
- •Лекция 1
- •Цели и задачи курса
- •Контрольные вопросы к лекции 1.
- •Лекция 4.
- •Конструкторско-технологические разновидности ПП.
- •Конструкционные материалы для изготовления ПП
- •Основные конструкционные материалы для производства ПП
- •Основные составляющие слоистых пластиков для изготовления ПП
- •Лекция 5
- •Основные этапы изготовления ПП
- •Ручная химическая и электрохимическая подготовка поверхности проводится в ваннах с различными растворами при покачивании заготовок и последующей их промывкой, а механизированная – на автооператорных линиях модульного типа по заданной программе.
- •Увеличение шероховатости диэлектрических поверхностей и клеевых композиций (слоев адгезива, например, в виде акрилбутадиенстирольного каучука) достигается механической (гидроабразивной) или химической обработкой.
- •Продолжение табл.5.1.
- •Окончание табл.5.1.
- •Для придания диэлектрику способности к металлизации (то есть каталитических свойств) и обеспечения адгезии химически осаждаемого металла на диэлектрик, производят сенсибилизацию и активацию его поверхности.
- •Таблица 5.2.
- •Сравнительные характеристики пленок химически осажденной
- •и гальванической меди
- •* По отношению к фольге, получаемой прокаткой, и соответствует 2-м перегибам на 180
- •Однако, гальваническое осаждение возможно только на электропроводящие поверхности и разброс по толщине осаждаемых пленок заметно больший, чем при химическом осаждении.
- •Офсетная печать состоит в изготовлении печатной формы, на поверхности которой формируется рисунок слоя (рис. 5.1).
- •Рис.5.1. Схема установки офсетной печати: 1 – диэлектрик; 2 – медная фольга; 3 – основание установки; 4 – печатная форма; 5 – офсетный цилиндр; 6 – валик для нанесения краски; 7 – краска; 8 – прижимной валик.
- •Рис.5.2. Принцип трафаретной печати: 1 – рама; 2 – фиксатор подложки; 3 – фольгированный диэлектрик; 4 – основание; 5 – трафаретная краска; 6 – трафарет;7 – напечатанный рисунок; 8 – ракель.
- •Проявление, окрашивание и задубливание жидких фоторезистов проводят в конвейерных струйных установках модульного типа, оснащенных устройствами подачи растворов с их фильтрацией и регулировкой давления; роликовым конвейером, соединяющим все модули.
- •Контроль качества изготовленной ПП осуществляют визуально и с помощью специальных контрольно-измерительных средств, при этом определяют:
- •Основные технологии изготовления печатных плат.
- •В зависимости от технологий формирования слоев металлизации и получения рисунка коммутирующих элементов различают следующие технологии изготовления ПП:
- •Лекция 6
- •Общие сведения о сборке и монтаже электронных устройств
- •Подготовка конструктивов к сборке и монтажу ячеек ЭВС
- •Лекция 9
- •Контактолы в виде ненаполненных полимеров.
- •Лекция 10
- •Лекция 11
- •Специфика регулировки микропроцессорных устройств
- •Герметизирующие конструкции и методы их герметизации. Технологические требования, предъявляемые к качеству герметизации.
- •Герметизирующие конструкции с учетом методов герметизации можно условно разделить на две группы:
- •Вне зависимости от метода герметизации для обеспечения качества и эффективности защиты электронных устройств (ЭУ) необходимо выполнять следующие условия:
- •- процессы приготовления герметизирующих смесей не должны загрязнять исходные материалы. Растворители в составе защитных лаков и эмалей следует удалять полностью при полимеризации полученных покрытий.
- •Выбор оптимального технологического процесса (ТП) герметизации ЭВС зависит от степени устойчивости изделия к влиянию климатических факторов, от условий эксплуатации изделия и от экономических факторов.
- •Общая структурная схема реализации ТП герметизации ЭРК, сборочных единиц и ЭУ приведена на рис.14.1. Важно рассмотреть входящие в состав ТП основные его этапы.
- •При входном контроле оцениваются технологические и другие характеристики и (или) параметры используемых материалов и конструктивов герметизируемых изделий.
- •Удаление влаги из герметизируемых изделий происходит путем их нагрева выше температуры кипения воды. В этом случае влага перемещается от зоны с большей влажностью к менее увлажненной и от зоны с большей температурой к менее нагретой.
- •В зависимости от способа нагрева герметизируемых изделий различают: конвекционную, радиационную и индукционную сушки.
- •Защиту изделий органическими материалами также осуществляют разными методами, например, пропиткой и обволакиванием, заливкой, опрессовыванием, переносом капли и др.
- •Рис. 14.4. Схема установки для вакуумной пропитки
- •Рис. 14.5. Схема установки для нанесения полимерных покрытий в электростатическом поле.
- •Рис. 14.6. Примеры герметизации с использованием капсул и жидкого компаунда (а); прессованной таблетки (б): 1 - капсула; 2 – основание платы микросборки; 3 - герметизирующий компаунд; 4 - выводы
- •Основные этапы ТП изготовления вакуумплотного корпуса, общая сборка и монтаж, а также герметизация конструктивов МЭА в корпусе приведены на рис.14.8.
- •Рис. 14.8. Основные этапы изготовления деталей вакуумплотных корпусов, сборка, монтаж и герметизация в них.
- •Рис. 14.9. Методы получения герметичных выводов в герметичных корпусах: а - сваркой; б - пайкой; в - спеканием.
- •Стабилизация параметров внутрикорпусной среды.
- •- испытание диэлектрика на пробивное напряжение проводится до и после термоциклов и циклов пребывания во влажной атмосфере. На тестовые образцы подается синусоидальное напряжение 1500 В частотой 50 Гц в течение 60 с;
- •После испытаний изделия проверяют на наличие: обрывов и коротких замыканий токопроводящих элементов; следов коррозии; различных дефектов в полимерных покрытиях.
- •Контрольные вопросы к лекциям 14 и 16.
- •1. Какие критерии используют при выборе материалов для герметизации?
- •2. Составьте типовую структуру ТП герметизации ЭВС и их конструктивов.
- •3. Приведите примеры и дайте технологическую характеристику органическим материалам, укажите методы герметизации с их применением.
- •4. Охарактеризуйте неорганические материалы и приведите примеры их использования для герметизации изделий электронной техники.
- •5. Какие и с какой целью осуществляют подготовительные операции перед герметизацией с использованием органических и неорганических материалов?
- •6. Какие методы пропитки применяют в производстве МЭА? Каким образом они реализуются?
- •7. Как производят заливку и обволакивание изделий?
- •8. Перечислите основные виды изделий, опрессовываемых пластмассой. Изложите суть изготовления монолитных пластмассовых корпусов.
- •9. В каких случаях используют и как осуществляют герметизацию изделий в металлополимерных корпусах?
- •10. Назовите методы герметизации изделий в вакуумплотных корпусах и кратко их охарактеризуйте.
- •11. Изобразите схему основных этапов герметизации МЭА в вакуумплотных корпусах с учетом изготовления корпусов, сборки и монтажа конструктивов в корпусе и контроля герметичности.
- •12. С какой целью и какими средствами обеспечивают стабилизацию параметров внутрикорпусной среды?
- •13. Как контролируют качество герметизации?
- •15. Составьте последовательность разных видов испытаний герметизирующих полимерных покрытий на ПП ответственных конструкций.
- •Лекция 15
а с учетом соотношений (1), (7) и n=1/d получим:
ρc ≈1.6 rk d Vотн−1.
Контактолы готовятся из отдельных компонентов непосредственно перед использованием. Образуемую смесь компонентов перетирают до образования густой однородной массы, не содержащей комков и крупинок. В полученную смесь затем вводят отвердители (если это необходимо по рецепту) и тщательно перемешивают композицию, добавляя в нее соответствующий разбавитель до получения требуемой вязкости.
Сборочно-монтажная технология с применением контактолов включает следующие
этапы:
-подготовку (химическую обработку с целью очистки) соединяемых деталей. Это важнейший этап, так как малейшие загрязнения резко снижают адгезию клея и ухудшают механическую прочность формируемого соединения;
-нанесение контактола. Для этого используется один из следующих способов: нанесение шприцем, трафаретной либо переносной печатью, пневмодозатором, переносом капли;
-позиционирование навесных компонентов с помощью специальных приспособлений и фиксацию компонентов (при необходимости) после их установки на клеевых точках;
-отверждение клея (контактола) в заданном режиме в инертной среде, температура отверждения Тотв находится в пределах 20÷100оС ;
-контроль качества сборки и монтажа навесных компонентов на платах. Так как в полимеризованном клеевом соединении (после термообработ-
ки) мелкодисперсные частицы металла находятся в промежутках сетки полимера и образуют точечные контакты с большим, по сравнению с монолитным металлом, удельным сопротивлением, то сопротивление ЭК (получаемых с помощью контактолов первой группы) выше, чем у паянных и сварных соединений. Это является основным недостатком контактолов, наряду с потребностью преимущественного использования драгоценных металлов; ограниченной жизнеспособностью исходных клеевых композиций (временной зависимостью их вязкости), а также склонностью органических материалов к старению в большей степени, чем неорганических. Эти недостатки нельзя назвать неустранимыми, так как работы по их устранению в последнее время дают положительные результаты.
Контактолы в виде ненаполненных полимеров.
Перспективной альтернативой контактолам на основе ЭПКМ 1-й группы (наполненным полимерам) являются электропроводящие полимеры 2-й группы, проводимость которых получают за счет образования сопряженных систем путем внутренних превращений в макромолекулах самих полимеров. Механизм электропроводности таких полимеров еще не до конца изучен, хо-
тя и получены полимеры с ρv < 10-4 Ом·см. Однако, исследования последних
1
десятилетий позволили сформулировать основные принципы синтеза электропроводящих полимеров. В частности для синтеза в этом случае необходимо наличие: длинной последовательности сопряженных двойных связей
или формы непрерывной системы π-электронов (в макромолекулах) по всему материалу; жесткой, лучше всего сшитой, структуры макромолекул; определенной концентрации несвязанных свободных электронов, распределенных по структуре молекул (с возможностями переходов от одной макромолекулы к другой). Большую практическую значимость представляют ЭПКМ 2-й группы, полимеризующиеся под действием излучений (ИК и УФ диапазонов), как более технологичные для ИМЭ.
Использование высокоэлектропроводящих полимеров позволит создать не только ЭК с м алым ρv, но и проводники с минимальными потерями, что обеспечит экономную передачу и использование электроэнергии.
Получение соединений накруткой.
Соединения накруткой впервые испытаны в промышленном масштабе в 1950 г. и описаны в работе Келлера в 1952 г. В настоящее время они применяются во всем мире преимущественно для межузлового монтажа. Соединения получаются путем накрутки (навивки) под натягом определенного числа витков провода вокруг жесткого вывода без изоляции, имеющего 2 или более острых ребра.
Число витков провода при накрутке составляет от 4 до 8, диаметр провода составляет 0,4-1,6 мм. В каждой накрутке создается от 20 до 30 контактных соединений, т.к. достаточно большое срезающее усилие разрушает оксидную пленку на проводе и выводе (штыре), образуя надежные контактные поверхности.
Следует отметить, что два первых и два последних витка накрутки могут не давать надежного контактного соединения, поэтому количество эффективных точек контакта провода со штырем определяют как сумму всех точек соприкосновения провода со штырем за вычетом четырех. Поперечные сечения штырей для навивки представлены на рис.9.5. Так, например, при получении соединения четырехгранного штыря с шестью витками провода количество эффективных контактных точек N составляет 20, с четырьмя – 12, в соответствии с расчетом по формуле:
N = n m − 4,
где n – число ребер штыря, m – число витков провода.
Для получения соединений таким способом необходимо удалить с соединяемых поверхностей окислы и загрязнения и образовать механическим методом между ними контакт. В реальных условиях для этого нужны значительные пластические деформации. Когда провод накручивается на штырь, оба они пластически деформируются в точках контакта на острых гранях штыря. Среднее давление между проводом и штырем в точках контакта составляет около (1,8-2,0) Н/м2, что значительно превосходит требования для
1
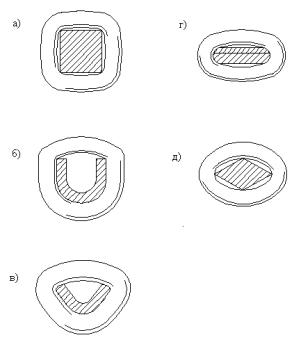
образования проволочного соединения. Последовательность операций при навивке показана на рис.9.6.
Натяжение провода при накрутке достаточно велико для разрушения окисной пленки на штыре и на навиваемом проводе, а также для обеспечения пластической деформации при вдавливании провода по граням штыря в точках контакта. В этих точках возникают центры «схватывания» между двумя поверхностями и образуется газонепроницаемое соединение в результате создания условий для протекания диффузии и образовании холодносварного соединения.
-Качество соединения, выполненного накруткой, зависит от многих факторов. Важно правильно выбрать форму, диаметр, материал провода и штыря, конструкцию рабочего инструмента, соблюдать технологию. При этом для накрутки используются одножильные провода диаметром от 0,2 до 1,6 мм (из меди, алюминия либо никеля). Монтажные штыри должны обладать достаточной прочностью на скручивание, чтобы выдерживать вращающий момент, возникающий при навивке. Они изготавливаются из сплавов бериллий-медь, медь-никель, луженой и нелуженой латуни, плакированной стали, фосфористой бронзы и др. Прочность на растяжение материала штыря должна быть больше или равной 47 кГ·с/мм2, а тве р-
дость по Бринелю не менее 140 кГс·/мм2. При выполнении накрутки в ручном производстве используют накручивающий электрический либо пневматический пистолет. Сначала с провода на определенной длине снимают изоляцию. Оголенный конец провода вставляют в отверстие накручивающей насадки до
Рис.9.5. Поперечное сечение штырей для навивки монтажных проводов:
1
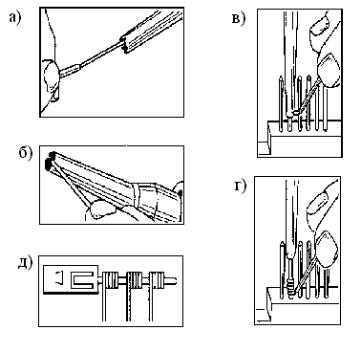
квадратное (а); полукруглые (б, в); прямоугольное (г); ромбовидное
(д).
Рис.9.6. Последовательность операций при навивке: снятие изоляции (а);
закладка провода в паз инструмента (б); навивка провода на штырь(в);снятие (отвод) инструмента со штыря (г);соединение, полученное навивкой (накруткой) (д).
упора и загибают, затем насаживают накручивающий инструмент на штырь. Весь процесс накрутки занимает около 3 с, причем собственно накрутка продолжается от 0,1 до 0,3 с.
При изготовлении соединений накруткой применяются полуавтоматические монтажные машины и автоматы. Автомат для накрутки работает от бухты провода, при этом обрезка и снятие изоляции происходит также автоматически.
Производительность автомата составляет от 500 до 1000 накруток в час. При работе с автоматом необходимо соблюдать следующие условия:
-все контакты должны лежать в одной плоскости;
-шаг должен быть стандартным (шаг – расстояние между центрами соседних витков);
-штыри должны иметь единые размеры;
1
- допуски на расстояния между всеми штырями должны иметь величины, обеспечиваемые автоматом.
При монтаже накруткой для повышения надежности соединений часто используют так называемое «модифицированное соединение». Отличается оно от обычного добавлением к виткам из неизолированного провода, соединяющимся со штырем, одного-двух витков провода с изоляцией у основания штыря. Это несколько увеличивает высоту соединения и его объем, но дает ряд преимуществ. Изоляция уменьшает концентрацию напряжения в точке, где провод касается грани штыря, и поэтому при модифицированном соединении поломка провода у первого витка соединения при вибрациях и перемещениях штырей менее вероятна.
Возможно соединение накруткой и для многожильного провода. Тогда провод не накручивают, а залуживают, и только после этого используют так называемое «бандажирование», представляющее собой соединение провода со штырем, имеющим острые кромки, при котором провод располагают параллельно штырю, вдоль его широкой поверхности. Затем провод крепят к штырю с помощью нескольких витков бандажной проволоки. Каждый виток проволоки «запирается» на двух углах штыря. С помощью бандажирования можно соединять штыри между собой, штырь с шиной и т.п.
Преимущества контактирования накруткой:
-отсутствие нагрева, припоя, флюсов и необходимости удаления остатков флюсов, продуктов флюсования и пайки;
-достаточно хорошая ремонтоспособность соединений;
-возможность автоматизации монтажа объемным проводом.
Тем не менее метод монтажа накруткой не нашел широкого применения из-за его недостатков:
-велик объем, занимаемый контактом (особенно по высоте);
-необходимы специальные меры для разгрузки ячеек и других узлов от усилий, возникающих при накрутке (один-полтора кг для провода диаметром 0,5мм);
-контактное сопротивление при накрутке получается большим, чем при пайке и сварке;
-низкий уровень автоматизации, из-за невозможности реализации групповой техноло-
гии.
Существуют и другие способы соединений подобного рода. Например, иногда соединения проводников получают скручиванием и намоткой, с помощью винтовых креплений, соединений сдавливанием (склепыванием, с применением металлических втулок и пружинных скоб). Возможно также присоединение проводников к соединительным узлам путем сжатия, с помощью зажимов, прижатия, обжимания.
Примеры оборудования для накрутки.
Полуавтомат накрутки ПАН-2 является прецизионным устройством. Он осуществляет поиск контактного штыря под накрутку и провода, необходимого для монтажа, выдает технологические указания.
Характеристики установки:
-размер поля позиционирования (X·Y) мм ………… 500·700
-шаг координатной сетки, мм ………………………. 0,5
-количество ячеек в кассе монтажного провода …… 9
-производительность, накр./ч …………………………200-400
Полуавтоматическая установка УМ-700 для монтажа блоков и панелей по программе.
1
Характеристики установки:
-размер рабочего поля (X·Y) мм ……………………………… 700·600
-максимальная скорость перемещения координатного стола, м/мин …6
-погрешность перемещения координатного стола, не более, мм …… ±0,25
-число ячеек магазина с насадками для штырей………………………… 70.
Контроль качества (КК) микроконтактирования.
Технологический КК монтажа изделий может быть разрушающим и неразрушающим.
Разрушающий контроль чаще всего выполняется выборочно для партий изделий на технологической контактной площадке, либо на тестовой микросборке. Оценка качества осуществляется главным образом по усилию отрыва проволоки от места контакта, это усилие сравнивается с нормированным значением. Недостатками этого метода являются: необходимость технологических элементов или специальных тестовых изделий, иногда с разрушением контролируемого объекта производства. Таким образом, разрушающий КК относится к пассивным методам контроля, так как используется после выполнения технологического процесса монтажа, не влияя на сам процесс.
Неразрушающий контроль дает большие возможности, чем разрушающий. В частности, неразрушающий КК эффективен для оценки качества не только выборки, но и 100% изделий. Такой контроль позволяет оценить качество объектов производства как после различных операций, так и в процессе их реализации, поэтому он может быть активным КК. Например, контрольно-измерительные средства могут быть встроены в модуль пайки; контроль качества пайки в этом случае осуществляется в момент начала кристаллизации припоя и сравнивается с эталоном структуры ЭК в памяти ЭВМ. При необходимости ЭВМ подает команду на корректировку режима пайки.
Методы контроля зависят от физических принципов, положенных в основу измерений того или иного параметра качества (по переходному сопротивлению, по шумовому сопротивлению, по тепловой нагрузке и др.).
Контрольные вопросы к лекции 9
1.С какой целью осуществляют монтаж ЭУ и каковы отличия монтажа модулей разного конструкторско-технологического уровня?
2.Перечислите основные технологические операции (этапы) при монтаже ТМК и ПМК и поясните в чем состоит причина отличия монтажных операций и какова при этом роль
микроконтактирования.
3.Охарактеризуйте основные методы микроконтактирования, указав их достоинства и недостатки.
4.По каким параметрам сравнивают методы микроконтактирования?
5.Какие известны разновидности электрических контактов и межконтактной коммутации? Поясните их возможности и перспективность применения.
6.С чем связаны требования, предъявляемые к ЭК? Перечислите и поясните эти требования.
7.Назовите основные процессы, характеризующие в своей совокупности механизм пайки.
1
8.За счет чего обеспечивается активация контактируемых поверхностей при пайке, а также смачивание припоем поверхностей металлов и его растекание по этим поверхностям?
9.Какова роль процессов растворения и диффузии в образовании макроструктуры ПС? Поясните значение этих процессов с использованием модели макроструктуры ПС и
эквивалентной схемы сопротивления ЭК, получаемого пайкой.
10.Перечислите факторы, влияющие на процесс кристаллизации при образовании ПС и укажите средства управления показателями качества в процессе пайки.
11.По каким признакам систематизируют разные способы пайки? Приведите примеры.
12.Что следует понимать под термином “индивидуальная пайка” и может ли она осуществляться групповым способом? Приведите пример.
13.В зависимости от каких факторов выбирают инструмент (и способ) индивидуальной пайки? Аргументируйте свой ответ.
14.Назовите основные операции при индивидуальном монтаже ТМК и ПМК на ПП. Поясните в чем состоят и в чем объясняются отличия ручного монтажа ТМК и ПМК.
15.Какие требования предъявляют к флюсам и припоям? Назовите основные ингредиенты в их составах. Что обозначает марка ПОС-61?
16.С какой целью разрабатываются припойные пасты?
17.Из каких соображений выбирают очистители смонтированных изделий? Какие из очистителей наиболее эффективны?
18.Перечислите основные виды загрязнений, которые могут оставаться в смонтированных ячейках ЭУ, и к каким негативным последствиям (для изделий) может приводить
наличие этих загрязнений.
19.Что такое контактол первой группы? Каков его состав?
20.Назовите основные требования, предъявляемые к контактолам.
21.В каких случаях целесообразно применять для монтажа контактолы?
22.Как определить сопротивление ЭК, полученного с помощью контактола первой группы?
23.Какова последовательность операций, выполняемых при сборке и монтаже контактолами?
24.Перечислите способы нанесения контактолов и укажите какой из способов обеспечивает наибольшую производительность.
25.Что собой представляют контактолы второй группы? Чем объясняется их перспективность?
26.С помощью каких механизмов реализуются механические и электрические соединения между конструктивами при использовании контактолов 1-й и 2-й групп?
27.Назовите основные достоинства и недостатки, связанные с использованием контакто-
28. |
лов 1-й и 2-й групп. |
22 |
Какова природа получаемых соединений при монтаже накруткой (навивкой)? |
|
|
29. |
Какова последовательность операций при монтаже навивкой? |
|
30. |
От чего зависит качество электрических соединений, получаемых навивкой? |
|
31. |
Какие условия необходимо соблюдать при работе с автоматом, реализующим соедине- |
|
|
ния накруткой? |
|
32.Каковы преимущества и недостатки монтажа накруткой?
33.Охарактеризуйте разрушающий и неразрушающий контроль качества монтажа.
1