
[elib.tsogu.ru]_kompjuternye-tekhnologii...83-a5 (2)
.pdfготовых формул, составленных разработчиками, пользователю предоставляется возможность составлять и использовать для анализа свои формулы.
Результаты моделирования технолог просматривает и обрабатывает в постпроцессоре «Мираж-3D», позволяющем загрузить файлы с результатами моделирования, полученных в модулях процессора, и в динамике просмотреть на компьютере тот или иной процесс в жизни отливки: заполнение формы, затвердевание отливки, локализация тепловых узлов и образование дефектов. Интерфейс постпроцессора позволяет пользователю поворачивать объект, делать в нем любые сечения, изменять масштаб изображения, трансформировать цветовую палитру, переходить от зон равных значений свойств к изолиниям, оцифровывать изображения, совмещать на экране одновременно несколько изображений. Счетчик реального времени процесса помимо индикации текущего момента дает возможность быстро перемещаться в любую точку временной оси и просматривать «кино» покадрово, либо непрерывно (в автоматическом режиме) с любого момента.
Следующее перспективное направление применения компьютерных технологий в литейном производстве, прежде всего в процессе подготовки производства, – проектирование технологии, проектирование оснастки, изготовление оснастки с использование CAD-систем и станков с ЧПУ.
Особенностью получения литых заготовок, в сравнении с другими стадиями обработки, является получение сложных поверхностей и сопряжений, поэтому литьем изготавливают детали, которые другими способами изготавливать или очень дорого, или вообще невозможно. В силу своей специфики подготовка производства в литье является наиболее длительным процессом. А в условиях мелкосерийного производства, кроме того, является фактором, значительно влияющим на конечную цену изделия. При этом наиболее трудоемкая и дорогостоящая часть подготовки – это разработка литейной технологии, проектирование и изготовление литейной оснастки.
Вусловиях мелкой серии, например 500 отливок для ЛВМ, что сейчас не редкость, стоимость оснастки будет сравнима со стоимостью собственно литья. Т.е. стоимость оснастки оказывает заметное влияние на конечную цену отливки. Кроме того, качество изготовления литейной оснастки определяет часто и качество литья, а значит и его стоимость. Хорошо сделанная оснастка снижает литейный брак, повышает производительность труда литейщиков, снижает затраты на механическую обработку. Для получения более сложных, а значит и более дорогих отливок требуется более сложная оснастка. Скорость изготовления оснастки очень часто определяет время выхода первых отливок и продолжительность изготовления всего заказа, что для литейных предприятий зачастую определяет возможность получения новых заказов. Т.о. скорость и качество проектирования и изготовления оснастки является одним из важнейших факторов влияющих в ту или иную сторону на экономику литейного предприятия.
Внастоящее время практически все литейные производства России
испытывает острую потребность |
в квалифицированных технологах |
и конструкторах литейной оснастки. |
Оставшиеся действующие технологи |
81
иконструкторы, как правило, могут быть отнесены к категории ветеранов, работающих по традиционным технологиям – кульман, бумага, карандаш, методы проб и ошибок при разработке новой технологии и освоении отливки. Такие методы разработки литейной технологии основаны на собственном многолетнем производственном опыте. Для изготовления оснастки в этом случае необходим выпуск комплекта бумажных чертежей. Выпуск чертежей сопряжен с многочисленными согласованиями, поскольку, за литье, проектирование и изготовления оснастки отвечают, как правило, различные подразделения предприятия, а изготовление оснастки ведется на универсальном оборудовании, что сопровождается неизбежными ошибками, как на стадии проектирования, так и на стадии изготовления, так как на эти процессы сильно влияет человеческий фактор. Все эти негативные особенности многократно усиливаются для оснастки, имеющей сложные поверхности
исостоящей из нескольких частей.
Традиционные способы проектирования и изготовления оснастки, в совокупности с устаревшим оборудованием большинства цехов, являются, кроме того, причиной низкой привлекательности литейного производства для молодых специалистов. При этом невосполнимо утрачивается многолетний опыт ветеранов производства.
Совершенно другая ситуация складывается при применении современного компьютеризированного подхода к начальному и самому важному этапу освоения производства отливок – разработке литейной технологии, проектированию и изготовлению литейной оснастки.
|
В общем виде такой подход предусматривает следующие этапы: |
|
получение от заказчика чертежа детали или отливки (возможно |
в электронном виде); |
|
|
разработка литейной технологии, разработка и построение в CAD-системе |
объемной модели отливки и согласование с заказчиком электронного или бумажного чертежа отливки;
|
при необходимости анализ и |
оптимизация литейной |
технологии |
с |
помощью системы компьютерного |
моделирования литейных |
процессов |
«Полигон»;
конструирование и проектирование литейной оснастки в CAD – системе;
обработка формообразующих поверхностей оснастки на станках с ЧПУ;
изготовление простых элементов оснастки на универсальном оборудовании;
сборка оснастки.
Может работать при изготовлении оснастки для любого способа литья: в кокиль, литье по выплавляемым моделям, в землю, под давлением и т.д. На некоторых заказах отдельные стадии процесса могут выпадать. Например, если от заказчика приходит уже объемная модель отливки или даже готовый проект пресс-формы. Но в целом технологическая цепочка остается.
Для детали «Niederhalter 30мм», представленной на рис. 3.8, показаны пресс-формы для изготовления методом ЛВМ рис. 3.9-3.11.
Общее время, потраченное на проектирование и изготовление этой, довольно сложной пресс-формы, составило 14 человеко-дней и 18 нормо-часов
82
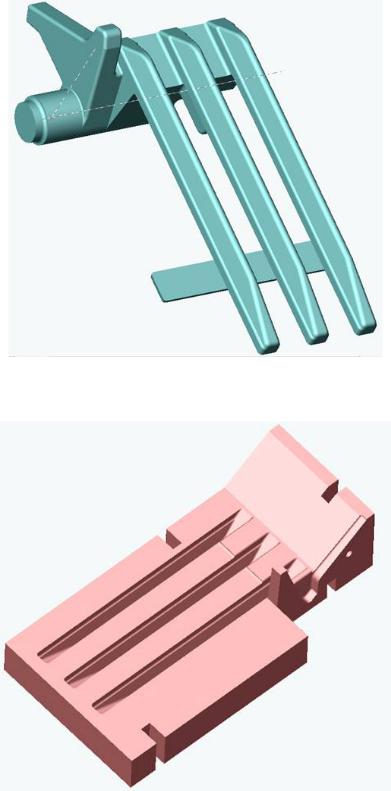
работы оборудования. При этом значительная треть времени ушло на процессы согласования чертежей отливки. Из этого примера видно, что предложенная технология изготовления оснастки вполне может конкурировать с традиционными методами изготовления оснастки и имеет неоспоримые преимущества.
Рис. 3.8. Объемная модель отливки
Рис. 3.9. Верхняя полуматрица
83

Рис. 3.10. Нижняя полуматрица и вкладная часть
Рис. 3.11. Готовая пресс-форма
К основным преимуществам использования информационных технологий можно отнести следующее:
Стоимость. Сопоставима с традиционной технологией, а для сложных отливок существенно ниже.
Скорость изготовления. По сути, любая оснастка средней сложности изготавливается за 2-3 недели в обычном рабочем режиме.
84
Качество оснастки. Практически всегда детали полуматриц изготавливаются из единой заготовки, а не собираются из нескольких частей как при традиционной технологии.
Отсюда возрастает точность изготовления оснастки. Кроме того, современные станки с ЧПУ имеют очень высокую точность – 0,005–0,01 мм.
В довершение всего компьютерное проектирование оснастки и моделирование литейной технологии позволяют избежать многих ошибок, характерных для традиционной технологии.
3.6.1. Моделирование обработки металлов давлением
DEFORM — специализированный программный комплекс, предназначенный для моделирования технологических процессов обработки металлов давлением, термообработки и механообработки. DEFORM — разработка американской компании Scientific Forming Technologies Corporation (SFTC),
всемирно признанного лидера в области моделирования процессов обработки металлов давления. DEFORM применяется ведущими промышленными предприятиями и исследовательскими центрами по всему миру. В России и странах СНГ компанию SFTC уже более пяти лет представляет инжиниринговая компания «ТЕСИС».
DEFORM создан специально для технологов, имеет простой русскоязычный Windows-интерфейс и не требует специальных математических знаний. Для работы с этим программным комплексом достаточно лишь владения навыками работы с персональным компьютером на уровне пользователя.
Впоследнее время все больше возрастает интерес к программному комплексу DEFORM со стороны промышленных предприятий и технических вузов России и Украины.
Вданной подразделе представлен материал об использовании программного комплекса DEFORM в промышленности и учебном процессе.
Интерес со стороны промышленных предприятий в первую очередь связан с требованиями современного рынка, где выживают только самые сильные, конкурентоспособные и технически оснащенные предприятия. Уходят в прошлое неэффективные, металлоемкие технологии, предприятия оснащаются новым современным оборудованием. Руководство предприятий начинает задумываться о путях сокращения затрат на производство и одновременно о сроках запуска в производство новых изделий. Один из таких путей — применение систем САПР, в том числе систем автоматизированного инженерного анализа.
Программный комплекс DEFORM представляет собой инструмент технолога. Он незаменим на самой длительной и дорогостоящей стадии технологической подготовки производства — стадии отработки, доводки
ивнедрения технологии получения заготовок.
Прежде все предприятия работали по одной и той же схеме. Технологи по стандартным методикам или, исходя из накопленного за годы работы
85
опыта, разрабатывали технологию изготовления изделия, подбирали заготовку и строили формообразующие части штампа.
Далее технология передавалась на производство, где штамп изготавливался в металле. В зависимости от возможностей и загруженности конкретного предприятия сроки изготовления штамповой оснастки могли доходить до нескольких месяцев.
Затем оснастка монтировалась на штамповочное оборудование и начинался этап проверки и отладки технологии. Лишь в единичных случаях сразу же удавалось получить изделие необходимого качества, но преимущественно оснастка дорабатывалась на месте. Практически на всех предприятиях найдется опытный мастер, проработавший там не один десяток лет и знающий что и как нужно менять. Как правило, увеличиваются радиусы и уклоны, корректируется форма и размеры заготовки. Все это делается исключительно по наитию, руководствуясь опытом данного человека и его интуицией. Но даже высококлассные специалисты порой бывают бессильны. Не всегда удается удачно подкорректировать геометрию формообразующих. Оснастка бракуется, а процесс возвращается технологу на переработку. Хорошо еще, если такой возврат будет всего один. Отработка особенно сложных деталей иногда длится по нескольку лет.
Программный комплекс DEFORM позволяет кардинально изменить подобную ситуацию. DEFORM не замещает технолога — он является его инструментом. Как и прежде, по стандартным методикам на основе накопленного опыта разрабатывается технология изготовления того или иного изделия. Далее, при помощи программного комплекса DEFORM, технологию проверяет сам технолог на своем рабочем месте.
В отличие от реального производства, где результаты можно получить лишь через несколько месяцев, компьютерное моделирование позволяет сделать это уже через несколько часов или даже минут. При этом технолог может заглянуть «внутрь» процесса, что невозможно на производстве, проследить за течением материала, увидеть возможные дефекты (складки, зажимы, утяжены, незаполнения и пр.). Плюс к тому, DEFORM включает возможности исследовательской лаборатории и позволяет получить информацию о напряженно-деформированном состоянии поковки/ штамповки на разных этапах деформирования, о распределении температуры, о макро- и микроструктуре, о напряжениях в инструменте, потребном усилии процесса деформирования и о многом другом.
Оперативно владея всей этой информацией, технолог лучше представляет себе данный технологический процесс, может оценить влияние на него различных параметров, видит возможные пути его исправления и оптимизации. Технолог может проверить десятки, а то и сотни вариантов технологического процесса и выбрать из них оптимальный с точки зрения затрат и качества.
Интерес к DEFORM со стороны вузов в первую очередь связан с требованиями современного рынка. Промышленные предприятия, работающие в жестких конкурентных условиях, требуют от молодых специалистов,
86
оканчивающих вузы, не только более высокого уровня технической подготовки, но и знания современных систем САПР.
Вторая причина повышенного интереса к DEFORM со стороны вузов
— ухудшение в последнее десятилетие их материльно-технической базы. Оборудование в университетских лабораториях, на котором студенты и аспиранты проводят исследовательские и практические работы, сильно износилось или устарело. Многие предприятия-шефы, на территории которых студенты традиционно проходили практику, отказываются работать с вузами или вообще прекращают свою кураторскую деятельность. DEFORM в этом отношении уникален, поскольку позволяет смоделировать поведение практически любого применяемого на производстве оборудования, такого как механический пресс, молот, гидравлический пресс, прокатный стан, раскатная машина и пр.
Использование DEFORM в учебном процессе обеспечивает значительное повышение уровня подготовки студентов. Во-первых, студенты лучше осваивают теорию обработки металлов давлением — не только по рисункам и диаграммам из справочников, но и на основе расчетов и анализа результатов в DEFORM. Во-вторых, проведение лабораторных работ в DEFORM помогает студентам лучше понять специфику каждого технологического процесса обработки металлов, изучить его особенности и проблемы. В-третьих, работа на компьютере для сегодняшних студентов намного привлекательнее работы в читальном зале библиотеки. Поэтому использование компьютерных технологий способствует повышению интереса студентов к обучению. А если студент учится с интересом, то и качество его обучения будет лучше.
Одним из примеров использования программного комплекса DEFORM стала научно-исследовательская работа «Вопросы моделирования процесса клиновой раскатки с применением программного комплекса DEFORM», проведенная совместно компанией «ТЕСИС», Нижегородским государственным техническим университетом и ОАО «ГАЗ».
Целью работы было сравнение результатов математического моделирования с геометрической (теоретической) моделью С.И.Губкина и результатами непосредственного замера деформации прокатанных винтов. Было проведено исследование активно движущихся слоев заготовки в процессе клиновой раскатки заготовки прямоугольного сечения (использовался метод непосредственного замера деформации прокатанных винтов). Произведено сопоставление полученных результатов с геометрической (теоретической) моделью С.И.Губкина и данными математического моделирования процесса раскатки методом конечных элементов (МКЭ) с применением программного комплекса DEFORM.
Геометрическая модель формы локально деформированного объема конструировалась по способу, предложенному С. И. Губкиным. Согласно его теории зона локализации, или форма конуса скольжения, определяется областью действия максимальных тангенциальных напряжений. Последние определяются формой и величиной контактной поверхности инструмента, находящегося в активном движении. Теоретическое выявление конфигурации
87
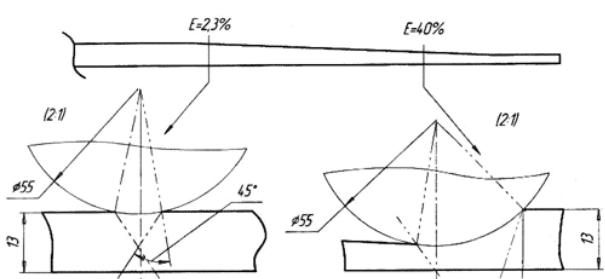
локальной зоны деформации при раскатке полосы на клин в промежуточных положениях представлено на рис. 3.12. Сверху геометрический очаг ограничивается активно движущейся контактной поверхностью инструмента-ролика, снизу — свободной поверхностью неподвижной опоры, слева и справа — границей, отделяющей текущий металл от его недеформированной части.
Рис. 3.12. Схемы направления главных тангенциальных напряжений при обжатиях
Рассмотрим результаты математического моделирования. При этом можно выделить зоны локального течения, активно движущиеся, свободные и пассивные поверхности.
Основное истечение металла происходит из областей, исходящих из краев точек периметра контакта ролика с заготовкой и образующих угол ~45° с касательными в этих точках. Это соответствует направлению максимальных тангенциальных напряжений. С увеличением обжатия направление максимальных тангенциальных напряжений от точки периметра контакта инструмента с металлом по ходу прокатки постоянно меняется, что влечет за собой изменение формы и размеров зоны интенсивной деформации. Картина эквивалентных напряжений представлена на рис. 3.13.
Приведенные данные свидетельствуют в целом о соответствии формы и положения зон локализации деформации теории С. И. Губкина о геометрической модели очага деформации.
Изменение формы и размеров локально деформированного объема обусловливает изменение интенсивности деформации слоев прокатываемой заготовки. При этом по мере увеличения степени обжатия вторая зона постоянно увеличивается и контур, отделяющий очаг деформации от металла, не вступившего в деформацию, начинает постепенно изгибаться. Картина эквивалентных деформаций представлена на рис. 3.14.
88

Рис. 3.13. Картины эквивалентных напряжений при обжатиях:
а — 4 %, б — 23 %, в — 40 %
Рис. 3.14. Картины эквивалентных деформаций при обжатиях:
а — 4 %, б — 23 %, в — 40 %
89
Сравнение результатов моделирования с оценкой неравномерности течения металла в слоях заготовки по величине деформации соответствующих слоев прокатанных винтов и величине их прогиба показало в целом их сопоставимость и объективность.
Можно отметить следующее: математическое моделирование процесса раскатки методом конечных элементов (МКЭ) с применением программного комплекса DЕFОRM достоверно воспроизводит данный технологический процесс.
4.КОМПЬЮТЕРНЫЕ ТЕХНОЛОГИИ
ВОБЕСПЕЧЕНИИ КАЧЕСТВА ИЗДЕЛИЯ
Повышение качества и конкурентоспособности отечественной промышленной продукции – проблема актуальная. Низкий уровень качества приводит к снижению доли товаров российского производства на внутреннем и внешнем рынках.
Системы менеджмента качества (СМК) могут содействовать организациям в постоянном совершенствовании своей продукции и своих процессов и повышении удовлетворенности потребителей. Системный подход к менеджменту качества побуждает организации анализировать требования потребителей, определять процессы, способствующие получению продукции, приемлемой для потребителей, а также поддерживать эти процессы в управляемом состоянии.
Стремление отечественных товаропроизводителей интегрироваться в мировую экономику требует создания на предприятиях СМК, отвечающих международным стандартам ИСО 9000:2008, и признаваемой на внешнем рынке сертификации СМК на соответствие этим стандартам.
4.1. Анализ состояния вопроса
Как показал анализ [1], более 50 % СМК на предприятиях России малоэффективны. Одной из причин этого является недостаточный объем применения информационных технологий на предприятиях. Подсистема сбора и анализа информации о дефектах и причинах отказов производимой продукции на всех этапах ее жизненного цикла (ЖЦ) фактически не работает. Информация в журналах и даже на отдельных ЭВМ, не связанных в единую информационную сеть, не позволяет выполнить комплексный анализ дефектов и причин их возникновения. Для разработки и реализации обоснованных конструкторско-технологических решений по обеспечению качества продукции на всех этапах ее ЖЦ необходимо иметь ежедневную актуальную информацию по всем технологическим параметрам. быть обеспечена возможность оперативного анализа всей собранной информации. Такая задача может быть решена только при наличии на предприятии интегрированной
90