
3068
.pdf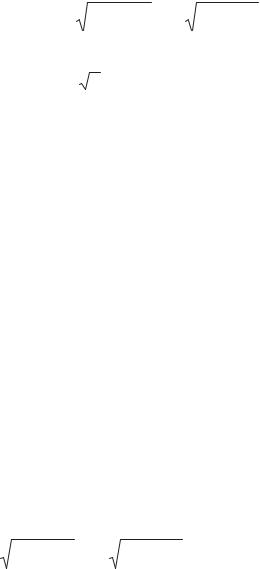
|
2 |
2 |
2 |
2 |
(11.11) |
|
'x |
'y |
Z 'Ȝ 'ȕ d Sɧɦ |
|
|
и при x = y = |
x,y и λ = β = λ,β получим |
|
|||
|
2 'x, y |
Z 'Ȝ,ȕ d 0,5 Sɧɦ |
(11.12) |
||
|
|
|
или |
|
|
|
'x, y Z 'Ȝ,ȕ d 0,35 Sɧɦ . |
(11.13) |
|||
В соответствии с этим при равном ограничении линейных и угло- |
|||||
вых параметров ( |
x,y = Z ∙ |
λ,β) требования к точности относительного |
положения устанавливаемого вала составят
± x = 0,17 ∙ Sнм; ± y = 0,17 ∙ Sнм; ± λ = 0,17 ∙ Sнм/Z; ± β = 0,17 ∙ Sнм/Z.
Для расширения условий собираемости на соединяемых цилиндрических поверхностях вала и корпуса создают фаски, которые при возможности малых перемещений вала относительно корпуса позволяют осуществить самоустановку вала в отверстие. Эта малая саморегулировка в пределах клиновой пары двух фасок обеспечивает пассивную адаптацию, которая широко применяется при автоматической сборке. Расширение условий собираемости в данном случае адекватно
увеличению зазора Sнм на величину: |
|
P = Cо ∙ tgφо + Cв ∙ tgφв, |
(11.14) |
где Со, Св и φо, φв – соответственно ширина и углы наклона фасок в отверстии и на валике.
С учетом (11.14) условие собираемости (11.11) принимает вид
'2x '2y Z '2Ȝ '2ȕ ≤ Sнм + Cо ∙ tgφо + Cв ∙ tgφв |
(11.15) |
В соответствии с этим допускаемые расширенные параметры |
точности положения устанавливаемого вала можно рассчитать по формулам:
– линейные: ± x = 0,17 (Sнм + P); ± |
y = 0,17 ∙(Sнм + P); |
(11.16) |
– угловые: ± λ = 0,17(Sнм + P)/Z; ± |
β(Sнм + P)/Z. |
(11.17) |
Полученные значения (± x, ± y) и (± λ, ± β) являются исходными данными для определения точности позиционирования конечных звеньев сборочных машин или роботов.
Требуемые относительные перемещения вала, совершаемые при его установке в корпус, определяет вектор = ( а, b, c, , , ), в котором с – задаваемое главное перемещение вала в направлении оси zо, а ( а, b) и ( , ) – малые линейные и угловые смещения, выполняемые в процессе самоцентрирования вала по отверстию.
231
Созданию автоматических сборочных систем должен предшествовать глубокий анализ существа сборочных переходов и самого процесса соединения деталей рассматриваемого узла. На основе такого анализа выявляют требования к технологичности соединяемых деталей узла и требования к точности автоматического сборочного оборудования. Узел, который в обычных условиях при ручной сборке не вызывает сложностей, при автоматической сборке может оказаться нетехнологичным. В общем случае имеют место следующие рекомендации для деталей при автоматической сборке. Соединяемые детали должны иметь на сопрягаемых поверхностях возможно большие по размерам заходные фаски. На втулках и кольцах подшипников, устанавливаемых в корпус с гарантированным натягом, заходные фаски желательновыполнятьступенчатыми, вначалесбольшимуглом(30 …45 ), азатем с меньшим (10 …15 ) (рис. 11.34, а). Все это способствует снижению усилий запрессовки, обеспечивает правильное центрирование и снижает деформации колец.
Более сложной представляется автоматическая сборка резьбовых соединений. Вектор относительных перемещений винта при его установке имеет вид = ( а, b, c, , , ). Он показывает, что требуется не только перемещение винта c вдоль оси, но и придание ему вращения для попадания в нитку резьбы и выполнения автоматического навинчивания. Малые смещения ( а, b) и повороты ( , ), совершаемые при пассивной адаптации, обеспечивают самоцентрирование винта в резьбовом отверстии. Для расширения условий собираемости торец винта делают в виде сферы (рис. 11.34, б), а на корпусе предусматривают фаски. С этой же целью изменяют конструкцию винтов и создают сравнительно большой заходный конус.
Для уменьшения сборочных переходов отдельные детали конструктивно объединяют в одну более сложную деталь. Так, например, вместо трех деталей (винта, шайбы и гровер-шайбы) применяют один винт, у которого на торце головки делают бурт с зубцами, исключающими самоотвинчивание (рис. 11.34, в). С целью уменьшения погрешности установки соединяемых деталей в их конструкции предусматривают точные базовые поверхности, по которым происходит их захват роботами (рис. 11.34, г).
У стопорных колец, устанавливаемых на вал или в отверстие для фиксации осевого положения деталей, требования автоматической
232
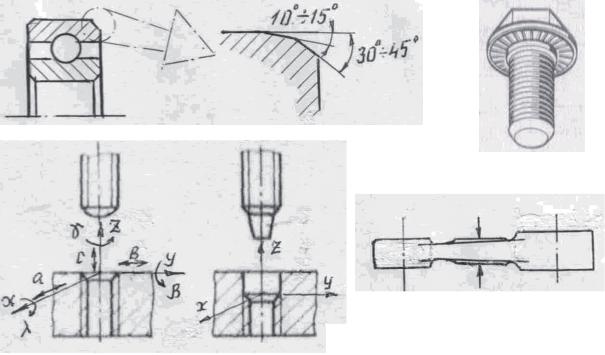
сборки определяют необходимость ужесточения допуска на толщину кольца и на точность геометрической формы. Устанавливаемые пружины имеют уменьшенный шаг между витками на концах и в середине пружины, благодаря этому упрощается их установка и уменьшается возможность их сцепляемости в ориентирующих устройствах сборочных машин.
а)
в)
г)
б)
Рис. 11.34. Повышение технологичности деталей для выполнения автоматической сборки: а – направляющие фаски на кольцах подшипников; б – геометрия деталей для соединения винтовых поверхностей; в – объединение винта, плоской и разрезной стопорной шайбы в одну деталь; г – создание на детали типа «рычаг» точных базовых поверхностей
Автоматические сборочные машины применяют для сборки определенных изделий, выпускаемых в условиях крупносерийного и массового производств. Это специальные высокопроизводительные сборочные автоматы, которые создают под конкретное изделие устойчивойконструкции(например, длясборкиподшипников). Сборочныемашины обладают малой технологической гибкостью, они практически не перенастраиваются на сборку другого изделия.
Сборочные машины могут быть однопозиционные и многопозиционные.
В первом случае сборка осуществляется на одной позиции с использованием несколько сборочных головок, в которых имеются нако-
233
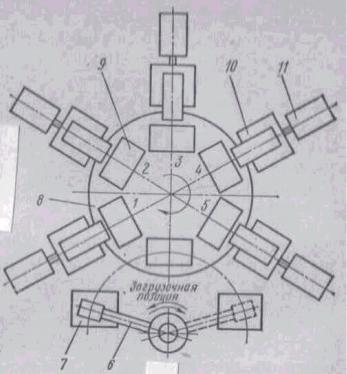
пителискомплектующимидеталями, ориентирующиеустройстваиисполнительные механизмы. Установка на рабочую позицию базовой детали осуществляется с помощью манипулятора, который осуществляет также съем собранного изделия. Однопозиционные машины применяются для сборки простых изделий с малым числом деталей. Ограниченность пространства на одной позиции не позволяет осуществить параллельную установку ряда деталей.
Вмногопозиционныхсборочныхмашинахсобираемыйобъектперемещаетсяотоднойрабочейпозициикдругой(рис. 11.35). Попериметру поворотного круглого стола устанавливают несколько сборочных головок, каждая из которых выполняет определенный переход. В результате происходит параллельнопоследовательное выполнение сборочных переходов. На первой позиции манипулятор устанавливает базовую деталь и снимает собранное изделие.
Сборка может выполняться с использованием одной или нескольких машин, соединенных транспортером в одну сборочную линию.
Автоматическая сборка с использованием промышленных роботов (ПР) иманипуляторовосуществляется как на отдельных сборочных модулях, так и на автоматических линиях. Основным преимуществом такого оборудования является технологическая гибкость, позволяю-
щая перенастроить модуль на сборку новых изделий с использованием других комплектующих деталей. Программирование робота осуществляется с помощью компьютерных систем управления. Управляющая программа в соответствии с технологией сборки разрабатывается заранее и при необходимости ее можно дополнить и внести коррекцию.
234
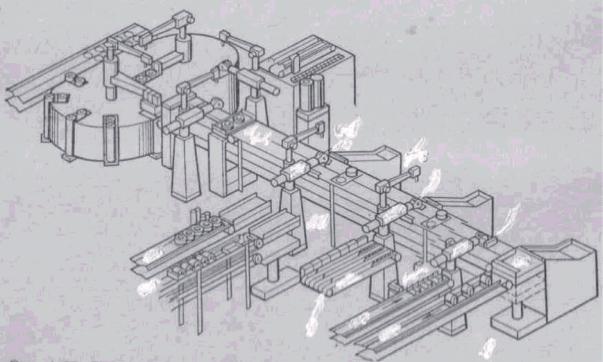
С помощью специальных сменных сборочных головок и схватов робот последовательно выполняет заданные технологические переходы, связанные с ориентацией, установкой, запрессовкой, завинчиванием деталей или измерением параметров точности. Сборочные головки и схваты имеют одинаковые базы и их замену на конечном звене робот также осуществляет автоматически по заданной программе. При последовательной сборке, выполняемой одним роботом, производительность модуля оказывается ниже, чем сборочных машин. Поэтому на базе роботов и манипуляторов создают автоматические линии, на которых осуществляется высокопроизводительная параллельнопоследовательная сборка (рис. 11.36).
Рис. 11.36. Автоматическая сборочная линия из промышленных роботов
Точность позиционирования конечных звеньев роботов обычно составляет 0,1…0,3 мм, между тем как соединение ряда деталей требует обеспечить точность их относительного положения в пределах0,01… 0,05 мм. Этого достигают за счет применения систем пассивной и активной адаптации, создающих малые ориентирующие перемещения непосредственно в момент соединения деталей. Конструктивно такие системы располагают в схвате робота или на столе, на котором устанавливают базовую деталь собираемого изделия. В системах активной адаптации в качестве датчиков обратной связи применяют датчики давления, силы, моментов и системы технического зрения.
235
Вопросы для самопроверки
1.Назовите сборочные единицы, образующие различные по конструкций машины.
2.В чем заключается сущность поточной формы организации техпроцесса сборки изделия?
3.Что следует понимать под понятием «такт выпуска»?
4.Какие исходные данные необходимо иметь для расчета такта выпуска?
5.Как рассчитывается общая трудоемкость сборки изделия?
6.Назовите виды подвижной поточной сборки.
7.Как организуется стационарная поточная сборка?
8.Как определяют количество рабочих позиций на сборочном конвейере?
9.С какой целью выполняют построение циклограммы сборки?
10.Как осуществляют монтаж опор на подшипниках скольжения?
11.Как выполняют монтаж опор на подшипниках качения?
12.Назовите технологические мероприятия, позволяющие уменьшить осевое биение валов на опорах скольжения.
13.Длячегосоздаютпредварительныйнатягвподшипникахкачения?
14.Назовите технологические мероприятия, позволяющие уменьшить радиальное биение на конце шпинделя.
15.Какие факторы определяют величину бокового зазора в цилиндрических зубчатых передачах?
16.Что определяют нормы кинематической точности для зубчатых передач?
17.Как можно проверить качество зацепления конических зубчатых колес?
18.Какие задачи достижения точности решают при сборке конической пары зубчатых колес?
19.Назовитенормыточности, устанавливаемыеназубчатыепередачи.
20.Как проверить величину бокового зазора в зубчатой передаче?
21.Какие параметры точности необходимо обеспечить при сборке червячных передач?
22.Что следует понимать под условиями собираемости при выполнении автоматической сборки?
236
23.Назовите мероприятия, позволяющие расширить условия собираемости в соединениях по цилиндрическим поверхностям.
24.В каких случаях для автоматизации сборки применяют сборочные машины или сборочные модули, создаваемые на базе промышленных роботов?
237
Глава 12. ОСНОВЫ РАЗРАБОТКИ ТЕХНОЛОГИЧЕСКОГО ПРОЦЕССА ИЗГОТОВЛЕНИЯ МАШИНЫ
12.1. Исходные данные и последовательность разработки технологического процесса изготовления машины
Для разработки технологического процесса изготовления машины необходимо иметь следующие исходные материалы: 1) краткое и точное описание служебного назначения машины; 2) технические требования и нормы, определяемые ее служебным назначением; 3) рабочие чертежи машины; 4) данные о объеме выпуска машины и о количестве машин, намеченных к выпуску по неизменяемым чертежам (величина серии); 6) условияорганизациииподготовкипроизводства(выпускмашин на существующем заводе с использованием имеющегося там оборудования или на вновь создаваемом заводе с перспективой получения нового оборудования); 7) данные о местонахождении завода, условиях снабжения и о возможности кооперирования с другими предприятиями; 8) наличие и перспективы получения кадров; 9) плановые сроки подготовки и освоения производства по выпуску машины.
Указанные исходные материалы являются основой детальной проработки комплекса поставленных технологических задач с учетом фактических условий организации производства и выпуска готовых изделий. Точная, конкретная формулировка поставленной задачи и условий ее реализации позволяет найти наилучшие технологические решения как по срокам их выполнения, так и по производимым затратам.
Выбор наиболее экономичного варианта технологического процесса, формы организации производства, необходимого оборудования, инструмента, технологической оснастки, а также уровня механизации и автоматизации напрямую зависит от намечаемого объема выпуска машин N и общего количества их выпуска Е по неизменяемым чертежам. Отношение Е/N определяет промежуток времени (количество лет), в течениекоторогопредполагаетсяосуществлятьвыпускмашиныбезизменения ее конструкции.
При больших объемах выпуска изделий в течение нескольких лет возникает задача создания крупносерийного или массового производ-
ства, для которого будет выбрана поточная форма его организации с
238
соблюдением постоянства такта выпуска. В соответствии с этим будут подробно разрабатываться наиболее совершенные технологические процессы сборки машины и изготовления ее деталей. Для реализации таких процессов будут использовать наиболее производительное технологическое оборудование, приспособления и инструмент, включая станки-автоматыиполуавтоматы, автоматическиелинииизагрегатных и других специальных станков.
Поточнаяформаорганизациипотребуетсозданияназаводеавтоматическихтранспортныхсистемиавтоматизированныхскладов, обеспечивающих непрерывность движения и требуемые скорости перемещения непересекающихся грузопотоков. Создание специального технологическогоитранспортногооборудованияпотребуетпроведениябольшогообъема проектно-конструкторскихработвсоответствиистехническимизадания- минапроектирование, которыесоставляюттехнологипорезультатамразработкитехнологическихпроцессовизготовлениямашины.
Вслучае необходимости периодического выпуска в больших объемах нескольких типов изделий, близких по служебному назначению
исвоим масса-техническим параметрам, потребуется организация переменно-поточного производства. Это потребует изыскания своих технологических решений, применения перенастраиваемого технологического оборудования и приспособлений, обеспечивающих возможность реализации групповой обработки однотипных деталей близких габаритных размеров.
Вслучаесравнительнонебольшихобъемовсерийноговыпускаизделийнесколькихнаименованийбудетиспользовананепоточнаяформаорганизации производства. Для этого будут созданы технологически замкнутые участки с расстановкой оборудования по ходу технологическогопроцесса. Технологическиепроцессыбудутразрабатыватьсясучетом применения быстро перенастраиваемого технологического оборудования, в том числе станков с ЧПУ и обрабатывающих центров. В производстве будет использована перенастраиваемая технологическая оснастка, например универсально-сборные приспособления (УСП). При этом такжепотребуетсясозданиеавтоматизированныхскладовиучастковдля промежуточного хранения производственных заделов.
Дляусловиймногономенклатурногомелкосерийногоиединичного производств будет принята непоточная форма их организации при расстановке оборудования по группам станков. Технологические процес-
239
сы будут разрабатывать с ориентацией на применение универсального технологического оборудования с использованием универсальных приспособлений и инструментов. С целью повышения производительности особое внимание будет уделено вопросам организации групповой обработки деталей.
Важно также знать условия, в которых будет выполняться разрабатываемый технологический процесс. Если технологический процесс разрабатывается для реализации на вновь создаваемом заводе, то технолог имеет возможность большего выбора вариантов технологических процессов, оборудования и инструмента. В случае, когда технологический процесс разрабатывается для реализации на действующем заводе при необходимости использования имеющегося там оборудовании, варианты выбора технологических решений значительно ограничиваются.
В последнем случае ограниченные возможности имеющегося оборудования и производственных мощностей отдельных цехов оказывают существенное влияние на варианты технологического проектирования и определяют необходимость кооперирования с другими заводами.
Знание места расположения завода позволяет выявить возможности кооперирования с другими заводами по изготовлению необходимых заготовок – отливок, поковок, проката. Это позволяет выявить возможности размещения заказов на изготовление отдельных деталей и сборочных единиц, а также возможности поставки унифицированных деталей и узлов (подшипников, крепежных нормалей, электродвигателей, насосов и др.), изготавливаемых на специализированных предприятиях.
Наличие кадров инженерно-технического персонала и производственных рабочих, а также знание перспективы их получения и подготовки также оказывает определенное влияние на разработку технологических процессов. Эффективное применение сложного технологического оборудования, например станков с ЧПУ, обрабатывающих центров, роботизированных технологических модулей, не возможно без наличия высококвалифицированных наладчиков, операторов и инженеров-технологов, обеспечивающих написание управляющих программ. При наличии на предприятии рабочего персонала сравнительно не высокой квалификации требуется более детальная,
240