами металлы и сплавы обладают и отвечают ли эти свойства требованиям, предъявляемым к готовым изделиям. Качество металлических изделий во многом определяется физическими, химическими, механическими, а также технологическими и эксплуатационными свойствами материалов, из которых они изготовлены.
Кфизическим свойствам металлов относятся
цвет;
плотность;
температура плавления;
теплопроводность;
12
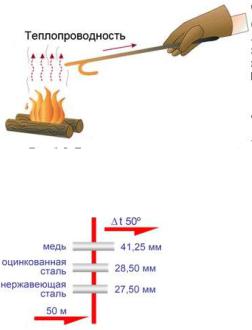
тепловое расширение;
теплоемкость;
электропроводность;
магнитные свойства и др.
Плотность (кг/м³) металла или сплава характеризуется его массой, заключенной в единице объема.
Легкие металлы и сплавы имеют плотность около 4500 кг/м³ и менее (алюминиевые, магниевые, титановые сплавы): алюминий – 2700 кг/м³, магний –
1700 кг/м³, титан – 4505 кг/м³.
Тяжелые металлы - железо (7800 кг/м³), вольфрам (19300 кг/м³), свинец (11400
кг/м³).
Плавкостью называется способность металлов расплавляться, то есть при нагревании переходить в жидкое состояние.
Температурой плавления (°C) называют температуру, при которой металл переходит из твердого состояния в жидкое.
По температуре плавления различают
тугоплавкие металлы (вольфрам→ 3416°C, тантал→ 2950°C, титан→
1725°C);
легкоплавкие металлы (олово→232°C, свинец→327°C, цинк→419,5°C, алюминий→660°C).
Температура плавления важна при выборе металлов для изготовления литых изделий, сварных и паяных соединений, термоэлектрических приборов.
Теплопроводность (Вт/(м·K)) - это
способность металлов передавать тепло от более нагретых к менее нагретым участкам тела (Рис. 1.1.5). Серебро, медь, алюминий обладают большой теплопроводностью. Железо имеет теплопроводность примерно в 3 раза меньше, чем алюминий и в 4 раз меньше, чем медь.
Рис. 1.1.5. Теплопроводность металлов.
Тепловым расширением (К-1) называют способность металлов увеличиваться в размерах при нагревании и уменьшаться при охлаждении. На рис. 1.1.6 показано тепловое расширение одинаковых труб из различных материалов длиной 50 м при нагреве на 50 градусов.
Рис.1.1.6. Тепловое расширение материалов.
13

Теплоемкостью (Дж/К) называют способность металла при нагревании поглощать определенное количество тепла. Удельной теплоёмкостью называется количество теплоты, которое необходимо для нагревания единичного количества вещества. Количество вещества может быть измерено в килограммах, кубических метрах и молях. В зависимости от того, к какой количественной единице относится теплоёмкость, различают массовую, объёмную и мольную теплоёмкости.
Например, удельная теплоемкость воды равняется 4,2 кДж/(кг•К). Это значит, что для того, чтобы нагреть один килограмм воды на один градус, необходимо передать этому килограмму воды 4,2 кДж энергии.
У подавляющего большинства материалов удельная теплоемкость порядка 1 кДж/(кг·К): таблица 1.1.1. Теплоемкость зависит от температуры. Вблизи нуля Кельвина она мала, в рабочем диапазоне температур - слабо меняется с ростом температуры.
Таблица 1.1.1. Теплопроводность и удельная теплоемкость различных материалов
|
Материал |
|
|
Теплопроводность, |
|
|
Удельная теплоёмкость, |
|
|
|
|
||||||
|
|
|
Вт/(м·K) |
|
|
кДж/(кг·К) |
|
|
|
|
|
|
|
|
|
||
|
|
|
|
|
|
|||
|
Медь |
|
|
382—390 |
|
|
0,385 |
|
|
|
|
|
|
|
|||
|
|
|
|
|
|
|||
|
Алюминий |
|
|
202—236 |
|
|
0,930 |
|
|
|
|
|
|
||||
|
Железо |
|
|
92 |
|
|
0,444 |
|
|
|
|
|
|
|
|||
|
|
|
|
|
||||
|
|
|
|
|
||||
|
Сталь |
|
|
47 |
|
|
0,47 |
|
|
|
|
|
|
|
|||
|
|
|
|
|
|
|||
|
Стекло |
|
|
1 |
|
|
0,67—0,84 |
|
|
|
|
|
|
|
|
||
|
|
|
|
|
|
|
||
|
Кирпич строительный |
|
|
0,2—0,7 |
|
|
0,84—1 |
|
|
|
|
|
|
|
|||
|
|
|
|
|
|
|||
|
Воздух (сухой неподвижный) |
|
|
0,024—0,031 |
|
|
1,005 |
|
|
|
|
|
|
|
|
|
|
Химические свойства характеризуют способность металлов и сплавов сопротивляться окислению или вступать в соединение с различными веществами: кислородом воздуха, растворами кислот, щелочей и др. Чем легче металл вступает в соединение с другими элементами, тем быстрее он разрушается.
Химическое разрушение металлов под действием на их поверхность внешней агрессивной среды называют коррозией
(рис. 1.1.7).
Рис. 1.1.7. Коррозионное разрушение трубы.
Когда на металлический образец действует сила или система сил, он реагирует на это, изменяя свою форму (деформируется). Способность металла сопротивляться воздействию внешних сил характеризуется механическими свойствами. Поэтому
14

при выборе материала для изготовления деталей машин учитывают его
механические свойства:
прочность;
упругость;
пластичность;
ударную вязкость;
твердость и др.
Эти свойства определяют по результатам механических испытаний, при которых металлы подвергают воздействию внешних сил (нагрузок).
Напряжение (механическое) – величина нагрузки, отнесенная к единице площади поперечного сечения испытуемого образца. Измеряется в Н/м2 (Па).
Деформация – изменение формы и размеров твердого тела под влиянием приложенных внешних сил.
Для определения прочности, упругости и пластичности металлы в виде образцов круглой или плоской формы испытывают на растяжение. Испытание проводят на разрывных машинах. В результате испытаний получают диаграмму растяжений (Рис. 1.1.8). По оси абсцисс этой диаграммы откладывают значения деформации, а по оси ординат – нагрузки, приложенные к образцу (возникшие механические напряжения). На диаграмме голубая часть соответствует упругим деформациям, при которых после снятия нагрузки образец получает исходную форму и размеры. Желтая часть диаграммы - область пластических
деформаций.
Рис.1.1.8. Диаграмма растяжения.
Прочность – способность материала сопротивляться разрушению под действием нагрузок, оценивается
пределом прочности;
пределом текучести.
Предел прочности σВ – это напряжение в МПа, соответствующее наибольшей нагрузке, предшествующей разрушению образца (на Рис. 1.1.8. точка В):
B |
|
Pmax |
(1.1.1.) |
|
F0 |
||||
|
|
|
где Pmax – наибольшая нагрузка, Н; F0 – начальная площадь поперечного сечения рабочей части образца, м2.
15
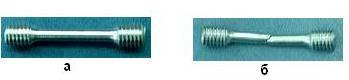
Предел текучести σT – это наименьшее напряжение (в МПа), при котором образец деформируется без заметного увеличения нагрузки (на Рис. 1.1.8. точка А):
|
|
|
P´T |
(1.1.2) |
|
T |
F0 |
||||
|
|
|
|||
|
|
|
|
где Pт – нагрузка, при которой на диаграмме растяжения наблюдается площадка текучести (площадка А…А'), Н.
Упругость – способность материала восстанавливать первоначальную форму и размеры после прекращения действия нагрузки.
Некоторые металлические конструкции намеренно проектируют так, чтобы они упруго деформировались. Так, от пружин обычно требуется довольно большая упругость. В других случаях упругую деформацию сводят к минимуму. Балки, детали механизмов и приборов делают по возможности более жесткими.
Пластичность – это способность материала принимать новую форму и размеры под действием внешних сил без разрушения. Пластичность можно оценить относительным удлинением.
Относительное удлинение (после разрыва) δ – это отношение приращения ɭ расчетной длины образца после разрыва к его первоначальной длине ɭ, выраженное в процентах (Рис. 1.1.9.):
|
l |
100% |
(1.1.3) |
|
l |
|
|
Рис.1.1.9 Образец до (а) и после (б) испытания
Относительное сужение (после разрыва) Ψ – это отношение уменьшения площади поперечного сечения образца в месте разрыва F к начальной площади F поперечного сечения, выраженное в процентах:
|
F |
100% |
(1.1.4) |
|
F |
|
|
Наличие металлической связи придает металлу способность к пластической деформации и к самоупрочнению в результате пластической деформации. Поэтому если внутри материала есть дефект или имеются концентраторы напряжений, то в этих местах напряжения достигают большой величины и даже может возникнуть трещина. Но так как пластичность металла высока, то в таком месте, в том числе в устье трещины, металл пластически деформируется, упрочняется, и процесс разрушения приостанавливается.
16

У неметаллов этого не наблюдается – когда напряжения превзойдут некоторую величину, произойдет разрушение.
Ударная вязкость – это способность материала сопротивляться динамическим нагрузкам (ударам). Определяется как отношение затраченной на излом образца работы W (в МДж) к площади его поперечного сечения F (в м2) в месте надреза (рис. 1.1.10):
KC |
W |
, МДж/м2 |
(1.1.5) |
|
F |
||||
|
|
|
Рис.1.1.10. Испытание на ударную вязкость
Твердостью называют способность материала сопротивляться проникновению в него другого, более твердого тела. На рис. 1.1.11. показано оборудование, предназначенное для разрыхления материалов. Винтышнеки должны обладать высокой твердостью.
Твердость металла определяют способами Бринелля, Роквелла и Виккерса.
Рис.1.1.11.Оборудование для разрыхления материалов
Способ Бринелля (Рис. 1.1.12, а) основан на том, что в плоскую поверхность металла вдавливают под постоянной нагрузкой стальной закаленный шарик диаметром D. Диаметр шарика и величину нагрузки Р устанавливают в зависимости от твердости и толщины испытываемого металла. Груз опускается и вдавливает шарик в испытываемый образец. На поверхности металла образуется отпечаток - лунка диаметром d. Чем больше отпечаток, тем металл мягче. Пример обозначения твердости по Бринеллю: НВ 300.
Способом Бринелля не рекомендуется измерять твердость материалов с НВ>450, например, закаленной стали, так как при измерении шарик деформируется и показания искажаются.
Рис.1.1.12 Схемы определения твердости: а - по Бринеллю; б – по Роквеллу; в – по Виккерсу.
17
Для испытания твердых материалов применяют способ Роквелла (Рис. 1.1.12, б). В образец вдавливают алмазный конус с углом при вершине 120° или стальной закаленный шарик диаметром 1,59 мм. Твердость по Роквеллу измеряется в условных единицах. Значение твердости определяют по глубине отпечатка h и отсчитывают по циферблату индикатора, установленному на приборе. При испытании металлов с высокой твердостью применяют алмазный конус и общую нагрузку Р=Р0+Р1=1500 Н. Твердость отсчитывают по шкале «С» и обозначают HRC. Если при испытании берется стальной шарик и общая нагрузка 1000 Н, то твердость отсчитывается по шкале «В» и обозначается HRB. При испытании очень твердых или тонких изделий используют алмазный конус и общую нагрузку 600 Н. Твердость отсчитывается по шкале «А» и обозначается HRA.
Пример обозначения твердости по Роквеллу HRC 50: твердость 50 по шкале «С».
При определении твердости способом Виккерса (Рис. 1.1.12, в) в качестве вдавливаемого в материал наконечника используют четырехгранную алмазную пирамиду с углом при вершине 136°. Пример обозначения твердости по Виккерсу:
HV 500.
Технологические свойства характеризуют способность металлов подвергаться обработке в холодном и горячем состоянии.
Косновным технологическим свойствам относятся:
обрабатываемость резанием;
свариваемость;
ковкость;
литейные свойства и др.
Обрабатываемость резанием – одно из важнейших технологических свойств, потому что подавляющее большинство заготовок, а также деталей сварных узлов и конструкций подвергается механической обработке (точению, сверлению, фрезерованию, шлифованию). Одни металлы обрабатываются хорошо до получения чистой и гладкой поверхности, другие, имеющие высокую твердость, плохо.
Заготовками для многих деталей являются прутки (продукция прокатного производства). Кроме того, заготовки получают путем отливки, ковки, штамповки. В процессе обработки резанием с заготовки снимается часть металла, переходящая при этом в стружку; эта часть называется припуском.
Снятие стружки с заготовки осуществляется различными режущими инструментами. Закрепление режущих инструментов и обрабатываемых деталей, а также их движение и относительное перемещение производятся рабочими органами металлорежущих станков.
Свариваемость – способность металлов образовывать сварное соединение, свойства которого близки к свойствам основного металла. Ее определяют пробой сваренного образца на изгиб или растяжение.
18
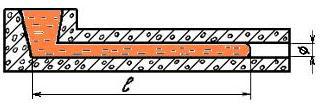
Сварку используют при строительстве резервуаров для хранения жидкостей и газов, трубопроводов, котлов, цистерн.
Ковкость – способность металла обрабатываться давлением в холодном или горячем состоянии без признаков разрушения.
Литейные свойства металлов характеризуют способность их образовывать отливки без трещин, раковин и других дефектов. Основными литейными свойствами являются
жидкотекучесть;
усадка;
ликвация.
Жидкотекучесть – способность расплавленного металла хорошо заполнять полость литейной формы. Жидкотекучесть определяют по стандартной пробе в виде канала определенной длины и диаметра (рис. 1.1.13).
Рис.1.1.13. Определение жидкотекучести
Усадка при кристаллизации – это уменьшение объема металла при переходе из жидкого состояния в твердое. Усадка является причиной образования усадочных раковин и усадочной пористости в слитках и отливках.
Ликвация – неоднородность химического состава сплавов, возникающая при их кристаллизации.
Эксплуатационные свойства определяют в зависимости от условий работы оборудования специальными испытаниями. К эксплуатационным свойствам относятся износостойкость, хладостойкость, жаропрочность, жаростойкость, антифрикционность.
Износостойкость – свойство материала оказывать сопротивление износу, то есть постепенному изменению размеров и формы тела вследствие разрушения поверхностного слоя изделия при трении.
Хладостойкость - способность материалов, элементов, конструкций и их соединений сопротивляться хрупким разрушениям при низких температурах окружающей среды.
Жаростойкость (окалиностойкость) — сопротивление металла окислению при высоких температурах.
19